催化裂化生产中常见问题
催化裂化装置结焦原因分析及对策研究

催化裂化装置结焦原因分析及对策研究催化裂化装置在长期运行过程中,由于操作条件、催化剂质量、原料质量等因素的影响,很容易出现结焦现象,严重影响装置运行稳定性和经济效益。
本文从结焦原因和处理方案两个方面进行分析研究。
一、结焦原因分析1. 催化剂质量不佳催化剂质量不佳往往会导致催化剂中的焦炭生成速度变快,一旦催化剂中焦炭过多,就会对催化剂活性和选择性进行破坏,进而导致催化剂失活。
而失活的催化剂不仅容易出现结焦现象,更会对生产造成较大的经济损失。
2. 操作条件不当操作条件不当也是造成催化裂化装置结焦的主要原因之一。
比如炉温过高、压力过低、流量过大等,都容易导致原料在装置内过热、过量分解,从而增加结焦风险。
3. 原料质量不稳定催化裂化装置原料质量的稳定性很重要。
如果原料中存在杂质、异物等不良物质,就容易引起催化剂中焦炭的快速生成,导致结焦现象的出现。
同时,原料成分的波动也容易影响催化剂的活性,从而增加催化剂失效的风险。
二、对策研究1. 改进催化剂质量针对催化剂质量不佳的问题,应优化催化剂生产的技术、提高催化剂活性等手段,尽可能延长催化剂寿命,减少催化剂中焦炭的生成,从根本上防止结焦现象的出现。
2. 优化操作条件优化操作条件是解决结焦问题的重要途径。
比如合理控制装置温度、压力、流量等参数,减小原料在装置内的分解程度,减少催化剂中焦炭的生成率,有效地增加装置运行的稳定性。
结语催化裂化装置结焦问题是长期以来困扰生产工艺的难点之一,笔者在此分析了造成结焦的原因,并提出了相应的防治策略。
不过,避免催化裂化装置结焦问题的出现,仅仅通过以上几种手段还是不够的,需要生产人员和技术人员综合发力,从各个方面对催化裂化装置进行管理和运行,以确保装置平稳运行,为生产水平的提高提供有力支持。
催化裂化装置烟气脱硫系统结垢原因分析及应对措施

催化裂扮装置烟气脱硫系统结垢原因分析及应对措施引言在石油化工生产过程中,催化裂扮装置广泛应用于石化行业中,它能够将重油转化为轻油和石油气,满足日益增长的能源需求。
然而,催化裂扮装置烟气脱硫系统在运行过程中会产生结垢问题,严峻影响设备的正常运行和脱硫效果。
本文将对催化裂扮装置烟气脱硫系统结垢问题的原因进行分析,并提出相应的应对措施。
一、催化裂扮装置烟气脱硫系统结垢原因分析1. 硫酸铵结垢烟气脱硫系统中使用的吸纳液中常含有硫酸铵,随着脱硫液循环使用,硫酸铵溶液中的硫酸铵会被氧化生成硫酸,而硫酸在高温环境中溶解度较低,容易结晶沉积在设备内壁上。
2. 碳酸钙结垢烟气脱硫液中常含有一定量的钙离子,烟气中的二氧化碳与钙离子反应生成碳酸钙,而碳酸钙在高温条件下结晶沉积,导致结垢问题。
3. 硫酸钙结垢烟气脱硫液中的硫酸钙浓度过高,超过了饱和度,或者温度提高时,硫酸钙会从溶液中析出结晶,生成结垢。
二、催化裂扮装置烟气脱硫系统结垢应对措施1. 控制吸纳液质量提高吸纳液性能,控制吸纳液中硫酸铵的浓度,缩减硫酸铵被氧化的速度。
增加吸纳液的循环次数,降低硫酸铵的浓度,缩减结垢的可能性。
2. 控制钙离子含量通过分析烟气成分,合理控制脱硫液中的钙离子含量,缩减碳酸钙的生成,降低烟气脱硫系统的结垢风险。
可以实行预处理方法,如提前剔除烟气中的二氧化碳等方法。
3. 降低硫酸钙浓度通过加强脱硫液的循环,增加氧化还原剂的投加量等方式,降低硫酸钙浓度,控制其不超过饱和度,缩减硫酸钙的析出。
4. 定期清洗结垢定期对烟气脱硫设备进行清洗,去除结垢,保证设备的通畅。
可以接受化学清洗或机械清洗等方式,依据结垢的状况选择合适的清洗剂和清洗方法。
5. 加强监测与维护加强对催化裂扮装置烟气脱硫系统的监测与维护,定期检查设备是否存在结垢状况,准时实行措施进行处理,防止结垢问题进一步恶化。
结论催化裂扮装置烟气脱硫系统结垢问题的产生主要与硫酸铵、碳酸钙、硫酸钙的析出有关。
催化裂化非正常操作及事故处理

催化裂化非正常操作及事故处理㈠流量不足,输出压力不够的原因及处理:1.入口管线,过滤网,叶轮堵塞凝结,切换泵,清扫检修.2.入口阀未开或开度过小,阀板掉等,切换泵,并配合切换流程处理.3.入口管线及泵体内有气体,泵出口放空阀排气.4.泵体及入口管线有漏气处.5.叶轮损坏或装反,切换检修.6.电机反转,切换泵,联系电工处理.7.吸入高度不够,提高液面或入口升压.8.油品温度低,粘度大,提高温度,降低粘度.9.口环磨损或内壳体各部间隙大,切换泵检修.㈡泵抽空不上量的原因及处理1.塔底,罐底液面过低或抽空,联系有关岗位处理液面,关泵出口阀憋压.2.切换流程时冷油进入泵体,联系有关岗位处理流程,关出口阀憋压.3.扫线蒸汽不严,蒸汽串入泵体,联系有关岗位检查各吹扫蒸汽阀是否关严.4.泵予热不当,排尽泵体水,汽及冷油,缓慢予热.5.油品中含水量大,过热汽化,联系有关岗位处理脱水.6.油品中轻油组分含量高,入泵后产生气阻,联系有关岗位调整工艺条件,检查工艺流程.7.塔201底油浆温度过低,联系分馏岗位,提高塔底温度.8.汽油,柴油,液态烃温度高,泵体喷淋水降温,联系有关岗位降温.9.汽油泵,液态烃泵入口压力下降,联系提高入口压力,憋压.10.泵内抽进杂物或入口堵塞,切换泵检修.11.端面密封安装不好,或动环静环磨损,向泵内串水,切换泵检修.12.打封量不合格,量大,适当降低封油量.13.泵入口阀开度小,泵壳压力太小,开大泵入口阀.14.泵入口管线,设备阀门漏,联系配合有关岗位处理,切换泵等.15.机泵故障,切换泵检修.㈢电机超负荷,发热爱有原因及处理1.循环量过大,泵出入口管连通阀和备用泵出口阀开度大,关小连通阀和备用泵出口阀.2.油品粘度过大,联系调节油温.3.机泵打水时,流量过大,适当关小出口阀,降流量.4.电机反转,切换泵,联系电工调整电路.5.叶轮中有杂物,切换泵,抢修,清洗杂物.6.电机与泵轴不同心,切换泵,重新找正.7.转子磨擦,口环磨损,切换泵抢修.8.轴承损坏切换泵,抢修.9.盘根压得过紧,机油无法润滑,适当松动盘根压盖.10.电压过大,过小,联系电工查找原因.11.电机故障,如电机受潮,定子绝缘不不良,三相电路断相,切换泵联系电工处理.㈣轴承发热的原因与处理1.泵轴与机轴线不对或震动,切换泵,重新找正.2.润滑脂,润滑油量少,注意油或切换泵,清洗轴承,润滑脂压温盒.3.润滑脂变质,润滑油乳化,含杂质等,切换泵,换油脂,清洗轴承.4.冷却水中断或不足,调节冷却水量.5.油环脱落,油环运行不正常,切换泵调整.6.电机负荷过大,电机发热,查找原因处理.㈤轴封泄漏过多的原因与处理1.泵抽空,使弹簧不能压紧,端面密封泄漏,切换泵.2.端面密封中有催化剂,使动环,静环磨损,联系降低油浆固含量,切换泵检修.3.预热不当,重油粘在弹簧上,伸缩受影响,使端面密封泄漏,预热好后,才能启动泵,可联系钳工处理,必要时切换泵处理.4.端面密封材料不合格,装配质量不好,切换泵处理.5.转子不平衡,震动剧烈,切换泵检修.6.中心线偏斜,切换泵找正.7.轴或轴套磨损,切换泵检修.8.轴弯曲,切换泵检修.9.盘根箱填料磨损,停泵,更换填料.10.盘根箱填料函盖不正,调整或切换泵检修.11.冷却,润滑不好,调整冷却水量和封油量.12.轴或轴套与盘根底套间隙过大,致使盘根被挤进泵内,切换泵检修.㈥机泵抱轴的原因与处理1.轴承缺油,造成温度高.2.轴承箱缺冷却水,造成温度高.3.轴承损坏,摩擦发热,温度高. 处理方法:切换泵抢修. ㈦泵振动或有噪音的原因与处理1.泵抽空,不上量,联系调整,必要时切换.2.地脚螺栓松动,紧固.3.泵实际流量远远小于设计流量,调大流量.4.叶轮中有异物或叶轮松动,切换泵,检修.5.泵与电机同心度有偏差,切换泵检修.6.轴承磨损后间隙增大或串轴,抱轴,切换泵检修.7.泵体或来液管内有气体,排除气体.8.吸入压力与耗油蒸汽压力相近,提高来油压力.9.轴弯曲或转子不平衡,切换泵检修.10.转子与定子产生摩擦,切换泵检修.11.泵体过热,查找原因处理.㈧电机起动不起来的原因与处理1.电压过低,联系电工查找原因.2.电路不通或接触不良,联系电工处理.3.电机负荷过大,查找原因处理.4.泵体内有异物卡住或安装不当,联系钳工处理.5.开关失灵,按钮不好用,熔断器的熔件烧断,联系电工处理.。
催化裂化装置结焦原因分析及对策研究

催化裂化装置结焦原因分析及对策研究
催化裂化装置结焦是指在催化裂化过程中,由于反应过程中产生的碳积累在催化剂表面,导致催化剂活性降低,反应效率下降,甚至催化剂失活的现象。
结焦问题严重影响了
催化裂化装置的生产效率和经济效益。
本文将分析催化裂化装置结焦的原因,并提出相应
的对策。
催化裂化装置结焦的原因主要包括以下几个方面:
1. 高温:催化裂化反应需要在较高温度条件下进行,高温会加速碳积聚的过程,导
致催化剂结焦。
2. 高碳含量的原料:催化裂化装置处理高碳含量的原料,会使得产生的碳积聚更多,导致催化剂结焦。
3. 高流速:高流速会引起催化剂表面的碳积聚过程加剧,进而促使催化剂的结焦。
4. 催化剂质量:催化剂材料的选择和质量会影响结焦问题,较差质量的催化剂容易
结焦。
5. 动力不足:催化裂化反应需要消耗大量的热力,如果动力系统供应不足,反应温
度无法保持在适宜的范围内,会导致结焦现象。
针对以上的原因,我们可以采取如下对策来应对催化裂化装置结焦问题:
1. 优化温度控制:通过合理控制反应温度,使其在适宜的范围内,既不过高也不过低,可以减少碳积聚的速度,降低催化剂结焦的风险。
3. 调整流速:合理调整反应器的流速,减缓碳积聚的速度,降低催化剂结焦的风
险。
4. 优化催化剂质量:选择高质量的催化剂材料,并严格控制催化剂制备的过程,以
提高催化剂的抗结焦能力。
催化裂化装置结焦问题是一个复杂的工艺问题,需要从温度控制、原料选择、流速调整、催化剂质量和动力供应等多个方面综合考虑,通过优化工艺参数和采取相应的对策,
才能有效降低结焦的风险,提高催化裂化装置的生产效率和经济效益。
催化裂化装置关键设备故障分析及对策

催化裂化装置关键设备故障分析及对策天津 300270摘要:催化裂化装置是石油加工工艺中的重要环节之一,同时也是炼油厂中最需要注重安全的场所之一。
在催化裂化装置运行过程中,可能会出现一些故障,这不仅会影响设备的性能和生产质量,还可能会对人员的生命财产造成威胁。
因此,下文将对催化裂化装置的关键设备故障进行详细的介绍和分析,以期提高我们对催化裂化装置的故障了解和维护能力。
关键词:催化裂化装置;关键设备;故障分析;对策;引言:催化裂化装置在石油加工工艺中占据着重要的地位,是炼油厂的关键设备之一。
然而,在其长期运行的过程中,可能会出现各种各样的故障,如催化剂失活、热点堵塞、噪声故障、泄漏故障等,这些故障都会对设备的性能和生产质量产生严重影响,甚至危及人员生命财产安全。
针对这些可能出现的故障,我们需要深入探究其原因和对策,及时制定应对方案。
例如,对于催化剂失活故障,需要重视对催化剂的清洗及维护;对于热点堵塞故障,需要定期对反应器进行清洗,保证设备的正常运行;对于噪声故障,需要加强设备的维护保养和调整;对于泄漏故障,需要进行紧急处理和加强安全防范措施等等。
在日益严格的环保和安全要求下,催化裂化装置的关键设备故障处理显得愈发重要,需要我们对其进行深入探究和分析,从而找到有效的对策方案,保障设备的正常运行,提高生产效率和产品质量。
本文将对催化裂化装置关键设备故障进行详细论述和分析,并提出一系列的对策希望能为行业发展做出一点贡献。
一、催化裂化装置简介催化裂化装置是一种高度技术化的炼油装置,用于将石油或石油产品中的高分子化合物裂解成较小的分子。
它采用一系列反应器、加热器、冷却器、催化剂等设备,通过改变化学反应条件,实现高分子化合物分解与分解产物再结合的反应过程。
在催化裂化装置中,原料石油或石油产品经过预热后,进入到第一反应器中,在高温(600℃-700℃)、低压(0.2-0.3MPa)的反应条件下,遇到催化剂开始反应。
重油催化裂化结焦原因及改进措施

重油催化裂化结焦原因及改进措施重油催化裂化是润滑油加工工艺的一个重要环节,是提高润滑油的质量的关键技术。
在重油催化裂化过程中,结焦是一个常见的问题,会严重降低催化裂化的效率。
重油催化裂化结焦的原因,主要有三个方面:首先,催化剂受污染。
催化剂通常是复合物,容易受到空气、产品成分和其他物质的侵蚀、混入或碳化,受到污染时,催化剂性能会受到严重影响,从而导致结焦。
其次,催化剂不可逆变化。
重油催化裂化温度高,使重油催化剂发生不可逆变化,催化剂的性能也下降,从而导致结焦等问题。
最后,温度控制不当。
重油催化裂化的温度控制是很重要的,太高或太低的温度都会影响催化剂的功能,导致结焦。
为了解决重油催化裂化结焦问题,应采取一些有效的措施。
首先,科学选用催化剂。
重油催化裂化中使用的催化剂一般是催化剂复合物,应根据实际需要科学选择恰当的催化剂,降低催化剂受污染的可能性。
其次,采用稳定性好的催化剂。
重油催化裂化时,要选择温度稳定性较好的催化剂,不变性的催化剂能有效降低结焦的可能性。
再次,做好温度控制。
重油催化裂化时,温度应稳定在一定范围内,太高或太低的温度都会影响催化剂的功能,因此应做好温度控制,以保证重油催化裂化效果。
最后,改善反应条件和催化裂化技术。
采用新型催化剂和剂的组合,改善反应条件,控制反应温度和反应压力,改进催化裂化技术,进一步提高重油催化裂化的效率。
综上所述,重油催化裂化结焦的主要原因是催化剂受污染、催化剂不可逆变化以及温度控制不当。
要改善这种情况,应采取有效的措施,如科学选用催化剂、采用稳定性好的催化剂、做好温度控制、改善反应条件和催化裂化技术等。
只有真正落实这些措施,才能有效防止重油催化裂化结焦,达到质量理想。
催化裂化装置结焦原因分析及对策研究

催化裂化装置结焦原因分析及对策研究催化裂化装置是炼油厂的关键设备之一,其作用是将重质石油馏分分解成轻质产品,包括汽油、柴油和液化石油气等。
由于操作不当或设备故障等原因,催化裂化装置很容易出现结焦现象,严重影响生产效率和产品质量。
对催化裂化装置结焦原因进行分析,并制定相应的对策,对于炼油厂的稳定运行和产品质量具有重要意义。
1. 温度控制不当催化裂化装置工作温度的控制是避免结焦的关键因素之一。
如果温度过高,容易导致催化剂在装置中的积炭过多,从而引发结焦现象。
温度过低也会使催化剂在反应过程中不能充分活化,同样容易导致结焦。
保持合适的工作温度是避免结焦的重要手段。
2. 催化剂质量不良催化裂化装置中使用的催化剂质量的好坏直接影响装置的运行情况。
如果催化剂中存在杂质或者受到空气污染,会导致催化剂的活性降低,从而影响反应的进行,最终导致结焦。
3. 操作人员不当操作催化裂化装置是复杂的设备,需要操作人员具备一定的专业知识和技能。
如果操作人员不当操作,比如在设备运行时不按规定添加催化剂,或者不及时清理催化剂床中的积炭,都会加重结焦的程度。
4. 设备故障设备故障是导致催化裂化装置结焦的另一重要原因。
比如设备堵塞、管道泄漏等故障,都会导致催化剂无法正常流动或者反应不能顺利进行,最终导致结焦。
二、催化裂化装置结焦对策研究为了避免催化裂化装置结焦,首先需要严格控制工作温度。
可以通过安装温度传感器和控制系统,不断监测和调节催化裂化装置的工作温度,保证其在安全范围内稳定运行。
选择高质量的催化剂是避免催化裂化装置结焦的重要措施。
可以通过提高催化剂的制备工艺、严格控制原料质量和加强催化剂检测等手段,提高催化剂的活性和稳定性。
催化裂化装置的操作人员需要接受系统的培训,掌握装置的结构与工作原理,熟悉操作规程,了解可能影响反应的因素,提高操作技能,以减少因操作不当而导致的结焦情况。
4. 定期检查与维护为了预防催化裂化装置结焦,需要定期检查设备的运行情况,发现问题及时处理。
催化裂化装置结焦原因分析及对策研究
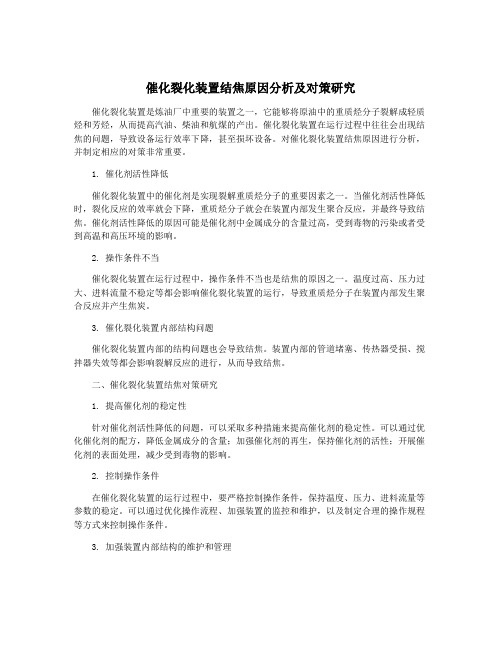
催化裂化装置结焦原因分析及对策研究催化裂化装置是炼油厂中重要的装置之一,它能够将原油中的重质烃分子裂解成轻质烃和芳烃,从而提高汽油、柴油和航煤的产出。
催化裂化装置在运行过程中往往会出现结焦的问题,导致设备运行效率下降,甚至损坏设备。
对催化裂化装置结焦原因进行分析,并制定相应的对策非常重要。
1. 催化剂活性降低催化裂化装置中的催化剂是实现裂解重质烃分子的重要因素之一。
当催化剂活性降低时,裂化反应的效率就会下降,重质烃分子就会在装置内部发生聚合反应,并最终导致结焦。
催化剂活性降低的原因可能是催化剂中金属成分的含量过高,受到毒物的污染或者受到高温和高压环境的影响。
2. 操作条件不当催化裂化装置在运行过程中,操作条件不当也是结焦的原因之一。
温度过高、压力过大、进料流量不稳定等都会影响催化裂化装置的运行,导致重质烃分子在装置内部发生聚合反应并产生焦炭。
3. 催化裂化装置内部结构问题催化裂化装置内部的结构问题也会导致结焦。
装置内部的管道堵塞、传热器受损、搅拌器失效等都会影响裂解反应的进行,从而导致结焦。
二、催化裂化装置结焦对策研究1. 提高催化剂的稳定性针对催化剂活性降低的问题,可以采取多种措施来提高催化剂的稳定性。
可以通过优化催化剂的配方,降低金属成分的含量;加强催化剂的再生,保持催化剂的活性;开展催化剂的表面处理,减少受到毒物的影响。
2. 控制操作条件在催化裂化装置的运行过程中,要严格控制操作条件,保持温度、压力、进料流量等参数的稳定。
可以通过优化操作流程、加强装置的监控和维护,以及制定合理的操作规程等方式来控制操作条件。
3. 加强装置内部结构的维护和管理为了避免装置内部结构问题导致结焦,需要加强装置的维护和管理。
定期清理管道和传热器、加强设备的检修和保养、进行装置内部结构的改进等,都可以有效减少结焦问题的发生。
催化裂化装置结焦是炼油生产中常见的问题,但通过对结焦原因的分析,并采取相应的对策,可以有效降低结焦的发生,保障装置的安全运行和生产效率。
- 1、下载文档前请自行甄别文档内容的完整性,平台不提供额外的编辑、内容补充、找答案等附加服务。
- 2、"仅部分预览"的文档,不可在线预览部分如存在完整性等问题,可反馈申请退款(可完整预览的文档不适用该条件!)。
- 3、如文档侵犯您的权益,请联系客服反馈,我们会尽快为您处理(人工客服工作时间:9:00-18:30)。
2021/4/11
25
催化裂化的尾燃现象
2021/4/11
26
再生器尾燃原因分析
2021/4/11
27
再生器尾燃原因分析
2021/4/11
28
再生器尾燃原因分析
2021/4/11
29
再生器尾燃原因分析
2、含有亚硫酸盐的液体送到氧化池,用 空气氧化,以减少COD。
2021/4/11
77
低温氧化脱NOx技术(LoTOx)
2021/4/11
78
低温氧化脱NOx技术(LoTOx)
在烟气中注入O3以氧化不溶于水的低价态 的氮氧化物转化成溶于水的高价态的氮氧 化物,从而通过湿洗法将氮氧化物从烟气 中除去。
烟气中 有害物
质
SO2 NOx 粉尘
2021/4/11
标准规定值 排放筒高 排放量
浓度
m
kg/h mg/m3
100
200
700
100
61
420
100
278
150
71
EDV湿法脱硫和除粉尘技术
一般原则: ➢FCC原料中硫含量<0.25%--硫转移剂 ➢FCC原料中硫含量>0.50%--烟气洗涤技术 ➢FCC原料中硫含量0.25~0.50%--评估选择
接……
2021/4/11
21
避免结焦的措施(3)
足够的防焦蒸汽,不留死区、死角 开工喷油温度要够, > 530 ℃
最好用蜡油开工,逐步置换 提出口温度不宜过低, > 480 ℃ 提高衬里水平,无热点,避免露点冷凝 提高检修水平,清焦彻底
2021/4/11
22
避免结焦的措施(4)
大油气管线线速35~45m/s 分馏塔底 <350 ℃ 油浆密度<1.1g/cm3 油浆线速 >1.5m/s 用好油浆阻垢剂
74
EDV技术特点
3、该液体含有催化剂粉尘、NaHSO3, Na2SO3和Na2SO4 4、部分饱和液被排除,送到PTU处理装 置进行处理
2021/4/11
75
PURGE TREATMENT UNIT FLOWSHEET
2021/4/11
76
PTU技术特点
1、来自EDV的废液,进入澄清池,除去粉 尘。
38
分馏塔结盐--原因(2)
通常分离塔顶条件下,水的露点在 90℃以上,而顶回流返塔温度较低 ~80℃ ,形成局部析水,溶盐
NH4Cl溶于水,并随水向下流动 随温度升高,脱水,析盐,堵塞降液
管和塔盘
39
分馏塔结盐—处理(水洗)
40
分馏塔结盐—处理(水洗)
进料量以维持操作为准,分馏塔底液面由油浆 外甩量控制
RxCAT技术
提升管
再生立管
15.6
7.8
722
0.35
+3.8 +4.9 5.46
0.70
2021/4/11
45
UOP的RefCAT技术示意图
技术特点: 1、两个反应器独立 2、公用一个再生器 3、汽油回炼 4、降烯烃,降硫、高液收
2021/4/11
46
UOP的RefCAT技术特点
2021/4/11
40~80
>80
含量 (%)
16.4
54.7
9.0
19.9
2021/4/11
19
避免结焦的措施(1)
采用高效雾化喷嘴, KH, LPC, BWJ……
小喷嘴,对称安装 足够的雾化蒸汽量,>5% 适度的预热温度,<5mm2/s,预热温度>200℃
粘度,mm2/s
50 45 44 40 35 30 25 20 15 10
2021/4/11
30
再生器尾燃原因分析
2021/4/11
31
再生器尾燃原因分析
2021/4/11
32
再生器改造前后的效果示意
2021/4/11
33
改造前后的再生稀密相温差
2021/4/11
34
关注—加剂(活性和温度)引起的周期性尾燃
2注021:/4/若11稀相催化剂密度为15kg/m3,则其热容约为烟气的12倍
35
分馏塔结盐分析
分馏塔结盐--现象
分馏塔压降增加,增值达 20~40kpa
柴油抽不出来,冲塔 塔顶温度难以控制,无法正常操作 产品不合格
37
分馏塔结盐—原因(1)
原料中有 Cl,N化物的存在 Cl 的盐水解生成HCl N化物在FCC条件下生成NH3 NH3和HCl在低温部位生成NH4Cl
催化裂化生产中常见问题
内容
➢ 减少生焦和避免结焦 ➢ 催化裂化的尾燃现象 ➢ 分馏塔结盐现象 ➢ 催化裂化的其它技术 ➢ 催化裂化的清洁生产技术 ➢ 未来的发展方向
2021/4/11
2
生焦的利与弊
➢ 为反应提供热量 ➢ 为系统提供蒸汽 ➢ 增加能耗 ➢ 增加投资 ➢ 结焦的前提
2021/4/11
67
不同区域的产物差异
2021/4/11
68
催化裂化的清洁生产技术
2021/4/11
69
美国催化烟气排放限制
项目 SOx,μg/g NOx,μg/g CO,μg/g 颗粒物,g/kg
2021/4/11
美国 25 20 1.0(0.5) 500(150)
备注
70
中国烟气排放标准(GB16297-1996)
2021/4/11
72
湿法处理再生烟气示意图
2021/4/11
73
EDV技术特点
1、含有催化剂粉尘和SO2的烟气进入喷淋 净化塔,喷淋水由循环泵分多层喷入喷淋 塔内
2、喷淋水含有碱性试剂,如NaOH等。 在喷淋塔内气液逆流或错流接触,烟气被 多层喷淋后,吸收,冷凝,并趋于饱和吸 收
2021/4/11
47
UOP的MSCC的结构示意图
2021/4/11
48
UOP的MSCC的结构示意图
2021/4/11
49
UOP的MSCC的技术特点
1、剂油垂直接触(剂向下,油水平) 2、高温、高剂油比的高苛刻度 3、短的剂油接触时间 4、强化一次裂化、弱化再裂化 5、好的高价产品选择性
2021/4/11
50
UOP的MSCC示范装置结果
2021/4/11
85
KBR改造设计降NOX的效果
2021/4/11
86
清洁生产的硫转移剂
1 2 3 4 5
2021/4/11
开发公司 INTERCAT DAVISON ENGELHARD
RIPP LPEC
硫转移剂 SUPER-SOX GETTER
SUPPER-DeSOx NO-SOXPC RFS-C LST-1
补水和粗汽油构成冷回流,并控制顶温 90~95℃ ,逐步停顶循,粗汽油改污油罐
顶循温度控制 105~115℃ ,排水至油水分离 罐,防止水下流
若柴油带水,应控制水量 水洗水分析至Cl-稳定为止,一般2~5h
41
分馏塔结盐—水洗水中Cl含量变化
42
催化裂化的其它技术
2021/4/11
43
UOP的RxCAT技术
2021/4/11
57
UOP的LOCC结果对比,W%
TOTAL
2021/4/11
94.2
93.2
58
NexCC的技术特点
1、反应和再生流化床同轴套装起来 2、外面的流化床作为再生器 3、套在里面的是反应器 4、反应温度600~650℃ 5、剂油比是常规FCC的2~3倍 6、剂油接触时间1~2s
2021/4/11
12
结焦发生的位置
2021/4/11
13
结焦发生的位置
2021/4/11
14
汽提段格栅上的大焦块
2021/4/11
15
结焦发生的位置
2021/4/11
16
旋分器锥体外壁结焦
2021/4/11
17
结焦发生的位置
2021/4/11
18
沉降器焦块中催化剂筛分
筛分 数据 (μm)
0~20
20~40
特点: ➢提高转化率 ➢增加汽油产率 ➢降低干气产率 ➢在恒定转化率下,降低焦炭 ➢增加再生时间 ➢降低两器循环量 ➢减少烟气排放
2021/4/11
44
UOP的RxCAT与常规FCC的比较
剂油比 再生温度,C
转化率,lv% 汽油,lv% 焦炭,m% 碳差
常规FCC
8.27 718 Base Base 5.62 0.68
2021/4/11
79
KBR降低NOX排放的再生器设计
2021/4/11
80
降低NOX排放的机理(KBR)
2021/4/11
81
再生器形式对NOX排放的影响
2021/4/11
82
KBR改造设计降NOX的实例1
2021/4/11
83
KBR改造设计降NOX的实例2
2021/4/11
84
KBR超正流改造设计降NOX的效果
2021/4/11
23
避免结焦的措施(5)
油浆在分馏塔底停留时间 <5min 分馏塔底蒸汽搅拌,+滤焦器 合理使用终止剂,减少二次裂化 选择重油裂化能力强的催化剂,
MA>60/64
2021/4/11
24
避免结焦的措施(6)
平衡剂上的钒含量 <0.8% 钙铁含量 <1.5% 控制并平稳原料质量: