轴承的计算公式
轴承压轴力计算公式

轴承压轴力计算公式轴承是机械设备中常用的零部件,用于支撑旋转机械零件的轴。
在轴承工作时,会受到来自旋转部件的轴向力的作用。
因此,对于轴承来说,计算轴向力是非常重要的。
本文将介绍轴承压轴力的计算公式及其应用。
轴承压轴力是指轴承在工作时所受到的轴向力。
在实际工程中,需要计算轴承压轴力,以确定轴承的选型和轴承座的设计。
轴承压轴力的计算公式如下:F = C0 × (Y × Fr + Y0 × Fa)。
其中,F为轴承压轴力,单位为N;C0为轴承的基本静载荷,单位为N;Y为轴承系数,取值范围一般为0.5-0.8;Fr为轴承的径向力,单位为N;Fa为轴承的轴向力,单位为N;Y0为轴承系数,取值范围一般为0.6-1.0。
在实际工程中,轴承的选型和轴承座的设计需要根据实际工况来确定。
在计算轴承压轴力时,需要考虑轴承所受的径向力和轴向力。
通常情况下,径向力是由旋转部件在轴向上的惯性力和离心力引起的,而轴向力则是由机械装置的工作负荷引起的。
因此,在计算轴承压轴力时,需要分别考虑这两种力的作用。
对于径向力Fr,可以通过以下公式进行计算:Fr = m × r ×ω^2。
其中,m为旋转部件的质量,单位为kg;r为旋转部件的半径,单位为m;ω为旋转部件的角速度,单位为rad/s。
对于轴向力Fa,可以通过以下公式进行计算:Fa = P ×η。
其中,P为机械装置的工作负荷,单位为N;η为机械装置的传动效率,取值范围一般为0.8-0.95。
通过上述公式,可以计算出轴承所受的径向力和轴向力,进而计算出轴承的压轴力。
在实际工程中,需要根据轴承所受的压轴力来选择合适的轴承型号和轴承座设计,以确保轴承能够正常工作并具有足够的寿命。
除了上述的计算公式,轴承压轴力的计算还需要考虑一些其他因素,如轴承的工作温度、润滑情况、安装方式等。
这些因素都会对轴承的压轴力产生影响,因此在实际工程中需要综合考虑这些因素,以确定轴承的选型和轴承座的设计。
导向轴承受力计算公式
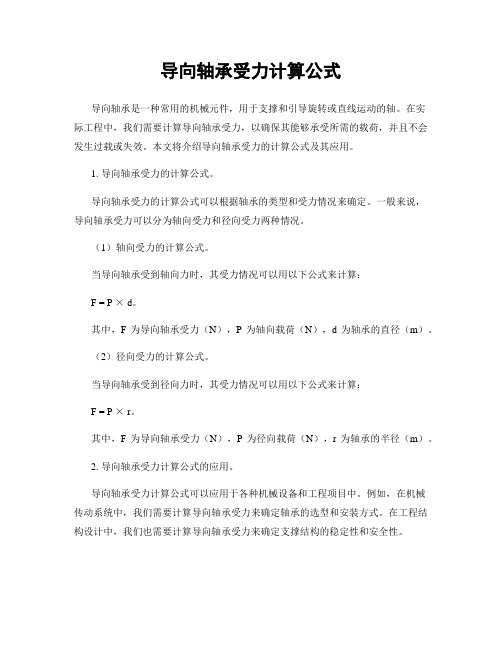
导向轴承受力计算公式导向轴承是一种常用的机械元件,用于支撑和引导旋转或直线运动的轴。
在实际工程中,我们需要计算导向轴承受力,以确保其能够承受所需的载荷,并且不会发生过载或失效。
本文将介绍导向轴承受力的计算公式及其应用。
1. 导向轴承受力的计算公式。
导向轴承受力的计算公式可以根据轴承的类型和受力情况来确定。
一般来说,导向轴承受力可以分为轴向受力和径向受力两种情况。
(1)轴向受力的计算公式。
当导向轴承受到轴向力时,其受力情况可以用以下公式来计算:F = P × d。
其中,F为导向轴承受力(N),P为轴向载荷(N),d为轴承的直径(m)。
(2)径向受力的计算公式。
当导向轴承受到径向力时,其受力情况可以用以下公式来计算:F = P × r。
其中,F为导向轴承受力(N),P为径向载荷(N),r为轴承的半径(m)。
2. 导向轴承受力计算公式的应用。
导向轴承受力计算公式可以应用于各种机械设备和工程项目中。
例如,在机械传动系统中,我们需要计算导向轴承受力来确定轴承的选型和安装方式。
在工程结构设计中,我们也需要计算导向轴承受力来确定支撑结构的稳定性和安全性。
在实际应用中,我们需要根据具体的受力情况和轴承类型来选择合适的计算公式,并进行详细的计算和分析。
同时,我们还需要考虑轴承的材料、制造工艺、润滑方式等因素,以确保导向轴承能够可靠地工作并具有足够的寿命。
3. 导向轴承受力计算的注意事项。
在进行导向轴承受力计算时,我们需要注意以下几个方面:(1)考虑受力情况,根据具体的工程情况和受力要求,选择合适的受力计算公式,并考虑轴承受力的方向和大小。
(2)考虑轴承类型,不同类型的导向轴承受力计算公式有所不同,需要根据轴承的类型和结构特点进行选择。
(3)考虑工作环境,在进行受力计算时,需要考虑导向轴承所处的工作环境和工作条件,如温度、湿度、振动等因素。
(4)考虑安全性和可靠性,在进行受力计算时,需要确保导向轴承具有足够的安全性和可靠性,以避免发生过载或失效的情况。
轴承的计算公式.
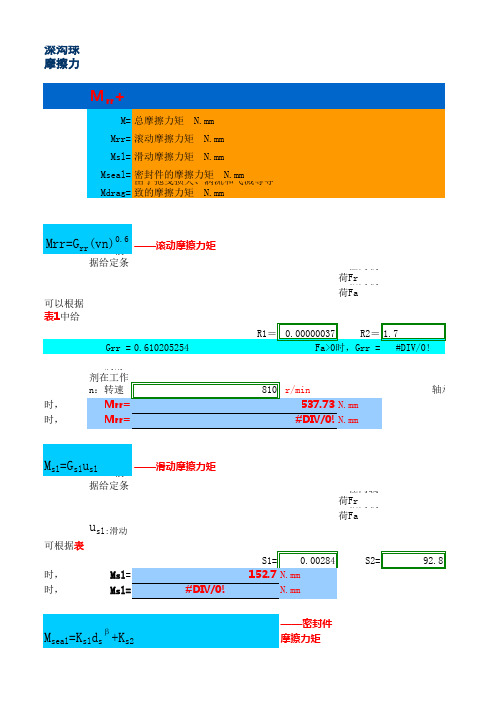
NR=
242.19713 W
Fa=0时
NR=
如果冷却系数(指轴承与环境温度之间每一度温差所带走的热量)是已知数,则可用以下公式粗略估算轴
∆T=N_R/W_s
∆T:温升 ℃
N_R:功率损耗 W
W_S:冷却系数
20
Δ T=
12.10986 ℃ Fa=0时
Δ T=
管方向,只取正值
10000 N 0N
117.5 mm
深沟球摩擦力矩的准确计算,要考虑四个不同导致摩擦的因素:
M=Mrr+Msl+Mseal+Mdrag
M= 总摩擦力矩 N.mm Mrr= 滚动摩擦力矩 N.mm Msl= 滑动摩擦力矩 N.mm Mseal= 密封件的摩擦力矩 N.mm Mdrag= 由于拖曳损失、涡流和飞溅等导致的摩擦力矩 N.mm
轴承额定动载荷C0=
100 mm2/s 76500 N
10000 N 0N
油);0.1(以传动液润滑)
摩擦系数Usl:
0.04
2.25 2
0.00017
1
列球轴承常数:
3.1
75
160
滚动摩擦的切入发热和贫油回填效应的
.28 v^0.64 )
油回填常数,脂润滑为: 0.00000006
2847.70 N.mm #DIV/0! N.mm
轴向载荷Fa
usl:滑动摩擦系数,当润滑条件良好,可取以下值:0.05(矿物油);0.04(合成油);0.1(以传动液润滑)
Gsl的值可根据表1中给出的公式计算,几何常数S则可从表2中找到
当Fa=0时, Msl=
S1= 0.00284
S2=
152.7 N.mm
轴承外径锥度如何计算公式

轴承外径锥度如何计算公式在机械制造和工程设计中,轴承是一种常见的零部件,用于支撑旋转机械元件。
轴承外径锥度是轴承的一个重要参数,它影响着轴承的安装和使用。
本文将介绍轴承外径锥度的计算公式,帮助读者更好地理解和应用这一参数。
轴承外径锥度的定义。
轴承外径锥度是指轴承外圈的圆锥度,通常用于描述轴承外圈的变形程度。
轴承外径锥度的大小直接影响着轴承的安装和使用,过大或过小的锥度都会导致轴承的不良运行。
因此,准确计算轴承外径锥度是非常重要的。
轴承外径锥度的计算公式。
轴承外径锥度的计算公式如下:ΔD = (Dmax Dmin) / Dmax。
其中,ΔD表示轴承外径锥度,Dmax表示轴承外径的最大值,Dmin表示轴承外径的最小值。
在实际应用中,轴承外径的最大值和最小值可以通过测量得到。
通常情况下,轴承外径的最大值是指轴承外圈的最大直径,轴承外径的最小值是指轴承外圈的最小直径。
通过测量这两个数值,就可以得到轴承外径锥度的具体数值。
轴承外径锥度的意义。
轴承外径锥度的大小对轴承的安装和使用都有着重要的影响。
如果轴承外径锥度过大,会导致轴承在安装时无法正确对中,从而影响轴承的旋转精度和稳定性。
另外,过大的锥度也会导致轴承在使用过程中产生过大的热量,加速轴承的磨损和损坏。
相反,如果轴承外径锥度过小,会导致轴承在安装时容易产生过大的压力,从而影响轴承的使用寿命和稳定性。
此外,过小的锥度也会导致轴承在使用过程中产生过大的摩擦力,增加轴承的能耗和磨损。
因此,合理计算和控制轴承外径锥度是非常重要的。
只有在合适的范围内,轴承外径锥度才能够保证轴承的正常运行和长期稳定性。
轴承外径锥度的测量方法。
为了准确计算轴承外径锥度,需要采用合适的测量方法。
一般来说,可以通过以下步骤来测量轴承外径锥度:1. 使用外径千分尺或外径测微仪等工具,测量轴承外径的最大值和最小值。
2. 将测量得到的最大值和最小值代入轴承外径锥度的计算公式中,即可得到轴承外径锥度的具体数值。
轴承设计寿命计算公式汇总
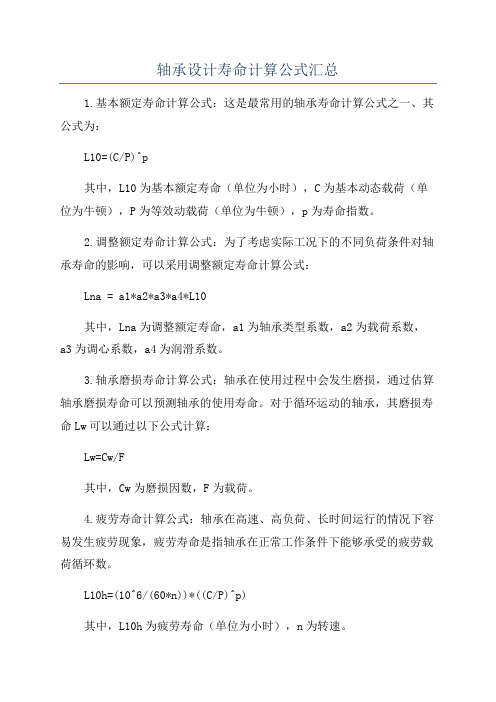
轴承设计寿命计算公式汇总
1.基本额定寿命计算公式:这是最常用的轴承寿命计算公式之一、其公式为:
L10=(C/P)^p
其中,L10为基本额定寿命(单位为小时),C为基本动态载荷(单位为牛顿),P为等效动载荷(单位为牛顿),p为寿命指数。
2.调整额定寿命计算公式:为了考虑实际工况下的不同负荷条件对轴承寿命的影响,可以采用调整额定寿命计算公式:
Lna = a1*a2*a3*a4*L10
其中,Lna为调整额定寿命,a1为轴承类型系数,a2为载荷系数,a3为调心系数,a4为润滑系数。
3.轴承磨损寿命计算公式:轴承在使用过程中会发生磨损,通过估算轴承磨损寿命可以预测轴承的使用寿命。
对于循环运动的轴承,其磨损寿命Lw可以通过以下公式计算:
Lw=Cw/F
其中,Cw为磨损因数,F为载荷。
4.疲劳寿命计算公式:轴承在高速、高负荷、长时间运行的情况下容易发生疲劳现象,疲劳寿命是指轴承在正常工作条件下能够承受的疲劳载荷循环数。
L10h=(10^6/(60*n))*((C/P)^p)
其中,L10h为疲劳寿命(单位为小时),n为转速。
5.温度因子计算公式:轴承在工作时会产生热量,可以通过计算温度因子来估算轴承的使用寿命。
温度因子aISO可以通过以下公式计算:aISO=a*〖10(ΔT/10)〗^b
其中,a、b为轴承类型参数,ΔT为温度变化。
以上是一些常用的轴承设计寿命计算公式汇总。
需要注意的是,不同类型的轴承有不同的设计寿命计算公式,具体应根据实际情况选择合适的计算方法。
此外,在进行寿命计算时还需要考虑轴承材料、润滑方式、工作温度等因素对轴承寿命的影响。
轴承轴向载荷计算公式

轴承轴向载荷计算公式
轴承是一种用于支撑机械旋转部件的重要元件。
在实际应用中,轴承通常承受着来自旋转部件的各种载荷,其中包括轴向载荷。
轴向载荷是指垂直于轴心线方向的力或压力,其作用方向与轴的轴向相同或相反。
轴向载荷的计算对于正确选择合适的轴承和确保轴承工作正常非常重要。
以下是常用的轴向载荷计算公式:
1. 线性轴承的轴向载荷计算公式:
轴向载荷 = 1/2 * (F1 + F2)
其中,F1和F2分别为轴承所受外力的大小,取正负号表示方向。
2. 圆柱滚子轴承的轴向载荷计算公式:
轴向载荷 = (F1 + F2) / 2
其中,F1和F2分别为轴承所受外力的大小,取正负号表示方向。
3. 锥形滚子轴承的轴向载荷计算公式:
轴向载荷= (F1 + F2) / 2 * cosα
其中,F1和F2分别为轴承所受外力的大小,取正负号表示方向;α为锥面与轴线的夹角。
4. 推力球轴承的轴向载荷计算公式:
轴向载荷 = F
其中,F为轴承所受外力的大小,取正负号表示方向。
需要注意的是,在实际应用中,轴向载荷不仅仅是由外力引起的,还可能由于转子离心力、温度变化等因素而产生。
因此,需要综合考虑这些因素对轴向载荷的影响,进行准确的计算。
在进行轴向载荷计算时,还需要考虑其他一些因素,如轴承的额定载荷、轴承的径向载荷等。
同时,还要根据具体的工况条件和设计要求,选择合适的轴承类型和规格。
轴向载荷的计算是轴承设计中非常重要的一部分。
通过合理计算和选择,可以确保轴承工作正常,并提高设备的安全性和可靠性。
轴承转速计算公式及方法
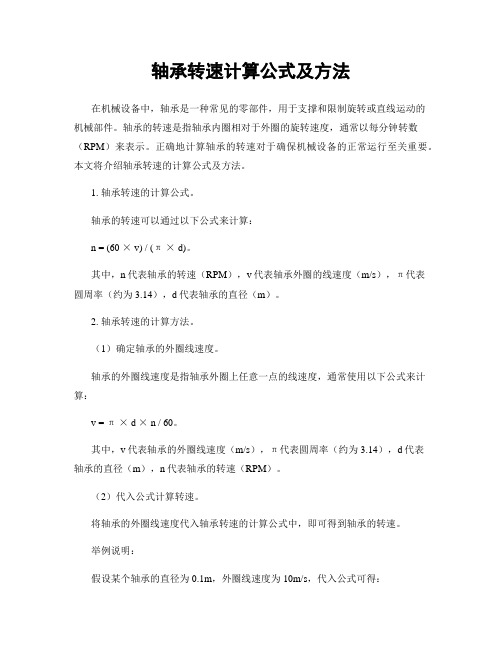
轴承转速计算公式及方法在机械设备中,轴承是一种常见的零部件,用于支撑和限制旋转或直线运动的机械部件。
轴承的转速是指轴承内圈相对于外圈的旋转速度,通常以每分钟转数(RPM)来表示。
正确地计算轴承的转速对于确保机械设备的正常运行至关重要。
本文将介绍轴承转速的计算公式及方法。
1. 轴承转速的计算公式。
轴承的转速可以通过以下公式来计算:n = (60 × v) / (π× d)。
其中,n代表轴承的转速(RPM),v代表轴承外圈的线速度(m/s),π代表圆周率(约为3.14),d代表轴承的直径(m)。
2. 轴承转速的计算方法。
(1)确定轴承的外圈线速度。
轴承的外圈线速度是指轴承外圈上任意一点的线速度,通常使用以下公式来计算:v = π× d × n / 60。
其中,v代表轴承的外圈线速度(m/s),π代表圆周率(约为3.14),d代表轴承的直径(m),n代表轴承的转速(RPM)。
(2)代入公式计算转速。
将轴承的外圈线速度代入轴承转速的计算公式中,即可得到轴承的转速。
举例说明:假设某个轴承的直径为0.1m,外圈线速度为10m/s,代入公式可得:n = (60 × 10) / (3.14 × 0.1) = 1910 RPM。
因此,该轴承的转速为1910 RPM。
3. 注意事项。
在进行轴承转速的计算时,需要注意以下几点:(1)确保使用正确的单位,在进行计算时,需要使用统一的单位,通常使用国际单位制(SI单位制)来进行计算。
(2)考虑轴承的额定转速,轴承通常会有一个额定转速,超过这个转速可能会导致轴承损坏,因此在计算轴承转速时需要考虑轴承的额定转速。
(3)考虑轴承的工作环境,在实际应用中,轴承的工作环境会对其转速产生影响,例如温度、润滑情况等因素都会对轴承的转速产生影响,因此需要根据实际情况进行适当的修正。
4. 结语。
轴承的转速是保证机械设备正常运行的重要参数,正确地计算轴承的转速对于确保机械设备的正常运行至关重要。
轴承内孔计算方法
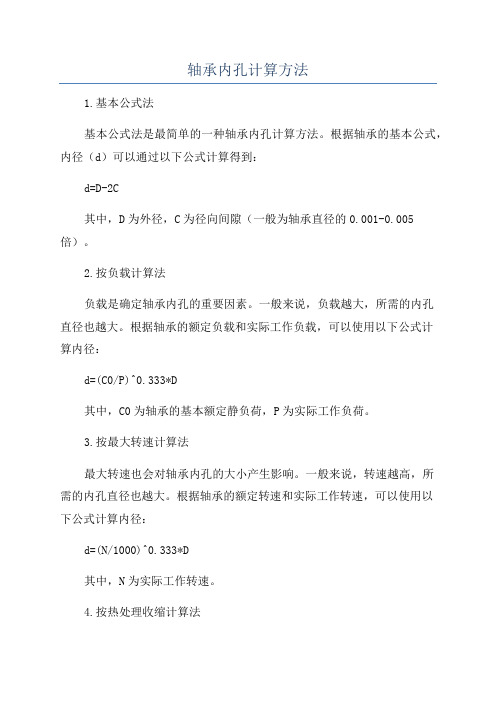
轴承内孔计算方法
1.基本公式法
基本公式法是最简单的一种轴承内孔计算方法。
根据轴承的基本公式,内径(d)可以通过以下公式计算得到:
d=D-2C
其中,D为外径,C为径向间隙(一般为轴承直径的0.001-0.005倍)。
2.按负载计算法
负载是确定轴承内孔的重要因素。
一般来说,负载越大,所需的内孔
直径也越大。
根据轴承的额定负载和实际工作负载,可以使用以下公式计
算内径:
d=(C0/P)^0.333*D
其中,C0为轴承的基本额定静负荷,P为实际工作负荷。
3.按最大转速计算法
最大转速也会对轴承内孔的大小产生影响。
一般来说,转速越高,所
需的内孔直径也越大。
根据轴承的额定转速和实际工作转速,可以使用以
下公式计算内径:
d=(N/1000)^0.333*D
其中,N为实际工作转速。
4.按热处理收缩计算法
热处理是一种可以改变轴承尺寸的方法。
通过对轴承进行热处理,可以收缩外径和内径。
根据热处理的情况,可以使用以下公式计算内径:d=D-2δ
其中,δ为根据热处理温度和材料系数计算的收缩量。
5.按轴承类型计算法
不同类型的轴承具有不同的计算方法。
例如,圆锥滚子轴承的内径计算方法与深沟球轴承不同。
根据具体轴承的类型,可以采用相应的计算方法进行计算。
总结:。
- 1、下载文档前请自行甄别文档内容的完整性,平台不提供额外的编辑、内容补充、找答案等附加服务。
- 2、"仅部分预览"的文档,不可在线预览部分如存在完整性等问题,可反馈申请退款(可完整预览的文档不适用该条件!)。
- 3、如文档侵犯您的权益,请联系客服反馈,我们会尽快为您处理(人工客服工作时间:9:00-18:30)。
M= Mrr+
M= 总摩擦力矩 N.mm
Mrr= 滚动摩擦力矩 N.mm
Msl= 滑动摩擦力矩 N.mm
Mseal= 密由封于件拖的曳摩损擦失力、矩 涡流和N.飞mm溅等导 Mdrag= 致的摩擦力矩 N.mm
Mrr=Grr(Grvrn:)根0.6 ——滚动摩擦力矩
据给定条
Grr的值 可以根据 表1中给
10000 N 0N
摩擦系数Usl:
0.04
2.25 2
0.00017
1 3.1
75 160
滚动摩擦的切入发热和贫油回填效应的
.28 v^0.64 )
0.00000006
2847.70 N.mm #DIV/0! N.mm
Fa=0时 Fa>0时
W Fa〉0
#DIV/0! 时
111
#DIV/0!
℃ Fa〉0 时
21.41 N.mm
iKzr=w=单球列
和d=双轴列承球 内D=径轴尺承 外径尺
在新的摩擦模型中引入了减少系数 和 ,分别用来考虑滚动摩擦的切入发
切影入响发:热
∅_ish ∅_rs
减少系
数:——
∅_ish=1/(1+1.84×〖10〗^(-9) 〖(n d_m )〗^1.28 v^0.64 )
0.923646
贫油回填 减少系 数:——
∅_rs=1/(e^(K_rs vn(d+D)) √(K_z/(2(D-d))))
3.663692474
贫油回填常
Krs= 数,脂润滑
将以上的 其它效应
=
功率 损M耗=∅_ish ∅_rs
因轴承的 摩擦而造
如果冷却 系数(指
NNR_=R功=1率.0损5×耗〖1W0〗^(-4) M n
Ksl:根 据ds轴:承轴类承 肩β部:直根据 轴Ks承2:和根密 据轴承和
需轴承厂商提供:
0.028 98.3
Mseal=
Mdrag=VmVmK:ba拖ll曳dm5 n2
损失变 Kball:球 轴承常
Mdrag=
853.93 N.mm
——拖曳导 致的摩擦力 矩
Vm=
K_ball=(i_rw K_z (d+D))/(D-d)×〖10〗^(-12)
当Fa=0 时当,Fa>0 时,
Fa=0时, Grr = 0.610205254
v:润滑 剂在工作 n:转速
Mrr= Mrr=
径向载 荷F轴r向载2= 1.7 Fa>0时,Grr = #DIV/0!
810 r/min 537.73 N.mm
#DIV/0! N.mm
轴承额定动载荷
Msl=GsluGslsl:根 ——滑动摩擦力矩
据给定条
Gsl的值 usl:滑动
可根据表
当Fa=0 时当,Fa>0 时,
Msl= Msl=
#DIV/0!
径向载 荷F轴r向载 荷Fa
S1= 0.00284
S2=
152.7 N.mm
N.mm
92.8
Mseal=Ksldsβ+Ks2
——密封件 摩擦力矩
M=轴承的总摩擦力矩 N.mm
n=转速 r/min
NR=
242.19713 W
Fa=0时
∆T=N_R/W_s
∆T:温升 ℃
N_R:功率损耗 W
W_S:冷却系数
20
ΔT=
12.10986 ℃ Fa=0时
NR= ΔT=
10000 N 0N
117.5 mm
轴承额定动载荷C0=
100 mm2/s 76500 N