转杯纺纱机纺纱原理及适纺原料
BD-D330型转杯纺纱机结构性能及纺纱工艺
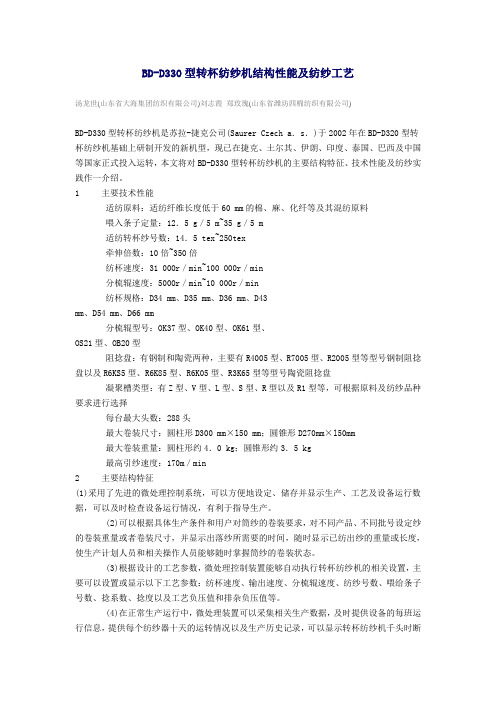
BD-D330型转杯纺纱机结构性能及纺纱工艺汤龙世(山东省大海集团纺织有限公司)刘志霞郑玫瑰(山东省潍坊四棉纺织有限公司)BD-D330型转杯纺纱机是苏拉-捷克公司(Saurer Czech a.s.)于2002年在BD-D320型转杯纺纱机基础上研制开发的新机型,现已在捷克、土尔其、伊朗、印度、泰国、巴西及中国等国家正式投入运转,本文将对BD-D330型转杯纺纱机的主要结构特征、技术性能及纺纱实践作一介绍。
1 主要技术性能适纺原料:适纺纤维长度低于60 mm的棉、麻、化纤等及其混纺原料喂入条子定量:12.5 g/5 m~35 g/5 m适纺转杯纱号数:14.5 tex~250tex牵伸倍数:10倍~350倍纺杯速度:31 000r/min~100 000r/min分梳辊速度:5000r/min~10 000r/min纺杯规格:D34 mm、D35 mm、D36 mm、D43mm、D54 mm、D66 mm分梳辊型号:OK37型、OK40型、OK61型、OS21型、OB20型阻捻盘:有钢制和陶瓷两种,主要有R4005型、R7005型、R2005型等型号钢制阻捻盘以及R6KS5型、R6K85型、R6K05型、R3K65型等型号陶瓷阻捻盘凝聚槽类型:有Z型、V型、L型、S型、R型以及R1型等,可根据原料及纺纱品种要求进行选择每台最大头数:288头最大卷装尺寸:圆柱形D300 mm×l50 mm;圆锥形D270mm×l50mm最大卷装重量:圆柱形约4.0 kg;圆锥形约3.5 kg最高引纱速度:170m/min2 主要结构特征(1)采用了先进的微处理控制系统,可以方便地设定、储存并显示生产、工艺及设备运行数据,可以及时检查设备运行情况,有利于指导生产。
(2)可以根据具体生产条件和用户对筒纱的卷装要求,对不同产品、不同批号设定纱的卷装重量或者卷装尺寸,并显示出落纱所需要的时间,随时显示已纺出纱的重量或长度,使生产计划人员和相关操作人员能够随时掌握筒纱的卷装状态。
棉纺手册 第三篇 成纱 第二章 转杯纺纱

第二章转杯纺纱(棉纺手册P687-775)第一节转杯纺纱的技术特点与机械构造一、技术特点转杯纺纱是通过高速回转的转杯及杯内负压完成纤维输送、凝聚、并合、加捻成纱的一种新型纺纱方法(属于自由端纺纱范畴)。
现代转杯纺纱机都是通过分梳辊将喂入条子分梳成连续不断的纤维并随气流均匀地输入转杯,由引纱卷绕机构将转杯纺的纱引出并卷绕成纱筒。
转杯纺纱使加捻与卷绕分开,解决了高速和大卷装间的矛盾。
转杯纺纱的原料以棉为主,还包括化纤、毛、麻、丝等。
废棉和再生纤维在转杯纺纱厂里也可使用。
转杯纺纱与传统的环锭纺纱相比,具有高速高产、大卷装、缩短工序、改善劳动条件、使用原料广泛、成纱均匀、结杂少、耐磨和染色性能好等特点。
因此,转杯纺纱是目前技术上最成熟、应用面最广、经济效益十分显著的一种新型纺纱方法。
二、机械构造和纺纱流程转杯纺纱的截面示意图如图3-2-1所示,转杯纺纱机的机械构造主要由喂给分梳机构、排杂回收机构、纤维输送机构、凝聚加捻机构、引纱卷绕机构和负压排风系统组成。
转杯纺纱机的电器、仪表和自动控制局部完成了机电一体化与自动化。
图3-2-1 转杯纺纱机截面示意图纺纱器是一个由喂给分梳机构、成纱机构及引纱管组成的独立部件,其示意图如图3-2-2所示。
转杯纺纱的纺纱流程与纤维流的运动规律见图3-2-3。
图3-2-2 纺纱器示意图1—转杯2—分梳辊3—排杂区4—假捻盘5—阻捻器6—输纤通道7—喂给罗拉8—喂给板9—引纱管10—可调补气阀图3-2-3 转杯纺纱的纺纱流程与纤维流的运动规律V1—条子喂给线速度V2—分梳辊线速度V3—输纤通道入口速度V4—输纤通道出口线速度V5—转杯滑移面线速度V6—转杯凝聚槽线速度V7—纱剥离点线速度V7—V6—纱剥离点相对转杯的线速度V8—引纱线速度V9—卷绕线速度三、转杯纺纱机的分类转杯可分为两类,排气式转杯(如图3-2-4)和抽气式转杯(如图3-2-5)。
排气式是在转杯上自身打有排气孔(一般是8个),回转时类似离心风扇的作用,在转杯内产生负压;抽气式是转杯自身无排气孔,依靠外界抽气在转杯上口与罩盖之间抽吸,产生转杯内负压。
转杯纺纺低捻纱工艺

转杯纺纺低捻纱工艺
转杯纺纺低捻纱工艺是一种纺纱工艺,主要用于生产低捻纱线。
这种工艺中,首先将纤维原料进行预整理和梳理处理,然后通过转杯纺机进行纺纱。
转杯纺纱工艺的主要步骤包括:
1. 纤维预整理:将纤维原料进行清洗、开松等处理,使纤维更加柔软和整齐。
2. 梳理处理:将预整理后的纤维送入梳机,通过梳理的过程使得纤维更加平行排列,并且去除其中的杂质和短纤维。
3. 转杯纺机纺纱:经过梳理的纤维进入转杯纺机,转杯纺机通过快速旋转的转杯将纤维拉伸并加以撕断,使其纤维变细,并同时添加适量的卡梳液或者润滑剂,使纤维更加柔软光滑。
4. 捻纱处理:将纺出的纱线通过捻纱机进行捻合,使得纱线有一定的紧密程度,增加其强度和耐磨性。
转杯纺纺低捻纱工艺相比传统的纺纱工艺,具有纺纱效率高、纤维细度均匀、纱线质量好等优点。
同时,由于添加润滑剂,纺织品的手感更加柔软舒适。
因此,转杯纺纺低捻纱工艺广泛应用于棉纺、毛纺、化纤等纺织行业。
喷气涡流纺与环锭纺转杯纺三种纺纱方法综合对比分析

差(%) CVb% +0.5 +1.6 +1.7 2.01 1.46 1.38
环锭纺 转杯纺 喷气涡 流纺
从以上对比数据中可以看出: 条干CV%和细节-50%:环锭纺最好,其次喷气涡流纺,转杯 纺最差。 粗节+50%:环锭纺最好,其次喷气涡流纺,转杯纺最差。 棉结+200%:喷气涡流纺最好,其次环锭纺,转杯纺最差。 单纱断裂强度:环锭纺最高,其次涡流纺,转杯纺最低。 条干CVb%:喷气涡流纺最好,其次转杯纺,环锭纺最差。
涡流
切向 开口 进风孔
涡流管
负压装置
2 原料使用
三种纺纱方法由于成纱结构不一样,相同规格 的原料所纺出的纱在强力、条干方面差异较大 针对不同的纺纱方法和纺纱支数,需要选择不同 规格的原料来弥补各自成纱中的不足
环锭纺选用 原料规格为 1.67dtex×3 8mm 100%, 成纱纤维根 数为118根 转杯纺配置 ¢33mm纺杯, 所选原料 1.33dtex×32m m 100%,成纱 纤维根数为148 根 喷气涡流纺 选用原料为 1.33dtex×3 8mm 100%, 成纱纤维根 数为148根
生产效率(%) 97.4 96.0 95.2 94.4 93.1 91.7 90.0 87.8 85.9 每台每小时断头率(根) 204.1 280.2 320.4 370.7 416.1 440.4 455.4 469.8 513.1 折千锭时断头率(根) 2551 3503 4005 4634 5201 5505 5693 5873 6414
3 工艺流程
3 喷气涡流 纺
FA002抓棉机→SFA035混开棉机→FA106A梳针开棉机→FA161振 动棉箱给棉机→A076F成卷机→FA204C梳棉机→FA306A并条机 (二道)→RSB D401自调匀整并条机→种纺纱方法生产的19.7tex粘胶纱成纱质量指标对比 原料 纺纱方 法 ( 条干 细节50% 3 13 6 dtex·mm) CV% 规格 1.67×38 1.33×32 1.33d×38 12.67 13.80 13.39 粗节 +50 % 17 38 29 棉节 +200 % 28 59 23 单纱强 力CV% 9.3 8.9 10.0 单纱断裂 强度 (cN/tex) 15.1 11.5 12.8 百米重 量 CV% 1.8 1.1 0.9 重量偏 条干
转杯纺纱机工作原理

转杯纺纱机工作原理
转杯纺纱机是一种常用于纺织工业的设备,它的工作原理通过以下步骤完成:
1. 预备工作:首先,将纺纱机的运转速度设定为所需速度,并进行必要的调整和检查确保机器正常运行。
2. 进纱:将纱线通过给纱管引线,使其进入转杯纺纱机的纱锭。
给纱管通过锭筒传送装置将纱线引导到转杯上。
3. 纺纱:在正常工作状态下,转杯纺纱机的纱锭以高速旋转。
当纱锭转动时,给纱管上的纱线受到离心力的作用,沿着纱锭上下移动。
4. 伸长和弯曲:纱线在纱锭上下移动时,同时也被拉伸和弯曲,以加强纱线的强度和稳定性。
5. 驱动力:纱线在纱锭上进行伸长和弯曲的过程中,受到纺纱机设置的驱动力的作用。
这种驱动力可以是摩擦力、张力或重力。
6. 纺纱速度调节:转杯纺纱机的工作速度可以通过调节纱锭的转速来实现。
较高的转速将导致纱线伸长和弯曲的速度更快,从而产生更细的纱线。
7. 排纱:在完成纺纱过程后,纺纱机将产生的纱线通过排纱管和卷绕装置传送到卷绕筒或其他储存装置。
总的来说,转杯纺纱机通过纱锭的高速旋转,使得纱线受到离心力的作用并进行伸长和弯曲,最终实现对原始纱线进行纺纱的过程。
这种方法可以生产高质量和稳定性的纱线,用于纺织品的生产。
(完整版)主要新型纺纱的比较

主要新型纺纱的比较1、成纱原理:转杯纺依靠调整回转的纺杯,将纱尾贴紧在纺杯内壁聚槽内,而头端为引纱罗拉握持并连续输出加捻成纱。
喷气纺靠两只喷嘴喷射相反方向的回旋气流,对由牵伸装置输出的须条先加捻后解捻,表面纤维形成包缠成纱。
摩擦纺一般用两只同向回转的摩擦元件,对其楔形区的纤维施加摩擦力偶,使纤维束滚动而加捻成纱。
2、成纱截面中纤维根数不同:喷气纱中最少纤维根数略高于环锭纱,可纺中低线密度纱;摩擦纺和转杯纺中的最少纤维根数较多。
3、对纤维性能要求不同:影响转杯纱强力的主要因素是纤维的强力和线密度,摩擦纱则是纤维的摩擦因数和强力。
4、纺纱速度和成纱线密度:环锭纺的可纺线密度覆盖面最广,但产量太低,各种新型纺纱的纺纱速度都比环锭纺高,但可纺线密度有局限性5、新型特点:新型纺纱取消了锭子、筒管、钢领、钢丝圈等加捻卷绕元件,并将加捻和卷绕作用分开完成,具有产量高,细纱机的产量取决于锭子的速度,而锭速的提高,一方面受钢丝圈速度的限制,另一方面受气圈张力的限制;卷装大,环锭细纱机上增大卷装的途径是增加筒管长度和加大钢领直径,但筒管加长则气圈高度加长,钢领加大则钢丝圈线速度增大,这些都会导致断头增多,而新型纺纱方法将加捻和卷绕分开进行,可直接纺成筒子纱;工艺流程短,新型纺纱采用条子喂入,直接纺成筒子纱,省去粗纱、络筒两道工序。
转杯纺1、原理:纺杯高速旋转,纺杯内便产生离心力,离心力可使从分流腔转移到纺杯内的棉纤维产生凝聚而成为须条,须条被加捻后便成为纱条。
2、工艺过程:条子从条筒中引出送入喂给罗拉,喂给罗拉与喂给板将条子向前输送,经分梳辊分梳成单纤维,被补风口和引纱管的气流吸入纺纱杯,沿纺纱杯壁滑入凝聚槽形成凝聚须条,由于纺纱杯高速回转产生的离心力使引纱纱尾贴附于凝聚槽面而与须条连接,并被纺纱杯摩擦握持而加捻成纱。
3、转杯纱结构与性能:转杯纱由纱芯与外包缠纤维两部分组成,内层的纱芯比较紧密,外层的包缠纤维结构松散;环锭纱没有纱芯,纤维在纱中大多呈螺旋线排列。
转杯纺纱机纺纱原理及适纺原料
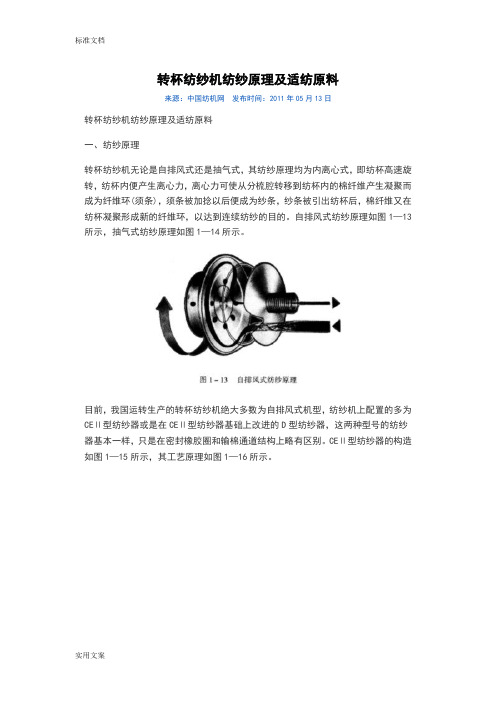
转杯纺纱机纺纱原理及适纺原料来源:中国纺机网发布时间:2011年05月13日转杯纺纱机纺纱原理及适纺原料一、纺纱原理转杯纺纱机无论是自排风式还是抽气式,其纺纱原理均为内离心式,即纺杯高速旋转,纺杯内便产生离心力,离心力可使从分梳腔转移到纺杯内的棉纤维产生凝聚而成为纤维环(须条),须条被加捻以后便成为纱条,纱条被引出纺杯后,棉纤维又在纺杯凝聚形成新的纤维环,以达到连续纺纱的目的。
自排风式纺纱原理如图1—13所示,抽气式纺纱原理如图1—14所示。
目前,我国运转生产的转杯纺纱机绝大多数为自排风式机型,纺纱机上配置的多为CEⅡ型纺纱器或是在CEⅡ型纺纱器基础上改进的D型纺纱器,这两种型号的纺纱器基本一样,只是在密封橡胶圈和输棉通道结构上略有区别。
CEⅡ型纺纱器的构造如图1—15所示,其工艺原理如图1—16所示。
喂入的棉条经给棉喇叭集束以后便进入给棉板与给棉罗拉的握持区,在压簧的作用下对给棉板产生26.5N的压力。
这时由给棉罗拉把棉条按牵伸倍数需要均匀地向前输送至高速旋转的分梳辊的抓取范围。
分梳辊对棉条进行开松并分解成单根纤维(单纤化过程),由于附面作用棉纤维便紧紧地附着在分梳辊齿端。
当分梳辊对棉条进行分解时,原来夹裹在棉纤维中的杂质,由于质量较大(较重),其离心力亦较大,便从棉条中分离出来,如图1—16所示。
杂质被分离出来后,在进入分梳腔排杂区时,借助排杂负压气流的吸引作用,通过纺纱器的排杂通道和排杂玻璃管被排到机身中部的总排杂管道中。
在自排风式转杯纺纱机中,由于高速旋转的纺杯把杯中原有的空气从底部的排气孔排出以后,纺杯内便产生负压(真空度),因纺杯的直径有大小之分,转速有快慢差别,并且又受纺纱器密封性能好坏的影响,因此,纺杯内负压高低存在着较大的差别。
图1—17所示为自排风式及抽气式纺杯内的负压值。
气压为了达到平衡,纺杯内原有的空气被排出后,外界的空气通过分梳腔和引纱玻璃管两个渠道源源不断地向纺杯内补充。
转杯纺纱机工作原理

转杯纺纱机工作原理
转杯纺纱机是一种常用于纺纱过程中的设备,用于将纤维材料纺成纱线。
以下是转杯纺纱机的工作原理:
1. 材料供给:首先,纤维材料(如棉花、化纤等)通过供纱装置送入转杯纺纱机的进给部分。
供纱装置通常是由锭子组成的,每个锭子上有一个供纱管,纤维通过供纱管进入转杯纺纱机。
2. 清理和准备:纤维材料通过供纱装置后,经过清理和准备过程。
这包括去除纤维中的杂质、粗纤维和疙瘩,并进行纤维的开松和整理。
3. 纺纱:准备好的纤维材料进入转杯纺纱机的转杯区域。
转杯纺纱机通常由多个旋转的杯子组成,每个杯子上面有一小段纺锭。
在转杯旋转的过程中,纤维材料会卷绕在纺锭上,并因纺锭的旋转而细长化。
4. 拉伸和捻合:纤维材料在转杯纺纱机上拉伸和捻合,形成连续的纱线。
拉伸和捻合过程会增加纱线的强度和稳定性。
5. 收纱:完成纺纱后,纱线通过收纱装置从转杯纺纱机上取下,并
绕在一个或多个纱锭上。
收纱装置通常由导纱棒和卷绕器等部件组成,确保纱线收集和整齐放置。
转杯纺纱机的工作原理基于纤维的拉伸和捻合。
通过不断旋转的转杯和纺锭,使纤维材料在拉伸和捻合的过程中逐渐变细,从而形成纱线。
转杯纺纱机通常用于中细纺纱,可以产生适用于不同用途的纱线。
- 1、下载文档前请自行甄别文档内容的完整性,平台不提供额外的编辑、内容补充、找答案等附加服务。
- 2、"仅部分预览"的文档,不可在线预览部分如存在完整性等问题,可反馈申请退款(可完整预览的文档不适用该条件!)。
- 3、如文档侵犯您的权益,请联系客服反馈,我们会尽快为您处理(人工客服工作时间:9:00-18:30)。
转杯纺纱机纺纱原理及适纺原料来源:中国纺机网发布时间:2011年05月13日转杯纺纱机纺纱原理及适纺原料一、纺纱原理转杯纺纱机无论是自排风式还是抽气式,其纺纱原理均为内离心式,即纺杯高速旋转,纺杯内便产生离心力,离心力可使从分梳腔转移到纺杯内的棉纤维产生凝聚而成为纤维环(须条),须条被加捻以后便成为纱条,纱条被引出纺杯后,棉纤维又在纺杯凝聚形成新的纤维环,以达到连续纺纱的目的。
自排风式纺纱原理如图1—13所示,抽气式纺纱原理如图1—14所示。
目前,我国运转生产的转杯纺纱机绝大多数为自排风式机型,纺纱机上配置的多为CEⅡ型纺纱器或是在CEⅡ型纺纱器基础上改进的D型纺纱器,这两种型号的纺纱器基本一样,只是在密封橡胶圈和输棉通道结构上略有区别。
CEⅡ型纺纱器的构造如图1—15所示,其工艺原理如图1—16所示。
喂入的棉条经给棉喇叭集束以后便进入给棉板与给棉罗拉的握持区,在压簧的作用下对给棉板产生26.5N的压力。
这时由给棉罗拉把棉条按牵伸倍数需要均匀地向前输送至高速旋转的分梳辊的抓取范围。
分梳辊对棉条进行开松并分解成单根纤维(单纤化过程),由于附面作用棉纤维便紧紧地附着在分梳辊齿端。
当分梳辊对棉条进行分解时,原来夹裹在棉纤维中的杂质,由于质量较大(较重),其离心力亦较大,便从棉条中分离出来,如图1—16所示。
杂质被分离出来后,在进入分梳腔排杂区时,借助排杂负压气流的吸引作用,通过纺纱器的排杂通道和排杂玻璃管被排到机身中部的总排杂管道中。
在自排风式转杯纺纱机中,由于高速旋转的纺杯把杯中原有的空气从底部的排气孔排出以后,纺杯内便产生负压(真空度),因纺杯的直径有大小之分,转速有快慢差别,并且又受纺纱器密封性能好坏的影响,因此,纺杯内负压高低存在着较大的差别。
图1—17所示为自排风式及抽气式纺杯内的负压值。
气压为了达到平衡,纺杯内原有的空气被排出后,外界的空气通过分梳腔和引纱玻璃管两个渠道源源不断地向纺杯内补充。
空气就这样不停地被排出后又不停地进行着补充,纺杯内的气流周而复始地进行着循环,因此,形成了较稳定的负压气流。
原先附着在分梳辊齿端的棉纤维,在负压气流的吸引下,便脱离分梳辊齿尖的控制,通过输棉通道和隔离盘进入纺杯。
棉纤维在纺杯高速旋转时所产生的离心力及负压气流的共同作用下,沿着纺杯的滑移面进入凝棉槽,由于棉纤维的凝聚与并合作用而形成纤维环,跟随纺杯一起旋转。
生头时,纱头在引纱玻璃管的口端,随着补人纺杯的负压气流进入纺杯后,便被甩向凝棉槽并与纤维环进行搭接。
当引纱罗拉从纺纱器中向外抽纱时,原先跟随纺杯旋转在凝棉槽中的纤维环(须条),经剥离后又在阻捻头的作用下加捻成为纱条。
(一)棉条的喂给与输送棉条的喂给是由喂给机构完成的,它主要包括给棉喇叭、给棉板和给棉罗拉。
给棉喇叭起集束作用,它把未进入给棉板和给棉罗拉握持区之前的棉条进行必要的压缩和整形。
经过喇叭口集束整理后,使原先形状不规则、密度不一致的棉条横截面成为扁平状并且密度一致,以有利于分梳辊抓取,还可避免棉条在分梳辊抓取时产生不均匀和分层现象。
给棉罗拉在给棉板的配合下,把棉条输送至分梳辊的抓取范围,为了使棉条被分梳辊均匀地抓取但又不损伤棉纤维,要求给棉板和给棉罗拉对棉条既要保持必要的握持力,但握持力又不能太大,一般为26.5N±1.5N。
(二)开松与除杂开松、除杂作用是由分梳辊、分梳腔右方的三角除尘刀和排杂通道完成的。
当给棉罗拉在给棉板的配合下把棉条均匀向前输送时,分梳辊以6000~8000r/min的转速对棉条进行抓取。
因各厂的棉条定量不一样,一般棉条横截面内含棉纤维2.2万-3万根,棉条基本被分梳辊分解为单根纤维,并被齿尖握持住,有时也出现两三根纤维粘连在一起的现象。
分梳辊在对棉条进行开松、分解的同时,也起分离排除夹裹在棉条中杂质的作用。
由于杂质多为被轧碎的棉秆、棉铃壳、草屑并都呈颗粒状或小片状,又因为它们的质量比棉纤维大得多,因而,其离心力也大。
此外,被分离出来的杂质途经除尘刀时,除尘刀对杂质起分离作用(图1—16中,排杂通道杂质人口处的三角形即为除尘刀)。
杂质还受排杂玻璃管内负压的吸引,在以上几种情况的共同作用下,原先夹裹在棉条中的杂质才有可能被分离出来而排除掉。
对分梳排杂机件有以下质量要求:(1)分梳辊应有足够的转速,以产生应有的分梳抓取力及排除杂质的离心力。
(2)分梳辊齿条应锋利光洁,以便对棉纤维进行抓取、分解和释放,以刺人棉条并有效地分离杂质。
(3)应根据所纺原料的性质,有针对性地选择分梳辊齿条的规格、型号,否则既影响成纱质量,又缩短了分梳辊齿条的使用寿命。
(4)分梳腔及排杂通道应十分光洁,以有利于棉纤维的流动和杂质的排除。
(三)棉纤维的释放与转移棉纤维的释放与转移就是把原先被分梳辊所握持的棉纤维,在纺杯负压气流的吸引下,使棉纤维脱离分梳辊齿尖的控制,从分梳腔经输棉通道最终进入纺杯。
棉纤维释放转移的条件:(1)纺杯内的负压必须高于分梳腔内的负压,也就是输棉通道口内的气流速度一定要大于分梳辊表面的气流速度。
(2)为了使棉纤维更好地转移和有序地流动,输棉通道内气流必须有加速流动的趋势,气流加速的梯度越大,对棉纤维的转移、伸直和舒展越有利,所以,输棉通道入棉口大而出棉口小,如图1—18所示。
抽气式转杯纺输棉通道的入棉口和出棉口悬殊更大。
(3)分梳辊齿尖一定要避免钩挂棉纤维,输棉通道的入棉口应非常光洁,以有利于棉纤维的定向和流动。
(四)棉纤维的凝聚棉纤维的凝聚就是把经过分梳辊分解成的单根纤维,以负压气流作为载体混合成纤维流,经过输棉通道形成一股自杯口流向杯底的旋转气流,空气则从纺杯底部的孔中排出,棉纤维便经纺杯的滑移面滑入凝棉槽,组合形成圆周形的纤维环,如图1—19所示。
在凝聚过程中,棉纤维会产生并合效应,也就是棉纤维一层层地叠加起来。
并合效应有利于改善棉纤维在纺杯凝棉槽中分布不均匀的情况,这也是转杯纺成纱条干比环锭纺成纱条干好的原因所在。
棉纤维凝聚过程必须建立在以下基础之上:(1)纺杯内必须有足够的负压,吸引分梳腔中被分梳辊所握持的棉纤维向纺杯内转移。
(2)纺杯必须有足够的离心力,使棉纤维通过纺杯的滑移面滑人凝棉槽并紧密抱合在一起而形成纤维环。
(3)纺杯必须具有促使棉纤维与气流分离的功能。
以上是棉纤维凝聚的三个必要条件,缺一不可。
(五)剥取与加捻剥取与加捻是聚集在纺杯凝棉槽内的棉纤维须条向纱条过渡的两个不同阶段。
但两者之间又是相辅相成密不可分的两个连续过程。
剥取阶段是凝棉槽内的须条经纱臂牵引而脱离凝棉槽,纱臂在阻捻头的作用下已获得捻度(回),但这时是假捻作用。
当然,在剥离点之后也有部分捻度渗透到须条上。
图1—20中/AB段为纱臂,从剥离点到阻捻头这段纱条上产生的是假捻,其作用是增加须条的动态强力,防止在这段纱条上产生断头。
转杯纺产生的断头有90%以上发生在剥离点至阻捻头这段须条上(即纱臂上)。
加捻阶段是须条从凝棉槽被剥离之后,在高速旋转纺杯的带动下以及在阻捻头的配合下,完成从阻捻头至引纱罗拉这段纱条加捻作用。
因此,从阻捻头至引纱罗拉,这段纱条才是转杯纺纱真正的加捻区,纱条上才获得真捻。
剥取与加捻必须具备以下条件才能实现:(1)剥离点处纱条与凝棉槽内须条的联系力,必须大于须条与纺杯凝棉槽之间的摩擦力和空气阻力,否则无法完成剥取作用。
(2)纱臂AB段的强力必须大于纺纱张力(纱条的轴向拉力),否则纱条要产生断头,无法正常纺纱。
(3)加捻力矩必须大于须条的抗扭力矩,也就是要确保须条棉纤维之间产生扭曲变形,否则捻度无法传递、渗透和形成。
越是粗硬的纤维,纺纱时纱条断头越多,就是这个道理。
(4)剥离点处须条内所包含的棉纤维根数,必须达到组成纱条内棉纤维应有的根数,否则纱条会产生细节或纱条偏细。
二、转杯纺适纺原料(一)转杯纺常用原料种类、性质及工艺技术纺织工业生产中所用的原料分为两大类,一类是天然纤维,另一类是化学纤维。
在天然纤维中又分为植物纤维、动物纤维和矿物纤维。
植物纤维主要有棉类和麻类。
动物纤维主要有羊毛(绒)、兔毛、驼毛、牛绒、桑蚕丝等。
矿物纤维主要有石棉纤维、玻璃纤维等。
化学纤维主要有再生纤维、合成纤维、无机纤维。
合成纤维主要有涤纶、腈纶、锦纶、丙纶、维纶等,再生纤维主要有纤维素纤维、蛋白质纤维及海藻纤维。
再生纤维素纤维主要有粘胶纤维、富强纤维等。
在以上诸多纤维原料当中,只有少数几种纤维适合转杯纺纺纱加工。
1.棉纤维棉纤维是最早被人类用作纺织原料的品种之一,由于它具有良好的保温性、吸湿性及透气性,因此,用它作原料纺成纱线后,进而加工成各种织物或服饰及生活用品都深受人们的喜爱。
棉农培植的棉株生长后开花,如图1—21所示,然后结成棉铃(桃),如图1—22所示,棉铃成熟后自然绽放出棉絮,如图1—23所示,棉絮由棉纤维集结组合而成。
实际上,棉纤维是由包裹在棉籽表皮的细胞发育成熟伸长后而形成的。
一根完整的棉纤维,从它的纵向—亡可分为基部、中部和梢部,其基部和中部较粗,而梢部较细。
人们在纺织技术资料中谈到的棉纤维细度是针对棉纤维中部的粗细而言。
不同品种棉纤维的细度及长度是不同的,转杯纺日常生产中所使用原棉的质量情况见表1—4,棉纤维的纵向具有自然转曲的特点。
表1—4转杯纺常用原棉质量情况主体长度(mm)纤维线密度(dtex)成熟度系数含水率(%)含杂率(%)短绒率(%)42927.5—29.51.85—1.55(5600—6800)1.25—1.757.5~10.53~4.511.5—1852726.1~28.51.80—1.30(5400~7200)1.00—1.508.5~11 3.5—6.513~2062322—251.50~1.10(6000~8000)0.75~1.258.5—12.5 4.6—8.217—25注1.有为锯齿棉。
2.棉纤维长度短于16mm为短绒。
3.表中所列数据仅供参考(非权威数据)。
4.括号内数字为公支制数。
棉纤维自然转曲多、强力高、质量好,在以后的纺纱过程中有利于增强棉纤维之间的抱和力和摩擦力,进而提高成纱强力,减少纱条断头。
棉纤维柔软、纤细,其线密度为0.125—0.2tex,长度适中,为19~31mm。
棉纤维的横截面多为不规则的腰圆形,并且是中空的,如图1-24所示。
棉纤维所具有的保温性、吸湿性、透气性均与这种中空腔髓结构有着十分密切的关系,这也是棉纤维不同于其他纤维的主要特征之一。
棉纤维的表面含有一层蜡质,俗称“棉蜡”,其多少与原棉的产地、品种及成熟度有一定的关系。
一般情况下,成熟度好的棉纤维表层棉蜡较多,成熟度差的棉纤维表层棉蜡较少。
棉蜡在纺纱过程中可起到滑润作用,这对棉纤维的牵伸、分离和防止粘结具有一定的作用。
棉蜡能反射光线,成熟度好的棉纤维对光线反射能力较强,用其纺成纱线的光泽、手感均较好。