塑料模设计塑料制件的设计
塑料模设计说明书
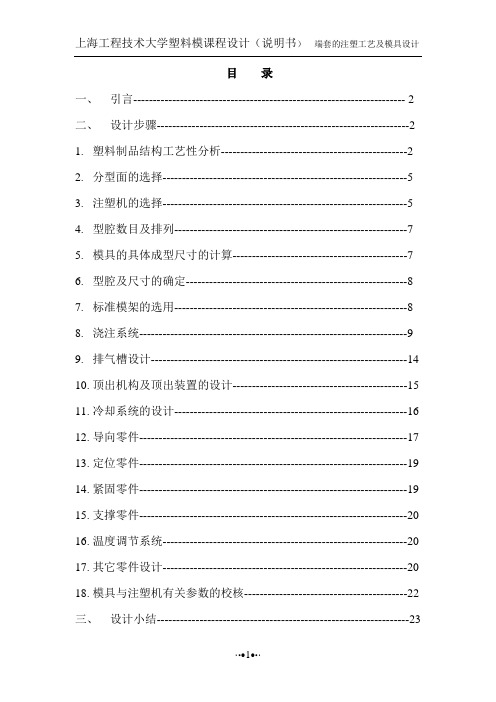
目录一、引言---------------------------------------------------------------------- 2二、设计步骤-----------------------------------------------------------------21.塑料制品结构工艺性分析------------------------------------------------22.分型面的选择---------------------------------------------------------------53.注塑机的选择---------------------------------------------------------------54.型腔数目及排列------------------------------------------------------------75.模具的具体成型尺寸的计算---------------------------------------------76.型腔及尺寸的确定---------------------------------------------------------87.标准模架的选用------------------------------------------------------------88.浇注系统---------------------------------------------------------------------99.排气槽设计------------------------------------------------------------------1410.顶出机构及顶出装置的设计---------------------------------------------1511.冷却系统的设计------------------------------------------------------------1612.导向零件---------------------------------------------------------------------1713.定位零件---------------------------------------------------------------------1914.紧固零件---------------------------------------------------------------------1915.支撑零件---------------------------------------------------------------------2016.温度调节系统---------------------------------------------------------------2017.其它零件设计---------------------------------------------------------------2018.模具与注塑机有关参数的校核------------------------------------------22三、设计小结-----------------------------------------------------------------23四、参考文献----------------------------------------------------------------23 一. 引言塑料工业是一门新兴的工业,是随着石油工业发展应运而生的。
塑料制品分析模具结构

塑料制品分析模具结构引言塑料制品在现代工业生产中占据着重要地位,而模具作为塑料制品生产的关键工具,其结构设计对于产品质量和生产效率有着直接影响。
本文将从塑料制品分析模具结构的角度出发,探讨模具结构的种类和设计原则。
1. 模具结构的种类1.1 单腔模具单腔模具是最简单的一种模具结构,适用于生产单一塑料制品。
其结构简单直接,易于制造和维护,成本相对较低。
然而,由于单腔模具每次只能生产一件产品,效率较低,适用于小批量生产。
1.2 多腔模具多腔模具是在一个模具中设置多个腔室,可以同时生产多个产品。
多腔模具的生产效率较高,适用于大批量生产。
然而,多腔模具的结构复杂,制造和维护难度较大,成本较高。
1.3 滑动模具滑动模具是指在模具中设置滑动块或滑动模块,用以实现产品中的倒角、凹槽等复杂结构。
滑动模具可以增加产品的设计灵活性和功能多样性,但同时增加了模具结构的复杂性和制造难度。
1.4 套模模具套模模具是指在一个模具中设置多个附加模块,用以实现产品中的套模结构,如套芯、套筒等。
套模模具可以实现产品的空心结构、腔体内壁的形状复杂性,但制造和维护难度较大。
2. 模具结构的设计原则2.1 结构简洁性模具结构应尽量简洁,减少额外的复杂部件和连接点。
简洁的结构有利于提高模具的制造和维护效率,并降低生产成本。
2.2 刚性和稳定性模具结构应设计成具有足够的刚性和稳定性,能够承受生产过程中的各种力和压力。
刚性和稳定性的不足会导致模具在生产过程中产生变形或破损,影响产品质量。
2.3 分模和脱模方便性模具结构应设计成易于分模和脱模的形式,以提高生产效率和降低脱模过程中的损耗。
合理的分模和脱模方式可以减少模具的损坏风险。
2.4 可靠性和耐久性模具结构应设计成可靠和耐久的形式,能够经受长时间高强度的生产使用。
可靠和耐久的模具结构可以减少维护和更换的频率,提高生产效率。
2.5 维护和保养便利性模具结构应设计成方便进行维护和保养的形式,以延长模具的使用寿命并降低维护成本。
塑胶模具设计的十大步骤

塑胶模具设计的十大步骤一、接受任务书成型塑料制件的任务书通常由制件设计者提出,其内容如下:1. 经过审签的正规制制件图纸,并注明采用塑料的牌号、透明度等。
2. 塑料制件说明书或技术要求。
3. 生产产量。
4. 塑料制件样品。
通常模具设计任务书由塑料制件工艺员根据成型塑料制件的任务书提出,模具设计人员以成型塑料制件任务书、模具设计任务书为依据来设计模具。
回复“模具”,查看更多二、收集、分析、消化原始资料收集整理有关制件设计、成型工艺、成型设备、机械加工及特殊加工资料,以备设计模具时使用。
1. 消化塑料制件图,了解制件的用途,分析塑料制件的工艺性,尺寸精度等技术要求。
例如塑料制件在外表形状、颜色透明度、使用性能方面的要求是什么,塑件的几何结构、斜度、嵌件等情况是否合理,熔接痕、缩孔等成型缺陷的允许程度,有无涂装、电镀、胶接、钻孔等后加工。
选择塑料制件尺寸精度最高的尺寸进行分析,看看估计成型公差是否低于塑料制件的公差,能否成型出合乎要求的塑料制件来。
此外,还要了解塑料的塑化及成型工艺参数。
2. 消化工艺资料,分析工艺任务书所提出的成型方法、设备型号、材料规格、模具结构类型等要求是否恰当,能否落实。
成型材料应当满足塑料制件的强度要求,具有好的流动性、均匀性和各向同性、热稳定性。
根据塑料制件的用途,成型材料应满足染色、镀金属的条件、装饰性能、必要的弹性和塑性、透明性或者相反的反射性能、胶接性或者焊接性等要求。
3. 确定成型方法——采用直压法、铸压法还是注塑法。
4、选择成型设备根据成型设备的种类来进行模具,因此必须熟知各种成型设备的性能、规格、特点。
例如对于注射机来说,在规格方面应当了解以下内容:注射容量、锁模压力、注射压力、模具安装尺寸、顶出装置及尺寸、喷嘴孔直径及喷嘴球面半径、浇口套定位圈尺寸、模具最大厚度和最小厚度、模板行程等,具体见相关参数。
要初步估计模具外形尺寸,判断模具能否在所选的注射机上安装和使用。
塑料制品的模具设计与生产工艺
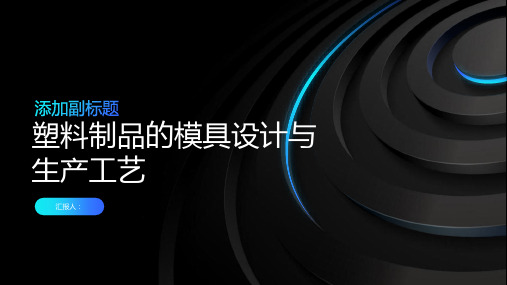
模具调试方法:检查模具闭合状态、调整模具间隙、测试模具成型效果
常见问题及解决方法:模具闭合不严、模具磨损、模具变形等
模具保养与维护:定期清洗模具、涂抹润滑剂、更换磨损部件等
制品质量检测与控制
检测方法:物理、化学、机械性能测试
检测设备:万能试验机、熔融指数仪、冲击试验机等
质量标准:符合相关行业标准和客户要求
智能化设计:利用AI技术进行模具设计,提高设计效率和质量
自动化生产:采用机器人和自动化设备进行模具生产,提高生产效率和精度
智能化监控:利用传感器和物联网技术对模具生产过程进行实时监控,提高生产安全和质量
自动化检测:采用自动化设备对模具进行检测,提高检测效率和准确性
环保与可持续发展要求
回收利用:提高塑料制品的回收利用率,减少环境污染
塑料制品的模具设计与生产工艺
汇报人:
目录
01
添加目录标题
02
塑料制品模具设计
03
塑料制品生产工艺
04
塑料制品模具设计实例分析
05
塑料制品生产工艺实例分析
06
塑料制品模具设计与生产工艺的未来发展
添加章节标题
塑料制品模具设计
设计原则与要求
满足产品性能要求:如尺寸精度、表面质量、力学性能等
考虑模具制造工艺:如模具材料、加工方法、热处理工艺等
模具材料选择:根据塑料制品的材质、形状和尺寸选择合适的模具材料
模具设计:根据塑料制品的尺寸和形状设计模具结构,包括型腔、型芯、冷却系统等
模具制造:采用数控机床、电火花、激光切割等工艺制造模具
塑料制品生产工艺
原材料准备
添加标题
添加标题
添加标题
添加标题
原料的干燥处理:去除原料中的水分和其他挥发性物质,保证制品的质量
塑料模具的设计与成型工艺

塑料模具的设计与成型工艺摘要:塑料成形是一种以人工合成金属树脂材料为基本合成原材料,加入其他一定量化学添加剂,在一定的工作压力、温度下,制成一定形状,并在室温下长久保持形状不变的材料。
塑料是20世纪末期发展壮大起来的一类工业新型材料,包装材料工业、日常用品制造工业,机械工业,医疗器械等工业领域。
医疗器械等领域。
塑料模具产品设计的基本技术要求之一是企业能不断生产研制出能在尺寸,精度,外观及热物理及流体力学性能等各方面条件均能充分满足实际使用性能要求的优质材料塑件。
在进行模具生产使用时,应该要力求模具生产过程效率高,自动化管理程度高,操作方便,寿命长;在应用模具结构制造工艺方面,要求模具结构设计合理,制造容易,成本低。
引言:20世纪70年代以来,石油危机持续爆发虽然使得目前我国大型塑料制品加工制造产业的主要产品原料价格上涨,其宏观经济发展趋势仍然受到很多较大一定程度的宏观经济因素抑制和被经济抑制。
所以,改善塑料的性能、推广和使用先进的模具设计制造技术,研究塑料快速成型技术显得尤为重要。
塑料模具是使塑件成型的主要工具,它可使塑件获得一定的结构形状及所需性能。
其发展受到很大程度的抑制抑制。
所以,改善塑料的性能、推广和使用先进的模具设计制造技术,研究塑料快速成型技术显得尤为重要。
塑料模具是使塑件成型的主要工具,它可使塑件获得一定的结构形状及所需性能。
用特殊模具工艺生产制造出来的的新型塑件产品具有高工艺复杂程度,高质量一致性,高操作精度、高生产率以及低材料消耗率等几大特点。
一、塑料模具简介塑料产品是用各种零件作为材料后再进行加工再成型而得以获得的一种产品。
而腔体模具就是一种利用其本身特定的腔体密闭性和腔体部件去加工成型,从而可以做成一种具有一定整体形状和大小尺寸的大型塑料金属制件的一种工具。
1、用新型机械塑料模具自动加工塑料生产工艺制造加工出来的的新型柔性塑件塑料制品。
它具有高度易操作和低精度、高性能和低一致性、高生产率和低使用材料资源消耗率等几个新的显著特点。
塑料成型工艺与模具设计概述

2. 收缩性
塑料在成型及冷却过程中发生的体积收缩性 质称为收缩性,塑料在熔融状态下的体积总比 其固态下的体积大。
影响塑料收缩性的因素有:塑料的组成及结 构、成型工艺方法、工艺条件、塑件几何形状 及金属镶件的数量、模具结构及浇口形状与尺 寸等。
三、塑料特性与应用 (一)热塑性塑料
热塑性塑料
主要性能
酸性
主要应用
PE聚乙烯
耐化学腐蚀、电绝 缘、吸水性小
小载荷齿轮、容器、轴承、阀件、 涂层、化工管道
PP聚丙烯
密度最小、耐腐蚀、 吸水性小、耐热
PVC聚氯乙烯 PS聚苯乙烯
耐腐蚀、电绝缘、 耐燃
电绝缘、透光、吸 湿低、硬度高、易
燃
ABS丙烯腈-丁 二烯-苯乙烯
(1)热收缩 (2)结构变化引起的收缩 (3)弹性恢复 (4)塑性变形
影响热固性塑料收缩率的原因还有:原材料、 模具结构、成型方法及成型工艺条件等。
2.流动性
热固性塑料的流动 性通常以拉西格流动性 来表示。
影响热固性塑料流 动性的主要因素有: (1)塑料原料 (2)模具及工艺条件的 影响
3.水分及挥发物含量 一是来自生产、运输和储存,二是来自化
安全在于心细,事故出在麻痹。20.10.2020.10.2017: 02:0517:02:05October 20, 2020
踏实肯干,努力奋斗。2020年10月20 日下午5 时2分2 0.10.20 20.10.2 0
追求至善凭技术开拓市场,凭管理增 创效益 ,凭服 务树立 形象。2020年10月20日星期 二下午5时2分5秒17:02:0520.10.20
塑料制品的设计(强行脱模、表面质量)

塑胶制品结构的设计
一.制品结构工艺设计的原则:
1.在保证制品性能和使用要求的情况下,尽量选用价廉、且成型性能好的塑料;
2.力求使制品结构简单,避免侧向凹凸结构,使模具结构简单,易于制造;(内侧凹凸结构有两种情况可不用内行位:碰穿和强行脱模)
•注:关于强行脱模:
1)当侧向凹凸较浅且允许有圆角时,可强行脱模;
2)可强行脱模的塑料有PE、PP、POM和PVC等;
三、制品的表面质量:
1、包括制造质量:型腔省模抛光,一般模具型腔粗糙度为
Ra0.02—1.25um,制品的粗糙度比模具型腔粗糙度低1-2级。
2、注塑质量:水花,蛇纹,熔接痕,顶白变形,黑斑,披锋、
凹痕等。
3、烤柒质量:
4、电镀质量:
5、丝印质量:
6、拉丝质量:
7、抛光质量:
8、汤金质量
9、贴纸质量
10、贴片
四.塑料制品的常见结构设计:
1.脱模斜度:
1).不同塑料的脱模斜度不同,在不影响产品性能的情况下,脱模斜度尽量取较大值;
2).脱模斜度不包括在公差范围之内;
3).晒纹脱模斜度应取较大值,
一般为3°~9°;
4).硬质塑料比软质塑料的脱模斜度大,收缩率大的塑料比收缩率小的脱模斜度大;
5)、制品高度越高,孔越深,为保证精度要求,脱模斜度宜取小一点;
6)、制品形状复杂难脱模时,脱模斜度要大一些;
7)、前模脱模斜度大于后模脱模斜度;
8)、配合精度要求越高,脱模斜度要越小;
9)、壁厚大的制品,脱模斜度可取较大值;机械性能强塑料,自润滑性塑料,脱模斜度可取小一些。
塑料成型工艺与模具设计名词解释

1名词解释1.注射成型:将粒状或粉状塑料从注射机的料斗送入高温的料筒内加热熔融塑化,使其成为粘流态熔体,然后在注射机柱塞或螺杆的高压推动下,以很大的流速通过喷嘴,注入模具型腔,经一定时间的保压冷却定型后,开启模具便可从型腔中脱出具有一定形状和尺寸塑料制件的成型方法,主要用于成型热塑性塑料件2.压缩成型:将粉状、粒状等的热固性塑料原料直接加入敞开的模具加料室内,然后在加热和加压的作用下,使塑料熔融充满型腔,并发生交联固化反应,硬化定型形成塑件,主要用于成型热固性塑料件3.压注成型:压注成型又称传递成型,其成型原理如图所示,先将固态成型物料加入加料腔内,使其受热软化转变为粘流态,并在压力机柱塞压力作用下,经过浇注系统充满型腔,塑料在型腔内继续受热受压,产生交联反应而固化定型4.挤出成型:挤出成型是将颗粒状塑料加入挤出机料筒内,经外部加热和料筒内螺杆机械作用而熔融成粘流态,并借助螺杆的旋转推进力使熔料通过机头里具有一定形状的孔道(口模),成为截面与口模形状相仿的连续体,经冷却凝固则得连续的塑料型材制品。
5.中空吹塑成型:将挤出或注射出来的熔融状态的管状坯料置于模具型腔内,借助压缩空气使管坯膨胀贴紧于模具型腔壁上,冷硬后获得中空塑件,这种成型方法称中空吹塑成型。
6.塑料:以高分子合成树脂为主要成份、在一定温度和压力下具有塑性和流动性,可被塑制成一定形状,且在一定条件下保持形状不变的材料。
7.热塑性塑料:具有线型分子链成支架型结构加热变软,冷却固化可逆的塑料。
8.热固性塑料:具有网状分子链结构加热软化,固化后不可逆。
9.塑化压力(背压)指螺杆式注射成型时,螺杆头部熔体在螺杆转动后退时所受到的阻力。
(背压一般不大于2MPa )10.注射压力:注射压力是指柱塞或螺杆顶部对塑料熔体所施加的压力。
11.保压压力型腔充满后,注射压力的作用在于对模内熔体的压实,此时的注射压力也可称为保压压力。
12.型腔压力型腔压力是注射压力在经过注射机喷嘴、模具的流道、浇口等的压力损失后,作用在型腔单位面积上的压力。
- 1、下载文档前请自行甄别文档内容的完整性,平台不提供额外的编辑、内容补充、找答案等附加服务。
- 2、"仅部分预览"的文档,不可在线预览部分如存在完整性等问题,可反馈申请退款(可完整预览的文档不适用该条件!)。
- 3、如文档侵犯您的权益,请联系客服反馈,我们会尽快为您处理(人工客服工作时间:9:00-18:30)。
2.4.1 脱模斜度
为便于塑件从模腔中脱出,在平行于 脱模方向的塑件表面上,必须设有一定的 斜度,此斜度称为脱模斜度。
斜度留取方向,对于塑件内表面是以小 端为基准(即保证径向基本尺寸),斜度向 扩大方向取,塑件外表面则应以大端为基 准(保证径向基本尺寸),斜度向缩小方向 取,如图2-6所示。
图2—6 塑件上斜度留取方向
塑件壁厚不均匀时,成型中各部分所需
冷却时间不同,收缩率也不同,容易造成塑件
的内应力和翘曲变形,因此设计塑件时应尽可
能减小各部分的壁厚差别,一般情况下应使壁
以成型侧孔和凸凹结构为例。比较两种 方案,从而选择优良的设计方案。
2.3 塑件形状设计
图2-1a所示塑件在取出模 具前,必须先由抽芯机构 抽出侧型芯,然后才能, 取出模具结构复杂。
图2-1b侧孔形式,无需侧 向型芯,模具结构简单。
图2-2a所示塑件的内侧有 凸起,需采用由侧向抽芯 机构驱动的组合式型芯, 模具制造困难。
2.2 尺寸精度与表面质量
影响塑件尺寸精度的因素: 1、模具制造的精度,约为1/3。 2、成型时工艺条件的变化,约为1/3。 3、模具磨损及收缩率的波动。 具体来说,对于小尺寸制品,模具制造 误差对尺寸精度影响最大;而大尺寸制品 则收缩波动为主要。
2.2 尺寸精度与表面质量
2.2.2 尺寸精度的确定
当塑件的内外侧凹陷较浅,同时成型塑件 的塑料为聚乙烯、聚丙烯、聚甲醛这类仍带 有足够弹性的塑料时,模具可采取强制脱模。
为使强制脱模时的脱模阻力不要过大引起 塑件损坏和变形,塑件侧凹深度必须在要求 的合理范围内,见图2—5下面的说明(公式), 同时还要重视将凹凸起伏处设计为圆角或斜 面过渡结构。
2.3 塑件形状设计
第2章 塑料制件的设计
2.1 塑件设计原则 2.2 尺寸精度与表面质量 2.3 塑件形状设计 2.4 塑件结构设计 2.5 嵌件、塑料螺纹等本章主要讲述塑件形状设计要求和设计
实例;脱模斜度的确定;塑件壁厚的设计 及壁厚均匀性;塑件的支承面、塑件上的 孔、嵌件、文字、凸凹纹的设计;塑件结 构设计示例;塑件的尺寸精度和表面粗糙 度的确定。
图2—5 可强制脱模的浅侧凹结构
a)(A-B)×100%/B≤5% b) (A-B)×100%/C≤5%
2.4 塑件结构设计
2.4.1 脱模斜度设计 2.4.2 塑件壁厚设计 2.4.3 设置加强筋 2.4.4 增加刚性减少变形的其他措施 2.4.5 塑件支承面的设计 2.4.6 塑件圆角的设计 2.4.7 塑件孔的设计 2.4.8 采用型芯拼合复杂型孔
设计塑件时如果未注明斜度,模具设计时 必须考虑脱模斜度。模具上脱模斜度留取方向是:
型芯是以小端为基准,向扩大方向取。 型腔是以大端为基准,向缩小方向取。
这样规定斜度方向有利于型芯和型腔径向尺寸修整。斜度 大小应在塑件径向尺寸公差范围内选取。当塑件尺寸精度与 脱模斜度无关时,应尽量地选取较大的脱模斜度。当塑件尺 寸精度要求严格时,可以在其尺寸公差范围内确定较为适当 的脱模斜度。
塑件内表面的脱模斜度应大于其外表面的脱模斜 度。
开模脱出塑件时,希望塑件留在有脱模装置
的模具一侧。要求塑件留在型芯上,则该塑件 内表面脱模斜度应比其外表面小。反之,若要 求塑件留在型腔内,则其外表面的脱模斜度应小于其 内表面的脱模斜度。 塑件上脱模斜度可以用线性尺寸、角度、比例等三 种方式来标注,如图2-7所示。 脱模斜度的推荐值可供设计塑件时参考。
②透明制品型腔和型芯粗糙度一致。 ③非透明制品的隐蔽面可取较大粗糙度, 即型芯表面相对型腔表面略为粗糙。
2.3 塑件形状设计
2.3.1 侧凹与侧凸
设计塑件的内外表面形状要尽量避免侧 凹结构,以避免模具采用侧向分型和侧向抽 芯机构,否则因设置这些机构而使模具结构 复杂.不但模具的制造成本提高,而且还会在 塑件上留下分型面线痕,增加了去除飞边的 后加工的困难。
表3—2是模塑件尺寸公差国家标准(GB/T 14486-1993),表3—3是常用塑料材料的 公差等级选用。
将表3—2和表3—3结合起来使用,先查表 3—3,根据模塑件的材料品种及用要求选定塑 件的尺寸精度等级,再从表3—2中查取塑件尺 寸公差。然后根据需要进行上、下偏差分配。 如基孔制的孔可取表中数值冠以(+)号,如基 轴制的轴可取表中数值冠以(-)号,其余情况则 根据材料特性和配合性质进行分配。
塑件设计原则:
⑴满足使用要求和外观要求 ⑵针对不同物理性能扬长避短 ⑶便于成型加工 ⑷尽量简化模具结构
2.2 尺寸精度与表面质量 2.2.1 尺寸精度 2.2.2 尺寸精度的确定 2.2.3 表面质量
2.2 尺寸精度与表面质量
2.2.1 尺寸精度
1、塑件尺寸概念 塑件尺寸——塑件的总体尺寸。
2、塑料制品总体尺寸受限制的主要因素: *塑料的流动性 *成型设备的能力
图2-2b避免了组合式型芯, 模具结构简单。
a
b
图2-1具有侧孔的塑件
a
b
图2-2塑件内侧表面形状改进
2.3 形状和结构设计
图2-3、2-4的图a形式需要侧抽芯,图b形式不需侧型 芯。
a
b
图2-3取消塑件上不必 要的侧凹结构
a
b
图2-4无需采用侧向抽 芯结构成型的孔结构
2.3 形状和结构设计
2.3.2 强制脱模
图2—7 脱模斜度的标注
返回
2.4.2 壁厚及壁厚均匀性
在满足工作要求和工艺要求的前提下,塑件壁 厚设计应遵循如下两项基本原则:
尽量减小壁厚;减小壁厚不仅可以节约材料,
节约能源,也可以缩短成型周期,也有利于获 得质量较优的塑件。塑件允许的最小壁厚与塑 料品种和塑件尺寸有关。
尽可能保持壁厚均匀。
2.2 尺寸精度与表面质量
2.2.3 表面质量
1、塑件制品的表面质量要求: ①表面粗糙度要求。
②表面光泽性、色彩均匀性要求。 ③云纹、冷疤、表面缩陷程度要求。 ④熔结痕、毛刺、拼接缝及推杆痕迹等缺陷 的要求。
2.2 尺寸精度与表面质量
2.2.3 表面质量
2、模具表面粗糙度要求
①一般,型腔表面粗糙度要求达0.20.4mm,模具表面粗糙度要比塑件的要求低 1~2级。