第3讲 压铸工艺参数的选择
压铸原理及工艺参数选择
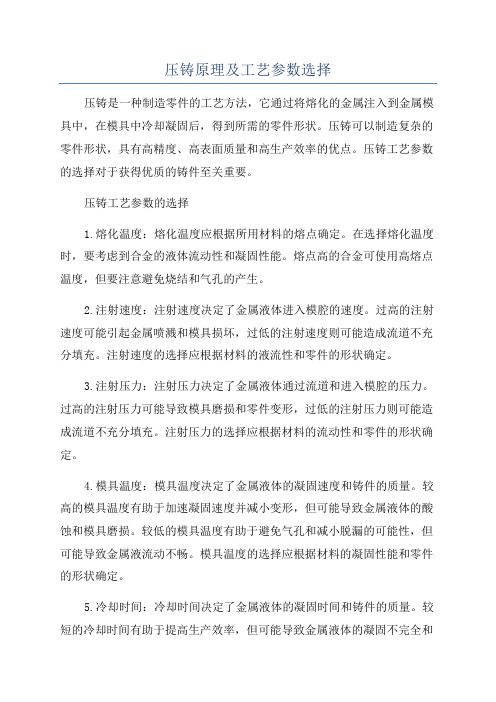
压铸原理及工艺参数选择压铸是一种制造零件的工艺方法,它通过将熔化的金属注入到金属模具中,在模具中冷却凝固后,得到所需的零件形状。
压铸可以制造复杂的零件形状,具有高精度、高表面质量和高生产效率的优点。
压铸工艺参数的选择对于获得优质的铸件至关重要。
压铸工艺参数的选择1.熔化温度:熔化温度应根据所用材料的熔点确定。
在选择熔化温度时,要考虑到合金的液体流动性和凝固性能。
熔点高的合金可使用高熔点温度,但要注意避免烧结和气孔的产生。
2.注射速度:注射速度决定了金属液体进入模腔的速度。
过高的注射速度可能引起金属喷溅和模具损坏,过低的注射速度则可能造成流道不充分填充。
注射速度的选择应根据材料的液流性和零件的形状确定。
3.注射压力:注射压力决定了金属液体通过流道和进入模腔的压力。
过高的注射压力可能导致模具磨损和零件变形,过低的注射压力则可能造成流道不充分填充。
注射压力的选择应根据材料的流动性和零件的形状确定。
4.模具温度:模具温度决定了金属液体的凝固速度和铸件的质量。
较高的模具温度有助于加速凝固速度并减小变形,但可能导致金属液体的酸蚀和模具磨损。
较低的模具温度有助于避免气孔和减小脱漏的可能性,但可能导致金属液流动不畅。
模具温度的选择应根据材料的凝固性能和零件的形状确定。
5.冷却时间:冷却时间决定了金属液体的凝固时间和铸件的质量。
较短的冷却时间有助于提高生产效率,但可能导致金属液体的凝固不完全和热裂纹的产生。
较长的冷却时间有助于提高铸件的密度和表面质量,但可能导致产量降低。
冷却时间的选择应根据材料的凝固性能和零件的形状确定。
总结压铸是一种高效、高精度的制造方法,工艺参数的选择对于获得优质的铸件至关重要。
在选择工艺参数时,要综合考虑材料的性质、零件的形状和制造要求,以及设备和模具的性能。
通过合理选择工艺参数,可以提高铸件的质量和生产效率,降低生产成本。
压铸件工艺参数的设定

压铸件工艺参数的设定2011-11-24 8:57:20在压铸行业,工艺参数对产品质量的影响更多的是靠试验的方法,许多工程技术人员不能深入的进行分析,生产铸件的条件无法用数据来描述。
本文就压铸工艺参数理论计算和实践两方面进行讨论研究。
压力铸造的主要工艺参数有行程(速度转换点)、速度、时间和压力等。
而本文重点分析速度和行程两个主要参数。
1. 压铸的四阶段压射计算压力铸造工艺参数,首先要定义压铸的四个压射阶段。
1.1.1 第一阶段:慢压射1为防止金属液溅出,冲头越过浇料口的过程,压射的第一阶段通常是缓慢的。
1.1.2 第二阶段:慢压射2金属液以较低的速度运动至内浇口的阶段,主要目的是排出压室内的空气,集中铝液于压室内。
1.1.3 第三阶段:快压射金属液由内浇口填充型腔直至充满为止,主要目的是成型并排出型腔中气体。
1.1.4 第四阶段:增压阶段型腔充满后建立最后的增压,使铸件在高压压力下凝固,从而使铸件致密。
1.2 计算模型1.2.1 根据1.1定义(参照图1),可以得到金属液在各阶段合金液的重量关系式。
G2=G浇G3+G4=G铸+G溢流其中:G3+G4为金属液刚达到内浇口处时冲头端面至冲头停止之间的铝液重量,即为快压射起始点位置至冲头停止行程内金属液的容量。
G铸为铸件重量G溢为溢流系统的重量G2为慢压射2行程内压室能容纳的金属液重量G浇为浇注系统的重量1.2.2 流道中单位时间内不同位置截面中通过合金液的流量关系式(见图2)金属液在流动过程中,单位时间内通过截面的流量Q相等,则Q=V1×S1=V2×S2= V3×S3 (注:V3×S3是利用等式,而非金属液流量)其中V1:冲头速度S1:冲头面积V2:内浇口速度S2:内浇口面积V3:排气槽气体速度(推荐值75m/s)S3:排气槽的面积1.2.3压铸时间[1]压铸时间包括充填时间,持压时间及铸件在压铸模型中停留的时间。
压铸工艺参数分析

压铸工艺参数分析1.注射压力:注射压力是指在铸造过程中,金属熔液被压入型腔的压力大小。
注射压力的大小对于铸件的排气、充盈、凝固过程以及零部件的尺寸稳定性有着重要的影响。
过高的注射压力会导致铸件内部气泡的形成、表面粗糙度增大等问题,而过低的注射压力则会导致型腔内充盈不充分。
2.注射速度:注射速度是指熔融金属进入模具腔体的速度。
适当的注射速度可以使熔融金属在型腔内充盈均匀,防止铸件出现疏松、夹杂等缺陷。
过高的注射速度会导致金属熔液的剪切力增加,容易产生气泡和金属破碎现象,而过低的注射速度则会导致金属熔液在充盈过程中受到阻力,形成冷障。
3.注射温度:注射温度是指金属熔液注入型腔时的温度。
注射温度的高低会直接影响到铸件的凝固形态和组织结构。
过高的注射温度会导致铸件的表面质量较差,因为金属熔液的冷却速度过快,易产生冷障和贝氏体组织。
而过低的注射温度则会导致金属熔液黏度增大,充盈性变差。
4.金属液温度:金属液温度是指金属熔体在注射之前的温度。
金属液温度的高低会直接影响到铸件的凝固过程和性能。
过高的金属液温度会导致铸件的组织粗大,出现热裂纹等问题。
而过低的金属液温度则会导致铸件的毛细孔增多,降低铸件的密实性。
5.压射机的闭模力:压射机的闭模力是指用于关闭型腔的力大小。
闭模力的大小会直接影响到铸件的尺寸稳定性和机械性能。
过高的闭模力会导致铸件的尺寸过大,形成表面凸起和冷障等问题。
而过低的闭模力则会导致铸件尺寸的不稳定性和机械性能的下降。
6.模具温度:模具温度是指模具在铸造过程中的温度。
模具温度的高低会直接影响到铸件的组织结构和表面质量。
适当的模具温度可以提高铸件的表面光洁度,减少气孔和缩松等问题。
过高的模具温度会导致铸件的热组织粗大,而过低的模具温度则会导致铸件充盈性差。
总结起来,压铸工艺参数对于铸件质量和性能有着直接的影响。
合理的控制和选择工艺参数可以有效地改善铸件的表面质量、减少缺陷率,提高铸件的力学性能和尺寸稳定性。
压铸件工艺参数的设定
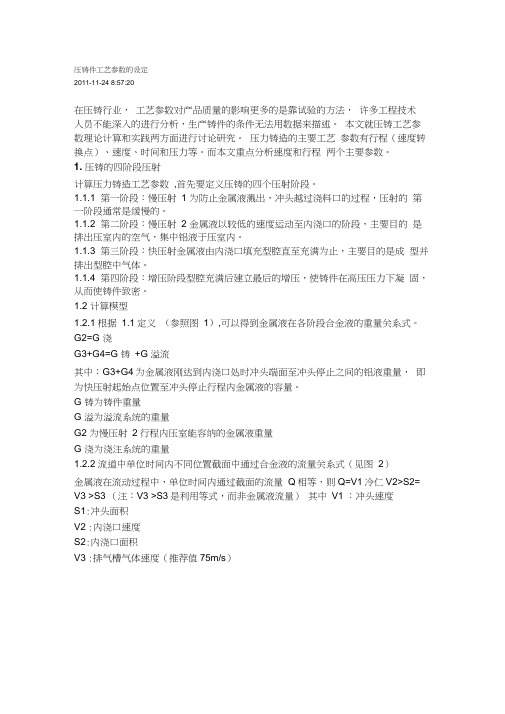
压铸件工艺参数的设定2011-11-24 8:57:20在压铸行业,工艺参数对产品质量的影响更多的是靠试验的方法,许多工程技术人员不能深入的进行分析,生产铸件的条件无法用数据来描述。
本文就压铸工艺参数理论计算和实践两方面进行讨论研究。
压力铸造的主要工艺参数有行程(速度转换点)、速度、时间和压力等。
而本文重点分析速度和行程两个主要参数。
1. 压铸的四阶段压射计算压力铸造工艺参数,首先要定义压铸的四个压射阶段。
1.1.1 第一阶段:慢压射1 为防止金属液溅出,冲头越过浇料口的过程,压射的第一阶段通常是缓慢的。
1.1.2 第二阶段:慢压射2 金属液以较低的速度运动至内浇口的阶段,主要目的是排出压室内的空气,集中铝液于压室内。
1.1.3 第三阶段:快压射金属液由内浇口填充型腔直至充满为止,主要目的是成型并排出型腔中气体。
1.1.4 第四阶段:增压阶段型腔充满后建立最后的增压,使铸件在高压压力下凝固,从而使铸件致密。
1.2 计算模型1.2.1 根据1.1定义(参照图1),可以得到金属液在各阶段合金液的重量关系式。
G2=G 浇G3+G4=G 铸+G 溢流其中:G3+G4为金属液刚达到内浇口处时冲头端面至冲头停止之间的铝液重量,即为快压射起始点位置至冲头停止行程内金属液的容量。
G 铸为铸件重量G 溢为溢流系统的重量G2 为慢压射2 行程内压室能容纳的金属液重量G 浇为浇注系统的重量1.2.2 流道中单位时间内不同位置截面中通过合金液的流量关系式(见图2)金属液在流动过程中,单位时间内通过截面的流量Q相等,则Q=V1冷仁V2>S2= V3 >S3 (注:V3 >S3是利用等式,而非金属液流量)其中V1 :冲头速度S1:冲头面积V2 :内浇口速度S2:内浇口面积V3 :排气槽气体速度(推荐值75m/s)铸时间[1]压铸时间包括充填时间,持压时间及铸件在压铸模型中停留的时间。
123.1充填时间:金属液开始进入内浇口到型腔充满所需的时间。
压力铸造工艺参数的选择

压力铸造工艺参数的选择压力铸造high pressure die casting(简称压铸)的实质是在高压作用下,使液态或半液态金属以较高的速度充填压铸型(压铸模具)型腔,并在压力下成型和凝固而获得铸件的方法。
与其它铸造方法相比,压铸有铸件尺寸精度高,产品质量好,生产效率高以及经济效益高等优势。
压力铸件的质量主要受控于压铸的填充过程中诸多因素的影响,如:压力、速度、温度、熔融金属的性质以及填充特性等等。
所以工艺参数的选择成为决定压力铸件是否成功的关键因素。
压铸工艺是将压铸机、压铸模和压铸合金综合运用的过程。
压铸时金属填充型腔的过程,是将压力、速度、温度以及时间等工艺因素得到有机组合的过程。
这些工艺因素既相互制约,相辅相成,只有正确选择和调整这些因素,使之协调一致,才能获得预期的结果。
压射过程中,不仅重视铸件结构的工艺性、铸型的先进性、压铸机性能和结构优良性,压铸合金选用的适应性和熔炼工艺的规范性。
也应重视压力、速度、温度和时间等工艺参数对铸件质量的重要作用。
这些工艺参数的选择与合理匹配,是保证压铸件综合性能的关键。
一、压力的选择在压力铸造的整个过程中,压射压力是压铸工艺最基本的成型参数,液态金属的充填流动和压实都是在压力和充填速度的作用下完成的,合理选择和确定压射压力和充填速度是压铸工艺的一个重要问题。
在压射过程中,随着冲头位置的移动,压力也出现不同的变化,这个变化规律都会对铸件质量产生重大影响。
1.压射力(F)压射力是压铸机压射机构中推动压射活塞运动的力,它是反映压铸机功能的一个主要参数。
压射力的大小,由压射缸的截面积和工作液的压力所决定。
压射力的计算公式如下:F=PπD²/4式中:F--压射力(N);P--压射油缸内工作液的压力(Pa);D--压射油缸的直径(m);π=3.1416。
2.比压(P)及其选择比压是压室内金属液单位面积上所受的压力,填充时的比压称为压射比压。
压射后的比压称为增压比压,它决定了压铸件最终所受的压力和模具的胀型力。
第3讲 压铸工艺参数的选择
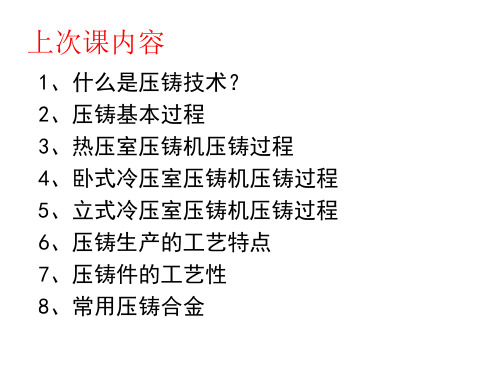
Fz主 pb A
式中:Fz主——主胀型力(N); pb ——压射比压(MPa); A ——压铸件在分型面的投影面积总和,一般另加30%作为浇注
系统与溢流排气系统的面积(mm2)。
(2)分胀型力
分胀型力:作用在滑块锁紧面上的法向分力引起的胀型力之和。 采用斜销抽芯、斜滑块抽芯机构时的分胀型力可按下式计算:
pb
Fy A
4Fy
d 2
式中:pb ——压射比压(MPa); Fy ——压射力; A ——压射冲头截面积(mm2); d ——压射冲头直径(mm)。
(2)压射比压的选择和调整
生产中根据铸件的形状尺寸、结构复杂程度、壁厚大小以 及压铸合金的特性和压铸温度,模具的浇注系统及排溢系统 设计情况等确定压射比压。
一般压铸件可按计算数值提高1.2倍,对有较大镶件的压铸 件或大模具压小铸件时可提高1.5~2倍。
2.充填速度
在压射冲头作用下,熔融合金通过内浇口进入型腔的线速度 称为充填速度。
充填速度偏低易造成铸件轮廓不清晰;采用较高的充填速度 可获得轮廓清晰、表面光洁的铸件。但是充填速度过高,易使 压铸件产生气泡,还会加速模具工作零件的磨损。
一.压力
1.压射力
压铸机压射缸内的工作液作用于 压射冲头,使其推动熔融合金充填 模具型腔的力。
(1)压射力变化规律 分为四个阶段: 第Ⅰ阶段:排气阶段; 第Ⅱ阶段:熔融合金堆积阶段; 第Ⅲ阶段:充填阶段; 第Ⅳ阶段:增压阶段。
(2)压射力计算
有增压机构时:
Fy
1 4
p zg D 2
无增压机构时:
Fz分 (A分 pb tan)
胀型力:
Fz FZ主 FZ分 (A A分 tan) pb
压铸工艺参数公式
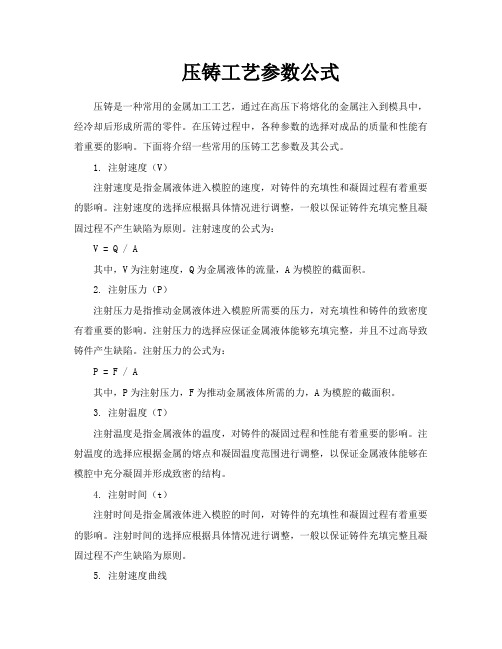
压铸工艺参数公式压铸是一种常用的金属加工工艺,通过在高压下将熔化的金属注入到模具中,经冷却后形成所需的零件。
在压铸过程中,各种参数的选择对成品的质量和性能有着重要的影响。
下面将介绍一些常用的压铸工艺参数及其公式。
1. 注射速度(V)注射速度是指金属液体进入模腔的速度,对铸件的充填性和凝固过程有着重要的影响。
注射速度的选择应根据具体情况进行调整,一般以保证铸件充填完整且凝固过程不产生缺陷为原则。
注射速度的公式为:V = Q / A其中,V为注射速度,Q为金属液体的流量,A为模腔的截面积。
2. 注射压力(P)注射压力是指推动金属液体进入模腔所需要的压力,对充填性和铸件的致密度有着重要的影响。
注射压力的选择应保证金属液体能够充填完整,并且不过高导致铸件产生缺陷。
注射压力的公式为:P = F / A其中,P为注射压力,F为推动金属液体所需的力,A为模腔的截面积。
3. 注射温度(T)注射温度是指金属液体的温度,对铸件的凝固过程和性能有着重要的影响。
注射温度的选择应根据金属的熔点和凝固温度范围进行调整,以保证金属液体能够在模腔中充分凝固并形成致密的结构。
4. 注射时间(t)注射时间是指金属液体进入模腔的时间,对铸件的充填性和凝固过程有着重要的影响。
注射时间的选择应根据具体情况进行调整,一般以保证铸件充填完整且凝固过程不产生缺陷为原则。
5. 注射速度曲线注射速度曲线是指注射过程中注射速度随时间的变化规律。
注射速度曲线的选择应根据具体情况进行调整,一般以保证铸件充填完整且凝固过程不产生缺陷为原则。
6. 注射压力曲线注射压力曲线是指注射过程中注射压力随时间的变化规律。
注射压力曲线的选择应根据具体情况进行调整,一般以保证铸件充填完整且凝固过程不产生缺陷为原则。
以上所述的压铸工艺参数及其公式只是一些常用的参考,实际应用中还需要根据具体情况进行调整和优化。
压铸工艺的优化是一个综合性的问题,需要考虑材料的性质、模具的设计、设备的性能等多个方面因素的综合影响。
压铸工艺参数

压铸工艺参数
一、压铸机参数
1.锁模力:压铸机锁模力是指压铸机在关闭模具时施加在模具上的力量,这个参数的选取要根据铸件的大小和形状来确定。
2.注射压力:指压铸机在注入合金液态金属时向模腔施加的压力,需
要根据合金的液态流动性来设定。
3.注射速度:指合金液态金属进入模腔的速度,需要控制在合适的范
围内,既要保证充模完全,又要避免过快造成气孔和模具损坏。
二、模具参数
1.冷却系统:合理的冷却系统可以提高铸件的质量和生产效率,可以
通过冷却水的流量、温度和冷却通道的设计来控制。
2.喷油系统:喷油系统用于在压铸之前,在模具表面形成一层润滑膜,减少金属与模具的摩擦,需要控制喷油量和喷油位置。
3.模具温度:模具温度会影响合金凝固速度和铸件表面质量,可以通
过加热、降温等方式来控制。
三、材料参数
1.合金成分:合金成分是对压铸件的力学性能和化学性能有很大影响
的因素,需要根据产品的要求选择合适的合金成分。
2.熔化温度:合金的熔化温度会影响注入流动性和凝固速度,需要根
据合金的熔化温度范围进行控制。
3.熔金温度:熔金温度是指合金进入模腔前的温度,需要根据合金的熔点和凝固温度来确定。
除了以上介绍的参数,还有一些其他的因素也会影响压铸工艺,比如模具的设计、铸件的几何形状以及工艺操作等。
这些参数和因素都需要通过实践和不断探索来确定和优化,以提高压铸的质量和效率。
对于不同的产品和工艺需求,压铸工艺参数也会有所差别,因此需要根据具体情况进行调整和优化。
- 1、下载文档前请自行甄别文档内容的完整性,平台不提供额外的编辑、内容补充、找答案等附加服务。
- 2、"仅部分预览"的文档,不可在线预览部分如存在完整性等问题,可反馈申请退款(可完整预览的文档不适用该条件!)。
- 3、如文档侵犯您的权益,请联系客服反馈,我们会尽快为您处理(人工客服工作时间:9:00-18:30)。
1 tm t j 25 3
式中:tm——模具工作温度; tj ——浇注温度
四.时间
1.充填时间 熔融合金从开始进入型腔到充满所需的时间。与压铸件 体积、复杂程度及压射比压、内浇口截面积等因素有关。 一般充填时间很短,在0.01~0.2s之间,根据生产实际进 行调整。 2.增压建压时间 是指熔融合金在充模的增压阶段,从充满型腔的瞬时开始, 至达到预定的增压压力所需的时间。该时间愈短愈好,但受 限于压铸机性能至少也要0.01~0.2s。
3.涂料种类 P25表1-32 4.涂敷 可喷涂、刷涂,均匀,不能太厚。不一定 每次压铸后都要涂,主要看压铸件大小质 量,以打出合格铸件为准。
例1-1
如图所示屏蔽盒压铸件,其材料为YZAlSi2,压铸件未注尺 寸精度取IT14级,未注铸造圆角R1.5mm。试对该压铸件进行 工艺分析制订压铸工艺。
3.保压时间
熔融合金充满型腔到凝固前,增压比压持续的时间。保压 可以加强补锁,获得组织更加致密的压铸件。 保压时间一般为1~2s,对于结晶温度范围大、壁厚的压铸 件可长些约为2~3s。
4.留模时间
指保压时间终了到开模推出压铸件的时间。以推出压铸件 不变形、不开裂的最短时间为宜。
在压铸工艺参数中,压力、速度、温度及 时间互相影响。相辅相成,互相制约。 复杂厚壁铸件——压力大 复杂薄璧铸件——速度高、浇注温度高、模 具温度高。 大而简单的铸件,充填时间长些,复杂和薄 壁铸件充填时间短些。
pb
Fy A
4 Fy
d 2
式中:pb ——压射比压(MPa); Fy ——压射力; A ——压射冲头截面积(mm2); d ——压射冲头直径(mm)。
(2)压射比压的选择和调整
生产中根据铸件的形状尺寸、结构复杂程度、壁厚大小以 及压铸合金的特性和压铸温度,模具的浇注系统及排溢系统 设计情况等确定压射比压。 一般压铸件的形状复杂,工艺条件较为苛刻时,常采用高 的压射比压和增压比压。但是过高的比压会使铸件质量变差, 降低模具寿命。 因此,在满足要求的前提下,尽可能选择较低的压射比压 和增压比压。
五.涂料
1.压铸涂料的作用 (1)避免熔融合金直接冲刷型芯和型腔表面,改善模具工作条 件; (2)防止粘模; (3)降低模具导热率,保持熔融合金的流动性,改善成型条件; (4)减小压铸件与模具成型部分的摩擦,便于推出压铸件。 2.对压铸涂料的要求 (1)高温时具有良好的润滑作用; (2)挥发点低,在100~150℃时,稀释剂能很快挥发; (3)涂敷性好,且对压铸件和模具无腐蚀作用; (4)性能稳定,无环境污染; (5)配置工艺简单,原材料丰富,价格低廉。
上次课内容
1、什么是压铸技术? 2、压铸基本过程 3、热压室压铸机压铸过程 4、卧式冷压室压铸机压铸过程 5、立式冷压室压铸机压铸过程 6、压铸生产的工艺特点 7、压铸件的工艺性 8、常用压铸合金
第四节 压铸工艺参数的选择
正确地选择和调整压铸工艺参数,尤其
是压射压力、压射速度、浇注温度和压铸
模温度以及充填时间等工艺参数,是保证
2.什么是充填速度?充填速度的高低对压铸件有何 影响? 答:在压射冲头作用下,熔融合金通过内浇口进入 型腔的线速度称为充填速度。 充填速度偏低易造成铸件轮廓不清晰;采用较高 的充填速度可获得轮廓清晰、表面光洁的铸件。但 是充填速度过高,易使压铸件产生气泡,还会加速 模具工作零件的磨损。 3.压铸生产中需要控制的温度有哪些? 答:浇注温度和模具温度。
压铸件质量、发挥压铸机的最大生产率和
正确设计压铸模的依据。
一.压力
1.压射力
压铸机压射缸内的工作液作用于
压射冲头,使其推动熔融合金充填 模具型腔的力。 (1)压射力变化规律 分为四个阶段:
第Ⅰ阶段:排气阶段;
第Ⅱ阶段:熔融合金堆积阶段; 第Ⅲ阶段:充填阶段; 第Ⅳ阶段:增压阶段。
(2)压射力计算
(2)分胀型力
分胀型力:作用在滑块锁紧面上的法向分力引起的胀型力之和。 采用斜销抽芯、斜滑块抽芯机构时的分胀型力可按下式计算:
Fz分 ( A分 pb tan )
胀型力:
Fz FZ主 FZ分 ( A A分 tan ) pb
式中: Fz分——由法向分力引起的分胀型力,为各个型芯产 生法向分力之和(N); A分——侧向活动型芯成型端面的投影面积(mm2) ; α ——楔紧块的楔紧角(°); Fz ——胀型力(N)。
二.速度
1.压射速度 压铸过程中,压射冲头移动的线速度称为压射速度。 压射过程第Ⅰ、Ⅱ阶段采用低速压射。 第Ⅲ阶段采用高速压射:
v yh
式中:vyh——高速压射速度(m/s); V——型腔容积(mm3); n ——型腔数; d ——压射冲头直径(mm); τ ——充填时间(s);
40V 1 0.1n 1 2 d
1.压铸件结构工艺性分析
屏蔽盒最小壁厚2.5mm,查表可知其符合工艺要求,方孔
5×10mm也符合工艺要求。尺寸 10 0 0.5
mm接近IT15级,
其余为IT14均符合工艺要求。铸造圆角R3mm、R5mm和为铸造
圆角R1.5mm均符合工艺要求。 因此,屏蔽盒符合压铸工艺要求。
2.工艺规程制订
一般压铸件可按计算数值提高1.2倍,对有较大镶件的压铸 件或大模具压小铸件时可提高1.5~2倍。
2.充填速度
在压射冲头作用下,熔融合金通过内浇口进入型腔的线速度 称为充填速度。 充填速度偏低易造成铸件轮廓不清晰;采用较高的充填速度 可获得轮廓清晰、表面光洁的铸件。但是充填速度过高,易使 压铸件产生气泡,还会加速模具工作零件的磨损。 充填速度与内浇口截面积有关,内浇口截面积小,充填速度 高,反之充填速度低。 通过调整压射速度,改变压射冲头直径、压射比以及内浇口 截面积等,都可以直接或间接调整充填速度。
总结
本章主要讲述金属压铸生产的基本原理、压铸件的工 艺性、常用压铸合金及压铸工艺参数。重点内容是压铸件 的结构工艺性、压铸工艺参数的确定与调整。
通过本章的学习,能够正确设计压铸件,并合理选择和
调整压铸过程中的压力、速度、温度和时间等工艺参数,
正确使用压铸模涂料,使压铸件符合质量要求。
作业:
1.如何选择压射比压? 答:生产中根据铸件的形状尺寸、结构复杂程度、壁厚大小 以及压铸合金的特性和压铸温度,模具的浇注系统及排溢系 统设计情况等确定压射比压。 一般压铸件的形状复杂,工艺条件较为苛刻时,常采用高 的压射比压和增压比压。但是过高的比压会使铸件质量变差, 降低模具寿命。 因此,在满足要求的前提下,尽可能选择较低的压射比压 和增压比压。
有增压机构时:
1 Fy p zgD 2 4
无增压机构时:
Fy
1 p g D 2 4
式中:Fy ——压射力; pzg——增压后,压射缸内的工作压力(MPa); pg ——压射缸内的工作压力(MPa); D ——压射缸的直径(mm)。
2.压射比压
(1)压射比压 是指在压室内,熔融合金单位面积上所受到的压力,充填 阶段的压力称为压射比压。压实阶段的比压称为增压比压。 压射比压可按下式计算:
三.温度
1.合金浇注温度 熔融合金自压室进入型腔的平均温度。 浇注温度过高,压铸件易变形开裂;过低,则造成充填 困难,易产生冷隔、表面流纹和浇注不足等缺陷。
2.模具温度
即模具的工作温度。压铸前应对模具充分预热到一定程度,主 要是基于如下考虑: (1)避免模具激热而胀裂; (2)避免熔融合金激热而充型困难,产生冷隔,造成开裂; (3)降低型腔中空气密度,利于排气。 压铸模工作温度按下式计算:
3.胀型力
充填型腔时,熔融合金对型腔壁和分型面的作用力。 (1)主胀型力:压铸件在分型面上的投影面积与压射比压的 乘积
Fz主 pb A
式中:Fz主——主胀型力(N); pb ——压射比压(MPa); A ——压铸件在分型面的投影面积总和,一般另加30%作为浇注 系统与溢流排气系统的面积(mm2)。