InsertMolding设计要点
INSERTMOLDING技术发展 共24页

母 模 NG狀態A是模源自與端子 配合空間紅色部分 為端子
公模
配合間隙A太小 導致塑膠無法進入
改善對策
上固定銷 下固定銷
成型模具加上下固定銷,起固定端子作用, 以保證足夠的配合間隙,利於塑膠流動,形成飽模
異常二 壓傷端子TAIL
•影響:成品TAIL邊緣出現銅絲,此為產品嚴重缺 陷
壓端子處
原因分析
產品用途
030-0001-008 030-0003-009
使用客戶
MOTOROLA
公司
第二節 生產流程圖
• 原料投入
原料幹燥
開機
• 裁切
調機
架模 端子投入
• 成型作業 包裝作業
入庫
第三節 制造 工藝特點
1)對機台,模具,端子定位精度要求很高;
機
台 送 料 機 構
送料定位紅外線感應報警
激感應顯示器
•
末來展朢
• 目前我們用INSERT MOLING制造的產 品有SWTCH一種,而我們期朢在不久的將 來能夠生產更多的產品.
谢谢!
立式成型
INSERT MOLDING
技術發展
目錄
• 一 立式成型 INSERT MOLDING介紹 • 二 生產流程介紹 • 三 製造工藝特點 • 四 制程問題及改善 • 五 進步與提高
第一節 立式成型 INSERT MOLDING
介紹
•INSERT MOLD • 將金屬嵌入預先制好的模腔內,然後將 •熔融之塑膠材料注入的一種成型方法
0.15MM,較CONN.端子薄弱,製程易拉巒形,造 成端子PITCH尺寸OUT OF SPEC
• 改善 a:來料製程管制端子扇形SPEC 0.10/76
简述嵌件注塑成型加工技术
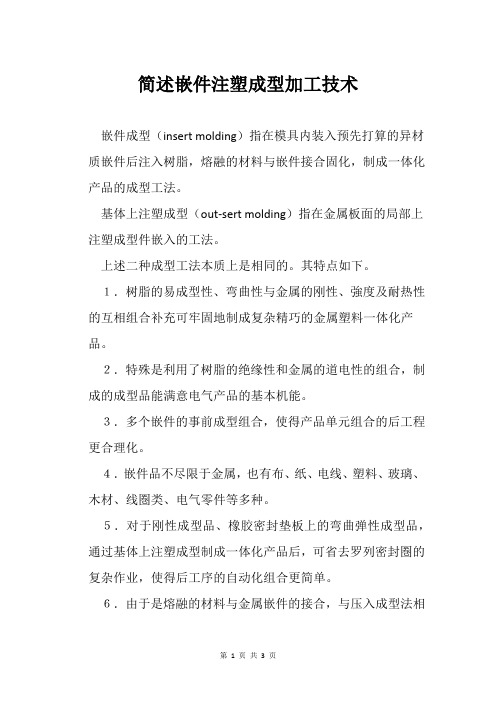
简述嵌件注塑成型加工技术嵌件成型(insert molding)指在模具内装入预先打算的异材质嵌件后注入树脂,熔融的材料与嵌件接合固化,制成一体化产品的成型工法。
基体上注塑成型(out-sert molding)指在金属板面的局部上注塑成型件嵌入的工法。
上述二种成型工法本质上是相同的。
其特点如下。
1.树脂的易成型性、弯曲性与金属的刚性、強度及耐热性的互相组合补充可牢固地制成复杂精巧的金属塑料一体化产品。
2.特殊是利用了树脂的绝缘性和金属的道电性的组合,制成的成型品能满意电气产品的基本机能。
3.多个嵌件的事前成型组合,使得产品单元组合的后工程更合理化。
4.嵌件品不尽限于金属,也有布、纸、电线、塑料、玻璃、木材、线圏类、电气零件等多种。
5.对于刚性成型品、橡胶密封垫板上的弯曲弹性成型品,通过基体上注塑成型制成一体化产品后,可省去罗列密封圏的复杂作业,使得后工序的自动化组合更简单。
6.由于是熔融的材料与金属嵌件的接合,与压入成型法相比较,金属嵌件间隙可以设计得更狭窄,复合产品成型的牢靠性更高。
7.抉择适当的树脂和成型条件,即是对于易変形破损的产品(如玻璃、线圈类、电气零件等),通过树脂也可密封固定。
8.抉择适当的模具构造,嵌件品也可彻低封入树脂内。
9.嵌件成型后,经过去芯孔处理,也可制成帯有中空凹槽的产品。
10.立式注塑机与机械手、嵌件品整列装置等的组合,嵌件成型工程大都可实现自动化生产。
自动嵌件成型系统设计抉择留意事项1.金属嵌件成型简单产生成型收缩率不均一,事先应做重要部位的样子、尺寸精度的极限实验。
2.注射过程中金属嵌件简单变形和移位,应充分考虑模具构成和简单保持金属嵌件的模具样子的设计。
对于嵌件样子不能转变的产品,事先实验是不行缺少的。
3.金属嵌件的罗列分别而使用输送器的场合下,金属嵌件之间和嵌件与振动球的接触,会使嵌件表面产生微小的损伤,而影响产品质量。
应事先确认其品质容许极限范围。
4.应事先测定金属嵌件由于冲压加工而引起的锯齿状、翘曲量、材料厚度差、直径差、敷金加工引起的厚度差等。
INSERTMOLDING模设计注意事项16页PPT

一.MOLDING模常見問題
1.端子尺寸与模仁尺寸配合問題.
A.端子尺寸与模仁尺寸配合干涉.
端子將 被刮壞 鍍層,嚴 重的將 令端子 彎曲影 響端子 平面度, 產品功 能受到 影響.
B.端子尺寸与模仁尺寸配合間隙過大.
端子与 模仁角 處將產 生溢膠 (毛邊) 不良,嚴 重的在 某些產 品結構 會影響 焊板.
五.端子頂出
&:如果端子外端离塑膠區域太遠.頂出後可能造成端子彎區不良.可在端子下方布頂針將 端子頂出(頂出型式不局限於頂針).
更多精品资源请访问
docin/sanshengshiyuan doc88/sanshenglu
四.模具排位
&:模具排位時要在研發設計端子同時進行.及時与研發溝通.確定好是端子單體擺放模式 &端子料帶擺放模式.模具結膠.端子尺寸和 模具結構關係緊密(如2板模須保證A尺寸足夠排流道和澆口).C尺寸要保證端子槽模仁的強 度足夠.B尺寸決定模具穴數和模座大小.
二.MOLDING模分模面選取
&:分模線要選取在端子伸出塑膠結合部分的表面,才能做出結構簡單,生產穩定,問題少 的MOLDING模具.根據這個原則可以確定產品是否可以開模.
前模 後模
三.端子槽模仁結構
&:端子槽溝槽尺寸与端子尺寸直接相關.設計此模仁尺寸須參考端子藍圖.
平靠封膠區域
斜角導引端子 落下區域
住宿工艺insertmolding紧固件标准

住宿工艺insertmolding紧固件标准插入成型(insert molding)是一种常用的住宿工艺,可以将紧固件固定在塑料零件中。
这种工艺的好处包括增加产品的强度和稳定性,提高生产效率,减少装配工艺。
在插入成型中,紧固件通常是预先组装在塑料件上,通过注塑成型工艺将它们固定在一起。
然而,为了确保成品符合质量标准,插入成型紧固件必须符合一些特定的标准。
首先,插入成型紧固件必须具有足够的强度和耐用性。
这是因为插入成型的过程会对紧固件施加较大的压力和力量,所以紧固件必须能够承受这些力量而不会断裂或损坏。
紧固件应该根据产品的需求制造,并且应该经过强度测试以确保其满足标准。
此外,紧固件的材料选择也很重要,应选择能够在特定环境条件下长时间使用而不会腐蚀或磨损的高质量材料。
其次,插入成型紧固件的尺寸和几何形状也必须符合标准。
紧固件的尺寸必须与塑料件的设计要求相匹配,以确保插入成型后的产品能够正常运行。
此外,在插入成型过程中,紧固件的几何形状也应该是可控的,以确保它们能够正确地插入塑料件中,并能够提供所需的功能。
另外,插入成型紧固件的表面处理也很重要。
紧固件的表面处理可以提高其耐腐蚀性能,并确保与塑料件的粘合良好。
表面处理的选择可以根据紧固件的材料和产品的要求来确定,常见的表面处理方法包括镀锌、镀铬、磷化和阳极氧化等。
所有的表面处理都应该符合相关的标准,以确保它们能够提供所需的保护和功能。
最后,插入成型紧固件的质量控制也是至关重要的。
在插入成型过程中,紧固件的位置和固定性必须得到准确控制,以确保产品的装配质量。
因此,质量控制应包括对紧固件的位置精度和固定力的测试,并根据测试结果进行必要的调整和改进。
此外,在产品质量控制过程中,还应包括对紧固件的尺寸、几何形状和材料的测试,以确保它们符合设计要求。
综上所述,插入成型紧固件的标准涉及强度和耐用性、尺寸和几何形状、表面处理以及质量控制等方面。
通过遵守这些标准,可以确保插入成型紧固件的质量和性能符合产品的设计要求,从而提高产品的可靠性和耐久性。
注塑insertmolding自动拉料成型技术

3.自动I/M开发简介 3.自动I/M开发简介 自动I/M
3-1-1自动I/M模块化设计-传送机构单元 自动I/M模块化设计I/M模块化设计
张力马达
传 送 方 向
拉力马达
Key Message:传送料带机构,主要利用拉张力步进马达转动+棘轮组动作 Message:传送料带机构 主要利用拉张力步进马达转动+ 传送料带机构,
Page:7 Page:7/15
3.自动I/M开发简介 3.自动I/M开发简介 自动I/M
3-1-2自动I/M模块化设计-模具单元 自动I/M模块化设计I/M模块化设计
1 2 1 2 3 4
3
A.托带定位设计 A.托带定位设计
B.端子定位设计 B.端子定位设计
Key Message:模具单元的精定位方式采由外而内设计可分成 Message:模具单元的精定位方式采由外而内设计可分成 A.料带托轨设计以 点定位B.端子设计以3 料带托轨设计以4 B.端子设计以 A.料带托轨设计以4点定位B.端子设计以3点定位 目的: 目的:稳定料带传输与确保端子精确植入
Fine Pitch 自动化I/M制造技术 (Pitch 0.5P以下) 自动化I/M I/M制造技术 0.5P以下 以下) 开发目标:0.4P 开发目标:0.4P PLUG BTB 22POS
Page:4 Page:4/15
2.立案背景 2.立案背景
2-2 I/M产能提升 I/M产能提升
4 PCS
Sensor On
Sensor OFF
Sensor动作示意 Sensor动作示意
Page:10/15 Page:10/15
3.自动I/M开发历程简介 3.自动I/M开发历程简介 自动I/M
INSERTMOLDING模具开发注意事项

INSERTMOLDING模具开发注意事项【摘要】INSERT MOLDING是塑胶模中的一类模具,俗称嵌件模具。
这类模具在塑胶材料的选用,模具设计及开发试模阶段中都会有一些与普通塑胶模具不同之处,以下进行详细讲述。
INSERT MOLDING模具中嵌件一般是冲压件,或者是螺纹嵌件,在注射合模前,它们必须在模具中保持一固定位置,而后在注射冲模完成后,最终与塑胶部分牢固的结合在一起,是非机械的连接。
此类产品的一般在产品开发中作为结构件出现,产品的强度要求较高,因此在选择塑胶材料上多选用含玻纤(GF)的料,一般有PC+GF,PA+GF,其中GF的含量一般在10%~50%。
玻纤是用玻璃制成的纤维,玻纤是标准的弹性体,伸长变形与应力成正比,直到断裂之前也没有屈服点,一旦去除应力,形变可完全恢复,从而具有优良的尺寸稳定性。
同时其在300度下强度保持不变,致使玻纤的增强塑料的拉伸强度提高2倍以上,其成型制品的强度与刚度都有所提高。
另外含玻纤的增强塑料具有较低的热传导性能和热变形温度,易于熔体在模腔内的充填,能在较高的温度下开模取出制品,因而缩短了模塑周期。
由于INSERT MOLDING产品结构的复杂性及材料的特殊性,决定了其产品设计及模具设计需要注意的细节。
产品设计方面:肉厚平均1.5mm,才能满足充填的流动特性和成型工艺要求,嵌件与塑件的结合才牢固。
脱模斜度比一般的塑件要大,因为产品的表面粗糙度差,脱模时摩擦力大。
模具设计方面:1)成品缩水率,由于产品的嵌件部分无收缩,所以要根据产品中嵌件的区域来放分段放缩水及不等方向放缩水来实现产品的尺寸要求。
有以下几种情况:塑件部分很少,绝大部分是嵌件的产品不放缩水率;塑件部分占少数,大面积都是嵌件部分不放缩水,反之部分按产品结构情况在XYZ三个方向放不等量缩水。
由于是分段放缩水率,因此分段后的整合技巧对模具设计人员就提出了相当高的设计经验和水平。
INSERT MOLDING的定位一般在模具上设置定位凸台,且需要对嵌件的X和Y方向进行精确定位。
塑料件IMD、INS工艺简介及设计注意要点

塑料件IMD、INS工艺简介及设计注意要点1. IMD、INS工艺原理及应用范围 (1)1.1 IMD、INS工艺简介 (1)1.2 IMD、INS工艺应用范围 (1)2. IMD、INS工艺流程 (1)2.1 IMD工艺流程 (1)2.2 INS工艺流程 (2)3. IMD与INS对比 (2)4. 设计注意要点 (2)4.1 IMD设计注意要点 (2)4.2 INS设计注意要点 (4)5. IMD、INS成本 (5)1.IMD、INS工艺原理及应用范围1.1IMD、INS工艺简介IMD(In-Mold Decoration):又称膜内装饰技术,将印制有花纹的膜直接放入模具内,使其吸附在注塑凹膜上,合模进行注塑。
INS(Insert Thermoforming-film to Molding):将预先吸塑成型并完成冲裁后的膜片放入注塑模具内,合模进行注塑。
1.2IMD、INS工艺应用范围IMD的应用范围:汽车左右出风口、中央面板、烟灰缸盖板、门护板装饰条等产品。
INS的应用范围:汽车排档器盖板、仪表罩、出风口、仪表板装饰条、门护板装饰条、散热器格栅等产品。
IMD、INS工艺的优点:注塑产品表面流纹及结合线可以被膜片饰条所覆盖。
2.IMD、INS工艺流程2.1IMD工艺流程IMD工艺流程如图1所示。
传输定位膜片夹紧吸附膜片合模注塑取件图12.2INS工艺流程输膜预成型冲裁3.IMD与INS对比IMD与INS对比见表1表14.设计注意要点4.1IMD设计注意要点●翻边角度:见图3●翻边深度:见图3● 结构圆角:见图3 ● 推荐结构:见图3图3● 双色IMD 工艺槽推荐结构:见图4图4推荐做成左边所示结构:翻边角度:β≥15°; 翻边深度:h ≤5mm ; 结构圆角:R ≥1mm 。
Rhβ双色IMD 工艺槽推荐结构: 工艺槽上部圆角:R 1≥0.5mm工艺槽底部圆角:R 2:(0.2-0.3)mm 工艺槽宽度:b ≥0.5mm 工艺槽深度:h=0.5mm R 1 R 2h b脱模方向4.2 INS 设计注意要点● 翻边角度:见图5 ● 翻边深度:见图5图5● 结构圆角:见图6图6βh翻边角度:β≥20° 翻边深度:h ≤90mmR结构圆角:R 极限是0mm 结构圆角推荐值:R ≥0.3mm脱模方向双色INS 工艺槽推荐结构:见图7图75. IMD 、INS 成本影响成本的主要因素: ① 膜的利用率② 膜的品质(花纹、厚度、质量、拉伸性等) ③ 零件尺寸由于INS 工艺比IMD 工艺多出两套模具(吸塑模具和冲切模具),故INS 工艺的成本比IMD 工艺的成本高。
Insert Molding设计要点

產 品 目 視 方 向
外輪Pin部 位
IM設計注意事項
b.篡動360加倒刺﹐正位度996﹐模仁沖歪產生毛 邊975
1.3灌膠影響及膠口設計 a. 膠口沖擊方向的端子易被沖歪(0.35MM料厚,簡支粱結構間距小於 4.0MM即要檢討)
b.AUDIO JACK膠口分拆﹐便于更換。
c.
IM設計注意事項
4.LED折彎尺寸對I/M后燈頭上翹的影響 7.98尺寸偏小會影響燈頭上翹
Contents:
一.端子于產品上的定位設計 二.端子于模具上的定位設計
一.端子定位設計
1.端子在塑膠成品中的牢固性 2.外部因素對端子固定牢固性的影響
3.塑膠外部端子在成型時的定位
4.塑膠產品上預先設計工藝孔以利 端子固定
由于通常都選用LCP(901-0006-016)原料縮水
取1.005 IM產品通常很小縮水只針對卡扣尺寸做相應調 整﹐其它地方不放縮水。 1.4 建分模面 注意模腔內一定要確保端子側面不會受到母模擦傷﹐這 一點是IM產品設計的關鍵這一點設計注意事項也有提到 分模面可以在模具組立圖或者零件圖下建立
IM設計步驟
四.設計步驟
1.5模仁分拆
1.1模仁分拆要注意封膠件的設計單一更換方便 1.2細長模仁要定位
1.6 尺寸標注 注意尺寸標注得完整
視圖對應關系
失效模式分析 五.失效模式分析
不 良 原 因 SH O R T不 1. 表面鍍錫﹐錫高溫熔化成錫絲 良 2. 端子未加隔欄被澆口沖歪 3. 端子漏切中carry 4. 折機壓出金屬絲 5. 端子浮在表面塑膠層太薄 不飽模 1. 產品肉厚不夠 2. 端子未定位變形 3. 成行條件 貼板不良 1. 端子貼板面變形 2. 來料正位度N G 3. 清模 植入不順 1. 沒有導向件或導向件不夠長 2. 端子來料變形 3. 切中carry變形 4. 制工圖面未管控端子來料 端子壓傷 1. 端子來料尺寸超差 2. 封膠件尺寸設計不合理 3. 模仁尺寸超規 4. 壓模 端子植反 1. 端子無折彎或折彎很小 1. 端子無折彎或折彎很小 2. LED 折彎折反 對 策 1. I/ 成型處不鍍或鍍層降低 M 2. 加隔欄定位 3. 加隔欄防呆 4. 拋光折彎模仁﹐控制來料截面 5. 增加定位PIN , 將端子在塑膠中准確定位 1. 與制工協調加肉厚 2. 正側面加定位pi n 3. 成行條件設置不當 1. 加墊塊滑塊整形 2.nsertm ol ng 前量測來料尺寸﹐確保來料 i di 3. 模具不清模是導致貼版不良的重要原因 1. 加導向件﹐導向設計標准化。 2. 導向件加寬﹐導向處寬度與成形處一致。 3. 與制工協調管控端子來料 4. 與制工協調管控端子來料 1. 與沖壓檢討﹐發對應模仁 2. 檢討放寬間隙﹐標准化 3. 模仁加工誤差 4. 壓模后封膠件沒有拋光 1. 加防呆設計 1. 加防呆設計 2. 折彎機加防呆機構﹐模具加防呆結構
- 1、下载文档前请自行甄别文档内容的完整性,平台不提供额外的编辑、内容补充、找答案等附加服务。
- 2、"仅部分预览"的文档,不可在线预览部分如存在完整性等问题,可反馈申请退款(可完整预览的文档不适用该条件!)。
- 3、如文档侵犯您的权益,请联系客服反馈,我们会尽快为您处理(人工客服工作时间:9:00-18:30)。
BY系列設計BKM
RJ45/RJ11系列
6.貼板型結構設計標准化如下圖
BY系列設計BKM
LED系列
1.LED極性防呆 用切腳長短防呆
2.LED封膠尺寸及負角度設計
BY系列設計BKM
LED系列
3.LED折彎尺寸變異大﹐模具管制端子變型加定位PIN及間隔PIN
限位﹐以防 側面露端子
端子到塑 膠表面距 離0.4以上 以確保飽
IM設計注意事項
1.6貼板產品設計 a.封膠處在端子直面處,折彎處因端子脹大 必須讓位以防貼板處端子被拉變形 b.圖面REV時要求封膠的直面段大於0.15以 確保,模仁強度 c.右圖A/C兩模仁留間隙0.01MM-0.02MM預 壓端子確保共面度
1.7模仁的硬度﹐封膠件的自我保護 膠口ASP﹐端子輿封膠件硬度比值362
要因一. 定位销定位及公差配合: 1-1.柱面定位
如下圖模具及定位銷所示:
圓柱直徑 E-(0.02~0.03)
定位圓銷在模具上位置
要因具体描述
要因二. 定位槽定位及公差配合: 设计时我们要考虑到端子的公差来确定模仁公差,准确的定位端子。 2-1.端子的水平方向 在I/M MOLDING中TAIL脚在水平方向就是靠定位槽的槽壁来定位的。
1.加墊塊滑塊整形
2.來料正位度N G
2.insertm olding 前量測來料尺寸﹐確保來料
3.清模
3.模具不清模是導致貼版不良的重要原因
植入不順 1.沒有導向件或導向件不夠長 1.加導向件﹐導向設計標准化。
2.端子來料變形
2.導向件加寬﹐導向處寬度與成形處一致。
3.切中carry變形
3.與制工協調管控端子來料
不同的塑膠原料有其不同的物理特性,其成型后的机 械性能(如強度)有很大的差異,因此在對產品使用過程中 有強度要求的,在選擇塑膠原料時需對原料的物理特性加 以考量.在成本允許的范圍內最大限度的使用机械性能好 的塑膠料.
現我們所用之工程塑膠均能滿足強度要求.如: PBT,LCP,PA6T,PA9T,PPA,PPS等.
IM設計注意事項
1.2端子外漏產品的模仁設計 a.內側露端子:如下圖A值公差影響內側刮出金屬屑或不飽模現象 側面肉厚要確保0.2以上同時端子要有尺寸管制才能確保不露端子 b. 外側露端子:外側漏端子跑滑塊方式成型,切記不可靠母模封膠方式成 型
即端子可以與公模側面有貼靠不能與母模有任何貼靠
c.上下表面露端子:上下表面露端子要注意端子防止塑膠之間剝離
定位不准就会出现压伤或者溢胶的现象。经过不断的摸索和验证得出了 比较合理的公差。如下所示:
端子尺寸为:W+/-a, 则定位槽為(W+a)+0.01/+0.005
影響端 子的強
度
端子的寬度
W 端子腳寬度 產品位置寬度
W 端子寬度
T 端子厚度
要因具体描述
要因二.定位槽定位及公差配合:
2-2.端子的垂直方向
Insert Molding設計要點
產品間介
INSERT MOLDING 埋入成型是指將埋入件放入模具成型的工藝過程 埋入件可以是塑膠或者金屬﹐這里我們主要講的是0.15MM-0.5MM板厚的 金屬件﹐埋入成形有密封﹐超薄﹐堅固等優點﹐同時成本也相對較高。 鑒于目前開發費用居高, 對于AUDO JACK一般變更腳長共用現有模具 LED盡量不開新模 JM一方面共用現有料號﹐一方面采用插端子形式替代﹐特別超薄料號可 以新開模具
Contents
一.產品圖確認 二.原料及機台選用 三.設計注意事項 四.設計步驟 五. 失效模式分析 六.BY系列設計BKM
產品圖確認
一.藍圖確認主要事項:
1.產品CPK尺寸公差標注單向公差調整 2.產品結構 ﹕逃料﹐肉厚﹐拔模﹐死角 3.IM產品端子外露面檢討(包括產品六個面) 4.端子標到塑膠的尺寸(該類尺寸受到來料影響) 5.端子CPK尺寸(功能尺寸,封膠工藝尺寸) 6.產品原料選擇
1-1.柱面定位
柱面定位销定位是靠销子的柱面定位,它的配合公差间
隙为0.01~0.03mm.在I/M MOLDING 中常用在料带式端子中.
定位不准可能会引起产品的溢胶,毛边等问题。
如下圖端子所示:
端子PITCH
圓孔直徑 E
端子 PITCH
端子的寬度
端子的寬度 圓孔直徑 E
產品位置寬度
要因具体描述
位
端子寬 模仁槽
模仁槽寬度方向: 規格值=端子上限 公差=0/+0.005
模仁槽厚度方向: 規格值=端子厚度 公差=+0.005/+0.01
要因具体描述
要因四.塑膠產品上預先設計工藝孔:
塑膠產品上預先設計工藝孔,以利于在后續設計模具時用銷子 壓緊端子,以防端子被衝歪.
目前廠內I/M基本已導入銷子定位端子結構.
4.制工圖面未管控端子來料 4.與制工協調管控端子來料
端子壓傷 1.端子來料尺寸超差
1.與沖壓檢討﹐發對應模仁
2.封膠件尺寸設計不合理
2.檢討放寬間隙﹐標准化
3.模仁尺寸超規
3.模仁加工誤差
4.壓模
4.壓模后封膠件沒有拋光
端子植反 1.端子無折彎或折彎很小
1.加防呆設計
1.端子無折彎或折彎很小
1.加防呆設計
IM設計注意事項
3.手動埋入件成型注意事項 3.1螺杆規格與塑件大小(機台噸位) 3.2埋入工序所用時間對成型的影響特別用PA46時 3.3端子剛性對成品的收縮及變形的影響
4. 自動埋入件成型注意事項 4.1確保自動埋入機構的重復定位精度 4.2注意植入件的導向機構設計﹐試模時先以手動試﹐確保
不壓傷模具。 4.3多模穴要確保平衡進膠
IM設計注意事項
三.IM設計注意事項
1 手動埋入件模具設計注意事項 1.1封膠及導向設計 a.埋入件封膠尺寸公差A+/-0.02MM b.封膠模仁尺寸公差A+0.02+0.005MM c.封膠件設計小型標准化便於更換便於加工 d.封膠件材料強度要確保比埋入件硬度高,確保壓端子後模仁沒有損傷,可以考 慮用鍍鈦等方式提高模仁硬度 e.白端子處封膠件要加導向便於ROBOT埋入端子,封膠處導向高度以不高出塑膠 成型面為優設計.導向與封膠一體設計以防錯位。 f.盡量不要采用斜面封膠, 斜面封膠對端子的尺寸要求比較苛刻,涉及到CPK尺寸 較難保正
1.4I/M應用三板模設計要點(能用兩板堅決不用三板) a.剝料板厚度大於20MM b.進膠口設計如圖 c.4根拉桿在母模階梯螺釘要削雙邊防轉 d.一模做2個料號時,注意流道轉向設計 e.產品料量與機台料管匹配
1.5開模方向的選擇 a.第一原則端子任意側面不能受力 b.第二原則封膠不選斜面方式 c.第三原則考慮拔模頂出跑滑塊
四.設計步驟
IM設計步驟
1.藍圖整理 1.1 根據2D建3D注意將建好的3D轉成2D對比制工2D藍圖 1.2 3D注意事項: 藍圖上的單向公差要調整﹐ 端子與塑膠建成一體零件 有需要拔模的地方跟制工溝通﹐并在2D藍圖中體現出來 確認的3D要反給制工更新2D藍圖
IM設計步驟
四.設計步驟
1.3 放縮水 由于通常都選用LCP(901-0006-016)原料縮水 取1.005 IM產品通常很小縮水只針對卡扣尺寸做相應調 整﹐其它地方不放縮水。 1.4 建分模面 注意模腔內一定要確保端子側面不會受到母模擦傷﹐這 一點是IM產品設計的關鍵這一點設計注意事項也有提到 分模面可以在模具組立圖或者零件圖下建立
定位孔
產 品 目 視 方 向
外輪Pin部 位
IM設計注意事項
b.篡動360加倒刺﹐正位度996﹐模仁沖歪產生毛 邊975
1.3灌膠影響及膠口設計 a. 膠口沖擊方向的端子易被沖歪(0.35MM料厚,簡支粱結構間距小於 4.0MM即要檢討) b.AUDIO JACK膠口分拆﹐便于更換。 c.
IM設計注意事項
2. 加隔欄定位
3.端子漏切中carry
3. 加隔欄防呆
4.折機壓出金屬絲
4. 拋光折彎模仁﹐控制來料截面
5.端子浮在表面塑膠層太薄
5. 增加定位PIN ,將端子在塑膠中准確定位
不飽模 1.產品肉厚不夠
1. 與制工協調加肉厚
2.端子未定位變形
3.成行條件
2. 正側面加定位pin
3.成行條件設置不當
貼板不良 1.端子貼板面變形
模
4.LED折彎尺寸對I/M后燈頭上翹的影響
7.98尺寸偏小會影響燈頭上翹
Contents:
一.端子于產品上的定位設計 二.端子于模具上的定位設計
一.端子定位設計
1.端子在塑膠成品中的牢固性 2.外部因素對端子固定牢固性的影響 3.塑膠外部端子在成型時的定位 4.塑膠產品上預先設計工藝孔以利
端子固定
BY系列設計BKM
RJ45/RJ11系列
4.產品肉厚設計要求﹐通常塑膠到端子的距離保証在0.20MM以上﹐以防 不飽模 當肉厚設計0.20MM時要加定位PIN定位端子以防端子被進膠沖擊浮到表 面
定位PIN防端子上浮 5.定位針設計需優先考慮大孔定位﹐定位針設計標准 化﹐如下圖其中 角度取6度不合理﹐頭部太鈍不利于擺放。
原料及機台選用
二 .原料及機台選用
1.原料選用原則: 1.1黑色LCP(901-0006-016)第一優先選擇 1.2有白色要求的用(901-0009-016) 1.3其它原料﹐需要驗証 2.機台選用 2.1JM類百塑/住友 手動作業兼ROBOT 2.2LED類立式機 手動作業 2.3JACK類臥式拉帶機
IM設計步驟
四.設計步驟 1.5模仁分拆 1.1模仁分拆要注意封膠件的設計單一更換方便 1.2細長模仁要定位
1.6效模式分析
五.失效模式分析
不良 原 因