高分子材料加工成型原理作业
高分子材料成型加工课件1

的比值约是多少? ②为何热塑性聚合物的成型加工一般不
在高弹态时进行?
共十八页
<<<
熔融指数仪
<<<
共十八页
加工(jiā gōng)方法与熔融指 数值
<<<
共十八页
模塑工艺(gōngyì) 条件
<<<
共十八页
螺旋(luóxuán)流动 试验
共十八页
<<<
内容(nèiróng)总结
高分子成型加工原理。基本任务:聚合物加工是将聚合物转变成实用材料 或制品的一门工程技术。② 应变:剪切应变:物体受外力作用后,一层相对 于另一层移动的距离。可挤压性是指聚合物通过挤压作用形变时获得形状和 保持(bǎochí)形状的能力。可模塑性是指材料在温度和压力作用下形变和在模具 中模制成型的能力。可延性表示无定型或半结晶聚合物在一个或两个方向上 受到压延或拉伸时变形的能力。★ 粘弹性:弹性和粘性的有机组合。螺旋 流动试验
性形变
★ T↑,γH,γV↑且对γV影响更大。 (2) 形变与作用力、作用时间的关系:
★ 当σ↑或T↑,使γH,γV↑;当T↑时,γV增加 的量比γH更多。
共十八页
<<<
1.2.4粘弹性形变(xíngbiàn)的滞后效应 (粘弹性的特例)
★ 概念:在动态力作用下,聚合物分子链由于跟 不上外力作用速度而造成的形变总是落 后于外力作用速度的效应。
• 可模塑性是指材料在温度和压力作用下形变和在模具中模制 成型的能力。
• 表征方法:螺旋流动试验。
模塑工艺条件
螺旋流动试验
共十八页
<<<
《高分子加工原理》课件
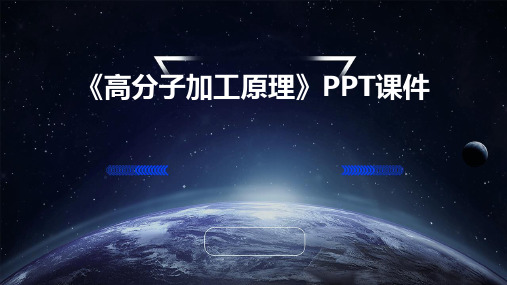
总结词
高分子材料具有粘弹性、热塑性、热固性、绝缘性等特点。
要点一
要点二
详细描述
高分子材料具有粘弹性,表现为在外力作用下既可发生弹性形变,也可发生塑性形变;热塑性是指高分子材料在加热时可以流动,冷却后可以固化;热固性是指高分子材料在加热时可以固化,冷却后性质稳定;绝缘性是指高分子材料具有良好的绝缘性能,不易导电。这些特性使得高分子材料在现代工业和科技领域中具有广泛的应用价值。
热力学第二定律
03
成型工艺参数
介绍影响成型质量的工艺参数,如温度、压力、时间等。
01
高分子材料的加工过程
详细介绍高分子材料的加工过程,包括原料准备、成型、后处理等环节。
02
成型方法
列举常见的成型方法,如注塑、挤出、压延等,并介绍其原理和特点。
高分子材料加工设备与工艺流程
04
设备日常维护
介绍了如何进行日常的设备检查、清洁和润滑工作。
高分子加工技术基础
02
高分子材料通过加热、加压等方式进行成型加工,使其从流动的液体状态转变为固态,并形成所需的形状和结构。
成型原理
成型加工需要使用各种成型设备,如注塑机、压延机、热压机等。
成型设备
成型加工过程中,需要控制各种工艺参数,如温度、压力、时间等,以获得高质量的成型品。
成型工艺参数
二次加工方法
高性能化:随着对高分子材料性能要求的不断提高,加工技术也在不断向高性能化方向发展。通过改进加工工艺和选用高性能的助剂,可以显著提高高分子材料的强度、刚性、耐热性和耐腐蚀性等性能。
高分子材料加工技术在航空航天领域具有广泛的应用前景。由于航空航天器对材料的轻量化和高性能要求极高,高分子材料成为重要的选择之一。通过采用先进的加工技术,可以实现高分子材料的轻量化、高性能化和多功能化,为航空航天器的制造提供更加可靠的支撑。
高分子材料成型加工(含答案)

1.高分子材料成型加工:通常是使固体状态(粉状或粒状)、糊状或溶液状态的高分子化合物熔融或变形,经过模具形成所摇的形状并保持其已经取得的形状,最终得到制品的工艺过程。
2.热塑性塑料:是指具有加热软化、冷却硬化特性的塑料(如:ABS、PP、POM、PC、PS、PVC、PA、PMMA等),它可以再回收利用。
具有可塑性可逆热固性塑料:是指受热或其他条件下能固化或具有不溶(熔)特性的塑料(如:酚醛树脂、环氧树脂、氨基树脂、聚胺酯、发泡聚苯乙烯、不饱和聚酯树脂等)具有可塑性,是不可逆的、不能再回收利用。
3. 通用塑料:一般是指产量大、用途广、成型性好、价格便宜的塑料工程塑料:指拉伸强度大于50MPa,冲击强度大于6KJ/m2,长期耐热温度超过100°C 的、刚性好、蠕变小、自润滑、电绝缘、耐腐蚀等的、可代替金属用作结构件的塑料.4.可挤压性:材料受挤压作用形变时,获取和保持形状的能力。
可模塑性:材料在温度和压力作用下,产生形变和在模具中模制成型的能力。
可延展性:材科在一个或两个万向上受到压延或拉伸的形变能力。
可纺性:材料通过成型而形成连续固态纤维的能力。
5.塑化效率:高分子化合物达到某一柔软程度时增塑剂的用量定义为增塑剂的塑化效率。
定义DOP的效率值为标准1,小于1的则较有效,大于1的较差.6.稳定流动:凡在输送通道中流动时,流体在任何部位的流动状况及一切影响流体流动的因素不随时间而变化,此种流动称为稳定流动。
不稳定流动:凡流体在输送通道中流动时,其流动状况及影响流动的各种因素都随时间而变化,此种流动称之不稳定流动。
7. 等温流动是指流体各处的温度保持不变情况下的流动。
(在等温流动情况下,流体与外界可以进行热量传递,但传入和输出的热量应保持相等)不等温流动:在塑料成型的实际条件下,由于成型工艺要求将流道各区域控制在不同的温度下:而且由于粘性流动过程中有生热和热效应,这些都使其在流道径向和轴向存在一定的温度差,因此聚合物流体的流动一般均呈现非等温状态。
高分子材料成形原理习题及答案

计算题1.PA-66原纤维支数为4500支,在不断增加负荷的作用下,当负荷为8克时,纤维被拉断。
试求:a)旦数D b)特数Tex c)绝对强力P d)相对强度PDPT e)断裂长度LP f)强度极限σ(ρ=1.14)2.某腈纶厂生产的产品经测量其含湿率为2.5%。
a)试折合为回潮率为多少?b)若知回潮率为2%,那么该纤维的每1000公斤的标准重量是多少?3.已知某纤维厂生产PET长丝,规格为128支/3L根,试求a)该长丝的旦数,50米卷重(1)单根纤维的旦数(2)单根纤维的断面直径是多少?(PET:ρ=1.38)4.PET的纺丝温度为286℃,计量泵规格为0.6cm3/r,转速为15r/min,喷丝板孔径为0.3mm,孔数为20孔,孔长为0.5mm,已知η0=210Pa.s,试求流经每孔的yw和压力降Δp。
若为非牛顿流体,非牛顿指数n=0.78,η=140 Pa.s时,其yw和Δp又为多少?5.聚丙烯腈的硫氰酸钠浓水溶液,已知其20℃时的零切粘度为40Pa.S,非牛顿指数为0.43,临界剪切速率为150S-1,粘流活化能为38KJ/mol,问:(1)20℃时,把剪切速率提高到3×104S-1,其表观粘度为多少?(2)把该溶液提高到60℃时其零切粘度为多少?6.涤纶纺丝工艺中所用工艺参数为:纺丝温度280℃,吹风温度30℃,纺丝线上固化点温度80℃,熔体密度ρ=1.20×10-3g/cm3 ,熔体比热容容1.88kJ/kg℃,卷绕丝密度1.38 g/cm3,空气导热系数2.6×10-4J/cm.s.℃,泵供量365g/min,空气运动粘度1.6×10-5m2/s,卷绕速度1000m/min,喷丝板规格Ø0.25mm×400孔,L/D=2,求:(1)纺丝线固化点前的平均直径;(2)纺丝线固化点前的平均速度;(3)纺丝线固化点前的平均给热系数;(4)固化时间。
高分子材料加工成型原理--物料组成及混合 ppt课件

种类
“内润滑”与“外润滑”是相对的,取决于润滑剂与聚合物之间的相溶 性;大多既有外润滑性质,又有内润滑性质,仅少数具有单一性质。
润滑剂
润滑剂加入的影响:
能降低聚合物的流动温度,增加其流动性; 过多的加入,在高的剪切作用条件下会缩短聚合物在设备中的停留时间,以致产生 不均匀熔融物料,同时对材料的玻璃化温度、热变形温度、机械强度和伸长率等都 会有影响; 所以使用润滑剂时应先研究其对熔化的影响,然后再考虑它们的润滑性能。
• 过多,易由成型表面析出(常称起霜),从而影响外观等; • 用量过少不足以起润滑作用;
润滑剂
润滑剂分类: 内润滑剂 外润滑剂 与聚合物的相溶性很小
相溶性
与聚合物相溶性的较大
作用机理
易从内部析至表面而粘附于设 减少聚合物分子间的内聚 备的接触表面 ( 或涂于设备的表 能,降低其熔体粘度,从 面上 ) ,形成一润滑剂层,降低 而削弱聚合物间的内摩擦, 了熔体和接触表面间的摩擦, 改进塑料熔体的流动性能 防止塑料熔体对设备的粘接
影响计量与操作环境
过细粒子易造成粉尘飞扬和容积计量的困难
水分及挥发物含量、结晶度、密度等的影响 对粉(粒)料的配制和制品性能有着较大影响,应很好的 加以控制
增塑剂
概念
作用
作用机理 性质要求
选用原则
使用现状
增塑剂
增塑剂
增塑剂是指增加塑料的可塑性,改善在成型加工时树脂的流动性,并使制品具有 柔韧性的有机物质。 它通常是一些高沸、难以挥发的粘稠液体或低熔点的固体,一般不与塑料发生化 学反应。
高分子加工原理与技术2-成型原理
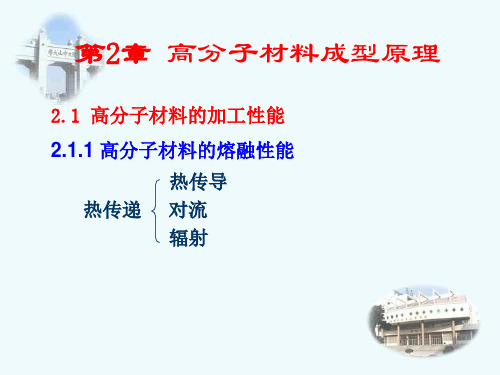
Q=
1 JBiblioteka τ γ·=1 Jηaγ·2
(2-2)
用摩擦热加热塑料是通过挤出机或注射机的螺杆与 料筒的相对旋转运动等途径来实现的。由于聚合物的 表观粘度随摩擦升温而降低,使物料熔体烧焦的可能 性不大,而且塑化效率高,塑化均匀。
2.1.2 高分子材料的流变性能
(1)流动类型
➢层流和湍流 ➢稳定流动与不稳定流动 ➢等温流动和非等温流动 ➢一维流动、二维流动和三维流动 ➢拉伸流动和剪切流动 ➢拖曳流动和压力流动
第2章 高分子材料成型原理
2.1 高分子材料的加工性能 2.1.1 高分子材料的熔融性能
热传导 热传递 对流
辐射
高分子材料的熔融方法:
无熔体移走的传导熔融 有强制熔体移走(由拖曳或压力引起)的传导熔融 耗散混合——熔融 利用电的、化学的或其它能源的耗散熔融方法 压缩熔融
热扩散系数及其影响因素
聚合物熔体在管隙中的流动分析
➢ 圆管通道 ➢ 圆锥形通道
流动缺陷
塑料流体在流道中流动时,常因种种原因使流动出现 不正常现象或缺陷。这种缺陷如果发生在成型时中,则常 会使制品的外观质量受到损伤,例如表面出现闷光、麻面、 波纹以致裂纹等,有时制品的强度或其它性能也会裂变。 这些现象与工艺条件、高聚物的非牛顿性、端末效应、离 模膨胀和熔体破裂有关。
(2)非牛顿型流动
图2-6 各类型流体的流动曲线 a-宾汉流体 b, e-假塑性流体 c-膨胀性流体 d-牛顿型流体
描述假塑性和膨胀性的非牛顿流体的流变行为, 用幂律函数方程 :
τ = Kγ·n
式中 K——流体稠度,Pa·s n——流动指数,也称非牛顿指数。
(3) 时间依赖性流体 这类流体的流变特征除与剪切速率与剪切应力
高分子材料作业
高分子材料作业(总5页) -CAL-FENGHAI.-(YICAI)-Company One1-CAL-本页仅作为文档封面,使用请直接删除高分子材料成型原理平时作业(2)(针对第四章、第五章教学内容)一、单项选择题1.对于切力变稀的纺丝流体, (c )。
A. η0 <ηa<η∞B.ηa<η且ηa<η∞C. η∞<ηa<ηD.ηa>η且ηa>η∞2.熔体纺丝过程的取向主要是( b )的作用。
A.喷丝孔道中的剪切流动取向B.纺丝线上的拉伸流动取向C.纺丝线上的拉伸形变取向D. B+C3. 溶剂的扩散系数 DS 和凝固剂的扩散系数 DN随凝固浴中溶剂含量的增加而( a )。
A. 增大B. 减小C有极小值 D. 有极大值4.拉伸过程中晶区取向因数fc与非晶区取向因素fa的大小通常为( c )。
A. fc>faB. fa>fcC.开始时fc>fa,然后 fa>fcD.开始时 fa>fc,然后fc>fa二、简答题1.简述聚合物流体切力变稀的原因。
2.简述在纺丝过程中减轻或避免漫流型细流的出现的措施。
2三、讨论题1.试述聚合物分子结构对聚合物流体剪切粘性的影响。
答:聚合物分子结构包括链结构、相对分子质量及相对分子质量分布。
(1)链结构的影响聚合物的链结构对流变性能有较大影响。
聚合物分子链柔性越大,缠结点越多,链的解缠和滑移越困难,聚合物流动时非牛顿性越强。
聚合物分子链刚性增加,分子间作用力愈大,粘度对剪切速率的敏感性减小,但粘度对温度的敏感性增加,提高这类聚合物的加工温度可有效改善其流动性。
聚合物分子中支链结构的存在对粘度也有很大的影响。
具有短支链的聚合物的粘度低于具有相同相对分子质量的直链聚合物的粘度;支链长度增加,粘度随之上升,支链长度增加到一定值,粘度急剧增高,且可能比直链聚合物大若干倍。
在相对分子质量相同的条件下,支链越多,越短,流动时的空间位阻越小,粘度越低,越容易流动。
压延成型—压延原理及成型工艺(高分子成型课件)
二、压延机的压延原理
(七)挠度影响及其补偿措施
n横压力:压力分布曲线积分乘以辊筒工作部分长度即为横压力 (分离力)。 n横压力(分离力)的存在使辊筒产生轴向的弹性弯曲变形,从而 出现挠度现象。 n挠度的产生使压延半成品沿宽度方向上的断面厚度不均匀,中间 厚度大,两边厚度小,从而降低了压延质量。 n为减少挠度的影响,必须进行补偿。 n补偿措施有三种: 中高度法;轴线交叉法;预负荷弯曲法。
二、压延机的压延原理
(四)物料在压延时的黏度效应 要使压延顺利进行,要求物料有良好流动性,粘度越小,流动性越好。
①剪切速率与粘度的关系
②压延速度与粘度的关系 n提高压延速度,可提高剪切速率, 降低粘度,提高流动性,有利于压 延成型,但太高时,回弹增加,表 面粗糙度增加,可能损伤帘子线。 n对于对切变速率敏感的聚合物,可 通过调节压延速度来调节流动性。
l-计量装置、2-捏合机3-密炼机4开炼机5-运输带6-压延机7-烘箱8压花机9-冷却辊10-卷取辊
偿效果可以调整,以适应物料性质和压延条件的变化要求,但因补偿 曲线和辊筒挠度曲线之间的差异而使补偿效果受到局限。
二、压延机的压延原理
(七)挠度影响及其补偿措施
3 预负荷弯曲法(预应力法)
辊筒工作负荷作用前,在辊筒轴承的两端 的轴颈上预先施加额外的负荷,其作用方 向正好与工作负荷相反,使辊筒产生的变 形与分离力引起的变形方向正好相反,这 样,在压延过程中辊筒所产生的两种变形 便可以互相时物料会受辊筒的挤压作用,受到压力的区域称为钳住区。辊筒 开始对物料加压的点称为始钳住点,加压终止点为终钳住点,两辊中心 (两辊筒圆心连线的中点)称为中心钳住点,钳住区压力最大处为最大压 力钳住点。 n压力分布:在钳住区,先增加后减小。 n横压力:压力分布曲线积分乘以辊筒工作部分长度即为横压力(分离 力),其与辊筒尺寸、速度、辊距及黏度等相关。 n生产中常通过控制黏度和辊距来控制横压力大小。
高分子材料加工成型原理题库word资料8页
高分子材料加工成型原理题库填空:1.聚合物具有一些特有的加工性质,如有良好的__可模塑性__,__可挤压性__,__可纺性__和__可延性__。
正是这些加工性质为聚合物材料提供了适于多种多样加工技术的可能性。
2.__熔融指数__是评价聚合物材料的__可挤压性__这一加工性质的一种简单而又实用的方法,而__螺旋流动试验__是评价聚合物材料的__可模塑性__这一加工性质的一种简单而又实用的方法。
3.在通常的加工条件下,聚合物形变主要由__高弹形变__和__粘性形变__所组成。
从形变性质来看包括__可逆形变__和__不可逆形变__两种成分,只是由于加工条件不同而存在着两种成分的相对差异。
4.聚苯乙烯(PS)、聚丙烯(PP)、聚氯乙烯(PVC)、聚碳酸酯(PC)、高密度聚乙烯(HDPE)、聚甲基丙烯酸甲酯(PMMA)和聚酰胺(PA)的缩写。
5.聚合物的粘弹性行为与加工温度T有密切关系,当T>Tf时,主要发生__粘性形变__,也有弹性效应,当Tg<T< Tf 时,主要发生__弹性形变__,也有粘性形变。
6.按照经典的粘弹性理论,加工过程线型聚合物的总形变可以看成是__普弹形变__、__推迟高弹形变__和__粘性形变三部分所组成。
7.假塑性流体在较宽的剪切速率范围内的流动曲线,按照变化特征可以分为三个区域,分别是:__第一牛顿区__、__非牛顿区__和__第二牛顿区__。
8.聚合物液体在管和槽中的流动时,按照受力方式划分可以分为__压力流动__、__收敛流动__和__拖拽流动__;按流动方向分布划分:__一维流动__、__二维流动__和__三维流动__。
9.用于测定聚合物流变性质的仪器一般称为__流变仪__或__粘度计__。
目前用得最广泛的主要有__毛细管粘度计__、__旋转粘度计__、__落球粘度计__和锥板粘度计__等几种。
10.影响聚合物流变形为的的主要因素有:_温度_、_压力_、_应变速率_和_聚合物结构因素_以及_组成_等。
高分子材料成型加工习题参考答案
高分子材料成型加工习题参考答案(1~5章)绪论1、高分子材料可应用于哪些方面? 有哪些特点, 答:高分子材料可应用于如下各个方面:结构材料:机械零部件、机电壳体、轴承……电器材料:电缆、绝缘版、电器零件、家用电器、通讯器材…… 建筑材料:贴面板、地贴、塑料门窗、上下水管…… 包装材料:各种瓶罐、桶、塑料袋、薄膜、绳、带、泡沫塑料…… 日用制品:家具、餐具、玩具、文具、办公用品、体育用品及器材……交通运输:道路交通设施、车辆、船舶部件……医疗器械:医疗器具、药品包装、医药附件、人造器官…… 航天航空:飞机、火箭、飞船、卫星零部件……军用器械:武器装备、军事淹体、防护器材…… 交通运输:道路交通设施、车辆、船舶部件……医疗器械:医疗器具、药品包装、医药附件、人造器官…… 航天航空:飞机、火箭、飞船、卫星零部件……军用器械:武器装备、军事淹体、防护器材…… 化纤类:布、线、服装、……高分子材料具有如下特点:优点: a.原料价格低廉; b.加工成本低; c.重量轻; d.耐腐蚀;e.造型容易;f.保温性能优良;g.电绝缘性好。
缺点: a.精度差; b.耐热性差; c.易燃烧; d.强度差; e.耐溶剂性差; f.易老化2、塑料制品生产的完整工序有哪五步组成,答:成型加工完整工序共五个1.成型前准备:原料准备:筛选,干燥,配制,混合 ?2.成型:赋预聚合物一定型样 ?3.机械加工:车,削,刨,铣等。
?4.修饰:美化制品。
?5.装配: 粘合,焊接,机械连接等。
?说明:a 并不是所有制品的加工都要完整地完成此5个工序b 五个次序不能颠倒3、学习本课程的重点是什么,答:本课程的重点是:高分子材料方面:应掌握高分子材料定义,高分子材料工程特征,高分子材料及其制品的制备方法,高分子材料的组成,添加剂的作用、机理、品种及其选择,高分子材料配方设计原则,配方分析,影响高分子材料性能的化学因素和物理因素。
成型加工方面:应掌握高分子材料制品各种成型方法,成型加工过程,成型工艺特点,成型工艺的适应性,成型工艺流程,成型设备结构及作用原理,成型工艺条件及其控制,成型工艺在橡胶、塑料、纤维加工中的共性和特殊性。
- 1、下载文档前请自行甄别文档内容的完整性,平台不提供额外的编辑、内容补充、找答案等附加服务。
- 2、"仅部分预览"的文档,不可在线预览部分如存在完整性等问题,可反馈申请退款(可完整预览的文档不适用该条件!)。
- 3、如文档侵犯您的权益,请联系客服反馈,我们会尽快为您处理(人工客服工作时间:9:00-18:30)。
高分子材料加工成型原理作
业
-标准化文件发布号:(9456-EUATWK-MWUB-WUNN-INNUL-DDQTY-KII
《高分子材料加工成型原理》主要习题
第二章 聚合物成型加工的理论基础
1、名词解释:牛顿流体、非牛顿流体、假塑性流体、胀塑性流体、拉伸粘度、剪
切粘度、滑移、端末效应、鲨鱼皮症。
牛顿流体:流体的剪切应力和剪切速率之间呈现线性关系的流体,服从牛顿黏性定律的流体称
为非牛顿流体。
非牛顿流体:流体的剪切应力和剪切速率之间呈现非线性关系的流体,凡不服从牛顿黏性定律
的流体称为非牛顿流体。
假塑性流体:是指无屈服应力,并具有黏度随剪切速率或剪切应力的增大而降低的流动特性的
流体,常称为“剪切变稀的流体”。
胀塑性流体:是指无屈服应力,并具有黏度随剪切速率或剪切应力的增大而升高的流动特性的
流体,常称为“剪切增稠的流体”。P13
拉伸粘度:用拉伸应力计算的粘度,称为拉伸粘度,表示流体对拉伸流动的阻力。
剪切粘度:在剪切流动时,流动产生的速度梯度的方向与流动方向垂直,此时流体的粘度称为
剪切粘度。
滑移:是指塑料熔体在高剪切应力下流动时,贴近管壁处的一层流体会发生间断的流动。P31
端末效应:适当增加长径比聚合物熔体在进入喷丝孔喇叭口时,由于空间变小,熔体流速增大
所损失的能量以弹性能贮存于体系之中,这种特征称为“入口效应”也称"端末效应"。
鲨鱼皮症:鲨鱼皮症是发生在挤出物表面上的一种缺陷,挤出物表面像鲨鱼皮那样,非常毛
糙。如果用显微镜观察,制品表面是细纹状。它是不正常流动引起的不良现象,只有当挤
出速度很大时才能看到。
6、大多数聚合物熔体表现出什么流体的流动行为为什么P16
大多数聚合物熔体表现出假塑性流体的流动行为。 假塑性流体是非牛顿型流体中最常见的一
种,聚合物熔体的一个显著特征是具有非牛顿行为,其黏度随剪切速率的增加而下降。此外,
高聚物的细长分子链,在流动方向的取向粘度下降。
7、剪切流动和拉伸流动有什么区别?
拉伸流动与剪切流动是根据流体内质点速度分布与流动方向的关系区分,拉伸流动是一个平面
两个质点的距离拉长,剪切流动是一个平面在另一个平面的滑动。
8、影响粘度的因素有那些是如何影响的
剪切速率的影响:粘度随剪切速率的增加而下降;
温度的影响:随温度升高,粘度降低;
压力的影响:压力增加,粘度增加;
分子参数和结构的影响:相对分子质量大,粘度高;相对分子质量分布宽,粘度低;支化程度
高,粘度高;
添加剂的影响:加入增塑剂会降低成型过程中熔体的粘度;加入润滑剂,熔体的粘度降低;加
入填料,粘度升高。
12、何谓熔体破裂产生熔体破裂的原因是什么如何避免
高聚物熔体在挤出过程中,当挤压速率超过某一临界值时挤出物表面出现众多的不规则的结
节、扭曲或竹节纹,甚至支离和断裂成碎片或柱段,这种现象称为熔体破裂。
原因:一种认为是由于熔体流动时,在口模壁上出现了滑移现象和熔体中弹性恢复所引起;另
一种是认为在口模内由于熔体各处受应力作用的历史不尽相同,因而在离开口模后所出现的弹
性恢复就不可能一致,如果弹性恢复力不为熔体强度所容忍,就会引起熔体破裂。
避免熔体破裂需注意:控制剪切应力与熔体温度;设计口模模唇时,提供一个合适的入口角,
使用流线型的结构是防止聚合物熔体滞留并防止挤出物不稳定的有效方法。
第三章 成型用的物料及其配制
4、简述增塑剂的增塑机理,如何选用增塑剂?
增塑剂在加入聚合物大分子后,增塑剂的分子因溶剂化及偶极力等作用而“插入”聚合物
分子之间并于聚合物分子的活性中心发生时解时结的联结点,由于有了增塑剂-聚合物的联结
点,聚合物之间原有的联结点就会减少,从而使其分子间的力减弱,并导致聚合物一系列性能
的改变。选用增塑剂要选择与树脂的相容性好、增速效率高、增塑效果持久、低温柔韧性好、
电绝缘性好、耐老化性好、阻燃性好、毒性低等。
5、何谓稳定剂?简述热稳定剂的稳定机理。
凡在成型加工和使用期间为有助于材料性能保持原始值或接近原始值而在塑料配方中加入
的物质称为稳定剂。热稳定剂的作用机理归纳如下:(1)捕捉降解时放出的HCL。(2)置换不
稳定的氯原子(3)钝化具有催化作用的金属氯化物(4)防止自动氧化(5)与共轭双键结构
起加成作用(6)能与自由基起反应。
8、何谓润滑剂为什么润滑剂有内、外之分
为改进塑料熔体的流动性能,减少或避免对设备的摩擦和粘附以及改进制品表面光亮度
等,而加入的一类助剂称为润滑剂。
润滑剂中有一类与高聚物有一定的相容性,加入后可减少高聚物分子的内聚力,降低其熔
融粘度,从而减弱高聚物分子间的内摩擦,此类润滑剂为内润滑剂。还有一类与高聚物仅有很
小的相容性,它在加工机械的金属表面和高聚物表面的界面上形成一润滑层,以降低高聚物与
加工设备之间的摩擦,此类润滑剂为外润滑剂。不同的相容性让润滑剂有了内外之分。
第五章 挤出成型
2、普通螺杆在结构上为何分段,分为几段各段的作用如何
螺杆的主要功能包括输送固体物料,压紧和熔化固体物料,均化、计量和产生足够的压
力以挤出熔融物料,所以根据物料在螺杆上运转的情况可将螺杆分为加料、压缩和计量三段。
加料段是自物料入口向前延伸约4~8D的一段,主要功能是卷取加料斗内物料并传送给压
缩段,同时加热物料;压缩段(又称过渡段)是螺杆中部的一段,在这段中物料除受热和前移
外,主要是由粒状固体逐渐被压实并软化为连续的熔体,同时还将夹带的空气排出;计量段是
螺杆的最后一段,其长度约为6~10D,主要的功能是使熔体进一步塑化均匀,克服口模的阻力
使物料定量、定压的由机头和口模流道中挤出,所以这一段也称为均化段。
3、根据固体输送率的基本公式,分析当螺杆的几何参数确定之后,提高固体输送
率的途径及工业实施方法。
提高固体输送率可从挤出机结构和挤出机挤出工艺两个方面采取措施。从挤出机结构角度
来考虑,可增加螺槽深度;其次,可降低塑料与螺杆的摩擦系数,这就需要提高螺杆的表面光
洁度;再者,可增大塑料与料筒的摩擦系数,料筒内表面要尽量光洁。
从挤出工艺角度来考虑,关键是控制送料段料筒和螺杆的温度。
9、何谓螺杆压缩比为什么要有压缩比在螺杆结构上如何实现
通常将加料段一个螺槽的溶剂与计量段一个螺槽容积之比称为螺杆的压缩比。
压缩比对塑料挤出成型工艺控制有重要影响。挤出不同的塑料,根据塑料的物理性能选择
螺杆的压缩比。
实现压缩比的途径:变动螺纹的高度或导程;螺杆根径由小变大或外径由大变小;螺纹
的头数由单头变成二头或三头。
13、 用方框图表示出挤出成型工艺,并注明各工艺环节所用的设备。
各工艺环节所用的设备:
原料的预处理和混合:烘箱或烘房;
挤出成型:挤出机、挤出机机头口模;
定性装置:真空定径(真空定径套、冷却水槽、真空泵等)和内压定径;
冷却装置:浸浴式冷却水箱或喷淋式冷却水箱;
牵引装置:滚轮式牵引机或履带式牵引机;
切割装置:圆盘锯切割机或自动星型锯切割机。
第六章 注射模塑
1、名词解释:塑化、塑化压力、注射压力
塑化是注射成型的准备过程,是指物料在料筒内受热达到流动状态并具有良好的可塑性的
全过程。
塑化压力:采用螺杆式注射机时,螺杆顶部熔料在螺杆转动后退时所受到的压力称为塑化
压力,亦称背压。
注射压力:是指柱塞或螺杆顶部对塑料所施加的压力,由油路压力换算而来。
2、注射成型方法适合于何种制品的生产为什么请用框图形式表示一个完整的注
射成型工艺过程。
适合于热塑性塑料及多种热固性塑料制品的生产。
注射成型的成型周期短、生产效率高,能一次成型外形复杂、尺寸精准、带有嵌件
的制品;生产热固性塑料时,不仅使其制品质量稳定、尺寸精准和性能提高,而且
使成型周期大大缩短,劳动条件也得到改善。
6、与挤出机的螺杆相比,注射机的螺杆在结构上、运动上及功能上有何特点?
(1)注射螺杆在旋转时有轴向位移,因此螺杆的有效长度是变化的;
(2)注射螺杆的长径比较小,一般为10-15之间;
(3)注射螺杆的压缩比较小,一般为2-2.5之间;
(4)注射螺杆因有轴向位移,因此加料段应该长,约为螺杆长度的一半,而压缩
段和计量段则各为螺杆长度的四分之一;注射螺杆的螺槽较深以提高生产率;
(5)注射螺杆在转动时只需要它能对物料进行塑化,不需要它提供稳定的压力,
塑化中物料承受的压力是调整背压来实现的;
(6)为使注射时不致出现熔料积存或沿螺槽回流的现象,应考虑螺杆头部的结
构。
13、为什么要保压保压对制品性能有何影响
熔体注入模腔后,由于模具的低温冷却作用,使模腔中的熔体产生收缩。为了
保证注射制品的致密性、尺寸精度和强度,必须使注射系统对模具施加一定的压力
(螺杆对熔体保持一定的压力),对模腔塑件进行补缩,直到浇注系统的塑料冻结
为止。
对制品的密度、克服制品表面缺陷、制品的致密性、尺寸精度和强度都有一定
的影响。
第七章 压延成型
2 简述压延机的基本结构和工作原理。
各类压延机除辊筒数目及排列方式不同外,其基本结构大致相同,主要由机
座、机架、辊筒、辊距调节装置、润滑系统、传动装置、紧急停车装置等部分组
成。
压延成型主要依靠辊筒异向旋转,将熔融塑化的物料带入辊筒间隙,由于辊筒间速比的存
在,辊隙间有速度梯度,使料层间产生相对运动。使熔料在辊筒间隙中受到辊筒挤压延展、拉
伸而成为具有一定规格尺寸连续片(膜)状制品。