机械加工精度的因素及误差分析研究
关于机械加工精度与加工误差的分析

关于机械加工精度与加工误差的分析笔者具体分析了加工精确度和加工误差等的基础内容。
以实践情况为例,具体的论述了误差产生的缘由,并且论述了降低误差现象发生几率的措施。
标签:加工精度;加工误差;减小误差引言在平时的工作中,我们不乏见到加工方面的内容,对精确性和误差等都不陌生。
不过真正深入了解的话,会发现其是一门非常深入的学科知识。
不管我们工作中如何努力,都无法将误差发生的几率降低为零,因此我们可以做的只能是通过合理的措施来切实的提升精确性,进而降低误差现象的发生几率。
1 加工精度与加工误差概述所谓的精确度,具体的说是零件在生产之后的具体的数值和设想数值之间符合程度。
不论是我们如何努力,都无法保证生产的零件和我们期待中的一模一样,都会存在各种各样的问题,我们将这种问题称为误差。
以工艺体系来看,它的组成部分有四个,分别是机床、刀具、工件以及夹具。
它们在工作的时候会生成很多不一样的误差,而此类误差在不一样的状态中会通过不一样的形式体现出来。
2 机械加工精度与加工误差的分析2.1 工艺系统集合误差2.1.1 机床的几何误差。
在工作中,刀具的的成形活动均是经由机床来实现的,所以,零件的加工精确性会对机床的精确性产生很大的干扰。
常见的机床生产方面的误差有如下的一些:主轴回转误差、导轨误差等。
如果机床磨损的话,就会导致它的精确性明显的变低。
(1)主轴回转误差。
主轴是机床非常关键的一个组成部分,它把力和运动传递给刀具等,一旦它出现了回转误差的话,就会导致零件的精确性受到很大的干扰。
所谓的回转误差,具体的说是主轴短时间的回转轴线比对于它的平均轴线来讲,出现的变动量。
常见的类型有三个,分别是径向圆跳动、轴向窜动和角度摆动。
导致它形成的原因有很多,比如轴承自身的问题,主轴的挠度等等。
不过它们对回转精确性的影响并不是完全一样的,会因为加工状态而产生变化。
产生轴向窜动的主要原因是主轴轴肩端面和轴承承载端面对主轴回转轴线有垂直度误差。
在机械加工过程中的误差分析及数学建模研究

在机械加工过程中的误差分析及数学建模研究机械加工是制造过程中不可或缺的一环。
然而,在机械加工过程中,由于种种因素的影响,难免会出现误差。
误差的存在直接影响到零部件的质量和精度,因此对机械加工过程中的误差进行分析和数学建模研究具有重要的意义。
一、误差来源分析在机械加工过程中,误差可以来源于多个方面,包括:1.制造设备的误差:制造设备本身的精度会对加工零件的准确性产生影响。
例如,机床的刚性、热变形、传动系统的间隙等都会造成误差的产生。
2.切削力的变化:由于刀具的磨损或者加工条件的变化,切削力会发生变化,从而导致零件加工中出现误差。
3.工件的变形:加工过程中,工件可能会因为切削力等原因而发生变形,使得加工结果与设计要求不符。
4.加工过程中的振动:振动是机械加工中不可避免的现象,但过大的振动会引起工件位置的偏移,从而影响加工精度。
二、误差分析方法为了更好地理解机械加工过程中的误差,并对其进行建模研究,我们通常采用以下几种误差分析方法:1.测量方法:通过测量零件的几何属性,使用测量仪器和测量技术分析零件的误差情况。
常用的测量方法包括三坐标测量、投影仪测量等。
2.试验方法:通过设计一系列的试验,控制其他因素不变,仅改变某个因素,如切削速度、刀具刃磨状况等,来测量零件加工结果的误差。
通过对试验结果的分析,可以得到误差与各个因素之间的关系。
3.仿真模拟方法:利用计算机建立机械加工过程的仿真模型,通过对模型进行参数调整和试验,得到加工结果的误差。
仿真模拟方法可以节省时间和成本,并能够更好地在加工过程中控制误差。
三、数学建模研究数学建模是解决误差分析问题的重要方法之一。
在机械加工领域,数学建模可以针对不同的误差来源进行研究,建立与之相关的数学模型,从而帮助我们更加深入地理解误差的本质,并提供改善加工精度和质量的方法。
在误差分析中,常用的数学模型包括:1.误差传递模型:利用数学方法研究误差在加工过程中的传递规律,分析传递路径和影响因素,以便为误差的减小提供方向。
机床机械加工误差产生的原因剖析

机床机械加工误差产生的原因剖析机床机械加工误差是指在机床加工过程中产生的加工尺寸偏离设计要求的现象。
机床机械加工误差会直接影响到加工件的质量和精度,因此产生机床机械加工误差的原因具有重要意义。
下面将从材料、结构、系统和操作四个方面对机床机械加工误差产生的原因进行剖析。
一、材料方面的原因1. 材料的变形:机床在使用过程中由于受到外力作用,材料会发生不可逆的变形。
尤其是对于长时间使用的机床来说,材料的蠕变和疲劳会导致加工误差的产生。
2. 热膨胀:加工过程中机床和工件会受到热源的影响,温度的升高会导致机床和工件的热膨胀,从而引起加工误差。
二、结构方面的原因1. 刚度的不足:机床在加工过程中需要经受各种加工力的冲击,如果机床的结构刚度不足,则容易产生振动和变形,从而导致加工误差的产生。
2. 机床的杂散运动:机床在加工过程中会产生各种杂散运动,如回程差、副轴的不平行等,这些杂散运动都会影响到机床的加工精度,从而导致加工误差的产生。
三、系统方面的原因1. 传动系统的误差:机床的传动系统包括齿轮传动、皮带传动等,这些传动系统在使用过程中会出现磨损和间隙,从而导致传动误差的产生。
2. 液压和气压系统的误差:机床的液压和气压系统在使用过程中会出现压力不稳定、压力波动等问题,这些问题都会直接影响到机床的工作精度,从而导致加工误差的产生。
四、操作方面的原因1. 人为误差:操作人员在使用机床时可能出现误差,如测量仪器的使用不准确、操作人员的操作不规范等,这些人为误差都会直接影响到机床的加工精度,从而引起加工误差。
2. 工艺参数的控制不当:机床的加工精度受到工艺参数的控制,如刀具的选择、切削速度的控制等。
如果工艺参数控制不当,就容易导致加工误差的产生。
机床机械加工误差的产生主要原因包括材料方面的变形和热膨胀、结构方面的刚度不足和杂散运动、系统方面的传动系统误差和液压、气压系统误差,以及操作方面的人为误差和工艺参数控制不当。
机械加工误差产生的原因及措施

机械加工误差产生的原因及措施1加工误差的原因分析由机床、刀具、夹具和工件组成了机械加工的工艺系统,整个系统的误差也就影响着加工误差。
工艺系统的误差是“因”,是根源;加工误差是“果”,是表现。
因此把工艺系统的误差称为原始误差。
系统条件改变了,误差则随之改变,在机械加工工艺系统中,加工误差的产生主要是由原始误差引起的。
这些原始误差主要可归纳为以下几个方面:1.1加工原理误差采用近似的加工运动或者近似的刀具轮廓,都会产生原理误差。
在较多的情况下,为了使工件表面符合规定要求,就需要工件和刀具两者之间有一定的运动联系。
例如,车螺纹就需要刀具与工件之间有螺旋运动的联系;滚切齿轮就需要滚刀与工件之间有准确的展成运动联系等,这种联系就叫做加工原理。
这种运动联系是用机床或夹具来保证的,或是用成型刀具来保证的。
但是在理论上采用的加工原理比较准确时,就需要机床或夹具制造得比较复杂,或者中间环节过多,反而增加了机床的运动误差,进而影响了加工精度的提高。
另外,在用成型刀具加工复杂的曲线表面时,刀具刃口只能近似符合理论曲线,因此就会产生原理误差。
1.2定位安装误差定位和安装是使用夹具固定工件的两个必要动作过程,定位元件决定工件的位置,而制造得非常准确的定位元件是不存在的,都允许有一定的公差范围,这样误差也就随之产生了。
另外,在安装工件时一般都是由人来操作完成的,即使全部由控制系统自动完成的定位安装,误差也会产生,工件形状和尺寸受工件定位夹装精度的影响很大,进而影响工件的装配精度。
因此,操作者不能完全消除定位安装误差,但应当尽量使误差降到最低限度。
1.3机床误差机床误差表现在自身的制造、磨损和安装三个方面。
一般来说,机床在制造、安装以及使用过程中都会出现一定的偏差,虽然机床出厂之前都要经过检验,但主要检验机床的重要零部件的形状和位置误差,而且这些检验是在没有切削载荷的情况下进行的,它反映的是机床的静误差。
在机床静误差中导轨误差、主轴误差和传动链误差三者对加工精度影响最大。
影响机械加工精度的几种因素及其相关对策研究
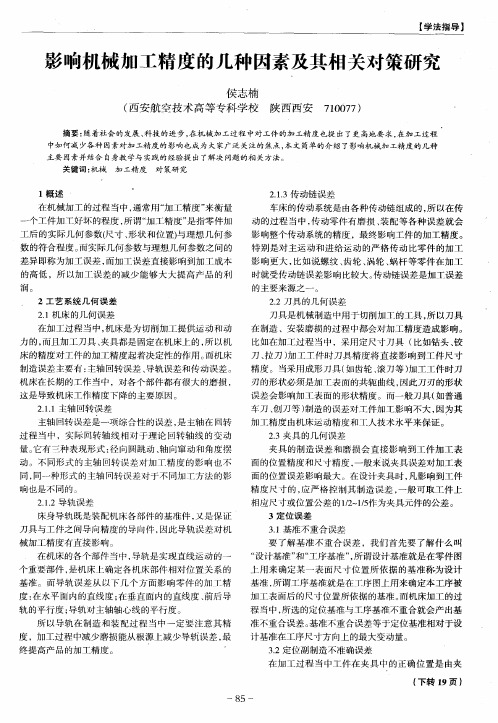
动 的过程 当中 , 传动零 件有磨损 、 装配等 各种误差 就会
影响整个传动系统的精度 ,最终 影响工件 的加 工精度 。 特别是对 主运动和进 给运动 的严 格传 动 比零件 的加 工 影响更大 , 比如说螺 纹 、 齿轮 、 涡轮 、 蜗杆等零 件在加 工 时就受传动链误差影响 比较大。 传动链误差是加_ T误差
关键 词 : 械 机 加 工精 度 对 策研 究
1概 述
21 .. 3传动链误差
在机械加工 的过程 当中 , 通常用 “ 加工精度 ” 来衡 量 个 工件加工好坏 的程度 , 所谓 “ 加工精度 ” 是指 零件加 工后的实 际几何 参数( 尺寸 、 形状 和位置) 与理 想几何 参
一
车床的传动系统是 由各种传 动链组 成的 , 以在传 所
刀具是 机械制 造中用 于切 削加丁 的工具 , 以刀具 所
在加工过程当 中, 机床是为切削加工提供运动 和动
力 的, 而且加工刀具 、 夹具都是固定在机床上的 , 以机 所
在制造 、安装磨损 的过程 中都会对加工精度造成影响 。 比如在加工过程 当中 ,采用定尺寸刀具 ( 比如钻头 、 铰
21 .. 轨误 差 2导
夹具 的制造误差 和磨损会 直接影 响到工件 加工表 面 的位置精度和尺寸精度 , 一般来说夹具误差对加工表 面 的位置误差影响最大 。在设计夹具时 , 凡影响到工件
精度 尺寸的 , 应严格 控制其制造 误差 , 一般可取工 件上 相应尺寸或位置公差 的1 ~ / 为夹具元件 的公差 。 / 1作 2 5
的主要来 源之一。
2 . 具 的几 何 误 差 2刀
数的符合程度 。 而实际几何 参数与理想几何参数之间的
差异 即称 为加工误差 , 而加工误差直接影 响到加 工成本 的高低 ,所 以加 工误 差 的减 少能够 大大提 高产 品的利
机械加工精度的影响因素及提高措施探讨
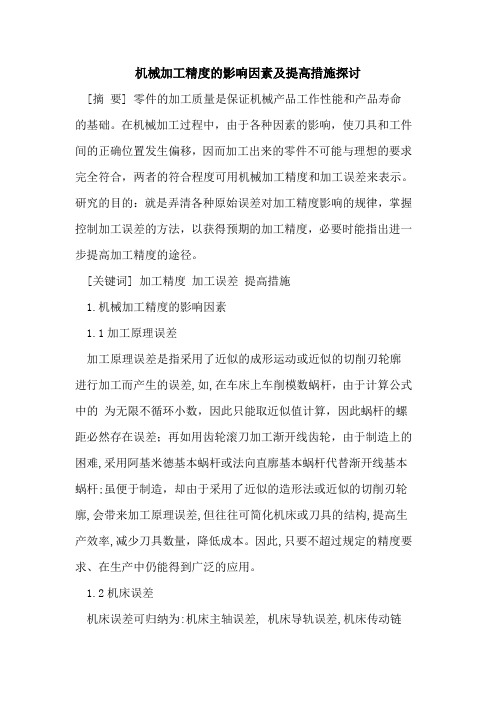
机械加工精度的影响因素及提高措施探讨[摘要] 零件的加工质量是保证机械产品工作性能和产品寿命的基础。
在机械加工过程中,由于各种因素的影响,使刀具和工件间的正确位置发生偏移,因而加工出来的零件不可能与理想的要求完全符合,两者的符合程度可用机械加工精度和加工误差来表示。
研究的目的:就是弄清各种原始误差对加工精度影响的规律,掌握控制加工误差的方法,以获得预期的加工精度,必要时能指出进一步提高加工精度的途径。
[关键词] 加工精度加工误差提高措施1.机械加工精度的影响因素1.1加工原理误差加工原理误差是指采用了近似的成形运动或近似的切削刃轮廓进行加工而产生的误差,如,在车床上车削模数蜗杆,由于计算公式中的为无限不循环小数,因此只能取近似值计算,因此蜗杆的螺距必然存在误差;再如用齿轮滚刀加工渐开线齿轮,由于制造上的困难,采用阿基米德基本蜗杆或法向直廓基本蜗杆代替渐开线基本蜗杆;虽便于制造,却由于采用了近似的造形法或近似的切削刃轮廓,会带来加工原理误差,但往往可简化机床或刀具的结构,提高生产效率,减少刀具数量,降低成本。
因此,只要不超过规定的精度要求、在生产中仍能得到广泛的应用。
1.2机床误差机床误差可归纳为:机床主轴误差, 机床导轨误差,机床传动链误差。
(1)主轴误差主轴误差即实际回转轴线与理想回转轴线的偏移量,具有三种基本形式:纯径向跳动,纯角度摆动,轴向窜动。
影响主轴回转精度的主要因素轴承本身误差、轴承间隙、轴承间同轴度误差,各段轴颈、轴孔的同轴度误差主轴系统的刚度和热变形等,但主轴部件的制造精度是主要的,是主轴回转精度的基础。
(2)机床导轨误差导轨是确定主要部件相对位置的基准和运动的基准,各项误差直接影响被加工工件的精度。
导轨误差分为:导轨在水平面内的误差,在垂直平面内的误差,两导轨的平行度误差。
(3)机床传动链误差是指由于传动链中的传动元件存在制造误差和装配误差引起的。
使用过程中有磨损,也会产生传动链误差。
机械加工精度误差分析及改进措施探讨
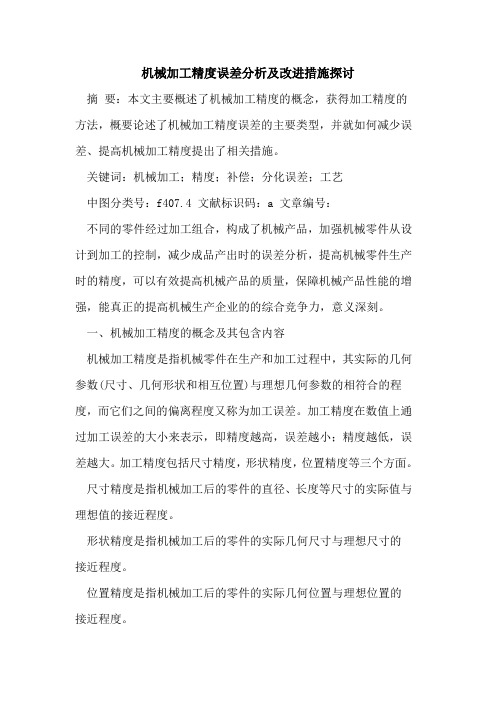
机械加工精度误差分析及改进措施探讨摘要:本文主要概述了机械加工精度的概念,获得加工精度的方法,概要论述了机械加工精度误差的主要类型,并就如何减少误差、提高机械加工精度提出了相关措施。
关键词:机械加工;精度;补偿;分化误差;工艺中图分类号:f407.4 文献标识码:a 文章编号:不同的零件经过加工组合,构成了机械产品,加强机械零件从设计到加工的控制,减少成品产出时的误差分析,提高机械零件生产时的精度,可以有效提高机械产品的质量,保障机械产品性能的增强,能真正的提高机械生产企业的的综合竞争力,意义深刻。
一、机械加工精度的概念及其包含内容机械加工精度是指机械零件在生产和加工过程中,其实际的几何参数(尺寸、几何形状和相互位置)与理想几何参数的相符合的程度,而它们之间的偏离程度又称为加工误差。
加工精度在数值上通过加工误差的大小来表示,即精度越高,误差越小;精度越低,误差越大。
加工精度包括尺寸精度,形状精度,位置精度等三个方面。
尺寸精度是指机械加工后的零件的直径、长度等尺寸的实际值与理想值的接近程度。
形状精度是指机械加工后的零件的实际几何尺寸与理想尺寸的接近程度。
位置精度是指机械加工后的零件的实际几何位置与理想位置的接近程度。
通常在设计零件及规定零件加工精度时,应注意将形状误差控制在位置公差内,位置误差又应小于尺寸公差。
即精密零件或零件的重要表面,其形状精度要求高于位置精度要求,位置精度要求高于尺寸精度要求。
二、获得加工精度的方法(一)试切法是指操作工人在每一工步或走刀前进行对刀,然后切出一小段,测量其尺寸是否合适。
其加工质量取决于工人的技术水平,常用于单件、小批量生产。
(二)调整法分为静调整法和动调整法。
静调整法(样切法)是在不切削的情况下对刀块或样件来调整刀具的位置。
动调整法(尺寸调整法)是按试切零件进行调整的方法,调整完毕即可加工。
(三)尺寸刀具法大多利用定尺寸的孔加工刀具,如钻头、拉刀等来加工孔。
方法四:主动测量法。
影响机械加工精度因素浅析

影响机械加工精度因素在机械加工过程中,往往有很多因素影响工件的最终加工质量,如何使工件的加工达到质量要求,如何减少各种因素对加工精度的影响,就成为加工前必须考虑的事情,也就是要对影响机械加工精度的因素进行分析。
一、集合误差1.机床的几何误差:加工中刀具相对于工件的成形运动一般都是通过机床完成的,因此,工件的加工精度在很大程度上取决于机床的精度。
机床制造误差对工件加工精度影响较大的有:主轴回转误差、导轨误差和传动链误差。
机床的磨损将使机床工作精度下降。
1) 主轴回转误差,机床主轴是装夹工件或刀具的基准,并将运动和动力传给工件或刀具,主轴回转误差将直接影响被加工工件的精度。
2) 导轨误差,导轨是中国论文联盟整理机床上确定各机床部件相对位置关系的基准,也是机床运动的基准。
除了导轨本身的制造误差外,导轨的不均匀磨损和安装质量,也使造成导轨误差的重要因素。
导轨磨损是机床精度下降的主要原因之一。
3) 传动链误差,传动链误差是指传动链始末两端传动元件间相对运动的误差。
一般用传动链末端元件的转角误差来衡量。
2.刀具的几何误差:刀具误差对加工精度的影响随刀具种类的不同而不同。
采用定尺寸刀具成形刀具展成刀具加工时,刀具的制造误差会直接影响工件的加工精度;而对一般刀具(如车刀等),其制造误差对工件加工精度无直接影响。
3.夹具的几何误差:夹具的作用时使工件相当于刀具和机床具有正确的位置,因此夹具的制造误差对工件的加工精度(特别是位置精度)有很大影响。
二、定位误差1.基准不重合误差:定位基准与设计基准不重合时所产生的基准不重合误差,只有在采用调整法加工时才会产生,在试切法加工中不会产生。
2.定位副制造不准确误差:工件在夹具中的正确位置是由夹具上的定位元件来确定的。
基准不重合误差的方向和定位副制造不准确误差的方向可能不相同,定位误差取为基准不重合误差和定位副制造不准确误差的矢量和。
三、工艺系统受力变形引起的误差1.基本概念:机械加工工艺系统在切削力、夹紧力、惯性力、重力、传动力等的作用下,会产生相应的变形,从而破坏了刀具和工件之间的正确的相对位置,使工件的加工精度下降。
- 1、下载文档前请自行甄别文档内容的完整性,平台不提供额外的编辑、内容补充、找答案等附加服务。
- 2、"仅部分预览"的文档,不可在线预览部分如存在完整性等问题,可反馈申请退款(可完整预览的文档不适用该条件!)。
- 3、如文档侵犯您的权益,请联系客服反馈,我们会尽快为您处理(人工客服工作时间:9:00-18:30)。
工过程中保持这个位置不变,以此保证被加工
参考文献
2 误差分析的方法研究
尺寸的精度。这种方法广泛用于各类半白动、自 [1]周丽丽,张平宽,王慧霖等.振动切削技术的
(1)分布曲线法
动机床和自动线卜,适用于成批、大量生产。 研究与发展应用[J].煤矿机械,2009(2).
在正常状态下
(3)定尺寸刀具法。这种方法是用刀具的相 [2]刘仲海.加工中心刀具半径补偿的妙用[J].天
的 40%~70%。(4)主轴回转误差,机床主轴是装 求为止。这种方法能达到较高的加工精度,但它 对加工精度的影响,研究了误差分析的方法,最
夹工件或刀具的基准,并将运动和动力传给工 的效率低,对操作者的技术水平要求高,主要适 后归纳了提高加工进度的方法,对于工艺系统
件或刀具,主轴回转误差将直接影响被加工工 用于单件小批生产。
正 态 分 布 曲 线 度来保证。由于可以提高刀具制造精度,因此用
图 2 正态分布曲线 的数学关系式为: 尺寸刀具加工能达到相当高的加工精度,同时
责任编辑:王俊
-65-
精度分析的急需研究的问题。
行工艺验证。
产。
1 工艺系统的制造和磨损对加工精度的影
(2)点图法
图 3 示出在内圆
响研究
若每隔 1 小时抽检 m 件零件,将 m 件零件 磨床上用自动控制法
加工精度与工艺系统密切相关。工艺系统 检查后算出其算术平均值,画在尺寸—时间图 磨孔的示意图。砂轮
误差是“因”,是根源;加工误差是“果”,是表现。 上,形成一系列的点,就成为点图。将点图上的 座带动砂轮,每往复
中的精度提高和误差控制有一定的现实意义,
件的精度。(5)传动链误差,传动链误差是指传
(2)调整法。这种方法是先调整好刀具和工 但是工艺系统的复杂要求具体情况具体分析,
动链始末两端传动元件间相对运动的误差。一 件在机床上的相对位置,并在—— —批零件的加 特殊的误差控制有待进一步研究。
般用传动链末端元件的转角误差来衡量。
正确位置受到破坏,影响机械加工精度。(3)工 刀具受热变形分析、度量误差分析和对刀误差
结束语
艺系统的受热变形,在热的作用下,工艺系统同 分析等方法。将上述各项误差综合起来,可以得
目前在国际市场上,产品的竞争实质上是
样不可避免地要产生变形,同样会使刀具相对 到总误差。
工艺技术的竞争,因此提高工艺系统的制造精
于工件的正确位置受到破坏,造成加工误差。特
3 提高加工精度的措施研究
度,掌握其变化的基本规律,从而采取相应的措
别是对于精密加工和大件加工,由于工艺系统
(1)试切法。这种方法就是通过试切、测量、 施减少加工误差是提高产品质量的一个突破
热变形所引起的加工误差常常占到加工总误差 调整、再试切,反复进行直到被加工尺寸达到要 口。本文系统地分析了工艺系统的制造和磨损
加工的一批零件,其 应尺寸和形状来保证被加工部位的尺寸和形 津职业院校联合学报,2009(2).
尺 寸 分 布 曲 线 将 接 状。例如,钻孔、铰孔、拉孔、镗孔、攻螺纹和铣槽 [3]李玉平.机械加工误差的分析[J].新余高专学
近正态分布曲线。 等。这种方法的加工精度主要由刀具本身的精 报,2005(2).
削加工提供运动和动力的,机床原有误差对加 然后分项计算误差,并判断是系统误差还是随
工精度的影响最为显著,也最为复杂。(2)工艺 机误差,最后按代数和及数理统计学方法将各
系统的受力变形,在力的作用下,工艺系统不可 项误差综合起来,就可以得到总的误差。
避免地要产生变形,从而使刀具相对于工件的
除以上常用的四种误差分析方法外,还有 图 4 内工误差的问题。
正态分布曲线的形状决定于均方差 σ,σ 环,即自动完成加工巾的切削、度量、补偿调整
如何提高精度,掌握其变化的基本规律,从而采 越大,加工方法的加工精度较低;σ 越小,加工 等一系列工作,当工件达到要求的尺寸时,机床
取相应的措施减少加工误差,是现在机械加工 精度较高。在生产中,可以利用正态分布曲线进 自动退刀停止加工。此法适用于成批和大量生
科技论坛
机械加工精度的因素及误差分析研究
赵利军 刘拥军 李 辉 (河南平高电气股份有限公司,河南 平顶山 467001)
摘 要:针对工艺系统中的加工精度问题,分析了其形成的因素,研究了误差分析的方法,最后归纳了提高加工精度的措施,对于工艺系统中的 精度提高和误差控制有一定的现实意义,但是工艺系统的复杂要求具体情况具体分析,特殊的误差控制有待进一步研究。
有个别点可能无关甚至相反。
图 1 原始误差分类图
(4)分析计算法
其中,常见的误差为机床误差、受力变形、
根据具体加工情况来定量分析影响加工精
受热变形、主轴回转误差和传动链误差。
度的各项因素。具体做法:先根据加工具体情况
(1)机床误差,在工艺系统中,机床是为切 分析影响加工精度的主要因素,舍去次要因素,
工艺系统误差又称之为原始误差。原始误差分 折线代之以光滑的曲线,就得到精度曲线图(图 走刀一次,塞规 5 借 图 3 时间/尺寸点图
类如图 1。
2),它反映了在一次调整中,尺寸精度与时间的 弹簧 6 之力测量孔一次。孔的尺寸若不到位,塞
关系。
规插不进孔内,这时没有信号发出,机床则继续
精度曲线是分布曲线在时间上的展开。两 工作。待孔的尺寸磨到公差范围以内时,塞规 5
机械加工精度是衡量零件的加工质量的指标之 术平均值;y—零件尺寸为 x 时所出现的概率密 的孔、螺纹和成形表面的加工。
一。在机械加工中,误差是不可避免的,但误差 度;σ—一批零件的均方差;n—一批零件的数
(4)自动控制法。这种方法是用度量装置、
必须在允许的范围内。保证和提高加工精度的 量。
进给机构和控制系统构成加工过程的自动循
者的差别在时间性,精度曲线比分布曲线优越。 插入孔内,这时触杆 1 向右运动,推动信号开
(3)相关分析法
关,发出改变磨削用量的信号,机床进入精磨过
函数关系:一般有函数表达式,知道其中一 程。当塞规 4 也能插入孔内时。
个变量值,就可以确切推出另一变量值。相关关
系:从总体上来看,两个变量之间是有关的,但
关 键 词 :工艺系统;加工精度;误差分析
引言 零件的质量直接影响着产品的性能、寿命、
y= 1 exp[-(x-x軃)2/2σ2] σ 姨2π
又避免了试切过程,生产率较高。其主要缺点是 刀具的制造复杂和耗费较大,使用的尺寸范围
效率、可靠性等指标,是保证产品质量的基础,
x—零件的尺寸;x—一批零件的尺寸的算 受到一定的限制。此法适用于各种生产规模中