甲烷水蒸汽转化
内燃机内甲烷水蒸气重整特性分析

内燃机内甲烷水蒸气重整特性分析高华光;龚希武【摘要】为了较为系统地认识甲烷水蒸气重整反应对内燃机性能的影响。
应用HSC 5.1软件对甲烷水蒸气重整反应在不同反应温度和水碳比的工况下进行分析,然后应用Chemkin‐pro程序,计算了在相同供热量下甲烷水蒸气重整气在不同物质的量比下比C H4的燃C H4消耗降低率。
结果表明,提高反应温度和水碳比可提高C H4的转化率;当温度为700℃、水碳比为3时,发热量提高了13.58%,在供热相同情况下,燃C H4消耗量可减少11.96%,C H4的转化率越高,循环效率越高;重整气效率比纯天然气高,随着物质的量比降低,重整气优势降低。
%To obtain a better view on the effect of steam reforming of methane (SRM ) reaction on performance of internal combustion (IC) engine ,by using HSC 5 .1 software ,SRM was analyzed at different temperature and steam/methane molar ratios .Then ,by using Chemkin‐pro software ,fuel consumption reduced rate of methane was calculated in synthesis gas of SRM and methane at different equivalence ratios .The results show that the increase of temperature and steam/methane molar ratios will increase conversion rate of methane .When the temperature is 700 ℃ andsteam/methane molar ratio is 3 under the same heating conditions ,heat value will increase 13 .58% ,fuel consumption will decrease 11 .96% ,and cycle efficiency of IC engine will increase with the increase of conversion rate of methane .Efficiency of synthesis gas of SRM is higher than pure methane ,unfortunately ,decreases with the decrease of the equivalentratio .【期刊名称】《石油与天然气化工》【年(卷),期】2016(000)001【总页数】6页(P46-51)【关键词】化学回热循环;甲烷水蒸气重整;内燃机;HSC5.1;Chemkin【作者】高华光;龚希武【作者单位】浙江海洋学院船舶与海洋工程学院;浙江海洋学院船舶与海洋工程学院【正文语种】中文【中图分类】TE624化学回热循环燃气轮机(Chemically Recuperated Gas Turbine,CRGT)和液化天然气(Liquefied Natural Gas,LNG)是船舶主动力装置应对能源危机和环境污染的有效手段和替代燃料[1-3]。
甲烷化工艺流程

甲烷化工艺流程
《甲烷化工艺流程》
甲烷化工艺是一种将甲烷转化为更有用化学物质的过程。
甲烷是一种富含碳和氢的简单有机化合物,是天然气的主要成分。
甲烷化工艺可以将甲烷转化为甲烷醇、甲醛、丙烷等更有用的化学品。
甲烷化工艺通常包括以下几个步骤:
1. 蒸汽重整:甲烷和水蒸汽经过反应生成一氧化碳和氢气。
这一步骤是甲烷化工艺的起始阶段,产生的一氧化碳和氢气可作为后续反应的原料。
2. 甲烷蒸氨:甲烷和氨气在催化剂的作用下发生反应,生成甲胺。
甲胺可以用于生产甲胺醛等化学品。
3. 碳氢化合物的加氢:甲烷和氢气通过催化剂反应,生成其他碳氢化合物,如丙烷、丁烷等。
4. 甲基化反应:甲烷和一氧化碳在高温下发生反应,生成甲醇。
这是甲烷化工艺中的重要步骤,因为甲醇是一种重要的工业原料。
以上是甲烷化工艺的基本流程,通过不同的反应组合可以得到各种不同的化学品。
甲烷化工艺在化工领域具有广泛的应用,
不仅可以提高甲烷的利用率,还可以生产出更多有用的化学品,为化工行业的发展做出贡献。
甲烷蒸汽转化的工艺流程说明

甲烷蒸汽转化的工艺流程说明下载温馨提示:该文档是我店铺精心编制而成,希望大家下载以后,能够帮助大家解决实际的问题。
文档下载后可定制随意修改,请根据实际需要进行相应的调整和使用,谢谢!并且,本店铺为大家提供各种各样类型的实用资料,如教育随笔、日记赏析、句子摘抄、古诗大全、经典美文、话题作文、工作总结、词语解析、文案摘录、其他资料等等,如想了解不同资料格式和写法,敬请关注!Download tips: This document is carefully compiled by theeditor.I hope that after you download them,they can help yousolve practical problems. The document can be customized andmodified after downloading,please adjust and use it according toactual needs, thank you!In addition, our shop provides you with various types ofpractical materials,such as educational essays, diaryappreciation,sentence excerpts,ancient poems,classic articles,topic composition,work summary,word parsing,copy excerpts,other materials and so on,want to know different data formats andwriting methods,please pay attention!甲烷蒸汽转化工艺流程详解甲烷蒸汽转化是一种重要的化学反应过程,主要用于将天然气中的主要成分甲烷转化为合成气(氢气和一氧化碳),是化工生产中不可或缺的一环。
级石油化工工艺学布置部分作业答案要点
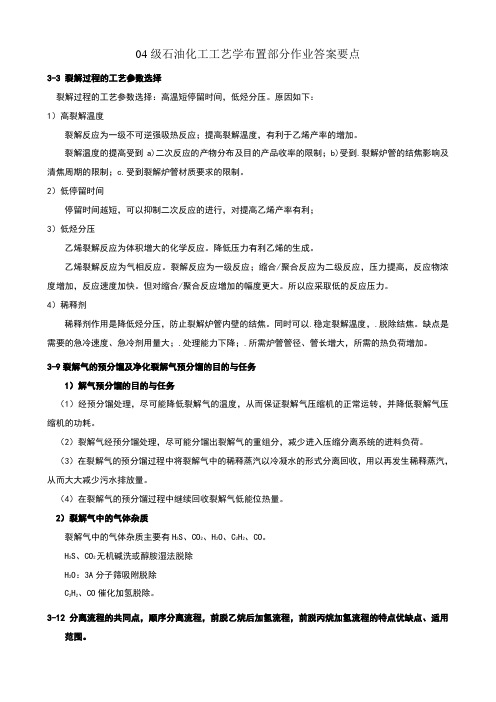
04级石油化工工艺学布置部分作业答案要点3-3 裂解过程的工艺参数选择裂解过程的工艺参数选择:高温短停留时间,低烃分压。
原因如下:1)高裂解温度裂解反应为一级不可逆强吸热反应;提高裂解温度,有利于乙烯产率的增加。
裂解温度的提高受到a)二次反应的产物分布及目的产品收率的限制;b)受到.裂解炉管的结焦影响及清焦周期的限制;c.受到裂解炉管材质要求的限制。
2)低停留时间停留时间越短,可以抑制二次反应的进行,对提高乙烯产率有利;3)低烃分压乙烯裂解反应为体积增大的化学反应。
降低压力有利乙烯的生成。
乙烯裂解反应为气相反应。
裂解反应为一级反应;缩合/聚合反应为二级反应,压力提高,反应物浓度增加,反应速度加快。
但对缩合/聚合反应增加的幅度更大。
所以应采取低的反应压力。
4)稀释剂稀释剂作用是降低烃分压,防止裂解炉管内壁的结焦。
同时可以.稳定裂解温度,.脱除结焦。
缺点是需要的急冷速度、急冷剂用量大;.处理能力下降;.所需炉管管径、管长增大,所需的热负荷增加。
3-9裂解气的预分馏及净化裂解气预分馏的目的与任务1)解气预分馏的目的与任务(1)经预分馏处理,尽可能降低裂解气的温度,从而保证裂解气压缩机的正常运转,并降低裂解气压缩机的功耗。
(2)裂解气经预分馏处理,尽可能分馏出裂解气的重组分,减少进入压缩分离系统的进料负荷。
(3)在裂解气的预分馏过程中将裂解气中的稀释蒸汽以冷凝水的形式分离回收,用以再发生稀释蒸汽,从而大大减少污水排放量。
(4)在裂解气的预分馏过程中继续回收裂解气低能位热量。
2)裂解气中的气体杂质裂解气中的气体杂质主要有H2S、CO2、H2O、C2H2、CO。
H2S、CO2无机碱洗或醇胺湿法脱除H2O:3A分子筛吸附脱除C2H2、CO催化加氢脱除。
3-12分离流程的共同点,顺序分离流程,前脱乙烷后加氢流程,前脱丙烷加氢流程的特点优缺点、适用范围。
1)分离流程的共同点:a.裂解气的分离由三个系统构成:气体净化系统,压缩与冷冻系统,精馏分离系统。
制氢技术的生命周期评价研究进展
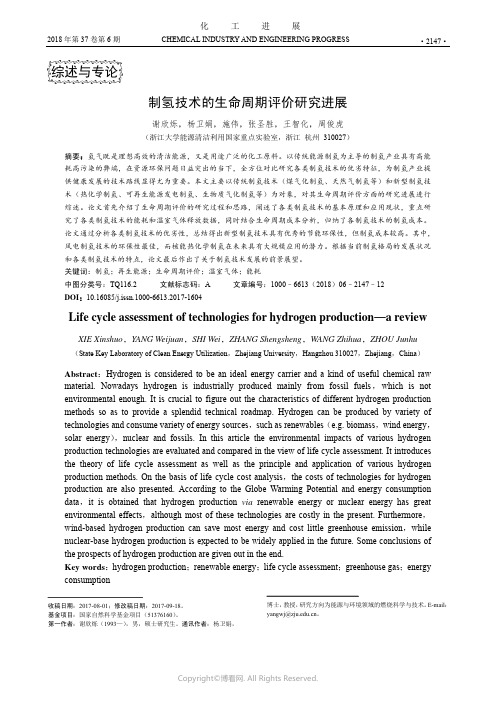
2018年第37卷第6期 CHEMICAL INDUSTRY AND ENGINEERING PROGRESS·2147·化 工 进展制氢技术的生命周期评价研究进展谢欣烁,杨卫娟,施伟,张圣胜,王智化,周俊虎(浙江大学能源清洁利用国家重点实验室,浙江 杭州 310027)摘要:氢气既是理想高效的清洁能源,又是用途广泛的化工原料。
以传统能源制氢为主导的制氢产业具有高能耗高污染的弊端,在资源环保问题日益突出的当下,全方位对比研究各类制氢技术的优劣特征,为制氢产业提供健康发展的技术路线显得尤为重要。
本文主要以传统制氢技术(煤气化制氢、天然气制氢等)和新型制氢技术(热化学制氢、可再生能源发电制氢、生物质气化制氢等)为对象,对其生命周期评价方面的研究进展进行综述。
论文首先介绍了生命周期评价的研究过程和思路,阐述了各类制氢技术的基本原理和应用现状,重点研究了各类制氢技术的能耗和温室气体释放数据,同时结合生命周期成本分析,归纳了各制氢技术的制氢成本。
论文通过分析各类制氢技术的优劣性,总结得出新型制氢技术具有优秀的节能环保性,但制氢成本较高。
其中,风电制氢技术的环保性最佳,而核能热化学制氢在未来具有大规模应用的潜力。
根据当前制氢格局的发展状况和各类制氢技术的特点,论文最后作出了关于制氢技术发展的前景展望。
关键词:制氢;再生能源;生命周期评价;温室气体;能耗中图分类号:TQ116.2 文献标志码:A 文章编号:1000–6613(2018)06–2147–12 DOI :10.16085/j.issn.1000-6613.2017-1604Life cycle assessment of technologies for hydrogen production —a reviewXIE Xinshuo ,YANG Weijuan ,SHI Wei ,ZHANG Shengsheng ,WANG Zhihua ,ZHOU Junhu(State Key Laboratory of Clean Energy Utilization ,Zhejiang University ,Hangzhou 310027,Zhejiang ,China )Abstract :Hydrogen is considered to be an ideal energy carrier and a kind of useful chemical rawmaterial. Nowadays hydrogen is industrially produced mainly from fossil fuels ,which is not environmental enough. It is crucial to figure out the characteristics of different hydrogen production methods so as to provide a splendid technical roadmap. Hydrogen can be produced by variety of technologies and consume variety of energy sources ,such as renewables (e.g. biomass ,wind energy ,solar energy ),nuclear and fossils. In this article the environmental impacts of various hydrogen production technologies are evaluated and compared in the view of life cycle assessment. It introduces the theory of life cycle assessment as well as the principle and application of various hydrogen production methods. On the basis of life cycle cost analysis ,the costs of technologies for hydrogen production are also presented. According to the Globe Warming Potential and energy consumption data ,it is obtained that hydrogen production via renewable energy or nuclear energy has great environmental effects ,although most of these technologies are costly in the present. Furthermore ,wind-based hydrogen production can save most energy and cost little greenhouse emission ,while nuclear-base hydrogen production is expected to be widely applied in the future. Some conclusions of the prospects of hydrogen production are given out in the end.Key words :hydrogen production ;renewable energy ;life cycle assessment ;greenhouse gas ;energy consumption博士,教授,研究方向为能源与环境领域的燃烧科学与技术。
烃类水蒸气转化法制氢概述

烃类水蒸气转化法制氢概述作者:杨金涛陈卫邦来源:《科海故事博览·科教论坛》2013年第11期摘要:本文以烃类水蒸气转化法为例概述了原料经过预处理、转化、中温变换、PSA变压吸附等步骤转化为氢气纯度达到99.9%以上的过程。
关键词:烃类水蒸气转化预处理吸附提纯1 烃类水蒸气转化法原理烃类水蒸汽转化是以烃类为原料,在一定温度和催化剂作用下使烃类和水蒸汽经过一系列的分解、裂化、脱氢、结炭、消炭、氧化、变换、甲烷化等反应,最终转化为H2、CO、CO2、和少量残余的CH4,其中H2是本阶段的目的产物。
烃类的蒸汽转化反应如下:CnHm+nH2O=nCO+(n+m/2)H2——QCH4+H2O=CO+3H2——206000KJ/KmolCO+H2O=CO2+H2——41200KJ/Kmol转化炉内进行的烃类蒸汽转化反应是一个极复杂的平行、顺序反应体系。
从以上反应原理中可以看出其反应过程需需要吸收大量的热,这就要就反应要有较高的反应温度,而烃类易在高温下裂解结炭特别是烯烃,结炭是转化过程中的必然反应,当结炭反应速度大于消炭反应速度时,转化催化剂就会积炭,使催化剂活性下降甚至丧失。
为保证催化剂活性,就要有大于反应所需求过量的水蒸气来进行消炭,从转化后阶段来看,反应生成的CO也需要水蒸汽与之反应,所以生产时要求转化进料始终保持一定的水碳比,使消炭速度大于结炭速度,避免催化剂上炭的沉积。
烃类水蒸气转化法其催化剂主要活性组分为单质Ni,其对原料品质有较高要求,原料中的硫、氯等有害杂质能与转化催化剂活性组分Ni反应生成不可逆转的化合物,从而使其永久性中毒失去活性。
为了充分发挥转化催化剂的活性,并获得较高的氢收率,转化床层一般装填有两种不同性能的催化剂,一般选用Z417/Z418转化催化剂。
Z417/Z418转化催化剂可以适应多种原料,并且对脱毒的需求相对较低。
Z417含有一定钾碱金属的抗结炭助剂因此作为上段催化剂使用,其具有较好的低温活性及抗积炭性能,Z418具有较高的转化活性作为下段床层催化剂。
通过案例分析水蒸气在焦炉气制甲醇工艺转化工段中的重要作用
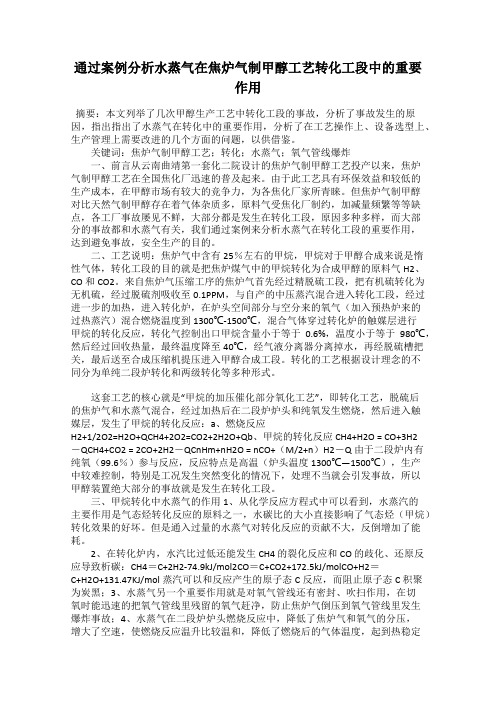
通过案例分析水蒸气在焦炉气制甲醇工艺转化工段中的重要作用摘要:本文列举了几次甲醇生产工艺中转化工段的事故,分析了事故发生的原因,指出指出了水蒸气在转化中的重要作用,分析了在工艺操作上、设备选型上、生产管理上需要改进的几个方面的问题,以供借鉴。
关键词:焦炉气制甲醇工艺;转化;水蒸气;氧气管线爆炸一、前言从云南曲靖第一套化二院设计的焦炉气制甲醇工艺投产以来,焦炉气制甲醇工艺在全国焦化厂迅速的普及起来。
由于此工艺具有环保效益和较低的生产成本,在甲醇市场有较大的竞争力,为各焦化厂家所青睐。
但焦炉气制甲醇对比天然气制甲醇存在着气体杂质多,原料气受焦化厂制约,加减量频繁等等缺点,各工厂事故屡见不鲜,大部分都是发生在转化工段,原因多种多样,而大部分的事故都和水蒸气有关,我们通过案例来分析水蒸气在转化工段的重要作用,达到避免事故,安全生产的目的。
二、工艺说明:焦炉气中含有25%左右的甲烷,甲烷对于甲醇合成来说是惰性气体,转化工段的目的就是把焦炉煤气中的甲烷转化为合成甲醇的原料气H2、CO 和CO2。
来自焦炉气压缩工序的焦炉气首先经过精脱硫工段,把有机硫转化为无机硫,经过脱硫剂吸收至0.1PPM,与自产的中压蒸汽混合进入转化工段,经过进一步的加热,进入转化炉,在炉头空间部分与空分来的氧气(加入预热炉来的过热蒸汽)混合燃烧温度到1300℃-1500℃,混合气体穿过转化炉的触媒层进行甲烷的转化反应,转化气控制出口甲烷含量小于等于0.6%,温度小于等于980℃,然后经过回收热量,最终温度降至40℃,经气液分离器分离掉水,再经脱硫槽把关,最后送至合成压缩机提压进入甲醇合成工段。
转化的工艺根据设计理念的不同分为单纯二段炉转化和两级转化等多种形式。
这套工艺的核心就是“甲烷的加压催化部分氧化工艺”,即转化工艺,脱硫后的焦炉气和水蒸气混合,经过加热后在二段炉炉头和纯氧发生燃烧,然后进入触媒层,发生了甲烷的转化反应:a、燃烧反应H2+1/2O2=H2O+QCH4+2O2=CO2+2H2O+Qb、甲烷的转化反应CH4+H2O = CO+3H2-QCH4+CO2 = 2CO+2H2-QCnHm+nH2O = nCO+(M/2+n)H2-Q由于二段炉内有纯氧(99.6%)参与反应,反应特点是高温(炉头温度1300℃—1500℃),生产中较难控制,特别是工况发生突然变化的情况下,处理不当就会引发事故,所以甲醇装置绝大部分的事故就是发生在转化工段。
甲烷重整反应
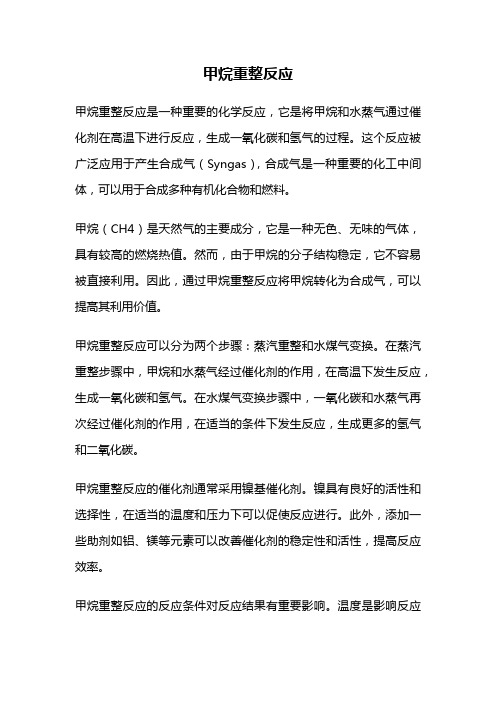
甲烷重整反应甲烷重整反应是一种重要的化学反应,它是将甲烷和水蒸气通过催化剂在高温下进行反应,生成一氧化碳和氢气的过程。
这个反应被广泛应用于产生合成气(Syngas),合成气是一种重要的化工中间体,可以用于合成多种有机化合物和燃料。
甲烷(CH4)是天然气的主要成分,它是一种无色、无味的气体,具有较高的燃烧热值。
然而,由于甲烷的分子结构稳定,它不容易被直接利用。
因此,通过甲烷重整反应将甲烷转化为合成气,可以提高其利用价值。
甲烷重整反应可以分为两个步骤:蒸汽重整和水煤气变换。
在蒸汽重整步骤中,甲烷和水蒸气经过催化剂的作用,在高温下发生反应,生成一氧化碳和氢气。
在水煤气变换步骤中,一氧化碳和水蒸气再次经过催化剂的作用,在适当的条件下发生反应,生成更多的氢气和二氧化碳。
甲烷重整反应的催化剂通常采用镍基催化剂。
镍具有良好的活性和选择性,在适当的温度和压力下可以促使反应进行。
此外,添加一些助剂如铝、镁等元素可以改善催化剂的稳定性和活性,提高反应效率。
甲烷重整反应的反应条件对反应结果有重要影响。
温度是影响反应速率和产物分布的关键因素。
较高的温度可以促使反应进行,但过高的温度会导致产物的选择性下降。
压力对反应的影响相对较小,一般在较低的压力下进行反应即可。
此外,反应物的摩尔比例也会对反应结果产生影响。
甲烷重整反应的产物主要是一氧化碳和氢气。
一氧化碳可以作为合成气的重要组成部分,用于合成甲醇、氨等有机化合物。
氢气是一种重要的化工原料,广泛应用于石油加工、化肥生产等行业。
甲烷重整反应具有很高的反应活性和选择性,但也存在一些问题。
例如,反应过程中会产生大量的二氧化碳,这对环境造成了一定的负面影响。
此外,催化剂的失活问题也需要解决,因为反应过程中催化剂会因为积碳、脱活等原因逐渐失去活性。
甲烷重整反应是一种重要的化学反应,可以将甲烷转化为合成气,提高其利用价值。
该反应具有高的活性和选择性,产物主要是一氧化碳和氢气,可以用于合成多种有机化合物和燃料。
- 1、下载文档前请自行甄别文档内容的完整性,平台不提供额外的编辑、内容补充、找答案等附加服务。
- 2、"仅部分预览"的文档,不可在线预览部分如存在完整性等问题,可反馈申请退款(可完整预览的文档不适用该条件!)。
- 3、如文档侵犯您的权益,请联系客服反馈,我们会尽快为您处理(人工客服工作时间:9:00-18:30)。
天然气转化天然气转化甲烷水蒸汽转化(sMR)甲烷水蒸汽转化工艺(SMR)作为传统的甲烷制合成气过程(图1一2),主要涉及下述反应:CH4+H2O!3H2+COvH298K=206.29kJ/mol这是一个强吸热过程,转化一般要在高温下进行(>1073K)"产物中HZ/Co约为3:1,为防止催化剂积炭,通常需要通入过量的水蒸汽,依合成气用途,原料气中HZO/CH4典型的摩尔比为2-5;并且为保持较高的生产速率,工业生产中压力通常高3.OMPa。
该反应过程的缺点是能耗高,设备庞大复杂!占地面积大,投资和操作费用昂贵。
联合转化工艺(SM侧oZR)联合重整工艺流程如图1-3所示,将SMR反应器出口的混合气送入二级氧化反应器内,未完全消耗的甲烷(在SMR出口处CH;转化率为90-92%)与0:发生部分氧化反应后,再进一步通过催化剂床层进行二次重整反应,生成的合成气HZ/CO 比在2.5~4.0,随后利用水汽转化(WGS)反应(见式4),调整产品中H:和CO比例,来满足下游合成的利用。
该工艺有效地减小了SRM的规模,降低了能耗,但不足之处是仍需两个反应器。
CH4+HZO03H2+COvH29sK=一4IkJ/mol中国石化集团四川维尼纶厂目前在运行的甲醇装置有两套,一为1996年建成投产的直接以天然气为原料的10万t/a甲醇装置,另一为2011年整合建成投产的以乙炔尾气为原料的77万t/a甲醇装置。
前者采用成熟的管式转化炉生产合成气,并利用德国Lurgi合成工艺技术生产甲醇;后者利用英国Davy公司合成工艺生产甲醇,并在合成环路驰放气的处理上采用了膜分离与ATR 转化工艺技术,以提高装置产能和降低综合能耗。
10万t/a甲醇装置通过天然气蒸汽转化制取合成气,故合成气具有氢多、碳少、惰性气体(CH4、N2、Ar 等)含量低的特点,其气质组成有利于甲醇合成反应。
77万t/a 甲醇装置以乙炔尾气为原料,由于乙炔尾气属于天然气部分氧化法制乙炔工艺的副产气,因而具有氢少、碳多、惰性气体含量偏高的特点,属于乏氢气质,需对系统进行补氢。
为深度利用甲醇合成环路驰放气和提高装置产能,工艺上增设了膜分离与ATR转化流程,但伴随而来的是驰放气中大量惰性气体随 ATR 转化气循环返回合成系统并累积,导致合成环路惰性气体的体积分数长期高达25%~30%,这也是该套装置甲醇产品质量不易控制、部分物耗能耗指标达不到设计值且制约甲醇产量进一步提高的主要原因。
针对如何利用天然气制合成气来降低乙炔尾气甲醇装置合成环路的惰性气体含量,提高甲醇产量,使装置运行更加优化与合理,本文通过现场调查以及对相关数据的计算、分析和研究,提出可工程实施的优化运行方案。
优化运行方案选择1)生产工艺与现状10万t/a甲醇装置合成气生产工艺与现状从中石化普光气田直接输送的3.0MPa的高压天然气经预热、脱硫后与水蒸气按n(C)/n(H2O)=1: 3.5的比例混合后继续升温进入管式转化炉,并通过回收烟道气中CO2用前补碳方式在镍催化剂的作用下转化为H2、CO、CO2 等,高温转化气通过废热锅炉以及预热锅炉给水、脱盐水等方式回收热量后再用循环水冷却至40℃,用作后道甲醇合成工序的原料气。
气体实际组成及参数见表 1。
从表1可知,合成气中残余CH4与设计值φ(CH4)为2.72%接近,且极低的N2、Ar含量也为甲醇合成反应提供了良好的反应环境,在通过合理的惰性气体吹除后较好地避免了环路惰性气体的累积。
77 万t/a甲醇装置ATR转化气生产工艺与现状该套装置是在整合了工厂原有的14万t/a与10万t/a两套乙炔尾气甲醇装置的基础上新建的一套以乙炔尾气为原料的甲醇装置,并通过外补H2运行。
乙炔尾气与H2混合后经过净化处理、压缩机升压后进入装有KATALCO51-9催化剂的甲醇合成反应系统,合成环路的驰放气经预洗涤后进入膜分离回收H2,膜分离后的富碳驰放气随即在加热升温后进入ATR反应器,并按一定比例混合加入O2与水蒸气后实现对驰放气中CH4的再回收利用,ATR转化气在通过废热锅炉、加热锅炉给水、精馏塔再沸器回收热量并冷却降温至45℃后返回合成气压缩机进入甲醇合成反应系统。
ATR 转化炉为自热式转化炉,是一种带耐火衬里的反应器,富碳驰放气与O2在ATR烧嘴中充分混合燃烧并进入镍基催化剂床层继续与水蒸气反应生成甲醇合成气。
ATR 转化气组成及工艺参数见表 2。
从表2可知,ATR 转化气中 N2、Ar、CH4 等惰性气体的总量较高,特别是φ(N2)高达15%,致使返回合成系统的惰性气体量QN(惰)≈10000m3/h,造成合成系统惰性气体总量增加,能耗上升并影响到甲醇合成反应。
合成系统惰性气体含量偏高的原因合成系统中惰性气体含量高低取决于补入工艺新鲜气中惰性气体的多少和从合成系统排放的惰性气体量。
在催化剂活性初期和后期,合成环路惰性气体的控制也不尽相同,主要取决于催化剂床层温度,一般初期要求适当高(φ(惰)≤20%),后期要求适当低(φ(惰)≤15%)。
实际生产中,在补入工艺新鲜气中的惰性气体不易改变的条件下,一般通过对合成环路的气体排放来控制惰性气体含量。
但对于高惰性气体含量的合成系统,排放量过多将导致有效气体的损失增加。
77万t/a乙炔尾气甲醇装置至投运以来,就一直存在合成系统中惰性气体含量太高的问题,合成反应器进口气体组成(表 3)中惰性气体体积分数一般约为 25%。
惰性气体在合成环路的存在和累积有几个方面的原因。
原料气影响(1)乙炔尾气。
受制于上游装置天然气部分氧化法制乙炔工艺的影响,副产乙炔尾气中残余 CH4、N2和Ar的体积分数分别为4.5%、1.2%和0.2%左右,这些惰性气体随着乙炔尾气进入甲醇装置并在合成环路累积。
乙炔尾气中的N2 与Ar主要来源于上游乙炔装置的原料氧气携带和乙炔尾气压缩机的干气密封系统。
(2)氢气。
为调节合成气 H/C 比,弥补系统中 H2 的缺失,补加了来自醋酸装置QN≈14000m3/h 的H2,补加H2中φ(CH4)≈1.2%、φ(N2+Ar)≈0.12%。
(3)合成氨装置解析气。
为优化装置运行,回收外送做燃料的合成氨解析气,合成氨装置QN≈6500m3/h的解析气添加到乙炔尾气甲醇装置,其中解析气中除H2外,φ(CH4)≈8%,φ(N2+Ar)≈1%。
内在工艺与设备条件影响(1)系统残余氮气。
装置开车初期,系统氮气置换时约有 0.5%体积分数的N2残留,开车正常后残余氮气很快被合成环路弛放气带出系统,基本不会在环路累积。
(2)原料气压缩机与合成气压缩机干气密封气体中N2的连续带入。
(3)合成反应过程中副反应生成的不凝性气体。
(4)ATR 转化气。
这是合成环路惰性气体含量长期居高不下的主要原因。
由表2可知,ATR 转化气中CH4、N2和Ar的体积分数分别为0.5%、15.2%和1.3%,大量的惰性气体连续返回合成系统并在系统累积。
通过以上分析,ATR 转化气的再循环利用是合成系统惰性气体偏高的主要原因。
外来原料气与压缩机干气密封气体虽然对此也有影响,但原料气由于受制于上游装置自身工艺条件,气体中的惰性气体含量不易降低,而采用N2作干气密封介质的压缩机,虽可采用类似于甲醇合成气组分的气体代替 N2作干气密封介质,但受制于气体中携带杂质的影响以及气体供给稳定性问题而实施替代的可行性较小。
惰性气体对系统与产品的影响(1)合成系统中惰性气体的大量存在和累积,不仅影响合了成气中有效气体成分的浓度,而且降低了有效气体 H2、CO、CO2 在气相中的分压,不利于甲醇合成反应的进行,并导致CO、CO2的单程转化率下降,甲醇时空收率降低,产量下降。
(2)惰性气体含量高,也影响合成反应器催化剂床层温度的分布,目前催化剂床层已出现温度分布不均且有高温区出现,并导致副反应增加和影响催化剂寿命。
(3)惰性气体中N2太多,在一定条件下会与合成气中的H2反应生成NH3,并继而与系统中的甲醇反应生成甲胺类物质,且氨进入甲醇合成反应器后,将会影响催化剂的活性、寿命及粗甲醇质量。
有关试验表明,当系统中φ(NH3)为(50~100)×10-6 时,催化剂活性较无氨时下降10%~20%。
另据有关资料报道,甲醇合成气中φ(NH3)为 20×106时,在甲醇合成的条件下,化学反应过程中就伴随有一甲胺、二甲胺和三甲胺的生成,其化学反应式如下:N2+3H2 →2NH3 (1)CH3OH+NH3→NH2CH3+H2O (2)2CH3OH+NH3 →NH(CH3)2+2H2O (3)3CH3OH+NH3 →N(CH3)3+3H2O (4)上述生成混胺反应导致生产出的粗甲醇夹带有较强异味。
另一方面,混胺类增多,碱值高,有利于生成杂醇的副反应发生,从而增加了粗甲醇中的杂质和精馏过程的难度,既影响甲醇产品质量,又增加各项物料的消耗。
(4)惰性气体在合成环路中的累积循环,系统总压力上升,导致循环压缩机做无用功并增加动力消耗,同时增加合成环路循环冷却水的消耗。
优化运行方案从77万t/a乙炔尾气甲醇装置1 年多的运行情况看,工艺上的主要问题仍然集中在合成系统的高惰性气体含量上,它是上述一系列问题产生的根本原因,并严重影响着装置的正常运行。
该问题属于装置设计遗留问题,在实际运行中已得到明证,若能够解决,将极大改善乙炔尾气甲醇装置的运行情况,并有利于优化合成气气质、提高甲醇产量、改善产品质量和降低装置物耗、能耗。
目前,在合成环路惰性气体排出量不能无限增大、现有工艺条件无法根本改变的前提下,利用不同合成气气质条件的差别,通过在乙炔尾气甲醇装置引入惰性气体含量低的合成气、移走惰性气体含量高的合成气,是降低合成系统惰性气体含量的最有效方法。
降低乙炔尾气甲醇装置合成环路惰气含量ATR转化气被天然气制合成气替代后,ATR 转化气从系统中引出进入另一套甲醇合成反应系统,而不再继续在原甲醇系统循环利用,其结果是乙炔尾气甲醇装置合成环路中的惰性气体含量大幅降低,甲醇合成反应环境极大改善,有利于抑制副反应的发生。
经初步测算,环路惰性气体总体积分数将从实际的25%降低到约17%,主要的变化是系统中的φ(N2+Ar)从15%降低到约5%,φ(CH4)从10%上升至12%。
优化气质、提高甲醇产量和质量替换方案实施后,乙炔尾气甲醇装置合成气质大幅改善。
乙炔尾气甲醇装置甲醇增产量与天然气制甲醇装置甲醇减产量相抵后,净增产量约0.5万t/a。
另外,由于惰性气体的减少与气质的优化,粗甲醇中甲胺类物质减少,产品异味明显改善,其它杂质与石蜡有望同比降低。
降低装置物耗能耗根据模拟计算,气体替换前后乙炔尾气甲醇装置合成环路循环量基本相当,主要区别为原在合成环路累积的部分惰性气体被有效气体组分取代后,循环气的平均分子量变小,初步测算循环压缩机的蒸汽消耗同比降低15%~20%,循环水的消耗也相应降低。