轴承加油脂量计算公式
电机轴承温度过高的原因及润滑油加油量
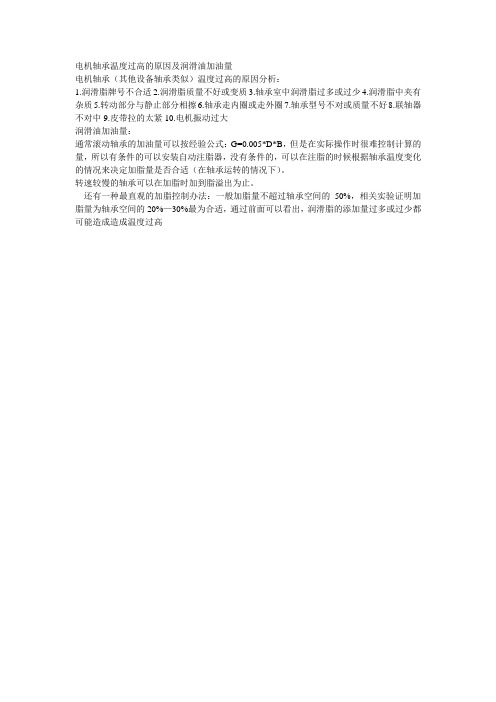
电机轴承温度过高的原因及润滑油加油量
电机轴承(其他设备轴承类似)温度过高的原因分析:
1.润滑脂牌号不合适
2.润滑脂质量不好或变质
3.轴承室中润滑脂过多或过少
4.润滑脂中夹有杂质
5.转动部分与静止部分相擦
6.轴承走内圈或走外圈
7.轴承型号不对或质量不好
8.联轴器不对中
9.皮带拉的太紧10.电机振动过大
润滑油加油量:
通常滚动轴承的加油量可以按经验公式:G=0.005*D*B,但是在实际操作时很难控制计算的量,所以有条件的可以安装自动注脂器,没有条件的,可以在注脂的时候根据轴承温度变化的情况来决定加脂量是否合适(在轴承运转的情况下)。
转速较慢的轴承可以在加脂时加到脂溢出为止。
还有一种最直观的加脂控制办法:一般加脂量不超过轴承空间的50%,相关实验证明加脂量为轴承空间的20%—30%最为合适,通过前面可以看出,润滑脂的添加量过多或过少都可能造成造成温度过高。
滚动轴承摩擦力矩、发热量及油量计算

滚动轴承摩擦力矩、发热量及油润滑所需油量的计算1、轴承的摩擦损失在轴承内部几乎全部变为热量,因而致使轴承温度升高,轴承的发热量可以用以下公式进行计算:Q⋅nM1.05⨯=-410式中Q : 发热量,kWM : 摩擦力矩,N.mmn : 轴承转速,r/min摩擦力矩的估算公式M⋅dP=μ5.0⋅式中M : 摩擦力矩,N.mmμ: 轴承的摩擦系数P : 当量动负荷,N关键点:参见教材“机械设计”P当量动载荷P的计算公式(13-8)。
320教材P338例题13-1有关于当量动载荷的具体计算,但是Fa/Fr的值我个人觉得需要分析轴承的结构,那么就要对轴承选型。
这里希望大家讨论下。
d : 轴承公称内径,mm附表:各类轴承的摩擦系数(参考)2、摩擦力矩的精确计算公式:+=M++MslMdragMsealMrr式中M : 总摩擦力矩, NmmMrr : 滚动摩擦力矩,NmmMsl : 滑动摩擦力矩,NmmMseal : 密封件的摩擦力矩,NmmMdrag: 由于拖曳损失、涡流和飞溅等导致的摩擦力矩,Nmm3、4、循环油润滑及喷油润滑所需油量计算公式Tr c dnP G ∆⋅⋅⋅⨯=-601088.14μ 式中G : 所需油量,L/minμ : 摩擦系数,d : 轴承公称内径,mmn : 轴承转速,r/minP : 轴承当量动负荷,Nc : 油的比热,kJ/kg ℃r : 油的密度,g/cm 3△T : 油的温升,℃上式计算得到的是发热量全部通过油带走时所需的油量,未考虑其余散热因素。
一般来说,实际油量约为以上计算油量的1/2-2/3。
但散热量随着使用机械及使用条件而有所不同,因此宜先以计算油量的2/3进行运转,通过测量轴承温度和进、排油温度逐渐减小油量,直至确定最佳油量。
润滑点需要油量的计算
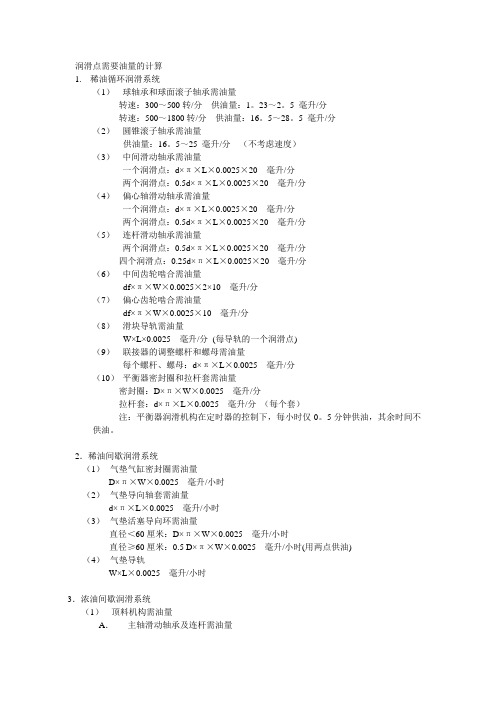
润滑点需要油量的计算1.稀油循环润滑系统(1)球轴承和球面滚子轴承需油量转速:300~500转/分供油量:1。
23~2。
5 毫升/分转速:500~1800转/分供油量:16。
5~28。
5 毫升/分(2)圆锥滚子轴承需油量供油量:16。
5~25 毫升/分(不考虑速度)(3)中间滑动轴承需油量一个润滑点:d×π×L×0.0025×20 毫升/分两个润滑点:0.5d×π×L×0.0025×20 毫升/分(4)偏心轴滑动轴承需油量一个润滑点:d×π×L×0.0025×20 毫升/分两个润滑点:0.5d×π×L×0.0025×20 毫升/分(5)连杆滑动轴承需油量两个润滑点:0.5d×π×L×0.0025×20 毫升/分四个润滑点:0.25d×π×L×0.0025×20 毫升/分(6)中间齿轮啮合需油量df×π×W×0.0025×2×10 毫升/分(7)偏心齿轮啮合需油量df×π×W×0.0025×10 毫升/分(8)滑块导轨需油量W×L×0.0025 毫升/分(每导轨的一个润滑点)(9)联接器的调整螺杆和螺母需油量每个螺杆、螺母:d×π×L×0.0025 毫升/分(10)平衡器密封圈和拉杆套需油量密封圈:D×π×W×0.0025 毫升/分拉杆套:d×π×L×0.0025 毫升/分(每个套)注:平衡器润滑机构在定时器的控制下,每小时仅0。
5分钟供油,其余时间不供油。
2.稀油间歇润滑系统(1)气垫气缸密封圈需油量D×π×W×0.0025 毫升/小时(2)气垫导向轴套需油量d×π×L×0.0025 毫升/小时(3)气垫活塞导向环需油量直径<60厘米:D×π×W×0.0025 毫升/小时直径≥60厘米:0.5 D×π×W×0.0025 毫升/小时(用两点供油) (4)气垫导轨W×L×0.0025 毫升/小时3.浓油间歇润滑系统(1)顶料机构需油量A.主轴滑动轴承及连杆需油量轴承处:d×π×L×0.008 毫升/2小时连杆轴承:0.5 d×π×L×0.008 毫升/2小时(每点)B.滑块导轨需油量W×L×0.008 毫升/2小时(每个导轨)C.凸轮机构需油量D×π×W×0.008 毫升/2小时D.轴套需油量d×π×L×0.008 毫升/2小时(每个套)E.拉杆套或销轴需油量d×π×L×0.008 毫升/2小时(每个润滑点)F.气缸活塞密封处不能用浓油润滑,必须用稀油润滑,油量计算公式同气垫气缸密封圈公式。
轴承的加脂量
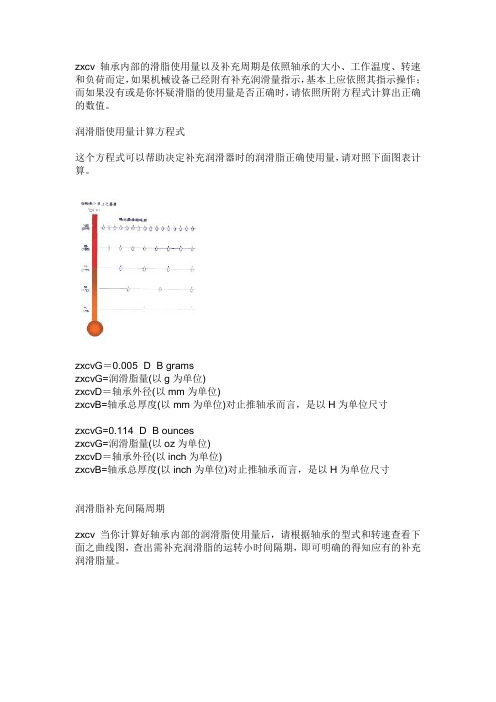
zxcv轴承内部的滑脂使用量以及补充周期是依照轴承的大小、工作温度、转速和负荷而定,如果机械设备已经附有补充润滑量指示,基本上应依照其指示操作;而如果没有或是你怀疑滑脂的使用量是否正确时,请依照所附方程式计算出正确的数值。
润滑脂使用量计算方程式这个方程式可以帮助决定补充润滑器时的润滑脂正确使用量,请对照下面图表计算。
zxcvG=0.005×D×B gramszxcvG=润滑脂量(以g为单位)zxcvD=轴承外径(以mm为单位)zxcvB=轴承总厚度(以mm为单位)对止推轴承而言,是以H为单位尺寸zxcvG=0.114×D×B ounceszxcvG=润滑脂量(以oz为单位)zxcvD=轴承外径(以inch为单位)zxcvB=轴承总厚度(以inch为单位)对止推轴承而言,是以H为单位尺寸润滑脂补充间隔周期zxcv当你计算好轴承内部的润滑脂使用量后,请根据轴承的型式和转速查看下面之曲线图,查出需补充润滑脂的运转小时间隔期,即可明确的得知应有的补充润滑脂量。
zxcvG÷运转小时=_______g/每小时「注意」zxcv左上曲线图之补充润滑脂的运转小时间隔期,只适用于一般负荷况且正常的轴承,当有以下情况时必须调整注脂时间周期:1.运转温度达70℃以上时,每升高15℃就必须加倍补充润滑脂量。
2.轴承会受到污染时,如尘土、水汽、酸碱环境等也必须加倍补充润滑脂量。
3.轴承负荷属于重载时,如震动、加压等也必须加倍补充润滑脂量。
● 假使运转条件同时具有以上状况时,则必须加倍再加倍的补给新鲜滑脂,以确保润滑品质。
正确的新陈代谢更新润滑脂zxcv如下图所示:轴承内部应保有适当的只有空间,让轴承在起动运转时可以将多余的润滑脂甩出,而且润滑脂的寿命是有限度的,如果能够经常的补充新鲜的润滑脂让已经被污染的润滑脂新陈代谢出来,则轴承可以发挥至最佳品质以及寿命。
滑动轴承的润滑油量

滑动轴承的润滑油量
液体动压和静压轴承的给油量,可参阅有关书籍及文献中的计算公式。
因为不同的轴承结构参数、工作条件其供油量也不同。
在普通滑动轴承的间隙中保持的油量为
γπL d D Q 4
)
(22-=
,g
式中γ——润滑油的密度(γ=0.9g /cm 3
);
D ——轴承孔的直径,cm d ——轴颈的直径,cm L ——轴承长度,cm 。
人工加油、滴油和线芯润滑的滑动轴承的耗油量,主要根据轴颈直径、转速、轴承长度
L 和轴颈直径d 的比值而定。
当专
d L =l 时,每班(8h)的耗油量可参见表1。
若d L
≠1时,则耗油量应将表上所查得数值再乘上d
L
的实际数值。
油绳油杯根据油线厚度不同其供油能力可参考表2。
采用油环润滑的滑动轴承,根据轴颈直径及油槽容积来确定其耗油量和加油量,可参考表3。
表3 滑动轴承油环润滑的耗油量
针阀油杯(GB1159—74)最小流量为每分钟不超过5滴。
如果观察到轴承流出来的油量非常少,说明供油量不足。
将会造成轴承温度上升,加剧轴颈和轴瓦的磨损。
因此要适当加大给油量;若流出的油都是新油,则说明给油量太多,这样又会造成浪费。
采用循环给油时的供油量,对于高速机械(例如涡轮鼓风机、高速电动机的轴承等)可由经验公式
Q=(0.06~0.15)DL, L/min
式中Q——给油量,L/min;
D——轴承孔直径,cm;
L——轴承长度,cm。
对于低速机械
Q=(0.003~0.006)DL, L/min。
润滑点需要油量的计算
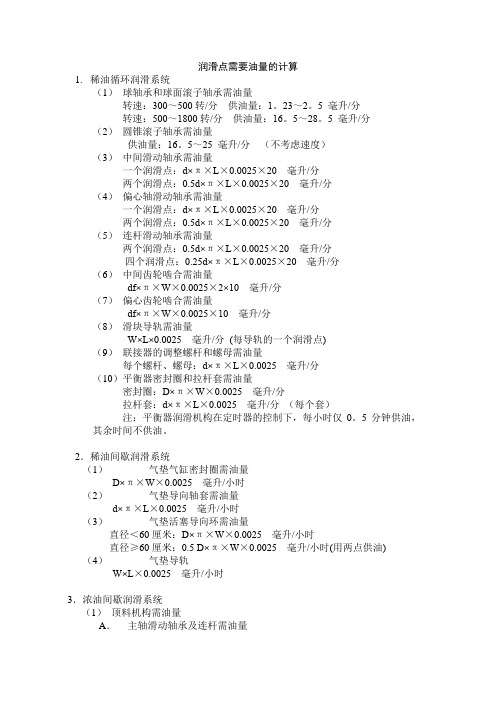
(4)偏心轴滑动轴承需油量
一个润滑点:d×π×L×0.0025×20毫升/分
两个润滑点:0.5d×π×L×0.0025×20毫升/分
(5)连杆滑动Байду номын сангаас承需油量
两个润滑点:0.5d×π×L×0.0025×20毫升/分
四个润滑点:0.25d×π×L×0.0025×20毫升/分
(6)中间齿轮啮合需油量
df×π×W×0.0025×2×10毫升/分
(7)偏心齿轮啮合需油量
df×π×W×0.0025×10毫升/分
(8)滑块导轨需油量
W×L×0.0025毫升/分(每导轨的一个润滑点)
(9)联接器的调整螺杆和螺母需油量
每个螺杆、螺母:d×π×L×0.0025毫升/分
(10)平衡器密封圈和拉杆套需油量
(3)气垫活塞导向环需油量
直径<60厘米:D×π×W×0.0025毫升/小时
直径≥60厘米:0.5 D×π×W×0.0025毫升/小时(用两点供油)
(4)气垫导轨
W×L×0.0025毫升/小时
3.浓油间歇润滑系统
(1)顶料机构需油量
A.主轴滑动轴承及连杆需油量
轴承处:d×π×L×0.008毫升/2小时
F.气缸活塞密封处不能用浓油润滑,必须用稀油润滑,油量计算公式同气垫气缸密封圈公式。
(2)内滑块导轨、气垫导轨需油量
计算公式同顶料机构滑块导轨计算公式。
4.油量计算公式的规定说明
d—内径(轴承、轴套、螺母等)厘米
D—外径(密封圈、凸轮、导向环等)厘米
df—齿轮分度圆厘米
L—长度(轴承、轴套、导轨等)厘米
密封圈:D×π×W×0.0025毫升/分
滑动轴承的润滑油量

滑动轴承的润滑油量
液体动压和静压轴承的给油量,可参阅有关书籍及文献中的计算公式。
因为不同的轴承结构参数、工作条件其供油量也不同。
在普通滑动轴承的间隙中保持的油量为
γπL d D Q 4
)
(22-=
,g
式中γ——润滑油的密度(γ=0.9g /cm 3
);
D ——轴承孔的直径,cm d ——轴颈的直径,cm L ——轴承长度,cm 。
人工加油、滴油和线芯润滑的滑动轴承的耗油量,主要根据轴颈直径、转速、轴承长度
L 和轴颈直径d 的比值而定。
当专
d L =l 时,每班(8h)的耗油量可参见表1。
若d L
≠1时,则耗油量应将表上所查得数值再乘上d
L
的实际数值。
油绳油杯根据油线厚度不同其供油能力可参考表2。
采用油环润滑的滑动轴承,根据轴颈直径及油槽容积来确定其耗油量和加油量,可参考表3。
表3 滑动轴承油环润滑的耗油量
针阀油杯(GB1159—74)最小流量为每分钟不超过5滴。
如果观察到轴承流出来的油量非常少,说明供油量不足。
将会造成轴承温度上升,加剧轴颈和轴瓦的磨损。
因此要适当加大给油量;若流出的油都是新油,则说明给油量太多,这样又会造成浪费。
采用循环给油时的供油量,对于高速机械(例如涡轮鼓风机、高速电动机的轴承等)可由经验公式
Q=(0.06~0.15)DL, L/min
式中Q——给油量,L/min;
D——轴承孔直径,cm;
L——轴承长度,cm。
对于低速机械
Q=(0.003~0.006)DL, L/min。
skf发电机轴承润滑油量计算
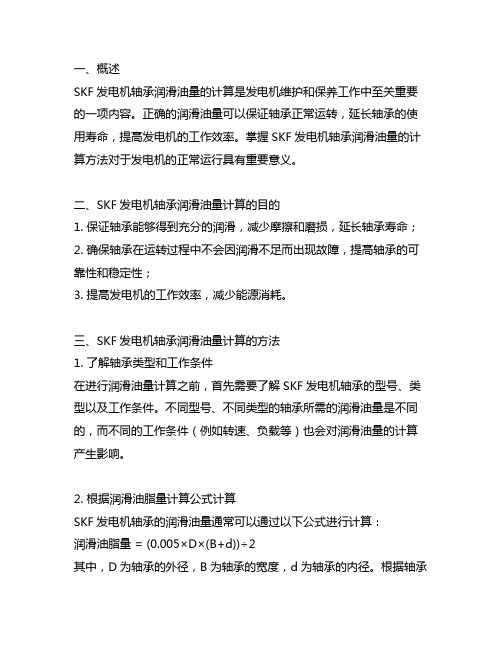
一、概述SKF发电机轴承润滑油量的计算是发电机维护和保养工作中至关重要的一项内容。
正确的润滑油量可以保证轴承正常运转,延长轴承的使用寿命,提高发电机的工作效率。
掌握SKF发电机轴承润滑油量的计算方法对于发电机的正常运行具有重要意义。
二、SKF发电机轴承润滑油量计算的目的1. 保证轴承能够得到充分的润滑,减少摩擦和磨损,延长轴承寿命;2. 确保轴承在运转过程中不会因润滑不足而出现故障,提高轴承的可靠性和稳定性;3. 提高发电机的工作效率,减少能源消耗。
三、SKF发电机轴承润滑油量计算的方法1. 了解轴承类型和工作条件在进行润滑油量计算之前,首先需要了解SKF发电机轴承的型号、类型以及工作条件。
不同型号、不同类型的轴承所需的润滑油量是不同的,而不同的工作条件(例如转速、负载等)也会对润滑油量的计算产生影响。
2. 根据润滑油脂量计算公式计算SKF发电机轴承的润滑油量通常可以通过以下公式进行计算:润滑油脂量= (0.005×D×(B+d))÷2其中,D为轴承的外径,B为轴承的宽度,d为轴承的内径。
根据轴承的尺寸数据,可以利用该公式计算出润滑油脂的量。
3. 结合实际工作条件进行调整在使用上述公式计算出润滑油脂量后,还需要根据实际的工作条件进行适当的调整。
在高速运转或者重负载工况下,需要增加润滑油脂的量;而在低速运转或者轻负载工况下,可以适当减少润滑油脂的量。
四、SKF发电机轴承润滑油量计算的注意事项1. 确保使用适当的润滑油脂在进行润滑油量计算时,需要选择适合的润滑油脂。
不同型号的轴承可能需要使用不同型号的润滑油脂,而且在不同工作条件下,润滑油脂的选择也会有所差异。
2. 注意润滑油脂的加注方法在确定了润滑油脂的量之后,需要注意润滑油脂的加注方法。
通常情况下,润滑油脂可以通过手动或者自动润滑系统进行加注,确保润滑油脂的均匀分布,以达到最佳的润滑效果。
3. 定期检查润滑油脂的情况润滑油脂的质量会随着使用时间的增加而逐渐下降,因此需要定期对润滑油脂进行检查和更换。
- 1、下载文档前请自行甄别文档内容的完整性,平台不提供额外的编辑、内容补充、找答案等附加服务。
- 2、"仅部分预览"的文档,不可在线预览部分如存在完整性等问题,可反馈申请退款(可完整预览的文档不适用该条件!)。
- 3、如文档侵犯您的权益,请联系客服反馈,我们会尽快为您处理(人工客服工作时间:9:00-18:30)。
轴承加油脂量计算公式:
按轴承外径和宽度估算填充量的公式:Q=0.005*D*B。
按轴承内径估算填充量的公式:Q=0.01*d*B。
轴承第二次加脂量的估计公式:Q=0.005*d*B。
高速轴承填充量的估算公式:Q=0.001*K*d.*B。
Q -- 润滑脂填充量,cm3。
K-- 轴承尺寸系数。
d -- 轴承内径,mm。
D -- 轴承外径,mm。
d.-- 轴承平均直径,d.=0.5(D+d),mm。
B -- 轴承宽度,mm。
轴承(Bearing)是当代机械设备中一种重要零部件。
它的主要功能是支撑机械旋转体,降低其运动过程中的摩擦系数(friction coefficient),并保证其回转精度(accuracy)。
按运动元件摩擦性质的不同,轴承可分为滚动轴承和滑动轴承两大类。
其中滚动轴承已经标准化、系列化,但与滑动轴承相比它的径向尺寸、振动和噪声较大,价格也较高。
滚动轴承一般由外圈、内圈、滚动体和保持架四部分组成,严格的说是由外圈、内圈、滚动体、保持架、密封、润滑油六大件组成。
主要具备外圈、内圈、滚动体就可定意为滚动轴承。
按滚动体的形状,滚动轴承分为球轴承和滚子轴承两大类。
根据轴承类型,添加油脂。
加脂量过大,会使摩擦力矩增大,温度升高,漏油污染环境,耗脂量增大;而加脂量过少,则不能获得可靠润滑而发生干摩擦。
一般来讲,适宜的加脂量为轴承内总空隙体积的:
零类轴承25%——40%;
精密轴承15%——25%
是指空间的百分比
【下载本文档,可以自由复制内容或自由编辑修改内容,更多精彩文章,期待你的好评和关注,我将一如既往为您服务】。