拐臂工艺设计说明书
杠杆工艺设计说明书
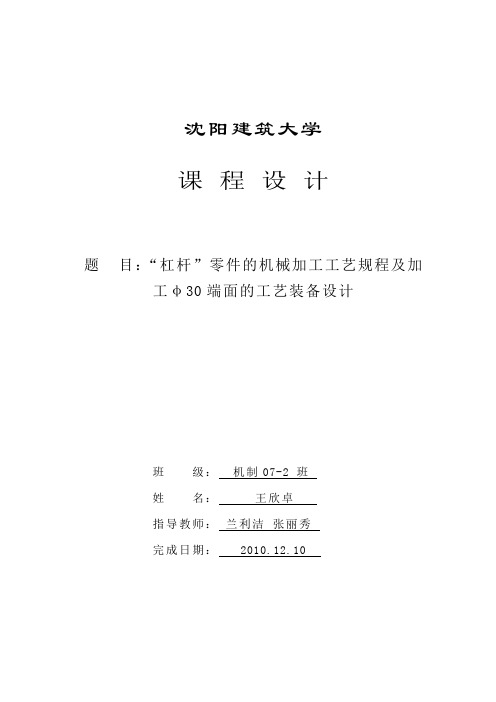
沈阳建筑大学课程设计题目:“杠杆”零件的机械加工工艺规程及加工φ30端面的工艺装备设计班级:机制07-2 班姓名:王欣卓指导教师:兰利洁张丽秀完成日期:2010.12.10辽宁工程技术大学课程设计I 一、设计题目“杠杆”零件的机械加工工艺规程及加工φ30端面的工艺装备设计二、设计要求设计的要求包括如下几个部分:1.绘制零件图1张2. 绘制夹具装配图(A0或A1) 1张3. 绘制夹具零件图1张4.编写课程设计说明书(约5000字)。
1份说明书主要包括以下内容(章节)(1).目录(3).零件工艺性分析(4).机械加工工艺规程设计(5).指定工序的专用机床夹具设计(6).方案综合评价与结论(7).体会与展望(8).参考文献列出参考文献(包括书、期刊、报告等)三、上交材料1.零件图1张2.夹具装配图1张3.夹具零件图1张4.设计说明书1份四、进度安排1.第l~2天查资料,熟悉题目阶段。
2.第3~5天,完成零件的工艺性分析,确定毛坯的类型、制造方法和机械加工工艺规程的设计并编制出零件的机械加工工艺卡片。
3.第5~10天,完成夹具总体方案设计(画出草图,与指导教师沟通,在其同意的前提下,进行课程设计的下一步),完成夹具总装图的绘制,零件图的绘制,整理并完成设计说明书的编写。
4.第11天,完成图纸和说明书的输出打印。
5.第12天,答辩五、指导教师评语成绩:指导教师日期摘要设计内容:“杠杆”零件的机械加工工艺规程及加工φ30端面工艺装备设计,并绘制出调速杠杆零件图、毛坯图、夹具零件图和夹具装配图,填写工艺卡片,编制课程设计说明书。
设计目的:通过该课程设计,使我把自己所学理论与生产实践很好地相结合,锻炼了我分析问题、解决问题的能力,在这个过程中我独立分析和解决了零件机械制造的工艺问题,设计了机床专用夹具这一典型的工艺装备,提高了结构设计能力,为今后的毕业设计及对自己未来将从事的工作进行了一次适应性训练,从而打下了良好的基础。
摇臂加工工艺规程及夹具设计
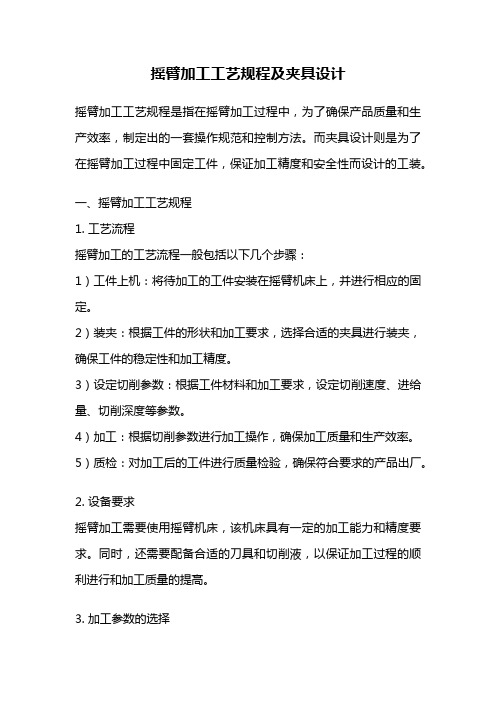
摇臂加工工艺规程及夹具设计摇臂加工工艺规程是指在摇臂加工过程中,为了确保产品质量和生产效率,制定出的一套操作规范和控制方法。
而夹具设计则是为了在摇臂加工过程中固定工件,保证加工精度和安全性而设计的工装。
一、摇臂加工工艺规程1. 工艺流程摇臂加工的工艺流程一般包括以下几个步骤:1)工件上机:将待加工的工件安装在摇臂机床上,并进行相应的固定。
2)装夹:根据工件的形状和加工要求,选择合适的夹具进行装夹,确保工件的稳定性和加工精度。
3)设定切削参数:根据工件材料和加工要求,设定切削速度、进给量、切削深度等参数。
4)加工:根据切削参数进行加工操作,确保加工质量和生产效率。
5)质检:对加工后的工件进行质量检验,确保符合要求的产品出厂。
2. 设备要求摇臂加工需要使用摇臂机床,该机床具有一定的加工能力和精度要求。
同时,还需要配备合适的刀具和切削液,以保证加工过程的顺利进行和加工质量的提高。
3. 加工参数的选择在摇臂加工中,选择合适的加工参数对于保证加工质量和提高生产效率至关重要。
加工参数包括切削速度、进给量、切削深度等。
不同的工件材料和形状需要选择不同的加工参数。
4. 质量控制摇臂加工过程中,需要进行质量控制,确保产品的加工精度和一致性。
质量控制包括加工过程中的监控和检验,以及对产品的最终质量进行评估和验证。
二、夹具设计1. 夹具的作用夹具在摇臂加工中起到固定工件的作用,保证加工过程中工件的稳定性和加工精度。
夹具设计的好坏直接影响到加工质量和生产效率。
2. 夹具的选择夹具的选择要根据工件的形状和加工要求来确定。
一般情况下,夹具应具备以下几个特点:1)稳定性:夹具要能够牢固地固定工件,确保加工过程中不发生移动或变形。
2)刚性:夹具要具备足够的刚性,以承受加工过程中的切削力和振动。
3)精度:夹具的设计要考虑到加工精度的要求,确保夹持工件的位置和角度精确。
4)易于操作:夹具设计要尽量简洁实用,便于操作和调整。
3. 夹具的设计原则夹具的设计应遵循以下原则:1)合理布局:夹具的各部件应布局合理,便于操作和调整。
毕业设计大型液压装载机动臂锻造工艺及模具设计说明书

大型液压装载机动臂锻造工艺及模具设计说明书摘要本次项目主要是通过铸改锻以及尝试通过修改锻造工艺和模具设计的方式来使动臂的性能加强,进而能够达到降低成本的同时延长工件寿命的目的。
由于铸造方式容易产生缩孔与与疏松,而锻造则会使坯料反复压制,让纤维连续,坯料中的疏松处压合,提高金属的致密度,细化金属晶粒,因此强度大于铸件。
设计过程中,锻件图和设备吨位已知,因此主要目的是将铸改锻后的锻造工艺和锻模设计成功运用于锻件的生产当中去,并且使生产出来的锻件满足力学性能的要求。
在这一过程中包括飞边槽形式和尺寸、制坯工步、切边模等都需要反复地设计修改,最终达到理论上的要求。
主要设计步骤有:分析锻件图;计算主要参数;确定设备吨位;确定毛边槽形式和尺寸;绘制计算毛坯图;选择制坯工步;确定坯料尺寸;制坯型槽设计;锻模型槽设计;绘制锻模图等。
通过此次铸改锻的生产方式转变,认识到锻造工艺的发展空间,为进一步提高生产效率提供了机会,也开阔了我们的视野。
关键词:动臂,锻造,模具设计,主要参数,绘制LARGE HYDRAULIC LOADER ARM FORGING TECHNOLOGY AND DIEDESIGN SPECIFICATIONABSTRACTThis project is mainly through casting and forging and attempts to modifytheproperties of forging process and die design way to boom to strengthen,and can reduce the cost and to prolong the life of the workpiece.Because thecasting prone to shrinkage and osteoporosis, while forging will make the blankrepeatedly pressing, let loose in continuous fiber, blank pressing,increase thedensity of metal, metal grain refinement, so the strength is higher than that ofcastings.In the process of design, forging drawings and equipment tonnage isknown, so the main objective is the forging process and die design of castingforging aftersuccessfully applied in forging production, and the production offorgings meet the requirements of mechanical properties. In this process,including the flash groove forms and sizes, making blank step, trimming die need to repeatedlymodify the design, finally achieve the theoretical requirements.The main design steps are: analysis of forging drawing; main parameters;determine the equipment tonnage; determine the groove forms and sizes;drawing blank map; selection of billet step; Determination of blank size; design of blank making groove; forging die groove design drawing die drawings.The casting and forging of the transformation of the mode of production, realizethe development space of forging technology, provides the opportunity to furtherimprove the production efficiency, but also broaden our view.KEY WORDS:The boom,Forging,Mold design,The main parameters,Draw目录前言第1章模锻件图设计§1.1 绘制锻件图的过程§1.1.1 确定分模的位置§1.1.2 锻件的质量§1.1.3 锻件的复杂系数§1.1.4 确定余块加工余量和公差§1.1.5 模锻斜度§1.1.6 圆角半径§1.1.7 技术条件§1.2 锻件的主要参数§1.2.1 锻件的周边长度§1.2.2 锻件的质量§1.2.3 锻件的体积第2章确定锻锤吨位第3章确定毛边槽形式和尺寸第4章热锻件设计第5章绘制计算毛坯图§5.1 计算毛坯图的用途§5.1.1 锻件选择坯料工步的依据§5.1.2 确定坯料尺寸的依据§5.1.3 设计制坯模腔的依据第6章制坯工步选择第7章确定坯料尺寸第8章制坯型槽设计§8.1 滚挤型槽设计的选用§8.2 弯曲型槽的设计第9章锻模模膛设计§9.1 预锻模膛设计§9.2 终锻模膛设计§9.2.1 终锻模膛的壁厚第10章锻模结构设计§10.1 检验角、燕尾和键槽尺寸的确定§10.2 模块尺寸第11章模具参数校核第12章模锻工艺流程第13章锻前加热、锻后冷却及热处理要求§13.1 确定加热方式及锻造温度范围§13.2 确定加热时间§13.3 确定冷却方式及规范§13.4 确定锻后热处理方式及要求参考文献前言随着我国现代化建设进程的不断推进,工程机械行业的发展得到极大的促进,市场对工程机械的结构提出了越来越高的要求,不仅要求有较高的承载能力,高的疲劳寿命,还要求减少原材料的使用,降低生产成本。
零件工艺设计说明书范文

零件工艺设计说明书范文
一、零件简介
该零件为一个典型的车削零件,用于汽车制造行业。
零件材料为高碳钢,具有良好的强度和耐磨性。
二、工艺流程设计
1.毛坯准备:选用高碳钢作为毛坯材料,并进行热处理以
提高其机械性能。
2.粗加工:去除毛坯大部分余量,为后续精加工提供基础。
3.精加工:对零件进行精细加工,确保尺寸精度和表面质
量。
4.热处理:对零件进行淬火和回火处理,以提高其硬度和
耐磨性。
5.检测:对零件进行检测,确保其符合设计要求。
三、工艺参数选择
1.切削速度:根据零件材料和加工要求,选择合适的切削
速度。
2.进给量:根据零件尺寸和表面质量要求,选择合适的进
给量。
3.切削深度:根据毛坯余量和加工要求,选择合适的切削
深度。
四、工艺装备设计
1.刀具:选用硬质合金刀具,以提高切削效率和刀具寿命。
2.机床:选用数控机床进行加工,以提高加工精度和生产
效率。
3.工装:设计专用工装,以固定零件并确保加工稳定性。
五、质量控制与安全
1.严格控制切削参数和刀具使用,避免超负荷切削和刀具
破损。
2.加强机床维护和保养,确保设备正常运行。
3.遵守安全操作规程,佩戴防护用品,确保生产安全。
转向臂机械加工工艺规程设计

机械加工工艺规程设计一、生产类型的确定由原始资料可知是中批量生产类型。
二、零件的分析1、零件的作用据资料所示,该转向臂的作用和方向盘、转向拉杆一起配合使用,从而达到控制转向轮的转向角度。
2、零件的工艺分析由零件图可知:φ16、φ9.3的孔中心线是主要的设计基准和加工基准。
该零件的主要加工面可分为两组:2·1、以φ16mm孔的中心线加工表面这一组加工表面包括:铣φ26mm单侧端面、钻φ16mm的孔、倒角1×45°、钻φ8.5mm的孔。
2·2、以φ9.3mm孔的中心线加工表面这一组加工表面包括:铣φ20mm两端面、钻φ9.3mm的孔、锪φ16mm的沉头。
概括:由于φ16、φ9.3的孔中心线位置精度不高,又φ16mm 内孔的精度比φ9.3mm内孔的精度较高。
所以由以上分析可知,对这两组加工表面而言,先加工第一组,再加工第二组。
由参考文献中有关面和孔加工精度及机床所能达到的位置精度可知,上述技术要求是可以达到的,零件的结构工艺性也是可行的。
三、选择毛坯、确定毛坯尺寸、设计毛坯图根据零件材料确定毛坯为可锻铸铁(KT35-10),中批量生产。
按《机械制造技术基础课程设计指南》第五章第一节可确定:1、求最大轮廓尺寸长133.6mm、宽47mm、高46mm故最大轮廓尺寸为133.6mm。
2、选取公差等级CT由表5-1,铸造方法按机械造型、铸件材料按可锻铸铁,得CT范围8~12级。
取为10级。
3、求铸件尺寸公差根据加工表面的基本尺寸和逐渐公差等级CT=10级,查表5-3得:公差带相对于基本尺寸对称分布。
4、求机械加工余量等级查表5-5,得机械加工余量等级范围为E~G,取为F级。
5、求RMA(要求的机械加工余量)对所有加工表面取同一个数值,由表5-4查最大轮廓尺寸为133.6mm,机械加工余量等级为F级,得RMA数值为1.5mm。
6、求毛坯基本尺寸依零件图可知:Φ16、φ9.3、φ8.5孔径较小,铸成实心。
转向臂机械加工工艺规程及专用夹具设计

转向臂机械加工工艺规程及专用夹具设计The document was finally revised on 2021目录一、生产类型的确定 (1)二、零件的分析 (1)1、零件的作用 (2)2、零件的工艺分析 (2)2.1、以φ16mm孔的中心线加工表面 (2)2.2、以φ9.3mm孔的中心线加工表面 (2)2.3、转向臂技术零件要求表 (2)三、选择毛坯、确定毛坯尺寸、设计毛坯图 (2)1、求最大轮廓尺寸 (3)2、选取公差等级CT (3)3、求铸件尺寸公差 (3)4、求机械加工余量等级 (3)5、求RMA(要求的机械加工余量) (3)6、求毛坯基本尺寸 (3)7、画毛坯图(见A3图纸) (4)四、工艺路线拟定 (4)1、定位基准的选择 (4)2、拟定加工方法和加工方案 (4)2.1、工艺路线: (4)五、选择加工设备及刀具、量具 (5)1、选择加工设备与工艺设备 (5)1.1、选择机床,根据不同的工序选择机床 (5)1.2、选择刀具,根据不同的工序选择刀具 (5)1.3选择量具 (5)2、确定工序尺寸 (7)2.1、面的加工(所有面) (7)2.2、孔的加工 (7)六、确定切削用量及基本时间 (7)工序号04: (7)七、夹具设计 (11)7.1 夹具设计的基本要求和步骤................... 错误!未定义书签。
7.1.1 基本要求............................. 错误!未定义书签。
7.1.2 设计步骤............................. 错误!未定义书签。
7.2夹具设计.................................... 错误!未定义书签。
........................................... 错误!未定义书签。
........................................... 错误!未定义书签。
通用机械臂设计说明书
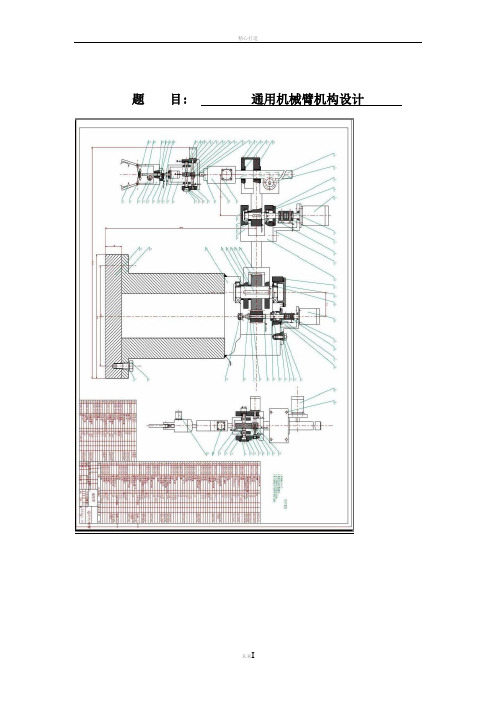
题目: 通用机械臂机构设计目录1.绪论 (1)1.1 选题背景 (1)1.2 国内外研究现状和趋势 (1)1.3机械臂的组成 (2)1.4 设计目的 (3)1.5研究内容 (4)2.机械臂的总体设计方案 (4)2.1 机械臂总体结构的类型 (4)2.2机械臂主要部件及其运动 (5)2.3驱动机构选择 (6)2.4机械臂技术参数 (6)3.机械臂手部计算 (7)3.1手部设计基本要求 (7)3.2典型手部结构 (7)3.3机械臂手爪的设计计算 (7)4.腕部的设计计算 (12)4.1腕部设计基本要求 (12)4.2腕部结构 (13)4.3腕部的设计计算 (13)5.臂部设计以及有关计算 (17)5.1臂部设计的基本要求 (18)5.2手臂的典型机构及其选择 (19)6机座设计 (24)结论 (24)参考文献 (25)1.绪论1.1 选题背景机械臂是在自动化生产过程中使用的一种具有抓取和移动工件功能的自动化装置,它是在机械化、自动化生产过程中发展起来的一种新型装置。
近年来,随着电子技术特别是电子计算机的广泛应用,机器人的研制和生产已成为高技术领域内迅速发展起来的一门新兴技术,它更加促进了机械臂的发展,使得机械臂能更好地实现与机械化和自动化的有机结合。
机械臂能代替人类完成危险、重复枯燥的工作,减轻人类劳动强度,提高劳动生产力。
机械臂越来越广泛的得到了应用,在机械行业中它可用于零部件组装,加工工件的搬运、装卸,特别是在自动化数控机床、组合机床上使用更普遍。
目前,机械臂已发展成为柔性制造系统FMS 和柔性制造单元FMC中一个重要组成部分。
把机床设备和机械臂共同构成一个柔性加工系统或柔性制造单元,它适应于中、小批量生产,可以节省庞大的工件输送装置,结构紧凑,而且适应性很强。
当工件变更时,柔性生产系统很容易改变,有利于企业不断更新适销对路的品种,提高产品质量,更好地适应市场竞争的需要。
而目前我国的工业机器人技术及其工程应用的水平和国外比还有一定的距离,应用规模和产业化水平低,机械臂的研究和开发直接影响到我国自动化生产水平的提高,从经济上、技术上考虑都是十分必要的。
转向臂机械加工工艺规程及专用夹具设计

目录1577一、零件生产类型的确定由原始资料可知:年产量Q=5000台/年零件数量n=1件/台备品率α=3%废品率β=%N=Qn(1+α)(1+β)=5000*1*(1+3%)(1+%)=5176件/年所以是大批量生产。
二、零件的分析1、零件的作用据资料所示,该转向臂的作用和方向盘、转向拉杆一起配合使用,从而达到控制转向轮的转向角度。
2、零件的工艺分析由零件图可知:φ16、φ的孔中心线是主要的设计基准和加工基准。
该零件的主要加工面可分为两组:2.1、以φ16mm孔的中心线加工表面这一组加工表面包括:铣φ26mm单侧端面、钻φ16mm的孔、倒角1×45°、钻φ的孔。
2.2、以φ孔的中心线加工表面这一组加工表面包括:铣φ20mm两端面、钻φ的孔、锪φ16mm的头。
概括:由于φ16、φ的孔中心线位置精度不高,又φ16mm内孔的精度比φ内孔的精度较高。
所以由以上分析可知,对这两组加工表面而言,先加工第一组,再加工第二组。
由参考文献中有关面和孔加工精度及机床所能达到的位置精度可知,上述技术要求是可以达到的,零件的结构工艺性也是可行的。
、转向臂技术零件要求表三、选择毛坯、确定毛坯尺寸、设计毛坯图根据零件材料确定毛坯为可锻铸铁(KT35-10),大批量生产。
按《机械制造技术基础课程设计指南》第五章第一节可确定:1、求最大轮廓尺寸长、宽、高,故最大轮廓尺寸为。
2、选取公差等级CT由<课程设计指导教程>P27表2-1,铸造方法按机械造型、铸件材料按铸铁,得CT范围8~12级。
取为10级。
3、求铸件尺寸公差根据加工表面的基本尺寸和逐渐公差等级CT=10级,查表2-3得:公差带相对于基本尺寸对称分布。
4、求机械加工余量等级查表2-5,得机械加工余量等级范围为E~G,取为F级。
5、求RMA(要求的机械加工余量)对所有加工表面取同一个数值,由表2-4查最大轮廓尺寸为,机械加工余量等级为F级,得RMA数值为。
- 1、下载文档前请自行甄别文档内容的完整性,平台不提供额外的编辑、内容补充、找答案等附加服务。
- 2、"仅部分预览"的文档,不可在线预览部分如存在完整性等问题,可反馈申请退款(可完整预览的文档不适用该条件!)。
- 3、如文档侵犯您的权益,请联系客服反馈,我们会尽快为您处理(人工客服工作时间:9:00-18:30)。
毕业设计说明书 专 业: ____________________ 班 级: ____________________ 姓 名: ____________________ 学 号: ____________________ 指导老师: ____________________
陕西国防工业职业技术学院 目 录 第一部分 工艺设计说明书………………………………………………………………………… ………… 第二部分 第40号工序夹具设计说明书………………………………………………………… ………… 第三部分 第30和40号工序量具设计说明书………………………………………………… ………… 第五部分 第50号工序数控编程设计说明书…………………………………………………… ………… 第六部分 毕业设计体会…………………………………………………………………………… ………… 第七部分 参考资料………………………………………………………………………………… 第一部分 工艺设计说明书 1.零件图工艺性分析 1.1零件结构功用分析 从标题栏可知:该零件的名称为拐臂。拐臂:是机器设备上常用的部件之一。通过螺钉与其它部件连接以实现连带运动等功能。其材料为HT200,属于轮廓类零件。零件的结构分析就是从设计要求和工艺要求出发,分析零件不同结构的功用。 1、从设计要求方面看,零件在机器中,可以起到支撑、容纳、传动、配合、连接、安装和定位等功用,这是决定零件主要结构的依据。 2、从工艺要求方面看,为了使零件的毛坯制造、加工、测量以及装配和调整工作能顺利、方便,应设计出圆角、起模斜度、倒角等结构,这是决定零件局部结构的依据。 3、从实用和美观方面看,不仅要求产品能使用,而且还要求经济、美观等,要从美学的角度来考虑结构形状。 1.2零件技术条件分析 分析技术要求包括五个方面。A. 加工表面的尺寸精度;B.主要加工表面的形状精度;C.主要加工表面的相互位置精度;D.加工表面的粗糙度和机械物理性能; E.热处理及其它要求。 分析零件技术要求的目的归结为一点,是保证零件使用性能前提下的经济合理性。在工程实际中要结合现有生产条件分析实现这些技术要求的可行性。分析零件图还包括图纸的尺寸、公差和表面粗糙度标准是否齐全。通过对零件形状和主要表面的了解之后,就可以基本形成零件工艺流程. 1.3零件结构工艺性分析 由零件图可知该零件图由圆弧、孔、直线等几何元素组成,各元素之间关系描述清楚、尺寸标注完整。基本内容有: 1.相同圆心主轴直径为80mm外圆以及直径为50mm的通孔,要求表面粗糙度为3.2,且保证外圆的高为45mm。 2.要求以直径为80mm外圆圆心为中心,夹角为 120度,长度为100mm点作为圆心距。要求连杆两外轮廓半径为r25,且以相同的圆心加工直径为25mm的通孔,其孔表面粗糙度要求为3.2,高度为15mm,且两连杆圆弧连接处圆弧半径为r25 3.注:要求加工前划线找正确定该零件的中心,保证外圆高度为45mm以及连杆高度为15mm,外圆直径为80mm上下表面粗糙度为3.2,其余表面粗糙度要求为6.3 4.技术要求:铸件不允许有裂纹,缩孔等缺陷,加工后的零件不允许有毛刺 5.零件材料为HT200 材料分析: 材料名称:灰铸铁 牌号:HT200 标准:GB9439-88 最低抗拉强度为200MPa的灰铸铁 铸铁级别 较高强度铸铁,基体为珠光体,强度,耐磨性,耐热性均好,减振性也良好,铸造性能较好,需要进行人工时效处理。
2.毛坯选择 2.1毛坯类型 毛坯种类的选择不仅影响毛坯的制造工艺及费用,而且也与零件的机械加工工艺和加工质量密切相关。正确选择合适的毛坯,对零件的加工质量.材料消耗和加工工时都有很大的影响。如果当毛坯的尺寸与零件图尺寸相近时,则就提高了工作效率,但是毛坯制造的成本就越高,所以选择合适的毛坯需要毛坯制造和机械加工两方面的工艺人员密切配合,合理地确定毛坯的种类、结构形状,并绘出毛坯图。 毛胚的选择: 1. 毛胚种类的选择:毛胚可分为a铸件:主要用于形状复杂或尺寸较大的毛胚;b锻件:主要用于加工余量小,精度高,性能好的毛胚;c型材:型材分为热轧和冷轧。热轧型材尺寸较大,精度低,多用于一般零件的毛胚尺寸较;冷热型材小,精度较高,多用于精度要求高的中小型零件;d焊接件:通过焊,电焊,气氩弧焊等焊接方式制造毛胚,主要用于大型零件的单间小批生产中; 2. 毛胚选择须应考虑的因素:a零件的材料及力学性能;b零件的结构形状及外形尺寸;c生产纲领;d:生产条件;e积极推广新工艺,新技术和新材料; 根据零件图的结构形状及外形尺寸分析,该零件外形结构多为轮廓,不易与加工方便且零件的材料为HT200,生产批量为小批量。综合1(a)2(a)故选用铸件为该零件的毛胚类型。 3. 选择设备: 根据零件图分析可得:该零件属于轮廓类零件,外形结构复杂且不适于一次完成该工序所有工步,所以故选用复合型数控加工中心 加工中心的特点:综合加工能力较强,工件一次装夹后能完成较多的加工内容,加工精度较高,就中等加工难度的批量工件,其效率是普通设备的5~10倍,特别是它能完成许多普通设备不能完成的加工,对形状较复杂,精度要求高的单件加工或中小批量多品种生产更为适用。 在加工中心上加工零件的特点是:被加工零件经过一次装夹后,数控系统能控制机床按不同的工序自动选择和更换刀具;自动改变机床主轴转速、进给量和刀具相对工件的运动轨迹及其它辅助功能,连续地对工件各加工面自动地进行钻孔、锪孔、铰孔、镗孔、攻螺纹、铣削等多工序加工。由于加工中心能集中地、自动地完成多种工序,避免了人为的操作误差、减少了工件装夹、测量和机床的调整时间及工件周转、搬运和存放时间,大大提高了加工效率和加工精度,所以具有良好的经济效益 2.2毛坯余量确定 加工余量是指加工过程中所切去的金属层厚度。余量有总加工余量和工序余量之分。金属层。工序余量是相邻两工序的工序尺寸之差,毛坯余量是毛坯尺寸与零件图样的设计尺寸之差。 由于工序尺寸有公差,故实际切除的余量大小不等。余量的确定有三种(1)经验估算法。(2)查表修正法。(3)分析计算法。 该零件要求表面粗糙度为3.2,尺寸要求较严格而且公差范围较小,故余量选择较为谨慎,根据公式确定铸件毛坯时余量为单边2mm,由机械手册查得:铸件单边余量为2mm不能达到尺寸要求,由计算得单边余量应大于等于为4mm,所以选择4mm即可.需粗加工和精加工来完成。所以本图采用查表修正法。 2.3毛坯-零件合图草图
3.机加工工艺路线确定 3.1加工方法分析确定 该零件图有圆弧、孔、直线等几何元素组成,各元素之间关系描述清楚、尺寸标注完整,拐臂厚40mm、中心孔为50mm,两边为孔Φ25,且均为通孔,表面粗糙度要求较高、公差要求严格,零件采用工序集中,工序集中就是将零件的加工集中在少数几道工序中完成,每道工序加工内容多,工艺路线短。 根据零件图的分析加工顺序的拟定按照基面先行,先粗后精,先面后孔,先主后次的原则确定,根据零件图和余量的选择,故该图一面两孔的定位原则。 3.2加工顺序的安排(宋体、加黑、小四)
方案一: 1:粗精铣A平面台阶,达到精度技术要求; 2:粗精铣B平面台阶,达到精度技术要求; 3:中心钻钻内孔为直径50的孔,达到精度技术要求; 4:中心钻钻内孔为直径25的孔,达到精度技术要求; 5:扩2*25的孔,以及直径为50的孔; 6::铰2*25的孔; 7:粗精铣外轮廓; 8:钳工去毛刺; 9:检验; 10:入库; 方案二: 1:粗精铣B平面台阶,达到精度技术要求; 2:中心钻钻内孔为直径50的孔,达到精度技术要求; 3: 扩Φ50的孔,达到精度技术要求; 4:粗精铣A平面台阶,达到精度技术要求; 5:中心钻钻内孔为直径25的孔,达到精度技术要求; 6:扩2*25的孔 7: 铰2*25的孔 8:粗精铣外轮廓,达到精度要求; 9:钳工去毛刺; 10:检验; 11:入库; 方案三 : 1:粗,精铣A面,达到精度要求; 2:粗精铣外轮廓,达到精度要求; 3:粗精铣外圆80,达到精度要求; 4:粗精铣孔25A表面,达到精度要求; 5:翻身粗精铣B面,达到精度要求; 6:粗精铣外圆80,达到精度要求; 7:粗精铣孔25B表面,达到精度要求; 8:粗精铣外轮廓,达到精度要求; 9:中心钻钻内孔为直径50的孔,以及2*直径为25的孔; 10:扩2*25的孔,以及直径为50的孔; 11:铰2*25的孔; 12:钳工去毛刺; 13:检验; 14:入库。 以上两种加工方案,根据加工理论的合理性,与一般人的加工零件的习惯等,经过对比方案一比较合理,因为此方案遵循了基面先行,先粗后精,先面后孔的原则,同时也保证了孔的同轴度,故选择第一种方案为加工该零件图的方案。
3.3定位基准选择 一:粗基准选择原则 选择粗基准时应该遵循以下几种要求: (1)以工件中重要表面的加工余量小而均匀,则应选择该表面为粗基准。所谓重要表面一般是工件上加工精度以及表面质量要求较高的表面,如床身的导轨面,车床主轴箱的主轴孔,都是各自的重要表面。因此,加工床身和主轴箱时,应以导轨面或主轴孔为粗基准。