工业纯铁方坯表面裂纹形成原因的分析
板坯边部纵裂纹产生的原因及解决措施
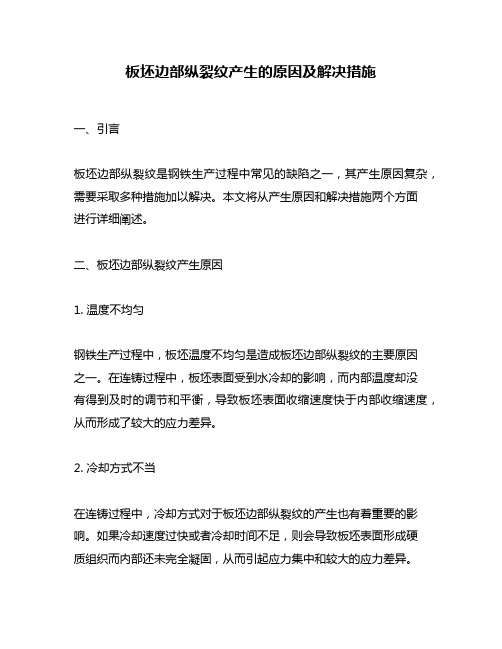
板坯边部纵裂纹产生的原因及解决措施一、引言板坯边部纵裂纹是钢铁生产过程中常见的缺陷之一,其产生原因复杂,需要采取多种措施加以解决。
本文将从产生原因和解决措施两个方面进行详细阐述。
二、板坯边部纵裂纹产生原因1. 温度不均匀钢铁生产过程中,板坯温度不均匀是造成板坯边部纵裂纹的主要原因之一。
在连铸过程中,板坯表面受到水冷却的影响,而内部温度却没有得到及时的调节和平衡,导致板坯表面收缩速度快于内部收缩速度,从而形成了较大的应力差异。
2. 冷却方式不当在连铸过程中,冷却方式对于板坯边部纵裂纹的产生也有着重要的影响。
如果冷却速度过快或者冷却时间不足,则会导致板坯表面形成硬质组织而内部还未完全凝固,从而引起应力集中和较大的应力差异。
3. 连铸机结构问题连铸机的结构问题也会对板坯边部纵裂纹的产生造成影响。
例如,如果连铸机的结构不合理或者设备老旧,就可能导致板坯内部温度不均匀或者冷却方式不当,从而引起板坯边部纵裂纹。
三、解决措施1. 调节温度钢铁生产过程中,调节温度是减少板坯边部纵裂纹的有效措施之一。
可以通过加强温度监测和调节系统来实现。
例如,在连铸过程中可以采用先进的热流体模拟技术来预测板坯内部温度分布情况,并及时调整冷却水量和喷淋位置等参数,以保证板坯内外温度平衡。
2. 改进冷却方式改进冷却方式也是减少板坯边部纵裂纹的有效措施之一。
可以通过增加喷淋头数量、改变喷淋角度、增加喷淋水量等方式来改善连铸过程中的冷却效果,并保证板坯表面和内部同时达到凝固要求。
3. 优化连铸机结构优化连铸机结构也是减少板坯边部纵裂纹的有效措施之一。
可以通过升级设备、改进结构、增加监测仪器等方式来提高连铸机的生产效率和准确性,从而保证板坯内部温度分布均匀和冷却方式合理。
四、总结综上所述,板坯边部纵裂纹是钢铁生产过程中常见的缺陷之一,其产生原因复杂,需要采取多种措施加以解决。
调节温度、改进冷却方式和优化连铸机结构是减少板坯边部纵裂纹的有效措施。
冶金缺陷引起的开裂

冶金缺陷引起的开裂引言:在冶金领域,开裂是一种常见的缺陷现象,它严重影响着金属材料的强度和耐久性。
开裂不仅会导致零件失效,还可能引发事故和人员伤亡。
因此,了解冶金缺陷引起的开裂原因以及预防措施对于确保材料的质量和安全至关重要。
一、热裂纹热裂纹是一种由于材料在高温下受到应力作用而引起的裂纹。
金属材料在冷却过程中,由于温度梯度和相变引起的体积变化,会产生内部应力,当应力超过材料的强度极限时,就会出现热裂纹。
避免热裂纹的方法包括合理设计冷却过程、控制温度梯度以及选择合适的材料。
二、晶粒界开裂晶粒界开裂是指裂纹沿着晶粒界扩展的现象。
晶粒界是由于晶体生长过程中晶粒的接触面形成的,它在金属材料中扮演着重要的角色。
当晶粒界处存在缺陷或杂质时,会导致晶粒界开裂。
预防晶粒界开裂的方法包括选择高纯度的金属材料、控制晶粒尺寸和形状、减少杂质含量等。
三、材料疲劳开裂材料在长时间的循环应力作用下会发生疲劳开裂。
疲劳开裂是由于材料在应力循环下的微小变形和应力集中引起的。
当应力超过材料的疲劳极限时,就会发生裂纹的扩展。
为了预防材料的疲劳开裂,可以采取一些措施,如增加材料的强度和硬度、改善材料的表面质量、减小应力集中等。
四、氢脆开裂氢脆开裂是指在金属材料中存在氢元素的情况下,当材料受到应力作用时发生的开裂现象。
氢元素会在材料中扩散并聚集在应力集中的区域,导致材料的脆性增加,从而引发开裂。
为了避免氢脆开裂,可以采取一些措施,如降低材料中的氢含量、控制材料的应力状态、改变材料的组织结构等。
五、应力腐蚀开裂应力腐蚀开裂是指在介质中存在腐蚀性物质的情况下,材料在受到应力作用时发生的开裂现象。
应力腐蚀开裂是由于介质中的化学物质与材料表面相互作用,导致材料的腐蚀和应力集中,从而引起开裂。
预防应力腐蚀开裂的方法包括选择耐腐蚀性较好的材料、控制介质中的化学物质浓度和温度、改变材料的表面处理等。
结论:冶金缺陷引起的开裂是一种严重影响金属材料性能和安全性的问题。
板坯边部纵裂纹产生的原因及解决措施

板坯边部纵裂纹产生的原因及解决措施板坯边部纵裂纹是钢铁生产过程中常见的问题之一,它会影响钢材的质量和使用寿命,因此必须采取措施加以解决。
本文将从产生原因和解决措施两个方面进行探讨。
一、产生原因
1.板坯温度不均匀:板坯温度不均匀是板坯边部纵裂纹产生的主要原因之一。
当板坯表面温度高于内部温度时,板坯边部会出现温度梯度,导致板坯边部产生应力,从而引起纵裂纹。
2.板坯结晶器结构不合理:板坯结晶器结构不合理也是板坯边部纵裂纹产生的原因之一。
结晶器结构不合理会导致板坯边部温度不均匀,从而引起纵裂纹。
3.轧制工艺不合理:轧制工艺不合理也是板坯边部纵裂纹产生的原因之一。
轧制工艺不合理会导致板坯边部应力过大,从而引起纵裂纹。
二、解决措施
1.优化板坯结晶器结构:优化板坯结晶器结构是解决板坯边部纵裂纹的有效措施之一。
合理的结晶器结构可以使板坯温度均匀,从而减少板坯边部应力,降低纵裂纹的发生率。
2.调整轧制工艺:调整轧制工艺也是解决板坯边部纵裂纹的有效措
施之一。
合理的轧制工艺可以使板坯边部应力适当,从而减少纵裂纹的发生率。
3.控制板坯温度:控制板坯温度也是解决板坯边部纵裂纹的有效措施之一。
合理的板坯温度可以使板坯温度均匀,从而减少板坯边部应力,降低纵裂纹的发生率。
板坯边部纵裂纹是钢铁生产过程中常见的问题之一,产生原因主要有板坯温度不均匀、板坯结晶器结构不合理和轧制工艺不合理等。
解决措施主要包括优化板坯结晶器结构、调整轧制工艺和控制板坯温度等。
只有采取有效的措施,才能有效地解决板坯边部纵裂纹问题,提高钢材的质量和使用寿命。
铸坯表面横裂纹的形成机理
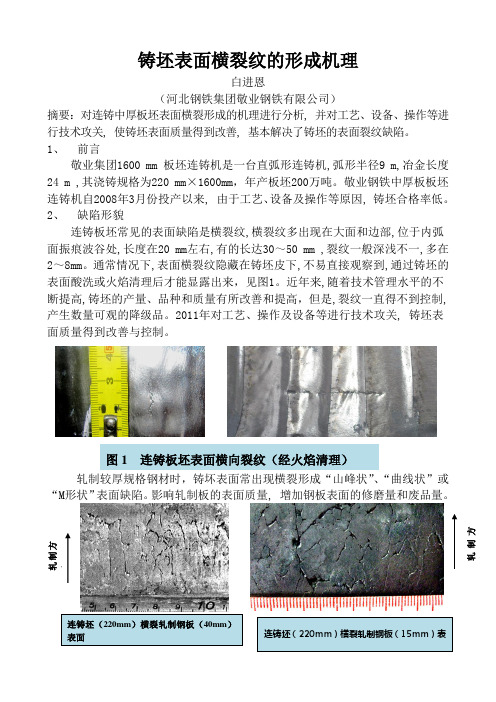
铸坯表面横裂纹的形成机理白进恩(河北钢铁集团敬业钢铁有限公司)摘要:对连铸中厚板坯表面横裂形成的机理进行分析, 并对工艺、设备、操作等进行技术攻关, 使铸坯表面质量得到改善, 基本解决了铸坯的表面裂纹缺陷。
1、 前言敬业集团1600 mm 板坯连铸机是一台直弧形连铸机,弧形半径9 m,冶金长度24 m ,其浇铸规格为220 mm ×1600mm ,年产板坯200万吨。
敬业钢铁中厚板板坯连铸机自2008年3月份投产以来, 由于工艺、设备及操作等原因, 铸坯合格率低。
2、 缺陷形貌连铸板坯常见的表面缺陷是横裂纹,横裂纹多出现在大面和边部,位于内弧面振痕波谷处,长度在20 mm 左右,有的长达30~50 mm ,裂纹一般深浅不一,多在2~8mm 。
通常情况下,表面横裂纹隐藏在铸坯皮下,不易直接观察到,通过铸坯的表面酸洗或火焰清理后才能显露出来,见图1。
近年来,随着技术管理水平的不断提高,铸坯的产量、品种和质量有所改善和提高,但是,裂纹一直得不到控制,产生数量可观的降级品。
2011年对工艺、操作及设备等进行技术攻关, 铸坯表面质量得到改善与控制。
轧制较厚规格钢材时,铸坏表面常出现横裂形成“山峰状”、“曲线状”或“M 形状”表面缺陷。
影响轧制板的表面质量, 增加钢板表面的修磨量和废品量。
图1 连铸板坯表面横向裂纹(经火焰清理)图2 钢板表面横裂实物图3、铸坯表面横裂纹形成机理结晶器振动的目的是防止初生坯壳与结晶器黏结漏钢,但不可避免地会在初生坯壳表面留下震动痕迹。
而铸坯横裂纹产生于振动痕迹的波谷处,振痕越深,横裂纹越严重。
裂纹的发生率还与振痕形貌有关,振痕越深,呈“沟槽”形,曲率半径越小,越容易发生横裂纹和角横裂。
连铸坯表面横裂起源于结晶器中振痕波谷处,最后在矫直过程中形成。
横裂形成具体分6个阶段:①靠结晶器壁生长正常的凝固组织,即细小等轴晶(坯壳晶、激冷层),其晶粒尺寸约500μm;②负滑脱凝壳向内运动,凝壳离开结晶器壁,温度达1 350℃;③导致表面晶粒异常长大,粗大化达到1mm~2mm;④在大晶粒晶界碳、氮化物析出,弱化的晶界产生微裂纹源;⑤在异常粗大的晶界上形成先共析相铁素体网,其强度是奥氏体的1/4,构成新的裂纹源;⑥在连铸坯矫直过程中微裂纹扩展成为裂纹。
27SiMn钢表面裂纹形成原因分析及控制措施

(山东钢铁股份有限公司莱芜分公司,山东 莱芜 271104)
摘 要:针对 27SiMn 钢轧材表面经常出现裂纹缺陷的问题,对问题钢材进行了取样分析,找到引起表面
裂纹的原因并提出控制措施。利用金相显微镜及扫描电镜对裂纹进行观察。分析结果表明,钢材化学成分
及力学性能符合设计要求,裂纹两侧有明显的脱碳层,裂纹内有大量 Si-Al 氧化物,确定裂纹为铸坯原有裂
1 铸坯表面裂纹因素分析
在连铸机中钢水凝固时,由于钢种自身的凝固
收缩、连铸工艺及设备状况等原因,铸坯多少都会 产生各种缺陷,缺陷的产生降低了铸机的生产率, 并影响到后续的生产。
1.1 化学成分的影响 钢中较高含量的硫会在连铸及热处理过程中
以硫化物的形式析出,增大铸坯裂纹形成的趋势, 有学者研究可以通过控制钢中的 Mn/S 比来控制裂 纹产生的倾向[1],当 Mn/S 比小于 1.345[%S]-0.7934 时, 就可以回引发铸坯对裂纹的敏感性。过高的硫还 会降低铸坯的热塑性,因此应尽可能降低钢中硫的 含量。磷对裂纹的影响,不同的学者有不同的看法 [2],有人认为适当增加其含量可提高钢在低温范围 内的热塑性,能减少横裂纹的发生率。但如果磷元
纹;结合实际生产情况,将铸坯矫直温度由 900℃提升至 930℃,钢材表面裂纹消失。
关键词:27SiMn 钢;表面裂纹;分析;控制;工艺优化
中图分类号:
文献标识码:B
Hale Waihona Puke 文章编号:1674-0971-(2019)01-012-03
Analysis and Control of Surface Crack Defect of 27SiMn Steel
第 25 卷 总第 98 期 2019 年第 1 期
小方坯凝固裂纹的影响因素与改善

小方坯凝固裂纹的影响因素与改善
铸坯从皮下到中心出现的裂纹都是内部裂纹,由于是在凝固过程中产生的裂纹,也叫凝固裂纹。
分析其影响因素有:
1、钢水的成分
1)碳含量
碳质量分数在0.16%以下时裂纹发生率最高,但碳质量分数大于0.16%时裂纹发生率明显降低。
因为碳质量分数在0.13-0.16%时正好处于包晶反应区,因此裂纹发生率高。
2)硫含量
随着钢中硫含量的增加,裂纹发生率迅速上升,当硫质量分数小于0.01%时,裂纹发生率为0,当硫质量分数大于0.02%时,裂纹发生率高达35%。
3)锰硫比
随着锰硫比的增加,裂纹发生率迅速下降,当锰硫比小于10时,裂纹发生率高达66.6 7%,当锰硫比大于30时,裂纹发生率降至15%。
2、过热度
降低过热度有利于降低裂纹发生率。
过热度控制在30℃以下时,裂纹发生率为5%左右,而当过热度超过30℃,裂纹发生率明显上升。
3、拉速
在工艺要求的范围内,拉速稳定于上限时,裂纹发生率最低。
根据以上分析,改善措施为:
1、碳含量按上限控制,避开包晶反应这一裂纹敏感区域;在各个工艺环节尽量降低硫含量,同时锰含量按工艺要求的上限控制,使锰硫比大于30。
2、控制过热度在20-30℃,采取低过热度的浇注方式防止坯壳薄而产生凹陷引起内裂。
3、拉速按上限控制,并尽量保持恒拉速,避免因拉速频繁变动引起的配水量和结晶器液面波动。
4、其他。
采用合理的结晶器倒锥度,优化水缝尺寸;根据不同的钢种,选择合适的保护渣;优化二冷水量,采用合理的弱冷制度;二冷区夹辊辊距要合适,要准确对弧,支撑辊间隙误差要符合技术要求。
裂纹原因分析

裂纹原因分析本页仅作为文档封面,使用时可以删除This document is for reference only-rar21year.March裂纹裂纹是锻压生产中常见的主要缺陷之一,通常是先形成微观裂纹,再扩展成宏观裂纹。
锻造工艺过程(包括加热和冷却)中裂纹的产生与受力情况、变形金属的组织结构、变形温度和变形速度等有关。
锻造工艺过程中除了工具给予工件的作用力之外,还有由于变形不均匀和变形速度不同引起的附加应力、由温度不均匀引起的热应力和由组织转变不同时进行而产生的组织应力。
应力状态、变形温度和变形速度是裂纹产生和扩展的外部条件;金属的组织结构是裂纹产生和扩展的内部依据。
前者是通过对金属组织及对微观机制的影响而对裂纹的发生和扩展发生作用的。
全面分析裂纹的成因应当综合地进行力学和组织的分析。
(一)形成裂纹的力学分析在外力作用下物体内各点处于一定应力状态,在不同的方位将作用不同的正应力及切应力。
裂纹的形式一般有两种:一是切断,断裂面是平行于最大切应力或最大切应变;另一种是正断,断裂面垂直于最大正应力或正应变方向。
至于材料产生何种破坏形式,主要取决于应力状态,即正应力σ与剪应力τ之比值。
也与材料所能承受的极限变形程度εmax及γmax有关。
例如,①对于塑性材料的扭转,由于最大正应力与切应力之比σ/τ=1是剪断破坏;②对于低塑性材料,由于不能承受大的拉应变,扭转时产生45°方向开裂。
由于断面形状突然变化或试件上有尖锐缺口,将引起应力集中,应力的比值σ/τ有很大变化,例如带缺口试件拉伸σ/τ=4,这时多发生正断。
下面分析不同外力引起开裂的情况。
1.由外力直接引起的裂纹压力加工生产中,在下列一些情况,由外力作用可能引起裂纹:弯曲和校直、脆性材料镦粗、冲头扩孔、扭转、拉拔、拉伸、胀形和内翻边等,现结合几个工序说明如下。
弯曲件在校正工序中(见图3-34)由于一侧受拉应力常易引起开裂。
例如某厂锻高速钢拉刀时,工具的断面是边长相差较大的矩形,沿窄边压缩时易产生弯曲,当弯曲比较严重,随后校正时常常开裂。
28 方坯表面横裂的原因分析及改进措施

纹敏感性强 ,经对横裂缺陷处取样做硫印检验 ,发现 均月发生 52支 ,较 2005年月减少横裂废品 80 t。年
在近铸坯表面有大颗粒的非金属夹杂物 ; 三是钢水 经济效益约 32万元 。
温度过低 ,铸坯在矫直区产生横裂纹 。 (2) 二次冷却的影响
5 结论
结晶器的工艺参数及振动参数对方坯表面横裂
二次冷却的影响主要是对铸坯热应力的影响 。 纹的产生有很大影响 ,采用合适的结晶器工艺参数 如果过度增大二冷冷却能力 ,会造成铸坯表面温降 及小振幅 、高振频的振动方式能很好着钢材市场的竞争日趋激烈 ,用户对钢材质
发生裂纹的主要原因是初生坯壳厚度不均匀 ,在
量的要求也提出了更高的要求 ,特别是近几年粗钢 坯壳薄的地方应力集中 ,当应力超过坯壳的抗拉强度
产量迅猛增长 、低技术含量的普通产品呈现供过于 时就产生裂纹。微裂纹形成后在外部因素的作用下可
2. 2 产生表面横裂的其他影响因素
(3) 加强结晶器的检验 ,淘汰不合格铜管 ,确保
(1) 钢水温度的影响
铜管工艺参数符合工艺要求 。
主要有三个方面 ,一是钢水过热度大 、坯壳薄且
(4) 加强振动机构的检验 ,保证其运行精度 ,避
热应力大 ,易产生裂纹 。经统计我厂钢水温度普遍 免偏振 、阻振现象 ,采用小振幅 (4mm)高振频 ( 230Hz)
均轧前挑废 244. 925 t,表面裂纹废品 156. 7 t。方坯 会发生包晶反应 ,促使在凝固点附近体积收缩率增
表面横裂废品占总内废的 51. 3% ,严重影响着方坯 大而产生表面裂纹 ,此范围属于裂纹敏感区 。研究
的钢水消耗和质量指标 ,给生产带来一系列的困难 。 表明 ,当碳含量在 0. 18% ~0. 22%铸坯凝固时 ,延
- 1、下载文档前请自行甄别文档内容的完整性,平台不提供额外的编辑、内容补充、找答案等附加服务。
- 2、"仅部分预览"的文档,不可在线预览部分如存在完整性等问题,可反馈申请退款(可完整预览的文档不适用该条件!)。
- 3、如文档侵犯您的权益,请联系客服反馈,我们会尽快为您处理(人工客服工作时间:9:00-18:30)。
工业纯铁方坯表面裂纹形成原因的分析
曾静许晓桂张友登刘静陈方玉
摘要采用金相检验、电子探针、透射电镜分析等方法,对工业纯铁方坯表面出现裂纹的原因进行了分析,结果表明:方坯在加热轧制过程中大量的第二相沿晶界析出是导致纯铁方坯产生网状裂纹的主要原因。
关键词工业纯铁析出物表面裂纹
CAUSE TO SURFACE CRACKING OF INDUSTRIAL PURE
IRON BILLETS
Zeng Jing Xu Xiao Gui Zhang Youdeng Liu Jing Chen Fangyu
(Wuhan Iron and Steel Corp.)
Synopsis Causes to the formation of the surfacecrackings in the pure industrial iron are analyzed by metalloscopy,electron probe micro-analysisand transmission electron microscope
examination .Results show that precipitation of the second phase in large quantity in the process of preheating billets is the primary cause leading to the occurrence of the reticular crackings in the pure industrial iron.
Keywords pure industrial iron precipitant surface cracking
1 前言
某厂生产的工业纯铁质量一直十分稳定,但在某次生产试验中,在加热轧成方坯后出现严重的表面裂纹。
本文对出现表面裂纹的原因进行了分析。
2 试验结果
2.1 化学成分分析
对纯铁缺陷方坯取样进行化学成分复验,结果列于表1。
表1 工业纯铁化学成分(w) %
2.2 宏观检验
图1为该工业纯铁轧成方坯后表面裂纹缺陷宏观照片。
裂纹大量分布于方坯表面和棱边,呈网络状、波纹状特征,裂口宽大且较深。
图1 表面裂纹缺陷宏观特征
2.3 酸浸低倍检验
取缺陷方坯横截面低倍试样,用过硫酸铵水溶液浸蚀后进行宏观低倍检查。
方坯A中裂纹由表面向内倾斜延伸,深度约5mm左右。
除4个角部晶粒较粗大外,整个截面上低倍组织均匀,局部可见少量针孔缺陷,见图2。
图2 方坯A低倍组织
方坯B中裂纹由表面向内倾斜延伸,深度约5~15mm,有的裂纹呈网络特征。
截面上晶粒明显不均匀,4个角部和心部晶粒明显粗大,局部地方有少许针孔缺陷,见图3。
图3 方坯B低倍组织
2.4 金相观察
在缺陷坯的裂纹部位取金相试样数件,分别磨制方坯的表面和截面观察。
磨掉表面氧化铁皮后可观察到除裂口较大的裂纹外,整个试样表面还分布有大量细小的网状裂纹。
在光学显微镜下,裂纹沿粗大的奥氏体晶界破坏,形态断续曲折,分支较多。
开裂处晶界氧化,氧化网络所勾画的晶粒轮廓颇为粗大。
用试剂浸蚀后观察,可见局部组织晶粒有反常长大特征,这些显微特征说明金属在加热炉内加热时温度有过高的倾向,见图4及图5。
图4 磨面为表面试样上裂纹沿晶界分布及周围组织晶粒反常长大特征
50×
图5 磨面为截面试样上裂纹沿晶界分布特征50×
光学显微镜下未观察到铜的富集相网络存在,亦未观察到非金属夹杂物与裂纹有关联的显微特征。
2.5 电子探针分析
用JXA8800R型电子探针对缺陷试样作微区成分分析,沿晶界裂纹内覆盖的灰色氧化物主要为氧化亚铁,局部细小裂纹(晶界)上有硫的偏聚分布。
某些开裂的晶界壁上可观察到韧窝花样,韧窝中附着一些化合物,它们的微区成份主要含O、Al、Si、S、Ca等元素。
这表明晶界裂纹是晶界析出物引起的沿晶韧性断裂。
2.6 透射电镜观察
在有裂纹的金相磨面上制成复型样,用JEM—2000FXⅡ型透射电镜观察,发现金属基体上有大量的第二相析出物质点。
图6为这些析出物质点透射扫描像,从图中可看出这些析出物质点有沿晶界分布的特征。
图7为析出物质点的透射形貌图,可见基体上还有更细小弥散分布的析出物质点。
对这些析出物质点作能谱分析,其主要成分为Cu、Mn、S、Fe,见图8及图9,可以判断它们是CuS、MnS和FeS的复相或单相析出物。
大的析出物质点尺寸在150nm左右,小的在几十nm左右。
图6 析出物质点透射扫描像×6K
图7 析出物质点形貌及分布×6K
图8 析出物质点透射图
图9 析出物质点透射能谱图
3 分析与讨论
(1)电子探针和透射电镜结果表明,工业纯铁方坯表面网状裂纹主要与钢中有大量第二相(Cu、FeS和MnS)析出物呈网络分布于晶界有关。
由于这些化合物有的熔点较低,当它们分布于晶界上时,在钢的轧制变形区间(1200~900℃)会成为熔融状态使钢的热塑性显著下降,而熔点高的析出物也抑制形变时晶界的迁移,使形变穿过晶粒的阻力增大,引起晶界应力集中并沿析出物产生微孔(韧窝)。
两类析出物的共同作用导致轧制变形中产生网裂。
钢中奥氏体晶界和晶内出现大量硫化合物析出的原因与钢中有效锰含量较低有关,据文献[1]介绍,低碳合金中发生与S和Mn含量相关的脆性 ,其临界条件是Mn/S<30,锰硫比低,脆性的倾向增大。
根据C.T.安德逊等人的意见[2],防止热脆性所需的锰浓度可由经验公式表示: w(Mn)=12.5w(S)+0.03
按照此公式计算,本文纯铁中S含量分别为0.0060%和0.0049%,其必需的Mn含量应分别为0.105%和0.09%,但从化学成份检验结果来看,该纯铁中的Mn含量仅分别为0.035%和0.044%,这样就不能保证钢中有足够量的锰含量仅分别为0.035%和0.044%,这样就不能保证钢中有足够量的锰与硫作用生成高熔点、稳定的MnS以限制硫的有害作用,钢中过量的硫会在轧制过程中与元素Cu、Fe作用形成低熔点化合物并优先在奥氏体晶界上析出,或者导致S的晶界偏析。
在文献报导,在超低碳钢中,如果Mn/S <20,只要钢的S含量大于30×10-6,就容易产生硫的晶界偏析,降低晶界强度,引起钢的热延性降低,而本文产生裂纹的钢坯Mn、S含量均满足这些条件。
(2)从低倍检验和金相组织上看,此方坯加热和轧制也不正常,表现为奥氏体晶粒颇为粗大,方坯截面组织不均匀和局部铁素体晶粒反常长大。
说明炉内加热温度偏高且不均匀,而加热温度愈高,高温下固溶于钢中的硫就会愈多。
这样,在轧制过程中可提供在奥氏体晶界析出或偏析的有效硫就愈多,对方坯表面裂纹缺陷的形成有一定促进作用。
4 结论
(1)工业纯铁方坯表面裂纹的形成主要是由于金属内大量CuS(含少量FeS、MnS)析出物质点呈网络状分布于晶界上,使晶界热塑性下降所致。
同时,该方坯加热温度偏高也进一步促进了表面缺陷的产生。
(2)控制适当的Mn/S比和合适的加热温度是避免方坯表面出现裂纹的主要措施。
联系人:曾静,工程师,武汉市(430080)武钢技术中心
作者单位:武汉钢铁集团公司
参考文献
1 G.A.Osinkolu, M.Taciowski,bined Effect of AIN and Sulphur on Hot Ductility of High-Purity Iron -Base
alloy.Materials Science and Technology,1985,1
2 赵坚,赵琳.优质钢缺陷.北京:治金工业出版社,1991。