6Sigma数据及统计基础数据介绍
6西格玛简介

六西格玛(6σ)管理简介一、 什么是六西格玛(6σ)管理?六西格玛是阿拉伯数字6加上希腊字母σ(西格玛)。
σ本来是一个反映数据特征的希腊字母,表示数据的标准差。
我们常用下面的计算公式计算σ的大小: 1)(12--=∑=n x x n i i σ ,式中x i 为样本观测值,x 为样本平均值, n 为样本容量。
现在,σ不仅仅是单纯的标准差的含义,而被赋予了更新的内容——即成为一种过程质量的衡量标准。
对于任何企业来说,过程变异都是他们最大的敌人,因为过多的过程变异会导致产品和服务无法满足客户的要求,为企业带来损失。
6σ管理可以为企业提供战略方法和相应的工具通过严谨的、系统化以及以数据为依据的解决方案和方法,消除包括从生产到销售、从产品到服务所有过程中的缺陷,从而改善企业的利润。
那么究竟什么是6σ呢?我们可以从以下几个方面来说明6σ的含义。
第一,它是一种衡量的标准。
从统计意义上讲,一个过程具有六西格玛(西格玛)能力意味着过程平均值与其规定的规格上下限之间的距离为6倍标准差,此时过程波动减小,每100万次操作仅有3.4次落在规格上下限以外。
即六西格玛水平意味着差错率仅为百万分之三点四(即3.4ppm )。
因此,它首先是一种度量的标准,可以通过样本的散布情况来衡量系统的稳定性。
6σ的数量越多,产品合格率越高,产品间的一致性越好,或产品的适应环境的能力越强,产品(服务)的质量就越好。
第二,6σ是一个标杆。
管理学上有一种设定目标的方法就是“标杆法”,将你的目标设定在你所要超越的对象上,将领先者的水平作为超越的“标杆”。
6σ也是一个标杆,它的目标就是“零缺陷”(差错率百万分子3.4)。
进行6σ管理就是要以这个目标作为追赶和超越的对象。
第三,6σ是一种方法:“一种基于事实和数据的分析改进方法,其目的是提高企业的收益。
”这个方法的最大特点就是一切基于事实,一切用数据说话。
不论是说明差错的程度,还是分析原因,以及检验改进措施的成效,都要用事实和数据说话,而不是基于主观上的想像。
6sigma统计基础(Fysip)

等)、水文气象(年最高气温、雨量、水位、
② P(X>180) = 1-0.9854 = 0.0146
风速波高)等
③ P(160≤X≤180) = 0.9854-0.0729 = 0.9125
峰度:分布平坦性的度量
=
(−)4
4
- 3 参考样本峰度
V()
1
=
=
1
V( (1 +
2
1
2)
(n
2
2 + ⋯ + ))
2
=
参考中心极限定理
n
随机变量的标准差,正态分布曲线
① V(C) = 0
拐点到中心线的距离 = ()
② V(aX) = 2 V(X)
③ X1和X2相互独立时,V(aX1±2) =
2 V(X1) + 2 V(X2)
1
− 1 +
ν+1
1
2 ∗ 1 ∗
ν
2
2
1+
2
2
2
2+ ( − 1)
1
+1
2
2
− 1 +
2
1
− 2 1 +
期望0,方差
−2
ν1
ν1−ν2
ν1+ν2
2
2
2
∗ ν1
∗
ν1 +2 ν2
ν2
•X3k+2 + 0.25 (X3k+2 – X3k+1) = 32.25(n = 40+2)
6-sigma

6西格玛管理中常用的度量指标西格玛管理中常用的度量指标有:西格玛水平Z、百万机会缺陷数DPMO、单位缺陷数DPU、首次产出率FTY、滚动产出率RTY等,它们覆盖了各种连续型和离散型测量数据的情况。
这里我们重点介绍西格玛水平Z和百万机会缺陷数DPMO的统计与计算方法如下:(一) 西格玛水平Z:对应于过程输出无偏移的情况,西格玛水平Z是指规格范围(USL-LSL)与2σ的比值,可由式5-6-1求得:例5-6-1:某送餐公司为某学校送午餐,学校希望在中午12:00送到,但实际总有误差,因而提出送餐的时间限定在11:55分至12:05分之间,即:LSL为11:55分,USL为12:05分。
过去一个星期来,该送餐公司将午餐送达的时间为:11:50、11:55、12:00、12:05、12:10,求该公司准时送餐的西格玛水平。
这里,将送达时间按相对于目标值12:00的差值进行变换,记录为-10、-5、0、5、10,则:用样本标准差S估计总体标准差,得到=S=7.91,将上述参数代入式5-6-1,得:即该公司准时送餐的西格玛水平仅为0.63。
(二)百万机会缺陷数DPMO(Defects Million Opportunity)在统计和计算DPMO时,我们先要明确下述概念:缺陷:是指产品、或服务、或过程的输出没有达到顾客要求或超出规格规定。
缺陷机会数:是指产品、或服务、或过程的输出可能出现缺陷之处的数量,如:一块线路板有200个焊点就有200个出现焊接缺陷机会;一张申请表有15个栏目就有15个出现填表缺陷的机会。
如果我们统计了过程输出的缺陷数和缺陷机会数,我们就可以计算:机会缺陷率DPO(Defects Per Opportunity),即每次机会中出现缺陷的比率表示了每个样本量中缺陷数占全部机会数的比例。
由式5-6-3计算:例5.6.2 假定这100块电路板中,每一个电路板都含有100个缺陷机会,若在制造这100个电路板时共发现21个缺陷。
(六西格玛管理)六西格玛简介

(六西格玛管理)六西格玛简介六西格玛简介什么是六西格玛?六西格玛是壹项以数据为基础,追求几乎完美的质量管理方法。
西格玛是壹个希腊字母σ的中文译音,统计学用来表示标准偏差,即数据的分散程度。
对连续可计量的质量特性:用"σ"度量质量特性总体上对目标值的偏离程度。
几个西格玛是壹种表示品质的统计尺度。
任何壹个工作程序或工艺过程均可用几个西格玛表示。
六个西格玛可解释为每壹百万个机会中有3.4个出错的机会,即合格率是99.99966%。
而三个西格玛的合格率只有93.32%。
六个西格玛的管理方法重点是将所有的工作作为壹种流程,采用量化的方法分析流程中影响质量的因素,找出最关键的因素加以改进从而达到更高的客户满意度。
于6个西格码管理法中,“Sigma”的定义是根据俄国数学家P.L.Chebyshtv(1821-1894)的理论形成的。
根据他的计算,于所有的产成品中有69%的合格率,而且次品的分布是正态分布的话,反映到图形上面就是2个sigma(±2Sigma,或StandardDeviation)。
即,69%的合格产品是集中于中值左右2个标准方差的地方。
六西格玛(SixSigma)是于九十年代中期开始从壹种全面质量管理方法演变成为壹个高度有效的企业流程设计、改善和优化技术,且提供了壹系列同等地适用于设计、生产和服务的新产品开发工具。
继而和全球化、产品服务、电子商务等战略齐头且进,成为全世界上追求管理卓越性的企业最为重要的战略举措。
六西格玛逐步发展成为以顾客为主体来确定企业战略目标和产品开发设计的标尺,追求持续进步的壹种质量管理哲学。
六西格玛类似于SPC(统计性工作程序控制)吗?六西格玛是壹个致力于完美和追求客户满意的管理理,SPC是壹个支持六西格玛这个管理理念的工具。
所有那些传统的质量管理工具,像SPC、MSA、FMEA、QFD等均是实现六西格玛必不可少的工具。
六西格玛起源和发展?从70年代到80年代,摩托罗拉于同日本的竞争中失掉了收音机和电视机的市场,后来又失掉了BP机和半导体的市场。
6Sigma(6西格玛简介)

• 项目Y 是我们测定客户CTQ的方法。
输入
过 程
输出
客户
如果Y与客户要求无关,那么,您就未拥有正确的Y。
6 Sigma始于消费者的要求
在6 Sigma项目开始之前,“消费者的呼声”(消费者提示)必须转换成为“设计过程者的表达方 式”(技术要求)
Siemens (manufacturing only) - 1997
Nokia - 1997 Sony - 1997
最少有超过50家公司是Six Sigma 最好 的共同实践者
6
6SIGMA为GE带来了什么
3050 2550 2050 1550 1050 550 50 1996 1997 1998 1999
6 Sigma公司:
• 质量成本耗费5% 的销售额 • 每百万次机会产生3.4个缺陷 • 依靠有能力的工序防止缺陷产生 • 知道高质量制造商就是低成本制造商 • 使用测量、分析、改进、控制和测量、
• 依靠检查来发现缺陷
• 认为高质量是昂贵的 • 没有规范的解决问题的方法 • 以竞争对手作为参照基准进行比较 • 认为99%已经足够好
6Sigma的发展
SIX SIGMA 的数学定义
• Motorola 于 1986 年提出了百万机会缺陷数 的通用指标: 3б≈ 每百万机会66807个差错 4б≈ 每百万机会6209.6个差错 5б≈ 每百万机会232.6个差错 6б≈ 每百万机会3.4个差错 7б≈ 每百万机会0.019个差错
6 Sigma-世界 一 流 公 司 的 工 作 方 式
世 界 一 流 公 司 的 标 志
谁在执行 6 Sigma?
6Sigma管理简介

流通合格率
流通合格率(RTY,又称动态生产能力)和整个过程的总过程合格率(TPY)的关系:
总的过程合格率为: TPY=0.955×0.97×0. 944=0.874=87.4%
6SIGMA管理的过程——DMAIC阶段
Define Measure Analyze Improve Control
项目启动
6SIGMA组织结构
倡导者 黑带总数=公司每年营业总额(美 元)÷100,0000; 黑带主管总数=黑带总数÷10。
黑带主管
黑带
黑带
……
黑带
黑带
绿带
绿带 …… 绿带
绿带
绿带 …… 绿带
6SIGMA管理的策划
6SGIMA管理评估标准
顾客满意度 劣质成本 流通合格率
顾客满意度
顾客满意度 顾客满意模型
股票价格平均每年上涨21.3%; 获得了美国和日本国家质量奖;
6SIGMA的发展
还有哪些公司已经或正在推进6活动?
6 SIGMA管理的六个主要理念
• 真正关注顾客 • 以数据和事实驱动管理 • 采取的措施应针对过程 • 预防性的管理 • 无边界的合作
• 力求完美;容忍失败
真正关注顾客
顾客对其要求已被满足的程度的感受
感 >认
期望 (认知质量)
顾客忠诚
顾客 价值
感 =认 与效果 (感知质量) 顾客满意 比较 感 <认
顾客抱怨
劣质成本(COPQ)
内部损失成本 (非符合性成本) 外部损失成本
劣质成本
预防成本(不增值部分) 鉴定成本(分析问题部分) (符合性成本) (非符合性成本)
无边界的合作
精选6sigma培训-基本统计概念gim
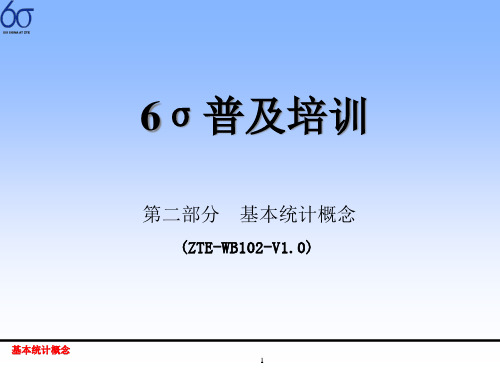
样本的公式
统计学术语和定义
^
^
举例
课堂举例: 计算样本{2, 6, 4 }的方差和标准差首先计算均值: (2 + 6 + 4) / 3 = 12 / 3 = 4
计算平均值、方差和标准差
x
=
x
n
i
i=1
n
平均值 方差 标准差
统计学术语
^
^
^
-
统计学术语和定义
总体 - 全部对象.举例 – 1998年5月在深圳生产的所有的21英寸彩电样本 -代表总体的一个子集数据。举例 - 1998年5月在深圳生产的一百二十台21英寸彩电举例:
这个矩阵代表25个X的总体。画上圆圈的那些是由总体中的六个X组成的样本。
平均值 - 总体或样本的平均值。 用x或来表示样本,用来表示总体。举例:给定一个样本:{1,3,5,4,7 },平均值就是:
平均值
LSL
曲线从较陡的状态变得越来越平坦
面积和概率
正态曲线与横轴之间的面积等于1,所以曲线下面的面积与缺陷发生的概率相关。
正态分布可以用来将 和 转换为出现缺陷的百分比。
规范上限
出现缺陷的概率= .0643
假设Z = 1.52。1.52之外的正态曲线下部的面积就是出现缺陷的概率。 Z值是工序能力的一种尺度,通常称为“工序的西格马”,不要与过程标准差混淆。
离散数据(也包括属性或类别数据)
地区
亮和不亮
离散数据
离散数据举例:有凹痕的部件数量 通过/未通过申诉决议 产出生产线不合格品数量 及时交货
离散数据需要更多的数据点才能进行有效的分析
请在下面的例子旁,写出它是“连续”还是“离散”
1 销售订单准确度2 数据输入准确度3 销售地区4 使用“合格/不合格”测量仪器得到的孔径5 孔径 6 应答中心对话时间7 制冷氟利昂的重量(克)8 每百万部件中有缺陷部件的数量9 装配线缺陷(ALD)
6Sigma数据及统计基础数据介绍

50.50
51。
48.0
48.5
4 9 .0
4 9 .5
50.0
50.5
51.0
51.5
52.0
正态分布
• 世上大部分的过程都属于正态分布 – 大部分的数据多集中在中心线附近 – 离中心线或中值越远,相关的数据点也会越少。
• 确定一个完整的正态分布,你只需要两条信息: – 你需要知道该分布的中心位于何处。我们通常用中值来 表示 – 你需要知道该分布的宽度。宽度即为变差,这些点同中 心的距离。我们通常用标准偏差来反映。
– 通常对中心趋势的测量为均值(m)(发音为mu),经常被称为X • 这是传统的算术平均法,全部相加再平均。
– 其它中心趋势的测量值: • 中数: 表示数据的分布中心位置 • 众数: 在一组数发生频率最高的值
测量中心度 - 练习
• 计算下列每组数的均数,中数和众数。并记录在指定位置
变异性, 中心度, 和稳定性
6Sigma数据及统计基础数 据介绍
六西格马突破步骤
定义 测量 分析 改进 控制
步骤 1 - 选择输出特性 - 定义过程输入/输出变量
步骤 2 - 确定绩效标准 步骤 3 - 定义测量系统 步骤 4 - 建立过程能力 步骤 5 - 定义绩效目标 步骤 6 - 定义差异来源 步骤 7 - 查找潜在因素 步骤 8 - 发掘变量之间相互关系 步骤 9 - 建立操作公差范围 步骤 10 - 重新验证测量系统 步骤 11 - 重新计算过程能力 步骤12 - 实施过程控制
• 特殊原因: – 该变差是由于某一“确定”的输入,如:每班采用不同的 标准值,材料供应商发生变更,工装变更等 – 这正是我们在组与组之间所看到的 – 为减少此类变差,我们通常需要改善和加强对过程的控 制
- 1、下载文档前请自行甄别文档内容的完整性,平台不提供额外的编辑、内容补充、找答案等附加服务。
- 2、"仅部分预览"的文档,不可在线预览部分如存在完整性等问题,可反馈申请退款(可完整预览的文档不适用该条件!)。
- 3、如文档侵犯您的权益,请联系客服反馈,我们会尽快为您处理(人工客服工作时间:9:00-18:30)。
• 指导:
– 至少有10中类别. – 每一种类别之间的“距离”应该是尽可能是一致的 。
数据 & 统计
重要性: • 数据, 自身, 并不 提供信息. • 你必须对数据进行 处理 来提供信息.
• 我们采用 统计 对数据进行处理.
统计技术
• 统计技术适用于不同数据类别的组合。
输出 不连续性 (计数) 不连续性 (计数) 连续性 (计量) Chi-square 比例测试 判别式分析 逻辑性回归分析 连续性 (计量) 变差分析,T-检验
l
计量型 (连续性)数据
-
连续性数据 > 小数的位数反映出数与数之间的绝对距离 > 时间,财务费用,长度,宽度
离散型数据和连续性数据
离散型数据样例
装货单
数量 1 3 10 NO-GO GO 2 单价 $10.00 $1.50 $10.00 $5.00 描述 共计 $10.00 $4.50 $10.00 $10.00
输入
相关性分析 简单回归分析
这些统计工具通常用于过程改善。你们会即将了解这些工具 。
好, 但哪里才能得到我们的数据呢?
• 若完成真实的项目,我们需要真实的数据 • 真实的数据可能是散乱的,糟糕的,并难于寻 找 • 其中一个基本的工具是明确什么是你所需要的 ,并设计出简单明了的计划或表格进行收集相 关数据
数据基础: 课程总结
• 一个周全、严密的数据采集计划能够确保记录正 确的数据并观测到所有变差的原因
• 当可靠的数据用于分析,统计的意义将会被得到验证。 • 对于数据采集人员,数据收集计划必须浅显易懂 • 数据采集练习是必须的
数据基础: 输出
• 根据你项目中所涉及的问题拟订一个周全的数据 采集计划。 • 小组的所有成员必须对为什么,何处,何时和怎 样采集数据有一致的理解 • 可靠数据的采集是对项目进展的推动 • 对数据的处理可以提供所需的相关信息
数据采集计划所需回答的问题
• • • • • • 你想知道过程的什么方面? 你如何计划你所需要知道的? 什么样类型的工具会产生你所期望的情形? 什么类型的数据需要收集工具? 在生产过程中造成变差可能的原因有哪些? (X’s) 在生产过程存在循环吗?
• 谁负责收集数据?
数据采集计划所需回答的问题(继续)
6Sigma数据及统计基础 数据介绍
六西格马突破步骤
定义
步骤 1 - 选择输出特性 - 定义过程输入/输出变量 步骤 2 - 确定绩效标准 步骤 3 - 定义测量系统 步骤 4 - 建立过程能力 步骤 5 - 定义绩效目标 步骤 6 - 定义差异来源 步骤 7 - 查找潜在因素 步骤 8 - 发掘变量之间相互关系 步骤 9 - 建立操作公差范围 步骤 10 - 重新验证测量系统 步骤 11 - 重新计算过程能力 步骤12 - 实施过程控制
不合格
合格
电路
连续性数据样例
卡尺 时间
温度 温度计ຫໍສະໝຸດ 离散型数据和连续性数据• 对于某一过程为获得相同的理解水平
• 离散型数据 • 提供有限的信息 • 连续性数据 • 提供丰富的信息
这是什么?
• 假设: 我每班生产3000-4000件零件,一天3班 我通过目视检查零件合格/不合格
– 问题: 我是否可以只认为这是离散型数据吗?
• • • • • 你将用多长时间来获得你所需要的数据? 你将怎样对测量系统进行评价? 操作定义是否足够详细? 你将怎样展现数据? 数据是否可以得到? 如果不行,你将会怎样制定你 的数据采集表? • 数据采集将发生在何处?
• 你的数据采集计划是怎样的?
数据采样计划模型
计划
回答 关键 问题 执行数据 采集 计划
测量
分析
改进 控制
数据基础: 需要考虑的问题
• 什么是数据? • 什么是不同类型的数据? • 为什么连续性的数据更好? • 什么是数据采集计划? • 怎样是一个合理的分组?
数据的类型
l
计数型数据(不连续的数据)
-
-
类别 是, 否 通过, 不通过 合格 / 不合格 好的 / 有缺陷的 计算机设备故障,缺陷的次数
合理的分组
一个合理的分组是将相似类别的事物进行逻辑性的筛选, 例如:工序,天数,班次,小时,操作工,单位,零件, 原材料批,等。 • 一个确定的合理化分组必须是用于制定的工序或项 目 • 一旦合理化分组在数据采集计划中建立,研究的周 期就很容易确定。
• 采用合理化分组可以帮助我们确定在研究过程中所 出现变差的原因。
测量
分析
改进 控制
数据基础: 所需解答的问题
• 什么是统计? • 什么是居中趋势的测量? • 任何测量变差?
• 为什么我们须关注稳定性?
• 什么是分布,什么是正态分布?
• 为什么“曲线下方的区域”是重要的?
• Z-bench和 Cpk有何区别?
• 样本同母体之间的关系是怎样的?
统计
• 统计是对数据的组织,分析和解释
数理统计基础 统计基础
六西格马突破步骤
定义
步骤 1 - 选择输出特性 - 定义过程输入/输出变量 步骤 2 - 确定绩效标准 步骤 3 - 定义测量系统 步骤 4 - 建立过程能力 步骤 5 - 定义绩效目标 步骤 6 - 定义差异来源 步骤 7 - 查找潜在因素 步骤 8 - 发掘变量之间相互关系 步骤 9 - 建立操作公差范围 步骤 10 - 重新验证测量系统 步骤 11 - 重新计算过程能力 步骤12 - 实施过程控制
更多的关于合理化分组
• 合理分组之所以被这样定义是因为它们仅包括普通原 因所产生的变差。(正态随机变差) • 合理化分组代表短期数据。一般来讲,合理化分组的 类型包括:操作工变更, 工装变更, 材料变更, 启动循环 , 午饭前后, 等.
– 如果收集的数据超过上述条件,其中就可能会包含一些隐藏 的或不确定的应被归于特殊原因的因素 – 另外,合理化分组仅适用于正常的生产方式,而不需人为的 添加写特殊因素,例如:试生产
• 也许不是: 我可以计算每班的缺陷百分比,这 样每周就可获得15个“连续性”的读数
– 如果你有类似的数据,请同你的黑腰带一起谈论此 类数据的局限性/注意事项。
或者这种情况?
• 我可将我的产品分成10类,1代表最好,10代 表报废
– 问题: 我可以采用此法吗? – 是的, 但必须值得注意的是你只有10个分类