特种加工作业
特种加工特点及应用

特种加工特点及应用特种加工是指对特殊材料、特殊形状的工件进行加工的一种工艺,其主要特点是加工难度大、工艺复杂、技术要求高、加工精度高等。
特种加工通常需要特殊的机械设备和加工工具,以及专门的操作和工艺掌握。
本文将从特种加工的定义、特点和应用领域三个方面进行详细描述。
首先,特种加工的定义是对特殊材料、特殊形状的工件进行加工的一种工艺。
特殊材料可以是高硬度材料如超硬材料、高温材料如钨钼合金等,亦或是具有特殊性能和特殊用途的材料如陶瓷材料、复合材料等。
特殊形状的工件可以是非常复杂的内外形状如齿轮、螺纹、电极等。
特种加工的目的是在保证工件材料性能的同时,满足特殊形状和尺寸的要求。
其次,特种加工的特点主要表现在以下几个方面。
首先,加工难度大。
特种材料具有较高的硬度、韧性以及热传导性能等,对机械设备和加工工具的性能要求较高,加工过程中易产生刀具磨损、工件变形等问题。
其次,工艺复杂。
特种材料及其特殊形状的工件加工需要经过多道工序,其中包括切削、磨削、电火花加工(EDM)、激光加工等多种工艺。
再者,技术要求高。
特种加工需要操作人员具备较高的技术水平和丰富的实际经验,对于加工工艺参数的选择和控制要求精细。
最后,加工精度高。
特种工件通常对尺寸、形状和表面质量等要求较高,因此特种加工需要具备较高的加工精度和加工表面的光洁度。
最后,特种加工在许多领域有着广泛的应用。
首先,在航空航天领域,许多航空发动机零件、航天器外壳等都采用了特种加工技术。
其次,在模具制造领域,由于特种材料具有高硬度、高耐磨性和高抗腐蚀性能,因此特种加工广泛应用于模具的加工和制造。
再者,在医疗器械制造领域,特种加工技术可以用于人工骨、人工关节等医疗器械的加工和制造。
此外,特种加工还在光学器件制造、微电子器件制造、汽车零部件制造等领域得到了广泛的应用。
综上所述,特种加工是一种对特殊材料、特殊形状的工件进行加工的工艺,其具有加工难度大、工艺复杂、技术要求高、加工精度高等特点。
特种加工知识点总结
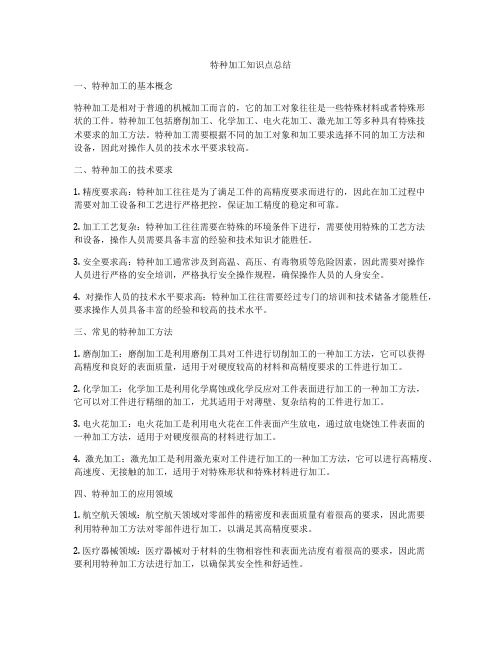
特种加工知识点总结一、特种加工的基本概念特种加工是相对于普通的机械加工而言的,它的加工对象往往是一些特殊材料或者特殊形状的工件。
特种加工包括磨削加工、化学加工、电火花加工、激光加工等多种具有特殊技术要求的加工方法。
特种加工需要根据不同的加工对象和加工要求选择不同的加工方法和设备,因此对操作人员的技术水平要求较高。
二、特种加工的技术要求1. 精度要求高:特种加工往往是为了满足工件的高精度要求而进行的,因此在加工过程中需要对加工设备和工艺进行严格把控,保证加工精度的稳定和可靠。
2. 加工工艺复杂:特种加工往往需要在特殊的环境条件下进行,需要使用特殊的工艺方法和设备,操作人员需要具备丰富的经验和技术知识才能胜任。
3. 安全要求高:特种加工通常涉及到高温、高压、有毒物质等危险因素,因此需要对操作人员进行严格的安全培训,严格执行安全操作规程,确保操作人员的人身安全。
4. 对操作人员的技术水平要求高:特种加工往往需要经过专门的培训和技术储备才能胜任,要求操作人员具备丰富的经验和较高的技术水平。
三、常见的特种加工方法1. 磨削加工:磨削加工是利用磨削工具对工件进行切削加工的一种加工方法,它可以获得高精度和良好的表面质量,适用于对硬度较高的材料和高精度要求的工件进行加工。
2. 化学加工:化学加工是利用化学腐蚀或化学反应对工件表面进行加工的一种加工方法,它可以对工件进行精细的加工,尤其适用于对薄壁、复杂结构的工件进行加工。
3. 电火花加工:电火花加工是利用电火花在工件表面产生放电,通过放电烧蚀工件表面的一种加工方法,适用于对硬度很高的材料进行加工。
4. 激光加工:激光加工是利用激光束对工件进行加工的一种加工方法,它可以进行高精度、高速度、无接触的加工,适用于对特殊形状和特殊材料进行加工。
四、特种加工的应用领域1. 航空航天领域:航空航天领域对零部件的精密度和表面质量有着很高的要求,因此需要利用特种加工方法对零部件进行加工,以满足其高精度要求。
《特种加工》期末作业

《特种加⼯》期末作业《特种加⼯》课程作业1、你认为特种加⼯将来能否完全取代传统加⼯?简要说明原因。
答:不能。
第⼀、特种加⼯加⼯装备⼤多数⽐较贵,需要⼀次性投资⼤,并且⼤部分只适合⼤批⼤量⽣产,⼩批量⽣产还是需要传统加⼯⽅法。
第⼆、特种加⼯中各种加⼯⼯艺所加⼯的零件精度都⽐较⾼,对于精度要求不⾼的零件⽤特种加⼯会提⾼⼯艺成本。
第三、特种加⼯需要⼤量的专业⼈才才能进⾏⽣产,⽽社会不可能提供那么多专业⼈才。
2、列表举出电⽕花加⼯机床中,快⾛丝和慢⾛丝两种类型有哪⼀些主要区别?答:如下表:3、列表举出电解加⼯与电⽕花加⼯的不同之处。
4、切削加⼯能否加⼯弯孔?特种加⼯⽅法中哪些可以加⼯弯孔?其原理如何?答:切削加⼯不能加⼯弯孔。
特种加⼯⽅法中可以加⼯弯孔的有:(1)电⼦束加⼯:利⽤电⼦束在磁场中偏转的原理,使其在⼯件内部偏转,可加⼯出微细弯孔;(2)离⼦束加⼯:利⽤离⼦束在磁场中偏转的原理,使其在⼯件内部偏转,可加⼯出弯孔;(3)电⽕花加⼯:将⼯具电极做成弯的就可以加⼯弯孔,⼯具电极相对于⼯件作进给运动,将⼯件电极的形状和尺⼨复制在⼯件上,从⽽加⼯出所需要的零件;(4)超声加⼯:利⽤⼯具端⾯作超声频振动,通过磨料悬浮液加⼯硬脆材料,可以加⼯出弯孔。
5、⾼能束加⼯包括哪⼀些特种加⼯⽅法?各有什么特点?答:⾼能束加⼯包括:激光加⼯、电⼦束加⼯、离⼦束加⼯、⽔射流加⼯等各⾃特点:⼀、激光加⼯:①、激光加⼯能量⾼,光能转化为热能,⼏乎可以熔化、⽓化任何材料,特别是⾼硬度⾼强度的材料;②、激光加⼯的光斑⼤⼩、输出功率可以进⾏调节,因此可以进⾏精密加⼯;③、属于⾮接触加⼯,加⼯过程中⽆⼑具磨损和切削⼒产⽣;④、加⼯速度快,热影响区⼩,容易实现加⼯的⾃动化;⑤、可以通过透明介质对密闭容器内进⾏加⼯;⑥、激光加⼯的重复精度和表⾯粗糙度难以保证,需进⾏重复加⼯;⑦、激光加⼯,⽣产效率⾼,质量可靠,经济效益好;⑧、需易通风抽⽓,操作⼈员应戴防护⽬镜。
特殊工种种类

特殊工种种类特殊工种种类一、特种作业工种范围:1、电工作业2、金属焊接切割作业3、起重机械(含电梯)作业4、企业内机动车辆驾驶5、登高架设及高空悬挂业6、制冷作业7、锅炉作业(含水质化验)8、压力容器操作9、爆破作业10、矿山通风作业(含瓦斯检验)11、矿山排水作业(含尾矿坝作业)12、其他二、特种作业操作项目1、电工作业(1)安装(2)维修(3)值班(4)矿山电工2、金属焊接切割作业(1)电焊(2)气割(3)气焊3、起重机械作业(1)桥门式起重机司机(2)塔式起重机司机(3)流动式起重机司机(4)门座式起重机司机(5)电梯司机(6)卷扬机司机(7)施工升降机司机(8)铁路专用起重司机(9)起重指挥(10)起重司索(11)电梯日常保养(12)电梯安装维修(13)桥门式起重机安装维修(14)塔式起重机安装维修(15)施工升降机安装维修(16)机械式停车设备安装维修(17)矿山提升机(绞车)操作工、信号工、把钩工4、企业内机动车辆驾驶(1)铲车(2)叉车(3)抓斗车(4)装载车(5)挖掘车(6)压路车(7)推土机(8)平地机(9)翻斗车(10)矿山电机车(11)矿山内燃机车(12)矿山自卸汽车5、登高架设及高空悬挂作业(1)木、竹质架设(2)钢管架设(3)外墙清洗(4)外墙装修6、制冷作业(1)操作(2)维修7、锅炉作业(含水质化验)8、压力容器操作9、爆破作业10、矿山通风作业(含瓦斯检验)(1)瓦斯检查员(2)矿井通风工(3)瓦斯抽放工11、矿山排水作业(含尾矿坝作业)(1)水泵工(2)尾矿工。
特种加工形成性作业
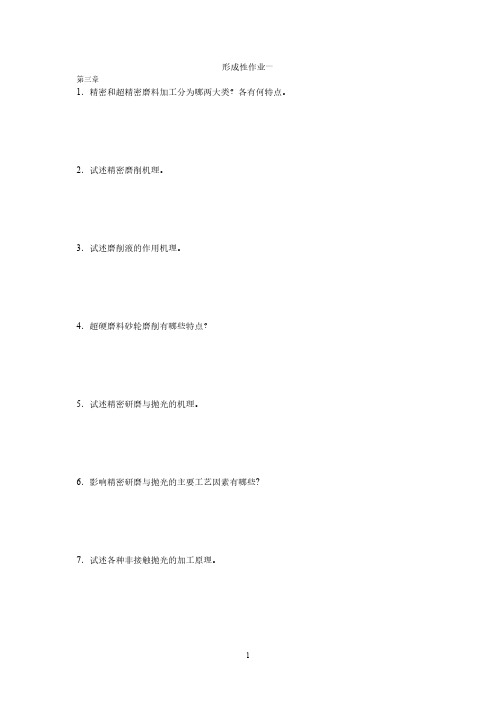
形成性作业一第三章1.精密和超精密磨料加工分为哪两大类?各有何特点。
2.试述精密磨削机理。
3.试述磨削液的作用机理。
4.超硬磨料砂轮磨削有哪些特点?5.试述精密研磨与抛光的机理。
6.影响精密研磨与抛光的主要工艺因素有哪些?7.试述各种非接触抛光的加工原理。
第四章1.电火花加工时,间隙液体介质的击穿机理是什么?2.电火花加工的机理是什么?3.什么是极性效应?在电火花加工中如何充分利用极性效应?4.电火花加工时,什么是间隙蚀除特性曲线?粗、中及精加工时,间隙蚀除特性曲线有何不同?6.在实际加工中如何处理加工速度、电极损耗与表面粗糙度之间的矛盾关系?7.电火花机床有哪些主要用途?8.电火花穿孔加工中常采用哪些加工方法?9.电火花成形加工中常采用哪些加工方法?10.电火花加工时的自动进给系统与传统加工机床的自动进给系统,在原理上、本质上有何不同?为什么会引起这种不同?11.试比较常用电极(如纯铜、黄铜、石墨等)的优缺点及使用场合。
12.什么是覆盖效应?请举例说明覆盖效应的用途。
形成性作业二第五章1.电火花线切割加工与电火花加工的不同特点。
2.电火花线切割的加工原理。
3.试分析影响表面粗糙度的因素。
4.试述线切割加工的主要工艺指标及其影响因素。
5.用3B代码编制加工图5.19所示的线切割加工程序。
6.用ISO代码编制加工图5.17所示的线切割加工程序。
要求同例5-2。
7.如图所示的某零件图(单位为mm),AB、AD为设计基准,圆孔E已经加工好,现用线切割加工圆孔F。
假设穿丝孔已经钻好,请说明将电极丝定位于欲加工圆孔中心F的方法。
第六章1.按其作用原理,电化学加工分为哪几类?各包括哪些加工方法?有何用途?2.什么叫电极电位、标准电极电位和平衡电极电位?3.电解加工过程中必须具备的工艺条件是什么?4.电解加工的加工间隙有哪几种?决定型孔尺寸和精度的是哪种间隙?5.电解液按酸碱度分为几大类,最常用的电解液有哪几种?6.电解加工中电解液的作用如何?对电解液有哪些基本要求?7.电解加工机床有哪些基本要求?8.选用电解加工工艺应考虑的基本原则是什么?电解加工主要应用在哪些方面?形成性作业三第七章1.激光产生的原理?2.激光的特性是什么?3.简述激光切割时激光与材料的作用过程。
特种加工安全注意事项

特种加工安全注意事项
特种加工是指对特定材料进行高精度、高难度的加工过程,需要严格控制工艺参数和操作规范,才能保证产品的质量和安全。
以下是特种加工安全注意事项:
1.操作前需进行安全检查,确保机器设备、工具和辅助设备完好无损,没有明显的安全隐患。
2.在加工过程中,要严格按照工艺流程和操作规范进行操作,不得擅自调整工艺参数和操作方式。
3.特种加工通常使用高速旋转的刀具和磨削工具,操作人员必须佩戴防护眼镜、耳塞、手套等个人防护用品,以避免碎片飞溅、噪声干扰和手部受伤。
4.在进行高温加工时,必须注意防火和防爆,加工场所必须配备灭火器材和应急处理预案。
5.特种加工涉及到的材料常常具有毒性、放射性、腐蚀性等危险性,操作人员必须了解其性质和注意事项,遵守相关的安全措施和操作规范。
6.加工完成后,必须对设备和工具进行清洁和维护,及时处理废弃物和危险废物,保持工作区域的整洁和安全。
7.特种加工作为一项高风险的技术活动,操作人员必须接受专业培训和考核,获得相应的资格证书方可从事相应的工作。
以上是特种加工安全注意事项,希望广大从事特种加工的人员能够认真落实,确保工作安全,提高工作效率。
吉大14秋学期《特种加工》在线作业一满分答案

吉大14秋学期《特种加工》在线作业一试卷得分:100单选题1. 电火花线切割加工过程中,电极丝与工件间存在的状态有( )A. 开路B. 短路C. 火花放电D. 电弧放电正确答案:C 满分:4 分得分:42. 电火花线切割加工称为( )A. EDMBB. WEDMC. ECMD. EBM正确答案:B 满分:4 分得分:43. 在加工较厚的工件时,要保证加工的稳定,放电间隙要大,所以( )A. 脉冲宽度和脉冲间隔都取较大值B. 脉冲宽度和脉冲间隔都取较小值C. 脉冲宽度取较大值,脉冲间隔取较小值D. 脉冲宽度取较小值,脉冲间隔取较大值正确答案:A 满分:4 分得分:44. 在快走丝线切割加工中,电极丝章紧力的大小应根据( )的情况来确定A. 电极丝的直径B. 加工工件的厚度C. 电极丝的材料D. 加工工件的精度要求正确答案:B 满分:4 分得分:45. 用线切割机床加工直径为10 mm的圆孔,在加工中当电极丝的补偿量设置为0.12 mm 时,加工孔的理论直径为10.02mm。
如果要使加工的孔径为10 mm,则采用的补偿量应为( )A. 0.10mmB. 0.11mmC. 0.12mmD. 0.13mm正确答案:B 满分:4 分得分:46. 在电火花加工中存在吸附效应,它主要影响( )A. 工件的可加工性B. 生产率C. 加工表面的变质层结构D. 工具电极的损耗正确答案:D 满分:4 分得分:47. 用电火花加工冲模时,若火花间隙能保证配合间隙的要求,应选用的工艺方法是( )。
特种加工实习报告
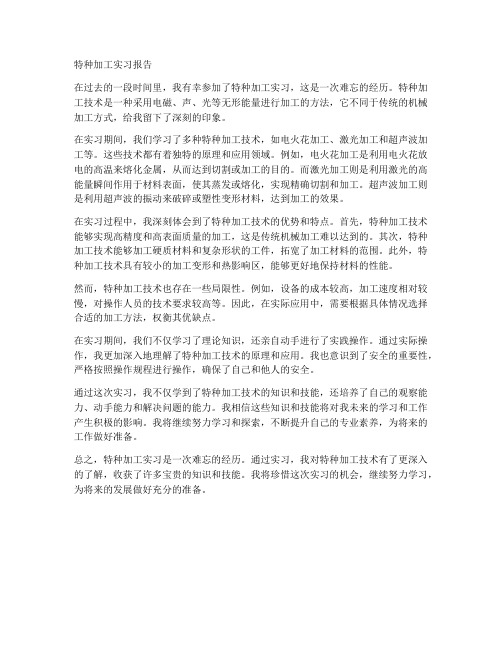
特种加工实习报告在过去的一段时间里,我有幸参加了特种加工实习,这是一次难忘的经历。
特种加工技术是一种采用电磁、声、光等无形能量进行加工的方法,它不同于传统的机械加工方式,给我留下了深刻的印象。
在实习期间,我们学习了多种特种加工技术,如电火花加工、激光加工和超声波加工等。
这些技术都有着独特的原理和应用领域。
例如,电火花加工是利用电火花放电的高温来熔化金属,从而达到切割或加工的目的。
而激光加工则是利用激光的高能量瞬间作用于材料表面,使其蒸发或熔化,实现精确切割和加工。
超声波加工则是利用超声波的振动来破碎或塑性变形材料,达到加工的效果。
在实习过程中,我深刻体会到了特种加工技术的优势和特点。
首先,特种加工技术能够实现高精度和高表面质量的加工,这是传统机械加工难以达到的。
其次,特种加工技术能够加工硬质材料和复杂形状的工件,拓宽了加工材料的范围。
此外,特种加工技术具有较小的加工变形和热影响区,能够更好地保持材料的性能。
然而,特种加工技术也存在一些局限性。
例如,设备的成本较高,加工速度相对较慢,对操作人员的技术要求较高等。
因此,在实际应用中,需要根据具体情况选择合适的加工方法,权衡其优缺点。
在实习期间,我们不仅学习了理论知识,还亲自动手进行了实践操作。
通过实际操作,我更加深入地理解了特种加工技术的原理和应用。
我也意识到了安全的重要性,严格按照操作规程进行操作,确保了自己和他人的安全。
通过这次实习,我不仅学到了特种加工技术的知识和技能,还培养了自己的观察能力、动手能力和解决问题的能力。
我相信这些知识和技能将对我未来的学习和工作产生积极的影响。
我将继续努力学习和探索,不断提升自己的专业素养,为将来的工作做好准备。
总之,特种加工实习是一次难忘的经历。
通过实习,我对特种加工技术有了更深入的了解,收获了许多宝贵的知识和技能。
我将珍惜这次实习的机会,继续努力学习,为将来的发展做好充分的准备。
- 1、下载文档前请自行甄别文档内容的完整性,平台不提供额外的编辑、内容补充、找答案等附加服务。
- 2、"仅部分预览"的文档,不可在线预览部分如存在完整性等问题,可反馈申请退款(可完整预览的文档不适用该条件!)。
- 3、如文档侵犯您的权益,请联系客服反馈,我们会尽快为您处理(人工客服工作时间:9:00-18:30)。
特种加工期末大作业(一)如图所示为一落料零件,用3B格式编制加工如图所示零件凸凹模的数控线切割程序。
已知电极丝直径为φ0.18mm,单边放电间隙为0.01mm。
零件图零件图(平均尺寸)工艺分析1右图图示尺寸为平均尺寸,故作相应偏移就可按此尺寸编程2凸模在模具中起着很重要的作用,它的设计形状、尺寸精度及材料硬度都直接影响模具的冲裁质量、使用寿命及冲压件的精度。
在实际生产加工中,由于工件毛坯内部的残留应力变形及放电产生的热应力变形,故应首先加工好穿丝孔进行封闭式切割,尽可能避免开放式切割而发生变形。
3凸模的轮廓线与毛坯边缘的宽度应至少保证在毛坯厚度的1/5。
4凹模在线切割加工前,模板已进行了冷加工、热加工,内部已产生了较大的残留应力。
因此,模板在线切割加工时,随着原有内应力的作用及火花放电所产生的加工热应力的影响,将产生不定向、无规则的变形,使后面的切割吃刀量厚薄不均,影响了加工质量和加工精度。
针对此种情况,对精度要求比较高的模板,通常采用4次切割加工。
第1次切割将所有型孔的废料切掉,取出废料后,再由机床的自动移位功能,完成第2次、第3次、第4次切割。
这种切割方式能使每个型孔加工后有足够的时间释放内应力,能将各个型孔因加工顺序不同而产生的相互影响、微量变形降低到最小程度,较好地保证模板的加工尺寸精度。
5预先在毛坯的适当位置用穿孔机或电火花成形机加工好Φ1.0—Φ1.5mm 穿丝孔,穿丝孔中心与凸模轮廓线间的引入切割线段长度选取3mm。
零件在毛坯上的定位凹模电极丝中心轨迹凸模电极丝中心轨迹凹模凸模确定补偿距离电极中心轨迹如图中双点划线所示。
补偿距离为:△R=(0.18/2+0.01)mm=0.1mm一、凹模切割路线的选择加工路线的选择在加工中,工件内部应力的释放要引起工件的变形,所以在选择加工路线时应尽量避免破坏工件或毛坯结构刚性。
合理地选择切割路线可简化编程计算,提高加工质量。
根据分析,选择穿丝孔在1顺时针走刀切割顺序按1→2→3→4→5→6→7→8→9→10→11→12→13→14→15→1计算交点坐标将电极丝中点轨迹划分成单一的直线或圆弧段(每点坐标以其前一点为坐标原点,圆弧则以圆心为坐标原点).即点2的坐标值以坐标轴x1-y1来计算,点3的坐标以x2-y2来计算……2(-22850,0)3(19859,0)4(19900,0)5(19859,-19859)6(-19859,0)7(0,-20171)8(19859,-19859)9(29659,0)10(0,20000)11(-20210,0)12(0,-20000)13(-29659,0)14(19859,19859)15(0,20171)3B程序编制◆B20359GxL3;(2)◆B1B1B19859GxL1;(3)◆B39800GySR3;(4)◆B1B1B19859GxL4;(5)◆B19859GxL3;(6)◆B20171GyL4;(7)◆B20000GyL2;(8)◆B29659GxL3;(9)◆B20000GyL2;(10)◆B20210GxL3;(11)◆B20000GyL4;(12)◆B29659GxL3;(13)◆B1B1B19859GxL1;(14)◆B20141GxL2;(15)◆B3000GxL1;(1)空走二、凸模切割路线的选择合理地选择切割路线可简化编程计算,提高加工质量。
根据分析,选择穿丝孔在1点,切割顺序按1→2→3→4→5→6→7→8→9→10→11→12→13→14→15→1计算交点坐标将电极丝中点轨迹划分成单一的直线或圆弧段(每点坐标以其前一点为坐标原点,圆弧则以圆心为坐标原点)。
即点2的坐标值以坐标轴x1-y1来计算,点3的坐标以x2-y2来计算……2(20459,20495)3(0,19925)4(-20141,0)5(20141,20141)6(20100,0)7(20141,-20141)8(-20141,0)9(0,-19925)10(20141,-20141)11(-30341,0)12(0,-20000)13(-19810,0)14(0,-2000)15(-30341,0)3B程序编制◆B22895GxL1;(2)◆B19925GyL2;(3)◆B20171GxL3;(4)◆B1B1B20171GyL1;(5)◆B20100GxSR3;(6)◆B20141GxL4;(7)◆B20141GxL3;(8)◆B19925GyL4;(9)◆B1B1B20141GxL4;(10)◆B30341GxL3;(11)◆B20000GyL2;(12)◆B19925GxL3;(13)◆B20000GyL4;(14)◆B30341GxL3;(15)◆B1B1B3000GxL3;(1)装夹方法装夹工件时,必须保证工件的切割部位位于机床工作台纵向、横向进给的允许范围之内,以避免超出极限,同时应考虑切割时电极丝的运动空间。
夹具应尽可能选择通用(或标准)件,所选夹具应方便装夹,以便于协调工件和机床的尺寸关系。
选用桥式支撑方式装夹。
如图所示,在通用夹具上放置垫铁后再装夹工件,装夹方便,这种方式对大、中、小型工件都适用。
(二)下图所示型腔表面粗糙度Ra1.25(1)设计加工型腔的精加工工具电极(不采用平动修整的工艺方法)。
(2)根据工艺参数曲线图表确定峰值电流、脉宽及脉间。
并说明该规准所能达到的加工效率、电极损耗率及单边侧面放电间隙。
型腔形状、位置尺寸如下图所示:型腔内部轮廓图:一、工具电极形式选择根据电极外形尺寸的大小与复杂程度、电机结构的工艺性等因素综合考虑,可分为:整体式电极、组合式电极、镶拼式电极。
组合式电极:在同一个凹模上有多个型孔时,可将多个电极组合在一起,一次穿孔完成各型孔的加工,这种电极称为组合式电极。
镶拼式电极:形状复杂,整体加工困难的电极,可采用镶拼式结构。
根据工具电极的部分参数及相关要求,择优选择电极形式为整体式电极二、选择电参数在型腔精加工时,需按表面粗糙度(见书本图2-36)来选择脉宽和峰值电流。
而表面粗造度应优于R1.25µm,一般都选用窄脉宽和小峰值电流进行加工,从而再可根据图(见书本图2-35,图2-37和图2-38)来查出相应参数选择,如放电间隙、腐蚀速度和电极损耗。
相应参数选择归纳如下表:型腔模的加工比较困难,因为是不通孔加工,工作液循环和电蚀产物排除条件差,工具电极损耗后无法靠主轴进给补偿精度,金属蚀除量大,其次是加工面积变化大,加工过程中店规准的变化范围大,并由于型腔复杂,电极损耗不均匀,对加工精度影响大。
因此对型腔模电火花加工,既要求蚀除量大,加工速度高,又要求电极损耗低,并保证所要求得精度和表面粗糙度。
依据精加工的电参数,最主要应注意的是:表面粗糙度、精度(放电间隙)、生产效率和电极损耗。
应尽量使腐蚀速度快,电极损耗小,峰值电流小(与尖角有关),所以择优选择第一组数据,i峰=4.3,t0=110,v=0.02,θ%=3.5,s=1.2。
三、电极尺寸计算电极尺寸与所加工模具的大小、形状、复杂程度有关;与电极材料、电加工参数、深度、余量及间隙有关。
水平尺寸确定:计算公式为a=A±kb其中:a为电极水平方向尺寸,b为电极单边缩放量(单边火花放电间隙),K 为系数,A为型腔图样上的名义尺寸设计电极水平尺寸时注意:1)型腔图样上的名义尺寸A应取中值尺寸。
2)计算出的电极尺寸应规定公差,一般可取凹模型孔公差的1/2—1/3单边放电间隙S=0.02a为取相应尺寸的中值尺寸a1=40.02-0.02=40c=20a3=100+2X0.02=100.04a4=20.01-2X0.02=20.97a5=19.99+2X0.02=20.03a6=80+2X0.02=80.04R1=20+0.02=20.02R2=20-0.02=19.98将上述尺寸进行标注,而公差可取型腔的1/2,电极零件形状图如下图所示:根据粗糙度的要求,电极的Ra值要比型腔的Ra值高一档次,故而可取电电极高度方向尺寸确定高度方向尺寸设计时应考虑型腔深度、压板余量、夹板尺寸等等诸多因素。
型腔深度20cm,压板余量留2cm,电极放电间隙s=0.03mm。
电极总高度H的确定:H=L1+L2L1:电极每加工一个型腔,在垂直方向的有效高度,包括型腔深度和电极端面损耗量,并扣除端面加工间隙值。
L2:考虑到加工结束时,电极夹具不和夹具模块或压板发生接触,以及同一电极需重复使用而增加的高度。
总高度H=L1+L2=20-0.02+20=39.98mm四、校核电流密度加工面积小时不宜选择过大的峰值电流,否则放电集中,易于拉弧。
一般小面积时以保持3-5A/cm2,大面积时以保持1-3A/cm2的视在电流密度为宜。
依据这个我们可以知道电流密度适宜。
五、防止产生塌角考虑到其他因素的影响,如排气孔,充油孔,脉肩等,应在电极相应部位进行适当的加工,尤其是尖角部位,要防止塌角的产生。
处理后的电极工具如下图所示:六、排气孔和冲油孔的设计当型腔加工时应及时将电加工过程中产生的气体排出,否则,容易出“放炮”现象。
放炮造成的震动容易使工件错位。
而且考虑到电火花加工时对工作液的要求,为了保证加工零件的精度,有时我们还应该适度的开设冲油孔保证工作液,及时进行排屑。
型腔加工一般为盲孔加工,排气、排屑比较困难,会影响加工速度、定性和表面质量。
在不易排屑的拐角、窄缝处开冲油孔。
但冲油孔冲、抽油时应该注意压力不能过大,冲抽油压力一般为20KPA左右,可随深度的增加而增加。
冲油压力增加,电极损耗也增加。
在蚀除面积较大以及电极端部有凹入的部位开排气孔,孔径一般为φ1-φ2。
若为一个孔以上,则孔距一般20-40左右,孔要适当错开。
七、装夹方式确定与校正根据设计电极参数,考虑到为了方便有效调节电极相对位置等因素,我们可采用如图所示装夹形式。
电极装夹好后必须进行校正才能加工,不仅要调节电极与工件基准面垂直,而且需在水平面内调节、转动一个角度,使工具电极的截面形状与将要加工的工件型孔或型腔定位的位置一致。
校校正常用的几种方法如下:1、当电极直臂面较长时,可用精密角尺对光校正或百分表校正。
2、可按电极或电极上固定板端面作辅助基准校正电极,这是使用百分表检验电机与工作台平行度。
3、对没有直臂面的电极,在校正时是比较困难的,只有采用精规准、小电流放电打印法,使用电极与工件四周火花放电均匀,已完成校正和找正工作。
下图为所设电极三维造型图:。