浸出工艺介绍.
浸出车间工艺流程
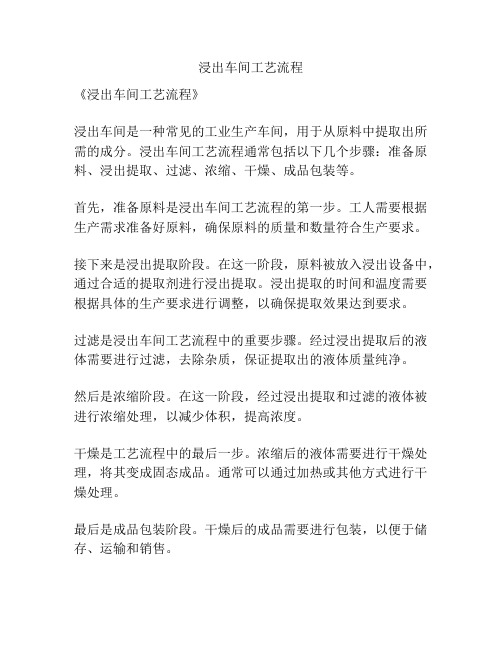
浸出车间工艺流程
《浸出车间工艺流程》
浸出车间是一种常见的工业生产车间,用于从原料中提取出所需的成分。
浸出车间工艺流程通常包括以下几个步骤:准备原料、浸出提取、过滤、浓缩、干燥、成品包装等。
首先,准备原料是浸出车间工艺流程的第一步。
工人需要根据生产需求准备好原料,确保原料的质量和数量符合生产要求。
接下来是浸出提取阶段。
在这一阶段,原料被放入浸出设备中,通过合适的提取剂进行浸出提取。
浸出提取的时间和温度需要根据具体的生产要求进行调整,以确保提取效果达到要求。
过滤是浸出车间工艺流程中的重要步骤。
经过浸出提取后的液体需要进行过滤,去除杂质,保证提取出的液体质量纯净。
然后是浓缩阶段。
在这一阶段,经过浸出提取和过滤的液体被进行浓缩处理,以减少体积,提高浓度。
干燥是工艺流程中的最后一步。
浓缩后的液体需要进行干燥处理,将其变成固态成品。
通常可以通过加热或其他方式进行干燥处理。
最后是成品包装阶段。
干燥后的成品需要进行包装,以便于储存、运输和销售。
总的来说,浸出车间工艺流程涉及多个步骤,每个步骤都需要严格控制和操作,以确保最终的产品符合质量标准。
同时,工艺流程的每个环节都需要根据实际情况进行调整,以提高生产效率和产品质量。
浸出工艺介绍

国标6号溶剂油: a.价格低廉 b.馏程宽,溶耗大
6号溶剂油与正己烷对比
溶剂
工业己烷 国标6号溶剂油
馏程(标准) 实测值
63-71 61-76 ①65.1-68.7 ②65.5-68.9 ①62.8-72.9 ②63-73
含硫
10mg/kg 不大于0.012%
参考标准
GB17602-1998 GB1669-96
湿粕
蒸锅
成品粕
循 环
混合油
并 联 蒸 汽 喷 射 泵
一蒸 二蒸 汽提 毛油
余热混合蒸汽
粕末分离器
热水罐
冷水 冷凝器(蒸)
解析塔
集液罐 油油换热 吸收塔
冷凝器(浸出系统)
自由气体 平衡罐 P211 废气 水封池 排入大气 分水箱 新鲜溶剂
溶剂蒸汽 混合蒸汽 溶剂管道 水管 混合油
P211:蒸汽喷射泵
两个冷凝系统水路 通气路不通
废水
水封池 蒸煮罐
2.1工艺流程说明一
1. 2. 3. 4. 预处理的芝麻饼经水平刮板运送至存料箱 存料箱:门口绿色小罐 存料箱&封闭绞龙均防止 溶剂逸出
经过B形刮板提升至封闭绞龙,经出料口落至浸出器
饼与溶剂在浸出器中接触,混合油浓度由1%以下升高至20%左右 混合油经过栅板流出,再经过滤器,分离混合油中粕末等固体杂质
蒸锅气相温 度表 蒸锅料门高 度
℃ m
90 1.3
三、过程管控参数及溶耗分析
序 号 控制仪表 单 位
一蒸出油 温度 ℃
实测 过程影响
60-62 温度高,可提高一蒸 出油浓度,以减小后 续工段负荷
溶耗结果影响 备注
提高一蒸温度 可降低毛油溶 残
第4章微生物浸出方法

4.2.4 矿堆的构筑
矿堆的构筑一般为2000到4000吨矿石构成一堆, 有时一堆高达5000吨,高度一般在2.5米到3米。 喷淋强度一般在30~50升/m2.h,大多数每天24小 时均匀喷淋,一堆喷淋至少在一个半月左右, 一般在10个月以上即可以达到完全浸出的目的。 虽然渣品位一般比搅拌浸出高一些,但是浸出 率可以基本上保持在70~75%左右。
4.3.3 薄层渗滤浸出(槽浸) 薄层渗滤浸出(槽浸)
薄层渗滤浸出(槽浸)是指将矿石预先堆 置在可以底部排液的渗滤池中,采用顶部喷淋 或底部进液的方式对矿石进行浸泡并浸出的过 程。它和槽式堆浸的方式基本上相同,只是填 矿的矿层比较薄一些,一般情况下矿层大约是 0.5m左右。
Microbio-hydrometallurgy
Microbio-hydrometallurgy
4.2.1 堆浸法的原理
堆浸法的原理:借助于喷洒于矿堆上含有细菌 堆浸法的原理 和化学的溶剂的水溶液流经矿堆时,缓慢流动 的处于非饱和流状态的溶液,经过矿石孔隙与 矿石表面接触,易溶解的金属即溶解在溶液中, 这样永远保证固液相表面溶剂有比较大的浓差。
图4-6 错流浸出工艺流程
Microbio-hydrometallurgy
逆流浸出
浸出时,浸出剂与被浸矿物料运动方向相反,即经几次浸出而 贫化后的矿物与新鲜浸出剂接触,而原始被浸矿物则与浸出液接 触 ,可较充分地利用浸出液中的剩余浸出剂,浸出液中目的组分 含量高,浸出剂消耗量较小,但浸出速度较低,浸出时间较长,需 较多的浸出段数。
Microbio-hydrometallurgy
4.2.8 O2和CO2的供给
一般控制充气速度为0.05~0.1m3/(m3·min)。 除保证供氧外 ,随空气带入的CO2一般也能满 足细菌对碳的需求。
mhp浸出工艺流程

MHP浸出工艺流程1. 简介MHP(氯化镁-氯化硅)浸出工艺是一种常用的提取硅的方法。
该工艺通过将硅矿石与氯化镁和氯化钠混合后加热反应,使硅溶于氯化镁和氯化钠溶液中,最终得到硅和溶液中的其他杂质。
2. 设备和材料准备在进行MHP浸出工艺之前,需要准备以下设备和材料:•反应釜:用于进行反应的容器,通常为不锈钢材质,具有耐腐蚀性。
•加热设备:用于提供反应温度的加热装置,可以是电加热器或火焰加热器。
•搅拌设备:用于搅拌反应物,以促进反应进行。
•氯化镁:作为浸出剂使用,可购买粉末或颗粒状。
•氯化钠:作为助剂使用,可购买晶体或颗粒状。
•硅矿石:待浸出的原料。
3. 浸出步骤MHP浸出工艺通常包括以下步骤:步骤1:准备反应体系1.将适量的氯化镁和氯化钠按照一定比例混合,制备成浸出剂。
根据具体需要和硅矿石的特性,可以调整浸出剂中氯化镁和氯化钠的比例。
2.将制备好的浸出剂倒入反应釜中。
步骤2:加入硅矿石1.将硅矿石加入到反应釜中。
硅矿石可以是粉末、颗粒或块状,根据具体情况选择合适的形式。
2.确保硅矿石均匀分布在浸出剂中。
步骤3:加热反应1.打开加热设备,将反应釜内的浸出体系加热至一定温度。
温度的选择取决于具体实验条件和硅矿石的特性,一般在200-400摄氏度之间。
2.在加热过程中,使用搅拌设备对反应物进行搅拌,以促进反应进行。
步骤4:控制反应时间1.根据实验要求和硅矿石的特性,确定合适的反应时间。
一般情况下,反应时间在2-6小时之间。
2.控制加热时间和温度,确保反应在设定的条件下进行。
步骤5:冷却反应体系1.在反应完成后,关闭加热设备,等待反应体系冷却至室温。
2.可以使用冷却水或其他冷却设备加快冷却速度。
步骤6:分离固液两相1.将浸出后的混合溶液进行固液分离。
可以使用离心机或过滤设备将固体和溶液分离。
2.将固体部分收集起来,即得到硅产品。
步骤7:处理溶液1.将分离得到的溶液进行处理。
根据具体需要和溶液中杂质的特性,可以选择不同的处理方法。
浸出工艺介绍范文

浸出工艺介绍范文浸出工艺是一种常用的化工分离技术,利用溶剂将原料中的有用组分从固体或液体中提取出来。
浸出工艺广泛应用于化学工业、食品工业、药品工业、环保行业等领域。
下面将详细介绍浸出工艺的基本原理、工艺流程和应用。
一、基本原理浸出工艺是利用溶剂与固体或液体原料发生物理或化学作用,从而使有用组分溶解到溶剂中。
该工艺的基本原理有以下几个方面:1.溶解平衡:溶剂在与原料接触后,有利于溶质在溶剂中溶解,形成溶解平衡。
2.扩散传质:浸出过程中,溶剂和溶质之间发生扩散传质过程,使溶质从原料中逐渐转移到溶剂中。
3.传热:浸出过程中,体系需要保持适当的温度,传热有利于提高浸出速率和溶解度。
二、工艺流程浸出工艺的流程可以简单分为以下几个步骤:1.原料制备:将原料进行预处理,如研磨、粉碎、切割等。
以提高溶出速率和回收率。
2.溶剂选择:根据对原料有用组分的溶解性、选择合适的溶剂。
常见的溶剂有水、有机溶剂、稀酸碱溶液等。
3.浸出过程:将原料与溶剂充分接触,使溶质溶解到溶剂中。
浸出时间和浸出温度是影响浸出效果的重要参数。
4.分离回收:将溶液和固体分离,常见的分离方法有过滤、离心、蒸发、结晶等。
通过分离操作,将溶液中的有用组分回收并纯化。
5.溶剂回收:经过浸出后的溶液可能还含有一定量的溶剂,可以通过蒸馏、蒸发等方法将溶剂回收再利用。
三、应用领域浸出工艺在化学工业、食品工业、药品工业、环保行业等领域有广泛应用。
1.化学工业:浸出工艺用于从矿石、矿渣、废弃物中提取金属,如铜、锌、铅等的浸出。
也用于生产有色金属、化肥、磷酸盐等。
2.食品工业:浸出工艺常用于植物油的生产过程中,通过将植物油原料与溶剂接触,将油脂组分溶解到溶剂中。
常用于生产食用油、调味品、提取植物色素等。
3.药品工业:浸出工艺用于药物中活性成分的提取和制备。
通过溶剂与药物原料的接触,将活性成分溶解出来,常用于制药中的提取、分离、纯化过程。
4.环保行业:浸出工艺用于废弃物处理,如污水处理、废弃物处理、固体废弃物的回收等,通过浸出可以将有害物质与废弃物分离,从而实现环境保护和资源回收利用。
【精品】浸出车间工艺流程
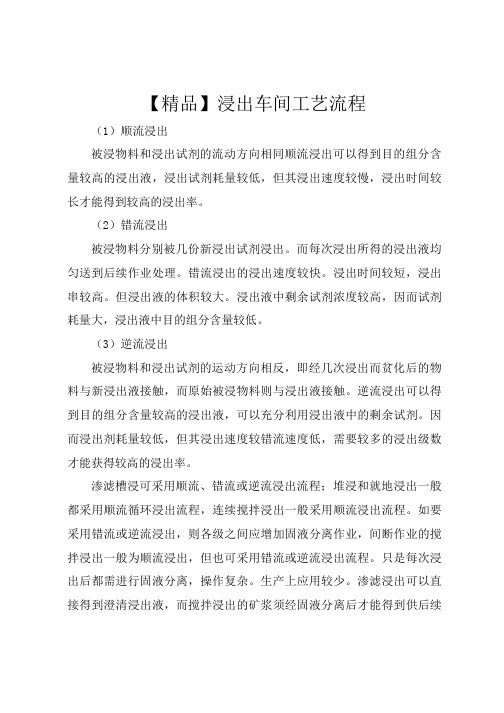
【精品】浸出车间工艺流程
(1)顺流浸出
被浸物料和浸出试剂的流动方向相同顺流浸出可以得到目的组分含量较高的浸出液,浸出试剂耗量较低,但其浸出速度较慢,浸出时间较长才能得到较高的浸出率。
(2)错流浸出
被浸物料分别被几份新浸出试剂浸出。
而每次浸出所得的浸出液均匀送到后续作业处理。
错流浸出的浸出速度较快。
浸出时间较短,浸出串较高。
但浸出液的体积较大。
浸出液中剩余试剂浓度较高,因而试剂耗量大,浸出液中目的组分含量较低。
(3)逆流浸出
被浸物料和浸出试剂的运动方向相反,即经几次浸出而贫化后的物料与新浸出液接触,而原始被浸物料则与浸出液接触。
逆流浸出可以得到目的组分含量较高的浸出液,可以充分利用浸出液中的剩余试剂。
因而浸出剂耗量较低,但其浸出速度较错流速度低,需要较多的浸出级数才能获得较高的浸出率。
渗滤槽浸可采用顺流、错流或逆流浸出流程;堆浸和就地浸出一般都采用顺流循环浸出流程,连续搅拌浸出一般采用顺流浸出流程。
如要采用错流或逆流浸出,则各级之间应增加固液分离作业,间断作业的搅拌浸出一般为顺流浸出,但也可采用错流或逆流浸出流程。
只是每次浸出后都需进行固液分离,操作复杂。
生产上应用较少。
渗滤浸出可以直接得到澄清浸出液,而搅拌浸出的矿浆须经固液分离后才能得到供后续
作业处理的澄清浸出液或含少量矿粒的稀矿浆。
浸出工艺流程图
浸出工艺流程图浸出工艺流程图是一种用来提取物质的常用工艺流程,主要适用于固体或液体物质与溶液接触后,通过溶解、扩散、从固体或液体中分离出目标物质的过程。
下面是一个典型的浸出工艺流程图:一、准备工作:1. 收集需要提取的原料和溶剂;2. 准备提取设备,包括浸泡机、浸出罐、过滤器等。
二、浸泡:1. 将原料放入浸泡机中;2. 加入足够的溶剂,使原料完全浸泡在溶液中;3. 调节浸泡时间和温度,以确保目标物质充分溶解。
三、浸出:1. 将浸泡好的原料倒入浸出罐中;2. 加热浸出罐,使溶液达到目标温度;3. 搅拌溶液,促进目标物质与溶剂的充分接触和扩散。
四、分离:1. 关闭浸出罐,将溶液倒入过滤器中;2. 通过过滤器分离固体和液体,得到目标物质的浸出液;3. 将浸出液收集起来,并做进一步处理或提纯。
五、固液分离:1. 将过滤后的固体物料放入离心机中;2. 进行离心分离,将固体与液体分离,得到干燥的固体物料。
六、最终处理:1. 根据需要,对固体物料进行干燥或粉碎处理,以提高储存、利用或销售的便利性;2. 对提取液进行浓缩、结晶、蒸馏等进一步处理,以提高目标物质的纯度。
通过以上浸出工艺流程图,可以清晰地了解到浸出工艺的基本步骤以及每个步骤的关键操作。
在实际应用中,根据不同的物质和提取要求,还可以对流程进行调整和优化。
这样的流程图有助于提取工艺的规范化和系统化,提高提取效率和产品质量。
值得注意的是,在进行浸出工艺时,应遵循安全操作规范,加强环境保护意识,确保操作人员和周围环境的安全。
此外,还需严格控制工艺条件和操作参数,确保提取效果和产品质量的稳定性和可控性。
只有科学合理地进行浸出工艺,才能更好地实现物质的提取和利用。
浸出工艺课件
第一章 概述 第二章 浸出系统 第三章 湿粕脱溶 第四章 混合油的蒸发系统 第五章 溶剂的冷凝冷却工序(包括总溶剂库) 第六章 自由气体吸收系统 第七章 DT立式脱溶机 第八章 浸出车间的开车和停车操作
第一章 概述
一、浸出法制油概念
浸出法制油是应用萃取的原理,选择某种 能够溶解油脂的有机溶剂,使其与经过预处理 的油料进行接触—浸泡或喷淋,使油料中油脂 被溶解出来的一种制油方法。
8、注意出粕情况,如发生搭桥,要设法消除搭桥的因素。
第三章 湿粕脱溶
为什么要进行脱溶?从浸出器出来的湿粕油料不 同,含溶剂量也不同,预榨饼浸出后含溶剂25%-30%, 在湿粕处理过程中首要任务是脱出粕中溶剂,浸出后 的含溶剂湿粕要进行脱溶剂处理,一是为了安全,二 则是为了溶剂的回收循环使用;三、也关系到粕品质 的优劣。
但同时6号溶剂的缺点也必须引起高度重视和警惕。 (1)它易燃易爆,闪点为-21.7C,遇火即燃,当其蒸 汽在空气中的浓度达到1.2%~7.5%(体积)时,遇到 明火即会发生爆炸。(2)溶剂蒸汽的密度是空气的 2.79倍。这样溶剂蒸汽便会沉积于低洼的地方。(3) 溶剂蒸汽有毒,会强烈地刺激人的神经系统。当其在 空气中的浓度达到30~40mg时,与人接触稍时即会置 人昏迷。
3、经常注意料层渗透是否正常,如发生混合油有溢流翻格现象, 应找出原因,设法排除,保障生产正常进行。
4、发生喷淋堵塞要拆卸清理。 5、定时检查粕中残油,指导生产。 6、各设备运转中要勤看、勤听、勤摸,发现异常和管道堵塞要 及时排除,恢复正常。
7、严禁泵体空运转,注意各泵的流量均衡,如需调节,要按正 常次序进行,不得开错。
入浸料含油15%左右,混合油浓度20-25%左右;
入浸料含油12%左右,混合油浓度18-20%左右;
浸出工艺及设备讲解
设备要求:
1)结构上要求:其搅拌效果好,相应地液-固〔或液-固-气)相 间有良好的传质条件,同时能按工艺要求控制适当的温度 和压力; 2)应有足够的强度且在作业条件下其材质对所处理的物料 有足够的耐腐蚀性能,即应选择适当的材料和内衬。
(1)机械搅拌浸出槽
• 1) 槽体:其材质应对所处理的溶液有良好的耐腐性。普通 碳素钢、搪瓷、钢壳上衬环氧树脂后再砌石墨砖或内衬橡 胶、不锈钢、铸铁、碳钢、高硅铁。 2) 加热系统。用夹套或螺管通蒸气间接加热、蒸气直接 加热。 3) 搅拌系统。涡轮式、锚式、螺旋式、框式、耙式等不 同类型。搅拌的转速、功率随槽尺寸和处理的矿浆性质和 工艺条件要求而定。
(b)连续逆流浸出
根据逆流原理进行精矿浸出,就是在一系列串联的分解槽 中。浸出剂和精矿浆分别由系列的两端加入,精矿与溶剂
4 浸出过程生产及设备
4.2浸出的方法及设备
4.2.1 搅拌浸出
实质:是将充分磨细(0.04~0.1mm以保证足够的比表面 积)原料,然后与浸出剂混合,在激烈搅拌并保证一定温 度的条件下进行反应。 • 参数:有矿石粒度、浸出剂的用量和耗量、液固比、温度 以及时间。 • 搅拌是:为了防止矿粒下沉,调匀浓度或温度,保证固液 相更好的相互接触,减小液膜扩散层的厚度,从而加快浸 出速率,也称“常规浸出”。
(2) 连续浸出
•
(a)连续并流浸出
并流连续浸出是将浸出剂、水和精矿连续加入到反应器 中,并连续卸料。在这种情况下,设计的搅拌系统必须 使固体和液体在溢流时保持进料时的比例。一般是在几 个串联起来的反应器内进行。
• 并流浸出(顺流浸出):被浸物料和浸出剂的流动方 向相同。 • 串联并流连续浸出的特点是: • (a)各单个反应器内反应物的浓度,反应速度是恒 定的,但同一串联系列中各个反应器则互不相同, 可根据浸出过程的要求在不同的反应器内控制不 同的温度、搅拌速度; • (b)设备生产能力大; • (c)易于进行自动控制; • (d)热利用率高,能耗低。 • (f)与连续逆流相比浸出率较低,过程试剂消耗大 残留溶剂浓度高。
浸出工艺和压榨工艺
浸出工艺和压榨工艺
浸出工艺是指将物质依据溶液的性质来进行抽取的工业工序,它是化学工业重要的原
料获取和产品萃取的主要技术手段之一。
浸出工艺涵盖了溶剂抽取、收集、制备和萃取运算,可以从混合物中抽取浓缩有利物质;可以萃取不同组分,同时过滤杂质,可以用于分
离相似分子量的物质、分离复合物的组分等等。
其工艺流程一般包括物料制备、溶剂选择、浸出器选择、溶剂添加和循环收集。
它可
以涉及到大量的分子原理,如蒸汽减压萃取、混合溶剂萃取、离子交换萃取、研磨技术等。
浸出器可以用来实现物质从混合溶液中抽取,将物质从一至多个溶剂中萃取等。
抽取操作
过程由物质和溶剂交换和平衡性决定,一般会比较复杂。
压榨工艺一般指利用机械设备物质乳汁的抽取。
它的原理是利用机械设备将原料通过
压榨使其中的有用组分(如油、乳汁等)从原料中抽取出来,而把残渣排出,对其中的有
用的原料进行清洁、筛拣和干燥等工艺操作,可以获得不同物质的抽取物,如油类和液体
类产品。
在具体操作过程中,需要把原料依据其物理和化学性质进行加工处理,使之变成易于
压榨的状态,否则效果不佳。
首先,原料可以用研磨机对其外部形态和内部结构进行研磨
处理,以加强压榨作用,并降低物料进入压榨机的温度,以减少热损失;同时,需要在进
行压榨前,事先将原料进行现场研磨,以最大限度地提高压榨效率。
在压榨完毕,应尽快
进行下一步操作,以Object减少产品的损失。
- 1、下载文档前请自行甄别文档内容的完整性,平台不提供额外的编辑、内容补充、找答案等附加服务。
- 2、"仅部分预览"的文档,不可在线预览部分如存在完整性等问题,可反馈申请退款(可完整预览的文档不适用该条件!)。
- 3、如文档侵犯您的权益,请联系客服反馈,我们会尽快为您处理(人工客服工作时间:9:00-18:30)。
2.3.4关键步骤说明-分水
自由汽体 冷凝液
分水器连续工作的基础:溶剂的液相压力=出水管中 水相的液相压力 冷凝液自进水管进入分水器,通过伞形帽将混合液 分散于溶剂和水的界面,溶剂相对密度小,浮在上 层,上层溶剂从溶剂出口管3排出。
溶剂
溶剂出口管
液面C
水 进水管 水
水的密度大,沉于底部上升至排水口上部,在这里 形成一个液柱bc,正是这个液柱,保持和溶剂相的 液压力相等,形成稳定的液面c,确保排水时不会将 溶剂排出。
6.
浸出器、热水罐、蒸发系统经蒸汽抽气泵抽出的自由气体,经过一蒸后至浸 出系统冷凝器,浸出系统冷凝器E205、E206、E207。(二楼的三个冷凝器)
2.3关键步骤说明
2.3.1.蒸发:初步除去混合油中溶剂 串联使用的2台长管蒸发器,采用间接蒸汽加热,汽提采用直接蒸汽加热
2.3.2关键步骤说明-汽提
介质2:冷却水
冷却水从进水管进入,经多次折流从 排水管排出。
特点:
两种介质在设备中的折流次数多, 使溶剂蒸汽与冷却水在设备中的 路程延长,便于充分冷凝冷却 增加传热效果:增加冷却水流速,可 大大增加冷却效果
1.进水口;2出水口;4.溶剂蒸汽 进口;11.冷凝液出口管;12.自 由汽体管;13.折流板;6.列管束
稀混合油
溶剂油
溶剂 工业己烷 馏程 63-71 含流量 10mg/kg 参考标准 GB17602-1998 价格元/吨 8000
国标6号溶剂油
63-73
不大于 0.012%
GB1669-96
6500
馏程:65-70℃,溶剂损耗率最低,60 ℃以下和80 ℃以上损耗率均比较高 含硫量高,造成设备腐蚀严重 工业己烷: a.沸点温度低,馏程窄,易蒸发&回收 b.操作温度低,对毛油损害程度低;
价格(元/ 吨)
8000 6500
国标6号:
63
73
因为6号溶剂的初馏点63℃,低于正己烷
69 正己烷:65 两种溶剂馏程对比
的65℃,故6号溶剂比正己烷需要更低的
冷凝温度,方可达到同样的回收效果。 正己烷 3000ppm(均值) 6号溶剂
溶剂种类
上层气相温度
粕残溶
100℃
5000以上
上层气相温度需在原有基础上提高,目前暂定提高10度,再测粕 残溶
原物料走向
浸出制油原理:固液萃取,用可溶解油脂的溶剂对油料喷淋和浸泡, 使油料中的油脂被萃取出来。
液体部分: 混合油 固体部分: 湿粕 蒸发蒸馏 脱溶 脱溶、干 燥 毛油
原料处理
有机溶剂 喷淋浸泡
成品粕
二、工艺流程
芝麻饼 浸出器 喷淋 溶剂
1.浸出系统 2.粕脱溶烘干系统 3.蒸发系统 4.冷凝回收系统
5. 进入第一长管蒸发器,出口温度达到60℃以上 6. 7. 混合油继续进入第二长管蒸发器,出口温度达到110-120℃ 混合油继续进入汽提塔(直接蒸汽加热),脱除毛油中残存溶剂与水分,出口温 度120℃ 8. 9. 浸出毛油泵入毛油暂存罐 板框过滤,进入毛油罐
2.2工艺流程说明二
1. 2. 3. 4. 5. 分水箱中新鲜溶剂 溶剂泵打入虹吸大喷淋
通过控制直接蒸汽的量可以控制气提程度。
单纯增加汽提直接蒸汽量,势必增加后端冷凝 压力,又增加尾气含溶:矛盾1→矛盾2
水蒸气C
2.3.3关键步骤说明-冷凝
3.冷凝:对溶剂蒸汽冷凝,2进3出 介质1:溶剂蒸汽 自进气管进入,经多次折流大部分溶 剂蒸汽在设备中冷凝,冷凝液从出液 管排出,不凝汽提从自由汽提管排出,
湿粕
蒸锅
成品粕
循 环
混合油
并 联 蒸 汽 喷 射 泵
一蒸 二蒸 汽提 毛油
余热混合蒸汽
粕末分离器
热水罐
冷水 冷凝器(蒸)
解析塔
集液罐 油油换热 吸收塔
冷凝器(浸出系统)
自由气体 平衡罐 P211 废气 水封池 排入大气 分水箱 新鲜溶剂
溶剂蒸汽 混合蒸汽 溶剂管道 水管 混合油
P211:蒸汽喷射泵
两个冷凝系统水路 通气路不通
备注
1 2
浸出器变频 器 转子流量计 阀门
浸出制油工艺介绍
2016年9月14日
一、原料介绍
二、工艺流程 三、过程管控参数与溶耗分析 四、溶耗计算与本期精进明细
一、原料介绍
原料饼:最好选小块、薄片状混合物,饼与溶剂接触面积大,容易扩散
圆饼 瓦饼 造粒
油脂浸出的两种扩散:分子扩散、对流扩散
溶 剂
油 料 oil
oil oil
对 浓混合油 流
废水
湿粕、毛油、磷脂等 杂质的混入会导致分 水箱内溶剂乳化
分水箱内溶剂乳化,会 导致分水不彻底,废水 含溶高,增加溶耗。
三、过程管控参数及溶耗分析
序 控制仪表 号 单 位
Hz
实测
38
过程影响
浸出&滴干时间 溶剂比&混合油 浓度
溶耗结果影响
湿粕浸出&滴干长→降 低粕残溶&残油 混合油浓度高→毛油可 降低溶残
国标6号溶剂油: a.价格低廉 b.馏程宽,溶耗大
6号溶剂油与正己烷对比
溶剂
工业己烷 国标6号溶剂油
馏程(标准) 实测值
63-71 61-76 ①65.1-68.7 ②65.5-68.9 ①62.8-72.9 ②63-73
含硫
10mg/kg 不大于0.012%
参考标准
GB17602-1998 GB1669-96
料格ห้องสมุดไป่ตู้合油泵打混合油至前端料格喷淋 滴干时间: 42-48min
溶剂与芝麻饼充分接触(喷淋滴干喷淋循环)
一蒸、二蒸、汽提、蒸锅等高温的溶剂蒸汽以及水蒸汽直接去蒸发系统冷凝 器冷凝E203/204/208,(三楼的三个冷凝器),其中最后一个冷凝器是真 空冷凝器,连接并联的两个蒸汽喷射泵,将走完E208还有余热的混合自由 气体拉至一蒸
2.汽提:实现气液分离,除去毛油中残溶 此过程与精炼制程脱臭类似:都是水蒸气蒸馏
BC排出
AB气液分离
B ABC建立新的汽液 C B AB 均向 A 相平衡:气相中大 气 部分为B→大量B C气相扩 相 扩散至C,B、C气 散 B B 相平衡 AB气液 平衡
A-油 B-溶剂气 C-水蒸气
AB气液平衡 被破坏 源源不断
废水
水封池 蒸煮罐
2.1工艺流程说明一
1. 2. 3. 4. 预处理的芝麻饼经水平刮板运送至存料箱 存料箱:门口绿色小罐 存料箱&封闭绞龙均防止 溶剂逸出
经过B形刮板提升至封闭绞龙,经出料口落至浸出器
饼与溶剂在浸出器中接触,混合油浓度由1%以下升高至20%左右 混合油经过栅板流出,再经过滤器,分离混合油中粕末等固体杂质