转炉脱硫分析与计算
先脱硫和后脱硫的比较

后脱硫代替先脱硫的分析郭振宇摘要:近期由于脱硫出现问题,导致半钢运不过来,严重影响生产节奏。
基于炼钢精炼LF也有脱硫能力,特提出后脱硫也具有可行性。
并把先脱硫和后脱硫的工序时间及成本对比,来分析先后脱硫的优劣性。
关键字:脱硫1、前言西昌钢钒炼钢厂目前有2座脱硫、1座提钒炉、2座转炉,当脱硫有问题时,严重影响炼钢厂整条生产线的顺行。
如果把脱硫任务放到LF炉,也就是后脱硫,从而来保证生产的顺行。
2、原理2.1碳化钙在铁水中脱硫能力很强,其反应为:CaC2(s)+[S]=CaS(s)+ C石墨(1-1)实际碳化钙在铁液中脱硫所达到的[S]最低水平比理论值高出几个数量级,显然这是动力学因素起主要作用。
铁水中的CaC2脱硫过程是固-液反应,其机制包括如下三个步骤:(1)铁水中的硫通过铁水一侧的界面向CaC2表面扩散;(2)在CaC2和铁水的固-液界面上发生化学反应,生成CaS;(3)硫通过CaC2表面的反应层向CaC2颗粒深处扩散。
在上面三个步骤中,(2)(3)不可能成为限制总反应速度的环节。
这是因为在高温时化学反应速度一般很快。
而碳化钙颗粒表面上附着的CaS层很疏松,硫通过扩散并不困难。
由此看来,脱硫反应的限制性环节乃是铁水一侧边界层中硫向CaC2表面的扩散,即液相中的扩散为其限制性环节。
由此可见,可以用加强熔池搅拌,提高反应温度和减小碳化钙的粒度等方法来增大反应界面的扩散系数,减小界面层厚度,从而增加CaC2在铁水中的脱硫反应速度。
2.2石灰是一种价格低廉的脱硫剂,其脱硫反应为:CaO(s)+[S]=CaS(s)+[O] (2-1)当铁水中存在大量的碳和硅时,石灰脱硫有如下反应:CaO(s)+[S]+C石墨=CaS(s)+CO(g) (2-2)2CaO(s)+[S]+1/2[Si]=CaS(s)+1/2Ca2SiO3(2-3)反应式(1-3)对氧化钙在脱硫过程中的有效利用具有很不利的影响,首先生成Ca2SiO3要消耗一部分CaO,更不利的是Ca2SiO3 还会附着在氧化钙粒子的表面,阻碍脱硫反应的进一步进行。
转炉出钢过程中渣洗脱硫的试验研究

( n a o n te C m a l , n a , e e ,5 0 5 Ha d n I n a d Se l o p n Ha d n H b i0 6 1 ) r y
Absr c :Th s l u i i f cin y, is ifu n i g f co s a d h nfu n e o h c tnto te ta t e de uph rzng e i ec t n l e c n a tr n te i l e c n t e one f se lby p e etd sa n BOF a p n a e be n sud e r m le lg o t p i g h v e t i d.I si dc t d t t h e ulhu ii g e fc e y i fe - ti n ia e ha :t e d s p rzn f inc sdif r i e tfo ifr ntsa n r m d fe e lg, a h hy ia r m e e sp a n d csver e;i e u esLF e nng tm e;i a nd t e p sc lpa a tr ly a e ii ol tr d c rf i i i tc n e ce ty r du e te piku fc r on a d slc n f rc l r le o c r n se 1 i f in l e c h c p o a b n i o o od o ld l w abo te . i Ke o d y W r s:p e etd sa d s ph rz t0 sud r m l l g; e ul u i ai n;t y e
2 渣洗 脱硫试 验 方案
15后 , 序 加 入 低 碳 锰 铁 、 块 、 熔 渣 及 石 灰 。 / 顺 铝 预
影响转炉脱硫因素分析

・ 等
() 钢 温度 的影 响 。钢渣 间 的脱硫 反应 属 于 吸热 反应 , 1炼 因此 , 温有 利 于脱 硫 反应 进行 。温 度 的重 要 高
3 2
河北 理工 大学学报 ( 自然 科学 版)
第3 3卷
() 2 炉渣 碱度 的影 响 。炉渣碱 度高 , 游离 C O多 , O 一 增 大 , 利 于脱硫 。但 过 高 的碱 度 , 出现 炉 渣 a ( ) 有 会 粘 度增 加 , 而 降低脱 硫效 果 。 反
4 效 果
.
通过对转炉吹塔工艺的优化和改进, 转炉的脱硫效果得到大幅度提高, 转炉的脱硫率由原来的2 %提 0 高到 3%P l 转炉终点平均硫含量为 000 转炉终点钢水硫的命中 0 A- , : .2 %, 率达到9 以上; o6 9 , 完全满足了钢种
的要求 , 提高 了产 品 的质量 。 也
脱 硫 的有利 条件 : 温 , 碱度 , ( e , 高 高 低 F O) 良好 的 流动性 。
3 转 炉脱 硫 冶 炼 工 艺控 制
3 1 控 制原 辅材 料质 量 . .
由于转 炉原辅 材料 特别是 冶金 石灰 质量直 接影 响着吹炼 过程 炉渣 的形 成和脱 硫能 力 。以前使 用 的冶 金 石 灰 中有 效 成分 和活性 度较低 , 不到 冶炼 的要 求 , 接 影响 转炉 脱硫 操作 。 自从 采用 活 性石 灰 后 , 炉 全 达 直 转 部 采用 活 性 度 大 于 3 0 0 ml的石 灰 , 灰 质 量 明 显 好 转 , 灰 消 耗 也 由原 来 的 8 . 6 k / ( ) 低 到 石 石 7 4 g t 钢 降 6 . 3 g t钢 ) 见表 2 O 5k /( , 。另外 对所 需 的其 它 等 熔 剂 以及 出钢合 金 化 所 需 合 金 的质 量 指 标 进 行 了严 格 的 控 制, 所需 的低 碳锰 铁 的硫含 量必 须在技 术要求 之 内 。
210转炉厂KR脱硫的工艺与设备介绍
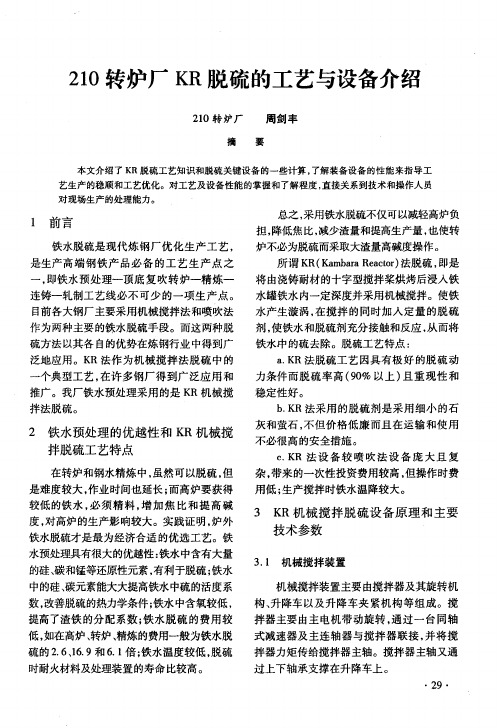
机械搅拌装置主要 由搅拌器及其旋转机
构、 升降 车 以及 升 降 车夹 紧机 构 等 组 成 。搅
拌器主要 由主电机带动旋转 , 通过一 台同轴 式减速器及主连轴器与搅拌器联接, 并将搅 拌器力矩传给搅拌器主轴。搅拌器主轴又通 过上下轴承支撑在升降车上。
光 测距 仪 定 位 , 2~2 m mi 度 之 间 内 在 0 / n速 变频 调速驱 动 , 车上 安装 有 带 铁 罐液 压 推 在
杆倾 转 装 置 。在 车 架 上 每 边 焊 接 有 固 定 齿 条 , 翻齿条通 过横 梁连 为一体 , 倾 固定齿 条 和
倾 翻齿条 牢固齿 合 。然 后通 过与 液压缸连 接 实 现 铁 水 罐 倾 翻。倾 翻 角 度 在 0 。一4 。 0 之
变频器控制 , 实行无 级 调速 , 带动 旋转 主 轴从 而带动搅拌 器转 动 。升 降导 轨及 框架 穿 越各 层平 台并 与 各平 台相连 , 整 个 框架 的结 构 使
稳定 。升 降小 车卷 扬 装 置采 用 双 卷 筒 卷扬 ,
铁 水在 吊罐位 和脱 硫位 之 间 的 转移 , 用 激 采
・
2 ・ 9
升 降车 及夹 紧机 构 主 要 由升 降小 车 、 升 降导轨 及框架 和升 降小 车卷扬组 成 。升降小 车在安装 有 导轨 的型钢 框 架 上运 行 , 架 内 框 部装有旋 转 电机 、 轴 器 、 转 接头 、 承 和 联 旋 轴 旋 转 主轴 。升 降小 车上下两 端分 别安装 有 四 个液 压 装 置 , 成 升 降 小 车 定 位 夹 紧 装 置 。 组
aK . R法 脱硫 工 艺 因具 有 极 好 的脱 硫 动
连铸一 轧制 工艺 线 必 不 可 少 的一 项 生 产 点 。 目前各 大钢 厂主要 采用 机械 搅拌 法和 喷吹法 作 为两 种 主要 的铁 水脱硫 手 段 。而这两 种脱 硫 方法 以其各 自的优势在 炼 钢行业 中得 到广
转炉炼钢脱硫工艺分析

24 转 炉 出钢 过 程 中渣 洗 脱硫 .
图1初始硫含量对脱硫的影响
钢水【】 s含量对脱硫的影 响在相同的脱硫条件下,初始硫含量 ( 即转 炉终点[] s )越高 ,渣洗脱硫率也越高;初始硫含量越低 ,渣洗过程脱硫
效果。
《
丽 ‘
删 钿
撂
岳
处理 _艺为 :高炉 出铁一高炉鱼雷罐一转炉铁水罐一 ( T 扒渣 )一脱 硫 一 扒渣 一 转 炉 。
23 单 喷 颗粒 镁 、复 合 喷 吹 脱 硫 工 艺 . 脱 硫 工 艺原 理 及特 点 : 单 喷 颗 粒 镁 和 复 合 喷 吹 属 于典 型 喷 吹 法 , 即利 用 惰 性 气 体 ( , N、
炉内硫主要 以有机硫 、硫化物及硫酸盐 的形式随炉料带人 ,这与高 炉类似在熔炼过程中,小部分 以气相形式 随炉气挥发 ,绝大部分分布于 铁水和炉渣中,提高脱硫率的有效措施就是提 高炉渣的含硫 量。 影 响炉渣脱硫率的因素有二: 1 炉渣 的碱 度 ( a ) C O/S ):碱度高¥ C O ,可 以增加 渣中 i O l 1a 多 ( 0 一)的浓度 ,从 而使炉 渣脱硫 能力 提高 ,一定 炉温下 碱度过 高反 而会 降低脱硫效率 。由于碱度太 高 ,炉渣 的熔 化性温度升高 ,在渣中 将 出2 a SO :固体颗粒 ,降低炉渣 的流动性 ,影响脱硫反 应进行 C O・ i 时 离子 问 的相互扩 散 ,且高 碱度 渣稳 定性 不好 ,易造 成炉 况不顺 。 C OSO a /i 的值 在1 左右较 好 ,对于复杂的炉料 ( 含有大量泥砂 )其碱度 ( a( Mg So 十 , C + O) i2 A10 )。以不小于 1 为宜。 . 5
现代转炉炼钢脱硫工艺

现代转炉炼钢脱硫工艺摘要对转炉出钢渣洗脱硫进行了理论分析和工业试验。
结果表明:除温度外,转炉出钢渣洗脱硫的热力学和动力学条件均优于炉内脱硫。
在顶渣流动性良好的前提下,提高碱度和降低渣中w(FeO+MnO)有利于脱硫。
预熔型脱硫剂的脱硫效果优于机械混合型脱硫剂,其平均脱硫率达到51%。
关键词:炼钢转炉脱硫工艺发展现状AbstractTheoretical analysis and commercial experiment on BOF tapping desulphurization are described in this paper.The results show that the dynamic and thermodynamic factors of tapping desulphurization are better than those in the converter desulphurization,except for temperature conditions.When the slag has better fluidity,increasing slag basicity and decreasing w(Fe +MnO)in slag are beneficial to desulphurization.The desulphurization effect of pre-melted desulphurizer is higher than that of simply mixed one.Its desulphurization efficiency was reached by 51% 。
Key words steelmaking converter desulphurization craft1 钢液脱硫的基本原理1.1.1 钢液的脱硫主要是通过两种途径来实现,即炉渣脱硫和气化脱硫,根据熔渣的分子理论,碱性氧化渣与金属间的脱硫反应为:[S] + (CaO) == (CaS) + [O] ;[S] + (MnO) == (MnS) + [O];[S] + (MgO) == (MgS) + [O];根据熔渣的离子理论,脱硫反应可表示为:[S] + (O2-) == (S2-) + [O]的方式被除去,反应式可表示为:气化脱硫是指金属液中[S]以气态SO2}[S] +2[O] == { SO21.1.2 影响钢渣间脱硫反应的因素(1)碱度:提高碱度有利于脱硫,降低钢中含硫量。
转炉炼钢简易脱硫工艺研究

1 前 言
目前 南 钢 转炉 炼 钢 厂 (0 转 炉 ) 量 高 , 3t 产 生 产 节 奏快 ,F炉 的 精 炼 作 用 不 能 得 到 充 分 L 的发 挥 , 同时 又 没有 铁 水 预 处 理 工 艺 , 得 转 使 炉 生 产 过 程 中硫 含 量 难 以 控 制 , 响 了 高 附 影 加 值 钢 种 的 开发 与 生 产 ( A 3 、6 1 如 H 6 1MI R等 ,
表 3 常 规 生 产 钢 包 顶 渣
其 余 铁 合 金 ) 出钢 2分 钟 后 加 入 第 三 批 脱 一
硫 剂 ( / ) 13 。
( ) 氩 喂丝 工 位 2吹
①钢 包 车 开 至 吹 氩 喂 丝 工 位 测 温 取 样 ( 样 、 样 ) , 进 行 喂 丝 脱 硫 操 作 , 求 钢 渣 后 即 要 喂丝 速 度 严 格 控 制 在 10~1 5米 , 丝 . . 喂
芯线 脱 硫 的 研 究 、 试验 。 2 2 根据 喂丝 脱 硫 要 求 , 制 钢 中 氧 含 量 是 . 控
有效脱硫的先决条 件 , 因此 要 开 发 出 一 种 高 效率 脱 硫 剂 , 证 一定 的脱 氧 和 脱 硫 能力 。 保
2 3 在 不 影 响 转 炉 炼 钢 厂 正 常 的 生 产 条 件 .
3 1 通 过 反 复 实验 验 证 : 钢 工 位 加 入 的脱 . 出
硫 剂 为 钙 质 复 合 脱 氧 剂 ( 分 见 表 1 , 进 成 )可 行 深脱 氧 , 时 钙 质 复 合 脱 氧 剂 中 C C ( 同 a2脱 氧 后 生 成 CO) a 还有 利 于 提 高 钢 包 顶 渣 碱 度 ; A D粉 ( 要 成 分 主 o 3和 部 分 难 分 离 的 铝 粉 ) 利 于 改 善 钢 包顶 渣 流 动 性 。 有
氧气转炉出钢脱硫-LF精炼生产超低硫钢的工艺

00 0 , . 2 % 通过 B F出钢过程加入 1 0 g二元合 成渣 C O C F 、0 g O 0k 0 a —a 220k 铝粒 , 并加入硅锰 和硅 铝钡合金 , 可使钢中 硫含量降低 0 0 7 . 0 % 00 8 , .0 % 脱硫 率达 3 %。在 L 0 F精炼 时 , 过进一 步加入 合成渣 80 k ,0 9 0L m n 通 0 g 60— 0 / it  ̄ r 氩, 加热后喂 6 0m硅钙线 ,0— 5L mi@  ̄ 1 i, 渣碱 度 R= . 5 5 钢 中硫 含量进 一步降低至0 0 1 ~ 0 3 4 / n , 0mn 终 45— . , .0 %
维普资讯
・
4 ・ 20 4 06年 1 1月
第2 7卷第 6期
特殊 钢
S EC AL S E L P I T E
V0. 7 No 6 12 . . N v mb r 2 o o e e o 6
氧气 转炉 出钢 脱 硫 -F精炼 生产 超 低 硫 钢 的工 艺 L
Ha n oNig 。Wa gXih a ,Wa gHato n n u n i ,L n u mi a iHo g ,C i Ai n ,Wa g G oin ,G n in n iLn n u l o gJa a d L i a ( col f ea ug a a dE ooi l n n e n ,U i r t o c neadTc nl y B i g10 8 ; 1Sho o t lr cl n clg a E g er g nv sy f i c n eh o g , ei 00 3 M l i c i i e i S e o j n 2 Sogn ru op B in 0 0 1 huagGopC r , eig10 ) j 4
- 1、下载文档前请自行甄别文档内容的完整性,平台不提供额外的编辑、内容补充、找答案等附加服务。
- 2、"仅部分预览"的文档,不可在线预览部分如存在完整性等问题,可反馈申请退款(可完整预览的文档不适用该条件!)。
- 3、如文档侵犯您的权益,请联系客服反馈,我们会尽快为您处理(人工客服工作时间:9:00-18:30)。
转炉脱硫能力分析
1、经过计算,本厂脱硫率达到51.61%,较一般转炉脱硫率的20%-40%已经处于很高水平;
2、经过分析本厂脱硫率高主要是因为铁水含残锰量较高(大于0.5%),据研究,不同铁水配加锰铁可以提高转炉的脱硫率:
不同铁水含Mn量与配加锰铁的关系
如果采取加锰铁措施,铁水脱硫率有可能再提高,但是由于目前本厂铁水含Mn量已经很高,最多只能再加入2-3kg/t钢的锰铁,否则钢中残Mn过高可能导致钢水出现废品Mn高; 因此配加锰铁在本厂只能提高5%-10%左右的脱硫率,即可增加脱硫0.005%,但成本增加约12-18元/t钢;如果不考虑成分要求,则脱硫率达到60%,需要增加锰铁投入10kg/t,约60-70元/t。
3、 如果采取双渣法操作,铁水脱硫率有可能再提高,但是成本有所增加,而且脱硫率也只能提高5%-10%左右,即可增加脱硫
0.005%,但成本增加约13-18元/t钢:
1)钢铁料消耗,由于双渣操作两次倒渣,增加约2kg/t,约6元/t钢;
2)石灰消耗,二次造渣,增加约5-10kg/t,约2元/t钢;
3)双渣造成的余Mn流失约0.05-0.10%,约5-10元/t钢。
4、如果采用高温法脱硫,则出钢温度每提高10℃,约提高2-5%的脱硫率,但是成本增加约9元/t钢。
1)钢铁料消耗,由于后吹造成FeO升高,钢铁料消耗增加约2kg/t,约6元/t钢;
2)氧气消耗2m3/t钢,约1.2元/t钢;
3)后吹造成拉碳率降低,出钢C降低约0.03-0.04%,增碳剂影响成本约1.2-1.6元/t钢。
4) 后吹造成FeO升高,脱氧剂消耗增加约0.044kg/t,约0.5-1元/t钢;
5) 高温高氧化性操作造成炉衬侵蚀严重,炉衬维护量增加,成本升高,生产节奏变缓,影响产能;
6)高温操作给后道的生产带来影响,减缓了连铸机的生产节奏,并且给铸坯质量带来影响。
5、根据以上分析,本厂铁水脱硫能力,最大可能在60%左右,即如果产品硫含量要求不大于0.045%,则出钢硫含量≤0.040%,要求硫的极限含量为0.100%-0.01-0.007=0.083%;但是需要增加成本投入60元以上。
如果出现铁水含硫量高于0.083%的炉次,则本厂转炉将不能将硫降至0.040%以下。
根据本厂脱硫能力51.61%,要求铁水正常含硫量不大于0.080%-0.01-0.007=0.063%。