轧钢五条线324资料
51钢铁PPT-轧钢基本理论课件

残余内应力的影响
▪ 宏观内应力 ▪ 引起新的变形,降低精度。 ▪ 微观内应力 ▪ 引起开裂,产生微裂纹。 ▪ 晶格畸变内应力 ▪ 强化金属;耐蚀性降低。
塑性变形的金属在加热时 组织和性能变化
▪ 1.回复
▪ 2.再结晶 ▪ 3.晶粒长大
塑性变形的金属在加热时 组织变化
回复
▪ 塑性变形后的金属在低温加热时,发生回复过程
轧钢基本理论
51钢铁收集整理
内容提要
▪ 1、金属压力加工; ▪ 2、塑性变形对组织和性能的影响; ▪ 3、钢材品种及用途; ▪ 4、型钢生产系统; ▪ 5、钢材产品标准及技术要求; ▪ 6、轧钢基本工序介绍; ▪ 7、轧制过程参数及变形规律; ▪ 8、宽展、前滑和后滑,以及影响其的因素; ▪ 9、轧制力能参数介绍。
金属压力变形分类
▪ 金属压力变形分为: ▪ 1、弹性变形:给其力则变形,力撤销其变形即消失。 ▪ 基本原理:外力应力原子离开平衡位置变形原子位能增加返
回趋势外力消失变形消失弹性变形 ▪ 条件:外力小于屈服极限 ▪ 2、塑性变形:给其力则变形,力撤销其变形依然存在。 ▪ 基本原理:金属塑性变形的实质——晶粒内部或晶粒之间产生的滑移及
冷加工对组织和性能的影响
▪ 冷加工 —— 在 T再 以下温度进行的变形加工,如低碳钢的冷拔、冷冲。
▪
冷加工时,无再结晶过程。
▪ 冷加工能产生加工硬化,提高强度和硬度,塑性和韧性下降。是重要的强化
手段,对不能热处理强化的合金尤其重 要。但增加继续塑性变形的抗力。
➢ 由于有加工硬化的存在,故冷变形可提高工件的强度和硬度,但冷变形 不能太大,否则易开裂;
再结晶温度(最低)
▪ 纯金属 T再 =0.4 T熔 ▪ 合 金 T再 =(0.5 ~ 0.7)T熔 ▪ (温度单位:绝对温度( K ))
第一节 轧钢基础知识
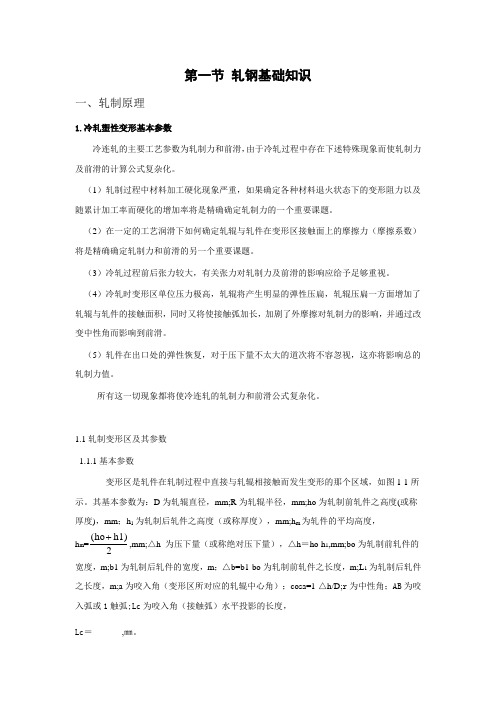
第一节轧钢基础知识一、轧制原理1.冷轧塑性变形基本参数冷连轧的主要工艺参数为轧制力和前滑,由于冷轧过程中存在下述特殊现象而使轧制力及前滑的计算公式复杂化。
(1)轧制过程中材料加工硬化现象严重,如果确定各种材料退火状态下的变形阻力以及随累计加工率而硬化的增加率将是精确确定轧制力的一个重要课题。
(2)在一定的工艺润滑下如何确定轧辊与轧件在变形区接触面上的摩擦力(摩擦系数)将是精确确定轧制力和前滑的另一个重要课题。
(3)冷轧过程前后张力较大,有关张力对轧制力及前滑的影响应给予足够重视。
(4)冷轧时变形区单位压力极高,轧辊将产生明显的弹性压扁,轧辊压扁一方面增加了轧辊与轧件的接触面积,同时又将使接触弧加长,加剧了外摩擦对轧制力的影响,并通过改变中性角而影响到前滑。
(5)轧件在出口处的弹性恢复,对于压下量不太大的道次将不容忽视,这亦将影响总的轧制力值。
所有这一切现象都将使冷连轧的轧制力和前滑公式复杂化。
1.1轧制变形区及其参数1.1.1基本参数变形区是轧件在轧制过程中直接与轧辊相接触而发生变形的那个区域,如图1-1所示。
其基本参数为:D为轧辊直径,mm;R为轧辊半径,mm;ho为轧制前轧件之高度(或称厚度),mm;h1为轧制后轧件之高度(或称厚度),mm;h m为轧件的平均高度,h m=2h1)(ho,mm;△h 为压下量(或称绝对压下量),△h=ho-h1,mm;bo为轧制前轧件的宽度,m;b1为轧制后轧件的宽度,m;△b=b1-bo为轧制前轧件之长度,m;L1为轧制后轧件之长度,m;a为咬入角(变形区所对应的轧辊中心角);cosa=1-△h/D;r为中性角;AB为咬入弧或1触弧;Lc为咬入角(接触弧)水平投影的长度,Lc=,㎜。
1.1.2 变形系数轧制时轧件塑性变形,使轧件尺寸在三个方向上都发生了变化,即:轧制之高度由ho减少到h1,比值h1/ho=η为轧件高度方向上的变形,η叫做压下系数。
图1-1 变形区基本参数轧件之宽度bo增加到b1,比值b1/bo=X为轧机宽度方向上的变形,X叫做宽度系数。
轧钢生产线工艺流程图
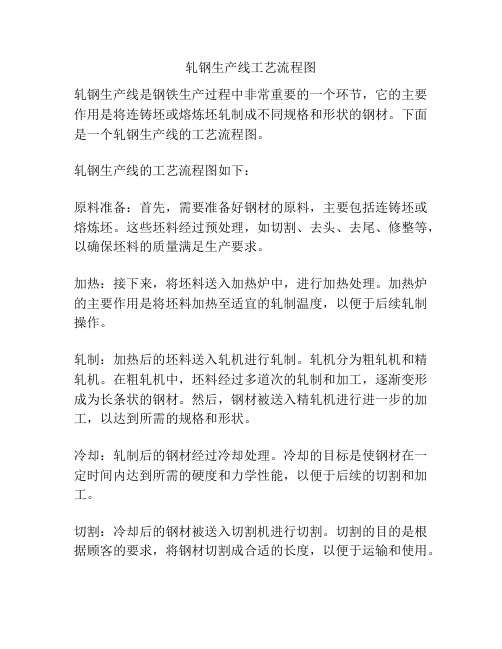
轧钢生产线工艺流程图
轧钢生产线是钢铁生产过程中非常重要的一个环节,它的主要作用是将连铸坯或熔炼坯轧制成不同规格和形状的钢材。
下面是一个轧钢生产线的工艺流程图。
轧钢生产线的工艺流程图如下:
原料准备:首先,需要准备好钢材的原料,主要包括连铸坯或熔炼坯。
这些坯料经过预处理,如切割、去头、去尾、修整等,以确保坯料的质量满足生产要求。
加热:接下来,将坯料送入加热炉中,进行加热处理。
加热炉的主要作用是将坯料加热至适宜的轧制温度,以便于后续轧制操作。
轧制:加热后的坯料送入轧机进行轧制。
轧机分为粗轧机和精轧机。
在粗轧机中,坯料经过多道次的轧制和加工,逐渐变形成为长条状的钢材。
然后,钢材被送入精轧机进行进一步的加工,以达到所需的规格和形状。
冷却:轧制后的钢材经过冷却处理。
冷却的目标是使钢材在一定时间内达到所需的硬度和力学性能,以便于后续的切割和加工。
切割:冷却后的钢材被送入切割机进行切割。
切割的目的是根据顾客的要求,将钢材切割成合适的长度,以便于运输和使用。
检测:切割后的钢材需要进行质量检测,以确保其满足规定的质量标准。
这包括外观检查、尺寸测量、化学成分分析和力学性能测试等。
包装和运输:通过质量检测的钢材被包装起来,以便于运输和储存。
包装通常采用钢带或木托盘等材料,以确保钢材的安全和完整。
以上就是一个大致的轧钢生产线工艺流程图,从原料准备到最后的包装和运输,每个环节都十分重要。
在具体的生产过程中,还会包括其他辅助工艺和设备,如铁水处理、连铸、热处理等,以满足不同钢材品种和规格的生产需求。
轧钢工高级工理论知识资料
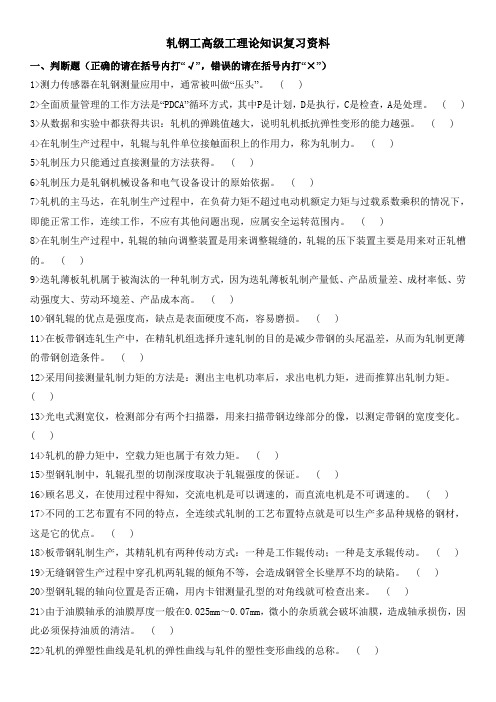
轧钢工高级工理论知识复习资料一、判断题(正确的请在括号内打“√”,错误的请在括号内打“×”)1>测力传感器在轧钢测量应用中,通常被叫做“压头”。
( )2>全面质量管理的工作方法是“PDCA”循环方式,其中P是计划,D是执行,C是检查,A是处理。
( )3>从数据和实验中都获得共识:轧机的弹跳值越大,说明轧机抵抗弹性变形的能力越强。
( )4>在轧制生产过程中,轧辊与轧件单位接触面积上的作用力,称为轧制力。
( )5>轧制压力只能通过直接测量的方法获得。
( )6>轧制压力是轧钢机械设备和电气设备设计的原始依据。
( )7>轧机的主马达,在轧制生产过程中,在负荷力矩不超过电动机额定力矩与过载系数乘积的情况下,即能正常工作,连续工作,不应有其他问题出现,应属安全运转范围内。
( )8>在轧制生产过程中,轧辊的轴向调整装置是用来调整辊缝的,轧辊的压下装置主要是用来对正轧槽的。
( )9>迭轧薄板轧机属于被淘汰的一种轧制方式,因为迭轧薄板轧制产量低、产品质量差、成材率低、劳动强度大、劳动环境差、产品成本高。
( )10>钢轧辊的优点是强度高,缺点是表面硬度不高,容易磨损。
( )11>在板带钢连轧生产中,在精轧机组选择升速轧制的目的是减少带钢的头尾温差,从而为轧制更薄的带钢创造条件。
( )12>采用间接测量轧制力矩的方法是:测出主电机功率后,求出电机力矩,进而推算出轧制力矩。
( )13>光电式测宽仪,检测部分有两个扫描器,用来扫描带钢边缘部分的像,以测定带钢的宽度变化。
( )14>轧机的静力矩中,空载力矩也属于有效力矩。
( )15>型钢轧制中,轧辊孔型的切削深度取决于轧辊强度的保证。
( )16>顾名思义,在使用过程中得知,交流电机是可以调速的,而直流电机是不可调速的。
( )17>不同的工艺布置有不同的特点,全连续式轧制的工艺布置特点就是可以生产多品种规格的钢材,这是它的优点。
轧钢基础知识课件
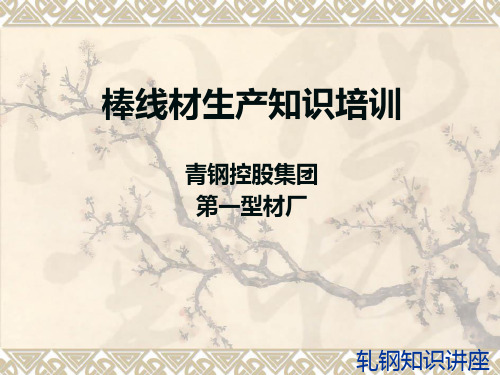
冷拔用软线材
冷拔轮胎用线材 焊条钢
冷拔各种丝材、钉子、金属网丝
汽车轮胎用帘线 焊条
轧钢知识讲座
表1.2 市场对部分棒、线材产品的质量要求和生产对策
钢 种 建筑用螺纹钢筋 机械结构用钢 市场需求、发展动向 高强度、低温韧性、耐盐蚀 对应生产措施 严格控制成分
淬火时省去软化退火,调质可以 软化材料(控制成分、控轧 提高强度 控冷)减少偏析
轧钢知识讲座
图3.2 半连续式轧机 1-粗轧机组,2-中轧机组,3-精轧机组,4-卷线机
轧钢知识讲座
1.3 传统连续式轧机 传统的连续式轧机主要是集体传动的水平辊底座,对线材进 行多线轧制,其基本形式见图3.3。由于这类轧机在轧制过程中 存在着扭转翻钢,所以轧制速度一般不高在20~30米/秒。
轧钢知识讲座
钢材的使用造成有害影响,清除后不应使钢材小于允许得最 小尺寸,清除宽度不应小于清除深度得5倍,允许有从实际 尺寸算起不超过公称尺寸公差一半的细小划痕、压痕、凹坑 存在。 4.易切削钢:钢材表面不得有裂纹、折叠、撕裂和结疤。上 述缺陷必须清除,清理深度不得超过公差之半。不得有超出 公差之半的划痕、黑斑和麻点,发纹深度不得大于公差的四 分之一; 5.管坯钢:表面不准出现目视可见的折叠、结疤、夹杂和深 度大于0.2mm的裂纹。
图3.4 型、棒材一体化节能型轧机车间布置图 0-钢包炉,1-钢包回转台,2-连铸机,3-钢坯冷床,4-热储存装置,5-冷上 料台驾,6-步进式加热炉,7-粗轧机组,8-中轧机组,9-精轧机,10水 冷装置,11-分段剪,12-冷床,13-多条矫直机和连续定尺冷飞剪,14非磁性全自动堆垛机,15-打捆机和称重装置
轧钢知识讲座
表1.1 棒、线材的产品分类和用途 钢 种 用 途
轧钢标准化第一阶段需上报的资料
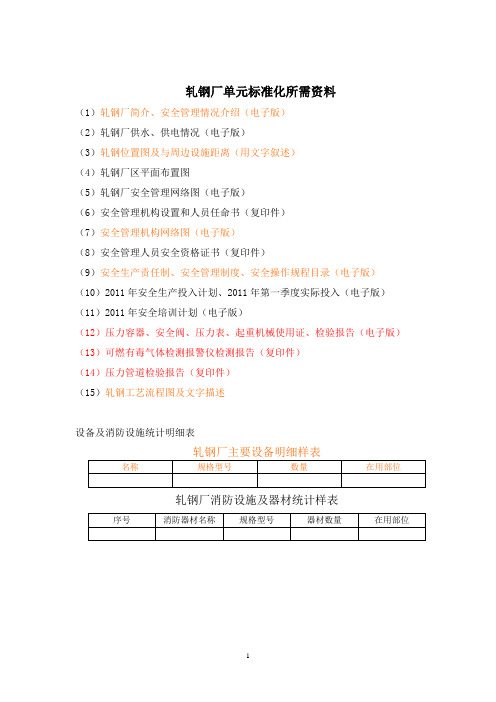
轧钢厂单元标准化所需资料
(1)轧钢厂简介、安全管理情况介绍(电子版)
(2)轧钢厂供水、供电情况(电子版)
(3)轧钢位置图及与周边设施距离(用文字叙述)
(4)轧钢厂区平面布置图
(5)轧钢厂安全管理网络图(电子版)
(6)安全管理机构设置和人员任命书(复印件)
(7)安全管理机构网络图(电子版)
(8)安全管理人员安全资格证书(复印件)
(9)安全生产责任制、安全管理制度、安全操作规程目录(电子版)(10)2011年安全生产投入计划、2011年第一季度实际投入(电子版)(11)2011年安全培训计划(电子版)
(12)压力容器、安全阀、压力表、起重机械使用证、检验报告(电子版)(13)可燃有毒气体检测报警仪检测报告(复印件)
(14)压力管道检验报告(复印件)
(15)轧钢工艺流程图及文字描述
设备及消防设施统计明细表
轧钢厂主要设备明细样表
轧钢厂消防设施及器材统计样表
1。
轧钢五条线324汇总资料
轧钢是一种塑性变形过程。与其它加工方法相比,主要具 有如下优点:
A.能改善组织性能。如减轻偏析、致密结构、细化晶粒等, 从而提高材料的综合力学性能。
B.金属废屑少。因塑性成形主要靠金属塑性状态下的体积 转移,不需切除大量的多余金属,所以金属收得率较高。
C.生产率高。这体现在塑性变形可采用高的加工速度,以 及可采用连续式(非周期式)的生产方式,因此特别适用 于大批量生产。
工艺流程:轧钢生产过程要经过多种工序,这些工序按顺 序的排列称为工艺流程。
基本工序:坯料准备、坯料加热、钢的轧制、精整。 钢材:一种具备了一定质量标准(尺寸、形状、性能),
并可直接供社会使用的产品。 国际习惯划分: 长材:铁道用钢材、型钢、棒材、钢筋、盘条等 扁平材(即钢板):厚度与宽度、长度比相差较大的平板 管材:两端开口并具中空断面,长度与周边比较大的钢材
预水冷 2#剪
120m冷床
冷剪
冷锯
收集
称重
入库
3.1.3、一轧车间主要工序、设备
热送热装 技术
坯料经热送台架、提升辊道后达到入炉辊道,随后准 备入炉加热。
热送温度大约在600℃以上,连铸坯热送热装,降低
能源消耗,符合国家节能减排政策。
双蓄热步进梁式加热炉
双蓄热步进梁式加热炉,采用蓄热式燃烧技术,充分利 用低热值高炉煤气,减少排放;金属氧化烧损低,温度均匀, 热效率高,能够保证多钢种的加热工艺,设计能力130t/h。
1.3.2. 组成:主要设备和辅助设备
主要设备:主机列。包括工作机座(机架、轴承、调整装 置、导卫)、传动装置(齿轮、减速机、连轴节)和主电 机。
辅助设备:主机列之外的其它设备。车间的自动化程度越 高,重量所占的比例越大。(是主要设备重量的3~4倍)
炼钢产线介绍范文
炼钢产线介绍范文炼钢是将原材料钢铁矿石经过一系列的物理和化学反应,在高温高压的条件下,经过冶炼、炼化、调质等过程,最终生产成合格的钢铁产品。
炼钢产线是指用于炼钢的设备及工艺流程的整个生产线。
下面将从原料准备、高炉冶炼、炼钢、连铸等方面来介绍炼钢产线。
首先是原料准备。
在炼钢产线的开始阶段,需要准备原材料,主要包括铁矿石、焦炭、废钢等。
铁矿石是炼钢的主要原料,其中含有大量的铁元素,而焦炭则是提供燃料和还原剂所需的碳源。
废钢是指回收利用的废旧钢铁制品,通过钢铁回收利用可以减少资源浪费和环境污染。
接下来是高炉冶炼。
在高炉中,将铁矿石、焦炭和废钢等原料放入高炉炉底,然后再通过煤气或液态燃料点火,使炉料逐渐加热。
在高炉中,炉料被分解成气态和固态两部分。
其中,气态部分主要是煤气,可以用作炼钢的燃料和还原剂。
固态部分则是炼钢的铁水和渣。
在高炉中,通过上、下和侧喷吹煤气,以及注入适量的氧气,可以进一步提高炉内的温度和增加还原反应,从而提高炼钢效率和产量。
然后是炼钢。
在高炉冶炼的过程中,通过炸碎高炉渣、焦粉和适量的石灰,可以调整炉渣的成分和质量。
然后将铁水从高炉中取出,通过倒炉车或搅炉车输送到炼钢车间。
在炼钢车间,铁水首先经过脱碳和净化处理。
脱碳主要是通过将含有大量碳的铁水与氧气接触,使其中的碳元素氧化并生成二氧化碳排出。
净化处理主要是通过去除铁水中的杂质,如硫、磷和氧等,以提高炼钢的质量。
然后,通过添加合适的合金元素和调整炉料的成分,可以根据不同用途的钢铁产品,制备不同牌号的钢水。
最后是连铸。
在炼钢后,将炼得的钢水输送到连铸机进行连铸。
连铸是将液态钢水通过连铸结晶器,通过凝固和形成连铸坯。
连铸结晶器具有一定长度和冷却速度,使钢水在结晶器内逐渐凝固成坯料。
然后,通过切割装置,将连铸坯进行切割和堆垛,形成合格的钢铁坯料。
连铸是炼钢产线的最后一个环节,也是从液态到固态的转变,为下一步的热轧、冷轧等后续加工提供了坯料。
总结起来,炼钢产线是将原材料和高炉冶炼、炼钢、连铸等工序有机地结合在一起,实现从矿石到钢铁产品的转化过程。
轧钢基础知识.ppt
• 以下两种方法是通过提高摩擦系数进而增加轧辊
对轧件向前的摩擦力来改善咬入的,也是较常用的 方法:
• 改善轧件或轧辊的表面状态,提高摩擦系数:
从轧件入手的常用方法是清除轧件表面的炉生氧 化铁皮;
从轧辊入手的常用方法是辊面压花,以增加摩擦 系数,这种方法在1500轧机轧辊的第一个孔型中 就有应用;
一是使轧辊可以重车并保持孔型不变;
• 二是可以减小车削量;增加轧辊的寿命;磨损量
一定的情况下,侧壁斜度越大,车削量越小;
• 轧辊重车率:全部重车量与轧辊名义直径(1500)
的百分比称为重车率。
• 2.7辊跳
在轧制过程中,轧机的各部件受轧制力的作用发 生弹性变形,如机架窗口高度扩大、轧辊弯曲、 压下螺丝和轴承受到压缩等。这些弹性变形最后 反映在两轧辊之间的缝隙增大,轧制中这种辊缝 增大的现象叫做辊跳。辊缝增大的总值称为辊跳 值。轧机刚性越好,辊跳值越小。轧件的变形抗 力越大,辊跳值越大。辊跳值的大小取决于轧机
充不满,造成过大的椭圆度,即轧件最大与最小 直径之差过大;
• 二是估计宽展较实际宽展过小,孔型充填过满,
形成耳子;这两种情况都是要尽量避免的。
• 以上两种情况分别如下图a、b所示
• 要正确的估算宽展量,那就必须知道影响宽展的
因素,影响宽展量的主要因素有以下几点:
• 压下量:宽展产生的原因就是因为有压下量,没
• 通常我们见到的轧制方式都是热轧,现将热轧与
冷轧进行简单的对比:
热轧的优点是可以破坏坯料的铸造组织,细化钢 材的晶粒,并消除显微组织的缺陷,从而使钢材 组织密实,力学性能得到改善等等;缺点是经过 热轧之后,钢材内部的非金属夹杂物(主要是硫 化物和氧化物,还有硅酸盐)被压成薄片,出现 分层(夹层)现象,而且如果冷却不均匀还会造 成残余应力。
轧钢五条线3-24详述
与传统的单线轧制工艺相比,切分轧制具有很多优点: ①减少机架数目,节省车间投资 ②可以缩短轧制节奏,大幅度的提高轧机产量。 ③可以用小轧机开大钢坯,为轧机的坯料选择提供了充分 的余地,并有利于解决轧机与连铸坯的衔接和匹配问题。 ④能较多的降低生产成本。
与单线同规格相 比切分孔型从13 号轧机开始变化, 在17#轧机出口后, 采用切分轮切开, 最后在19#轧机出 成品。
③温度均匀,热效率高,加热能力随产量波动小,高效蓄 热式加热炉的热效率可达到70%以上; ④资源利用率高,可充分利用热值低的高炉煤气。
高压水除鳞
钢坯出炉及高压水除磷,出炉温度控制在960-1000℃之间, 除磷压力一般在19-22Mpa左右。
轧机机组
一轧采用平立交替布置的高刚度短应力线轧机机组,实现 无扭转微张力轧制;轧线配备控轧控冷穿水系统(DANIELI 公司设备和技术),能够满足轧制高强度螺纹钢和高精度优质 合金棒材的需要。
1.3.2. 组成:主要设备和辅助设备
主要设备:主机列。包括工作机座(机架、轴承、调整装 置、导卫)、传动装置(齿轮、减速机、连轴节)和主电 机。
辅助设备:主机列之外的其它设备。车间的自动化程度越 高,重量所占的比例越大。(是主要设备重量的3~4倍)
2.1、棒线材简介
棒材:简单断面型钢一般成根供应,又称棒材,主要包括圆钢和 螺纹钢筋。近年来,随着生产技术的发展,小型棒材亦可成卷 供应。
热锯
热锯房:根据合同要求锯切尺寸
冷床收集
冷床分快摇和慢摇两种,根据钢种不同可以调整冷床摇动速 度,来保证入缓冷箱(坑)温度。
冷床收集
下冷床之后进行收集,吊运至缓冷箱(坑)。
缓冷
缓冷箱
成品入坑缓冷过程
收集打捆
- 1、下载文档前请自行甄别文档内容的完整性,平台不提供额外的编辑、内容补充、找答案等附加服务。
- 2、"仅部分预览"的文档,不可在线预览部分如存在完整性等问题,可反馈申请退款(可完整预览的文档不适用该条件!)。
- 3、如文档侵犯您的权益,请联系客服反馈,我们会尽快为您处理(人工客服工作时间:9:00-18:30)。
3.1.1、一轧车间设计能力
设计总要求:
轧线年产量:120万吨 主要品种规格: 螺纹棒材φ12-φ40(φ18以下螺纹采用切分轧制); 普通圆钢φ16-φ60 优质合金棒:φ16-φ60 钢种:普碳钢、优碳钢、低合金钢、冷镦钢、轴承钢、弹簧
芜湖新兴可以生产断面直径为5-270mm规格的产品,几乎涵盖 国内外所有的棒线材规格。
2.2、棒线材一般生产工艺流程
连铸坯(热送/热送)→测长、称重→装炉 →加热→轧制→控制冷却→检查→打捆→ 收集→称重→入库
2.3、棒线材的分类和用途
钢种
建筑用螺纹钢 油质碳素结构钢
合金结构钢 弹簧钢 易切削钢 工具钢 轴承钢 不锈钢
芜湖新兴铸管 轧钢生产线介绍
2016年1月
主要内容
1、轧钢介绍 2、棒线材的生产、分类和用途 3、轧钢车间及其典型设备工序产品介绍 3.1、一轧钢车间介绍 3.2、大棒(二轧)车间介绍 3.3 、双高线车间介绍 3.4、 中棒车间介绍
1.1、轧钢的基本概念
轧钢:在旋转的轧辊间改变钢锭,钢坯形状的压 力加工过程叫轧钢。轧钢的目的与其他压力加工 一样,一方面是为了得到所需要的形状,另一方 面是为了改善钢的内部质量。简单的说就是将钢 锭或连铸坯轧制成钢材的过程。
轧钢是一种塑性变形过程。与其它加工方法相比,主要具 有如下优点:
A.能改善组织性能。如减轻偏析、致密结构、细化晶粒等, 从而提高材料的综合力学性能。
B.金属废屑少。因塑性成形主要靠金属塑性状态下的体积 转移,不需切除大量的多余金属,所以金属收得率较高。
C.生产率高。这体现在塑性变形可采用高的加工速度,以 及可采用连续式(非周期式)的生产方式,因此特别适用 于大批量生产。
1.3.2. 组成:主要设备和辅助设备
主要设备:主机列。包括工作机座(机架、轴承、调整装 置、导卫)、传动装置(齿轮、减速机、连轴节)和主电 机。
辅助设备:主机列之外的其它设备。车间的自动化程度越 高,重量所占的比例越大。(是主要设备重量的3~4倍)
2.1、棒线材简介
棒材:简单断面型钢一般成根供应,又称棒材,主要包括圆钢和 螺纹钢筋。近年来,随着生产技术的发展,小型棒材亦可成卷 供应。
钢种
市场需求、发展动向
对应生产措施
建筑用螺纹钢筋 高强度、低温韧性、耐腐蚀
严格材料(控制成分、控制冷
可以提高强度
却)减少偏析
弹簧钢
高强度、耐疲劳
严格控制成分,减少夹杂
易切削钢 冷加工材
硬线、轮胎用线 材
提高车削效率和刀具寿命 减少冷顶锻开裂 减少拉拔道次 省略软化退火
预水冷 2#剪
120m冷床
冷剪
冷锯
收集
称重
入库
3.1.3、一轧车间主要工序、设备
热送热装 技术
坯料经热送台架、提升辊道后达到入炉辊道,随后准 备入炉加热。
热送温度大约在600℃以上,连铸坯热送热装,降低
能源消耗,符合国家节能减排政策。
双蓄热步进梁式加热炉
双蓄热步进梁式加热炉,采用蓄热式燃烧技术,充分利 用低热值高炉煤气,减少排放;金属氧化烧损低,温度均匀, 热效率高,能够保证多钢种的加热工艺,设计能力130t/h。
减少断线 提高强度
控制夹杂物 消除表面缺陷
高精度轧制 软化材料 消除表面缺陷和内部偏析 控制冷却 严格控制成分
目前轧钢部共有四个车间,含五条生产线。
一轧车间:一条连轧生产线,主要生产螺纹钢、部分圆钢 和精轧螺纹。
二轧车间(大棒车间):一条开坯机+八连轧生产线。
双高线车间:两条生产线,其中A线为国产设备,主要生 产建筑用盘螺;B线为进口第六代摩根设备,目前主要以 生产冷镦用盘圆为主。
钢 坯料断面尺寸(mm×mm):150×150、165×165、
180×180. 坯料长度(mm):6000、12000。 最高轧制速度:18m/s
加热炉
一轧轧制工艺流程
Φ710×2+Φ610×4+Φ530×2
水除鳞
1#剪
水冷
Φ390×4
4#剪
预留Danieli 两辊减定径
3#剪
Φ430×8
工艺流程:轧钢生产过程要经过多种工序,这些工序按顺 序的排列称为工艺流程。
基本工序:坯料准备、坯料加热、钢的轧制、精整。 钢材:一种具备了一定质量标准(尺寸、形状、性能),
并可直接供社会使用的产品。 国际习惯划分: 长材:铁道用钢材、型钢、棒材、钢筋、盘条等 扁平材(即钢板):厚度与宽度、长度比相差较大的平板 管材:两端开口并具中空断面,长度与周边比较大的钢材
1.2、轧钢生产的基本工艺流程
1.3、轧钢机的定义和组成
1.3.1. 定义
狭义定义:轧制钢材的机械设备。它使轧件在旋转的轧辊 间产生塑性变形,轧出所需断面形状和尺寸的钢材。即主 要设备——主机列。(厚板、中板、薄板、轨梁、槽钢、 角钢、螺纹钢筋、线材等)
广义定义:用于轧制钢材生产工艺全部所需的主要设备和 辅助设备的成套机组。包括轧制,运输、翻钢、冷却、剪 切、矫直等设备。
冷拔用软线材 冷拔轮胎用线材
焊条钢
一般机械零件、标准件
钢筋混凝土建筑 汽车零件、机械零件、标准件 重要的汽车零件、机械零件、标准件
汽车、机械用弹簧钢 机械零件和标准件 切削刀具、钻头、模具、手工工具
轴承 各种不锈钢制品 冷拔各种丝材、钉子、金属网丝 汽车轮胎用连线
焊条
棒线材的典型用途:
2.4、市场对部分棒线材产品的质量要求 和生产对策
车间设计时定位是以合金钢等机械制造用钢为主,投产初 期以生产普通螺纹钢、圆钢为主,所以为了保证产品质量, 选用了双蓄热步进式加热炉。
采用蓄热式加热炉技术,增大了连铸坯断面,工序能耗也 显著降低,节约生产成本,具体体现在以下几个方面:
线材:是热轧生产中断面最小,长度最长而且成盘卷状交货的产 品。线材的品种按断面形状分,有圆形、六角形、方形、螺纹 圆形、扁形、梯形及Z字形等,主要是圆形和螺纹圆形。
通常认为,棒材的断面直径是9-300mm,线材的断面直径是540mm,呈盘卷状交货的产品最大断面直径是40mm。国内在生产 时约定俗成的认为:棒材车间的产品范围是断面直径10-50mm, 线材车间的产品断面直径是5-10mm。