中南大学机械制造工艺学实验报告之加工误差的统计分析报告
中南大学机械制造工艺处理学实验报告
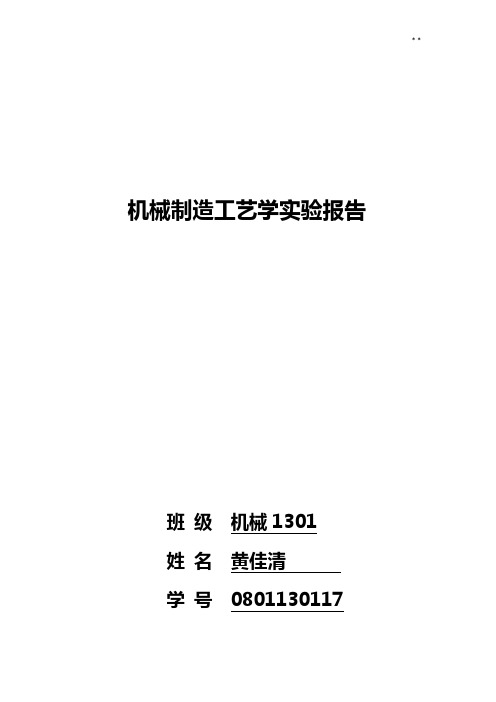
机械制造工艺学实验报告班级机械1301姓名黄佳清学号0801130117中南大学机电学院《机械制造工艺学》课程实验报告实验名称:加工误差的统计分析姓名:黄佳清班级:机械1301 学号:0801130117实验日期:2015 年10 月18 日指导教师:成绩:1. 实验目的(1)掌握加工误差统计分析方法的基本原理和应用。
(2)掌握样本数据的采集与处理方法,要求:能正确地采集样本数据,并能通过对样本数据的处理,正确绘制出加工误差的实验分布曲线和图。
(3)能对实验分布曲线和图进行正确地分析,对加工误差的性质、工序能力及工艺稳定性做出准确的鉴别。
(4)培养对加工误差进行综合分析的能力。
2. 实验内容与实验步骤1.按加工顺序测量工件的加工尺寸,记录测量结果。
2.绘制直方图和分布曲线1)找出这批工件加工尺寸数据的最大值x max和最小值x min,按下式计算出极差R。
R=x max一x min2)确定分组数K(K一般根据样本容量来选择,建议可选在8~11之间)。
3)按下式计算组距d。
4)确定组界(测量单位:微米)。
5)做频数分布表。
6)计算x和 。
7)画直方图以样本数据值为横坐标,标出各组组界;以各组频率密度为纵坐标,画出直方图。
8)画分布曲线若工艺过程稳定,则误差分布曲线接近正态分布曲线;若工艺过程不稳定,则应根据实际情况确定其分布曲线。
画出分布曲线,注意使分布曲线与直方图协调一致。
9)画公差带在横轴下方画出公差带,以便与分布曲线相比较。
3.绘制图1)确定样组容量,对样本进行分组样组容量m通常取4或5件。
按样组容量和加工时间顺序,将样本划分成若干个样组。
2)计算各样组的平均值和极差对于第i个样组,其平均值和极差计算公式为:∑==mjijixmx11式中——第i个样组的平均值;——第i个样组的标准差;——第i个样组第j个零件的测量值;——第i个样组数据的最大值;——第i个样组数据的最小值3)计算图控制限(计算公式见实验原理)4)绘制图以样组序号为横坐标,分别以各样组的平均值和极差R为纵坐标,画出图,并在图上标出中心线和上、下控制限。
加工误差统计分析实验报告

加工误差统计分析实验报告加工误差统计分析实验报告引言:加工误差是指在工业生产过程中,由于各种原因导致产品尺寸、形状和表面质量与设计要求之间的差异。
加工误差的控制对于保证产品质量、提高生产效率和降低成本具有重要意义。
本实验旨在通过对加工误差进行统计分析,探讨误差来源及其影响因素,为工业生产过程中的质量控制提供参考依据。
实验设计:本实验选取了一台数控铣床进行实验,以铣削加工尺寸为研究对象。
首先,我们选择了一种常见的零件,对其进行加工。
然后,通过测量加工后的尺寸与设计要求进行对比,得到加工误差数据。
最后,我们对这些数据进行统计分析,探究加工误差的分布规律和影响因素。
实验过程:1. 加工准备:选择合适的刀具、夹具和工艺参数,进行加工准备工作。
2. 加工操作:按照设计要求进行铣削加工,并记录下每次加工后的尺寸数据。
3. 尺寸测量:使用测量工具对加工后的零件进行尺寸测量,并记录测量结果。
4. 数据整理:将测量得到的数据整理成表格,方便后续的统计分析。
统计分析:1. 加工误差分布:通过绘制加工误差的频率分布直方图,我们可以观察到误差值的分布情况。
通常情况下,加工误差符合正态分布,但也可能存在其他分布形式,例如偏态分布或双峰分布。
通过分析分布形式,可以判断加工过程中是否存在特殊的误差来源。
2. 加工误差与加工参数的关系:通过对加工误差与加工参数(如切削速度、进给速度等)进行相关性分析,可以了解不同参数对加工误差的影响程度。
这有助于我们确定合适的工艺参数范围,以减小加工误差。
3. 加工误差与刀具磨损的关系:刀具磨损是导致加工误差增大的重要因素之一。
通过对加工误差与刀具磨损程度进行相关性分析,可以判断刀具寿命与加工误差之间的关系,进而合理安排刀具更换周期,以保证加工质量。
4. 加工误差与工件材料的关系:不同材料的加工性能不同,可能导致加工误差的差异。
通过对加工误差与工件材料进行相关性分析,可以了解不同材料对加工误差的影响程度,为材料选择和工艺优化提供依据。
机械制造工艺学加工误差统计分析报告

机械制造加工误差的统计分析一、实验目的:1.通过实验掌握加工精度统计分析的基本原理和方法,运用此方法综合分析零件尺寸的变化规律。
2.掌握样本数据的采集与处理方法,正确的绘制加工误差的实验分布曲线和x-R图并能对其进行正确地分析。
3.通过实验结果,分析影响加工零件精度的原因提出解决问题的方法,改进工艺规程,以达到提高零件加工精度的目的,进一步掌握统计分析在全面质量管理中的应用。
二、实验用材料、工具、设备1.50个被测工件;2.千分尺一只(量程25~50);3.记录用纸和计算器。
三、实验原理:生产实际中影响加工误差的因素是复杂的,因此不能以单个工件的检测得出结论,因为单个工件不能暴露出误差的性质和变化规律,单个工件的误差大小也不能代表整批工件的误差大小。
在一批工件的加工过程中,即有系统性误差因素,也有随机性误差因素。
在连续加工一批零件时,系统性误差的大小和方向或是保持不变或是按一定的规律而变化,前者称为常值系统误差,如原理误差、一次调整误差。
机床、刀具、夹具、量具的制造误差、工艺系统的静力变形系统性误差。
如机床的热变形、刀具的磨损等都属于此,他们都是随着加工顺序(即加工时间)而规律的变化着。
在加工中提高加工精度。
常用的统计分析有点图法和分布曲线法。
批零件时,误差的大小和方向如果是无规律的变化,则称为随机性误差。
如毛坯误差的复映、定位误差、加紧误差、多次调整误差、内应力引起的变形误差等都属于随机性误差。
鉴于以上分析,要提高加工精度,就应以生产现场内对许多工件进行检查的结果为基础,运行数理统计分析的方法去处理这些结果,进而找出规律性的东西,用以找出解决问题的途径,改进加工工艺,提高加工精度。
四、实验步骤:1.对工件预先编号(1~50)。
2.用千分尺对50个工件按序对其直径进行测量,3. 把测量结果填入表并将测量数据计入表1。
表内的实测值为测量值与零件标准值之差,单位取µm五、 数据处理并画出分布分析图:组 距: 44.59)35(1411min max =--=--=-=k x x k Rd µm 5.5=d µm 各组组界: ),,3,2,1(2)1(min k j dd j x =±-+ 各组中值: d j x )1(min -+16.1111-==∑=ni i x n x µm 28.12)(1112=--=∑=ni i x x n σ六、 误差分析1.加工误差性质样本数据分布与正态分布基本相符,加工过程系统误差影响很小。
实验二 加工误差统计分析实验

实验二 加工误差统计分析实验一、实验目的1.培养学生综合运用数理统计、计算机技术、加工精度分析等方面知识的能力。
2.熟练掌握在实际生产中工艺过程精度统计分析的内容和方法。
3.学会分析在加工过程中各种误差因素对加工精度的影响。
4.学会用分布图法计算零件废品率和合格品率和点图分析法。
二、实验设备及工件1.普通车床2.检具和测量系统3.工件4.计算机三、实验原理1、工艺过程的分布图分析法(1)样本容量n 的确定 样本容量不能太大或太小。
本实验取n=100。
(2)样本数据的测量 使用检测仪器实测100个试件尺寸,并按加工顺序纪录在数据表中。
(3)异常数据的剔除当工件测量数据服从正态分布时,|x k -x |>3σ,则x k 为异常数据,应于以剔除。
(4)实际分布图的绘制a .确定尺寸间隔数j 尺寸间隔数(尺寸分组数)j 不可随意确定。
一般可参考下表选取。
b .确定尺寸间隔大小(区间宽度)Δx 只要找到样本中个体的最大值x max 和x min 即可算得的jx x x min max -=∆ 为了使x max 和x min 皆落在尺寸间隔中,在坐标轴上取j=j+1个点。
c .画实际分布图 列出测量数据的计算表格如下表所示。
画图时,实际频数值应在尺寸区间中点的纵坐标上。
计算表格(5)理论分布图的绘制将以概率密度为纵坐标的理论分布图转化成以频数为纵坐标的理论分布图。
正态分布曲线的理论频数曲线最大值和拐点处的理论频数值分别为:xn xn y f ∆=∆='σ14.0max maxxn xn y f ∆=∆='σσσ124.0 理论频数曲线最大值的横坐标为x ;两个拐点的横坐标分别为(σ±x );分散范围为(σ3+x )和(σ3-x )。
根据这些数据,就可以画出以频数为纵坐标的理论分布曲线。
(6)工艺过程的分布图分析a .判断加工误差性质 如果通过检验,确认样本是服从正态分布的,就可以认为工艺过程中变值系统性误差很小(或不显著);如果工件尺寸误差的实际分布中心x 与公差带中心有偏移ε,表明工艺过程中有常值系统性误差存在。
加工误差统计分析实验报告

加工误差统计分析实验报告一、实验目的通过统计分析加工误差数据,探究加工工艺对产品加工误差的影响,并提出相应的改进措施。
二、实验原理加工误差是指产品实际尺寸与设计尺寸之间的差异,主要受到原材料、加工设备、操作工艺等因素的影响。
统计分析可以通过数学模型和数据处理方法,定量地描述和评估加工误差的分布情况,为加工工艺改进提供依据。
三、实验步骤1.随机选择一批相同产品进行加工,保持其他加工条件不变。
2.测量每个产品的实际尺寸,记录数据并整理成表格。
3.统计每组数据的平均值、方差以及标准差。
4.构建加工误差的概率分布函数,通过正态性检验和偏度、峰度检验判断数据是否符合正态分布。
5.进行加工误差数据的t检验,分析不同因素对加工误差的影响程度。
四、实验数据产品编号,实际尺寸 (mm)--------,--------------1,10.012,10.02...,...100,10.08五、数据处理及分析1.计算平均值、方差和标准差:平均值μ=(10.01+10.02+...+10.08)/100=10.05方差s^2=((10.01-10.05)^2+(10.02-10.05)^2+...+(10.08-10.05)^2)/99标准差s=√s^22.正态性检验:根据实验数据计算样本均值和样本标准差,绘制加工误差的概率密度分布曲线。
通过观察曲线形状以及进行偏度、峰度检验,判断数据是否符合正态分布。
3.t检验:根据产品加工误差数据,进行t检验来分析不同因素对加工误差的影响程度。
比如,可以比较不同机器加工出的产品误差是否有显著性差异。
六、实验结果分析1.样本加工误差符合正态分布,数据较为集中,无明显偏离。
2.通过t检验发现:不同机器加工出的产品误差差异不显著,说明机器之间的加工稳定性较好。
3.根据样本数据及数据处理结果,可以得到加工误差的基本分布情况,对加工工艺的控制和改进提供依据。
例如,可以调整机器参数、改进操作工艺等。
机械加工误差统计分析实验报告

机械加工误差统计分析实验报告机械加工误差统计分析实验一、实验目的:了解机械加工过程中工件的尺寸分布状态和变化规律,学习、掌握加工误差的统计分析方法。
二、实验原理:机械加工过程中存在系统性和随机性误差的综合影响,造成工件的加工尺寸不断变化。
统计分析方法就是以生产现场对一定数量的工件测量所得的结果为基础,运用数理统计方法进行处理,评定其加工情况,进而研究误差的性质及影响因素。
机械加工中采用的统计分析有两种方法:即分布图法和点图法。
1、分布图法理论研究与生产实践证明,在调整好的机床上连续加工一批工件,如果没有系统性误差存在,只在随机性误差因素的作用下,加工工件的尺寸将服从正态分布,(见图4-1),它的方程为:()()22σ?Χ?Χ?Χ=式中:X--工件的尺寸;Χ--工件的平均尺寸;σ--均方根偏差(标准差)。
根据概率论与数理统计原理:工件的尺寸可近似的认为分布在X ±3σ的范围内,那么该工序的工艺能力系数:6C δσΡ=式中:δ—图纸上规定的工件的公差值。
在实验过程中,根据加工情况所做实验分布曲线符合正态分布,则说明工艺过程是稳定的。
若出现明显差异,说明工艺过程不稳定,工艺系统中存在系统误差因素。
因此,根据分布曲线可以很方便的推测、判断工序的加工情况。
2、点图法在生产实践中常用点图法来观察尺寸变化趋势,控制加工过程。
在调整好的机床上连续加工一批工件,依次进行分组,计算小组平均值X 和极差R ,以加工组序或时间为横坐标,则平均值Χ为纵坐标,做出X 图;极差R为纵坐标,作出R 图(见图4-2)Χ能够反映变值系统性误差的变化规律,R 图则反映随机性误差的大小。
对于稳定工艺过程,若样组数为m ,则点图的中心线及上、下控制线按表4-1 各式计算:上表4-2式中:A 、D 1、D 2--系数,可根据工件分组情况查表得出;若点子超出R 图控制线,则说明随机误差过大,工艺系统出现了异常情况,都应对机床重新调整或停机检查。
加工误差
加工误差统计分析实验报告实验名称加工误差统计分析实验日期2014年12月30日班级机械117班姓名安建廷同组人王云利杨磊戚晓彤丁兴一﹑实验目的统计分析法是通过一批工件加工误差的表现形式,来研究产生误差原因的一种方法。
做加工误差统计分析实验的目的在于,巩固已学过的统计分析法的基本理论;掌握运用统计分析法的步骤,练习使用统计分析法判断问题的能力。
1. 掌握绘制工件尺寸实际分布图的方法,并能根据分布图分析加工误差的性质,计算工序能力系数,合格品率,废品率等,能提出工艺改进的措施;2. 掌握绘制X-R 点图的方法,能根据X-R 点图分析工艺过程的稳定性。
二﹑实验仪器设备设备:M1040无心磨床量仪:数显千分尺一把试件:工件一批三﹑实验原理在M1040 无心磨床上用纵磨法磨削工件一批,检查其每件尺寸。
做出实际分布图以及X—R 控制图。
在机械加工中应用数理统计方法对加工误差(或其他质量指标)进行分析,是进行过程控制的一种有效方法,也是实施全面质量管理的一个重要方面。
其基本原理是利用加工误差的统计特性,对测量数据进行处理,做出分布图和点图,据此对加工误差的性质、工序能力及工艺稳定性等进行识别和判断,进而对加工误差做出综合分析。
四﹑实验数据记录与处理1. 实验原始数据2. 绘制实际分布图(1)剔除异常数据==∑=ni i x n x 1119.9915=--=∑=n i ix x n 12)(11σ0.017若σ3>-x x k ,认为k x 为异常数据,应剔除。
(2)确定尺寸间距和分组数1)初选分组数 K一般应根据样本容量来选择,容量为100。
2)确定组距找出样本数据的最大值 X max 和最小值X min ,并计算组距:计算求得组距d=0.016选取与计算的 d'值相近的且为测量值尾数整倍数的数值为组距。
3)确定分组数 共分为9组(3)制作频率分布表(4)绘制实际分布图(5)加工误差统计分析(误差性质、改进措施、工序能力、合格品率等)通过对直方图的分析,可以看出总体来说满足要求,误差范围也较小,但是还是有一部分不满足加工要求仍需要改进。
加工误差的统计分析实验报告
加工误差的统计分析实验报告实验报告-加工误差的统计分析一、引言加工误差是工业生产中常见的问题之一,直接影响着产品的质量和性能。
了解加工误差的统计分布和规律,对于优化加工工艺、提高产品精度具有重要意义。
本实验旨在通过统计分析加工误差数据,探讨加工误差的分布及其对产品质量的影响。
二、实验设计1.实验目标:观察加工误差的统计分布及其规律。
2.实验工具:数控加工机床,三坐标测量仪3.实验材料:其中一种金属材料4.实验步骤:a.设计并加工若干个样品b.使用三坐标测量仪测量每个样品的加工误差c.记录加工误差数据并进行统计分析三、实验结果1.加工误差数据记录表样品编号,加工误差(mm----------,--------------A,0.0B,0.0C,0.0D,0.0E,-0.0F,0.0G,0.0H,-0.0I,0.0J,0.02.加工误差的统计分析a. 加工误差的均值(μ):0.01mmb. 加工误差的标准差(σ):0.02mmc. 加工误差的方差(σ^2):0.0004mm^2四、结果分析1. 加工误差的均值与标准差分别表示了加工误差的集中程度和离散程度。
实验结果显示,加工误差的均值为0.01mm,说明整体上加工误差集中在一个较小的范围内。
而标准差为0.02mm,表明加工误差的离散程度较大。
2.通过加工误差的统计分布分析,可以更准确地评估加工精度的稳定性和可靠性。
3.经过正态性检验,加工误差近似符合正态分布,这与许多加工误差服从中心极限定理的理论支持一致。
五、结论1. 通过加工误差数据的统计分析,得出样品加工误差的均值为0.01mm,标准差为0.02mm,方差为0.0004mm^22.样品的加工误差数据近似符合正态分布,说明加工误差在一定程度上服从中心极限定理。
3.实验结果进一步表明,加工误差的集中程度较高,但其离散程度相对较大。
六、改进建议1.根据加工误差的分布规律,可以对加工工艺进行优化,减小加工误差的产生。
加工误差统计分析实验报告
实验价值:为企业提供有效的 质量控制方法和改进措施
添加 标题
加工误差的定义:加工误差是指零件加 工后实际几何参数(尺寸、形状和位置) 与理想几何参数的偏离程度。
添加 标题
加工误差的分类:根据其产生的原因和 性质,加工误差可分为随机误差、系统 误差和粗大误差三类。
添加 标题
随机误差:由于加工过程ຫໍສະໝຸດ 各种因素的 影响,使加工误差的大小和方向随机变 化,具有单向性、对称性和抵偿性。
加工误差的影响程度:对产 品质量、生产效率、成本等 方面的影响
加工误差产生的原因:机床、 刀具、夹具、测量仪器等因 素导致的误差
加工误差的分类:系统误差、 随机误差、粗大误差等
加工误差的检测方法:直接 测量法、间接测量法、比较
测量法等
提高加工精度:采用更精确的加工设备和工艺,减少误差 加强过程控制:对加工过程进行严格监控,确保每个环节的准确性 引入先进技术:采用先进的误差检测和校正技术,提高加工精度 加强员工培训:提高员工对加工误差的认识和技能水平,减少人为因素造成的误差
,a click to unlimited possibilities
01 实 验 目 的 02 实 验 原 理 03 实 验 步 骤 04 实 验 结 果 05 实 验 结 论 06 参 考 文 献
实验目的:分析加工误差的来 源和影响因素
实验意义:提高加工精度,降 低误差,提高产品质量
实验目标:确定加工误差的分 布规律和变化趋势
采集方法:直接 测量、间接测量、 组合测量
采集工具:测量 仪器、传感器、 计算机等
数据处理:对采 集到的数据进行 预处理、分析、 整理等操作
数据收集:通过实验测量获得数 据
数据处理:对数据进行预处理和 变换
加工误差的统计分析实验报告
加工误差的统计分析实验报告
《加工误差的统计分析实验报告》
在工业生产中,加工误差是一个常见的问题,它会直接影响产品的质量和性能。
为了解决这一问题,我们进行了一项加工误差的统计分析实验,以期找到有效
的控制和改善方法。
实验过程中,我们选择了一批相同规格的零件进行加工,并对加工过程中的误
差进行了详细记录和分析。
首先,我们对零件的尺寸进行了测量,并得到了一
系列的数据。
然后,我们使用统计学方法对这些数据进行了处理和分析,得出
了一些有价值的结论。
通过实验,我们发现加工误差的分布呈现出一定的规律性,大部分误差集中在
一个较小的范围内,但也存在一些异常值。
此外,我们还发现了一些可能导致
加工误差的原因,比如加工设备的精度、操作人员的技术水平等。
基于实验结果,我们提出了一些改善措施。
首先,我们建议对加工设备进行定
期检修和维护,以保证其加工精度。
其次,我们还提出了加强操作人员培训和
技术指导的建议,以提高其加工技术水平。
最后,我们还计划对加工工艺进行
优化,以减小加工误差的发生概率。
总的来说,通过这次实验,我们对加工误差有了更深入的了解,并提出了一些
有效的改善措施。
我们相信,通过这些措施的实施,我们能够有效地控制和减
小加工误差,提高产品的质量和性能。
希望我们的实验报告能够对其他相关领
域的研究和实践提供一定的借鉴和参考。
- 1、下载文档前请自行甄别文档内容的完整性,平台不提供额外的编辑、内容补充、找答案等附加服务。
- 2、"仅部分预览"的文档,不可在线预览部分如存在完整性等问题,可反馈申请退款(可完整预览的文档不适用该条件!)。
- 3、如文档侵犯您的权益,请联系客服反馈,我们会尽快为您处理(人工客服工作时间:9:00-18:30)。
《机械制造工艺学》课程实验报告
实验名称:加工误差的统计分析
姓名:* * * 班级:机械13**班学号:080113**** 实验日期:2015年10月22 日指导教师:何老师成绩:
1. 实验目的
(1)掌握加工误差统计分析方法的基本原理和应用。
(2)掌握样本数据的采集与处理方法,要求:能正确地采集样本数据,并能通过对样本数据的处理,正确绘制出加工误差的实验分布曲线和图。
(3)能对实验分布曲线和图进行正确地分析,对加工误差的性质、工序能力及工艺稳定性做出准确的鉴别。
(4)培养对加工误差进行综合分析的能力。
2. 实验内容与实验步骤
(一)实验内容:在调整好的无心磨床上连续加工一批同样尺寸的试件,测量其加
工尺寸,对测得的数据进行不同的处理,以巩固机制工艺学课程中所学到的有关加工误差统计分析方法的基本理论知识,并用来分析此工序的加工精度。
(二)原理分析:在实际生产中,为保证加工精度,常常通过对生产现场中实际加
工出的一批工件进行检测,运用数理统计的方法加以处理和分析,从中寻找误差产生的规律,找出提高加工精度的途径。
这就是加工误差统计分析方法。
加工误差分析的方法有两种形式,一种为分布图分析法,另一种为点图分析法。
1.分布图分析法
分布图分析法是通过测量一批加工零件的尺寸,把所测到的尺寸范围分为若干个段。
画出该批零件加工尺寸(或误差)的实验分布图。
其折线图就接近于理论分布曲线。
在没有明显变值系统误差的情况下,即工件的误差是由很多相互独立的微小的随机误差综合作用的结果,则工件尺寸分布符合正态分布。
利用分布曲线图可以比较方便地判断加工误差性质,确定工序能力,并估算合格品率,但利用分布图分析法控制加工精度,必须待一批工件全部加工完毕,测量了样本零件的尺寸后,才能绘制分布图,因此不能在加工过程中及时提供控制精度的信息,这在生产上将是很不方便的。
2.点图法
在生产中常用的另一种误差分析方法是点图法或图法。
点图法是以顺序加工的零件序号为横坐标,零件的加工尺寸为纵坐标,把按加工顺序定期测量的工件尺寸画在点图上。
点图可以反映加工尺寸和时间的关系,可以看出尺寸变化的趋势,找出产生误差的原因。
图称为平均尺寸——极差质量控制图。
一般是在生产过程开始前,先加工一批试件(本实验中即用本批加工的零件作为试件),根据加工所得的尺寸,求出平均值x和极差R而绘制成的。
x 点图:中线 ∑==k
i i x k x 1
1
上控制线 R A x x s 2+= 下控制线 R A x x x 2-=
R 点图:中线 ∑==k
i i R k R 1
1
上控制线 R s = D 1R 下控制线 R x = D 2R
i x 是将一批工件依照加工顺序按n 个分为一组第i 组的平均值,共分成k 组; i R 是第i 组的极差;
式中A 2、D 1、D 2的数值根据数理统计原理而定出(见表1)。
将生产中定期抽样的尺寸结果,点在图上,从点子在图中的位置便可看出x 和R 的波动,它反映了工件平均值的变化趋势和随机误差的分散程度。
图上的控制界限线,就是用来判断工艺是否稳定的界限。
因此图是用来判断工艺过程的稳定性的。
(三)实验步骤:
1. 按无心磨床的操作方法,加工一批零件(本实验为100件)。
加工完的零件,擦
洗干净,按加工顺序放置好。
2. 按加工顺序测量工件的加工尺寸,记录测量结果。
3. 绘制直方图和分布曲线
1)找出这批工件加工尺寸数据的最大值x max 和最小值x min ,按下式计算出极差
R 。
R =x max 一x min
2)确定分组数K (K 一般根据样本容量来选择,建议可选在8~11之间)。
3)按下式计算组距 d 。
4)确定组界(测量单位:微米)。
5)做频数分布表。
6)计算x 和σ。
7)画直方图
以样本数据值为横坐标,标出各组组界;以各组频率密度为纵坐标,画出直方图。
8)画分布曲线
若工艺过程稳定,则误差分布曲线接近正态分布曲线;若工艺过程不稳定,则应根据实际情况确定其分布曲线。
画出分布曲线,注意使分布曲线与直方图协调一致。
9)画公差带
在横轴下方画出公差带,以便与分布曲线相比较。
4. 绘制图
(1) 确定样组容量,对样本进行分组
样组容量m 通常取4或5件。
按样组容量和加工时间顺序,将样本划分成若干个样组。
(2) 计算各样组的平均值和极差
对于第i 个样组,其平均值和极差计算公式为:
∑==m
j ij i x m x 1
1
式
中 i
x ——第i 个样组的平均值;
i
R —
—
第
i
个
样
组
的
标
准
差
;
ij x ——第i 个样组第
j 个零件的测量值;
max i x ——第
i
个样组数据的最大值;
m in i x ——第i 个样组数据的最小值
(3) 计算图控制限(计算公式见实验原理)
(4) 绘制图
以样组序号为横坐标,分别以各样组的平均值和极差R 为纵坐标,画出图,并
在图上标出中心线和上、下控制限。
5.按下式计算工序能力系数Cp
6.判别工艺过程稳定性
可按下表所列标准进行判别。
注意,同时满足表中左列3个条件,工艺过程稳定;表中右列条件之一不满足,即表示工艺过程不稳定。
表2
7.加工误差综合分析
通过对分布图和图的分析,可以初步判断误差的性质。
进而结合具体加工条件,分析影响加工误差的的各种因素,必要时,可对工艺系统的误差环节进行测量和实验。
3. 实验环境
设备:无心磨床
量仪:0~25mm数显千分尺一把
试件:φ24(±0.01)×32的45钢(淬火)100件
4. 实验过程与分析
序号记录数据序号记录数据序号记录数据序号记录数据
1 23.995 26 23.994 51 23.993 76 23.995
2 23.990 27 23.987 52 23.992 77 23.995
3 23.997 28 23.989 53 23.990 78 23.989
4 23.99
5 29 23.995 54 23.992 79 23.995
5 23.998 30 23.997 55 23.992 80 23.995
组 号 组界
中心值 xi
频数 mi 频率 fi xi-x (xi-x )2 (xi-x )
2
mi
1 23.9775—23.979 1 1 -0.0160
0.00025
0.00026
2 23.9805
—23.982
0 0 -0.0130 0.00016
3 23.9835-23.98623.985 5
5 -0.0100 0.0001
0.0005
4 23.9865—23.988 1
5 15 -0.0070 4.9E-05
0.00074
5 23.9895—23.991 35 35 -0.0040 1.6E-05
0.00056
6 23.9925—23.994 21 21 -0.0010 1E-06
0.00002
7 23.9955—23.997 13 13 0.0020 4E-06
0.00005
8 23.9985—24.000 9 9 0.0050 2.5E-05
0.00023
9 24.0015—24.003 0 0 0.0080 6.4E-05
10
24.0045
—24.006
1 1 0.0110 0.00012
0.00012
11 12 13 14 15 16 17 18
2
min
max x x xi -==0.026, n
m x x i
i ∑=
=23.995
n
m x x
i i
∑-=
2)(σ=0.0157
表1-4 实际分布曲线图(直方图)
表1-5 x-R控制图数据
x
组序R
x-R控制图
5. 实验结果总结
1.本工序的实验分布曲线图是否接近正态分布曲线?为什么? 答:本工序的实验分布曲线图接近正态分布曲线
2.根据工序能力系数Cp ,本工序属哪一级?如果出现了废品,试分析产生废品的原因 答:σ=0.0157mm T=0.02mm σ
6T
C p =
=0.1308 所以:工序等级属于四级
工件要求最大尺寸:m ax d =24.01mm ,最小尺寸 min d =23.99mm 可能出现的最大尺寸m ax A =x+3δ=23.995+3*0.0157=24.0421mm 最小尺寸min A =x-3δ=23.995-3*0.0157=23.9479mm
所以m ax A >m ax d 会出现可修复的废品,min A <min d 会出现不可修复废品。
原因:①可修复废品原因:刀具进给量不足 ②不可修复废品原因:进刀量过大
3.从图看,本工序的工艺过程稳定吗?如果不稳定,试分析其原因。
答:从x 图上可以看出,x 点不在中心线x 附近波动,有连续多个的点出现在中心线上侧或下侧,说明分布中心不稳定,有明显的变值系统误差影响; 原因:刀具热变形及刀具尺寸磨损。