博朗清洗中心说明书
博朗9090cc中文说明书
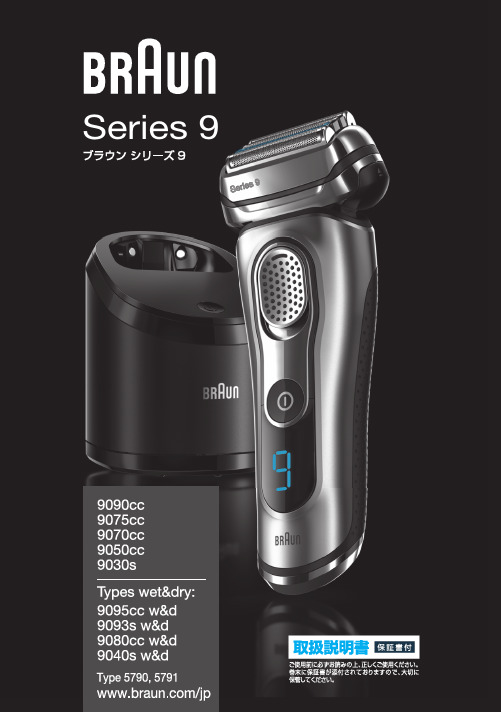
Series 9Japan/UK 97318678/III-15Series 9Serie s 99090ccSeries 9Series 9EnglishOur products are designed to meet the highest standards of quality, functionality and design. Thank you for your trust in Braun’s quality, and we hope you enjoy your new Braun shaver.Read these instructions completely, they contain safety information. Keep them for future reference.WarningYour appliance is provided with a special cord set, which has an integrated Safety Extra Low Voltage power supply. Do not exchange or tamper with any part of it, otherwise there is risk of an electric shock. Only use the special cord set provided with your appliance.The shaver is suitable for cleaningunder running tap water. Detachthe shaver from the power supplybefore cleaning it in water.Models 9095cc w&d/9093s w&d/9080cc w&d/9040s w&d only:This appliance is suitable forcleaning under running water anduse in a bath or shower. For safetyreasons it can only be operatedcordlessly.Note: Only models 9093s w&d and 9040s w&d can be used with foam or gel. Do not shave with a damaged foil or cord. This appliance can be used by children aged from 8 years and above and per-sons with reduced physical, sensory or mental capabilities or lack of experience and knowledge if they have been given supervision or instruction concerning the safe use of the appliance and under-stand the hazards involved. Children shall not play with the appliance. Clean-ing and user maintenance shall not be made by children unless they are older than 8 years and supervised.Oil bottle (not with all models)Keep out of reach of children. Do not swallow. Do not apply to eyes. Dispose of properly when empty.Clean&Charge Station (models9095cc w&d/9090cc/9080cc w&d/ 9075cc/9070cc/9050cc)To prevent the cleaning fluid from leaking, ensure that the Clean&Charge Station is placed on a flat surface. When a cleaning cartridge is installed, do not tip, move suddenly or transport the station in any way as cleaning fluid might spill out of the cartridge. Do not place the station inside a mirror cabinet, nor place it on a polished or lacquered surface. The cleaning cartridge contains a highly flammable liquid so keep it away from sources of ignition. Do not expose to direct sunlight and cigarette smoking nor store it over a radiator.Do not refill the cartridge and use only original Braun refill cartridges.1 Foil & Cutter cassette2 Cassette release buttons3 MultiHeadLock switch4 On/off switch5 Shaver display6 Long hair trimmer7 Shaver-to-stationcontacts8 Release button for long hair trimmer9 Model number of shaver10 Shaver power socket11 Special cord set12 Brush13 Hard travel casePrior to first use remove the protection foil if any from the shaver display. Connect the shaver to an electrical outlet by snapping the special cord set (11) into the power socket (10) or for cc models via the Clean&Charge Station (see Chapter «Clean&Charge Station»).Charging and basic operating information• When charging for the first time, charge continuously for 1 hour.• A full charge provides up to 50 minutes of cordless shaving time. This may vary according to your• Recommended ambient temperature for charging is 5 °C to 35 °C. The battery may not charge properly or at all under extreme low or high temperatures.• Recommended ambient temperature for shaving is 15 °C to 35 °C.• Do not expose the appliance to temperatures higher than 50 °C for extended periods of time.• When the shaver is connected to an electrical outlet, it may take some minutes until the display illuminates.Charge statusThe shaver display (5) shows the charge status of the battery when connected to an electrical outlet:• During charging the respective battery segment will blink.• When fully charged all battery segments will light up for a few seconds then the display turns off. Low chargeThe low-charge light flashes red when the battery is running low. You should be able to finish your shave. With switching off the shaver a beep sound reminds of the low charge status.Models 9095cc w&d/9093s w&d/9090cc: The last9 minutes of remaining shaving time are displayed in digits.Cleaning status (models 9095cc w&d/9090cc/ 9080cc w&d/9075cc/9070cc/9050cc)Travel lockThe lock symbol lights up when the shaver has been locked to avoid unintended starting of the motor (e.g. for storing in a suitcase).Press the on/off switch (4) to operate the shaver. Tips for a perfect dry shave1. Always shave before washing your face.2. At all times, hold the shaver at the right angle(90°) to your skin.3. Stretch your skin and shave against thedirection of your beard growth.MultiHeadLock switch (head lock)To shave hard-to-reach areas (e.g. under the nose) slide the MultiHeadLock switch (3) down to lock the shaver head. The shaver head can be locked in five positions. To change position, move the shaver head with your thumb and forefinger back or forth. It will Models 9095cc w&d/9090cc/9080cc w&d/9075cc/ 9070cc/9050cc: For automatic cleaning in theClean&Charge Station the head lock should be released. Long hair trimmerTo trim sideburns, moustache or beard press the release button (8) and slide the long hair trimmer (6) upwards.Shaving with the cord (not for models 9095cc w&d/ 9093s w&d/9080cc w&d/9040s w&d)If the shaver has run out of power (discharged), you may also shave with the shaver connected to an electrical outlet via the special cord set.Travel lock• Activation: By pressing the on/off switch (4) for3 seconds the shaver is locked. This is confirmed by a beep sound and the lock symbol in the display. Afterwards the display turns off.• Deactivation: By pressing the on/off switch for3 seconds the shaver is unlocked again.Cleaning under running water• Switch on the shaver (cordless) and rinse the shaver head under hot running water until all residues have been removed. You may use liquid soap without abrasive substances. Rinse off all foam and let the shaver run for a few more seconds.• Next, switch off the shaver, press the release buttons (2) to remove the Foil & Cutter cassette (1) and let it dry completely.• If you regularly clean the shaver under water, then apply once a week a drop of light machine oil on top of the Foil & Cutter cassette.Models 9093s w&d/9040s w&d only: The shaver should be cleaned after each foam usage. Cleaning with a brush• Switch off the shaver. Remove the Foil & Cutter cassette (1) and tap it out on a flat surface. Using the brush, clean the inner area of the pivoting head. Do not clean the cassette with the brush as this may damage it!The Foil & Cutter cassette can be attached either way. There is no impact on the shaving performance. The Clean&Charge Station has been developed for cleaning, charging, lubricating, disinfecting, drying14 Station power socket15 Lift button for cartridge exchange16 Station-to-shaver contacts17 Clean&Charge Station display17a L evel indicator17b Status light17c Cleaning program indicator (models 9095cc w&d/ 9090cc/9080cc w&d/9075cc only)18 Start button19 Cleaning cartridgeInstalling the Clean&Charge Station (see fig. D)• Remove the protection foil if any from theClean&Charge Station display.• Press the lift button (15) at the rear side of the Clean&Charge Station to lift up the housing.• Hold the cleaning cartridge (19) down on a flat, stable surface (e.g. table).• Carefully remove the lid from the cartridge.• Slide the cartridge from the rear side into the base of the station until it snaps into place.• Slowly close the housing by pushing it down until it locks.• Connect the station to an electrical outlet by snapping the special cord set (11) into the power socket (14).Charging the shaver in the Clean&Charge Station (see fig. D)Insert the shaver head with the front showing and released head lock into the cleaning station. Important: The shaver needs to be dry and free from any foam or soap residue!The contacts (7) on the back of the shaver need to align with the contacts (16) in the station. Push the shaver in the correct position. A beep sound confirms that the shaver sits properly in the station. Charging will start automatically.Cleaning the shaver (see fig. D)Station, as described above and press the start button (18).The hygiene status will be analyzed and is shownby the cleaning program indicators (17c) in the Clean&Charge Station display (models 9095cc w&d/ 9090cc/9080cc w&d/9075cc only).If status light (17b) does not shine (Clean&Charge Station switches to stand-by after ca. 10 minutes), press start button twice. Otherwise cleaning will not start. For best shaving results, we recommend cleaning after each shave.The cleaning process consists of several cycles, in which cleaning fluid is flushed through the shaver head. Depending on your Clean&Charge Station model and/or program selected, the cleaning time takes up to 3 minutes, followed by an active drying phase of about 40 minutes, during which a fan is running.Afterwards charging will resume, which is indicated in the shaver display. When the shaver is fully charged the display turns off.Cleaning programsshort economical cleaningnormal level of cleaninghigh intensive cleaningModels 9070cc/9050cc:One standard cleaning program is included. Removing the shaver from the Clean&Charge Station (see fig. E)Hold the Clean&Charge Station with one hand and tilt the shaver slightly to the front to release it. Cleaning Cartridge / Replacement (see fig. F)When the level indicator (17a) lights up permanently red, the remaining fluid in the cartridge is sufficient for about 3 more cycles. When the level indicator blinks red, the cartridge needs to be replaced (about every 3 weeks when used daily).After having pressed the lift button (15) to open the housing, wait for a few seconds before removing the used cartridge to avoid any dripping. Before discarding the used cartridge, make sure to close the openings using the lid of the new cartridge, since the used cartridge will contain contaminated cleaning solution.The hygienic cleaning cartridge contains denatured ethanol (specification see cartridge), which once opened will naturally evaporate slowly. Each cartridge, if not used daily, should be replaced after approximately 8 weeks to ensure optimal disinfection. The cleaning cartridge also contains lubricants for the shaving system, which may leave residual marks on the outer foil frame and the cleaning chamber of the Clean&Charge Station. These marks can be removed easily by wiping gently with a damp cloth. Braun recommends changing your shaver’s Foil & Cutter cassette every 18 months to maintain your shaver‘s maximum performance.Available at your dealer or Braun Service Centres:• Foil & Cutter cassette: 90S/90B• Cleaning cartridge Clean&Charge Station: CCR • Braun Shaver cleaner sprayThe cleaning cartridge can be disposed of with regular household waste.Subject to change without notice.For electric specifications, see printing on thespecial cord set.。
博朗清洗及安装方法
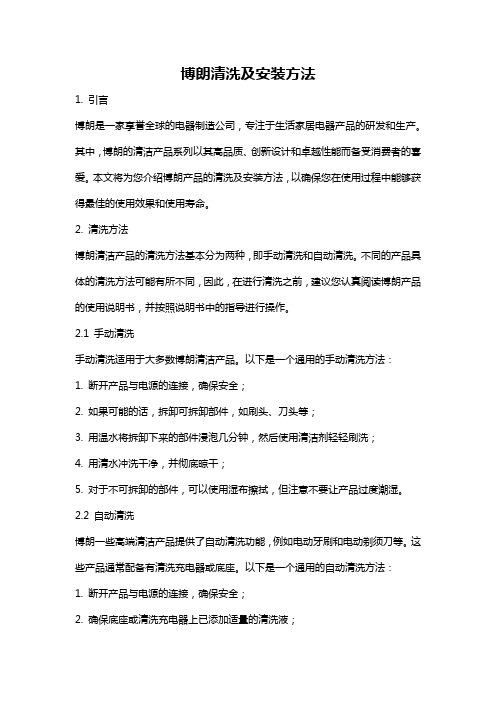
博朗清洗及安装方法1. 引言博朗是一家享誉全球的电器制造公司,专注于生活家居电器产品的研发和生产。
其中,博朗的清洁产品系列以其高品质、创新设计和卓越性能而备受消费者的喜爱。
本文将为您介绍博朗产品的清洗及安装方法,以确保您在使用过程中能够获得最佳的使用效果和使用寿命。
2. 清洗方法博朗清洁产品的清洗方法基本分为两种,即手动清洗和自动清洗。
不同的产品具体的清洗方法可能有所不同,因此,在进行清洗之前,建议您认真阅读博朗产品的使用说明书,并按照说明书中的指导进行操作。
2.1 手动清洗手动清洗适用于大多数博朗清洁产品。
以下是一个通用的手动清洗方法:1. 断开产品与电源的连接,确保安全;2. 如果可能的话,拆卸可拆卸部件,如刷头、刀头等;3. 用温水将拆卸下来的部件浸泡几分钟,然后使用清洁剂轻轻刷洗;4. 用清水冲洗干净,并彻底晾干;5. 对于不可拆卸的部件,可以使用湿布擦拭,但注意不要让产品过度潮湿。
2.2 自动清洗博朗一些高端清洁产品提供了自动清洗功能,例如电动牙刷和电动剃须刀等。
这些产品通常配备有清洗充电器或底座。
以下是一个通用的自动清洗方法:1. 断开产品与电源的连接,确保安全;2. 确保底座或清洗充电器上已添加适量的清洗液;3. 将产品插入底座或清洗充电器中;4. 启动自动清洗程序,按照产品说明书中的指引进行;5. 清洗完成后,将产品取出并用清水冲洗干净;6. 彻底晾干后可重新安装。
3. 安装方法博朗的清洁产品通常需要安装和拆卸,以确保其正常运行和清洗。
下面以博朗电动牙刷为例,介绍一个通用的安装方法:1. 打开牙刷包装盒,取出牙刷主体和刷头,确保所有部件齐全;2. 将刷头与牙刷主体对准插头位置,插入并稍微转动一下,确保牢固连接;3. 将牙刷插入充电器或底座,连接电源;4. 充电器或底座会显示充电状态,等待充电完成;5. 充电完成后,即可拔出充电器或底座,准备使用。
请注意,安装方法可能因产品型号和种类的不同而有所差异。
博朗自动清洁中心使用说明书

博朗自动清洁中心使用说明书一、产品介绍二、使用准备1.确保清洁中心处于平稳的地面上,并且周围没有障碍物。
2.将清洁中心插入电源插座,并确保供电正常。
3.打开清洁中心的开关,等待设备启动。
三、清洁模式选择清洁中心提供多种清洁模式,以满足不同环境的需求。
用户可以根据自己的需要选择适合的清洁模式。
1.自动清洁模式:清洁中心将自动感应并清洁地面,根据地面情况自动调整清洁力度和清洁路径。
2.手动清洁模式:用户可以通过遥控器控制清洁中心的运动,自由选择清洁路径和清洁力度。
3.定时清洁模式:用户可以设置清洁中心的定时清洁功能,在指定的时间自动开启清洁工作。
四、操作指南1.自动清洁模式:a.确保地面上没有障碍物,否则清洁中心将自动绕过。
b.清洁中心将自动感应并清洁地面,清洁路径会根据地面情况自动调整。
c.清洁中心将在清洁完成后自动返回充电座,进行充电。
2.手动清洁模式:a.使用遥控器控制清洁中心的运动,可以选择清洁路径和清洁力度。
b.清洁中心将按照遥控器的指令进行清洁,直到用户停止或清洁完成。
3.定时清洁模式:a.在清洁中心上设置定时清洁功能,指定清洁的时间。
b.清洁中心将在指定的时间自动开启清洁工作,直到清洁完成或用户手动停止。
五、注意事项1.在使用清洁中心前,确保地面上没有杂物和障碍物,以免影响清洁效果和设备运行。
2.在清洁中心工作时,禁止将手或其他物体伸入设备内部,以免发生意外伤害。
3.长时间使用清洁中心后,应及时清理设备内部的垃圾和杂物,以保证设备的正常运行。
4.当清洁中心的电量低于20%时,设备会自动返回充电座进行充电,用户不需要手动操作。
5.清洁中心的滤芯需要定期更换,以保证空气净化效果。
请参考滤芯更换说明进行操作。
六、保养与维修1.清洁中心的外壳可以使用湿布进行擦拭,但不可浸泡在水中清洗。
2.清洁中心的滤芯需要定期更换,以保证空气净化效果。
请参考滤芯更换说明进行操作。
七、常见问题解答1.清洁中心清洁效果不佳怎么办?2.清洁中心工作时发出异常噪音怎么办?3.清洁中心无法充电怎么办?4.清洁中心遇到障碍物无法绕过怎么办?八、售后服务以上就是博朗自动清洁中心的使用说明书,希望能够帮助您正确使用和保养清洁中心,提供一个清洁舒适的生活环境。
博朗,说明书
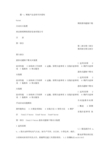
篇一:博朗产品说明书全系列buran博朗系列超细干粉自动灭火装置南京燕苑博朗消防设备有限公司目录第一部分第二部分第三部分第四部分第五部分第六部分悬挂式超细干粉灭火装置1 适用范围2 技术性能3 结构和工作原理4 运输、保管注意事项5 安装注意事项6 维护注意事项7 装箱单8 售后服务悬挂式超细干粉灭火装置1 适用范围2 技术性能3 结构和工作原理4 运输、保管注意事项5 安装注意事项6 维护注意事项7 装箱单8 售后服务悬挂式超细干粉灭火装置1 适用范围2 技术性能3 结构和工作原理4 运输、保管注意事项5 安装注意事项6 维护注意事项7 装箱单8 售后服务自动温感启动器手动启动功能模块1 概述2 探测器性能特点3 主要技术指标4 安装方法5 使用方法6 维护安装注意事项备注 fzxa2.5-buran fzxa5-buran fzxa8-buran第一部分 fzxa2.5-buran悬挂式超细干粉灭火装置1 适用范围1.1 能迅速扑灭a、b、c类火灾和带电电气火灾。
如生产车间、办公室、小型仓库、商店、配电房等层高比较小的相对封闭空间及火车、船舶等交通工具消防使用。
1.2 防爆标志exibiibt32 技术性能2.1 外形尺寸(含固定架;mm)直径 ??????????????200±5高度??????????????375±52.2 灭火装置重量(kg)?????????????????????6.0±0.5 2.3 灭火超细干粉重量(kg)???????????????????2.5±0.125 2.4保护面积、体积(不密闭程度5%)2.5自动温感启动器启动温度(℃)???????????????? ≥70 2.6启动电流(a)????????????????????????≥1 2.7 检查电启动的安全电流(ma)????????????????≤150 2.8 喷射时间(秒)????????????????????????≤5 2.9 灭火时间(秒)???????????????????????≤1 2.10 使用环境温度(℃)?????????????????? -40~+50 2.11 装置启动有效期(年)?????????????????????10 2.12 可人控电启动或与火灾自动报警系统配套使用。
清洗机使用说明书(最终版)_pdf
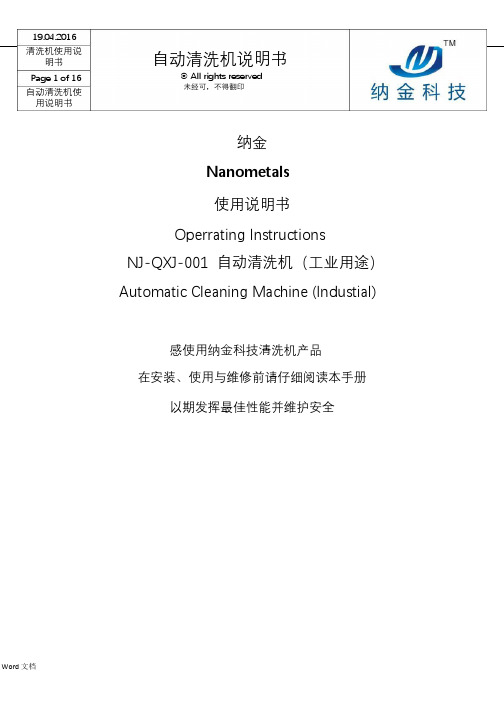
清洗机使用说明书 自动清洗机说明书All rights reserved未经可,不得翻印Page 1 of 16 自动清洗机使 用说明书纳金 Nanometals 使用说明书 Operrating InstructionsNJ-QXJ-001 自动清洗机(工业用途) Automatic Cleaning Machine (Industial)感使用纳金科技清洗机产品 在安装、使用与维修前请仔细阅读本手册以期发挥最佳性能并维护安全All rights reserved未经可,不得翻印Page 2 of 16 自动清洗机使 用说明书目录●安全注意事项 ●重要信息●清洗机主要规格参数 ●零部件名称和附图说明 ●显示屏附图说明及含义 ∙主界面 ∙手动画面 ∙参数设置 ●使用步骤 ∙触膜屏的设置 ∙锥形瓶的固定 ∙启动程序 ∙其他面 ●维护及保养All rights reserved未经可,不得翻印Page 3 of 16 自动清洗机使 用说明书安全注意事项●启动机器前,必须穿实验服,戴手套,带口罩,带上护目眼镜 (否则可能会导致轻微中毒,灼伤皮肤和眼睛) ●禁止将头伸入,通风橱里的机器中,以免发生意外 (否则可能会导致轻微中毒,或者头部会被夹伤) ●启动机器前,必须将通风橱的开关打开(否则可能会导致有害气体不能够及时排出,人体接触会轻微 腐蚀和中毒)●请把放锥形瓶的槽格都装满,装满后务必把固定盖板合上 (否则可能会导致部分强酸强碱,溅出水槽以外,腐蚀部分零 件,机器寿命变短)●禁不戴手套直接用手触碰固定盖板 (否则可能会导致触碰的部位被轻微腐蚀) ●在机器运行时禁将通风橱中的开关断开(否则可能会导致清洗中的有害气体不能及时排出实验室外) ●在机器运行时,出现紧急情况,立即断开电源 (否则可能会导致冒烟、起火、触电或腐蚀)All rights reserved未经可,不得翻印Page 4 of 16 自动清洗机使 用说明书若工作中出现以下异常或故障 ∙喷头结构没有正常的上或下移动 ∙长形喷头没有正常的喷出液体 ∙旋转放置机构没有正常的左右翻转 ∙排液时电磁阀没有按照设定次序打开排液管 ∙电磁阀出现异常,不能止水或同时打开 ∙光电感应器异常亮起 ∙存在其他异常情况或故障请立即按掉显示屏上的“停止”开关,上述任一情况若依 然存在异常则立即按掉总电源,并与客户咨询服务中心联系进 行检查和修理。
博朗7855s说明书

博朗7855s说明书随着科技的发展,现代家庭使用电器的种类越来越多,博朗7855s无疑是其中之一。
博朗7855s 是一款烫衣板,自带蒸汽熨斗,为家庭生活带来了很大方便。
下面我们来看看博朗7855s 的说明书。
一、外观及功能简介博朗7855s 的主体部分为烫衣板,可以自由调整高度,适合使用者的身高。
它还有一个带有水箱的蒸汽熨斗,可以自动控制温度和蒸汽量,熨斗底部有多个蒸汽孔,可以有效地熨平不同材质的衣物。
二、使用前准备在使用之前,需要先准备好博朗7855s,取下蒸汽熨斗的水箱盖,将其置于水龙头下,用自来水加满水。
放回水箱盖,并将它插入蒸汽熨斗上方的连接器中。
接下来插电,开关熨衣机电源。
打开熨斗上的开关,等待几分钟,熨铁就可以使用了。
三、使用步骤在使用之前,需要先将冷烫板预热1-2分钟。
1. 调整高度:根据个人身高和熨衣物的位置,将烫衣板的高度调整到最合适的位置。
2. 烫衣物:在准备好要熨烫的衣服之后,将其平放在烫衣板上。
用烙铁上的熨斗对其进行熨烫。
熨斗的温度和蒸汽量可以通过按钮进行调节。
3. 熨烫衬衫领口:将衬衫的领口平放于烫衣板上,将控制面板上的转盘旋转到相应的领子设置,将熨斗按下,在烫板前部按下“额外蒸汽”按钮,并使用蒸汽熨斗来蒸烫衣领口。
四、注意事项1. 在使用博朗7855s 的时候,要避免从水箱上沾水,注意保持安全距离。
2. 当熨铁上的水不足时,熨斗会停止工作并发出一个声音。
此时需要先关掉熨斗的电源,然后等待熨铁冷却,才能填充水箱。
3. 当不使用博朗7855s 时,请拔掉电源插头并关闭水箱盖。
以上便是关于博朗7855s 的说明书,通过了解这些基本信息,我们可以更好地使用熨烫机。
它带来的便利在家庭中无疑是不可或缺的。
如果你还没有尝试过这款产品,建议你去体验一下它带来的方便和快捷。
祝你生活愉快!。
4520详细说明书

第一页:博朗耳温枪4520 型号6022 Thermscan耳温枪4020 型号6023 Made in Germany: 德国制造输入/输出按钮记忆按钮Braun Kronberg: 博朗科隆堡第二页:英语 4 GB 博朗热线: 0800 783 70 10 网址:www: 制造商:德国科隆堡,法兰克福特大街145号,博朗有限责任公司。
邮编:61476德国印刷,英国/韩国6-022-435/00/VⅢ-06第三页:耳温枪4520 耳温枪4020第四页:英语博朗Thermscan温度计研发精致,能精确、安全、快速地测量耳内温度。
外观设计避免了迅速插入耳道而损坏耳膜。
如同任一款温度计,切当的技术关切到测取准确的温度,所以请仔细通读使用说明书。
注意:此温度计适用于气温-10-40℃(50-104华氏°F)中。
切勿暴露于极限温度(<﹣20℃/﹣4°F或>50℃/122°F)切勿过湿(>95%RH)此产品只使用原配博朗Thermscan滤光镜(LF40)。
未装新的、洁净的滤光镜,切勿使用。
滤光镜放置于儿童触及不到之处。
此产品仅用于家用。
此产品不可替代保健产品。
工作原理:博朗Thermscan温度计测量耳膜和周边组织辐射出的红外热度。
为避免总温差,感应器温度与人体体温相近。
产品放入耳内后能持续监测红外辐射。
监测结束便显示精确结果。
测耳原因:该温度计旨在测量重要器官的体温节律。
因耳膜贯通大脑中下丘脑温度控制中心的血液供应,所以耳温精确反映体温节律,耳温测量更准确即时地反应体温变化,胜于其他器官。
腋下温度计指测量皮肤温度,不能有效反应体温节律;口腔温度计会受饮食、呼吸影响;直肠温度计滞后于体温节律,且又交叉感染的风险。
第五页:体温节律正常体温有个范围。
下表显示正常范围也受体位影响。
所以,不同体位的数值不可直接比较。
不同体位的数值:腋下: 34.7 – 37.3 °C 94.5 – 99.1 °F口腔: 35.5 – 37.5 °C 95.9 – 99.5 °F直肠: 36.6 – 38.0 °C 97.9 – 100.4 °F热扫描摄影机: 35.8 – 38.0 °C 96.4 – 100.4 °F同样,正常体温会随年龄而变。
BRAUN布朗说明书

Post Office Box 29, Mount Holly, N.C. 28120 USA Phone (704) 822-2993 Fax (704) 822-1292E-mail: BRAUNINST @ Post O Ph E-ffice Box 1106, D71301 Waiblingenone (+49) 07151/956230 Fax (+49) 07151/956250 mail: info @ braun-tacho.de ernet: www.braun-tacho.deIntManualE16A323 (with RS232-Interface, Board Mounting) E16E323 (with RS232-Interface, 19" Rack)E16A324 (with Profibus-Interface, Board Mounting) E16E324 (with Profibus-Interface, 19" Rack)Turbine Overspeed Protection Systemwith SIL3/IEC61508 ApprovalGenerator E1696.31 Monitor E1655.41Monitor E1655.41 Monitor E1655.41Note: Shown is model E16E323Contents page Characteristics (3)FunctionStructure (3)SystemSpeed Sensors (3)Electronics (3)SystemMonitor E1655 (4)Test Generator E1696 (4)Alarms provided by the system (4)Alarms (4)TripOverspeedWarning Alarms (4)ChannelSystem Failure Alarms (4)Modules (5)E1655Overspeed Setpoint (SP1) (5)Sensor Failure Monitor (5)Sensor Pulse Train Comparison (5)Low Speed Check (SP2) (5)External Trip Input (6)Input (6)SignalSensorSensor Signal Repeater (6)Testing (7)E1696 Generator (7)Automatic test routine (7)function (8)WatchdogFailure signals (8)Display and Keys of E1696 (9)Error-Messages of E1696 (10)Display and Keys of E1655 (11)Error-Messages of E1655 (11)Programming of the modules (12)parameters (12)toAccessListing of E1655 (13)ParameterParameters of E1655 (14)Listing of E1696 (19)ParameterParameters of E1696 (19)Function Diagram (24)Diagram (25)WiringRear View of 19"Rack (E-Version) (26)ElectricalSpecifications (27)Dimensions of E-Version (19" Rack) (28)A-Version (Board Mounting) (30)DimensionsofSummary of Versions and Spare Part Recommendation (31)Function CharacteristicsTurbine Speed Monitoring against overspeed with redundancy by 3 independent channels with trip relay outputs 1 each per channel.Function Test Facility with discrete selection by external signals, or automatic test routine with watchdog and system failure warning. 3 channel structure with independent monitoring modulesoptions for externally controlled test or automatic test routineEach channel has its own comprehensive measurement and alarm section,realized by a Monitor Module in each channel. Measurement is based on thefast responding digital pulse interval principle with automatic floating numberof periods. Inputs include sensor monitoring. Each of the three MonitorModules ends up to an alarm outputs (breaking overspeed trip circuit). Anyfailure of sensor or measuring function detected also sets the trip output of themonitor to overspeed position. Further, each channel releases its own failurewarning signal, free available to the periphery as N/O contact.The overall response to an overspeed condition is shorter than 15 millisec(plus 1 pulse interval of the input pulse train).fast response to overspeedEach module within the system has its own data port at the front, usable forthe configuration of the module, and also for data calling. Available as RS232(standard) or as PROFIBUS DP Interface.Data interface facilitySystem Structure(see also function diagram)Speed Sensors3 Hall-Effect based speed sensors series A5S... are placed at the turbine shaftfor a non-contact sensing of its rotational speed. Milled slots in the shaft, or apole wheel, form a profile to generate a pulse frequency corresponding to thespeed. The sensors have an incorporated signal amplifier providing anadequate signal level for the transmission to the E16 Electronics.Non-contact speed sensingSystem ElectronicsThe E16 Electronics includes 3 Monitor Modules E1655, one each for each channel A, B, C. Further, 1 Test Generator Module E1696.They are plugged into a card file, which is ready wired to perform the monitoring function. Terminal strips connect to the periphery. The System and its ModulesMonitor E1655This module provides:Sensor circuit monitoring and sensor signal lead monitoring, sensors pulse train comparison.Sensor signal repeating output.Digital speed measurement with display in RPM terms.Overspeed trip setpoint (SP1) 2 alarm signal outputs,also offering the facility of an external alarm control.Low end setpoint (SP2) to perform the plausibility check,with starter facility.“channel warning alarm” relay output"sensor failure alarm" relay output.All functions are digital, with 5 digits resolution and accuracy of+ 0.01% + 1 in the last digit.Parameters are programmable from the front keys (with access lock), or via data interface.Functions included into the Monitor module E1655. Detailed description on following pagesTest Generator E1696This module provides:Adjustable frequency generator to substitute the sensor signal under test condition, with display in RPM terms.Channel test selection by external control, or automatic test cycle with “System Failure” outputs. Functions included into the Test Module E1696Detailed Description on following pagesAlarms provided by the System Overspeed Trip AlarmsThe trip alarm of the monitor module E1655 within each channel will be released under one or more of these conditions:1.overspeed setpoint (SP1) exceeded,2.sensor failure detected (supply and signal lead monitor),3.sensor signal voltage failure detected (only at zero speed)4.sensor pulse train discrepancy detected,5.low end setpoint (SP2) not exceeded after starter phase,6.external alarm control actuated7.self test failure conditions for channel trip alarmChannel warning alarmThis signal contact, available from each channel to the periphery, breaks under one or more of these conditions:1.overspeed setpoint (SP1) exceeded (if programmed).2.external trip control actuated,3.low end setpoint (SP2) not exceeded after starter phase4.sensor pulse train discrepancy detected5.self test failure of a neighbor channel. conditions for channel warning alarmSensor failure alarmThis signal contact, available from each channel to the periphery, breaks under one or more of these conditions:1.sensor failure detected (supply and signal lead monitor),2.sensor signal level failure detected. conditions for sensor failure alarmSystem Failure warningsThe System Failure Alarms 1 and 2 , available as (N/O) contact will be signalized if one of the channels does not duly respond to the test procedure. see section Automatic Test Cycle for details of System failure warningsThe E1655 ModulesAlarms and Checks performedOverspeed Setpoint (SP1)The overspeed setpoint SP1 can be programmed to any speed level, in terms of RPM. Its setting can be called to display. Further programmable are the hysteresis width, and the event memory. If not memorized, the signal returns to “no excess” with the measurement decreasing below setpoint (minus hysteresis), otherwise it must be cancelled by an external acknowledge signal.details of the overspeed alarm (SP1)Sensor Failure MonitorThis function includes 2 sections, the sensor supply monitor and the sensor signal lead monitor. Both have certain preconditions, as explained below. They are met by all BRAUN sensors of series A5S... with push/pull output stage, possibly not by others. Check the sensor data sheet for validity. If not applicable, disengage the function.The supply monitor checks the current drain, and the voltage of the sensor supply lead. Thereby it detects a break as well as a short circuit in the sensor connection. Obviously, this requires a sensor with adequate power consumption (>7ma).The sensor signal lead monitor checks the level of this input to be either definitely on high or on low level, as a push/pull output is, if not broken. As primarily intended to monitor the signal lead in standstill state, the function automatically disengages when the sensor supplies a signal frequency. A failure thus detected will be memorized or not, as programmed.Sensor Failure Monitor Sensor Pulse Train ComparisonThis function checks for proper sensor signals during run of the machine. Each monitor Module E1655 compares the pulse train delivered from its own sensor to those of its both neighbor channels. If they differ, the monitor finds its own sensor to be faulty. This checks performs at any frequency, and does not depend on a speed measurement.Active sensor signal checkLow Speed Check (SP2)If the speed measurement drops below the (programmable) setpoint SP2 of the Monitor Module during operation, from whatever reason, a failure will be signalized. A very comprehensive check, including sensor and measurement function.The level SP2 will be set at the low speed end, to 30 % for instance. For start-up, it will be overrun by the starter function of the E1655 module, activated by an auxiliary contact from the machine control, and held for a programmable period of time (0...999 sec) after its end.This alarm is programmable to be memorized or not, or to be disengaged.Low speed alarm checks for full performanceDisplayThe numerical display of the E1655 module serves as a programming aid (if not programmed by the data interface), indicating the program group number, the step number, and the parameter addressed.When not in the programming phase, the display reads the actually measured speed, in terms of RPM or any other desired unit (also during the test phase). By pushbuttons, the setpoints SP1 and SP2 can be called (but not modified that way).By red and green LEDs, the module indicates its alarm conditions for SP1 and SP2.External Trip InputIn addition to the alarm and failure conditions as described before, the trip alarm may also be released by an external binary signal. This feature allows to include a condition from outside the speed monitor into the trip release, maybe a temperature signal, or a pressure contact. The high/low level for the response of this control input is adjustable. Trip release by external signalSensor Signal InputThe input accepts and feeds preferably 3-leads sensors, as BRAUN sensorseries A5S.. with p/p output. Others may give restrictions, in frequency range,transmission distance, and the safety checks that can be performed.By a control signal from the Test Generator Module, the monitor input isswitched to a second input, which receives the test frequency as emitted fromthe Test Generator.Sensor signal inputSensor Signal RepeaterThis isolated output repeats the signal as received from the sensor to the periphery. Feeds for instance a speed controller, or external display. The output is firmly tied to the sensor signal of the specific channel, not affected when the monitor is switched to the test frequency. Isolated sensor signal repetitionTesting with E1696 Test Generator Module Externally controlled test procedureThe E1696 provides a test frequency to be switched to the channels A, B, C of the system, one after the other, by means of external (DC) control signals. This frequency can be set (in terms of RPM) at the test generator, and then tuned up and down by pushbutton. The front display reads the actual frequency.3 control inputs to the system are assigned to the 3 channels A,B,C. The one input held high switches its channel to test, substituting the sensor signal by the frequency of the test generator. Note: the repeater output of the module remains with the sensor input, not affected by the test procedure. The control inputs are locked against each other, to prevent of inadvertently switching 2 or 3 channel to test at the same time (this protection can be disengaged by program).The channel under test reads the test frequency as received and measured at its numerical display (by RPM). If it exceeds its setpoint, it will signalize o-verspeed by its alarm relay and LED display.A contact set of an external voter must signalize the correct response to the test generator. externally controlled test proceduresystem reaction to externally controlled testAutomatic Test RoutineThe Test Module repeats the automatic test routine with an adjustable time interval (1 ... 9 999 min).The test routine itself is performed in three steps. With each step, the three monitors are tested subsequently.Step one:Simulated test speed 1 (n >SP1, feedback of tested channel must be trip), Step two:Simulated test speed 2 (n <SP1, feedback of tested channel must be no trip), Step three:Forced trip (n <SP1, feedback of tested channel must be trip).During step three, the monitor receives test speed 2.If measurement and alarming serve duly, the Monitor Module under test must release its trip alarm with step 1 at simulated test speed 1, but must not with step 2 at simulated test speed 2.With step 3 the forced trip input of the monitor is tested. At step 3 each monitor is switched to simulated test speed 2 (below overspeed) but the tested channel must feed back the trip signal.The Test Module checks for a corresponding response. It is returned from a contact set of an external device (magnetic valve).With an incorrect response from a channel, the routine immediately interrupts (to prevent the entire system of an unfounded overspeed trip alarm to the machine) and a system failure signal is released.The Test Module throws the faulty channel into its overspeed condition (by means of the forced trip input). Thus, the overspeed safety is maintained – the system now responds with a 1 of 2 characteristics, in other words, if just one other channel detects overspeed or an internal fault, the turbine will be shut down. regularly performed automatic test routine: checking the response of all channels to 2 test frequencies safety maintained after failure in one channelWatchdog FunctionThe watchdog section on the E1696 module performs an identical test step sequence, independent from the above but in close synchronism. If both, test routine and watchdog are not at the same step at the same moment, system failure is signalized. But more, the above mentioned measure of forcing a faulty channel to its overspeed condition also requires the said coincidence between routine cycle and watch dog. In other words, the measure is taken only if the stepping sequence up to this moment was correct. This prevents the system from an unfounded overspeed alarming, and thus further increases the reliability, and the availability of the machine.Incorrect stepping however generates a warning, by the System Failure alarm output, which should immediately be observed. watchdog checks for correct stepping sequenceand crosschecks trip signalsFailure signals to the peripheryThe Test Generator Module E1696 provides failure signals (1) and (2), as N/O relay contacts, de-energized to announce a failure, also with power supply missing.Both respond to an alarm from one or more of the channels A, B, C, and to a failure detected in the testing sequence, or to an incorrect performance of one of the Monitor Modules during test. system failure signals from test and watchdog sectionDisplay and Keys of E1696During auto test sequenceGenerator E1696LED2: flashing = channel B is testedOn = channel B signalizes tripLED3: flashing = channel C is testedchannel C signalizes tripLED4: On = Auto-Test-Mode activeOff = Manual-Test-Mode activeIn normal operation the display reads:With key the value of test speed 1,with key the value of test speed 2.With keys and depressed : the remaining time (XXXX.X minutes) until the next auto test sequence is started Start of an auto test sequenceAn auto test sequence can be manually started by depressing keys and .Reset of latched alarms with key .Display (error) messages refer to next page.Error-messages of test generator E1696During normal operation:C0-E1 : channel A signalizes trip, B and C notC0-E2 : channel B signalizes trip, A and C notC0-E3 : channel A and B signalize trip, C notC0-E4 : channel C signalizes trip, A and B notC0-E5 : channel A and C signalize trip, B notC0-E6 : channel B and C signalize trip, A notDuring an auto-test-sequence:C1-E1 : incorrect feedback of channel A at simulated test speed 1 C2-E1 : incorrect feedback of channel B at simulated test speed 1 C3-E1 : incorrect feedback of channel C at simulated test speed 1 C1-E2 : incorrect feedback of channel A at simulated test speed 2 C2-E2 : incorrect feedback of channel B at simulated test speed 2 C3-E2 : incorrect feedback of channel C at simulated test speed 2 C1-E3 : incorrect feedback of channel A at test of forced tripC2-E3 : incorrect feedback of channel B at test of forced tripC3-E3 : incorrect feedback of channel C at test of forced tripC9-E1 : channel A not ready for testC9-E2 : channel B not ready for testC9-E3 : channel A and B not ready for testC9-E4 : channel C not ready for testC9-E5 : channel A and C not ready for testC9-E6 : channel B and C not ready for testC9-E7 : channel A, B and C not ready for test Error-Messages from E1696 (C = Check, E = Error)Other display-messagesFC-1 : test of forced tripSELF : E1696 performs a self test routine (subsequent to each auto testsequence)FC = Function CheckDisplay and keys of E1655Monitor E1655In normal operation the display readsWith key the value of SP1,with key the value of SP2.Error messages(SE = Selftest-Error, CE = Check-Error)SE-01: sensor supply failure or sensor lead failure,SE-02: pulse train difference,SE-03: SE-01 and SE-02 simultaneously,SE-04: low end failure,SE-05: SE-01 and SE-04 simultaneously,SE-06: SE-02 and SE-04 simultaneously,SE-07: SE-01, SE-02 and SE-04 simultaneously.SE-10 : test speed of generator = zero (= failure of test generator)ortest time exceeds 10 minutes (= failure of test generator)orneighbourchannelsignalizes permanent self test (= failure of neighbor channel)SE-20 : neighbour channel fails to produce self test within 5 hours time of operation (= failure of neighbor channel) CE-1 : monitor switched to forced trip by E1696Reset of latched alarms with keys and .Other display-messages :(FC = Function Check)FC-1 : test of forced trip by E1696FC-2 : external trip control actuatedSELF : self test of monitor (periodically repeated after each 2 hours)Programming of the modulesAccess to parametersPrinciple: Select a Parameter by it's "Name" Pgg.ss,where gg = Parameter- Group-No. andss = Step-No. within Group,then verify the value and change it according the application Programming:To enter the programming phase, press both keys and simultaneously; insteadof normal display, P00.00 will be shown.Select group- or. step-no. with keys , .Toggle between group- and step-range with key .Show parameter's value with key .Select (move ) active digit with key .Adjust figure in active digit with keys , .Acknowledge with key , Cancel (old value still valid) with key .Return to normal operation with keyExample: change value of parameter P01.01 from 2386 to 2387 or 2385:Enter = new, changed value is validParameter listing of Monitors E1655:Summary of programming steps and their initial parameters (default values) as set on deliveryprogram- data set on delivery Step No. parameter function (initial data)P00 .00 access code request 0000 .01 new code figure 0000.02 lock status (1 = unlocked, 0 = locked) 1 = unlockedP01 .00 input: scaling decimals of input signal frequency 0 = none .01 value of nominal input frequency (Hz) 10000.02 decimals of corresponding speed 0 = none.03 corresponding speed (unit as desired) 10000.04 low end of speed range 00001P02 .00 zeroed LSDs in display 0 = none .01 display updating sequence (X.X sec) 0.3 (sec).02 time elapse of starter phase (XXX sec) 000 (sec).03 truth-level of external trip signal (0 = low, 1 = high) 1 = high.04 sensor monitoring (0=off,1=on,2=on,latched) 1 = on.05 mode of sensor monitoring (0=none,1=current,2=voltage,3=both) 1 = current.06 lowspeed monitoring (0=off,1=on,2=on,latched) 1 = on.07 sensor signal deviation monitoring (0=off,1=on) 0 = off.08 reset interval of deviation counters (1....9999 pulses) 1000.09 allowable deviation between counters (0...99 pulses) 50.10 limit of error counter (1...99 deviation detections) 5.11 warning alarm at overspeed (0=no,1=yes,2=yes and at test overspeed) 1 = yesP03 .00 setpoint (SP1) in unit as programmed for display 10000 .01 hysteresis bandwidth SP1 (XX.X % of SP1) 05.0 (%).02 alarm to be latched (0=no, 1=yes) 0 = noP04 .00 setpoint (SP2) in unit as programmed for display 00100 .01 hysteresis bandwidth SP2 (XX.X % of SP2) 05.0 (%).02 alarm to be latched (0=no, 1=yes) 0 = noP05 .00 hardware address added to device address (0=no,1=yes) 0 = no .01 device address (range 1...125) 001Parameter Group P00.xx of E1655:Data Access, PasswordKey figure to accessProgramming access to all parameters can be locked by a password number.If not properly served, the parameters may be called to display but not varied. If not properly served, the display reads -E1-,and any programming in a later program step will be rejected.Note:If the knowledge of the password number went lost it may be recalled to display by a procedure, as described in a separate sheet K0-095 (not included into these instructions). The code figure then appears by 4 digits.In a subsequent program step, a new code may be established, substituting the one previously valid.The key function may be disengaged by a next program step. With authorized access, set parameter to 1 in step No .02, to generally unlock the key. This may prove practical during the installation phase to facilitate the adjustments. Once installed, the key function should be reactivated, by programming parameter 0 in this step. Step P00.00:Code figure to access Step P00.01:new code figure Step P00.02: unlock access keyParameter Group P01.xx of E1655: Measurement Configuration, Scaling I nputScaling defines the relation between the input signal frequency (in terms of Hz), and the corresponding display (in terms of RPM). Both values are freely programmable by their decimals and numerical amount. Of course, they must refer to the same operation level. This reference point is recommended close to the high end of the intended operation range. In later operation however, it may be overrun without error.Scaling ExampleThe speed is measured by a contactless probe scanning a gear wheel on the turbine shaft with 90 teeth.Thus, a speed of 3000 rpm results in a signal frequency of 3000x90:60 (Hz) = 4500 (Hz). With this as the reference level, the following parameters are to be set:Step P01.00 parameter 0 (= no decimals)P01.01 parameter 04500P01.02 parameter 0 (= no decimals)P01.03 parameter 03000 scaling inputsignal frequency (Hz):Step P01.00 =number of decimals,Step P01.01= value. corresponding value of rpm: Step P01.02 =number of decimals,Step P01.03 = valueLow end for shut-offIf the speed falls lower than this level, the measurement will be cancelled to zero.The low end is programmed by the same terms, as defined for the speed by steps P01.02 and P01.03. Step P01.04 low end of operating rangeParameter Group P02.xx of E1655: Display, Starter time, Failure Monitoring LSDs on zeroIf the display of the speed uses 4 or more digits, for application reasons, the lesser significant digits (LSD) may appear fluctuating. To avoid irritations by not significant digits, a number of them may be permanently kept at zero. Set the parameter to the number of LSDs to be kept on zero. Step P02.00: zeroing LSDsDisplay updating sequenceIndependent from the response time used for other functions, the display may have its own up-dating sequence - again in the interest of stabilized and well legible readings. Set the parameter to the time in steps of 0.1 sec.A recommended value is 0.3 sec. Step P02.01: display updatingStarter time periodThis step sets the starter time period (elapse). Starter phase state for SP2 lasts from the beginning of the external starter signal plus the programmed time elapse following its end. Range 000...999 sec. StepP02.02:starter time elapseTruth level of External Trip SignalTo match the control source, and specific safety aspects, the parameter of this step defines either high or low signal level to make the condition true. StepP02.03:Truth level ofExternal Trip Signalparameter0 : high = control true1 : low = control trueEnable/Disable of sensor failure detectionSensors without power supply (for example inductive sensors) cannot be monitored against failure.If the sensor is monitored, it is possible to latch a failure alarm until it is reset. StepP02.04:Monitoring of sensorparameter0 : off1 : on, alarm not latched2 : on, alarm latchedMode of sensor monitoringThe sensor can be monitored versus current drain (alarm if current drops below 7 mamps or exceeds 150 mamps) and/or signal voltage level during zerospeed of the turbine.Note:Signal voltage level monitoring only possible with BRAUN sensors with incorporated push/pull output (series A5S...). StepP02.05:Mode of sensor monitoringparameter0 : no monitoring1 : current monitoring2 : voltage monitoring3 : current and voltageLowspeed monitoring (n < SP2)The lowspeed monitoring can be switched off. If the lowspeed monitoring is enabled, the speed of the turbine must exceed SP2 (after starter time has elapsed). StepP02.06:lowspeed monitoringparameter0 : off1 : on, alarm not latched2 : on, alarm latchedSensor Pulse Train ComparisonPurpose of this function:•Detection of a faulty position of the sensor (cleareance to big or wrong angular position) during starter phase of the turbine (n<SP2). •Deviation detection of the sensor signals during normal operation of the turbine (n>SP2).Function principle:The pulses of all three sensors are counted in each monitor. The main sensor of the monitor is detected as faulty if the main counter deviates from both neighbour counters. The allowable deviation between the counters is adjustable.The counters are periodically reset after an adjustable number of pulses or if a fault is detected.Subsequent counter evaluations that indicate a faulty sensor increase an error counter. This counter is reset by an evaluation that indicates a proper working sensor. If the error counter exceeds an adjustable limit, the alarm is released.Programming steps for deviation monitoring:Step P02.07 : monitoring on/offStep P02.08 : number of pulses for periodically reset of counters(range from 1 to 9999 pulses)Step P02.09 : allowable deviation between counters (range 1 to 99 pulses) Step P02.10 : limit of error counter(range from 1 to 99)Example:P02.07 set to 1 (monitoring on)P02.08 set to 1000 (counters will be reset after 1000 pulses, of any sensor)P02.09 set to 50 (allowable deviation of 50 pulses within 1000 pulses)P02.10 set to 5 (5 subsequent error detections until alarm is released)With above settings a non operational main sensor will be detected after 250 pulses of the other two sensors (5 error detections after 50 pulses). StepP02.07:sensor pulse train comparisonon/offparameter0 : off1 : onStep P02.08:number of pulses for reset ofpulse countersrange 0001 to 9999 pulsesStep P02.09:allowable deviation betweencounters until error counter isincreasedrange 01 to 99 pulsesStep P02.10:limit of error counter until alarmis releasedrange 01 to 99Warning alarm at overspeed conditionIt can be programmed whether the warning alarm will be released at a real overspeed condition or additionally at a test overspeed condition. StepP02.11:warning alarm at overspeedparameter0 : no1 : yes, only at real overspeed2 : yes, at real and test over-speed。
- 1、下载文档前请自行甄别文档内容的完整性,平台不提供额外的编辑、内容补充、找答案等附加服务。
- 2、"仅部分预览"的文档,不可在线预览部分如存在完整性等问题,可反馈申请退款(可完整预览的文档不适用该条件!)。
- 3、如文档侵犯您的权益,请联系客服反馈,我们会尽快为您处理(人工客服工作时间:9:00-18:30)。
博朗清洗中心说明书
博朗清洗中心是一种全新的清洗方式,适用于各种材质的衣物和家居用品。
本说明书将详细介绍博朗清洗中心的使用方法、注意事项和保养方式,以确保您能够正确地使用和保护这一清洗设备。
一、使用方法
1.准备工作
在使用博朗清洗中心前,需要准备以下物品:衣物、家居用品、洗涤剂、水。
其中,洗涤剂的种类根据不同的清洗需求选择,可以是普通的洗衣粉、液体洗衣剂、衣物柔软剂等。
2.操作步骤
(1)将衣物或家居用品放入清洗中心的清洗筐中。
(2)根据清洗需求,添加适量的洗涤剂和清水。
(3)按下清洗键,开始清洗。
清洗中心会自动进行清洗和漂洗,整个过程不需要人工干预。
(4)清洗完成后,取出衣物或家居用品,进行晾干或烘干即可。
二、注意事项
1.使用前仔细阅读说明书,并按照要求正确操作。
2.不要在清洗中心中清洗过多的衣物或家居用品,以免影响清洗效果。
3.选择适当的洗涤剂,避免对衣物或家居用品造成损伤。
4.清洗后,及时将清洗筐和水箱中的残留物清理干净,避免积累影响清洗效果。
5.定期对清洗中心进行维护保养,保证其正常使用。
三、保养方式
1.清洗中心的外壳可以用干净的湿布擦拭,避免使用化学清洁剂或粗糙的抹布。
2.清洗筐和水箱需要定期清洗,避免积累影响清洗效果。
3.清洗中心需要定期进行维护保养,如更换滤网、清理电机等。
4.在长时间不使用时,需要将清洗中心的电源拔出,并将其存放在干燥通风的地方。
博朗清洗中心是一种非常便捷、高效的清洗设备,但在使用过程中需要注意一些事项和保养方式。
希望本说明书能够为使用者提供帮助,让您的清洗工作更加轻松愉快!。