球铁冒口设计的基本原理(精)
铸铁件冒口设计手册

铸铁件冒口设计手册诸葛胜福士科铸造材料(中国)有限公司铸铁冒口设计手册一、概述冒口是一个个储存金属液的空腔。
其主要作用是在铸件成形过程中提供由于体积变化所需要补偿的金属液,以防止在铸件中出现的收缩类型缺陷(如图1和图2所示),而这些需要补偿的体积变化可能有:图1 各种缩孔图2 缩孔生产图a)和冒口的补缩图b)1—一次缩孔 2—二次缩孔 3—缩松 1—缩孔 2—型腔胀大 3—铸件(虚线以内) 4—显微缩松 5—缩陷(缩凹,外缩孔)(1)铸型的胀大(2)金属的液态收缩(3)金属的凝固收缩补偿这些体积变化所需要的金属液量随着铸型和金属种类的不同而异。
此外,冒口还有排气及浮渣和非金属夹杂物的作用。
铸件制成后,冒口部分(残留在铸件上的凸块)将从铸件上除去。
由此,在保证铸件质量要求的前提下,冒口应尽可能的小些,以节省金属液,提高铸件成品率。
由此冒口的补缩效率越高,冒口将越小,铸件成品率越高、越经济。
FOSECO公司的发热保温冒口具有高达35%的补缩效率;因而,具有极高的成品率和极其优越的经济性。
在金属炉料价格飞涨的情况下,其优越性显得尤其突出。
另外,高品质发热保温冒口,及其稳定可靠的产品质量是获得高品质铸件的重要手段和可靠的质量保证。
二、铸铁的特点铸钢和铸铁都是铁碳合金,它们在凝固收缩过程中有共同之处)如凝固前期均析出初生奥氏体树枝晶,都存在着液态、凝固态和固态下的收缩),但也有不同的特点。
其根本不同之处是铸铁在凝固后期有“奥氏体+石墨”的共晶转变,析出石墨而发生体积膨胀,从而可部分地或全部抵消凝固前期所发生的体积收缩,即,具备有“自补缩的能力”。
因此在铸型刚性足够大时,铸铁件可以不设冒口或采用较小的冒口进行补缩。
灰铸铁在共晶转变过程中析出石墨,并在与枝晶间的液体直接接触的尖端优先长大,其石墨长大时所产生的体积膨胀直接作用在晶间液体上,进行“自补缩”。
对于一般低牌号的灰铁铸件,因碳硅含量高,石墨化比较完全,其体积膨胀量足以补偿凝固时的体收缩,故不需要设置冒口,只放排气口。
球墨铸铁的凝固特性和铸件冒口的设置

球墨铸铁的凝固特性和铸件冒口的设置中国铸造协会李传栻一般说来,球墨铸铁件产生缩孔、缩松的倾向比灰铸铁件大得多,防止收缩缺陷往往是工艺设计中十分棘手的问题。
在这方面,从实际生产中总结出来的经验很不一致,各有自己的见解:有人认为应该遵循顺序凝固的原则,在最后凝固的部位放置大冒口,以补充铸件在凝固过程中产生的体积收缩;有人认为球墨铸铁件只需要采用小冒口,有时不用冒口也能生产出健全的铸件。
要在确保铸件质量的条件下最大限度地提高工艺出品率,仅仅依靠控制铸铁的化学成分是不够的,必须在了解球墨铸铁凝固特性的基础上,切实控制铸铁熔炼、球化处理、孕育处理和浇注作业的全过程,而且要有效地控制铸型的刚度。
一、球墨铸铁的凝固特性实际生产中采用的球墨铸铁,大多数都接近共晶成分。
厚壁铸件采用亚共晶成分,薄壁铸件采用过共晶成分,但偏离共晶成分都不远。
共晶成分、过共晶成分的球墨铸铁,共晶凝固时都是先自液相中析出小石墨球。
即使是亚共晶成分的球墨铸铁,由于球化处理和孕育处理后铁液的过冷度增大,也会在远高于平衡共晶转变温度的温度下先析出小石墨球。
第一批小石墨球在1300℃甚至更高的温度下就已形成。
在此后的凝固过程中,随着温度的降低,首批小石墨球有的长大,有的再次溶入铁液,同时也会有新的石墨球析出。
石墨球的析出和长大是在一个很宽的温度范围内进行的。
石墨球长大时,其周围的铁液中碳含量降低,就会在石墨球的周围形成包围石墨球的奥氏体外壳。
奥氏体外壳形成的时间与铸件在铸型中的冷却速率有关:冷却速率高,铁液中的碳来不及扩散均匀,形成奥氏体外壳就较早;冷却速率低,有利于铁液中的碳扩散均匀,奥氏体外壳的形成就较晚。
奥氏体外壳形成以前,石墨球直接与碳含量高的铁液直接接触,铁液中的碳易于向石墨球扩散,使石墨球长大。
奥氏体外壳形成后,铁液中的碳向石墨球的扩散受阻,石墨球的长大速度急剧下降。
由于自铁液中析出石墨时释放的结晶潜热多,约3600 J/g,自铁液中析出奥氏体时释放的结晶潜热少,约200 J/g,在石墨球周围形成奥氏体外壳、石墨球的长大受阻,就会使结晶潜热的释放显著减缓。
冒口系统设计

冒口系统设计一﹑冒口设计1. 冒口设计的基本原则1)冒口的凝固时间应大于或等于铸件(被补缩部分)的凝固时间。
2)冒口应有足够大的体积,以保证有足够的金属液补充铸件的液态收缩和凝固收缩,补缩浇注后型腔扩大的体积。
3)在铸件整个凝固的过程中,冒口与被补缩部位之间的补缩通道应该畅通,即使扩张角始终向着冒口。
对于结晶温度间隔较宽、易于产生分散性缩松的合金铸件,还需要注意将冒口与浇注系统、冷铁、工艺补贴等配合使用,使铸件在较大的温度梯度下,自远离冒口的末端区逐渐向着冒口方向实现明显的顺序凝固2. 冒口设计的基本内容1)冒口的种类和形状(1)冒口的种类⎧⎧⎧⎪⎪⎪⎨⎪⎪⎪⎪⎪⎨⎩⎪⎪⎪⎧⎪⎪⎨⎪⎪⎩⎩⎪⎧⎧⎪⎪⎪⎪⎨⎪⎪⎪⎪⎪⎨⎩⎪⎪⎪⎧⎪⎪⎪⎪⎪⎪⎪⎨⎨⎪⎪⎪⎪⎪⎪⎩⎪⎪⎪⎪⎪⎪⎪⎪⎪⎪⎪⎩⎩顶冒口依位置分侧冒口贴边冒口普通冒口明冒口依顶部覆盖分暗冒口大气压力冒口依加压方式分压缩空气冒口通用冒口(传统)发气压力冒口保温冒口发热冒口特种冒口依加热方式分加氧冒口电弧加热冒口,煤气加热冒口易割冒口直接实用冒口(浇注系统当铸铁件的实用冒口(均衡凝固)⎧⎪⎪⎪⎪⎪⎪⎪⎪⎪⎪⎪⎪⎪⎪⎨⎪⎪⎪⎪⎪⎪⎪⎪⎪⎪⎪⎧⎪⎪⎨⎪⎪⎪⎩⎩冒口)控制压力冒口冒口无补缩 图1 冒口分类(2)冒口的形状常用的冒口有球形、圆柱形、长方体形、腰圆柱形等。
对于具体铸件,冒口形状的选择主要应考虑以下几方面:a)球形 b)球顶圆柱形 c)圆柱形 d)腰圆柱形(明) e)腰圆柱形(暗)图2 常用的冒口形状①冒口的补缩效果: 冒口的形状不同,补缩效果也不同,常用冒口模数(M)的大小来评定冒口的补缩效果(M=冒口体积/冒口散热面积),在冒口体积相同的情况下,球形冒口的散热面积最小,模数最大,凝固时间最长,补缩效果最好,其它形状冒口的补缩效果,依次为圆柱形,长方体形等。
②铸件被补缩部位的结构情祝: 冒口形状的选泽还要考虑铸件被补缩部位的结构形状和造型工艺是否方便。
铸铁件冒口设计手册

铸铁件冒口设计手册诸葛胜福士科铸造材料(中国)有限公司铸铁冒口设计手册一、概述冒口是一个个储存金属液的空腔。
其主要作用是在铸件成形过程中提供由于体积变化所需要补偿的金属液,以防止在铸件中出现的收缩类型缺陷(如图1和图2所示),而这些需要补偿的体积变化可能有:图1 各种缩孔图2 缩孔生产图a)和冒口的补缩图b)1—一次缩孔 2—二次缩孔 3—缩松 1—缩孔 2—型腔胀大 3—铸件(虚线以内) 4—显微缩松 5—缩陷(缩凹,外缩孔)(1)铸型的胀大(2)金属的液态收缩(3)金属的凝固收缩补偿这些体积变化所需要的金属液量随着铸型和金属种类的不同而异。
此外,冒口还有排气及浮渣和非金属夹杂物的作用。
铸件制成后,冒口部分(残留在铸件上的凸块)将从铸件上除去。
由此,在保证铸件质量要求的前提下,冒口应尽可能的小些,以节省金属液,提高铸件成品率。
由此冒口的补缩效率越高,冒口将越小,铸件成品率越高、越经济。
FOSECO公司的发热保温冒口具有高达35%的补缩效率;因而,具有极高的成品率和极其优越的经济性。
在金属炉料价格飞涨的情况下,其优越性显得尤其突出。
另外,高品质发热保温冒口,及其稳定可靠的产品质量是获得高品质铸件的重要手段和可靠的质量保证。
二、铸铁的特点铸钢和铸铁都是铁碳合金,它们在凝固收缩过程中有共同之处)如凝固前期均析出初生奥氏体树枝晶,都存在着液态、凝固态和固态下的收缩),但也有不同的特点。
其根本不同之处是铸铁在凝固后期有“奥氏体+石墨”的共晶转变,析出石墨而发生体积膨胀,从而可部分地或全部抵消凝固前期所发生的体积收缩,即,具备有“自补缩的能力”。
因此在铸型刚性足够大时,铸铁件可以不设冒口或采用较小的冒口进行补缩。
灰铸铁在共晶转变过程中析出石墨,并在与枝晶间的液体直接接触的尖端优先长大,其石墨长大时所产生的体积膨胀直接作用在晶间液体上,进行“自补缩”。
对于一般低牌号的灰铁铸件,因碳硅含量高,石墨化比较完全,其体积膨胀量足以补偿凝固时的体收缩,故不需要设置冒口,只放排气口。
铸造工艺学-冒口设计

2 冒口位置的选择原则
① 在热节的上方或侧旁;
② 尽量在铸件最高、最厚部位, 低处热结设补贴或冷铁;
③不应设在铸件最重要、受力 大的部位;
④ 不要选在铸造应力集中处, 应减轻对铸件的收缩阻碍,避免 裂纹;
⑤ 尽量用一个冒口同时补缩几 个热节或铸件;
⑥ 冒口布置在加工面上,可节 约铸件精整工时,外观好;
可锻铸铁:补缩距离为4-4.5T。
3)有色合金的冒口补缩距离 铜合金见表。
锡青铜、磷青铜:糊状凝固,有效补缩距离短,易出现 分散缩松。
无锡青铜和黄铜:凝固范围窄,补缩距离大。黄铜5-9T。 铝、锰青铜5-8T。
共晶型铝合金:4.5T。 非共晶型的铝合金:2T。
4)外冷铁对补缩距 离的影响
在两个冒口间放冷铁, 形成两个末端区,显著 增加有效补缩距离。 端 部放冷铁延长末端区。
冒口是铸型内用以储存金属液的空腔,在金属冷却和 凝固过程中,补给金属液,从而防止缩孔、缩松的形成, 同时还有集渣和排气的作用。
习惯上 ,把冒口所铸成的金属实体也称为冒口。
8.1.1 冒口的种类和形状
顶冒口
1 按工艺冒口分为
依位置分
侧(边)冒口
普通冒口
明冒口
依顶部覆盖
暗冒口
通用冒口
大气压力冒口
依加压方式
ε=5% m补=548kg 1)计算模数M件铸件体积
V=[π(63²-33²)ˣ43/(4ˣ2)]=48607.2cm² 铸件的表面积=两个平面+两个侧面+上下端面 A=[(63-33)ˣ43+ π(63+33)ˣ43/2+ π(63²-33²)]/4=10031.76 M件=V/A=48607.2/10031.76=4.85 ≈5cm (2)计算冒口模数
铸钢件冒口的设计规范
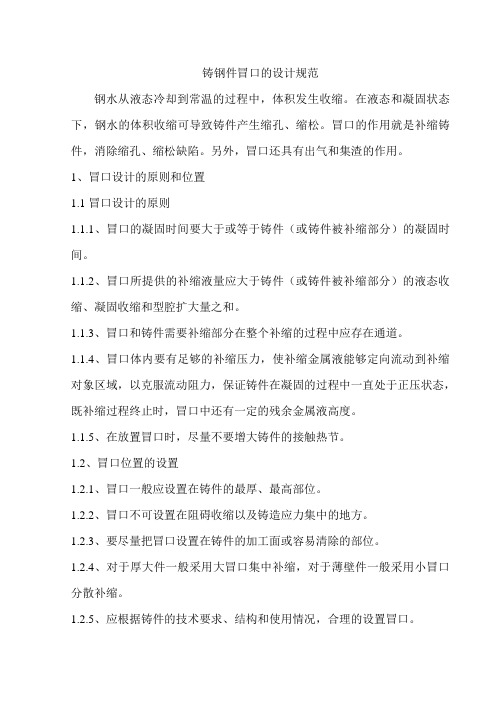
铸钢件冒口的设计规范钢水从液态冷却到常温的过程中,体积发生收缩。
在液态和凝固状态下,钢水的体积收缩可导致铸件产生缩孔、缩松。
冒口的作用就是补缩铸件,消除缩孔、缩松缺陷。
另外,冒口还具有出气和集渣的作用。
1、冒口设计的原则和位置1.1冒口设计的原则1.1.1、冒口的凝固时间要大于或等于铸件(或铸件被补缩部分)的凝固时间。
1.1.2、冒口所提供的补缩液量应大于铸件(或铸件被补缩部分)的液态收缩、凝固收缩和型腔扩大量之和。
1.1.3、冒口和铸件需要补缩部分在整个补缩的过程中应存在通道。
1.1.4、冒口体内要有足够的补缩压力,使补缩金属液能够定向流动到补缩对象区域,以克服流动阻力,保证铸件在凝固的过程中一直处于正压状态,既补缩过程终止时,冒口中还有一定的残余金属液高度。
1.1.5、在放置冒口时,尽量不要增大铸件的接触热节。
1.2、冒口位置的设置1.2.1、冒口一般应设置在铸件的最厚、最高部位。
1.2.2、冒口不可设置在阻碍收缩以及铸造应力集中的地方。
1.2.3、要尽量把冒口设置在铸件的加工面或容易清除的部位。
1.2.4、对于厚大件一般采用大冒口集中补缩,对于薄壁件一般采用小冒口分散补缩。
1.2.5、应根据铸件的技术要求、结构和使用情况,合理的设置冒口。
1.2.6、对于清理冒口困难的钢种,如高锰钢、耐热钢铸件的冒口,要少放或不放,非放不可的,也尽量采用易割冒口或缩脖型冒口。
2、设置冒口的步骤与方法冒口的大小、位置及数量对于铸钢件的质量至关重要。
对于大型铸钢件来说,必须把握技术标准及使用情况,充分了解设计意图,分清主次部位,集中解决关键部位的补缩。
以模数法为例,冒口设计的步骤如下:2.1、对于大、中型铸钢件,分型面确定之后,首先要根据铸件的结构划分补缩范围,并计算铸件的模数(或铸件被补缩部分的模数)M铸。
2.2、根据铸件(或铸件被补缩部分)的模数M铸,确定冒口模数M冒。
2.3、计算铸件的体收缩ε。
2.4、确定冒口的具体形状和尺寸。
球形喷口原理
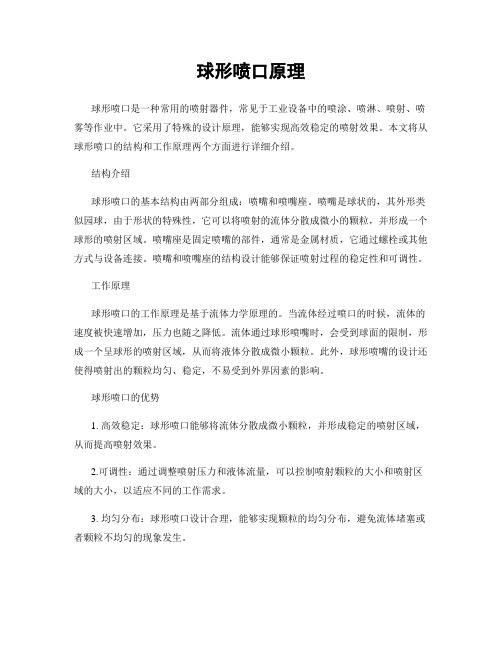
球形喷口原理球形喷口是一种常用的喷射器件,常见于工业设备中的喷涂、喷淋、喷射、喷雾等作业中。
它采用了特殊的设计原理,能够实现高效稳定的喷射效果。
本文将从球形喷口的结构和工作原理两个方面进行详细介绍。
结构介绍球形喷口的基本结构由两部分组成:喷嘴和喷嘴座。
喷嘴是球状的,其外形类似园球,由于形状的特殊性,它可以将喷射的流体分散成微小的颗粒,并形成一个球形的喷射区域。
喷嘴座是固定喷嘴的部件,通常是金属材质,它通过螺栓或其他方式与设备连接。
喷嘴和喷嘴座的结构设计能够保证喷射过程的稳定性和可调性。
工作原理球形喷口的工作原理是基于流体力学原理的。
当流体经过喷口的时候,流体的速度被快速增加,压力也随之降低。
流体通过球形喷嘴时,会受到球面的限制,形成一个呈球形的喷射区域,从而将液体分散成微小颗粒。
此外,球形喷嘴的设计还使得喷射出的颗粒均匀、稳定,不易受到外界因素的影响。
球形喷口的优势1. 高效稳定:球形喷口能够将流体分散成微小颗粒,并形成稳定的喷射区域,从而提高喷射效果。
2.可调性:通过调整喷射压力和液体流量,可以控制喷射颗粒的大小和喷射区域的大小,以适应不同的工作需求。
3. 均匀分布:球形喷口设计合理,能够实现颗粒的均匀分布,避免流体堵塞或者颗粒不均匀的现象发生。
4. 耐用性:球形喷口多采用金属材质制作,具有较强的耐磨性和耐腐蚀性,能够适应各种工况环境。
5. 安全性:球形喷口的结构紧凑,不易堵塞,避免工作中发生液体泄漏或喷射器件损坏的情况。
应用领域球形喷口广泛应用于涂装、喷涂、化工、冶金、环保等行业。
在汽车工业中,球形喷口可用于喷漆作业,实现车身颜色均匀、光亮的效果。
在冶金行业中,球形喷口可用于喷炉作业,实现矿石的均匀喷洒,提高操作效率。
在环保领域,球形喷口可用于喷淋作业,实现雾化喷射降低粉尘污染。
总结球形喷口是一种高效稳定的喷射器件,它通过流体力学原理的应用实现了流体的分散和微细颗粒的形成,具有高均匀性、可调性、耐用性和安全性等优势。
知识篇——铸件的冒口设计计算

知识篇——铸件的冒口设计计算1.冒口设计的基本原理铸件冒口主要是在铸钢件上使用。
铸铁件只用于个别的厚大件的灰铸铁件和球铁件上。
金属液在液态降温和凝固过程中,体积要收缩。
铸件的体收缩大约为线收缩的3倍。
因此,铸钢的体收缩通常按3---6%考虑,灰铸铁按2---3%,不过由于灰铸铁和球墨铸铁凝固时的石墨化膨胀,可以抵消部分体积收缩,所以如果壁厚均匀,铸型紧实度高,通常不需要设计冒口。
铸件的体收缩如果得不到补充,就会在铸件上或者内部形成缩孔、缩陷或者缩松。
严重时常常造成铸件报废。
冒口尺寸计算原则是,首先计算需要补缩的金属液需要多少。
通常把这一部分金属液假设成球体,并求出直径(设为d0)用于冒口计算。
冒口补缩铸件是有一定的范围------叫有效补缩距离,设为L,对厚度为h的板状零件通常L=3~5h 。
对棒状零件L=(25~30)√h 式子中,h------铸件厚度2.冒口尺寸的基本计算方法冒口计算的公式、图线、表格等有很多。
介绍如下。
最常用的方法是,冒口直径 D=d0+h理由是假定冒口和铸件以相同的速度凝固,凝固过程是从铸件的两个表面向内层进行,当铸件完全凝固终了,正好冒口凝固了同样的厚度,这时还剩下中间的空心的缩孔,体积正好等于补缩球的体积,这部分金属液在凝固过程中正好补缩进了铸件。
当铸件存在热节时,可以把h换成热节的直径T即可。
即D=do+T 。
另外设计冒口,还有个重要的部位,就是冒口颈,所谓冒口颈就是冒口和铸件的连接通道,冒口里的金属液都是经由冒口颈补缩到铸件里的。
所以对冒口颈的截面是有要求的,通常取冒口颈的直径dj=(0.6~0.8)T 。
冒口高度 H=(1.5~2.5)D 。
H的高度还应该考虑要高于需要补缩部位的高度,否则就成了反补缩了,铸件补缩了冒口,这是要避免的。
3.其它计算方法常用的经验计算方法还有不计算需要估算补缩的金属液,直接将热节园的直径乘个系数得出冒口直径。
例如简单铸件 D=(1.05~1.15)T 外形简单,热节比较集中。