出口澳洲消费品包装要求标准
进出口商品的包装要求

进出口商品的包装要求进出口商品的包装材料只有符合进口规定,才能被准许输入进口国,否则进口国海关将不放行。
许多国家以法规形式对进口商品的包装材料进行限制或进行强制性监督和管理。
例如:美国规定进口商品包装不得用稻草,否则将被强行烧毁,新西兰农渔部规定进口商品的包装不得为干草、稻草、竹席等。
为避免上述情况的发生应做到以下几点:1、避免使用含有毒性的材料由于包装不可避免地使用印刷原料或使用粘胶等材料以使两种不同包装材料接合在一起,因此,印刷原料应禁止使用有毒的金属原料,如金粉、银粉或铜粉等,包装容器或标签上所使用的颜料、染料、油漆等应采用不含重金属的原料,作为接合材料的粘剂,除应不含毒性或有害成份外,还应在分离时易于分解。
商品包装业常用泡壳包装材料,如聚氯乙烯(PVC)。
由于这种材料燃烧后产生氯化物,不仅对人体有害,也会对地球臭氧层造成破坏,现已被许多国家列为禁用,因而泡壳包装材料宜使用聚对苯二甲酸乙醋(PET)等无害且易回收的替代品。
2、尽可能使用循环再生材料许多国家或地区的产品越来越多地使用可循环再生材料进行包装,并以此作为进口外国商品的条件之一。
因此,使用可循环再生材料时商品包装是未来产品是否具有竞争力的标志之一。
国际上使用的可循环再生材料多是再生纸,以废纸回收制成的再生纸箱、模制纸浆、蜂浆纸板和纸管等,这些可循环再生材料一般可用于包装内部的缓冲材料或外部包装材料,如发达国家出口电脑、微波炉、复印机等商品均使用此种材料作为包装内垫或外包装材料,深受进口国欢迎。
3、积极开发以植物为包装材料的技术由于植物基本上可以延续不息地重产繁殖,而且大量使用植物一般不会对环境、生态平衡和资源的维护造成危害,囚此,目前许多发达国家都在积极开发以植物为包装材料的技术。
例如美国以玉米、蜀葵、黍子等植物或作物为原料,采用生物分解或光分解技术制成塑胶作为包装物,或由谷类制成植物性包装材料,此外还有些国家将植物性淀粉质材料与瓦楞纸板混合制成可溶性包装材料,回收后不需将两种材料分离,可直接再生为纸制品,这是目前国际上食品类商品包装的一大趋势。
澳洲亨氏食品标准
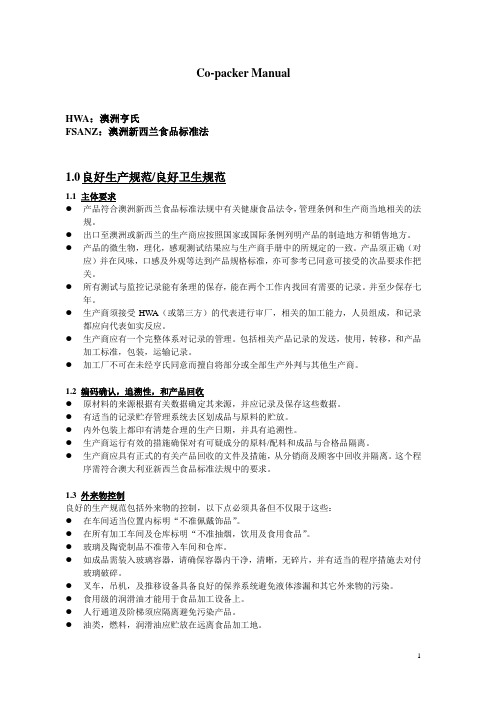
Co-packer ManualHWA:澳洲亨氏FSANZ:澳洲新西兰食品标准法1.0良好生产规范/良好卫生规范1.1 主体要求●产品符合澳洲新西兰食品标准法规中有关健康食品法令,管理条例和生产商当地相关的法规。
●出口至澳洲或新西兰的生产商应按照国家或国际条例列明产品的制造地方和销售地方。
●产品的微生物,理化,感观测试结果应与生产商手册中的所规定的一致。
产品须正确(对应)并在风味,口感及外观等达到产品规格标准,亦可参考已同意可接受的次品要求作把关。
●所有测试与监控记录能有条理的保存,能在两个工作内找回有需要的记录。
并至少保存七年。
●生产商须接受HW A(或第三方)的代表进行审厂,相关的加工能力,人员组成,和记录都应向代表如实反应。
●生产商应有一个完整体系对记录的管理。
包括相关产品记录的发送,使用,转移,和产品加工标准,包装,运输记录。
●加工厂不可在未经亨氏同意而擅自将部分或全部生产外判与其他生产商。
1.2 编码确认,追溯性,和产品回收●原材料的来源根据有关数据确定其来源,并应记录及保存这些数据。
●有适当的记录贮存管理系统去区划成品与原料的贮放。
●内外包装上都印有清楚合理的生产日期,并具有追溯性。
●生产商运行有效的措施确保对有可疑成分的原料/配料和成品与合格品隔离。
●生产商应具有正式的有关产品回收的文件及措施,从分销商及顾客中回收并隔离。
这个程序需符合澳大利亚新西兰食品标准法规中的要求。
1.3 外来物控制良好的生产规范包括外来物的控制,以下点必须具备但不仅限于这些:●在车间适当位置内标明“不准佩戴饰品”。
●在所有加工车间及仓库标明“不准抽烟,饮用及食用食品”。
●玻璃及陶瓷制品不准带入车间和仓库。
●如成品需装入玻璃容器,请确保容器内干净,清晰,无碎片,并有适当的程序措施去对付玻璃破碎。
●叉车,吊机,及推移设备具备良好的保养系统避免液体渗漏和其它外来物的污染。
●食用级的润滑油才能用于食品加工设备上。
●人行通道及阶梯须应隔离避免污染产品。
跨境电商中的产品包装与运输规范
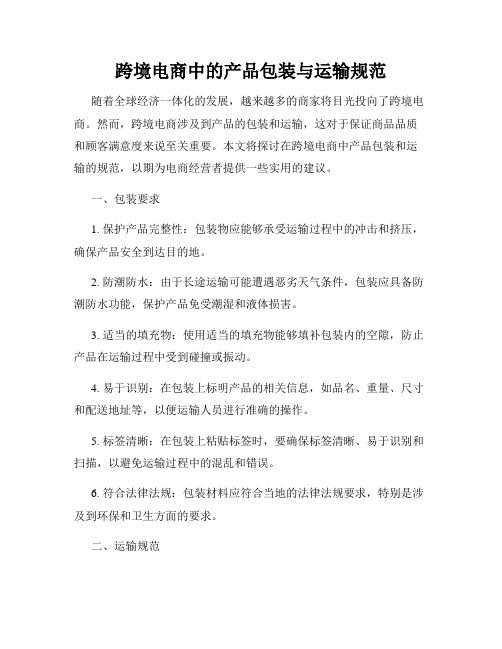
跨境电商中的产品包装与运输规范随着全球经济一体化的发展,越来越多的商家将目光投向了跨境电商。
然而,跨境电商涉及到产品的包装和运输,这对于保证商品品质和顾客满意度来说至关重要。
本文将探讨在跨境电商中产品包装和运输的规范,以期为电商经营者提供一些实用的建议。
一、包装要求1. 保护产品完整性:包装物应能够承受运输过程中的冲击和挤压,确保产品安全到达目的地。
2. 防潮防水:由于长途运输可能遭遇恶劣天气条件,包装应具备防潮防水功能,保护产品免受潮湿和液体损害。
3. 适当的填充物:使用适当的填充物能够填补包装内的空隙,防止产品在运输过程中受到碰撞或振动。
4. 易于识别:在包装上标明产品的相关信息,如品名、重量、尺寸和配送地址等,以便运输人员进行准确的操作。
5. 标签清晰:在包装上粘贴标签时,要确保标签清晰、易于识别和扫描,以避免运输过程中的混乱和错误。
6. 符合法律法规:包装材料应符合当地的法律法规要求,特别是涉及到环保和卫生方面的要求。
二、运输规范1. 合法运输:在跨境电商中,必须确保产品的运输符合两国或多国的相关法律法规,包括运输证件和许可等。
2. 选择可靠的物流公司:电商经营者应选择有良好信誉和专业经验的物流公司合作,确保产品能够及时准确地送达目的地。
3. 合理的运输路径:电商经营者应根据目的地的要求,选择最佳的运输路径和运输方式,以确保产品能够快速而安全地送达。
4. 尽量避免特殊费用:了解各国的运输政策和法规,尽量避免产生额外的特殊费用,如关税、清关费和仓储费等。
5. 合理安排运输时间:根据产品的特性和目的地的需求,合理安排运输时间,以确保产品能够按时送达顾客手中。
6. 跟踪运输进展:在整个运输过程中,及时跟踪运输进展,确保能够及时解决运输中出现的问题,提供更好的服务。
总结:在跨境电商中,产品包装和运输规范至关重要。
通过合理的包装和选择可靠的物流合作伙伴,电商经营者可以保证产品的完整性和安全性,提高顾客满意度。
出口商品的包装要求
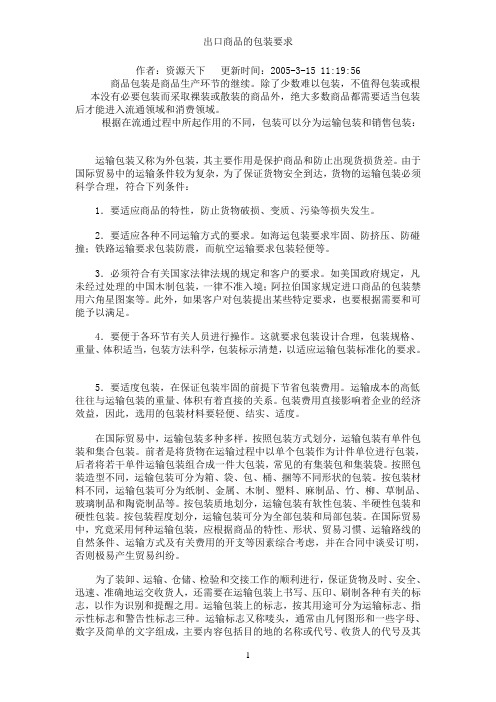
出口商品的包装要求作者:资源天下更新时间:2005-3-15 11:19:56商品包装是商品生产环节的继续。
除了少数难以包装,不值得包装或根本没有必要包装而采取裸装或散装的商品外,绝大多数商品都需要适当包装后才能进入流通领域和消费领域。
根据在流通过程中所起作用的不同,包装可以分为运输包装和销售包装:运输包装又称为外包装,其主要作用是保护商品和防止出现货损货差。
由于国际贸易中的运输条件较为复杂,为了保证货物安全到达,货物的运输包装必须科学合理,符合下列条件:1.要适应商品的特性,防止货物破损、变质、污染等损失发生。
2.要适应各种不同运输方式的要求。
如海运包装要求牢固、防挤压、防碰撞;铁路运输要求包装防震,而航空运输要求包装轻便等。
3.必须符合有关国家法律法规的规定和客户的要求。
如美国政府规定,凡未经过处理的中国木制包装,一律不准入境;阿拉伯国家规定进口商品的包装禁用六角星图案等。
此外,如果客户对包装提出某些特定要求,也要根据需要和可能予以满足。
4.要便于各环节有关人员进行操作。
这就要求包装设计合理,包装规格、重量、体积适当,包装方法科学,包装标示清楚,以适应运输包装标准化的要求。
5.要适度包装,在保证包装牢固的前提下节省包装费用。
运输成本的高低往往与运输包装的重量、体积有着直接的关系。
包装费用直接影响着企业的经济效益,因此,选用的包装材料要轻便、结实、适度。
在国际贸易中,运输包装多种多样。
按照包装方式划分,运输包装有单件包装和集合包装。
前者是将货物在运输过程中以单个包装作为计件单位进行包装,后者将若干单件运输包装组合成一件大包装,常见的有集装包和集装袋。
按照包装造型不同,运输包装可分为箱、袋、包、桶、捆等不同形状的包装。
按包装材料不同,运输包装可分为纸制、金属、木制、塑料、麻制品、竹、柳、草制品、玻璃制品和陶瓷制品等。
按包装质地划分,运输包装有软性包装、半硬性包装和硬性包装。
按包装程度划分,运输包装可分为全部包装和局部包装。
澳大利亚产品标准

STANDARDS USED BY ELECTRICAL REGULATORY AUTHORITIES FOR TYPE TESTING OF PRODUCTSTYPE OF PRODUCT STANDARDAerial amplifier AS/NZS 60065Air cleaner AS/NZS 3350.2.65 or AS/NZS 60335.2.65 Air conditioner AS/NZS 3350.2.40 or AS/NZS 60335.2.40 Air curtain AS/NZS 3350.1 or AS/NZS 60335.1 Appliance connector AS/NZS 60320.1Appliance inlet socket AS/NZS 60320.1Aquarium heater AS/NZS 3350.2.55 or AS/NZS 60335.2.55 Aquarium pump AS/NZS 3350.2.41 or AS/NZS 60335.2.41 Arc welding machine AS/NZS 3195Audio appliances AS/NZS 60065Autoclave AS/NZS 3350.1 or AS/NZS 60335.1 Ballast (electronic) AS/NZS 61347.2.3Ballast (conventional) AS/NZS 61347.2.8Barbecue (outdoor) AS/NZS 3350.2.78 or AS/NZS 60335.2.78 Battery charger (automotive) AS/NZS 3350.2.29 or AS/NZS 60335.2.29 Battery charger (general) AS/NZS 3350.2.29 or AS/NZS 60335.2.29 orAS/NZS 60950Battery charger (industrial, transformer type) AS/NZS 61558Bayonet lampholder adaptor AS 3119Bayonet lampholder—15 or 22 mm AS 3117Beauty therapy equipment AS/NZS 60335.1Bell (alarm) AS/NZS 3100Beverage dispenser AS/NZS 3350.2.75 or AS/NZS 60335.2.75 Blanket AS/NZS 3350.2.17 or AS/NZS 60335.2.17 Blower (garden use) AS/NZS 60335.2.100Bread toaster/Breadmaker AS/NZS 3350.2.9 or AS/NZS 60335.2.9 Business equipment AS/NZS 60950Bustrack system AS/NZS 3100Cable thermoplastic (for fixed wiring) AS/NZS 5000.1 and AS/NZS 5000.2 Capacitor for discharge lamps AS 2644Cash register AS/NZS 60950Ceiling rose AS 3113Chair (motorized) AS/NZS 3350.1 or AS/NZS 60335.1Chair (massage) AS/NZS 3350.2.32 or AS/NZS 60335.2.32Circuit-breaker (not miniature) AS 3947.2 or AS 2184Circuit-breaker (miniature) AS 3111 or AS/NZS 60898.1 or AS/NZS 61009.1 Circular saw (portable) AS/NZS 60745-2-5Clock AS/NZS 3350.2.26 or AS/NZS 60335.2.26Clipper (animal) AS/NZS 3350.2.8 or AS/NZS 60335.2.8Clothes dryer (rotary) AS/NZS 3350.2.11 or AS/NZS 60335.2.11Clothes dryer (cabinet) AS/NZS 3350.2.43 or AS/NZS 60335.2.43Coffee percolator AS/NZS 3350.2.15 or AS/NZS 60335.2.15Compact fluorescent lamp ballast (electronic) AS 61347.2.3Compact fluorescent lamp ballast (conventional) AS 61347.2.8Compressor (refrigerant) AS/NZS 3350.2.34 or AS/NZS 60335.2.3460950 Computer AS/NZS Condenser (air cooled) AS/NZS 3350.1 or AS/NZS 60335.1Conditioning device (portable) AS/NZS 3197Conduits and fittings AS/NZS 2053Connector (appliance) AS/NZS 60320.1Connector (fixed wiring) AS/NZS 3131Connector (industrial) AS/NZS 3123Control device (portable) AS/NZS 3197Controls (automatic) AS/NZS 3161 (for thermostats)Cooking appliance (portable) AS/NZS 3350.2.9 or AS/NZS 60335.2.9Cooking appliance (portable, liquid) AS/NZS 3350.2.15 or AS/NZS 60335.2.15Copying machines AS/NZS 60950Cord extension socket AS/NZS 3120Cord (supply flexible) AS/NZS 3191Cord-line switch AS 3127Cord-line trimmer AS/NZS 60745Data handling equipment AS/NZS 60950Decorative lighting outfit AS/NZS 60598.2.20Deep fryer AS/NZS 3350.2.13 or AS/NZS 60335.2.13 Dehumidifier AS/NZS 3350.2.40 or AS/NZS 60335.2.40 Dishwasher (commercial) AS/NZS 3350.1 or AS/NZS 60335.1Dishwasher (domestic) AS/NZS 3350.2.5 or AS/NZS 60335.2.5Dispensing machine AS/NZS 3350.2.75 or AS/NZS 60335.2.75Display cabinet (illuminated) AS/NZS 60598.1Door opener AS/NZS 3350.2.95 or AS/NZS 60335.2.95Drill (handheld) AS/NZS 60745.2.1Duct heaters AS 3102Ducted skirting AS/NZS 42964296 Ducting AS/NZS Edge trimmer AS/NZS 3350.2.91 or AS/NZS 60335.2.91Edison screw lampholder AS 3140Enclosure for Switchgear or controlgear AS/NZS 3439.3Fabric steamer AS/NZS 3350.2.85 or AS/NZS 60335.2.85Facsimile machine AS/NZS 60950Fan AS/NZS 3350.2.80 or AS/NZS 60335.2.80Fence energizer AS/NZS 3350.2.76 or AS/NZS 60335.2.76Fixed wiring connector AS/NZS 3131Flexible heating pad AS/NZS 3350.2.17 or AS/NZS 60335.2.17Flexible cord (for supply) AS/NZS 3191Floodlight (fixed) AS/NZS 60598.2.1Floor sander (commercial) AS/NZS 3350.1 or AS/NZS 60335.1Floor polisher/scrubber AS/NZS 3350.2.10 or AS/NZS 60335.2.10Floor lamp AS/NZS 3128* or AS/NZS 60598.2.4Fluorescent lamp ballast (electronic) AS/NZS61347.2.361347.2.8Fluorescent lamp ballast (conventional) AS/NZSFluorescent lamp starter (glow) AS/NZS 60155Food mixer/processor (commercial) AS/NZS 3350.1 or AS/NZS 60335.1Food preparation appliance (household) AS/NZS 3350.2.14 or AS/NZS 60335.2.1460335.2.89Food refrigeration cabinets (commercial) AS/NZSFood waste disposers AS/NZS 3350.2.16 or AS/NZS 60335.2.16 Freezer AS/NZS 3350.2.24 or AS/NZS 60335.2.24 Frypan AS/NZS 3350.2.13 or AS/NZS 60335.2.13 Gaming machine (electronic) AS/NZS 60950Garment/fabric steamers AS/NZS 3350.2.85 or AS/NZS 60335.2.85 General purpose outlet AS/NZS 3112Glasswasher (commercial) AS/NZS 3350.1 or AS/NZS 60335.1 Glue gun AS/NZS 3350.2.45 or AS/NZS 60335.2.45 Griller (commercial) AS/NZS 3350.1 or AS/NZS 60335.1 Griller (portable) AS/NZS 3350.2.9 or AS/NZS 60335.2.9 Grinder (portable) AS/NZS 60745.2.3Hair dryer (helmet type) AS/NZS 3350.2.23 or AS/NZS 60335.2.23 Hair dryer (portable) AS/NZS 3350.2.23 or AS/NZS 60335.2.23 Hair care appliances AS/NZS 3350.2.23 or AS/NZS 60335.2.23 Hair clipper AS/NZS 3350.2.8 or AS/NZS 60335.2.8 Hand dryer AS/NZS 3350.2.23 or AS/NZS 60335.2.23 Handlamp (inspection) AS/NZS 60598.2.8Heat pump AS/NZS 3350.2.40 or AS/NZS 60335.2.40 Heater (duct type) AS 3102Heater (room) AS/NZS 3350.2.30 or AS/NZS 60335.2.30 Heater (sauna) AS/NZS 3350.2.53 or AS/NZS 60335.2.53 Heater (thermal storage) AS/NZS 3350.2.61 or AS/NZS 60335.2.61 Heating pad (flexible) AS/NZS 3350.2.17 or AS/NZS 60335.2.17 Heating tool AS/NZS 3350.2.45 or AS/NZS 60335.2.45 Hedge clipper AS/NZS 60745.2.15Hi-Fi equipment AS/NZS 60065High pressure water cleanerAS/NZS 3350.2.79 or AS/NZS 60335.2.79 (commercial/industrial)Hob AS/NZS 3350.2.6 or AS/NZS 60335.2.6 Hot dog steamer AS/NZS 3350.2.15 or AS/NZS 60335.2.15 Hotplate (portable) AS/NZS 3350.2.9 or AS/NZS 60335.2.9 Hotplate unit (hob) AS/NZS 3350.2.6 or AS/NZS 60335.2.6 Humidifier AS/NZS 3350.2.98 or AS/NZS 60335.2.98Immersion heater (fixed) AS/NZS 3350.2.73 or AS/NZS 60335.2.73 Immersion heater (portable) AS/NZS 3350.2.74 or AS/NZS 60335.2.74 Industrial plugs and sockets AS/NZS 3123Information technology equipment AS/NZS 60950Infra-red motion sensor luminaire AS/NZS 60598.2.1Infra-red therapeutic lamp AS/NZS 3350.2.27 or AS/NZS 60335.2.27 Insect repellent device (vaporiser) AS/NZS 3350.1 or AS/NZS 60335.1 Insect electrocutor AS/NZS 3350.2.59 or AS/NZS 60335.2.59 Inspection handlamp AS/NZS 60598.2.8Ironing press AS/NZS 3350.2.44 or AS/NZS 60335.2.44 Iron AS/NZS 3350.2.3 or AS/NZS 60335.2.3 Jigsaw AS/NZS 60745.2.11Jug AS/NZS 3350.2.15 or AS/NZS 60335.2.15 Kettle AS/NZS 3350.2.15 or AS/NZS 60335.2.15 Kitchen machine AS/NZS 3350.2.14 or AS/NZS 60335.2.14 Laboratory equipment AS/NZS 3350.1 or AS/NZS 60335.1 Lampholder (BC 15 or 22 mm) AS/NZS 3117Lampholder adaptor (BC to any) AS/NZS 3119Lampholder (ES 14 or 27 mm) AS/NZS 3140Lawn care appliance AS/NZS 3350.2.91 or 3350.2.92 or AS/NZS60335.2.91 or 60335.2.92Lawnmower AS/NZS 3350.2.77 or AS/NZS 60335.2.77 Light fitting (fixed) AS/NZS 60598.2.1Light fitting (portable) AS/NZS 3128* or AS/NZS 60598.2.4 Lighting transformer AS/NZS 61046Lights (Christmas tree) AS/NZS 60598.2.20Lights (decorative) AS/NZS 60598.2.20Line or flexible blade trimmer AS/NZS 3350.2.91 or AS/NZS 60335.2.91 Liquid heating appliance AS/NZS 3350.2.15 or AS/NZS 60335.2.15 Luminaire (fixed) AS/NZS 60598.2.1Luminaire (motion sensing) AS/NZS 60598.2.1Luminaire (portable) AS/NZS 3128* or AS/NZS 60598.2.4 Massage appliance AS/NZS 3350.2.32 or AS/NZS 60335.2.32Microfilm reader AS/NZS 60950Microwave oven AS/NZS 3350.2.25 or AS/NZS 60335.2.25 Miniature overcurrent circuit-breaker AS 3111 or AS/NZS 60898.1 or AS/NZS 61009.1 Monitor (computer) AS/NZS 60950Motion sensing luminaire AS/NZS 60598.2.1Motor operated appliance (not otherwise listed) AS/NZS 3350.1 or AS/NZS 60335.1Moulded case circuit-breaker (non-domestic) AS 2184 or AS 3947.2Office equipment AS/NZS 60950Office partition/work station AS 3100Oral hygiene appliance AS/NZS 3350.2.52 or AS/NZS 60335.2.52Outlet device (portable) AS/NZS 3105Outlet device (integral pins) AS/NZS 3122Oven (portable) AS/NZS 3350.2.9 or AS/NZS 60335.2.9Oven AS/NZS 3350.2.6 or AS/NZS 60335.2.6Pest controller (electronic) AS/NZS 3350.1 or AS/NZS 60335.160950 Photocopier AS/NZS Planer (portable) AS/NZS 60745.2.14Plug (domestic) AS/NZS 3112Plug (industrial) AS/NZS 3123Plug (appliance) AS/NZS 60320.1Plug pack (electronic) AS/NZS 60950 or AS/NZS 61558.2.17 (& AS/NZS3112 App J)Plug pack (transformer)—general use AS/NZS 61558.2.8 (& AS/NZS 3112 AppJ)Plugs and sockets for installations AS/NZS 3131Point of sale terminal AS/NZS 60950Pool equipment AS/NZS 3136Power supply (electronic) AS/NZS 61558.2.17 or AS/NZS 60950Power supply (transformer)—general use AS/NZS 61558.2.6Pressure cleaner AS/NZS 3350.2.79 or AS/NZS 60335.2.79Printer (computer) AS/NZS 60950Projector (video type) AS/NZS 60065Projector (data type) AS/NZS 60950Projector (overhead, film or slide type) AS/NZS 3350.2.56 or AS/NZS 60335.2.56Pump (aerosol type) AS/NZS 3350.1 or AS/NZS 60335.1Pump (aquarium) AS/NZS 3350.2.41 or AS/NZS 60335.2.41Pump AS/NZS 3350.2.41 or AS/NZS 60335.2.41Pump (swimming pool or spa) AS/NZS 3350.2.41 or AS/NZS 60335.2.41Range AS/NZS 3350.2.6 or AS/NZS 60335.2.6Range hood AS/NZS 3350.2.31 or AS/NZS 60335.2.31Razor AS/NZS 3350.2.8 or AS/NZS 60335.2.8Refrigerant recovery unit AS/NZS 3350.1 or AS/NZS 60335.1Refrigerated food cabinets (commercial) AS/NZS 60335.2.89Refrigerator AS/NZS 3350.2.24 or AS/NZS 60335.2.24Residual current devices (portable) AS 3190Residual current devices (fixed) AS 3190 or AS/NZS 61009.1Rice cooker AS/NZS 3350.2.15 or AS/NZS 60335.2.15Roaster AS/NZS 3350.2.9 or AS/NZS 60335.2.9Room heater AS/NZS 3350.2.30 or AS/NZS 60335.2.30Room heater (storage type) AS/NZS 3350.2.61 or AS/NZS 60335.2.61Router (portable) AS/NZS 60745.2.17Sander (portable) AS/NZS 60745.2.4Saucepan (portable) AS/NZS 3350.2.15 or AS/NZS 60335.2.15Sauna heating appliance AS/NZS 3350.2.53 or AS/NZS 60335.2.53Saw (portable/sabre) AS/NZS 60745.25Scales (electronic) AS/NZS 6095060745.2.2 Screwdriver AS/NZSSewing machine AS/NZS 3350.2.28 or AS/NZS 60335.2.28Shaver AS/NZS 3350.2.8 or AS/NZS 60335.2.8Shaver supply unit AS/NZS 3194Skin care appliance AS/NZS 3350.2.23 or AS/NZS 60335.2.23Smoke detector AS/NZS 3100Socket (cord extension) AS/NZS 3120Socket-outlet adaptor AS/NZS 31223112 Socket-outlet AS/NZSSocket-outlet (industrial) AS/NZS 3123Soldering iron AS/NZS 3350.2.45 or AS/NZS 60335.2.45 Spa pool equipment AS/NZS 3136Spin extractor AS/NZS 3350.2.4 or AS/NZS 60335.2.4 Starter (glow) AS/NZS 60155Starter (electronic) AS/NZS 61347-2-1Supply flexible cord AS/NZS 3191Surface cleaners using liquids AS/NZS 3350.2.54 or AS/NZS 60335.2.54 Swimming pool equipment AS/NZS 3136Switch (component) AS/NZS 61058.1Switch (cord line) AS 3127Switch (for lights or GPO) AS 3133Switch (appliance) AS/NZS 61058.1Switch (wall) AS 3133Switch (non-domestic) AS 3947.3Switchboard (non-domestic) AS 3439Switchgear enclosure AS 3439.3Table lamp AS/NZS 3128* or AS/NZS 60598.2.4 Television receiver AS/NZS 60065Therapeutic lamp AS/NZS 3350.2.27 or AS/NZS 60335.2.27 Thermostat (component) AS/NZS 3161Tile cutter (fixed) AS/NZS 3350.1 or AS/NZS 60335.1 Time switch AS/NZS 3100Toaster (bread) AS/NZS 3350.2.9 or AS/NZS 60335.2.9 Toaster oven (benchtop) AS/NZS 3350.2.9 or AS/NZS 60335.2.9 Tool—Portable type AS/NZS 60745.1Toothbrush AS/NZS 3350.2.52 or AS/NZS 60335.2.52 Touch dimmer AS/NZS 3100 or IEC 60669-2-1Towel rail AS/NZS 3350.2.43 or AS/NZS 60335.2.43 Traffic lantern AS/NZS 3100Traffic controller AS/NZS 3100Transformer (component) AS/NZS 61558Transformer (isolating) AS/NZS 61558.2.6Typewriter (electronic) AS/NZS 60950Ultraviolet therapeutic lamp AS/NZS 3350.2.27 or AS/NZS 60335.2.27 Urn AS/NZS 3350.2.15 or AS/NZS 60335.2.15 Vacuum cleaner AS/NZS 3350.2.2 or AS/NZS 60335.2.2 Vending machine AS/NZS 3350.2.75 or AS/NZS 60335.2.75 Video cassette recorder AS/NZS 60065Video equipment AS/NZS 60065Wall switch AS 3133Warming plate AS/NZS 3350.2.12 or AS/NZS 60335.2.12 Washing machine AS/NZS 3350.2.7 or AS/NZS 60335.2.7 Water bed heater AS/NZS 3350.2.66 or AS/NZS 60335.2.66 Water cooler AS/NZS 3350.2.75 or AS/NZS 60335.2.75 Water heater (instantaneous) AS/NZS 3350.2.35 or AS/NZS 60335.2.35 Water heater (storage) AS/NZS 3350.2.21 or AS/NZS 60335.2.21 Water suction cleaner AS/NZS 3350.2.2 or AS/NZS 60335.2.2 Welding machine (gas shielded) AS/NZS 3195Welding machine (arc) AS/NZS 3195Wok AS/NZS 3350.2.13 or AS/NZS 60335.2.13。
木箱出口澳大利亚标准

木箱出口澳大利亚标准
木箱出口澳大利亚的标准包括以下要求:
1. 澳大利亚、新西兰的检疫要求:出口包装木箱由中国出境前经检疫处理的,须提供中国官方出具的《熏蒸/消毒证书》,方可入境。
如果在中国出境前未能取得中国官方出具的《熏蒸/消毒证书》,该批货物木质包装也可以在输入国口岸的检疫部门监督下,拆除木箱包装进行处理,或连同货物一并处理。
因此,这类货物木质包装在出口前是否向检验检疫机构申报检疫处理由出口企业自行决定。
2. 美国、加拿大、巴西的检疫要求:出口包装木箱使用木质包装的,必须在中国出境前经检疫处理,并取得中国官方出具的《熏蒸/消毒证书》,方可入境。
否则,将被退货、或其他检疫处理。
出口木箱未使用木质包装的,出口企业可以自行出具无木质包装证明或在装箱单、提单、发票上注明该批货物无木质包装声明,便可入境。
3. 欧盟的检疫要求:1999年6月10日起实施的紧急法令(简称1号法令):“木质包装不得带有树皮,不能有直径大于3毫米的虫蛀洞;或者必须对木质包装进行烘干处理,使木材含水量低于20%”。
由于该法令未要求出具官方检疫证书,因此,只要出口企业所使用的木质包装符合上述标准,便可直接出口。
但是,在入境时被输入国检疫部门抽查发现所使用的木质包装不符合上述标准的,将被退货或其他检疫处理。
为了出口木箱在输入国顺利通关,出口企业认为所使用的出口包装木箱不符合上述要求的,可向检验检疫机构申请检疫处理并出具《熏蒸/消毒证书》。
请注意,对于需要使用木质包装的货物,如果出口企业在中国出境前未能取得中国官方出具的《熏蒸/消毒证书》,可以选择在输入国口岸的检疫部门监督下,拆除木箱包装进行处理,或连同货物一并处理。
出口商品包装通则

出口商品包装通则1 范围本标准规定了出口商品包装的基本要求、技术要求、标签、标志和标识。
本标准适用于出口商品(不包括危险货物)包装(以下简称“包装”)。
2 规范性引用文件下列文件对于本文件的应用是必不可少的。
凡是注日期的引用文件,仅注日期的版本适用于本文件。
凡是不注日期的引用文件,其最新版本(包括所有的修改单)适用于本文件。
GB/T 191 包装储运图示标志GB/T 1413 系列1 集装箱分类、尺寸和额定质量GB/T 2934 联运通用平托盘主要尺寸及公差GB/T 4122.1 包装术语第1部分:基础GB/T 4768 防霉包装GB/T 4857.17 包装运输包装件编制性能试验大纲的一般原理GB/T 4879 防锈包装GB/T 4892 硬质直方体运输包装尺寸系列GB/T 5048 防潮包装GB/T 6388 运输包装收发货标志GB/T 7350 防水包装GB/T 13201 圆柱体运输包装尺寸系列GB/T 13757 袋类运输包装尺寸系列GB/T 15233 包装单元货物尺寸GB/T 16470 托盘单元货载GB/T 16716.1 包装与包装废弃物第1部分:处理和利用通则GB/T 16716.3 包装与包装废弃物第3部分:预先减少用量GB/T 16716.5 包装与包装废弃物第5部分:材料循环再生GB/T 16716.6 包装与包装废弃物第6部分:能量回收利用GB/T 16716.7 包装与包装废弃物第7部分:生物降解和堆肥GB/T 17448 集装袋运输包装尺寸系列GB/T 18127 商品条码物流单元编码与条码表示GB/T 18455 包装回收标志GB/T 23156 包装包装与环境术语GB 23350 限制商品过度包装要求食品和化妆品GB/T 28060 进出境货物木质包装材料检疫管理准则GB/T 28206 可堆肥塑料技术要求3 术语和定义GB/T 4122.1和GB/T 23156界定的以及下列术语和定义适用于本文件。
澳洲包装标准

Health and Safety ServicesPolicy for Manual Handling OperationsWithin the University of Paisley CONTENTSCONTENTSINTRODUCTIONRESPONSIBILITY FOR CARRYING OUT RISK ASSESSMENTS ON MANUAL HANDLING OPERATIONS1 General2 Responsibilities of Local Health and Safety Managers LEGISLATION3 Management of Health and Safety at Work Regulations 19994 Manual Handling Operations Regulations 19924.1 Interpretation of the relevant Regulations4.1.1 Regulation 2 - Interpretation - Definition of Certain Terms4.1.2 Regulation 4 – Risk Assessment4.1.3 Reducing the Risk of Injury4.1.4 Reviewing the Manual Handling Assessment4.1.5 Regulation 5 - Duty of Employees5 TRAINING5.1 Manual Handling Techniques for Operators5.2 Training for Manual Handling Assessors6 MAKING A SPECIFIC MANUAL HANDLING ASSESSMENTTask:6.1 TheLoad:6.2 The6.3 The Working Environment:Capability:6.4 IndividualFactors6.5 OtherAppendix 1- Generic Manual Handling Risk Assessment(detailed assessment guidelines filter)Appendix 2 - Good Handling Technique.Appendix 3 - Manual Handling Operations Risk Assessment Form Appendix 4 - Text of the RegulationsINTRODUCTIONThe requirement to carry out risk assessment is implicit in the Health and Safety at Work etc, Act 1974. The duty to assess risks arising out of manual handling operations has been made explicit in the Manual Handling Operations Regulations 1992 which were made under the Health and Safety at Work etc, Act 1974. The duty to assess risk is absolute – it is an offence not to carry out such risk assessments. The Manual Handling Operations Regulations 1992 apply directly to the University of Paisley.This policy document intended to assist Local Health and Safety Managers in:complying with the Manual Handling Operations Regulations 1992carrying out suitable and sufficient risk assessment of manual handling operations andcontrolling the risks arising out of such operations.This policy applies to all departments and units of the University of Paisley including academic, service and self-financing units (units staffed by University employees that provide a commercial service). The requirement to carry out risk assessment of manual handling operations applies to all work within or under the control of the University including research work, undergraduate experiments and both undergraduate and postgraduate project work (including fieldwork) as well as work carried out in service and administrative areas.This policy is not intended to take the place of the Manual Handling Operations Regulations 1992 and the Guidance associated with those Regulations. Local Health and Safety Managers and Manual Handlind Operations Assessors should refer to the above documents as well as this Policy.RESPONSIBILITY FOR CARRYING OUT RISK ASSESSMENTS ON MANUAL HANDLING OPERATIONS1. General1.1 At Unit level the responsibility to ensure that risk assessments are carried out rests with the Local Health and Safety Manager. The process of assessment of manual handling risk requires some knowledge of ergonomics, therefore such assessments must be carried out by staff who have had suitable training in risk assessment of manual handling operations. However the initial decision as to whether an operation falls within the scope of the generic risk assessment (detailed assessment guidelines filter)contained within Appendix 1 of this policy may be made by staff who have had no specialist training. This generic risk assessment is a preliminary assessment and the individual whose work is giving rise to the manual handling risk may carry out this preliminary assessment. The Local Health and Safety Manager must ensure, however, that the work falls within the scope of the generic risk assessment by, for example, auditing of risk assessments during Local Health and Safety Inspections.1.2 Within the University sector, risk assessment of manual handling operations falling outside the scope of the Generic Risk Assessment is carried out at Unit level by those individuals designated and trained as manual handling operations assessors.1.3 The role of Health and Safety Services is to facilitate training and give advice and support as well as auditing risk assessments to ensure that they are “suitable and sufficient” and that, so far as reasonably practicable, appropriate actions have been taken to control risks identified by the risk assessments. It is not the role of Health and Safety Services to carry out risk assessments for units. Health and Safety Services do not have the resources to give that level of support but may give assistance to manual handling operations assessors with particularly difficult assessments.1.4 Courses both for those individuals carrying out manual handling operations and those carrying out the risk assessments for manual handling operations are facilitated by Health and Safety Services.2 Responsibilities of Local Health and Safety ManagersThe Local Health and Safety Manager (LHSM) is required by the University of Paisley Health and Safety Policy to ensure that:a. So far as reasonably practicable, the need for employees (and students) to carry out manual handling operations, that involve a risk of injury, is eliminated.b. All manual handling operations within their unit are identified and compared with the generic assessment contained within Appendix 1 of this document. This is the preliminary assessment.c. Operations not covered by the generic assessment are assessed by a trained manual handling operations assessor and the risk assessment (including appropriate control measures) recorded using the risk assessment form contained within appendix 3 of this document as well as the information and guidance also contained within this document.d. All risk assessments are reviewed at appropriate intervals (annually) or when any change is identified in any of the factors taken into account in making the assessment.e. So far as reasonably practicable, all measures identified in the risk assessment as being necessary to control the risk arising out of manual handling operations are implemented and maintained.f. All employees are made aware of those manual handling assessments relevant to them and the findings of those assessments (including where appropriate the generic risk assessment contained in Appendix 1 of this document and any other generic risk assessments developed by the assessor.g. All employees are trained as necessary in manual handling and the avoidance of injury arising out of manual handling operations. h. All employees are given general indications of the weight and characteristics (centre of gravity, rigidity, etc) of each load and, where reasonably practicable, this information is given by markings on the load.i. All employees are made aware of their legal duty to report accidents and any perceived shortcomings in the risk assessments, manual handling training given or suitability and use of any equipment providedto eliminate or reduce the risk of manual handling injury.j. Those employees nominated to carry out manual handling risk assessments are suitably trained and are provided with the resources to carry out this taskk. All equipment provided to eliminate or reduce the risk of manual handling injury is regularly user checked and where appropriate, formally inspected and, if necessary, tested.LEGISLATION3 Management of Health and Safety at Work Regulations 1999a. The above legislation requires that all hazards are identified and controlled so as to prevent injury. Should the hazard be considered significant then the assessment is required to be recorded and made available to all staff.b. University of Paisley Health and Safety Policy documents “Policy for Carrying out Risk Assessment within the University of Paisley” and “Responsibility for Health and Safety Management”at Faculty/School, Academic Division, Service Division and Unit Level” make clear that the responsibility for ensuring that such risk assessments are carried out lies with the Local Health and Safety Manager.c. During the risk assessment process, should manual handling tasks be identified as likely to cause injury then a separate manual handling assessment is required by the Manual Handling Operations Regulations1992. This may be the generic risk assessment given in Appendix 1 or, if that is not suitable and sufficient, a risk assessment specific to the operations.4 Manual Handling Operations Regulations 1992The objective of the Regulations is to reduce the high numbers of injuries resulting from manual handling , currently about a 25% of all injuries that are reportable to the enforcing authorities.To achieve this the Regulations adopted an ergonomic approach to manual handling which takes into account not only the weight of the load to be moved but also the nature of the task, the working environment and the individual’s capability. It is most important that an assessment should be made of all manual handling operations to determine whether they can be avoided, especially where there is a foreseeable risk of injury. Where elimination is not reasonably practicable, then the introduction of mechanical means to undertake the manual handling operation should be investigated. Finally where elimination or mechanisation of operations is not possible then proper training (incorporatingsuitable ergonomic principles) should be made available for individuals carrying out manual handling operations.4.1 Interpretation of the relevant Regulations4.1.1Regulation 2 - Interpretation - Definition of Certain Termsa. Load - This is defined as a ‘discrete movable object’, such as a box of stationery, a person or animal, a chair or other piece of furniture etc. In the case of an implement or a piece of equipment it would only be described as a load whilst it was being carried eg transported to its place of use, not during its use.b. Manual Handling Operations - This refers to the handling of loads by human effort and not by mechanical means such as hoists, cranes etc. It covers the transporting or supporting by a load, including the lifting, putting down, pushing, pulling, carrying or moving.Where the application of human effort is other than transporting or supporting a load it is not a manual handling operation e.g. pulling on a rope to secure a load (as distinct from dragging it), or operating a control lever on a machine (as distinct from levering a load with a crowbar).4.1.2Regulation 4 – Risk AssessmentIf the general risk assessment carried out as required by the Management of Health and Safety at Work Regulations 1999 indicates a possible risk of injury from manual handling operations it is necessary to consider the following course of action in order of priority:a. Elimination of Manual Handling - Where injury is possible, the first question to ask is whether the movement of the load is necessary, perhaps the desired result could be achieved by other means i.e. by not moving and handling. It may be possible to achieve the objective without manual handling, for example by having suppliers deliver materials to the point of use rather than toa remote storage area.b. Mechanisation/Automation - If the elimination of the tasks is not possible then consideration should be given to mechanisation methods. Examples would be the use of fork-lift or palette trucks or cranes. Even hand barrows and sack trucks while not eliminating manual handling entirely, can reduce the risk. It shouldremembered that some forms of mechanisation can introduce other risks which may need to be addressed.c. Assessment of Risk - In cases where manual handling cannot be avoided or when the weights in the generic assessment at appendix 1 are exceeded or when the general risk assessment made under the Management of Health and Safety at Work Regulations 1992 shows that there is a likelihood of injury, a specific manual handling risk assessment is required. The detail required in each specific risk assessment will depend on the individual circumstances of the manual handling operation being assessed, but each will demand a structured approach, requiring an examination of the task, the load, the working environment and individual capability.Examples of manual handling operations that could demand a detailed assessment are:• wheel-changing on vehicles• transferring boxes of literature or photocopy paper• moving laboratory equipment• handling large quantities of stationery and mail• moving large parcels• stacking/moving chairs• moving gymnasium equipment• handling computer equipment• carrying ladders• loading waste materials onto skips or lorries• pushing loaded trolleysBefore such an assessment is carried out it must be decided how it is to be undertaken, and by whom, and whether there is any relevant information which may be of help.The person carrying out the assessment should have a practical understanding of the type of manual handling task to be performed, the loads to be handled, and the working environment in which the task(s) will be carried out. They should also be a manual handling operations assessor, having successfully completed a manual handling operations assessors course approved by the University of Paisley Health and Safety Services and attended any “top-up” or refresher courses/workshops organised by the University.When carrying out manual handling operations assessments, the views of employees involved in the operations being assessed should be sought and they should be encouraged to play apositive part in the assessment process. They may be more aware of additional factors that can affect the manual handling operation being carried out and how this makes it differ from the management and assessors perception of the operation.Records of accidents and ill-health are particularly useful in the assessment process, not only by identifying accidents associated with manual handling but by also linking bad manual handling practice with ill-health problems such as back or shoulder pain.d. Level of detail in an assessment - The Regulations state that an assessment should be ‘suitable and sufficient’. The complete range of manual handling tasks employees are expected to perform should therefore be carefully considered. Where similar tasks are carried out generic risk assessments are quite acceptable. Thes should, however, set control measures based on the highest risk operation covered by the generic risk assessment. Those carrying out the assessment must be familiar with the manual handling operations and consult with employees. For example the delivery of packages and mail to a number of sites could be investigated by looking at the types of task, the load and working environment and then reviewing a selection of them. Having established a range of manual handling risks it is then essential to decide on the appropriate steps to eliminate or reduce those risks. Assessments can only cover those risks that are known and which are foreseeable, and the measures taken to deal with these may be used as a ‘template’ for the unusual or one-off manual handling tasks.e. Recording the assessment - Where an assessment illustrates significant findings it should be recorded and so long as it remains relevant it must be readily accessible.However the assessment need not be recorded if:• • it could be easily repeated and the task is simple e.g. normal basic everyday manual handling operations such as carrying a bag of tools, re-moving/replacing files or light equipment, lifting and carrying a bucket of water. However, all of these would be covered by the generic risk assessment at Appendix 1.the manual handling operations are straight forward, are being carried out by individuals who have received manual handling training, are of low risk (as perceived by a trained manual handling assessor), and of shortduration, so that the time taken to record them would bedisproportionate to the risk.Section 6 details the questioning required to complete a manual handling assessment and Appendix 3 is the manual handling assessment form.4.1.3Reducing the Risk of InjuryWhere it is not possible to avoid the need for employees to undertake manual handling operations that may involve a risk of injury, steps must be taken to avoid, so far as is reasonably practicable, the risk.Again this must be tackled with the same structured approach used duringthe assessment, considering the task, the load, the working environment and individual capability of those invoved in the operation. The assessor must look at these factors holistically, taking into account the relationship between them. This structured, ergonomic approach should ensure that the manual handling operation is tailored to suit the individual rather than the other way round.As previously stated the use of mechanical aids should always be considered when manual handling tasks are deemed essential. These aids can take the following forms:-a. a simple lever reduces the risk of injury by lessening the bodily force required to move a load or by removing fingers from a possible ‘trapping’ or crushing injury.b. hoist (powered or hand operated).c. a trolley, sack truck, or roller conveyor to avoid lifting and carrying.d. chutes using gravity, to move loads.e.hand-held hooks or suction pads assist in handling loads that are difficult to grasp.f. Boxes to contain small and/or slippery objects or packagesIt is important when choosing a mechanical aid that it is suitable for the task and does not in itself create other or additional risks. An example of this is the manually operated hoist which can lead to the operator developing shoulder pain from the action needed to elevate the hoist. Many models of hoist have a battery operated option which, while more expensive, is preferable when the hoist is to be used frequently.It may be useful to hire or lease equipment such as powered stair climbing barrows prior to or instead of purchasing it.This gives theusers and the assessors the opportunity to determine the equipment’s suitability for purpose prior to purchase.Users must be trained in the use of any equipment provided to reduce risk arising out of the manual handling operations The Provision and Use of Work Equipment Regulations 1998 apply to all such equipment.If mechanical aids cannot be used or the task modified to reduce the risk of injury then employees should be suitably trained in moving and handling.4.1.4Reviewing the Manual Handling AssessmentAll manual handling assessments should be reviewed annually or when there has been a significant change to the task, load, environment or the individual.Reassessment should always be carried out if there is any reason to believe that the original assessment may no longer valid for any reason, for example following an accident or receipt of relevant information from operators4.1.5Regulation 5 - Duty of EmployeesThis regulation supplements the general duties placed on employees by Section 7 of the Health and Safety at Work etc Act 1974 and Regulation 12 of the the Management of Health and Safety at Work Regulations 1999.Regulation 5 of the Manual Handling Operations Regulations 1992 requires employees to follow appropriate systems of work developed out of manual handling risk assessments to ensure their health and safety while carrying out manual handling tasks. The Guidance to these Regulations makes it clear that employees are required to co-operate with their employer to enable that employer to comply with their health and safety duties. Regulation 5, therefore, requires employees of the University of Paisley to follow appropriate systems of work provided by the University to ensure their health and safety whilst carrying out manual handling tasks.Section 7 of the Health and Safety at Work etc Act 1974 requires that employees ensure their own health and safety and that of others who could be affected by their acts and omissions. Regulation 12 of the the Management of Health and Safety at Work Regulations 1999 requires employers to co-operate with their employer to ensure health and safety. They are required by this regulation to follow procedures for health and safety and use anything provided for their health and safety in accordance with training and instruction they have received. “Anything”, in thiscontext, includes equipment supplied for health and safety and safe systems of work. Employees are also required to to point out to their employer any situation that could give rise to serious or immediate danger to health and safety or any shortcomings in health and safety arrangements in the workplace. This requirement would include notifying the employer of any change to a manual handling operation that (in the opinion of the operator) could affect the validity of the risk assessment.Finally, regulation 10 of the Personal Protective Equipment at Work Regulations 1992, requires that employees use personal protective equipment (eg. Back supports, safety shoes, gloves, etc), that is supplied as the result of a risk assessment, in accordance with training and instruction.5 TRAINING5.1Manual Handling Techniques for OperatorsLocal Health and Safety Managers are required to ensure that all employees under their control who may undertake manual handling tasks are suitably trained and retrained, as necessary, in manual handling techniques. Health and Safety Services facilitate such courses on a regular basis.Retraining will be given on the basis of a risk assessment that will include, length of time since initial training or top-up/refresher training last received, changes to University Health and Safety Policy, legislation, guidance or good practice, indications of problems with manual handling operations leading to an accident or accidents arising out of such operations, etc.5.2Training for Manual Handling AssessorsOnly those staff who have successfully completed a manual handling assessors training course approved by Health and Safety Services may carry out manual handling risk assessment. Health and Safety Services facilitate such training and will organise places on approved courses as required and as soon as reasonably practicable after the need for such training arises.In addition, manual handling operations risk assessors may be required individually or as a group to attend top-up/refresher training to reinforce or modify their initial manual handlingoperations assessor’s training. Top-up/refresher training will be organised on the basis of needs identified by Health and Safety Services as the result of a risk assessment. Factors considered in such a risk assessment will include, length of time since initial training or top-up/refresher training last received, changes to legislation, guidance or good practice, indications of problems with manual handling operations leading to a Divisional or institutional increase in the number of accidents arising out of such operations, etc.6 MAKING A SPECIFIC MANUAL HANDLING ASSESSMENTWhen the generic risk assessment at appendix 1 does not cover a manual handling operation (or group of operations), a specific assessment will be required for that operation, or a generic assessment for the group of similar operations. The assessment should be structured using the question set below.Task:6.1 TheIs the load held or manipulated at a distance from the trunk?As the load is moved away from the trunk, the level of stress on the lower back rises. As a rough guide, holding a load at arms’ length imposes about five times the stress experienced when holding the load close to the body. Equally the further away the load, the less easy it is to control. The arms and hands become fatigued more quickly and there is also a loss of the assistance provided by friction between the load and the operator’s torso.Is the operator adopting a good posture?Good posture is vital to maintain control of the load. For example if the body weight is forward so that the heels are off the ground and the feet are close together the lack of stability could result in injury. Feet should be planted firmly on the ground or floor and be nseparated (by approximately the width of the hips) for stability.Does the task involve twisting the trunk?If the trunk is twisted, especially whilst carrying a load, stress on the lower back will be significantly increased and so this postural movement must be avoided .Does the task involve stooping?This occurs when the handler stoops by bending the back or by leaning forward with the back straight. In both cases the trunk is thrust forward and its weight is added to the load being handled.Does the task involve reaching upwards?This posture puts stress on the back and arms and makes it more difficult to control the load.Does the task involve lifting or lowering through an excessive distance?Whenever possible lifts starting at ground level should be avoided, if this is not feasible the lift should terminate at waist height. Excessive lifting or lowering can also demand a change in grip part way through the lift, thereby increasing the risk of injury.Does the task involve excessive carrying distances?If a load can be safely lifted and lowered it can also be carried without risk of injury, however, distances should be limited to 10 metres, to avoid the effort required for carrying exceeding that necessary to lift and lower the load.Does the task involve excessive pushing or pulling of the load?The risk of injury is increased if pushing or pulling is carried out with the hands much below the height of the knuckle of the hands when placed at the sides of the body, or above shoulder height.In addition, because the pushing and pulling forces are transmitted from the handler’s feet to the floor, there is a risk of slipping, especially if unsuitable footwear is worn or the floor is slippery.Does the task involve a risk of suddenor unpredictable movement of the load?Loads that suddenly jerk free can cause injury, especially if the handler’s posture is unstable. These problems are often encountered when moving and handling people, especially if they are confused and uncooperative. Loads packed in unsuitable containers, such as old cardboard boxes are also a potential hazard. This is especially true where the box is too large for the load and consequently allows the to move around within the box, giving a constantly changing centre of gravity.Does the task involve frequent or prolonged physical effort?Frequent movement of a load can result in unsynchronised or hurried movements that can multiply the load’s effect on the body. Prolongued repeated physical effort may cause fatigue that can lead to loss of control of the load.Does the task involve insufficient rest periods?Muscles need time to recover from physical exertion Tired muscles are more susceptible to injury.Does the task involve a rate of work imposed by a process?Though this often refers to the hazards of production line work it can arise when there is pressure of work in a situation in which work has to be completed within a prescribed time. Good systems of work are therefore crucial to safe manual handling.Does the task involve handling while seated?This method of handling puts stress on the weaker muscles of the arms and trunk. Lifting below the level of the work surface will also result in twisting and stooping.Does the task involve team handling?Loads which are beyond the capability of one person should be handled by two or more. It should be remembered however that as a general guide, the capability of a two person team is two thirds the sum of the their individual capabilities. In the case of steps or slopes, e.g. ramps, most of the weight will be borne by the handler(s) at the lower end. Care must also be taken to ensure that team members do not interfere with each other’s vision or movement. Team handling can be hazardous when team members have different levels of expertise, physical ability or height differences. It is important that a strategy for the lift is decided by the team before attempting the lift. One member of the team must be designated as the team leader and the other team members required to follow that member’s direction. This further implies that the training that staff have received is consistent.6.2 TheLoad:Is the load heavy?The weight of the load is only one consideration affecting the risk of injury, The traditional approach, relying on a symmetrical two handed lift of a heavy load, i.e. in front of, and close to the body, is no longer appropriate. Many lifts are asymmetrical, i.e. involving sideways movement and twisting of the trunk, therefore an approach to manual handling which relies solely on weight and symmetry, can be misleading.。
- 1、下载文档前请自行甄别文档内容的完整性,平台不提供额外的编辑、内容补充、找答案等附加服务。
- 2、"仅部分预览"的文档,不可在线预览部分如存在完整性等问题,可反馈申请退款(可完整预览的文档不适用该条件!)。
- 3、如文档侵犯您的权益,请联系客服反馈,我们会尽快为您处理(人工客服工作时间:9:00-18:30)。
出口澳洲消费品包装要求标准澳大利亚作为一个发达国家和世界上最大的消费品进口国之一,对进口商品的包装要求非常严格。
澳洲消费品包装要求标准体现了消费者健康安全、环境保护和信息透明等方面的考虑。
本文将详细介绍澳洲对进口消费品包装的要求标准。
首先,澳大利亚消费品包装要求标准充分保障了消费者的健康安全。
所有进口消费品的包装必须符合澳洲相关法规和标准,确保包装材料不会对商品质量和消费者健康产生任何危害。
比如,食品包装必须符合澳洲食品标准局(FSANZ)制定的标准,包括包装材料的食品安全性、防腐剂和添加剂的使用等方面的要求。
此外,药品、化妆品等特殊商品的包装也需要符合相应的法规和标准,确保产品的安全性和有效性。
其次,澳大利亚消费品包装要求标准注重环境保护。
澳洲一直致力于推动可持续发展和环境保护,因此,对进口消费品的包装提出了严格的要求。
包装材料必须符合环保要求,比如食品包装不得使用有毒有害的化学物质,塑料包装必须经过环境友好的处理等。
此外,澳
洲还鼓励回收利用和减少包装废物的产生,进口商品的包装必须符合相关回收和再利用的要求。
另外,澳洲消费品包装要求标准还注重信息透明。
包装上必须清晰地标明商品的相关信息,包括商品名称、性能参数、规格型号、生产日期、保质期、生产厂商和进口商的信息等。
这样可以使消费者了解产品的基本情况,并能够进行准确的选择和比较。
此外,对于某些特殊商品,比如药品、化妆品和婴儿食品等,包装上还必须标示详细的使用说明和警示语,以保障消费者的安全。
最后,值得注意的是,澳大利亚消费品包装要求标准是根据不同类型的商品和特定领域的法规制定的,具体要求可能会有所不同。
比如,食品包装的要求会涉及到食品安全法规和标准,而药品包装则会受到药品管理法规的约束。
因此,进口商在将商品出口澳大利亚之前必须对相关法规和标准有充分的了解和遵守。
总结起来,澳大利亚消费品包装要求标准是为了保障消费者的健康安全、环境保护和信息透明,是进口商品顺利销售和畅通消费者信任的基础。
进口商在出口澳洲消费品之前,必须仔细研究和遵守相关标准,确保产品的合规性。
同时,澳洲政府也应继续加强监管力度,
确保进口商品的包装质量和合规性。
只有保持对消费品包装要求标准的持续关注和规范管理,才能促进消费品贸易和消费者权益的双赢。