杯盖模具设计说明书
开水瓶盖塑料模具设计说明书

一、拟定模具的结构形式1、塑件的成型工艺性分析该塑件属于薄壁塑件,生产批量不大,材料选用聚已烯(PE),成型工艺性好,可以采用注射成型。
英文名称:Polyethylene(简称PE)比重:0.94-0.96克/立方厘米成型收缩率:1.5-3.6% 成型温度:140-220℃特点:耐腐蚀性,电绝缘性(尤其高频绝缘性)优良,可以氯化,化学交联、辐照交联改性,可用玻璃纤维增强.低压聚乙烯的熔点,刚性,硬度和强度较高,吸水性小,有良好的电性能和耐辐射性;高压聚乙烯的柔软性,伸长率,冲击强度和渗透性较好;超高分子量聚乙烯冲击强度高,耐疲劳,耐磨.低压聚乙烯适于制作耐腐蚀零件和绝缘零件;高压聚乙烯适于制作薄膜等;超高分子量聚乙烯适于制作减震,耐磨及传动零件.成型特性1.结晶料,吸湿小,不须充分干燥,流动性极好流动性对压力敏感,成型时宜用高压注射,料温均匀,填充速度快,保压充分.不宜用直接浇口,以防收缩不均,内应力增大.注意选择浇口位置,防止产生缩孔和变形.2.收缩范围和收缩值大,方向性明显,易变形翘曲.冷却速度宜慢,模具设冷料穴,并有冷却系统.3.加热时间不宜过长,否则会发生分解.4.软质塑件有较浅的侧凹槽时,可强行脱模.5.可能发生融体破裂,不宜与有机溶剂接触,以防开裂各类聚乙烯产品用途高压聚乙烯:一半以上用于薄膜制品,其次是管材、注射成型制品、电线包裹层等中低、压聚乙烯:以注射成型制品及中空制品为主。
超高压聚乙烯:由于超高分子聚乙烯优异的综合性能,可作为工程塑料使用。
熔点 140摄氏度熔化焓292.88J/g2、分型面的选择根椐塑件的结构形式(如下图所示),分型面选在塑件的底平面。
3、确定型腔的数量和排列方式1)型腔数量的确定该塑件的精度要求不高,属于中小批量生产,而且该塑件的体积比较大,再考虑到模具的制造成本,可以初定为一模一腔的模具形式。
2)型腔排列形式的确定由于是一模一腔的形式,所以采用中央放置。
瓶盖塑料模具设计
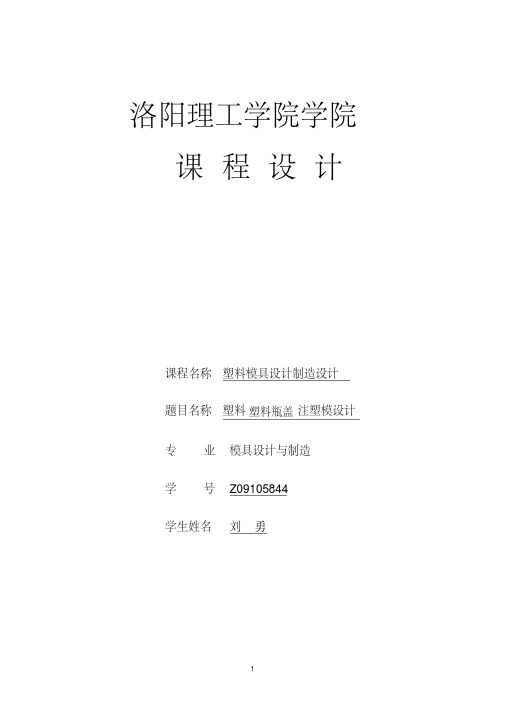
根据塑件的形状特点, 确定模具型腔的定模部分, 模具型芯在动模部分。 塑件 成型开模后, 塑件与型芯一起留在动模一侧。 该塑件有螺纹孔, 螺纹部分是由螺 纹型芯成型的, 由于成型该塑件的塑料 ABS可以采用强制脱模, 但是该制件是有 内螺纹的圆形制件, 故有需要较大的脱模力, 故采用推件版推出机构。 为了避免 推件孔的内表面与型芯的螺纹摩擦, 造成型芯的迅速刮伤, 将推件版的内孔与型 芯成型面做成单边斜度为 5~10 度的锥面,并且可以准确定位推件版,避免了该 处的飞边溢斜。
(1) 主流道的设计
6
主流道是连接注射机喷油嘴与分流道的一段通道, 轴线上,端面为圆形, 由注塑机的参数可知 : 喷嘴的直径为 d0=4mm 喷嘴的前端球半径 R0=15mm 根据主流道与喷嘴的关系得到: 主流道进口端球面半径 R=R0+(1~2)取 R=16mm
主流道进口端孔直径 d=d0+0.5=4+0.5=4.5mm.
3
10
120
105
0~220
325
15 螺杆式
125
模板的最大厚度 /mm
300
模板的最小厚度 /mm
200
最大模板尺寸 /mm 370*320
拉杆空间 /mm
345 345
合模方式
液压机械
电机功率 /KW
15
定位圈深度 /mm
10
喷嘴孔直径 /mm
4
最大成型面积 / cm 2
320
注塑速率 / (g.s 1 )
3
( 2) 塑件表面质量分析
该塑件表面没有很高的要求,在一般情况下,要求塑件光洁,表面粗糙度为
Rs,
对外表面可以取 0.8 μm;对内表面的 Rs 可以取 3.2 μ m。
水杯模具设计说明书

课程设计说明书专业:模具设计与制造学生姓名:学号:指导教师:2014年6月26 日摘要本次课程设计课题是PP水杯注塑模设计,本文详细介绍了注射模具模架、成型零部件、浇注系统和脱模系统等模具主要的设计过程,并对模具强度要求做了说明。
设计中对注射机的相关参数进行了验证,包括模具闭合厚度、模具安装尺寸、模具开模行程、注射机的锁模力等。
校核合格后进行了成型零件加工工艺过程的制定,既保证了塑件的质量,又兼顾了经济性。
最后在设计过程中运用Auto CAD、UG 软件进行注塑模结构设计与计算,并绘制出了模具总装图以及部分零件图,从而得出完整的理论设计结果,为今后工程设计打下了基础。
目录前言 (1)一概述 (2)1.1设计目的 (2)1.2 模具设计的主要内容和任务 (2)1.2.1 塑料模具设计任务 (2)1.2.2 收集、分析、消化原始资料 (2)1.2.3 确定成型方法 (3)二塑件成型工艺性分析 (4)2.1塑件的分析 (4)2.1.1外形尺寸 (4)2.1.2 精度等级 (5)2.2 PP性能分析 (5)2.3 PP的注射成型过程及工艺参数 (5)三拟定模具的结构形式 (7)3.1分型面位置的确定 (7)3.2 型腔数量和排列方式的确定 (8)3.3注射机型号的确定 (9)四浇注系统和成型零件的设计 (12)4.1 浇注系统的设计 (13)4.1.1 主流道的设计 (13)4.1.2 分流道的设计 (14)4.1.3 浇口的设计 (15)4.1.4 冷料井的设计 (17)4.2 成型零件的结构设计及计算 (17)4.2.1成型零件的结构设计 (17)4.2.2成型零件钢材的选用 (18)4.2.3成型零件工作尺寸的计算 (18)4.2.4 成型零件尺寸及动模垫块厚度的计算 (19)4.2.5 排气槽的设计 (19)五模架和推出机构的设计 (20)5.1 模架的确定 (20)5.1.1 各模板尺寸的确定 (20)5.1.2模架各尺寸的校核 (20)5.2 脱模推出机构的设计 (21)5.2.1脱模机构 (21)5.2.2推出方式的确定 (21)5.3 导向和定位结构的设计 (22)第6章总结 (23)附录总装图 (24)前言本说明书为PP水杯注塑模设计说明书,是根据塑料模具手册上的设计过程及相关工艺编写的。
小瓶盖塑料注塑模具设计说明书
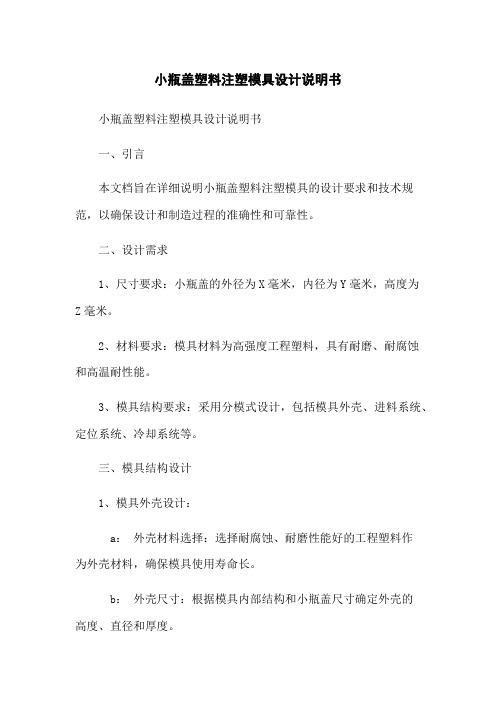
小瓶盖塑料注塑模具设计说明书小瓶盖塑料注塑模具设计说明书一、引言本文档旨在详细说明小瓶盖塑料注塑模具的设计要求和技术规范,以确保设计和制造过程的准确性和可靠性。
二、设计需求1、尺寸要求:小瓶盖的外径为X毫米,内径为Y毫米,高度为Z毫米。
2、材料要求:模具材料为高强度工程塑料,具有耐磨、耐腐蚀和高温耐性能。
3、模具结构要求:采用分模式设计,包括模具外壳、进料系统、定位系统、冷却系统等。
三、模具结构设计1、模具外壳设计:a:外壳材料选择:选择耐腐蚀、耐磨性能好的工程塑料作为外壳材料,确保模具使用寿命长。
b:外壳尺寸:根据模具内部结构和小瓶盖尺寸确定外壳的高度、直径和厚度。
c:模具外壳装配:确保外壳的装配牢固,能够承受注塑过程中的压力和冲击。
2、进料系统设计:a:进料口位置:进料口位于模具外壳上方,方便塑料材料的注入和冷却。
b:进料系统结构:进料系统包括进料管道、进料阀门和喷嘴等组成,确保塑料均匀流动。
3、定位系统设计:a:定位杆:在模具内部设置定位杆,以确保小瓶盖注塑时的位置准确性。
b:定位孔:在小瓶盖上开设定位孔,使得小瓶盖能够准确地套在定位杆上。
4、冷却系统设计:a:冷却通道:在模具内部设置冷却通道,以降低注塑过程中的温度,提高生产效率和产品质量。
b:冷却介质:选择高效的冷却介质,如冷水或冷气等,快速降低模具温度。
四、模具制造要求1、加工工艺:采用先进的数控加工设备和工艺,确保模具的加工精度和表面光洁度。
2、查漏测试:在模具制造过程中进行查漏测试,确保模具没有任何渗漏。
五、附录本文档涉及以下附件:1、小瓶盖的详细尺寸图纸。
2、模具的3D设计图纸。
六、法律名词及注释1、注塑模具:指用于塑料注塑成型的模具,可分为热流道模具和冷流道模具。
2、工程塑料:指具有高强度、耐磨、耐腐蚀和高温耐性能的塑料材料。
3、渗漏:指模具在注塑过程中出现塑料渗漏的现象,对产品质量产生负面影响。
模具毕业设计42咖啡杯盖注塑模具设计
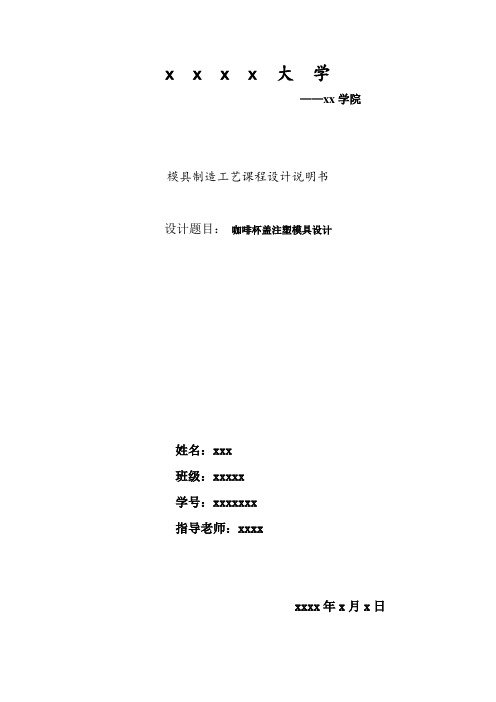
x x x x 大学——xx学院模具制造工艺课程设计说明书设计题目:咖啡杯盖注塑模具设计姓名:xxx班级:xxxxx学号:xxxxxxx指导老师:xxxxxxxx年x月x日xxxxxxxx学院xx 级学生专业课程设计任务书079013班模具设计与制造专业类学生: xxxx日期:自xxxx年xx 月xx日至 xxxx年x月x日指导教师: xxxx目录目录........................................................................................................................................ - 3 - 一.塑件的分析.......................................................................................................................... - 6 - 二.注射机的选择...................................................................................................................... - 7 - 三.注射机有关工艺参数的校核.............................................................................................. - 7 -1.型腔数量的确定和校核........................................................................................................... - 7 -2.锁模力的校核................................................................................................................... - 8 -3.注射压力的校核............................................................................................................... - 8 -4.开模行程的校核............................................................................................................... - 8 -5.推出装置的校核............................................................................................................... - 8 -四.型腔的布局与分型面设计..................................................................................................... - 9 -1.型腔的布局....................................................................................................................... - 9 -2.分型面的选择................................................................................................................... - 9 - 五.浇注系统的设计................................................................................................................ - 11 -1.主流道的设计................................................................................................................. - 11 -2.分流道设计..................................................................................................................... - 11 -(1).分流道的形状与尺寸..................................................................................... - 11 -(2).分流道的长度................................................................................................. - 11 -(3).分流道的表面粗糙度..................................................................................... - 11 -3.浇口的设计..................................................................................................................... - 12 -(1).浇口的选用..................................................................................................... - 12 -(2).浇口位置的选择............................................................................................. - 12 - 六.成型零部件的设计............................................................................................................ - 13 -1.凹模和凸模的结构设计................................................................................................. - 13 -2.成型零件的工作尺寸计算............................................................................................. - 14 -(1)型腔和型芯径向尺寸的计算.......................................................................... - 14 -(2)型腔深度和型芯高度尺寸的计算.................................................................. - 15 - 七.合模导向机构设计............................................................................................................... - 16 - 八.推出机构设计.................................................................................................................... - 17 -1.推出机构及机构组成..................................................................................................... - 17 -2.推出机构的分类............................................................................................................. - 17 -3.推出结构的设计要求..................................................................................................... - 17 -4.推杆的设计..................................................................................................................... - 17 -(1)推杆的形状...................................................................................................... - 17 -(2)推杆位置的选择.............................................................................................. - 18 - 九.侧向分型与抽芯机构的设计............................................................................................ - 18 -1.抽芯力与抽芯距的确定................................................................................................. - 19 -(1)抽心力的确定.................................................................................................. - 19 -(2)抽芯距地确定.................................................................................................. - 19 -2.斜导柱的设计................................................................................................................. - 19 -(1)斜导柱的基本形式.......................................................................................... - 19 -(2)斜导柱倾斜角的选择...................................................................................... - 20 -(3)斜导柱长度计算.............................................................................................. - 20 -(4)侧滑块的设计....................................................................................................... - 21 - 十.设计小结............................................................................................................................ - 22 - 十一.参考文献........................................................................................................................ - 22 -塑料模具课程设计————咖啡杯盖塑件名称:咖啡杯盖材料:ABS产品塑件图一.塑件的分析ABS塑料,化学名称:丙烯腈-丁二烯-苯乙烯共聚物,英文名称:Acrylonitrile Butadiene Styrene,比重:1.08~1.2克/立方厘米。
毕业设计杯子模具设计说明书

1. 塑件的分析脱模斜度0.75度图1.1 塑件结构示意图1.1外形尺寸该塑件壁厚为2mm,塑件外形尺寸不大,塑件熔体流程不太长,塑件材料为无填充材料的PP,流动性好,适合于注射成型。
1.2精度等级本塑件采用一般精度4级。
1.3脱模斜度由于该塑件的脱模高度约为70mm,由脱模斜度表可查得:聚丙烯PP的脱模斜度为0.75°。
2. 成型材料PP的成型特性与工艺参数2.1 PP的成型特性聚丙烯为白色蜡状塑料,外观似聚乙烯,但比聚乙烯更轻,密度为0.9~0.91g/cm3,强度、刚度、硬度、耐热性均优于低压聚乙烯,可在100℃左右使用,具有良好的电性能和高频绝缘性,不受温度影响,但低温时易变脆、不耐磨,易老化,适于制作一般机械零件、耐腐蚀零件和绝缘零件。
PP的主要性能指标如表2.1所示表2.1 PP物理性能参数名称参数密度0.9~0.91g/cm3比体积 1.10~1.11cm3/g吸水率0.03%~0.04%熔点170~176℃收缩率 1.0%~3.0%比热容1930J/(Kg.℃)屈服强度37Mpa拉伸弹性模量 1.65×103Mpa弯曲强度67Mpa弯曲弹性模量 1.45×103Mpa2.2 PP的工艺参数聚丙烯PP是非极性结晶性塑料,吸湿性小,约为0.03﹪~0.04﹪,一般不需干燥,流动性好,溢边料为0.025~0.04mm,收缩范围及收缩值大,并具各向异性,易发生缩孔、凹痕和变形,热稳定性好,成型温度范围较宽,抗氧化能力低,在塑化前应加入一定比例的抗氧剂,塑料壁厚应均匀,避免缺胶、尖角,以防应力集中。
其注射工艺参数如表2.2所示表2.2 PP的注射工艺参数名称参数螺杆转速30~60r/min 料筒温度前段160~180℃中段180~200℃后段200~230℃喷嘴温度180~190℃模具温度40~80℃注射压力70~120Mpa冷却时间20~90s成型时间40~120s3. 设备型号的确定3.1估算塑件一次成型的注射量3.1.1塑件体积和质量的计算塑件的体积按式3.1计算ab a a a d V l l h d h ⋅⋅+⋅⋅+⋅∏+⋅⋅⋅∏=⎪⎭⎫ ⎝⎛222212塑(式 3.1)cm33210264)2161221246227064(-⨯⨯⨯+⨯⨯+⨯⨯∏+⨯⨯⨯∏=⎪⎭⎫ ⎝⎛=36.07cm 3塑件的质量按式3.2计算V 塑塑⋅=ρm(式 3.2)g 82.3207.3691.0=⨯=式中: ρ----聚丙烯的密度,取0.91g/cm 3选择注射机型号为SZ ——100/60,其理论注射量Vc=100cm 3。
玻璃容器盖子模具设计说明书

课程设计玻璃容器盖子注塑模具设计学院机械学院班级机制1215姓名焕樟学号 8摘要关于模具发展趋势,我认为这主要取决于两个方面,即一方面是模具为之服务的各行各业的发展趋势,另一方面是整个社会和世界科学技术的发展趋势,这实际上就是需要和可能。
模具是为制件,也就是成形产品服务的,因此模具必然要以制件(成形产品) 的发展趋势为自己的发展趋势,模具必须满足他们的要求。
制件发展趋势主要是轻巧、精美、快速高效生产、低成本与高质量,每一项都预示了模具发展趋势。
本设计主要针对玻璃容器盖子塑件,应用计算机辅助模具设计。
设计中首先根据塑料制品要求拟定成型工艺方案、初选成型设备、确定模具结构方案,设计浇注系统并进行模流分析、选用模架、选择和校核注射机,完成模具型腔设计并对模具主要零件设计计算,然后应用proE软件,完成整副模具的三维设计,并对模具进行了虚拟装配和试模,针对其中出现的问题,对模具进行了修改,最后导出模具二维工程图。
关键词:玻璃容器盖子;顶出机构;塑料模;模具AbstractAbout mold development trend, I think it depends mainly on two aspects, that is, on the one hand is development trend of the mould service for all walks of life, on the other hand, the whole society and the world trend of the development of science and technology, it is actually need and possible. Moulds for the parts, that is, forming products and services, so the mould must to stamping forming products () for their own development trend, the development trend of die must meet their requirements. Development trend of the main parts is light and elegant, fast and efficient production, low cost and high quality, each announced a mold development trend.This design mainly for glass lid plastic parts, application of computer aided mould design. First according to the request of plastic products in the design of drawing up scheme, primary molding equipment, molding process of mould structure scheme, gating system design and mold flow analysis, selects the die set, select and check injection machine, the main parts to complete the mold design and mold design and calculation, and then using proE software, completed the entire mould 3 d design, and on the mould virtual assembly and test, and problems which appear on the mold modification, finally export mold two-dimensional engineering graphics.Keywords: Glass lid; Ejection agencies; Plastic mould; The mould目录摘要 (I)Abstract (II)目录 (III)1、前言 (1)1.1模具行业及产品发展现状 (1)1. 2选题意义 (2)2、塑件设计分析 (3)2.1塑件模型建立 (3)2.2塑件参数设计 (3)2.3 材料选择 (3)2.4塑件的壁厚 (4)2.5 塑件的脱模斜度 (4)2.6分型面设计 (4)2.7 确定型腔数量以及排列方式 (5)3、注塑设备和模架选择 (6)3.1 注塑设备选择 (6)3.2注塑机重要参数校核 (7)3.2.1型腔数量的确定和校核 (7)3.2.2 注塑容量校核 (8)3.2.3锁模力校核 (9)3.2.4注塑压力校核 (9)3.2.5开模行程校核 (10)3.2.6 推出装置校核 (10)3.2.7 模具外形尺寸校核 (11)3.3 模架选择 (11)3.3.1模架类型选择的前提条件 (11)3.3.2模架系列的选择 (11)4、浇注系统设计 (13)4.1 主流道设计 (13)4.1.1 浇口套设计 (13)4.1.2 浇口套的固定形式 (13)4.2 分流道的设计 (14)4.2.1 分流道的形状及尺寸选择 (14)4.2.2 分流道的设计 (14)4.3 浇口设计 (14)4.4 冷料穴和钩料脱模装置 (15)4.5排气系统的设计 (16)5、成型零件设计 (17)5.1 型腔模的设计 (17)5.2型芯模的设计 (17)6、推出机构设计 (21)6.1推筒推出机构 (21)6.2 推出机构的复位 (21)6.3 推出机构的布局 (22)7、冷却系统设计 (23)7.1 冷却管道的工艺计算 (23)7.2 冷却水道的结构设计 (24)总结 (25)参考文献 (26)致 (27)1、前言1.1模具行业及产品发展现状关于模具发展趋势,我认为这主要取决于两个方面,即一方面是模具为之服务的各行各业的发展趋势,另一方面是整个社会和世界科学技术的发展趋势,这实际上就是需要和可能。
乐扣杯杯盖毕业设计说明书
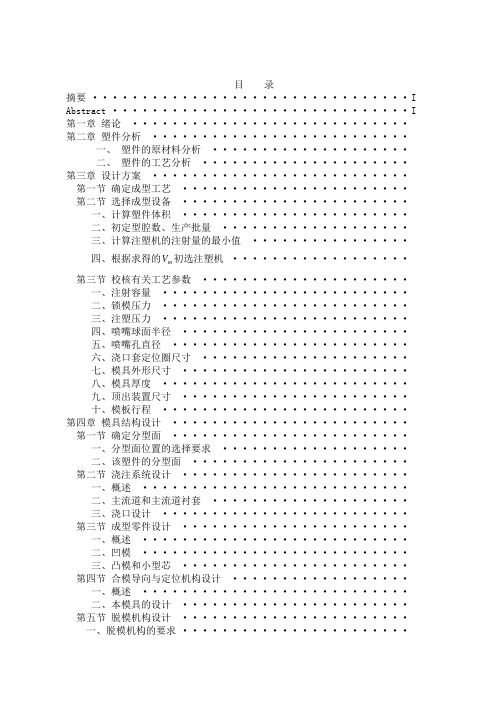
目录摘要 (I)Abstract (I)第一章绪论····························第二章塑件分析··························一、塑件的原材料分析····················二、塑件的工艺分析·····················第三章设计方案··························第一节确定成型工艺·······················第二节选择成型设备·······················一、计算塑件体积·······················二、初定型腔数、生产批量···················三、计算注塑机的注射量的最小值················V初选注塑机··················四、根据求得的m第三节校核有关工艺参数·····················一、注射容量·························二、锁模压力·························三、注塑压力·························四、喷嘴球面半径·······················五、喷嘴孔直径························六、浇口套定位圈尺寸·····················七、模具外形尺寸·······················八、模具厚度·························九、顶出装置尺寸·······················十、模板行程·························第四章模具结构设计························第一节确定分型面························一、分型面位置的选择要求···················二、该塑件的分型面······················第二节浇注系统设计·······················一、概述···························二、主流道和主流道衬套····················三、浇口设计·························第三节成型零件设计·······················一、概述···························二、凹模···························三、凸模和小型芯·······················第四节合模导向与定位机构设计··················一、概述···························二、本模具的设计·······················第五节脱模机构设计·······················一、脱模机构的要求·······················二、本模具的设计························第六节侧向分型与抽芯机构设计··················一、概述····························二、本模具的设计························第七节温度调节系统设计·····················一、冷却系统设计要求······················二、本模具的设计························第八节排气系统设计·······················第五章模具使用说明························一、生产前的准备·······················二、上模····························三、润滑保养··························结论································致谢································参考文献······························第一章塑件分析一、塑件的原材料分析塑件的原材料采用聚丙烯(PP),PP为结晶型高聚物,常用塑料中PP最轻。
- 1、下载文档前请自行甄别文档内容的完整性,平台不提供额外的编辑、内容补充、找答案等附加服务。
- 2、"仅部分预览"的文档,不可在线预览部分如存在完整性等问题,可反馈申请退款(可完整预览的文档不适用该条件!)。
- 3、如文档侵犯您的权益,请联系客服反馈,我们会尽快为您处理(人工客服工作时间:9:00-18:30)。
杯盖模具设计说明书
1. 塑料成型工艺性分析
本产品采用PS 原料,PS 是无色透明并有光泽的非结晶型的线形结构的高聚物,密度为31.054g/cm .PS 有优良的电性能和一定的化学稳定性。
聚苯乙烯耐热性低,热变形温度一般在
7098C C o
o
所以只能在不高的温度下
使用,PS 质地硬而脆,有高的热膨胀系数,塑件易产生内应力易开裂。
PS 成型性能优良具有⑴吸水性好⑵收缩性好⑶比热容小⑷热膨胀系数高。
塑件壁厚属薄壁塑件,生产批量很大,
采用注射成型。
杯盖如图1所示: 图1 2. 分型面的分析与确定
根据要求该模具采用双分型面,经过两次分型,由塑件的结构形式,塑件的分型面选在杯盖的外表面,如图2:
图2
3. 确定型腔数量和排列方式
根据设计要求,模具采用一模两腔,采用水平排列。
型腔布局如图3:
图3
4. 注射机型号的选定 4.1 注射量的计算
通过计算可得,塑件的体积v 塑件的质量m 流道凝料的质量2m 还是个未知数,可按塑件质量0.6倍计算,从上述分析中确定为一模两腔,所以注射量为
11.6 1.62 6.2620.045m nm ==⨯⨯=
4.2 塑件和流道凝料在分型面上的投影面积及所要锁模力计算
流道凝料(包括浇口)在分型面上的投影面积2A ,在模具设计前是个未知数。
型多型腔模腔模的统计分析,2A 是每个塑件在分型面的投影面积1A 的
0.2~0.5倍,可用10.3nA 来进行估算,则:
2
12
123115.665
28412.296258412.296210.370m d A A nA nA mm F Ap KN
π⎛⎫
== ⎪⎝⎭
=+===⨯=型
其中P 为型腔中的压力取25Mpa ,(因为是壁薄零件,浇口为点浇口,压力取大一些,见表113-),常用塑料注射成型时所选用的型腔压力值见表1:
表1
4.3 选择注塑机
根据每一生产周期的注射量和锁模力的计算值,可选用60/450SZ -卧式注射机(上海第一塑料机械厂)见表2:
表2
4.4注塑机有关参数的校核
4.4.1由注射剂料筒塑化速率校核模具的型腔数n .
210.8 5.6300.62 6.26
20.2626.26
t km m n m -⨯⨯-⨯⨯≤
==? 型腔数校核合格
式中 k -注射剂最大注射量的利用系数一般为0.8 m -注射机的额定塑化量()5.6/g s t -成型周期取30s
4.4.2注射压力的校核
1.3130169e P k Mpa '≥=⨯=,而170e P Mpa =注射压力校核合格
式中 k '-注射压力安全系数,一般取 1.25~1.4k '=
0P -塑件成型时所需的注射力,生产实践中其值一般为70~150Mpa 0130p MPa =
4.4.3锁模力校核
1.2210.30725
2.368F KAP KN ≥=⨯=型
而450F KN =,则锁模力校核合格
式中 K -锁模安全系数一般取 1.1~1.2K = P -型型腔的平均压力,选用件表3
5.浇注系统的设计 5.1主流道设计 5.1.1主流道尺寸
根据所选注射机,则主流道小端尺寸为:
()0.5~10 3.50.54d mm =+=+=喷嘴尺寸 主流道球面半径为:
()1220222SR mm =+-=+=喷嘴球面半径 5.1.2主流道衬套形式
本设计是小模具,为了便于加工和缩短主流道长度,衬套和定位圈设计成
分体式,主流道长度取35,锥度为
03,衬套如图4,材料用10T 钢。
热
处理淬火后,表面硬度为
53HRC-57HRC
图4
5.1.3主流道凝料体积
22
33n 4 6.1d L 40800.7785mm 0.5cm 4
4
2
q π
π
+=
=
⨯⨯==主(
) 5.1.4有经验公式得
1312
3
3.31840.191840510n
q r s s R π--=
==<⨯ 20.8 2.7722 5.943 5.46q q q q =++=++⨯=分主塑件
(4 6.1)/2 5.25
2.52522
n R +=
== 5.2分流道的设计
第一级分流道190mm L = 第二级分流道210mm L =
1) 分流道应满足良好的压力传递和保持理想的填充状态,使塑料熔体尽快地
经分流道均匀的分配到个个型腔。
因此第一级分流道采用半圆形截面。
2) 分流道的形状,截面尺寸及凝料体积。
第一级分流道形状及截面尺寸,为了便于机械加工及凝料脱模。
本设计的分流道设置在第一分型面定模板上,截面形状采用加工工艺性良好的半圆形截面,半圆形截面对塑料熔体及流动阻力均不大,对于壁厚小于3mm 质量在200g 以下的塑件可用下述经验公式确定分流道直径1
12
4
2.6544D w L =≈
式中D ——分流道的直径mm
W ——塑件的质量g L ——分流道长度mm
第二级分流道,根据设计要求分流道设计呈锥形,开设在中间板上,其中
分流长度为10mm,大端直径为4mm,锥度为0
17,截面形状如图5:
图5
5.3浇口的设计
5.3.1根据塑件特征看塑件属于壁薄零件,需要快速注射成型,为了便于使浇注凝料与塑件自动脱落,因此采用点浇口,一般点浇口直径0.3~2
,
d mm
综合考虑取浇口尺寸为1mm。
根据Proe软件塑料浇注分析如图6,浇口位置选在杯盖顶部中心。
图6
浇口截面形状如下图7:
图7。