设计FMEA探测度评价表
设计FMEA检查表

编制部门:产品发展科
设计FMEA检 查 表
编制日期:
产品名称
球头拉杆机械/动力
图号
顾客原图号
接头总成右/左
问题
是
否
负责部门/
负责人
完成日期
1
是否使用了克莱斯勒、福特和通用汽车公司潜在的失效模式及后果分析(FMEA) 参考手册来制定SFMEA和/或DFMEA?
√
2
是否已对过去已发生事件和保修数据进行评审?
√
3
是否 已 考 虑 了 类 似 的 零 件DFMEAs?
√
4SFMEA和/或DFra bibliotekMEA是否识别了特殊特性?
√
目前 公 司 没 有 做SFMEA
5
是否已确认了影响风险最先失效模式的设计特性?
√
6
对高风险顺序数项目是否已确定了适当的纠正措施?
√
7
对严重度数高的项目是否已确定了适当的纠正措施?
√
8
当纠正措施实施完成并经验证后,高风险顺序数是否已得到修正?
√
核 准
审查
制表
20XX.10.10
2019FMEA5th严重度频度探测度评价

产品经验:在公司内使用产品的历史(新品设计、应用或使用案例)。已经完成的探测控制结果提供了设计经验。
预防控制:在产品设计中使用最佳实践、设计规则、公司标准、经验教训、行业标准、材料规范、政府规定,以及以预防为导向的分析工具的有效性(分析工具包括计算机辅助工程、数学建模、模拟研究、公差叠加和设计安全边际)。
或,100%的产品需要返工,但可以在生产线外进行,不需要停生产线
4
低
装配和外观等项目不符合要求,大多数顾客发现有缺陷(≥75%)
或,产品可能必须要筛选,产品经筛选,部分(少于100%)需要返工,产品没有被报废
3
装配和外观等项目不符合要求,有50%左右的顾客发现有缺陷
或,部分(少于100%)产品可能必须在生产线上的工序外返工,产品没有被报废
低-非常低
7-10
M
中
5-6
M
高
2-4
L
非常高
1
L
高
6-7
低-非常低
7-10
L
中
5-6
L
高
2-4
L
非常高
1
L
中
4-5
低-非常低
7-10
L
中
5-6
L
高
2-4
L
非常高
1
L
低
2-3
低-非常低
7-10
L
中
5-6
L
高
2-4
L
非常高
1
L
非常低
1
非常高-非常低
1-10
L
没有可觉察到的影响
1
非常低
1-10
非常高-非常低
2
非常低
新版标准FMEA表格(D+P)

备注
621L
2.关注要素的失效 模式(FM)
失效影响的严重度(S)
车窗升降电机的扭矩和转动速度过低
换向系统的角度偏差导
6
致间歇性错误连接线圈 (L1、L3和L2,而不是
L1、L2和L3)
由公司确定 DFMEA所有者的姓名 商业使用、专有、保密
)
DFMEA风险分析(步骤五)
对失效起
3.下一较低级要素或特性的 因的当前
2
试:依据 测试规范 MRJ82/60 测量电刷 盒的弹性 和塑性变
2
L
形影响。
MRJ1140 最终产 品测 试;根 据测试 无 规范 MRJ1140 在最苛 刻条件 下测量 电流
测试工程 师Max 年月
Mueller 日 先生
DFMEA优化(步骤六)
已 计 划
负责人姓名
目标完成日期 状态
采取基于证据的措施 完成日期
持续改善
设计失效模 式及影响分 析(设计
规划和准备(步骤一) 公司名称: 工程地点: 顾客名称: 年型/项目:
结构分析(步骤二)
问题#
历史/变更授权 (适用时)
1.对上一较高 级别
2.关注要素
3.下一较低 级别或特性类型
车窗升降电机 换向系统
电刷盒基座
规划和准备(步骤一)
负责设计FMEA的公司名称
地理位置
顾客名称或产品名称 顾客应用或公司型号/风
格
项目: DFMEA 开始日期: DFMEA 修订日期:
跨职能团队:
功能分析(步骤三)
1.对上一较高级别功能 及要求
2.关注要素功 3.下一较低级别功
设计FMEA的评价等级

非常高
不适用于检出:故障预防
由于通过设计方面的解决对策(例:被证明有效的设计标准、最佳实践或者通用材料等)可以完全预防,不肯能个发生故障原因或者故障模式。
1
基本上能检出
发生频度评价表/DFMEA
故障发生的概率
基准:原因的发生频次-DFMEA
(设计寿命、零部件、车辆的信赖度)
基准:原因的发生频次-DFMEA
(部件/每辆车的发生问题数量)
等级
非常高
从未有过的新技术/新设计
100以上/1,000
1以上/10
10
高
新设计、新应用、或者由于负荷周期/制动条件的变更无法避免故障的发生。
50/1,000
1/20
9
新设计、新应用、或者由于负荷周期/制动条件的变更导致可能发生故障。
20/1,000
1/50
8
存在新设计、新应用、或者由于负荷周期/制动条件的变更,故障发生的可能性不确定。
8
微弱
与故障试验(故障发生之前的部件系统或者系统相对的试验、系统相互作用的试验等)同时进行设计完成后或量产前的产品验证/稳妥性确认。
7
非常低
与劣化试验(耐久试验结束后对零件系统或者系统进行试验。例如功能检测)同时进行设计完成后或量产前产品的验证/稳妥性。
6
低
设计完成前
进行合格与否试验(例:性能合格与否判定基准、功能检测等)的设计完成前产品的稳妥性确认(信赖性试验、开发或者稳妥性试验)。
项目No.
5.2
改版
3
Form No.
5.2-6
严格程度评价表/DFMEA检出评价表/DFMEA
影响
基准:对产品影响的严格程度(对客户的影响)
fmea探测度评分标准

fmea探测度评分标准FMEA(故障模式与影响分析)是一种常用的风险分析工具,目的是通过系统性的分析和评估,检测和识别潜在的设计或过程问题,并采取适当的措施来消除或减少这些潜在问题的影响。
在FMEA中,探测度评分是其中的一个重要指标,用于衡量当前探测到问题的能力,评估预防措施的效果,并提出改进建议。
以下将介绍FMEA探测度评分标准。
FMEA探测度评分标准可以分为数值评分和描述性评分两种方式。
数值评分是指根据一定的指标体系,通过对每个评分项进行打分,最后综合得出一个总分来衡量探测度的高低。
而描述性评分则是通过对探测度的几个维度进行描述,通过文字方式来表达探测度的状况。
一、数值评分标准:1.提前探测度评分(detection ranking):提前探测度评分是指在设计或过程中,是否有合适的探测手段来及时发现问题。
评分范围通常从1到10,其中1表示探测度非常低,10表示探测度非常高。
2.异常探测度评分(severity ranking):异常探测度评分是指在问题发生时,其对系统性能、安全性和可靠性的影响程度。
评分范围通常从1到10,其中1表示对系统性能、安全性和可靠性的影响非常低,10表示对系统性能、安全性和可靠性的影响非常高。
3.测试探测度评分(testing effectiveness ranking):测试探测度评分是指通过测试手段能够探测问题的能力。
评分范围通常从1到10,其中1表示测试手段几乎无法探测到问题,10表示测试手段可以完全探测到问题。
4.预防探测度评分(prevention ranking):预防探测度评分是指预防措施对问题的发生几率的控制能力。
评分范围通常从1到10,其中1表示预防措施无法控制问题的发生几率,10表示预防措施能够完全控制问题的发生几率。
以上各项评分分值将综合考虑来评估探测度的高低,常用的方法是将各项评分的数值相乘或相加,得出一个综合得分。
二、描述性评分标准:除了数值评分外,FMEA中的探测度评分也可以通过对几个维度的描述来进行评估。
fmea示例表

fmea示例表
FMEA(Failure Mode and Effects Analysis)表格是一个用于评估产品或过程中潜在失效模式及其影响的工具。
以下是一个简单的FMEA表格示例:
序号失效模式潜在原因严重程度发生频率检测难度控制措施
:--: :--: :--: :--: :--: :--: :--:
1 电池充电时间过长电池老化高低中等定期更换电池
2 显示器黑屏显示器故障高中等中等定期检查显示器
3 按键失灵按键老化或损坏中等高低定期检查按键状态
4 音频失真音频驱动程序问题或硬件故障中等低高更新音频驱动程
序或更换硬件设备
5 数据传输速度慢网络拥堵或设备性能问题低高中等优化网络环境
或升级设备性能
在这个示例中,FMEA表格包含了失效模式、潜在原因、严重程度、发生频率、检测难度和控制措施等列。
根据实际情况,你可以在表格中添加或删除列,以满足特定需求。
请注意,这只是一个示例表格,实际应用中需要根据具体的产品或过程进行详细的分析和评估。
FMEA分析需要具备相关领域的知识和经验,以便准确识别潜在的失效模式和制定有效的控制措施。
设计FMEA探测度评价准则对照表模板
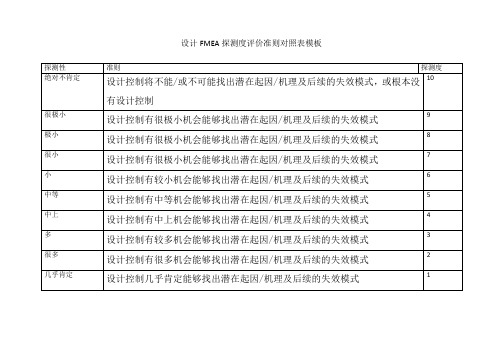
探测性
准则
探测度
绝对不肯定
设计控制将不能/或不可能找出潜在起因/机理及后续的失效模式,或根本没有设计控制
10
很极小
设计控制有很极小机会能够找出潜在起因/机理及后续的失效模式
9
极小
设计控制有很极小机会能够找出潜在起因/机理及后续的失效模式
8
很小
设计控制有很极小机会能够找出潜在起因/机理及后续的能够找出潜在起因/机理及后续的失效模式
1
7
小
设计控制有较小机会能够找出潜在起因/机理及后续的失效模式
6
中等
设计控制有中等机会能够找出潜在起因/机理及后续的失效模式
5
中上
设计控制有中上机会能够找出潜在起因/机理及后续的失效模式
4
多
设计控制有较多机会能够找出潜在起因/机理及后续的失效模式
3
很多
设计控制有很多机会能够找出潜在起因/机理及后续的失效模式
FMEA标准表

设计FMEA的标准表
系统潜在失效模式及后果FMEA编号
子系统(设计FMEA)共页,第页部件设计责任部门编制人
车型年/车辆类型关键日期FEMA日期(编制)(修订)核心小组
.资料. . .
过程FMEA的标准表
潜在失效模式及后果FMEA编号
(过程FMEA)共页,第页项目名称过程责任部门编制人
车型年/车辆类型关键日期FEMA日期(编制)(修订)核心小组
.资料. . .
潜在失效模式及后果分析
(设计FMEA)
系统FMEA编号1234 ①
X 子系统共 1 页,第 1 页部件01.03/车密封②设计责任部门车身工程部③编制人泰特-X6412-车身工程师④
车型年/车辆类型199X/狮牌4门/旅行车⑤关键日期9X 03 01 ⑹FMEA日期(编制)8X 03 22修订8X 07 14⑦
.资料. . .
.资料. . .
潜在失效模式及后果分析
(过程FMEA)
FMEA编号1450 ①
共 1 页,第 1 页
项目名称:左前门/H8HX-A ②过程责任部门车身工程部/ 装配部③编制人J.Ford-------X6512-----装配部门④车型年/车辆类型199X/狮牌4门/旅行车⑤关键日期9X 03 01 9X 0826 工序#1 ⑹FMEA日期(编制)9X 05 17修订9X 11 06⑦
.资料. . .
.资料. . .
潜在失效模式及后果分析
(设计FMEA)
.资料. . .
.资料. . .
.资料. . .
.资料. . .。
- 1、下载文档前请自行甄别文档内容的完整性,平台不提供额外的编辑、内容补充、找答案等附加服务。
- 2、"仅部分预览"的文档,不可在线预览部分如存在完整性等问题,可反馈申请退款(可完整预览的文档不适用该条件!)。
- 3、如文档侵犯您的权益,请联系客服反馈,我们会尽快为您处理(人工客服工作时间:9:00-18:30)。
几乎确定
设计失效模式和后果分析
表DFMEA建议预防/探测评价准则
探测机会
评价准则:
过程控制探测的可能性
级别
探测可能性
没有探测机会
没有现有控制:不能探测或不能解析
10
几乎不可能
在任何阶段不太可能探测
失效模式和/错误(要因)不容易探测(如:随机检查)
9
非常微小
加工后问题探测
操作者通过目测/排列/耳听法的/事后失效模式探测
8
微小
开始时问题探测
操作者通过直观/目测/排列/耳听法的在位置上做失效模式探测/或操作者通过使用特性测量(行/不行、手动转矩检查等)做加工后的探测
7
非常低
加工后问题探测
操作者通过使用变量测量或通过位置上通过使用特性测量事后失效模式探测(行/不行、手动转矩检查等)
6
低
开始时问题探测
操作者通过使用变量测量或通过位置上的自动控制探测差异零件和通知操作者(光、杂音等)。在设置上或首件检查时执行测量(仅对于设置要因)。
5
一般
加工后问题探测
由自动控制探测变异零件并锁住零件预防进一步加工的事后失效模式探测
4
一般自动锁住零件,预防进一步加工的失效模式探测
3
高
错误探测和/或问题预防
由自动控制在位置上探测错误并预防制造中的变异零件的错误(要因)探测
2
非常高
探测不能用:防错
以夹具设计、机械设计或零件设计所做的错误(要因)预防。因为过程产品/设计的防错项目,不会产生变异零件