LF精炼过程的钢水温度控制
LF精炼炉钢水温度预报方法
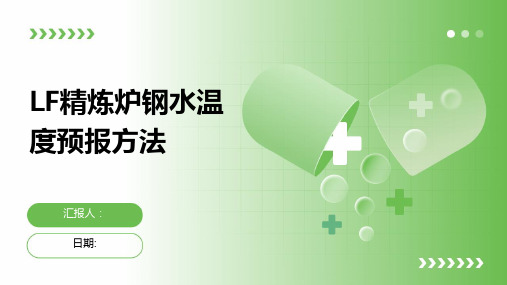
在温度预报方法的基础上,进一步研究降 低能耗、减少排放的绿色炼钢技术,推动 炼钢行业的可持续发展。
针对高温环境下材料性能的变化规律,开 展深入研究,为优化温度预报方法提供理 论支持。
THANKS
感谢观看
温度预报模型建立
模型选择
根据问题特性和数据规模 ,选择合适的温度预报模 型,如线性回归、支持向 量机、神经网络等。
参数调优
对选定的模型进行参数调 优,通过交叉验证等方法 确定最佳参数组合。
模型评估
使用历史数据对模型进行 训练,并通过评估指标( 如均方误差、准确率等) 对模型性能进行评估。
Hale Waihona Puke 实时温度预报04温度预报方法的应用与优 化建议
温度预报方法在炼钢厂的应用情况
实时监控与调整
炼钢厂利用温度预报方法,实现对LF精炼炉钢水温度的实时监控和调整,确保 钢水温度处于目标范围内,提高产品质量和生产效率。
数据驱动决策
通过温度预报方法提供的数据,炼钢厂能够更科学地制定生产计划和调度,减 少能源消耗和生产成本。
LF精炼炉钢水温 度预报方法
汇报人: 日期:
目录
• LF精炼炉工艺简介 • 基于数据模型的钢水温度预报 • 基于物理模型的钢水温度预报 • 温度预报方法的应用与优化建议
01
LF精炼炉工艺简介
LF精炼炉工作原理
电热原理
LF精炼炉利用强大的电流通过钢水产生热量,使钢水达到所 需温度。
搅拌原理
通过电磁搅拌或气体搅拌等方式,促进钢水成分和温度的均 匀分布。
分析炉子输入和输出的热量,包括电极加热、炉壁散热、钢水辐 射等,以评估炉内的热平衡状态。
热传导模型
研究钢水在炉内的热传导过程,考虑钢水的对流、传导和辐射传热 ,以及电极和炉渣的热影响。
LF炉精炼过程钢水温度预报模型

Science &Technology Vision科技视界LF 炉具有投资少,功能强的特点,因此近年来被广泛采用。
LF 炉主要功能是在非氧化性气氛下,通过电弧加热制造高碱度还原渣,并从钢包底部吹入惰性气体,强化精炼反应,进行钢液的脱氧、脱硫、合金化等冶金反应,以净化钢液、调整钢液温度和合金成分、促进钢液温度和合金成分的均匀化,从而达到生产工艺和钢种质量的要求。
LF 炉精炼过程钢水温度模型是建立在对LF 炉精炼工艺和功能深入理解的基础上,结合现代自动控制技术,采用先进的算法,开发出钢包精炼炉温度预报模型。
可以有效地提高自动化水平,提高生产效率,降低劳动强度,减少生产成本,并获得优质的钢水。
1LF 温度模型简介LF 温度模型主要有如下功能:根据钢液温度已有的实际测量值与采取的工艺操作,实时推定钢液的当前温度和预报未来时刻钢液的温度,并根据所预报的在标准处理时刻钢液的温度与目标温度的差值计算需要的通电量。
操作人员根据模型所提供的信息,可以有效的对处理过程进行控制,减少通电升温的次数,提高处理终了温度的命中率,同时能够稳定操作,缩短处理周期。
为了计算方便,将所有事件的发生时刻,如加合金与脱硫剂时刻、通电加热开始结束时刻转化成相对时间。
相对时间即为事件的发生时间与LF 炉处理开始时间的差值,如处理开始时刻即为相对时刻0,处理开始1分钟为相对时刻1。
2LF 温度模型的基本构成2.1温度模型的基本结构假定钢液的温度随时间的变化函数为T(t),T(t)包括以下几部分:T (t )=Ts+T NATURAL (t )+T ALLOYS +T HEAT +T LASLEB (t )+T FW +T ELSE +T SELFTS :温度的实际测量值或者是由前工序温度计算出的钢水的初始温度;T NATURAL (t ):自然温降;T ALLOYS :合金及脱硫剂的加入对钢液温度的影响;T HEAT :通电加热对钢液温度的影响;T LASLEB (t ):钢包热状态及冷钢重量对钢液温度的影响;T FW :喂丝对钢液温度的影响;T ELSE :其它因素对钢液温度的影响,暂时预留;T SELF :温度模型中自适应量,暂时预留。
LF钢包精炼炉工艺技术操作规程
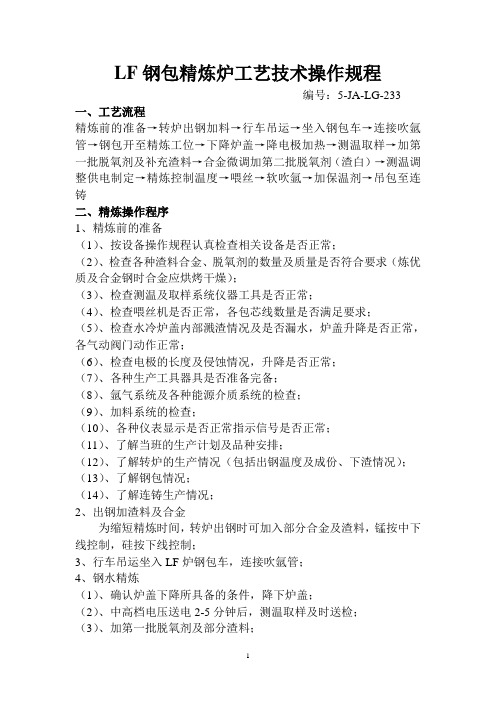
LF钢包精炼炉工艺技术操作规程编号:5-JA-LG-233 一、工艺流程精炼前的准备→转炉出钢加料→行车吊运→坐入钢包车→连接吹氩管→钢包开至精炼工位→下降炉盖→降电极加热→测温取样→加第一批脱氧剂及补充渣料→合金微调加第二批脱氧剂(渣白)→测温调整供电制定→精炼控制温度→喂丝→软吹氩→加保温剂→吊包至连铸二、精炼操作程序1、精炼前的准备(1)、按设备操作规程认真检查相关设备是否正常;(2)、检查各种渣料合金、脱氧剂的数量及质量是否符合要求(炼优质及合金钢时合金应烘烤干燥);(3)、检查测温及取样系统仪器工具是否正常;(4)、检查喂丝机是否正常,各包芯线数量是否满足要求;(5)、检查水冷炉盖内部溅渣情况及是否漏水,炉盖升降是否正常,各气动阀门动作正常;(6)、检查电极的长度及侵蚀情况,升降是否正常;(7)、各种生产工具器具是否准备完备;(8)、氩气系统及各种能源介质系统的检查;(9)、加料系统的检查;(10)、各种仪表显示是否正常指示信号是否正常;(11)、了解当班的生产计划及品种安排;(12)、了解转炉的生产情况(包括出钢温度及成份、下渣情况);(13)、了解钢包情况;(14)、了解连铸生产情况;2、出钢加渣料及合金为缩短精炼时间,转炉出钢时可加入部分合金及渣料,锰按中下线控制,硅按下线控制;3、行车吊运坐入LF炉钢包车,连接吹氩管;4、钢水精炼(1)、确认炉盖下降所具备的条件,降下炉盖;(2)、中高档电压送电2-5分钟后,测温取样及时送检;(3)、加第一批脱氧剂及部分渣料;(4)、化验结果报回成份微调,加入第二批脱氧剂;(5)、根据测温结果调整供电制度(过程温度控制按高于处理目标温度10℃左右控制,需深度脱硫的炉次可适当提高温度10-20℃);(6)、渣量配比及造渣制度①.渣料配比:石灰:萤石=5-6:1(或加入专用精炼渣);②.造渣制度:一般钢,渣料加入量:10-15千克/吨钢,深脱硫钢渣料加入量15-20千克/吨钢(全部渣量不超过25千克/吨钢,包括转炉下渣量);(7)、白渣操作①.加料3-5分钟第一批融化良好,加入第一批脱氧剂(加入总量的三分之二),当加料成分微调后此时钢渣应变黄白色,同时泡沫渣已形成接着加入第二批脱氧剂(加入总量的三分之一)约3-5分钟后,钢渣应全部变为白渣(有些低碳钢种渣呈黄白色);②.精炼期至渣料变白的时间约为10-15分钟,保持白渣时间应大于10分钟;(8)、合金调整①.合金成分调整应在黄白渣或白渣条件下进行;②.合金加入顺序应按元素活泼程度的先后顺序加入;③.合金加入量计算加入量=钢水量*(目标值-实际值)/合金元素含量*收得率;④.合金元素含量控制遵守以下原则:合金元素调整按规格中线控制,连浇炉次钢水成份要考虑上、下炉次间成份偏差,〔C〕≤0.02%,〔Mn〕≤0.10%,〔Si〕≤0.05%;(9)、在加入合金及增碳剂后要适当加大吹氩量(但钢渣不要破顶)。
LF精炼工艺和效果的研究
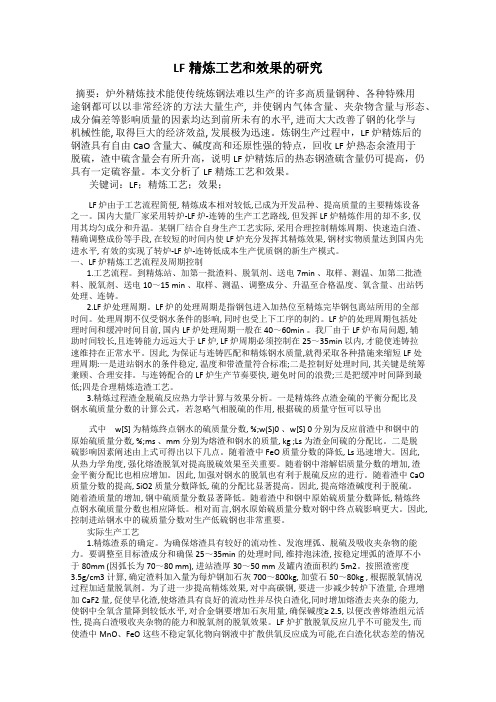
LF精炼工艺和效果的研究摘要:炉外精炼技术能使传统炼钢法难以生产的许多高质量钢种、各种特殊用途钢都可以以非常经济的方法大量生产, 并使钢内气体含量、夹杂物含量与形态、成分偏差等影响质量的因素均达到前所未有的水平, 进而大大改善了钢的化学与机械性能, 取得巨大的经济效益, 发展极为迅速。
炼钢生产过程中,LF 炉精炼后的钢渣具有自由CaO 含量大、碱度高和还原性强的特点,回收LF 炉热态余渣用于脱硫,渣中硫含量会有所升高,说明LF 炉精炼后的热态钢渣硫含量仍可提高,仍具有一定硫容量。
本文分析了LF精炼工艺和效果。
关键词:LF;精炼工艺;效果;LF 炉由于工艺流程简便, 精炼成本相对较低,已成为开发品种、提高质量的主要精炼设备之一。
国内大量厂家采用转炉-LF 炉-连铸的生产工艺路线, 但发挥LF 炉精炼作用的却不多, 仅用其均匀成分和升温。
某钢厂结合自身生产工艺实际, 采用合理控制精炼周期、快速造白渣、精确调整成份等手段, 在较短的时间内使LF 炉充分发挥其精炼效果, 钢材实物质量达到国内先进水平, 有效的实现了转炉-LF 炉-连铸低成本生产优质钢的新生产模式。
一、LF 炉精炼工艺流程及周期控制1.工艺流程。
到精炼站、加第一批渣料、脱氧剂、送电7min 、取样、测温、加第二批渣料、脱氧剂、送电10~15 min 、取样、测温、调整成分、升温至合格温度、氧含量、出站钙处理、连铸。
2.LF 炉处理周期。
LF 炉的处理周期是指钢包进入加热位至精炼完毕钢包离站所用的全部时间。
处理周期不仅受钢水条件的影响, 同时也受上下工序的制约。
LF 炉的处理周期包括处理时间和缓冲时间目前, 国内LF 炉处理周期一般在40~60min 。
我厂由于LF 炉布局问题, 辅助时间较长,且连铸能力远远大于LF 炉, LF 炉周期必须控制在25~35min 以内, 才能使连铸拉速维持在正常水平。
因此, 为保证与连铸匹配和精炼钢水质量,就得采取各种措施来缩短LF处理周期:一是进站钢水的条件稳定, 温度和带渣量符合标准;二是控制好处理时间, 其关键是统筹兼顾、合理安排。
lf炉精炼研究总结(总结-包括供电制度、吹氩制度、温度控制等)
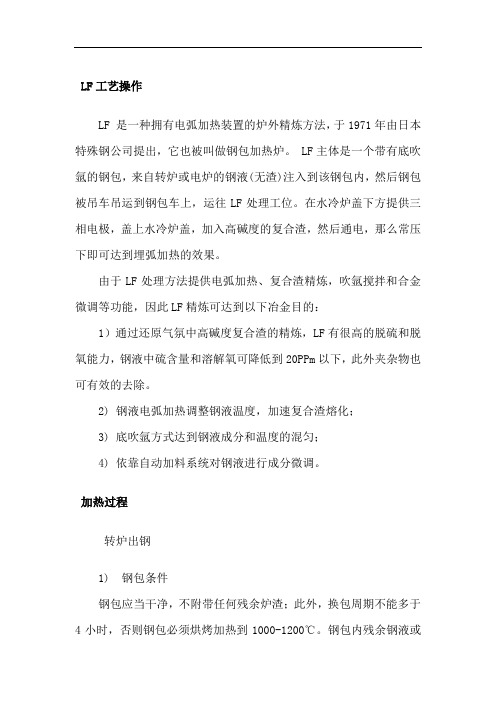
LF工艺操作LF 是一种拥有电弧加热装置的炉外精炼方法,于1971年由日本特殊钢公司提出,它也被叫做钢包加热炉。
LF主体是一个带有底吹氩的钢包,来自转炉或电炉的钢液(无渣)注入到该钢包内,然后钢包被吊车吊运到钢包车上,运往LF处理工位。
在水冷炉盖下方提供三相电极,盖上水冷炉盖,加入高碱度的复合渣,然后通电,那么常压下即可达到埋弧加热的效果。
由于LF处理方法提供电弧加热、复合渣精炼,吹氩搅拌和合金微调等功能,因此LF精炼可达到以下冶金目的:1)通过还原气氛中高碱度复合渣的精炼,LF有很高的脱硫和脱氧能力,钢液中硫含量和溶解氧可降低到20PPm以下,此外夹杂物也可有效的去除。
2) 钢液电弧加热调整钢液温度,加速复合渣熔化;3) 底吹氩方式达到钢液成分和温度的混匀;4) 依靠自动加料系统对钢液进行成分微调。
加热过程转炉出钢1) 钢包条件钢包应当干净,不附带任何残余炉渣;此外,换包周期不能多于4小时,否则钢包必须烘烤加热到1000-1200℃。
钢包内残余钢液或炉渣会引起钢包温降,失去的热量需LF处理补偿,这些因素在LF电脑模型中都需要考虑进去。
2) 挡渣转炉出钢需要进行挡渣,众所周知转炉顶吹终点,钢液中存在一定含量的溶解氧,它与渣中氧保持平衡。
渣中FeO 和 P2O5含量很高。
当还原剂加入钢包钢液中溶解氧含量降低,钢渣间的氧平衡被打破,渣中 FeO 含量减小。
因为炉渣的氧化性降低,发生回磷现象。
因此为了阻止钢液回磷和保证稳定的LF加热过程,转炉出钢要求挡渣。
3)合金和造渣剂的添加为保证钢液成分,出钢过程中需加入合金和还原剂。
LF加热过程钢包精炼工艺包括几个过程,彼此间相互关联。
对于不同钢种,加热操作不尽相同,且处理过程参数均有相关的标准计算模型。
步骤A:搅拌当钢包抵达LF处理位,接通自动快换接头向钢包提供氩气,根据钢种选择不同的吹氩模式。
a) 吹氩量: 150~300Nl/min步骤B:混匀依据钢种提供不同的混匀方法a) 吹氩量: 300~600Nl/minb) 还原剂:硅铁,铝丸不同混匀模式中,还原剂用量是一定的 (~TS).这个步骤分为两个加热阶段,第一阶段持续1分钟,加热速度越慢越好,温度上升大约3℃/mi n,这是起弧阶段。
120吨LF钢包精炼炉短网及电气控制系统
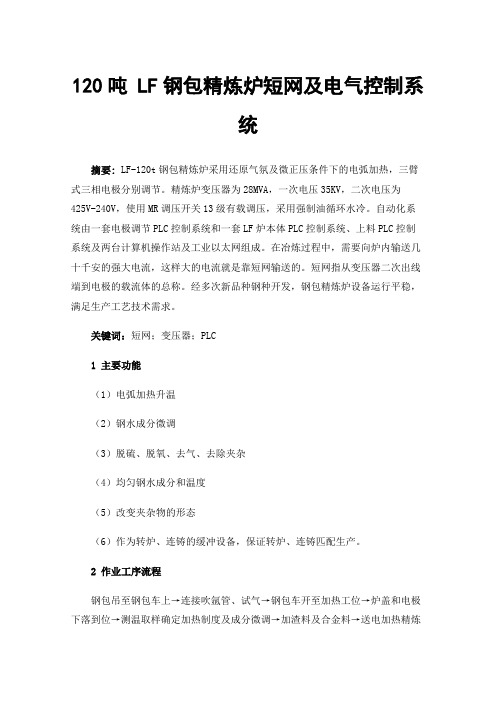
120吨 LF钢包精炼炉短网及电气控制系统摘要: LF-120t钢包精炼炉采用还原气氛及微正压条件下的电弧加热,三臂式三相电极分别调节。
精炼炉变压器为28MVA,一次电压35KV,二次电压为425V-240V,使用MR调压开关13级有载调压,采用强制油循环水冷。
自动化系统由一套电极调节PLC控制系统和一套LF炉本体PLC控制系统、上料PLC控制系统及两台计算机操作站及工业以太网组成。
在冶炼过程中,需要向炉内输送几十千安的强大电流,这样大的电流就是靠短网输送的。
短网指从变压器二次出线端到电极的载流体的总称。
经多次新品种钢种开发,钢包精炼炉设备运行平稳,满足生产工艺技术需求。
关键词:短网;变压器;PLC1主要功能(1)电弧加热升温(2)钢水成分微调(3)脱硫、脱氧、去气、去除夹杂(4)均匀钢水成分和温度(5)改变夹杂物的形态(6)作为转炉、连铸的缓冲设备,保证转炉、连铸匹配生产。
2作业工序流程钢包吊至钢包车上→连接吹氩管、试气→钢包车开至加热工位→炉盖和电极下落到位→测温取样确定加热制度及成分微调→加渣料及合金料→送电加热精炼→测温取样→炉盖、电极升起→钢包车开出加热工位→喂丝→加保温剂→软吹氩及气洗→断开吹氩管及吊出钢包3短网从变压器二次端头到电极的二次母线设备总称短网。
短网的电参数对精炼炉的正常运行起作决定性的作用,精炼炉的生产率、炉衬寿命、功率损耗及功率因数等在很大程度上都取决于短网的电参数的选择。
短网主要由水冷补偿器、水冷电缆、导电横臂、电极、电极夹持器等部件组成。
3.1短网具有以下特点(1)电流大。
在短网导体中流过几十千安乃至上百千安的强大电流,必将在短网导体四周形成强大的磁场,在短网导体及其四周的钢铁构件中降产生很大的功率损耗,引起发热。
(2)长度短。
整个短网长度,大型炉子不超过20米,由于短网损耗非常大,在设计时,(3)结构复杂。
短网各段导体的结构,形状不同,并联导体根数不同,排列方式也不同,因此,在进行短网的设计时,既要考虑集肤效应和邻近效应的影响,按规定的电流密度选择导体截面,又要注意导体的合理配置,最佳换位,使有效电感尽量减小,各导体电流均衡及各相参数尽量接近。
涟钢LF精炼温度变化研究
图1 L F处 理 前 温 度 频 率 分 布
2 2 精炼 处 理 时间 .
对 精炼总处 理时 间进 行 了统计 分析 见 图 1精炼 总处理 时间主要 集 中分 布在 3 5  ̄ , 5~ 0C
键, 钢水加热调温则是炼钢 与连铸之间的重 要工序 , 用 L 利 F炉 电 加 热 完成 调 温 功 能 是
使用 得较 多 的一 种 方式 。L F钢 包 炉 作 为 一 种精 炼方 法 已经成为 炼钢一 连铸 生产流 程 中
重要 的中间环 节 , 在 精炼 过 程 中对 温 度控 它
以钢包包 衬 温度 继 续 升高 , 吸收 热 量 导致 钢 水 温度 下降 。特别是 新钢包 投入 运转 的前 几 个循 环 , 由于包衬 温度更 低 , 其吸 收的热量 也 多, 对钢水 温度 的影 响也较 大 。 b钢 包包 口的散 热 : 包 在 运输 等待 过 。 钢 程中, 钢包 的上表 面 将 通过 辐 射 散 热 造 成钢 水 温降 。钢包运 输等 待时 间越长 , 温降 越大 。
涟钢 L F精炼温度 变化研究
2 0转 特 r 1
摘
邓 必荣
要
采用多元 回归分析方法建立 了涟 钢 20转炉厂 L 1 F钢 包炉精炼终点钢水 温度的变化模 型 , 应用该模型对 L F精炼终点钢水温度进 行预测 , 对预测 结果进行 了统计分析 , 结果 表 明该模型
对 L F钢包 炉精炼终点温度的预测误差较小 , 能对现场产生指导意义。
通 电 时 刚 m i n
图3 L F处 理 过 程 中总 通 电 时 间 频 率 分 布
始温度、 合金加入量等因素之间的回归关系。
2 1 精 炼前 钢水 温度 .
LF精炼技术
1 LF精炼目的
• 钢水温度满足连铸工艺要求; • 处理时间满足多炉连浇要求; • 成份微调能保证产品具有合格的成份及
实现最低成本控制; • 钢水纯净度能满足产品质量要求; • 均衡物流的手段; • 取消电炉还原期。
2 LF精炼工艺
• 电炉或转炉出钢→ 去渣→ 脱氧(加还原渣、加 脱氧剂)→ 加热(加合金、取样)→ 浇注
代入式(1)、(2)计算可得:
对 40t 钢液引起的钢液温降为 0.0075℃/min;
对 60t 钢液引起的钢液温降为 0.005℃/min;
对 80t 钢液引起的钢液温降为 0.0037℃/min。
由此可见,氩气吸热对钢液温降的影响完全可以忽略不计。
5.3.2 吹氩搅拌引起钢液温降分析
• 钢包包衬的蓄热
。
浇注温度
工艺要求:正常条件下,保护浇注温度为±5℃ ,浇注工可根据条件改变。
浇注过程中的成分偏差
工艺要求:成分最大偏差满足以下要求:C 0.03%;Mn 0.12%,Si 0.1% CEQ 0.03%。
存在问题:如果钢成分不在成分偏差的最大范围,钢质量降级。
•N
精炼结束后,钢包吊往连铸。
• 工艺过程中应注意
规程。操作者应该能生产规定的所有钢种。
6 控制设备 测温枪、定氧仪、合金称量设备及喂线机被控制并按计划校准。
3 LF工艺过程操作要点
• 根据钢液中酸溶铝的要求及钢液中溶解氧控制加铝 量的喂铝线操作;
• 考虑埋弧加热、脱硫、吸附夹杂物的造渣操作;
• 考虑防止吸气、卷渣以及加快夹杂物去除的最佳搅 拌模型控制的吹氩搅拌处理;
•C
钢包到钢包炉等待位置后,钢包炉处吹氩接通,吹 氩时保证不裸露钢液面,但当要从料仓加料时,增加 氩气流量,吹开渣面,料加到裸露的钢液面上。
精炼工艺和设备介绍LF
设备组成:电气设备
高压设备 变压器 基础自动化及控制画面系统 仪表设备
设备组成:辅助设备
钢包台车 喂丝系统 测温取样装置 钢包底吹氩系统 电极接长和储放站 事故吹氩枪 加料溜槽系统 保温剂投入装置
LF钢包精炼炉精炼工艺
LF作为转炉的炉外精炼设备,对转炉的初炼钢 水进行温度控制、合金微调、脱氧、脱硫以及 对钢水成份和温度均匀化等精炼处理。与连铸 机配合时,LF在转炉与连铸机之间起到缓冲作 用,向连铸机及时提供合格钢水。
钢包运输
行车将钢包吊至LF钢包台车上,此时, 钢包底部吹氩管路自动接通,并开始吹 氩搅拌。在此工位,LF处理前的各项准 备就绪,如:电极准备、设备确认、通 电准备、冷却水准备、合金及辅材准备、 液压准备。完成之后,钢包台车开到LF 处理工位。
钢包处理
钢包被运到LF处理工位后,进行钢包处 理: 人工手动或自动测定渣厚、炉盖下 降、吹氩操作,吹氩搅拌的强度根据模 型调整,通过人工确认,并且全程吹氩。
Lቤተ መጻሕፍቲ ባይዱ处理
在达到目标温度和化学成分后精炼完成。 然后电极提升,炉盖提升,钢包台车从 精炼工位开到保温剂投入工位,投入保 温剂后台车开至钢包起吊工位,由行车 运到连铸机。开至钢包起吊工位,由行 车吊运到连铸机浇铸。
LF处理
钢水首次加温是为了使温度和化学成分均匀以 及熔渣。如果必须的话,进一步添加合成渣。 渣料熔化后,测温取样,接着继续升温。根据 试样分析的结果和钢种目标值,LF计算机算出 需要加入的LF的物料种类和物料量,并将指令 发送至上料系统PLC,该系统可根据LF计算机 指令在规定时间向LF加入规定牌号的剂量的造 渣料或铁合金并加入到钢包中。对有特殊要求 的钢种,可进行额外的加合金步骤,喂丝,软 搅拌纯净处理,或者液态钢水仅仅放在LF直到 下道工序准备接收("缓冲功能")。
lf炉精炼工艺流程
lf炉精炼工艺流程
《lf炉精炼工艺流程》
LF炉(Ladle Furnace)是钢铁冶炼过程中的重要设备,用于
对钢水进行精炼处理,以提高钢水的质量和纯度。
LF炉精炼
工艺是通过控制冶炼过程中的温度、化学成分和气体成分,达到减少氧化物和非金属夹杂物的目的。
首先,钢水被倒入LF炉的中部容器中,然后通过底部的电极
加热钢水到一定温度。
在加热过程中,通入适量的吹气量,以氧化非金属夹杂物。
随着温度的升高,非金属夹杂物逐渐被氧化,减少对钢水质量的影响。
接着,通过对氧气的控制,调整钢水中的碳含量和氧化还原平衡。
在一定的氧气条件下,钢水中的碳含量可以得到控制和调整,以满足不同材质的需求。
最后,对钢水进行搅拌,促使温度、成分和气相的均匀分布,使钢水的质量得到进一步改善。
随后,再将精炼后的钢水倒出,用于连铸或其他下游生产工艺。
总的来说,LF炉精炼工艺流程通过对温度、化学成分和气体
成分的控制,实现了对钢水质量的精炼和提升,为后续钢材生产提供了更优质的原料。
- 1、下载文档前请自行甄别文档内容的完整性,平台不提供额外的编辑、内容补充、找答案等附加服务。
- 2、"仅部分预览"的文档,不可在线预览部分如存在完整性等问题,可反馈申请退款(可完整预览的文档不适用该条件!)。
- 3、如文档侵犯您的权益,请联系客服反馈,我们会尽快为您处理(人工客服工作时间:9:00-18:30)。
LF精炼过程的钢水温度控制
1前言:
近年来,随着洁净钢冶炼技术的发展,LF作为主要的炉外精炼手段,在洁净钢冶炼过程中得到
了广泛应用,其生产技术也在不断地完善和发展。
同电弧炉相比,LF的熔池要深得多,
为了保证连铸的生产顺行,LF冶炼过程的温度控制是其主要冶炼目标之一,因此其加热过程的温度控制显得非常重要。
本文在分析LF炉能量平衡的基础上,进行了LF精炼过程温度控制工业试验,对实现LF炉内钢液处理温度的合理控制有着重要意义。
2影响LF冶炼过程钢水温度变化的因素
2 .1由于LF化学反应热效应很小,可以忽略不计,因此为LF炉提供的能量只有从变压器输出的电能,即变压器的有功功率e。
变压器二次侧输出的电能,一部分功率被线路上存在的电阻消耗掉,称之为线路损失的功率r,另一部分转变为电弧热量即电弧功率arc。
由电弧产生的热能arc 一部分传给熔池(炉渣和钢水),另一部分损失掉,传递给包衬和水冷包盖ar。
而电弧电能传给熔池的比例主要取决于电弧埋入炉渣的深度。
进入熔池的热量ab又可分为三大去向。
第一部分用于钢水和炉渣的加热升温所需热量m和渣料及合金熔化升温所需热量ch,两者之和即为加热熔池的热量bath。
第二部分是指通过包衬损失的热量ls,其中又分成两部分,一部分热量成为包衬耐火材料的蓄热ln而使包衬温度升高,另一部分是由包壳与周围大气的热交换而损失的热量shell。
第三部分热量是通过渣面损失的热量sa,其中一部分是通过渣面的辐射和对流传热的热损sl,另一部分是由熔池内产生的高温气体通过渣面排走的热量g。
上述分析可以清楚地表LF炉能量的输入和输出及其分配关系。
在LF炉的操作过程中,由于上述因素相互作用、相互影响,因此,其实际的温度控制较为复杂。
3 LF炉温度控制试验3. 1试验内容为了实现LF炉稳定的温度控制,首先根据150tLF炉的供电系统特点及电阻与电抗值,结合电、热参数绘制出不同电压下“电热特性曲线”,根据理论计算确定的工作点,对Q235A钢种进行了LF炉冶炼试验,试验安排及结果见表1。
图21#电热特性曲线表1比较实验结果序号工作点钢液重量/t加热时间/min温升/℃升/℃温·速m 度in11)热率效2)注备1283224135.715151530232.0/1.75 11.53/1.340.3970.323化渣2282432156.5101010122 41.2/1.212.4/2.420.2920.521化渣3283224158.810 101012131.2/1.231.3/1.330.2700.322化渣4283224 160.810101017251.7/1.762.5/2.590.3750.590化渣528243215710779101.29/1.301.43/1.450.3000.3 16化渣6282432152.815151521301.4/1.382.0/1.970 .3260.424化渣7283224159.51010109100.9/0.931.0 /1.030.2110.239化渣注:1)分母为折合成155t钢水时的升温速度;2)因忽略炉渣吸收的热量,使此值小于实际LF炉热效率。
3.2试验结果分析从表2中可以看出,在化渣期结束后,由于在试验条件下LF炉没有采用造埋弧渣等提高LF炉热效率的措施,LF炉的升温效率较低,化渣后的升温速度波动在0.93~2.59℃/min之间,平均升温速度仅为1.6℃/min。
LF炉的平均热效率在0.36以上,此时钢包的热效率为0.40~0.4 5。
工作点24、28、32kA,单位时间消耗的电功率依次明显增加,但工作点在24,32 kA时的升温速度相当,即表2中7炉中有3炉比较接近,有4炉差距较大。
由于受操作过程多种因素的影响,如钢种、钢包烘烤、转炉出钢温度、钢液的运输以及精炼时间等影响,试验过程中工作点对升温速度的影响规律不明显。
因此,对冶炼温度的控制应不仅仅考虑供电制度的控制,还应考虑冶炼过程中其他因素对温度的影响加以综合控制。
LF精炼过程的钢水温度控制实验图3、图4分别为该厂150tLF进站钢水温度和出站温度分布
情况。
从图3中可以看出,LF进站温度主要分布在1550~1590℃
图4中可以看出,LF 出站温度84.1%的炉次分布在1560~1600
从进站和出站的平均温度差值看,LF精炼过程的平均升温幅度仅为5.2℃。
按上述试验结果, 平均升温速度为1.6℃/min计算,纯升温时间为3.25min。
但是,实际LF操作过程并非如此,由于影响LF 炉钢液温度的因素较多,且LF进站温度波动范围较大,最高和最低温度的差值接近100℃,造成各炉次间的升温时间差别很大,其纯升温时间通常达到15min以上,甚至达到30min以上。
而对于深脱硫钢种,其整个冶炼周期经常达到50min以上,这是远远满足不了多炉连浇要求的,对LF炉稳定的工艺控制也是非常不利的。
图3LF进站温度图4 LF出站温度该LF炉的设计最大升温速度为4℃/min,而目前的平均升温速度仅为 1.6℃/min,与设计值存在较大差距,因此可见,对该工艺过程的优化还有很大的潜力。
LF 装置热效率由0.36提高到0.4,使加热速率提高15%,将进一步缩短加热时间、降低电耗。
5结论
(1 ) 通过分析LF冶炼过程的能量平衡系统图,得到了LF炉能量的输入和输出及其分配关系。
(2 ) 通过对计算LF装置的电阻与电抗值,结合电、热参数绘制出不同电压下电热特性曲线,对于L F炉供电制度的制定有着重要的指导意义。
(3) 进行LF温度控制试验,得到150tLF炉平均升温速度为1.6℃/min,平均热效率在0.36以上,钢包本体热效率为0.40~0. 45。
(4) 单纯考虑供电制度,无法满足LF的温度控制要求,建议采取诸如加强钢包衬的绝热、充分烤包、减少LF炉的散热以及造好泡沫渣等措施,提高LF冶炼过程的温度控制效率。
LF精炼过程的钢水温度控制
参考:
@张慧书$东北大学材料与冶金学院!辽宁沈阳110004
@战东平$东北大学材料与冶金学院!辽宁沈阳110004
@姜周华$东北大学材料与冶金学院!辽宁沈阳110004LF;;精炼;;温度;;炼钢在对L F能量平衡分析的基础上,进行150tLF温度控制试验。
试验结果表明,单纯考虑供电制度的选择无法满足LF的温度控制要求,必须进行综合控制研究。
<1>傅杰.发展我国钢的二次精炼技术的建议.特殊钢,1999,20(增刊):23-25.
<2>万真雅.LF炉精炼GCr15轴承钢的温度制度.华东冶金学院学报,1992,(9):7-12.
<3>李晶.钢包精炼过程中钢水成分微调及温度.预报钢铁研究学报,1999,11(2):6-8.
<4>武拥军,姜周华,姜茂发.LF炉精炼过程钢水温度预报技术.东北大学学报(自然科学版),2002,23(3):247-250.
<5>OLIKA B BO B.Prediction of Steel Temperature in Ladle Through Time/Temperature Simulation.Scand JMetallurgy,1993,(22):219-231.
<6>TOMAZIN C E,UPTON E A,WALLIS R A.The Effect of Ladle Refractories and Practice on Steel Temperature Control.Steelmaking Proceedings,1986,(69):223-230.
<7>唐东.LF炉热效率和电极消耗的研究.沈阳:东北大学,2002.17-22.F 装置的电阻与电抗值,结合电、热参数绘制出不同电压下电热特性曲线,对于LF炉供电制度的制定有着重要的指导意义。
(3)进行LF温度控制试验,得到150tLF炉平均升温速度为1. 6℃/min,平均热效率在0.36以上,钢包本体热效率为0.40~0.45。
(4)单纯考虑供电制度,无法满足LF的温度控制要求,建议采取诸如加强钢包衬的绝热、充分烤包、减少LF炉的散热以及造好泡沫渣等措施,提高LF冶炼过程的温度控制效率。
LF精炼过程的钢水温度控制@张慧书$东北大学材料与冶金学院!辽宁沈阳110004
@战东平$东北大学材料与冶金学院!辽宁沈阳110004
@姜周华$东北大学材料与冶金学院!辽宁沈阳110004LF;;精炼;;温度;;炼钢在对L F能量平衡分析
的基础上,进行150tLF温度控制试验。
试验结果表明,单纯考虑供电制度的选择无法满足LF的温度控制要求,必须进行综合控制研究。
<1>傅杰.发展我国钢的二次精炼技术的建议.特殊钢,1999,20(增刊):23-25.
<2>万真雅.LF炉精炼GCr15轴承钢的温度制度.华东冶金学院学报,1992,(9):7-12.
<3>李晶.钢包精炼过程中钢水成分微调及温度.预报钢铁研究学报,1999,11(2):6-8.
<4>武拥军,姜周华,姜茂发.LF炉精炼过程钢水温度预报技术.东北大学学报(自然科学版),2002,23(3):247-250.。