质量问题分析解决七步法
pfema七步法
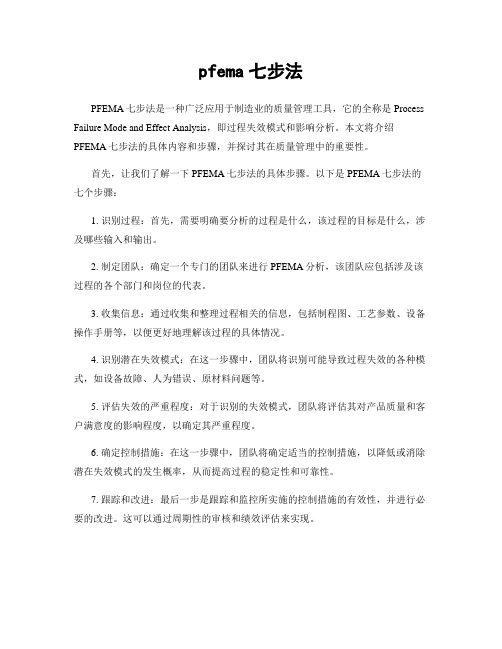
pfema七步法PFEMA七步法是一种广泛应用于制造业的质量管理工具,它的全称是Process Failure Mode and Effect Analysis,即过程失效模式和影响分析。
本文将介绍PFEMA七步法的具体内容和步骤,并探讨其在质量管理中的重要性。
首先,让我们了解一下PFEMA七步法的具体步骤。
以下是PFEMA七步法的七个步骤:1. 识别过程:首先,需要明确要分析的过程是什么,该过程的目标是什么,涉及哪些输入和输出。
2. 制定团队:确定一个专门的团队来进行PFEMA分析,该团队应包括涉及该过程的各个部门和岗位的代表。
3. 收集信息:通过收集和整理过程相关的信息,包括制程图、工艺参数、设备操作手册等,以便更好地理解该过程的具体情况。
4. 识别潜在失效模式:在这一步骤中,团队将识别可能导致过程失效的各种模式,如设备故障、人为错误、原材料问题等。
5. 评估失效的严重程度:对于识别的失效模式,团队将评估其对产品质量和客户满意度的影响程度,以确定其严重程度。
6. 确定控制措施:在这一步骤中,团队将确定适当的控制措施,以降低或消除潜在失效模式的发生概率,从而提高过程的稳定性和可靠性。
7. 跟踪和改进:最后一步是跟踪和监控所实施的控制措施的有效性,并进行必要的改进。
这可以通过周期性的审核和绩效评估来实现。
经过以上七个步骤的分析和实施,PFEMA七步法可以帮助制造企业识别潜在的风险和问题,并采取相应的控制措施,以确保产品质量和客户满意度。
下面我们将探讨PFEMA七步法在质量管理中的重要性。
首先,PFEMA七步法有助于预防问题的发生。
通过识别潜在的失效模式和评估其严重程度,企业可以采取相应的控制措施,以避免问题的出现。
这有助于降低产品的不合格率和退换货率,提高企业的生产效率和经济效益。
其次,PFEMA七步法可以提高企业的管理能力。
通过制定专门的团队来进行PFEMA分析,并收集和整理相关信息,企业能够更全面地了解和控制其生产过程。
fmea的7步法

fmea的7步法FMEA的7步法随着现代工业的发展,各行各业对产品质量和安全性的要求越来越高。
为了确保产品在设计和生产过程中的质量和可靠性,FMEA(失效模式与影响分析)成为一种被广泛采用的方法。
FMEA通过对潜在失效模式的分析和评估,可以帮助我们识别和减少潜在的风险和问题,从而提高产品的质量和可靠性。
本文将介绍FMEA的七个步骤,以帮助读者更好地理解和应用FMEA。
第一步:确定团队和范围在进行FMEA之前,首先需要确定一个专门的团队来进行分析。
团队成员应包括设计师、工程师、生产人员等相关人员。
确定团队后,需要明确分析的范围,包括产品、过程或系统等。
确定团队和范围是FMEA分析的基础,确保分析的全面性和准确性。
第二步:收集产品和过程信息在进行FMEA之前,需要收集关于产品和过程的相关信息。
这些信息可以包括产品规格、设计图纸、工艺流程、设备参数等。
通过收集这些信息,可以全面了解产品和过程的特点和要求,为后续的分析提供准确的基础。
第三步:识别潜在失效模式在这一步骤中,团队成员需要识别出产品或过程中可能出现的潜在失效模式。
失效模式是指产品或过程在特定条件下的失效形式。
通过集思广益和经验分享,团队成员可以识别出多种可能的失效模式,包括设计失效、工艺失效、材料失效等。
第四步:评估失效的严重性在这一步骤中,团队成员需要评估每个失效模式的严重性,即失效对产品或过程的影响程度。
评估严重性可以从多个方面考虑,如安全性、可靠性、经济性等。
通过评估失效的严重性,可以确定优先处理的失效模式,以确保资源的合理利用。
第五步:确定失效的原因在这一步骤中,团队成员需要分析并确定每个失效模式的原因,即导致失效发生的根本原因。
原因分析可以使用各种方法,如鱼骨图、5W1H法等。
通过确定失效的原因,可以为下一步的控制措施提供指导和依据。
第六步:制定控制措施在这一步骤中,团队成员需要制定相应的控制措施,以减少或消除潜在失效的发生。
控制措施可以包括改进设计、优化工艺、改进材料等。
质量管理七步法

质量管理七步法质量管理七步法是一种有效的质量管理方法,它可以帮助企业提高产品和服务的质量,提高客户满意度,增强企业竞争力。
本文将详细介绍质量管理七步法的具体内容和实施步骤。
第一步:明确质量目标明确质量目标是质量管理的第一步。
企业应该根据市场需求和客户要求,制定符合实际的质量目标。
质量目标应该具有可衡量性和可达成性,同时也要与企业的战略目标相一致。
明确质量目标可以帮助企业更好地规划和组织质量管理工作,提高工作效率和质量水平。
第二步:制定质量计划制定质量计划是质量管理的第二步。
质量计划是指为实现质量目标而制定的具体措施和方法。
质量计划应该包括质量标准、质量控制点、质量检查方法、质量纠正措施等内容。
制定质量计划可以帮助企业更好地组织和管理质量工作,确保产品和服务的质量符合要求。
第三步:实施质量计划实施质量计划是质量管理的第三步。
实施质量计划需要全面、系统地执行质量计划中的各项措施和方法。
企业应该建立质量管理体系,明确各项质量管理职责和任务,加强质量培训和教育,提高员工的质量意识和技能。
实施质量计划可以帮助企业更好地控制和管理产品和服务的质量,提高客户满意度。
第四步:检查质量检查质量是质量管理的第四步。
检查质量是指对产品和服务进行质量检查和测试,以确保其符合质量标准和要求。
企业应该建立质量检查机制,制定质量检查标准和方法,加强质量检查人员的培训和教育。
检查质量可以帮助企业及时发现和纠正质量问题,提高产品和服务的质量水平。
第五步:纠正质量问题纠正质量问题是质量管理的第五步。
纠正质量问题是指对发现的质量问题进行分析和处理,以消除质量问题的根本原因。
企业应该建立质量纠正机制,制定质量纠正措施和方法,加强质量纠正人员的培训和教育。
纠正质量问题可以帮助企业提高产品和服务的质量水平,增强客户信任和忠诚度。
第六步:预防质量问题预防质量问题是质量管理的第六步。
预防质量问题是指对可能出现的质量问题进行预测和预防,以避免质量问题的发生。
QC 7 七步法

分 层 法 举 例
问题解决七步法 —— 4、研讨对策
用头脑风暴法 选择目前可实施的方案 制定行动计划
运用创造性思维
对策表
序 号 1 主要 原因 现状 目标 对策 负责 人 完成 日 。 人员 工序不良中,插 从事插头 未培 头焊接不良占不 焊接的作 训 良总数的32%, 业员全部 而且工序返工率 培训合格, 高.在可户不良 确保产品 质量 返品中,插头焊 接不良占不良总 数的46% 培训 。。。 合格、 颁发证 书 人员技 能档案 佩带资 格认定 牌
问题解决七步法 —— 3、要因分析
5W提问
用层别法对问题作更深
一层的区分 用散布图分析试验结果 成对比较法
分层法
分层法根据数据的特征(何人?何处?何 种方法?何种设备?)而将数据化成若干 组的方法——分门别类 目的是能更确切的反映问题 按操作者或作业方法分 按机器设备分 按原料分 按时间分 按操作环境分
七种工具:
分层法 调查表法 因果图法 排列图法 控制图法 直方图法 散布图法(相关图法)
某产品重量实测值分布调查表
调查人: 调查数: 频数
30 25 T 一 正 下 正 正 正 止 正 正 正 正 一 正 正 正 正 正 正 正 正 正 正 正 止 下
调查日期:
20
15
10
5 正 5
15
25
40
50
60
不合格位置调查表
车型 工序 检查目的 喷漆缺陷 检查部位 检查人 检查件数 车身 年月日 380
第一 季度 21 第二 季度 28 第三 季度 90 90 80 70 60 50 40
质量管理七步法
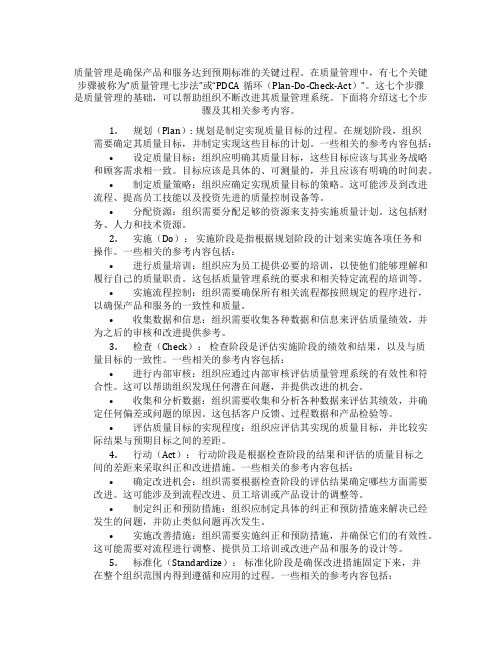
质量管理是确保产品和服务达到预期标准的关键过程。
在质量管理中,有七个关键步骤被称为“质量管理七步法”或“PDCA循环(Plan-Do-Check-Act)”。
这七个步骤是质量管理的基础,可以帮助组织不断改进其质量管理系统。
下面将介绍这七个步骤及其相关参考内容。
1.规划(Plan): 规划是制定实现质量目标的过程。
在规划阶段,组织需要确定其质量目标,并制定实现这些目标的计划。
一些相关的参考内容包括:•设定质量目标:组织应明确其质量目标,这些目标应该与其业务战略和顾客需求相一致。
目标应该是具体的、可测量的,并且应该有明确的时间表。
•制定质量策略:组织应确定实现质量目标的策略。
这可能涉及到改进流程、提高员工技能以及投资先进的质量控制设备等。
•分配资源:组织需要分配足够的资源来支持实施质量计划。
这包括财务、人力和技术资源。
2.实施(Do):实施阶段是指根据规划阶段的计划来实施各项任务和操作。
一些相关的参考内容包括:•进行质量培训:组织应为员工提供必要的培训,以使他们能够理解和履行自己的质量职责。
这包括质量管理系统的要求和相关特定流程的培训等。
•实施流程控制:组织需要确保所有相关流程都按照规定的程序进行,以确保产品和服务的一致性和质量。
•收集数据和信息:组织需要收集各种数据和信息来评估质量绩效,并为之后的审核和改进提供参考。
3.检查(Check):检查阶段是评估实施阶段的绩效和结果,以及与质量目标的一致性。
一些相关的参考内容包括:•进行内部审核:组织应通过内部审核评估质量管理系统的有效性和符合性。
这可以帮助组织发现任何潜在问题,并提供改进的机会。
•收集和分析数据:组织需要收集和分析各种数据来评估其绩效,并确定任何偏差或问题的原因。
这包括客户反馈、过程数据和产品检验等。
•评估质量目标的实现程度:组织应评估其实现的质量目标,并比较实际结果与预期目标之间的差距。
4.行动(Act):行动阶段是根据检查阶段的结果和评估的质量目标之间的差距来采取纠正和改进措施。
8D和七步工作法

❖ 不是以数据为基础来解决问题,而是根据意 见直接确定解决方案
❖ 仅凭个人来确定问题原因,没有依靠团队力 量
❖ 从第一步直接跳到第六步
❖ 将“操作工已得到培训”或“操作工已按要 求操作”做为消除根本原因的方案
❖ 七步工作法常用的一些质量工具:
❖ 答:柱状图、排列图、流程图、运行图、因 果图、头脑风暴、FMEA、5 Why、DOE、 SPC、防错、检查表、问题分析、决策树/分 析、是/否矩阵图、工作流程分析等等;简而 言之,可以把七步工作法看作是一个工具集, 非常多的质量工作和统计工具都可以在七步 工作法不同的阶段使用。
8D改进工作流程和工作要点简述
通过上述的工作过程回答: 1、问题是什么?(2D);2、问题如何解决?(3D~6D);3、将来该问题如何预防?(7D)
质量改进项目关键阶段控制评审内容
首先要分清楚什么是:
❖ 现象 ❖ 问题 ❖ 原因 ❖ 什么是纠正措施 ❖ 什么是临时措施 ❖ 什么是长期措施
8D方法常用工具:
• D8:表彰团队及个人贡献(小组祝贺) 承认小组的集体努力,对小组工作进 行总结并祝贺 。
• 关键要点:有选择的保留重要文档;浏览小 组工作,将心得形成文件;了解小组对解决 问题的集体力量,及对解决问题作出的贡 献;必要的物质、精神奖励 。
8D与七步工作法
❖ 8D法是美国福特公司解决产品质量问题的一种方法, 曾在供应商中广泛推行,现已成为国际汽车行业 (特别是汽车零部件产家)广泛采用来解决产品质 量问题最好的、有效的方法。
❖ “七步法”是美国康明斯公司解决质量问题、进行 质量改进的常用方法,在康明斯全球范围内通用。
❖ “七步法”与8D管理思路相同,只是福特公司将第 七步分成了独立的两步,康明斯将第一步成立改进 小组与第二步问题描述合并, 二者本质上都是基于 PDCA原理的改进方法。
质量分析工具——七步法培训资料

应用“五个为什么”可以深刻地分析原因,有助于头脑风暴过程的进行。 “五个为什么”问题:停不下来的车 这辆车为什么停不下来? 因为这车的刹车坏了 刹车为什么会坏? 因为刹车液漏了 刹车液为什么会漏? 因为有个密封垫坏了 那个密封垫为什么会坏? 因为那个密封垫的包装不合适 包装为什么不合适? 因为缺乏包装标准和程序 应用FMEA、问题分析法等工具对原因分级。小组成员运用上述工具及“专家 意见”投票选出最重要的原因供验证。 质量工具
通过下述方法将可能原因减至最少:
◦ 进一步用鱼刺图集中对根本原因进行分析,或 ◦ 五个为什么
料 法
结果
测量
人
机
鱼刺图
• 头脑风暴——“获得重要意见的最佳途径就是收集许许多多的意见,并把不好的意见扔掉”。 • 在进行头脑风暴时: – 开始时让大家安静的思考 – 在头脑风暴过程中不对意见进行批评或评价 – 搭便车——建立于已有意见之上 – 意见越多越好 – 不对意见作解释 – 不要试图解决问题 – 鼓励分歧意见而不是统一思想
当原因及解决方法不明时 当问题需要跨部门协调解决时 当问题是反复发生的问题时 当问题花费很大不允许重复发生时 在需要原因和解决方法的证据时
在采取了及时措施或隔离措施后,即:
◦ 核实现有库存合格可以交付 ◦ 访问用户以挑选/返工现有的或急需的物料 ◦ 注意与第三步的关系
三、为何要用七步工作法?
数据
没有确切的事实和数据我们无法解 决问题。没有数据我们只能猜想产 生问题的原因。
第三步
采取临时措施
第五步
进行试验,分析数据, 选择解决方案
第四步
收集数据并设计 试验来确定原因
五、与其他形式解决问题方法的关系
与福特公司8D法相同,只是福特公司将第七步分成了独立的两步
工厂质量问题解决的七个实用步骤

工厂质量问题解决的七个实用步骤工厂的质量问题是一个不容忽视的重要问题,对于企业的形象和利益来说都具有重要的影响。
为了解决工厂的质量问题,以下提出了七个实用步骤,帮助企业有效地解决质量问题。
第一步:建立质量控制体系建立一个完善的质量控制体系是解决工厂质量问题的基础。
这个体系应该包括质量目标的设定、质量标准的确定、质量检测方法的规范化等。
通过建立质量控制体系,工厂能够明确质量责任、规范质量流程,从而提高产品的质量。
第二步:快速反应质量问题在发现质量问题时,工厂应该采取快速反应的措施。
这包括及时停止生产、查找问题根源、拟定解决方案等。
通过快速反应,可以有效地阻止质量问题扩大,减少经济损失。
第三步:追踪质量问题解决工厂质量问题需要持续的努力。
工厂应该建立质量问题追踪机制,对已解决的质量问题进行追踪和评估。
通过追踪,可以发现潜在的问题和薄弱环节,进一步完善质量控制措施。
第四步:加强员工培训员工是质量问题的重要因素。
工厂应该加强员工的培训,提高员工的质量意识和技能水平。
培训内容可以包括产品知识、质量标准、质量检测方法等。
通过培训,员工能够更好地了解质量要求,提高质量工作的效果。
第五步:建立供应商管理制度供应商是工厂质量问题的重要来源之一。
建立供应商管理制度,对供应商进行严格的筛选和评估,确保供应商的质量符合要求。
同时,与供应商建立稳定的合作关系,共同解决质量问题,提高产品的整体质量。
第六步:进行质量管理评估定期进行质量管理评估是解决工厂质量问题的重要手段。
通过评估,可以发现问题存在的根本原因,并制定相应的改进措施。
评估结果还可以作为工厂质量工作的衡量标准,推动质量管理的持续改进。
第七步:优化生产流程优化生产流程是提高产品质量的关键。
工厂应该对生产流程进行分析和优化,找出问题环节并进行改进。
通过优化生产流程,可以提高生产效率和产品质量,减少质量问题的发生。
通过以上的七个实用步骤,工厂能够有效地解决质量问题,提高产品的质量和企业的竞争力。
- 1、下载文档前请自行甄别文档内容的完整性,平台不提供额外的编辑、内容补充、找答案等附加服务。
- 2、"仅部分预览"的文档,不可在线预览部分如存在完整性等问题,可反馈申请退款(可完整预览的文档不适用该条件!)。
- 3、如文档侵犯您的权益,请联系客服反馈,我们会尽快为您处理(人工客服工作时间:9:00-18:30)。
5
实施解决方案 Implement Solutions
6
标准化解决方案 Standardize Solutions
7
下一步 Determine Next Steps
产出/Output: ▪ 采取临时性的防范措施 Apply Emergency
Containment Action(ECA)
▪ 建立问题解决团队 Establish a team ▪ 陈述问题 Develop a Problem Statement ▪ 量化问题影响结果,排列解决优先级 Quantify
▪ 防止问题影响到当前产品和客户,或防止影响到下游生产线
▪ 临时性的
▪ 非必须的 ▪ 需要将客户的抱怨值先在一定的程度下降
步骤一: 界定问题 DEFINE PROBLEM`
▪ 例如:FS500主电机与检测同步带在运行过程 中断了,
步骤三: 分析原因制 定假设IDENTIFY CAUSES
临时措施:更换相同规格的同步皮带
问题发生/Problem Occurrence
问题表现和症状 /Symptom
问题陈述 Problem Statement
可能的原因/ Most Probable
Cause(s)
根本原因/Root Cause
“是什么地方出了什么情况?” ‘What is wrong with what?’
问题陈述:
步骤七: 下一 步工作NEXT STEPS
目的/Purpose:
▪ 界定问题范围,区分问题重要程度Identify the problem and the importance of working on it.
3
分析原因 Identify Causes
4
制定解决方案 Develop Solutions
步骤五: 实施解决方 案IMPLEMENT SOLUTIONS
步骤二 : 现状描述CURRENT SITUATION
步骤四 : 制定解决方案DEVELOP SOLUTIONS
步骤六: STANDARDIZE SOLUTIONS
步骤七: 下一步 工作NEXT STEPS
关于ECA的重点
➢ 例子:对受影响的批次进行Screen或Test(抽样或100%)、目检等,同时对厂内或在制进行检查 ➢ 实施临时性应对措施必须经过关键stakeholder的一致认可,通常会涉及的关键职能有生产、工艺、质量
▪ 考虑需要解决的问题,该团队是由来自不同职能部门的人组成,甚至包含工厂以外的人(例如 外部的材料或设备供应商)
▪ 为确保效率,往往3-5个人为最佳
▪ 必须选定一个团队Leader,负责获取资源(时间与人力)、协调和跟踪任务、向高层或客户汇 报进度
▪ 基于需解决的问题,给团队成员提供必要的培训(方法、技术、工具等)
步骤一: 界定问题 DEFINE PROBLEM`
步骤三: 分析原因 制定假设 IDENTIFY CAUSES
步骤五: 实施解决 方案IMPLEMENT SOLUTIONS
,以及被影响的业务部(Business Unit)。由于问题不同,涉及到的关键职能可能和上述列举的不同
➢ 临时性应对措施(ECA)最终将被短期的应对措施(SCA, Short-term Containment Action)取代
Copyright © 2012 Accenture All rights reserved.
Copyright © 2012 Accenture All rights reserved.
2
Technical Structured Problem Solving ——结构化的问题解决流程
面对纷繁复杂的问题,我们遵循以下步骤进行分析,利用结构化的思路,从问题表象挖掘根本原 因,“由现象看本质”,并采取差异性的对策
10
如果面对的是一个多原因造成的复杂问题…… If It’s a Multiple Problem…
步骤一: 界定问题 DEFINE PROBLEM`
步骤三: 分析原因 制定假设 IDENTIFY CAUSES
步骤五: 实施解决 方案IMPLEMENT SOLUTIONS
步骤二 : 现状描述CURRENT SITUATION
▪ 量化分析问题影响,将有助于加快问题前期分析
Copyright © 2012 Accenture All rights reserved.
9
怎么做出好的问题陈述?
步骤一: 界定问题 DEFINE PROBLEM`
步骤三: 分析原因 制定假设 IDENTIFY CAUSES
步骤五: 实施解决 方案IMPLEMENT SOLUTIONS
▪ 问题解决小组的组长通常:质量代表做为组长,协调总体解决小组实施问题解决;流程定义: 重大级由质量总监担任,普通级由质量工程师担任 (确定小组成员的职责及内容)
Copyright © 2012 Accenture All rights reserved.
8
结构化的问题解决流程——陈述问题
步骤一: 界定问题 DEFINE PROBLEM`
7
组建团队 Forming the Working Team
步骤一: 界定问题 DEFINE PROBLEM`
步骤三: 分析原因 制定假设 IDENTIFY CAUSES
步骤五: 实施解决 方案IMPLEMENT SOLUTIONS
步骤二 : 现状描述CURRENT SITUATION
步骤四 : 制定解决方案DEVELOP SOLUTIONS
Title: Product:
Date Opened: Technical Process:
Last Updated:
Team Leader: Team Members: Problem Statement: 步骤一: 界定问题
问题主要表现:
Organization:
Customers:
步骤二 : 现状描述CURRENT SITUATION 问题描述:
Technical Structured Problem Solving 结构化问题解决的思路——七步法
‘Something Changed’ Problem
在生产运营当中,我们经常遇到的问题就是:产线状态发生了变化。
Performance
预期水平
生 产 线 绩 效
突然降低
逐渐降低
实际水平
Time 时间
1
界定问题 Define Problem
2
描述现状 Document Current Situation
3
分析原因 Identify Causes
4
制定解决方案 Develop Solutions
5
实施解决方案 Implement Solutions
▪结构化的问题解决思路被概括 为这七步,对于任何一个问题, 我们都可以采取这种思路进行思 考和分析
步骤六: STANDARDIZE SOLUTIONS
步骤七: 下一 步工作NEXT STEPS
▪ 问题负责人和生产经理共同确定人员,组成该问题的解决团队。人员需具备足够的技能、知识 和时间,并需具备相应的职能权限(例如决策、协调等)。往往涉及的人员有:研发人员(软 件,算法)、工程人员、生产人员、质量人员、采购人员等nnel, etc..)
步骤二 : 现状描述CURRENT SITUATION
步骤四 : 制定解决方案DEVELOP SOLUTIONS
步骤六: STANDARDIZE SOLUTIONS
步骤七: 下一 步工作NEXT STEPS
重复问团队和自己:“为什么?”,用这个方法缩小范围,使问题逐渐变得更清晰
A Small Test 小测验
▪是一种分析思路,是一种方法
6
标准化解决方案 Standardize Solutions
7
下一步 Determine Next Steps
Copyright © 2012 Accenture All rights reserved.
4
Technical Structured Problem Solving TOOL 结构化问题解决的关键工具介绍——TSPS Re,生产线的failure(失效)、生产效率浪费、 换型时间过长等),包括客户希望值是什么?
▪好的问题陈述应该是:
− 清晰、简明,通俗易懂
− 避免模糊而泛泛或太过详细,使团队能够关注特定范围的问题,帮助缩小寻找root cause(根本原因) 的范围
− 避免过早下结论(JUMP TO CONCLUSIONS)。用以验证的事实和实际观察来描述,不要提及可能的 解决方法,更不要定义这是什么原因造成“主观行为”
步骤四 : 制定解决方案DEVELOP SOLUTIONS
步骤六: STANDARDIZE SOLUTIONS
步骤七: 下一 步工作NEXT STEPS
我们经常面对的问题是复杂的、多种原因共同造成的结果,因此必须分解一个复杂的问题成多个 单独的问题,一次解决一个问题,逐步完成
基本原则
▪ 分析数据,观察现场,了解问题,确认是否是多方面原因造成的(例如,当设备故障增加,停机协助 增多,分析是否有多方面原因,包括设备、模具、人为操作、物料等)
问题发生/Problem Occurrence
预防 /Prevent
问题表现和症状 /Symptom
可能的原因/ Most Probable
Cause(s)
根本原因/Root Cause
解决/Fix
Copyright © 2012 Accenture All rights reserved.
3
Technical Structured Problem Solving 结构化问题解决的思路——七步法