事故后果模拟分析
氢气气瓶爆炸事故后果模拟分析

氢气气瓶爆炸事故后果模拟分析摘要:氢气是一种极易燃烧,无色透明、无臭无味的气体,广泛的应用于化工、冶金、电力、食品、电子等多种行业,氢气通常以压缩气体的形式盛装在气瓶中。
本文通过对氢气气瓶物理爆炸进行事故后果模拟分析,为使用氢气气瓶的单位提供参考。
关键词:氢气气瓶物理爆炸事故后果模拟1 氢气的危险性分析氢气为无色、无臭的气体,沸点-252.8℃,气体密度0.0899g/L,极易燃。
氢气广泛的应用于化工、冶金、电力、食品、电子等多种行业,通常以压缩气体的形式盛装在气瓶中。
氢气气瓶属于压力容器,由于气瓶质量不合格或储存使用不当等均可能会导致气瓶发生爆炸事故。
氢气瓶爆炸属于物理爆炸,物理爆炸就是物质状态参数(温度、压力、体积)迅速发生变化,在瞬间释放出大量能量并对外做功。
气瓶爆炸时,气体膨胀所释放的能量不仅与气体压力和容器的容积有关,而且与介质在容器内的物性相态相关。
容积与压力相同而相态不容的介质,在容器破裂时产生的爆破能量也不同,而且爆炸过程也不完全相同,其能量计算公式也不同。
2 事故后果模拟2.1 气瓶爆炸事故后果模拟1、气瓶爆炸能量计算氢气瓶中的氢气是以气态形式存在而发生物理爆炸,爆炸的能量与气瓶内气体的压力和体积有关,其释放的爆炸能量的计算公式为:式中:Eg—气体的爆炸能量,kJ;P—容器内的绝对压强,MPa;V—容器的容积,m3;k—气体的绝热指数,即气体的定压比热与定容比热之比。
2、爆炸冲击波及其伤害、破坏作用压力容器爆炸时,能量向外释放时以冲击波能量、破片能量和容器残余变形能量3种形式表现出来,但后两者所消耗的能量只占总能量的3%~15%,即绝大部分的能量以冲击波的形式释放,冲击波是由压缩波叠加形成的,是波阵面以突进形式在介质中传播的压缩波。
超压准则认为,只要爆炸波的超压达到一定值,便会对建筑物构件及各种生物造成一定程度的破坏或损伤。
超压冲击波对人体的伤害和对建筑物的破坏作用见表2.1-1和表2.1-2。
2事故后果模拟分析讲解

2事故后果模拟分析讲解事故后果模拟分析是指通过对事故发生后可能产生的各种后果进行系统模拟和分析,以评估事故对环境、人员和财产等方面可能造成的影响和损失。
通过这样的分析,可以帮助企业和政府机构采取相应的应对措施,减少潜在的事故风险。
事故后果模拟分析的目的是对事故后可能发生的各种后果进行全面、客观的评估和预测,以便为事故应急预案和风险管理提供科学依据。
其基本思路是通过建立适当的模型,模拟分析事故发生后可能引发的各种后果,如物质泄漏、火灾爆炸、环境污染、人员伤亡等,从而揭示事故的潜在影响范围和强度,并提出相应的控制和应对措施。
事故后果模拟分析的方法主要分为定量方法和定性方法两种。
定量方法是通过建立适当的物理、数学或统计模型,对事故发生后可能产生的后果进行量化分析。
这种方法需要充分考虑各种因素的影响和相互作用,如事故规模、周围环境、气象条件等。
通常通过模拟和计算来得到事故后的后果值,如损失金额、人员伤亡数量等。
定量方法可以提供比较准确的数值结果,但对数据和模型的要求较高。
定性方法是通过专家经验和专业知识来对事故后果进行评估和预测。
这种方法主要依靠专家的判断和分析,通过专家讨论、问卷调查、案例分析等方式来获取相关信息。
然后通过专家评价或专家打分等方法,对事故后果进行定性描述和排序。
定性方法具有灵活性强、成本较低的优点,但受主观因素的影响较大,结果可能存在一定的不确定性。
事故后果模拟分析的实施过程主要包括以下几个步骤:第一步,确定分析目标和范围。
明确需要分析的事故类型、区域范围、关注的后果等,以便有针对性地采集和处理相关数据。
第二步,收集和整理所需数据。
收集和整理有关事故和后果的数据,包括事故发生地的地理信息、设备参数、周围环境信息、气象数据、人员伤亡和财产损失等。
数据的准确性和完整性对分析结果的可靠性起着决定性作用。
第三步,建立模型和参数设定。
根据分析目标和范围,建立适当的模型和计算方法,将数据应用于模型中,设定相应的参数和假设条件,以便进行后续的模拟和分析。
蒸汽云爆炸事故后果模拟分析法
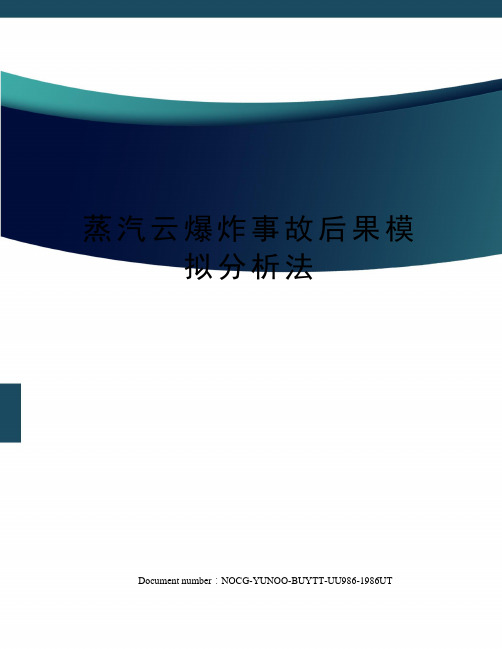
蒸汽云爆炸事故后果模拟分析法Document number:NOCG-YUNOO-BUYTT-UU986-1986UT蒸汽云爆炸事故后果模拟分析法超压:1)TNT当量通常,以TNT当量法来预测蒸气云爆炸的威力。
如某次事故造成的破坏状况与kgTNT炸药爆炸所造成的破坏相当,则称此次爆炸的威力为kgTNT当量。
蒸气云爆炸的TNT当量W TNT计算式如下:W TNT=×α×W f×Q f/Q TNT式中,W TNT—蒸气云的TNT当量(kg)α—蒸气云的TNT当量系数,正己烷取α=;W f—蒸气云爆炸中烧掉的总质量(kg)Q f—物质的燃烧热值(kJ/kg),正己烷的燃烧热值按×106J/kg,参与爆炸的正己烷按最大使用量792kg计算,则爆炸能量为×109J将爆炸能量换算成TNT当量q,一般取平均爆破能量为×106J/kg,因此W TNT= ×α×W f×Q f /q TNT+ =××792××106/×106=609kg2)危害半径为了估计爆炸所造成的人员伤亡情况,一种简单但较为合理的预测程序是将危险源周围划分为死亡区、重伤区、轻伤区和安全区。
死亡区内的人员如缺少防护,则被认为将无例外的蒙受重伤或死亡,其内径为0,外径为R ,表示外周围处人员因冲击波作用导致肺出血而死亡的概率为,它与爆炸量之间的关系为:= m重伤区的人员如缺少防护,则绝大多数将遭受严重伤害,极少数人可能死亡或受伤。
其内径就是死亡半径R1,外径记为R2,代表该处人员因冲击波作用耳膜破损的概率为,它要求的冲击波峰值超压为44000Pa。
∆按下式计算:冲击波超压P∆=++式中:P∆——冲击波超压,Pa;PZ——中间因子,等于;E——蒸气云爆炸能量值,J;P0——大气压,Pa,取101325得R2=轻伤区的人员如缺少防护,则绝大多数将遭受轻微伤害,少数人将受重伤或者平安无事。
氯气泄漏重大事故后果模拟分析

国内外统计资料显示,因防爆装置不作用而造成焊缝爆裂或大裂纹泄漏的重大事故概率仅约为×10-7~×10-8/年左右,一般发生的泄漏事故多为进出料管道连接处的泄漏;据我国不完全统计,设备容器一般破裂泄漏的事故概率在1×10-5/年;此外,据储罐事故分析报道,储存系统发生火灾爆炸等重大事故概率小于1×10-6,随着近年来防灾技术水平的提高,呈下降趋势;第七章氯气泄漏重大事故后果模拟分析危险区域的确定概述:泄漏类型分为连续泄漏小量泄漏和瞬间泄漏大量泄漏,前者是指容器或管道破裂、阀门损坏、单个包装的单处泄漏,特点是连续释放但流速不变,使连续少量泄漏形成有毒气体呈扇形向下风扩散;后者是指化学容器爆炸解体瞬间、大包装容器的泄漏、许多小包装的多处泄漏,使大量泄漏物形成一定高度的毒气云团呈扇形向下风扩散;氯泄漏后虽不燃烧,但是会造成大面积的毒害区域,会在较大范围内对环境造成破坏,致人中毒,甚至死亡;根据不同的事故类型、氯气泄漏扩散模型,危害区域会有所不同;氯设备泄漏、爆炸事故概率低,一旦发生可造成严重的后果;以下液氯钢瓶中的液氯泄漏作为事故模型进行危险区域分析;毒害区域的计算方法:1设液氯重量为Wkg,破裂前液氯温度为t℃,液氯比热为C kj/kg .℃,当钢瓶破裂时瓶内压力降至大气压,处于过热状态的液氯迅速降至标准沸点t0℃,此时全部液氯放出的热量为:Q=WCt-t0设这些热量全部用于液氯蒸发,如汽化热为qkj/kg,则其蒸发量W为:W=Q/q=WCt-t0/q氯的相对分子质量为M r,则在沸点下蒸发的液氯体积V g m3为:V g=M r273+t0/273V g =t-t0/ M r q273+t0 /273氯的有关理化数据和有毒气体的危险浓度如下:相对分子质量:71沸点: -34℃液体平均此热:kg.℃汽化热: ×102kj/kg吸入5-10mim致死浓度:%吸入-1h致死浓度: 吸入-1h致重病浓度:已知氯的危险浓度,则可求出其危险浓度下的有毒空气体积:氯在空气中的浓度达到%时,人吸入5~10min即致死;则V g m3的液氯可以产生令人致死的有毒空气体积为:V1 = V g×100/ = 1111V g m3氯在空气中的浓度达到~%时,人吸入~1h,则V g m3的液氯可以产生令人致死的有毒空气体积为:V2=V g×100/=23529V g m3氯在空气中的浓度达到~%时,人吸入~1 h,则V g m3的液氯可以产生令人致重病的有毒空气体积为:V3=V g×100/=57l43V g m3假设这些有毒空气以半球形向地面扩散,则可求出该有毒气体的扩散气体半径为:R=V g /C/1/2×4/3π1/3式中: R —有毒气体半径mV g—液氯的蒸汽体积m3C —有毒介质在空气中危险浓度值%液氯泄漏事故毒害区域模拟计算以一只液氯钢瓶1000kg发生严重泄漏事故后果计量如液氯泄漏量W =1000kg,环境温度瓶内t=250C,计算有毒气体扩散半径: 液氯蒸发热Q:Q = WCt-t0= 1000××25--34= 56640kj蒸发量W:W = Q/q= 56640/×102= 196kg液氯沸点下蒸发气体体积V g:V g = M r×273+t0/273= ×196/71×273+-34/ 273= m3氯气在致死的浓度C1的体积V1和有毒气体的扩散半径R1:V1 = V g×100/C1= ×100/= 60155m3R1 = V1/1/3= m氯气在致死的浓度c2时的体积V2和有毒气体的扩散半径R2: V2 = V g×100/c2= ×100/= 1273882 m3R2 = V2/1/3= m氯气在致重病的浓度c3时的体积v3和有毒气体的扩散半径R3 V3 = V g×100/C3= ×100/= 3093714m3R3 = V3/1/3= m氯气泄漏静风状态毒害区域:图9-1 氯钢瓶泄漏在静风状态下的毒害区域注:①吸入5~10mim浓度%的致死半径:R1= 30.62m②吸入~l h浓度%的致死半径:R2 = 84.73m③吸入~1 h浓度%的致重病半径:R3= 113.89m事故后果模拟分析及建议以上是以氯钢瓶严重泄漏造成的事故后果的模拟,其危害是相当严重的;由于该建设项目在用氯过程中,涉及用氯的设备设施有液氯钢瓶、液氯汽化器、氯管线、反应釜等,因此都可能存在氯的泄漏;风向决定毒气云团的扩散方向,风速决定毒气云团的下风向的扩散范围,气压和地形影响毒气对人的危害程度,如果空气流动性小、温度大,毒气在低洼处停留不易扩散,可造成人畜中毒,甚至死亡;氯气泄漏后,在有风的条件下,氯气通常呈60°左右的夹角向下风向扩散,在扩散的过程中由于空气的补充,浓度会逐渐降低,但相应下风向的防护距离增加;一般在小泄漏状态下泄漏量≤200L,首次隔离距离为30m,下风向撤离范围白天为0.3km,夜间为1.1km;在大量泄漏状态下泄漏量>200L,首次隔离距离为275m,下风向撤离范围白天为2.7km,夜间为6.8km;污染范围不明时先按上述方法确定防护距离,然后分段测试氯气浓度再调整防护距离;建议企业应制定针对氯泄漏的事故应急救援预案,如发生氯泄漏应立即启动预案,在日常过程中,加强氯设备设施的安全管理,严防氯的泄漏;常备抢修器材表和常备防护用品表如下:第七章劳动卫生预评价根据危险、有害因素分析本工程劳动卫生方面主要危害因素是毒物危害、噪声危害和生产性粉尘危害;本工程劳动卫生预评价采用某些企业类似生产装置检测数据作为类比值进行评价;毒物危害评价7.1.1 评价方法按照职业性接触毒物危害程度分级GB5044-85将职业性接触的毒物危害程度分为Ⅰ级极度危害、Ⅱ级高度危害、Ⅲ级中度危害、Ⅳ级轻度危害;根据有毒作业分级GB12331-90规定,以有毒作业分级指数法对本工程的有毒作业岗位进行评价;有毒作业分级指数法是根据毒物危害程度级别、有毒作业劳动时间及毒物浓度超标倍数三项指标,分别用D、L、B表示;依据三项指标求得指数,根据指数范围进行分级;具体做法是按照GB12331-90求出分级指数C;C=D·L·B式中:C—分级指数D—毒物危害程度级别权数L—有毒作业劳动实时间权数B—毒物浓度超标倍数1有毒作业危害分级级别表7.1.1 有毒作业分级级别表7.1.2 毒物危害程度级别权数3有毒作业劳动时间权数表7.1.3 有毒作业劳动时间权数B=Mc/Ms-1式中:Mc—测定毒物浓度均值mg/m3Ms—该种毒物最高容许浓度mg/m35有毒作业分级级别表根据有毒作业的毒物浓度超标倍数、毒物危害程度级别、有毒作业劳动时间三项指标,综合评价,制定出有毒作业分级级别表;当有毒作业工作地点空气中存在多种毒物中,应分别进行毒物作业的分级,以最严重的级别定级,同时注明其他生产性毒物作业的级别;表7.1.4 有毒作业分级表不懂7.1.2 毒物危害评价结果本项目中主要有毒物质有溴素、氯丙烯等,主要在相关生产岗位和储存岗位使用,可能形成有毒作业场所;以上毒性物质具体危害情况见危险化学品危险有害性分析;噪声危害评价7.2.1 评价内容本工程项目的主要噪声声源为物料输送的泵、压缩机、风机、粉碎机等;7.2.2 评价方法对原厂区装置噪声的类比数据进行分析计算,作为对本工程噪声危害程度的参考,在综合分析的基础上,与国家卫生标准进行比较分析做出评价,提出相应的对策措施;1噪声作业分级依据噪声作业危害程度级别进行噪声危害评价;噪声作业危害程度分级见表7.2.1;表7.2.1 噪声作业分级级别表7.2.2 工业地点噪声声级卫生限值GBZ1-20023噪声作业分级查表法为了简化噪声危害指数的计算过程,便于实际操作而采用此方法见表7.2.3第八章事故后果模拟分析事故后果分析是危险源危险性分析的一个主要组成部分,其目的在于定量的描述一个可能发生的重大事故对工厂、对厂内职工、对厂外居民甚至对环境造成危害的严重程度;华通化学最常见的事故是火灾、爆炸和中毒,本工程产品是精细化工产品,使用的危险化学品数量不大,而使用的有毒气体比较多,故本评价对有毒气体毒害区进行模拟分析,选择液氯和液氨液化气体容器破裂时毒害区进行估算,由于缺乏氟化氢的相关数据,故未作模拟分析;1液氯气瓶破裂时毒害区估算液氯是剧毒物质,使用气瓶包装,现对液氯气瓶破裂毒害区域进行分析估算;设有液氯气瓶中存有液氯1000kg,容器破裂前罐内液氯温度t为25℃,液氯的比热c为kg·℃,当容器破裂时器内压力降至大气压,处于过热状态的液氯温度迅速降到标准沸点t0为-34℃,此时全部液体所放出的热量为:设这些热量全部用于容器内液体的蒸发,汽化热Q为×102kj/kg,则蒸发量为:液氯分子量为M=71,则在沸点下蒸发的体积Vg:据查氯在浓度达到目前为%浓度时,吸入5~10min可致死,则Vg氯气可以产生令人致死的有害空气体积为V= Vg×100/=×100/=74988.89 m3假设这些有毒气体以半球型向地面扩散,则可求出氯气扩散半径为:由此液氯气瓶发生破裂事故引发有毒气体扩散,其毒害区半径为32.96 m;2液氨气瓶破裂时毒害区估算烟磺酰胺生产中使用液氨气瓶,如果发生意外液氨气瓶破裂可能发生蒸汽爆炸;液氨是有毒物质,爆炸后若不燃烧,便会造成大面积的毒害区域;一般情况液氨在补充时易发生事故,现对液氨气瓶毒害区域进行分析估算;液氨气瓶中存有液氨1000kg,容器破裂前罐内液氨温度t为25℃,液氨的比热c为kg·℃,当容器破裂时器内压力降至大气压,处于过热状态的液氨温度迅速降到标准沸点t0为-33℃,此时全部液体所放出的热量为:Q=W·ct-t0==500××25--33=133400kj设这些热量全部用于容器内液体的蒸发,汽化热Q为×103kj/kg,则蒸发量为:液氨分子量为M=17,则在沸点下蒸发的体积Vg:据查氨在浓度达到目前为%浓度时,吸入5~10min可致死,则Vg氨气可以产生令人致死的有害空气体积为V= Vg×100/=×100/=28031.63 m3假设这些有毒气体以半球型向地面扩散,则可求出氨气扩散半径为:由此液氨气瓶发生爆炸事故引发有毒气体扩散,其毒害区半径为30.38m;第四节事故树分析评价由于本项目为电解项目,涉及较多电气设备,发生人员触电的危险性较大,故采用事故树分析对用电系统进行专门评价;一、评价方法简介事故树分析FaultTreeAnalysis,所写FTA又称故障树分析,时一种演绎的系统安全分析方法;它时从要分析的特定事故或故障开始,层层分析其发生原因,一直分析到不能再分解为止;将特定的事故和各层原因危险因素之间用逻辑门符号连接起来,得到形象、简洁地表达其逻辑关系因果关系地逻辑树图形,即事故树;通过对事故树简化、计算达到分析、评价地目的;事故树分析方法可用于各种复杂系统和广阔范围的各类系统的可靠性及安全性分析、各种生产装置可靠性分析和伤亡事故分析等;二、事故树分析基本步骤1.确定分析对象系统和要分析的个对象事件顶上事件通过经验分析、事故树分析和故障类型和影响分析确定顶上事件何时、何地、何类;明确对象系统的边界、分析深度、初始条件、前提条件何不考虑条件,熟悉系统、收集相关资料工艺、设备、操作、环境、事故等方面的情况何资料;2.确定系统是个发生概率、事故损失的安全目标值3.调查原因事件调查与事故有关的所有直接原因和各种因素设备故障、人的失误和环境不良因素;4.编制事故树从顶上事件起,一级一级往下找出所有原因事件直到最基本的原因事件为止,按其逻辑关系画出事故树;每个顶上事件对应一株事故树;5.定性分析按事故树结果进行简化,求出最小割集和最小径集,确定各基本事件的结构重要度;6.定量分析找出各基本事件的发生概率,计算出顶上事件的发生概率,求出概率重要度和结构重要度;7.结论当事故发生概率超过预定目标值时,从最小割集着手研究降低事故发生概率的所有可能方案,利用最小径集找出消除事故的最佳方案;通过重要度重要系数分析确定采取对策措施的重点和先后顺序;从而得出分析、评价的结论;具体分析时,要根据分析的目的、人力物力的条件、分析人员的能力选择上述步骤的全部或部分内容实施分析、评价;对事故树规模很大的复杂系统进行分析时,可应用事故树分析软件包,利用计算机进行定性、定量分析;三、触电事故树分析1.概述将“触电发生伤亡事故”作为顶上事件,在计算、分析同类事故案例的基础上,作事故树,见图6-12.事故树事故树分析如图6-1图6-1 触电事故树图中:T-顶上事件;A,B-中间事件了;X-基本事件;T-触电伤亡事故;A1-设备漏电, A2-人体接触带电体;B1-绝缘损坏, B2-绝缘老化;B3-保护接地、接零不当, B4-保护开关失灵;X1-缺乏用电安全知识, X2-电气设备漏电;X3-电气设备外壳带电, X4-违章作业;X5-防护用品使用不当, X6-电工违章作业,非电工操作;X7-开关漏电, X8-接触开关的带电体;图6-2 防止触电成功树3.计算事故树的最先割集、最小径集该事故树的结构函数为:T=A1A2=B1+B2B3+B4=X1+X2+X3+X4X5+X6+X7·X8=X1+X2+X3+X4X5+X6+X7·X8=X1X5+X1X6+X1X7X8+X2X5+X2X6+X2X7X8+X3X+X3X6+X3X7X8+X4X5+X4X6+X4X7X8…… (1)在事故树分析中,如果所有的基本事件都发生则顶上事件必然发生,但是在很多情况下往往只要部分基本事件发生则顶上事件就能发生;因此,了解哪些基本事件的组合对顶上事件发生具有较大影响,这对有效地、经济地预防事故发生是非常重要地;事故树分析中地割集就是系统发生事故地模式;引起顶上事件发生地最小限度地割集称最小割集;每一个最小割集即表示顶上事件发生地每一种可能性;事故树中最小割集越多,顶上事件发生地可能性就越大,系统就越危险;式1为事故树地最小割集表达式,共有12个最小割集,即:K1=X1X5K2=X1X6K3=X1X7X8…………K12=X4X7X8该事故树额达最小径集为:T=A1+A2=B1B2+B3B4=X1X2X3X4+X5X6X7+X8=X1X2X3X4+X5X6X7+X5X6X84.重要度分析如何辨别各基本事件地发生对顶上事件发生额影响就必须对事故树进行基本事件地主要度分析;重要度分析方法有多种,其中不考虑基本事件发生地概率,仅从事故树结构上分析各基本事件额发生对顶上事件发生地重要度地方法称“基本事件地结构重要度分析”,精确计算各基本事件结构重要度系数工作量很大,常用地式通过估算求得系数;通过计算得:IX1=IX2=IX3=IX4=IX5=IX6>=IX7=IX8可见各基本事件对顶上事件发生得影响程度是相同的;从事故树结构上看,要避免顶上事件发生,最佳的方法是根据基本事件结构重要度大小依次采取措施;如果各基本事件的发生概率有差别,则需要作概率重要度分析和临界重要度分析;5.预防事故模式如前所述,事故树表达式中的每一个最小径集就是系统有效防止事故的一种模式;最小经济中集中基本事件较少的,则预防最为有效;从对同类事故案例分析汇总可得出预防触电事故最主要途径为:保持电气设备处于安全状态、确保电工按章操作和杜绝非电工进行电作业;1保持电气设备处于安全状态对应的基本事件有:X1,X2,X3,X4,X7,X82确保按章操作对应的基本事件有:X5,X66.结果分析即安全对策1“触电事故”事故树的最小径集有12个,说明在检测作业中有发生伤亡事故的可能性;如果不采取必要的安全措施,这样的系统是可能造成人员和设备伤害的;该事故树的最小径集有2个,说明要预防伤亡事故就必须从这2个方面进行考虑;2个基本事件对顶上事件发生的影响程度是相同的;3预防触电事故最主要途径:保持检测设备处于安全状态、确保操作工按章操作和杜绝违章操作;具体措施为:①为防止触电伤害事故的发生,必须提高工作人员的安全素质、责任心,要求具有一定的专业知识,并按国家有关规定,电工为特种作业,必须经过培训、考核、持证上岗,非操作人员严禁从事该项作业;②应采用不同方式、不同用途的接地措施;安全接地主要有保护接地、重复接地等;③采用保护接地时,接地电阻必须符合要求;④对电气设备要定期进行维护、检修,发现故障缺陷要及时处理,保证各类电气设备、线路在无故障的情况下运行,确保安全;在进行电气作业时,要严格按照安全操作规程进行操作;第七章典型事故案例及重大事故原因分析事故原因及后果分析过程,是根据评价对象的特点着重了解同类行业的事故类型、典型事故案例,并对此进行对照、类比、分析、总结,将有效地帮助我们采取预防措施,避免同类事故的发生;第一节重大事故原因分析根据统计资料,按事故原因进行分析,则得出表7-1所列结果:表7-1 按事故原因分类的事故频率分布表从事故发生频率的分布来看,由于阀门、管线的泄漏而引起的特大火灾爆炸事故所占比重很大,占%;由于泵、设备故障及仪表、电气失控比重也不小,占%;对于管理问题,完全可以避免的人为损失失误亦达到%;而装置内物料突沸和反应失控的比例占了%;不可忽视的雷击、静电、自然灾害引发事故也占到%,因此,除设备质量、工艺控制、作业管理外,防雪、避雷、防静电也必须应予以相当的重视;此外,在100起特大火灾爆炸事故中,报警及消防不力也是事态扩大的一个重要因素,其中竟有12起是因消防水泵无法启动而造成灾难性后果;值得注意的是易燃、易爆蒸汽等飘逸扩散的蒸汽云团以及易燃、易爆蒸汽积聚,或弥漫在建筑物内产生的爆炸不仅所占事故比例高达至43%,而且这种爆炸是最具毁灭性的,其爆炸产生的冲击波、热辐射以及飞散抛掷物等还会造成二次事故;据统计分析,国内40余年间石油化工企业发生的事故,经济损失在10万元以上的有204起,其中经济损失超过100万元的有7起;按事故原因分类可得出表7-2所列结果:表7-2 国内40年间经济损失10万元以上的事故原因分析表由上述列表数据分析可知,违章动火包括措施不当及误操作竟占到65%的事故率,比例之大,令人触目惊心,对此采取应对策措施以杜绝违章动火、避免误操作十分重要,有举足轻重的作用;设备损坏、仪表失灵、腐蚀引起的事故也占到20%,在现代化连续化生产工艺普遍使用并依赖集散控制系统控制的今天,仪表、设备的选择包括材质及其安装、维护、保养,对保证安全生产正常运行极为重要,其对策措施需要特别加强;雷电、静电、电气火灾、爆炸所占比例甚大,防雷、防电气引起的火灾、爆炸是石油、化工行业的一个重要方面,马虎不得,应有严密的对策措施;第二节典型事故案例本节通过一些事故案例,分析事故发生的原因,总结经验,引以为鉴;案例1 广西桂平县磷肥厂硫酸灼伤事故重伤1人、轻伤2人1.事故经过和危害1990年5月31日,广西壮族自治区桂平县磷肥厂从柳州锌品厂发至贵港森工站储木场的运硫酸槽车于5月30日到站,厂部组织5人到贵港装酸泵,准备从运酸槽车上卸硫酸;5月30日10分,他们将酸泵装上本厂汽车,运至贵港;5月31日17时,安装好电机、电线与酸泵后,进行空载试机3次,每次交流接触器都跳闸,酸泵密封处冒烟,不能使用;20时,厂又派3人前往贵港,22时30分到达现场修理;修理工用手扳动泵轴,发现有一方向偏紧,认为没有问题,即叫电工改用闸刀开关直接起动;2名工人用14铁丝扎2圈套在软塑料管与泵出口铁管接头上扎好,抬酸泵装进槽车内,安装完毕后,4人离开现场,6名电工在闸刀开关处,2人在槽车上;听到试泵命令后,电工合上电源开关,不到半分钟,1人从槽车上跳下,边走边用地面积水洗伤处;另1人也从槽车上跳下,其头部、面部、上肢、胸部、下肢等多处被出口管喷出的硫酸烧伤,后被送入医院抢救,造成烧伤面积35%,深Ⅲ度烧伤,双目失明,预计经济损失3万元;另外2名轻伤也送入医院治疗;2.事故原因分析①酸泵附件有缺陷,空载试机3次交流接触器都跳闸,仍然冒险运转;②酸泵出口铁管与软塑料管没有接好,致使软塑料管与铁管脱开,使硫酸喷到操作人员身上;③操作人员没有穿戴耐酸的工作服、工作帽、防护靴、耐酸手套、防护眼镜,违章作业;④工作环境恶劣,现场照明差,操作人员在试泵时也未远离现场;⑤缺乏急救常识,没有用清水在现场先冲洗处理,使受伤人员伤势加重;3.防止同类事故发生的措施①不穿戴齐全个人防护用品者,不准上岗;②加强领导、车间主任、安全员、工人的安全职责,杜绝违章指挥、违章作业,严禁设备带病、冒险运转;③加强运酸槽车的管理,配备良好的酸泵和其他设备,输送酸之前,先用水试压无问题再打酸并配合安全意识好的人员进行操作和管理;④电器设备、闸刀、线路严格按照电器管理规程进行操作,不准随意拆除和更改;案例2 哈尔滨亚麻厂“3.15”特大亚麻粉尘爆炸事故1.事故经过和危害1987年3月15日凌晨2时39分,该厂正在生产的梳麻、前纺、准备3个车间的联合厂房,突然发生亚麻粉尘爆炸起火;一瞬间,停电停水;当班的477名职工大部分被围困在火海之中;在公安消防干警、解放军指战员、市救护站和工厂职工的及时抢救下,才使多数职工脱离了险区;4时左右,火势被控制住,6时明火被扑灭,事故死亡58人,受伤177人,直接经济损失880多万元;2.事故原因分析根据黑龙江省地震办所属哈尔滨地震台提供的这次爆炸的地震效应记录,表明首爆的震级最大,能量也最大;爆炸事故现场有两个能量较大的炸点:一个是中央换气室南部,一个是地下麻库南区;爆炸的地震效应说明中央换气室南部首爆,即从中央换气室南部两个除尘器内的粉尘爆炸开的,通过地沟、吸尘管和送风管道的传播导致其他除尘器的连续爆炸、燃烧和厂房内空间爆炸;3.预防措施①积极制定和严格执行有关防火、防爆的规程、标准、案例;把防止亚麻粉尘爆炸作为企业重要工作来抓;②做好有关人员的培训、考核;落实各级岗位责任制;提高全体职工的安全素质;③开展对亚麻粉尘爆炸和静电引爆特性的研究工作,为亚麻纺织工业的防爆措施提供科学依据;④亚麻企业一定要优先落实防爆技术措施计划;案例3 湖北省某金属锻造厂电击事故 1人重伤1.事故经过和危害2003年9月17日18:55分,湖北某金属锻造厂电工陈学祥、余廷培两人为一组,对电动葫芦的电源线进行安装,由于工作重陈军误送电,致电工陈学祥被电击,从2.6米高出堕落,立即送往医院进行开颅手术;伤者陈学祥于9月17日16时后,将1开关柜空气开关电源线接好后,并拉掉空气开关,在吃过晚饭后,约18:55分左右,陈学祥对同档做事的余廷培讲,去拉掉电源开关,准备做事,陈学祥便爬到离地面2.6米高的一棚顶边缘。
基于仿真模拟的碰撞事故后果评估与损伤分析研究

基于仿真模拟的碰撞事故后果评估与损伤分析研究近年来,交通事故频发,给人们的生命财产安全带来了巨大威胁。
碰撞事故是常见的一种交通事故类型,对车辆乘员和行人都可能带来严重的后果。
因此,研究碰撞事故后果评估与损伤分析成为了交通安全领域中的热门课题之一。
本文旨在探讨基于仿真模拟的碰撞事故后果评估与损伤分析方法。
1. 碰撞事故后果评估的重要性在交通事故中,碰撞事故是最常见的一种。
无论是车辆碰撞还是车辆与行人碰撞,都有可能造成人员伤亡和车辆损毁。
因此,准确评估碰撞事故后果对于制定交通安全政策、改进车辆结构设计以及提高救援效率等方面都具有重要意义。
2. 基于仿真模拟的碰撞事故后果评估方法为了更准确地评估碰撞事故后果,研究者采用了基于仿真模拟的方法。
通过建立车辆和行人的仿真模型,并模拟真实的碰撞过程,可以得到碰撞事故发生后的车辆损伤情况和人员受伤情况。
(1)车辆碰撞事故仿真模拟在车辆碰撞事故仿真模拟中,研究者首先需要获取车辆的几何模型和物理特性。
根据实际数据和相关测试,建立车辆的仿真模型,并确定仿真中所需的物理参数。
接下来,通过仿真软件(如ANSYS、ABAQUS等)进行碰撞仿真,模拟真实碰撞过程中车辆的动力学响应和损伤情况。
最终,根据仿真结果可以评估车辆碰撞事故的严重程度和造成的损毁范围。
(2)行人碰撞事故仿真模拟对于行人碰撞事故,研究者同样需要建立行人的仿真模型。
通过采集行人的运动数据和人体结构特征,建立相应的仿真模型。
然后,通过仿真软件进行碰撞仿真,模拟真实碰撞过程中行人的受力情况和伤害程度。
通过对仿真结果的分析,可以准确评估行人碰撞事故的严重程度和造成的损伤情况。
3. 碰撞事故后果评估与损伤分析方法的局限性基于仿真模拟的碰撞事故后果评估与损伤分析方法具有一定的局限性。
首先,模型的准确性对结果的可靠性具有重要影响。
若模型的参数设置不合理或者数据采集不准确,将会导致评估结果的误差。
其次,碰撞事故的真实情况往往受到多种因素的影响,如环境条件、车辆状态、行人行为等。
事故后果模拟分析

事故后果模拟分析事故后果模拟分析是指通过使用数学、物理学、化学等相关理论和方法,对事故后果进行定量分析和模拟,以便更好地预防事故并制定应急预案。
本文将从概念、方法和实践案例三个方面展开,深入介绍事故后果模拟分析的意义和应用。
概念事故后果模拟分析是指通过模拟和预测事故发生后的影响范围、危害程度和后果,以便在事故发生前就能采取相应的措施进行预防和应急处理的一种技术手段。
它是结合相关技术和工具,运用数学模型和计算机仿真等技术手段对事故的后果进行系统性、定量化的分析和预测。
方法1.系统分析方法:通过研究事故的发生机理、影响因素及其相互关系,构建事故后果的评估指标体系,对事故影响的各个方面进行定量分析和评估。
2.危险源模拟方法:对事故可能发生的危险源进行建模和模拟,通过引入概率统计方法,分析事故的发生概率和可能的后果范围,以便提前采取相应的预防和控制措施。
3.仿真模拟方法:通过在计算机上对事故发生后的各种可能情况进行模拟,并对其后果进行定量分析,以获得事故的影响范围、可能的伤亡人数、环境污染程度等信息。
实践案例以石油化工行业为例,该行业存在着重大事故发生的风险,因此事故后果模拟分析非常重要。
1.模拟溢油事故:通过对石油储罐泄漏的溢油事故进行模拟,预测泄漏量、扩散面积和影响范围,以便制定合理的应急预案,有效减少事故造成的损失。
2.模拟火灾事故:通过对石化企业发生火灾事故的可能性和后果进行模拟分析,评估烟气扩散的范围和浓度,对火灾事故的灭火措施和疏散逃生进行优化设计。
3.模拟爆炸事故:通过对化工装置中的爆炸事故进行模拟分析,预测爆炸震荡波的传播范围和破坏程度,以及可能的伤亡人数和财产损失,以便在事故发生前采取相应的控制措施和预防措施。
意义与应用1.事故防范决策:通过模拟分析,及早发现和解决事故隐患,对可能发生的事故进行预防和控制。
2.应急预案制定:根据模拟分析结果,合理安排应急资源,明确应急救援措施,提高事故处理的效率和准确性。
火灾、爆炸事故后果模拟计算
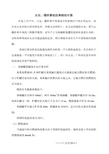
火灾、爆炸事故后果模拟计算在化工生产中,火灾、爆炸和中毒事故不但影响生产的正常运行,而且对人员有较大的身体危害,导致人员的伤亡。
本文运用地面火灾、蒸气云爆炸和中毒的三种数学模型,对年产2万吨顺酐装置的原料库来进行分析,分析各种事故对人员可能造成的危害,借以帮助企业在生产中采取相应的措施。
事故后果分析是危险源危险性分析的一个主要组成部分,其目的在于定量描述一个可能发生的重大事故对工厂、对厂内人员、厂外居民甚至对环境造成危害的严重程度。
一、苯储罐泄漏池火灾后果分析苯系易燃液体,在苯贮罐区苯泄漏后遇到点火源就会被点燃而着火燃烧。
由于贮罐区设有防火堤,苯泄漏后积聚在防火堤之内,它被点燃后的燃烧方式为池火。
模拟有关数据参数如下。
苯储罐区有两台800m3、两台500m3的苯储罐,苯储罐单罐直径10.5m,每两台罐为一组,贮罐区防火堤尺寸为33×16 m,模拟液池半径为18.3m;苯储罐单台最大贮存量600t,泄漏量为15%时,足以在防火堤内形成液池;周围环境温度设为25℃;(1)燃烧速度当液池中的可燃液体的沸点高于周围环境温度时,液体表面上单位面积的燃烧速度dm/dt为:………(公式F5-1)0.001H cdm/dt =C P(T b-T0)+H式中dm/dt~单位表面积的燃烧速度,kg/m2.sH c~液体燃烧热,J/kg。
苯H c=41792344J/kg。
C P~液体的定压比热容,J/kg.K。
苯C P=1729 J/kg.K。
T b~液体的沸点,K b=353.1K。
T0~环境温度,环境温度为25℃,K。
= 298K。
H~液体的气化热,J/kg。
苯H=428325J/kg。
(25℃)计算:dm/dt=0.001×41792344/﹝1729(353.1-298)+428325﹞=0.0798 kg/m2.s(2)火焰高度模拟液池为园池,半径为18.3m,其火焰高度可按下式计算:dm/dth=84r﹝﹞0.61………(公式F5-2)ρ0(2gr)1/2式中h~火焰高度,m;r~液池半径,m;取r=18.3mρ0~周围空气密度,kg/m3;取ρ0=1.185kg/m3(25℃)g~重力加速度,9.8m/s2;dm/dt~单位表面积的燃烧速度,己知0.0798kg/m2.s计算:h=84×18.3×{0.0798/[1.185×(2×9.8×18.3)1/2]}0.61=49.3m(3)热辐射通量当液池燃烧时放出的总热辐射通量为:Q=(兀r2+2兀rh)dm/dt·η·H c/﹝72(dm/dt)0.6+1﹞…(公式F5-3)Q~总热辐射通量,W;η~效率因子,可取0.13~0.35。
蒸汽云爆炸事故后果模拟分析法

蒸汽云爆炸事故后果模拟分析法Prepared on 22 November 2020蒸汽云爆炸事故后果模拟分析法超压:1)TNT当量通常,以TNT当量法来预测蒸气云爆炸的威力。
如某次事故造成的破坏状况与kgTNT炸药爆炸所造成的破坏相当,则称此次爆炸的威力为kgTNT当量。
蒸气云爆炸的TNT当量W TNT计算式如下:W TNT=×α×W f×Q f/Q TNT式中,W TNT—蒸气云的TNT当量(kg)α—蒸气云的TNT当量系数,正己烷取α=;W f—蒸气云爆炸中烧掉的总质量(kg)Q f—物质的燃烧热值(kJ/kg),正己烷的燃烧热值按×106J/kg,参与爆炸的正己烷按最大使用量792kg计算,则爆炸能量为×109J将爆炸能量换算成TNT当量q,一般取平均爆破能量为×106J/kg,因此W TNT= ×α×W f×Q f /q TNT+ =××792××106/×106=609kg2)危害半径为了估计爆炸所造成的人员伤亡情况,一种简单但较为合理的预测程序是将危险源周围划分为死亡区、重伤区、轻伤区和安全区。
死亡区内的人员如缺少防护,则被认为将无例外的蒙受重伤或死亡,其内径为0,外径为R ,表示外周围处人员因冲击波作用导致肺出血而死亡的概率为,它与爆炸量之间的关系为:= m重伤区的人员如缺少防护,则绝大多数将遭受严重伤害,极少数人可能死亡或受伤。
其内径就是死亡半径R1,外径记为R2,代表该处人员因冲击波作用耳膜破损的概率为,它要求的冲击波峰值超压为44000Pa。
∆按下式计算:冲击波超压P∆=++式中:P∆——冲击波超压,Pa;PZ——中间因子,等于;E——蒸气云爆炸能量值,J;P0——大气压,Pa,取101325得R2=轻伤区的人员如缺少防护,则绝大多数将遭受轻微伤害,少数人将受重伤或者平安无事。
- 1、下载文档前请自行甄别文档内容的完整性,平台不提供额外的编辑、内容补充、找答案等附加服务。
- 2、"仅部分预览"的文档,不可在线预览部分如存在完整性等问题,可反馈申请退款(可完整预览的文档不适用该条件!)。
- 3、如文档侵犯您的权益,请联系客服反馈,我们会尽快为您处理(人工客服工作时间:9:00-18:30)。
2.2事故后果模拟分析法火灾、爆炸、中毒是常见的重大事故,经常造成严重的人员伤亡和巨大的财产损失,影响社会安定。
这里重点介绍有关火灾、爆炸和中毒事故(热辐射、爆炸波、中毒)后果分析,在分析过程中运用了数学模型。
通常一个复杂的问题或现象用数学模型来描述,往往是在一个系列的假设的前提下按理想的情况建立的,有递增模型经过小型试验的验证,有的则可能与实际情况有较大出入,但对辨识危险性来说是可参考的。
2.2.1 泄漏由于设备损坏或操作失误引起泄漏,大量易燃、易爆、有毒有害物质的释放,将会导致火灾、爆炸、中毒等重大事故发生,因此,后果分析由泄漏分析开始。
2.2.1.1 泄漏情况分析2.1.1.1.1泄漏的主要设备根据各种设备泄漏情况分析,可将工厂(特别是化工厂)中易发生泄漏的设备归纳为以下10类:管道、挠性连接器、过滤器、阀门、压力容器或反应器、泵、压缩机、储罐、加压或冷冻气体容器,火炬燃烧装置或放散管等。
⑴管道。
它包括管道、法兰和接头,其典型情况和裂口尺寸分别取管径的20%~100%、20%和20%~100%。
⑵挠性连接器。
它包括软管、波纹管和铰接器,其典型泄漏情况和裂口尺寸为:①连接器本体破裂泄漏,裂口尺寸取管径的20%~100%;②接头处的泄漏,裂口尺寸取管径的20%;③连接装置损坏泄漏,裂口尺寸取管径的100%。
⑶过滤器。
它由过滤器本体、管道、滤网等组成,其典型泄漏情况和裂口尺寸分别取管径的20%~100%和20%。
⑷阀。
其典型泄漏情况和裂口尺寸为:①阀壳体泄漏,裂口尺寸取管径的20%~100%;②阀盖泄漏,裂口尺寸取管径的20%;③阀杆损坏泄漏,裂口尺寸取管径的20%。
⑸压力容器或反应器。
包括化工生产中常用的分离器、气体洗涤器、反应釜、热交换器、各种罐和容器等。
其常见的此类泄漏情况和裂口尺寸为:①容器破裂而泄漏,裂口尺寸取容器本身尺寸;②容器本体泄漏,裂口尺寸取与其连接的粗管道管径的100%;③孔盖泄漏,裂口尺寸取管径的20%;④喷嘴断裂而泄漏,裂口尺寸取管径的100%;⑤仪表管路破裂泄漏,裂口尺寸取管径的20%~100%;⑥容器内部爆炸,全部破裂。
⑹泵。
其典型泄漏情况和裂口尺寸为:①泵体损坏泄漏,裂口尺寸取与其连接管径的20%~100%;②密封压盖处泄漏,裂口尺寸取管径的20%;⑺压缩机。
包括离心式、轴流式和往复式压缩机,其典型泄漏情况和裂口尺寸为:①压缩机机壳损坏而泄漏,裂口尺寸取与其连接管道管径的20%~100%;②压缩机密封套泄漏,裂口尺寸取管径的20%。
⑻储罐。
露天储存危险物质的容器或压力容器,也包括与其连接的管道和辅助设备,其典型泄漏情况和裂口尺寸为:①罐体损坏而泄漏,裂口尺寸为本体尺寸;②接头泄漏,裂口尺寸为与其连接管道管径的20%~100%;③辅助设备泄漏,酌情确定裂口尺寸。
⑼加压或冷冻气体容器。
包括露天或埋地放置的储存器、压力容器或运输槽车等,其典型泄漏情况和裂口尺寸为:①露天容器内部气体爆炸使容器完全破裂,裂口尺寸取本体尺寸;②容器破裂而泄漏,裂口尺寸取本体尺寸;③焊接点(接管)断裂泄漏,取管径的20%~100%。
⑽火炬燃烧器或放散管。
它们包括燃烧装置、放散管、多通接头、气体洗涤器和分离罐等,泄漏主要发生在筒体和多通接头部位,裂口尺寸取管径的20%~100%。
表2-1典型泄漏情况和裂口尺寸取值表2.1.1.1.2造成泄漏的原因从人-机系统来考虑造成各种泄漏事故的原因主要有四类:⑴设计失误①基础设计错误,如地基下沉,造成容器底部产生裂缝,或设备变形、错位等;②选材不当,如强度不够、耐腐蚀性差、规格不符等;③布置不合理,如压缩机和输出管道没有弹性连接,因振动而使管道破裂;④选用机械不合适,如转速过高,耐温、耐压性能差等;⑤选用计测仪器不合适;⑥储罐、储槽未加液位计,反应器(炉)未加溢流管或放散管等。
⑵设备原因①加工不符合要求,或未经检验擅自采用代用材料;②加工质量差,特别是不具有操作证的焊工焊接质量差;③施工和安装精度不高,如泵和电动机不同轴,机械设备不平衡,管道连接不严密等;④选用的标准定型产品质量不合格;⑤对安装的设备未按《机械设备安装工程及验收规范》进行验收;⑥设备长期使用后未按规定检修期进行检修,或检修质量差造成泄漏;⑦计测仪表未定期校验,造成计量不准;⑧阀门损坏或开关泄漏,又未及时更换;⑨设备附件质量差,或长期使用后材料变质、腐蚀或破裂等。
⑶管理原因①没有制定完善的安全操作规程;②对安全漠不关心,已发现问题不及时解决;③没有严格执行监督检查制度;④指挥错误,甚至违章指挥;⑤让未经培训的工人上岗,知识不足,不能判断错误;⑥检修制度不严,没有及时检修已出现故障的设备,使设备带病运转。
⑷人为失误①误操作,违反操作规程;②判断失误,如记错阀门位置或开错阀门;③擅自离岗;④思想不集中;⑤发现异常现象不知如何处理;2.1.1.1.3泄漏后果泄漏一旦出现,其后果不单与物质的数量、易燃性、毒性有关,而且与泄漏物质的相态、压力、温度等状态有关。
这些状态可有多种不同的结合,在后果分析中,常见的可能结合有4种:①常压液体;②加压液化气体;③低温液化气体;④加压气体。
泄漏物质的物性不同,其泄漏后果也不同。
⑴可燃气体泄漏可燃气体泄漏后与空气混合达到爆炸极限时,遇到引火源就会发生燃烧或爆炸。
泄漏后起火的时间不同,泄漏后果也不相同。
①立即起火。
可燃气体从容器中往外泄出时即被点燃,发生扩散燃烧,产生喷射性火焰或形成火球,它能迅速地危及泄漏现场,但很少会影响到厂区的外部。
②泄后起火。
可燃气体泄出后与空气混合形成可燃蒸气云团,并随风飘移,遇火源发生爆炸或爆轰,能引起较大范围的破坏。
⑵有毒气体泄漏有毒气体泄漏形成云团在空气中扩散,有毒气体的浓密云团将笼罩很大的空间,影响范围大。
⑶液体泄漏一般情况下,泄漏的液体在空气中蒸发而生成气体,泄漏后果与液体的性质和储存条件(温度、压力)有关。
①常温常压下液体泄漏。
这种液体泄漏后聚集在防液堤内或地势低洼处形成液池,液体由于持表面风的对流而缓慢蒸发,若遇引火源就会发生池火灾。
②加压液化气体泄漏。
一些液体泄漏时将瞬间蒸发,剩下的液体将形成一个液池,吸收周围的热量继续蒸发。
液体瞬时蒸发的比例决定于物质的性质及环境温度。
有些泄漏物可能在泄漏过程中全部蒸发。
③低温液体泄漏。
这种液体泄漏时将形成液池,吸收周围热量蒸发,蒸发量低于加压液化气体的泄漏量,高于常温常压下液体的泄漏量。
无论是气体泄漏还是液体泄漏,泄漏量的多少都是决定后果严重程度的主要因素,而泄漏量又与泄漏时间长短有关。
2.2.1.2 泄漏量的计算当发生泄漏的设备的裂口是规则的,而且裂口尺寸及泄漏物质的有关热力学、物理化学性质及参数已知时,可根据流体力学中的有关方程式计算泄漏量。
当裂口不规则时,可采取等效尺寸代替;当遇到泄漏过程中压力变化等情况时,往往采用经验公式计算。
(1)液体泄漏计算液体泄漏速度可用流体力学的伯努利方程计算,其泄漏速度为: ()gh 2ρp p 2A ρC Q 0d 0++=Q 0=C d A ρ(2[p+P 0]/ρ+2gh)1/2 (1)式中 Q 0——液体泄漏速度,kg/s ;C d ——液体泄漏系数,按表2-1选取;A ——裂口面积,m 2;ρ——泄漏液体密度,㎏∕m 3;p ——容器内介质压力,Pa ;p 0——环境压力,Pa ;g ——重力加速度,9.8m ∕s 2;h ——裂口之上液位高度,m ;表2-2 液体泄漏系数Cd对于常压下的液体泄漏速度,取决于裂口之上液位的高低;对于非常压下的液体泄漏速度,主要取决于容器内介质与环境压力之差和液位高低。
当容器内液体是过热液体,即液体的沸点低于周围环境温度,液体流过裂口时由于压力减小而突然蒸发。
蒸发所需热量取自于液体本身,而容器内剩下液体的温度将降至常压沸点。
在这种情况下,泄漏时直接蒸发的液体所占百分比F 可按下式计算:F=Cp(T-T 0)/H (2)式中 Cp ——液体的定压比热,J ∕kg ·K ;T ——泄漏前液体的温度,K ;T0——液体在常压下的沸点,K;H ——液体的气化热,J∕kg;按式(2)计算的结果,几乎总是在0~1之间。
事实上,泄漏时直接蒸发的液体将以细小烟雾的形式形成云团,与空气相混合而吸收蒸发。
如果空气传给液体烟雾的热量不足以使其蒸发,有一些液体烟雾将凝结成液滴降落到地面,形成液池。
根据经验,当F>0.2时,一般不会形成液池;当F<0.2时,F与带走液体之比有线性关系,即当F=0时没有液体带走(蒸发),当F=0.1时有50%的液体被带走。
(2)气体泄漏量计算气体从裂口泄漏的速度与其流动状态有关。
因此,计算泄漏量时首先要判断泄漏时气体流动属于音速还是亚音速流动,前者称为临界流,后者称为次临界流。
当式(3)成立时,气体流动属音速流动:p0/p≤[2/(k+1)]k/(k-1)(3)当式(4)成立时,气体流动属亚音速流动:p0/p≥[2/(k+1)]k/(k-1) (4)式中p0、p——符号意义同前;k——气体的绝热指数,即定压比热Cp与定容比热Cv之比。
气体呈音速流动时,其泄漏量为:Q0=C d Aρ[(Mk/RT)×(2/(k+1))k+1/(k-1)]1/2(5) 气体呈亚音速流动时,其泄漏量为:Q0=YC d Aρ[(Mk/RT)×(2/(k+1))k+1/(k-1)]1/2(6)上两式中Cd——气体泄漏系数,当裂口形状为圆形时取1.00,三角形时取0.95,长方形时取0.90;Y——气体膨胀因子,它由下式计算:Y={(1/(k-1))((k+1)/2)k+1/k-1(p0/p)2/k[1-(p0/p)(k-1)/k]}1/2(7)M——分子量;ρ——气体密度,kg/m3;R——气体常数,J/mol•K;T——气体温度,K。
当容器内物质随泄漏而减少或压力降低而影响泄漏速度时,泄漏速度的计算比复杂。
如果流速小或时间短,在后果计算中可采用最初排放速度,否则应计算等效泄漏速度。
(3)两相流动泄漏量计算在过热液体发生泄漏时,有时会出现气、液两相流动。
均匀两相流动的泄漏速度可按下式计算:Q0=C d A[2ρ(p-p c)]1/2 (8)式中Q0——两相流动混合物泄漏速度,kg/s;C d——两相流动混合物泄漏系数,可取0.8;A ——裂口面积,m2;p ——两相混合物的压力,Pa;p c ——临界压力,Pa,可取p c=0.55Pa;ρ——两相混合物的平均密度,kg/m3,它由下式计算:ρ=1/(Fv/ρ1+(1-Fv)/ρ2)(9)ρ1——液体蒸发的蒸气密度,kg/m3;ρ2——液体密度,kg/m3 ;Fv ——蒸发的液体占液体总量的比例,它由下式计算:Fv=C p(T-T c)/H (10)C p——两相混合物的定压比热,J/kg•K;T ——两相混合物的温度,K;T c——临界温度,K;H ——液体的气化热,J/g。