支架零件图设计
支座铸造工艺设计.

热加工工艺课程设计支座铸造工艺设计院系:工学院机械系专业:机械设计制造及其自动化班级:机电n班姓名:欢迎学弟学妹咨询学号:qq********指导老师:***时间:2012年6月2日黄河科技学院课程设计任务书工学院机械系机械设计制造及其自动化专业2011级班学号姓名指导教师刘万福设计题目: 支座铸造工艺设计课程名称:热加工工艺课程设计课程设计时间:5 月26 日至6 月 2 日共 2 周课程设计工作内容与基本要求(已知技术参数、设计要求、设计任务、工作计划、所需相关资料)(纸张不够可加页)1、已知技术参数:图1 支座零件图2、设计任务与要求:(1)设计任务1 选择零件的铸型种类,并选择零件的材料牌号。
2 分析零件的结构,找出几种分型方案,并分别用符号标出。
3 从保证质量和简化工艺两方面进行分析比较,选出最佳分型方案,标出浇注位置和造型方法。
4 画出零件的铸造工艺图(图上标出最佳浇注位置与分型面位置、画出机加工余量、起模斜度、铸造圆角、型芯及型芯头,图下注明收缩量)5 绘制出铸件图。
(2)设计要求1设计图样一律按工程制图要求,采用手绘或机绘完成,并用三号图纸出图。
2 按所设计内容及相应顺序要求,认真编写说明书(不少于3000字)。
3、工作计划熟悉设计题目,查阅资料,做准备工作1天确定铸造工艺方案1天工艺设计和工艺计算2天绘制铸件铸造工艺图1天确定铸件铸造工艺步骤2天编写设计说明书3天答辩 1天4.主要参考资料《热加工工艺基础》、《金属成形工艺设计》、《机械设计手册》系主任审批意见:审批人签名:时间:2012年月日黄河科技学院课程设计说明书第1页摘要热加工技术是机械类个专业一门重要的综合性技术学科。
在机械制造过程中,由于加工过程十分复杂,加工工序繁多,工艺过程不仅有铸造成型,锻压成形,焊接成形,还有非金属的模压成形,挤压成形等。
因此选着合适的工艺是保证产品质量的重要依据。
本次课程设计,将进行铸造工艺的总结和学习。
支架零件铸造工艺设计说明书

支架零件铸造工艺设计一、零件的生产条件、结构及技术要求1、生产性质:大批量生产2、材料:HT2003、零件加工方法:零件上有多个孔,除中间的大孔需要铸造以外,其他孔在考虑加工余量后不宜铸造成型,采用机械方法加工,均不铸出。
造型方法:机器造型;造芯方法:机器制芯4、主要技术要求:满足HT200的机械性能要求,去毛刺及锐边,铸件表面不允取有缺陷。
二、零件图及立体图结构分析1、零件图如下:零件主视图零件俯视图2、立体图如下:三、工艺设计过程1、铸造工艺设计方法及分析(1)铸件壁厚为了避免浇不到、冷隔等缺陷,铸件不应太薄。
铸件的最小允许壁厚与铸造的流动性密切相关。
在普通砂型铸造的条件下,铸件最小允许壁厚见表1。
表1. 铸件最小允许壁厚查得灰铁铸件在100~200mm的轮廓尺寸下,最小允许壁厚为5~6mm。
由零件图可知,零件中不存在壁厚小于设计要求的结构,在设计过程中,也没有出现壁厚小于最小壁厚要求的情况。
(2)造型、制芯方法造型方法:该零件需批量生产,为中小型铸件,因此,采用湿型粘土砂机器造型,模样采用金属模,采用技术先进的机器造型。
制芯方法:在造芯用料及方法选择中,如用粘土砂制作砂芯原料成本较低,但是烘干后容易产生裂纹,容易变形。
在大批量生产的条件下,由于需要提高造芯效率,且常要求砂芯具有高的尺寸精度,此工艺所需的砂芯采用热芯盒法生产砂芯,以增加其强度及保证铸件质量。
选择使用射芯工艺生产砂芯。
采用热芯盒制芯工艺热芯盒法制芯,是用液态固性树脂粘结剂和催化剂制成的一种芯砂,填入加热到一定的芯盒内,贴近芯盒表面的砂芯受热,其粘结剂在很短的时间内硬化。
而且只要砂芯表层有数毫米的硬壳即可自芯取出,中心部分的砂芯利用余热可自行硬化。
(3)砂箱中铸件数目的确定及排布初步确定一箱中放几个铸件,作为进行浇冒口设计的依据。
一箱中的铸件数目,应该是在保证铸件质量的前提下越多越好。
本铸件在一砂箱中高约130mm,长约200mm,宽约110mm,体积约99.7cm^3,密度7.2g/cm^3,重约0.8Kg。
机械制图任务6.2 支架零件图的识读
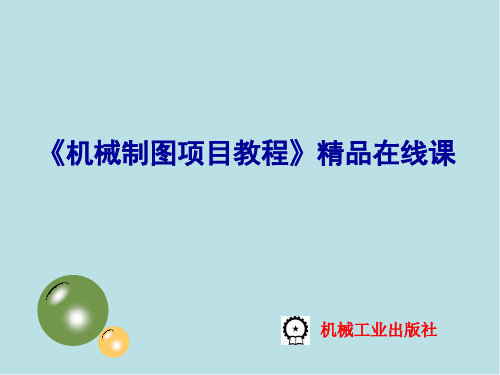
遵守课堂纪律
5
5
总分
100
综合评价(自评分×20%+互评分×40%+组长或教师*评分×40%)
教师签字:
签名:
成绩
参考学时
4
互评
组长或教师﹡评 分
日期:
任务引入
任务分析
从上图所示的零件图可知,该零件图属于典型的叉 架类零件,通过识读零件图想象出支架空间结构图,我 们必须掌握叉架类零件图表达方案、分析叉架类零件的 尺寸标注、技术要求等相关知识。
知识链接
1)零件图的识读方法与步骤及其测绘的相关知识(详见项目三中的任务三) 2)叉架类零件图的特点: (1)结构特点 支架类零件通常由工作部分、支承(或安装)部分及连接部分 组成,形状比较复杂且不规则。零件上常有叉形结构、肋板和孔、槽等。 (2)加工方法 毛坯多为铸件或锻件,经车、镗、铣、刨、钻等多种工序加工 而成。 (3)视图表达 一般需要两个以上基本视图表达。常以工作位置为主视图,反 映重要形状特征。连接部分和细部结构采用局部视图或斜视图、并用剖视图、断面 图、局部放大图表达局部结构。 (4)尺寸表注 尺寸标注比较复杂。各部分的形状和相对位置的尺寸要直接标 注。尺寸基准常选择安装基面、对称平面、孔的中心线和轴线。定位尺寸较多,往 往还有角度尺寸。为了便于制作木模,一般采用形体分析法标注定形尺寸。 (5)技术要求 支承部分、运动配合面,均有较严的尺寸公差、形位公差和表 面粗糙度要求。
任务计划与决策
专业 组别
班级 任务名称
支架零件图的识读
任
务 计
各组根据任务内容制定支架零件图的识读的任务计划
划
项目
可选方案
方案分析
任
方案1
务 决
支架夹具设计说明

题 目 支架钻孔加工专用夹具设计院(系)别 机电及自动化学院专 业 机械制造及其自动化级 别 2009级学 号 0911116036姓 名 沈华坤指导老师 黄国钦 华侨大学机电及自动化学院2012年10月专业课程综合设计目录第一章夹具设计任务 (1)1.1 零件(产品)结构分析及零件图 (1)1.2 支架钻孔工序的重点技术要求分析 (2)第二章拨叉夹具设计方案的确定 (3)2.1 基准面的选择(夹具体方案的确定) (3)2.2 定位方式及定位元件的选择 (3)2.3 夹紧方案及夹紧元件选择 (3)2.4夹具结构 (4)第三章主要零件设计及计算说明 (6)3.1夹紧力计算 (6)3.2其他零件设计计算 (8)第四章夹具定位误差计算 (14)第五章夹具的装配要求及使用说明 (15)参考文献附录第一章夹具设计任务1.1零件(产品)结构分析及零件图1、零件的二维图如图1.1所示图1.1 支架CAD图2、零件的三维图如图1.2所示图1.2 支架三维图1.2 支架钻孔工序六的重点技术要求分析1、支架钻孔工序图六如图1.3所示图1.3 工序图2、工装及切削要素数据表如表1.1所示表1.1工装及切削要素数据表如表 工步号 工 步 内 容工 艺 装 备 主轴转速 切削速度 进给量 切削深度 进给次数 工步工时 r/min m/min mm/r mm 机动 辅助 01 钻与φ18垂直的孔φ10至φ9.8X525卧式铣床 545 17.1 0.4 4.9 1 0.18 02 粗铰与φ18垂直的孔φ10 锥柄麻花钻8.9φ 680 21 0.3 0.1 1 0.153、工序的重点技术要求分析由工件的零件图和三维立体图可以看出,钻与18φ垂直的孔10φ至8.9φ的重点是保证两通孔的垂直度要求。
故夹具体应围绕保证其垂直度的精度来设计,同时也要保证其表面粗糙度及位置精度。
第二章支架夹具设计方案的确定2.1 基准面的选择(夹具体方案的确定)因采用卧式钻床,故待加平面处于水平位置。
复合模实例
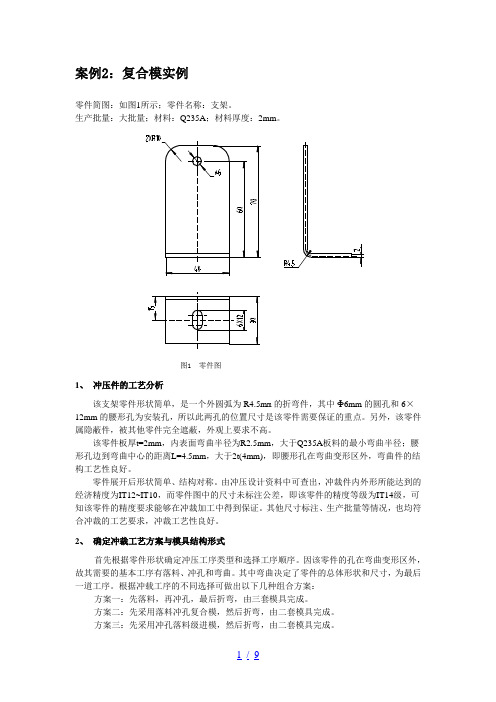
案例2:复合模实例零件简图:如图1所示;零件名称:支架。
生产批量:大批量;材料:Q235A;材料厚度:2mm。
图1 零件图1、冲压件的工艺分析该支架零件形状简单,是一个外圆弧为R4.5m m的折弯件,其中Ф6mm的圆孔和6×12mm的腰形孔为安装孔,所以此两孔的位置尺寸是该零件需要保证的重点。
另外,该零件属隐蔽件,被其他零件完全遮蔽,外观上要求不高。
该零件板厚t=2mm,内表面弯曲半径为R2.5mm,大于Q235A板料的最小弯曲半径;腰形孔边到弯曲中心的距离L=4.5mm,大于2t(4mm),即腰形孔在弯曲变形区外,弯曲件的结构工艺性良好。
零件展开后形状简单、结构对称。
由冲压设计资料中可查出,冲裁件内外形所能达到的经济精度为IT12~IT10,而零件图中的尺寸未标注公差,即该零件的精度等级为IT14级,可知该零件的精度要求能够在冲裁加工中得到保证。
其他尺寸标注、生产批量等情况,也均符合冲裁的工艺要求,冲裁工艺性良好。
2、确定冲裁工艺方案与模具结构形式首先根据零件形状确定冲压工序类型和选择工序顺序。
因该零件的孔在弯曲变形区外,故其需要的基本工序有落料、冲孔和弯曲。
其中弯曲决定了零件的总体形状和尺寸,为最后一道工序。
根据冲载工序的不同选择可做出以下几种组合方案:方案一:先落料,再冲孔,最后折弯,由三套模具完成。
方案二:先采用落料冲孔复合模,然后折弯,由二套模具完成。
方案三:先采用冲孔落料级进模,然后折弯,由二套模具完成。
比较上述各方案可以看出,方案一的优点是:模具结构简单、寿命长、制造周期短、投产快。
缺点是:工序分散,需用模具、压力机和操作人员较多,劳动生产率低。
方案二落料冲孔在一道工序内完成,内、外形的位置尺寸精度高,工件的平整性好;方案三由于是先冲孔后落料,内、外形的位置尺寸精度不如方案二高,工件易弯曲,平整性不如方案二好,但操作安全、方便。
方案二和方案三与方案一相比,工序集中,劳动生产率高,但模具结构复杂,制造周期长。
机械制图任务6.1 托脚零件图的绘制

任务分析
叉架类零件多数形状不规则,外形 结构比内腔复杂,且整体结构复杂多样,形 状差异较大,常有弯曲或倾斜结构。其上常 有肋板、轴孔、耳板、底板等结构,局部结 构常有油槽、油孔、螺孔、沉孔等,表面常 有铸造圆角和过渡线。而托脚零件属于典型 的叉架类零件,要画出其零件图,我们必须 掌握叉架类零件的视图表达方法、叉架类零 件的尺寸标注、技术要求、识读叉架类零件 图的方法等相关知识。
2.除主视图外,一般还需1~2个基本视图将零件的主要结构表 达清楚。
3. 常用局部视图、局部剖表达零件上的凹坑、凸台等。筋板、 杆体常用断面图表示。用斜视图表示零件上的倾斜结构。
8
2.视图选择举例——拨叉
⑴ 结构分析
叉口 连接板
安装孔
9
⑵ 视图分析
主视图:拨叉的主视 图侧重表达外形,下部的 安装孔处用了局部剖视;
知识链接
一、叉架类零件视图的表达方案 常见零件 各种拔叉、连杆、摇杆、支架、支座等。
1.叉架类零件视图的选择
结构特点
此类零件由铸造或模锻制成毛坯,经机械加工而成。结 构大都比较复杂,一般分为工作部分、支承部分和连接部分。 其上常有凸台、凹坑、销孔、螺纹孔、和成型孔等结构。
表达方法
1.零件一般水平放置,选择零件形状特征明显的方向作为主视 图。
计
划பைடு நூலகம்
项目
可选方案
方案分析
任
方案1
务 决
主视图方向 方案2
机械类专业毕业论文题目
机械类专业毕业论文题目第1-100个题目1.支架零件图设计2.斜联结管数控加工和工艺3.CA6140型铝活塞的机械加工工艺设计及夹具设计4.MG132320-W型采煤左牵引部机壳的加工工艺规程及数控编程5.MG132320-W型采煤左牵引部机壳的加工工艺规程及数控编程6.MG250591-WD型采煤机右摇臂壳体的加工工艺规程及数控编程7.工艺-SSCK20A数控车床主轴和箱体加工编程8.工艺-WHX112减速机壳加工工艺及夹具设计9.工艺-X5020B立式升降台铣床拔叉壳体工艺规程制订10.工艺-X62W铣床主轴机械加工工艺规程与钻床夹具设计11.工艺-Z90型电动阀门装置及数控加工工艺的设计12.工艺-“填料箱盖”零件的工艺规程及钻孔夹具设计13.工艺-加工涡轮盘榫槽的卧式拉床夹具14.工艺-回转盘工艺规程设计及镗孔工序夹具设计15.工艺-壳体的工艺与工装的设计16.工艺-支承套零件加工工艺编程及夹具17.机电一体化-T6113电气控制系统的设计18.机电一体化-连杆平行度测量仪19.设计-CA-20地下自卸汽车工作、转向液压系统20.JX0020+设计-DTⅡ型皮带机设计21.设计-GBW92外圆滚压装置设计22.NK型凝汽式汽轮机调节系统的设计23.SPT120推料装置24.T611镗床主轴箱传动设计及尾柱设计25.XQB小型泥浆泵的结构设计26.YZJ压装机整机液压系统设计27.三自由度圆柱坐标型工业机器人设计28.乳化液泵的设计29.双柱式机械式举升机设计30.外圆磨床设计31.大型制药厂热电冷三联供32.大型轴齿轮专用机床设计33.大模数蜗杆铣刀专用机床设计34.小型轧钢机设计35.巷道堆垛类自动化立体车库36.巷道式自动化立体车库升降部分37.拖拉机变速箱体上四个定位平面专用夹具及组合机床设计38.板材送进夹钳装置39.校直机设计40.棒料切割机41.涡轮盘液压立拉夹具42.液压式双头套皮辊机43.液压绞车设计44.玉米脱粒机设计45.车载装置升降系统的开发46.铲平机的设计47.5吨中级桥式起重机电气控制系统的PLC改造设计48.C618数控车床的主传动系统设计49.TH5940型数控加工中心进给系统设计50.减速器箱体钻口面孔组合机床总体设计及主轴箱设计51.拖拉机拨叉铣专机52.数控机床主传动系统设计53.数控车床主传动机构设计54.数控车床纵向进给及导轨润滑机构设计55.三通管的塑料模设计56.电气工程及其自动化(电力)毕业设计57.C616型普通车床改造为经济型数控车床58.CA6140杠杆加工工艺59.CA6140杠杆加工工艺及夹具设计60.车床后托架的加工工艺与钻床夹具设计61.CA6140车床数控改造装配图62.CG2-150型仿型切割机63.CG2-150型仿型切割机64.CKP预粉磨设计(总体及壳体)65.FXS80双出风口笼形转子选粉机66.J45-6.3型双动拉伸压力机的设计67.J45-6.3型双动拉伸压力机的设计68.J550×3000双轴搅拌机设计69.JLY3809机立窑(窑体及卸料部件)70.JLY3809机立窑(加料及窑罩部件)设计71.JLY3809机立窑(总体及传动部件)设计72.L-108空气压缩机曲轴零件73.L050压缩式垃圾车设计74.LED显示屏动态显示和远程监控的实现75.MR141剥绒机锯筒部、工作箱部和总体设计76.N10000-OSEPA选粉机77.PE10自行车无级变速器设计78.PF455S插秧机及其侧离合器手柄的探讨和改善设计79.PLC-Z30130X31型钻床控制系统的PLC改造80.PLC-三菱FX2NPLC在电梯控制中的应用292.某大型水压机的驱动系统和控制系统293.汽车离合器(EQ153)的设计294.汽车离合器(螺旋430)的设计295.液位平衡控制系统实验装置设计296.清淤船的设计297.精密播种机298.马路保洁车299.CA6140法兰盘零件的机械加工工艺规程及工艺装备300.用于带式运输机上的传动及减速装置第301-400个题目301.S195柴油机机体三面精镗组合机床总体设计及夹具设计302.车床主轴箱箱体右侧10-M8螺纹底孔组合钻床设计303.货车底盘布置304.轴向柱塞泵设计305.轿车双摆臂悬架的设计及产品建模306.输出轴工艺与工装设计307.输出轴的工装工艺设计308.过桥齿轮轴机械加工工艺规程309.连杆零件加工工艺310.金属切削加工车间设备布局与管理311.钻四槽铣床与夹具图纸312.连杆零件加工工艺313.钻泵体盖6-φ2孔机床与夹具图纸314.钻6-φ7机床与夹具图纸315.闭式双级圆柱齿轮减速器316.青饲料切割机317.面筋成型机318.面筋成形生产线319.颗粒状糖果包装机设计320.外墙清洗机之升降机的设计321.高速数字多功能土槽试验台车的设计322.齿轮架零件的机械加工工艺规程及专用夹具设计323.齿轮泵前盖的数控加工和三维造型。
支架零件图——精选推荐
1. 绪论冲压是利用安装在压力机上的模具对材料施加压力使板料经分离或塑性变形而得到所需零件的一种压力加工方法。
常温下进行的板料冲压加工称为冷冲压。
一. 冷冲压在工业生产中的地位模具是大批生产同形产品的工具,是工业生产的主要工艺装备。
模具工业是国民经济的基础工业。
模具可保证冲压产品的尺寸精度。
使产品质量稳定,而在加工中不破坏产品表面。
用模具生产零部件可以采用冶金厂大量生产的廉价的轧制刚板、刚带为坯料,且在生产中不需加热,具有生产效率高质量好重量轻、成本低且节约能源和原材料等一系列优点,是其它加工方法所不能比拟的。
使用模具已成为当代工业生产的重要手段和工艺发展方向。
现代制造工业的发展和技术水平的提高,很大程度上取决于模具工业的发展。
目前,工业生产中普遍采用模具成形工艺方法,以提高产品的生产率和质量。
一般压力机加工,一台普通压力机设备每分钟可生产零件几件到几十件,高速压力机的生产率已达到每分钟数百件甚至上千件。
据不完全统计,飞机汽车拖拉机电机电器仪器仪表等产品,60%左右的零件是用模具加工出来的;而自行车手表洗衣机电冰箱及电风扇等轻工产品,90%左右的零件是用模具加工出来的;至于日用五金,餐具等物品的大批量生产基本上完全靠模具来进行。
显而易见,模具作为一种专用的工艺装备,在生产中决定性作用和重要地位逐渐为人们所共识。
二. 冷冲压模具的历史发展与现状第1章分离弯曲冲孔复合模设工件名称:支架零件图工件简图:如图材料:Q235料厚:2mm产量:大批量表面:1.2 设计内容(1)零件工艺性分析;(2)模具主要设计计算;(3)模具总体设计;(4)模具主要零部件设计;(5)模具装配图的确定及工作原理;(6)工件成型出现的工艺质量问题及解决措施5. 图 1第2章工件工艺性分析2.1 工艺性冲裁件的工艺性是指工件对冲压加工工艺的适合性。
良好的工艺性体现在材料消耗少,工序数目少,模具结构简单而寿命长,产品质量稳定,操作简单等方面。
机械类专业毕业论文题目
机械类专业毕业论文题目第1-100个题目1.支架零件图设计2.斜联结管数控加工和工艺3.CA6140型铝活塞的机械加工工艺设计及夹具设计4.MG132320-W型采煤左牵引部机壳的加工工艺规程及数控编程5.MG132320-W型采煤左牵引部机壳的加工工艺规程及数控编程6.MG250591-WD型采煤机右摇臂壳体的加工工艺规程及数控编程7.工艺-SSCK20A数控车床主轴和箱体加工编程8.工艺-WHX112减速机壳加工工艺及夹具设计9.工艺-X5020B立式升降台铣床拔叉壳体工艺规程制订10.工艺-X62W铣床主轴机械加工工艺规程与钻床夹具设计11.工艺-Z90型电动阀门装置及数控加工工艺的设计12.工艺-“填料箱盖”零件的工艺规程及钻孔夹具设计13.工艺-加工涡轮盘榫槽的卧式拉床夹具14.工艺-回转盘工艺规程设计及镗孔工序夹具设计15.工艺-壳体的工艺与工装的设计16.工艺-支承套零件加工工艺编程及夹具17.机电一体化-T6113电气控制系统的设计18.机电一体化-连杆平行度测量仪19.设计-CA-20地下自卸汽车工作、转向液压系统20.JX0020+设计-DTⅡ型皮带机设计21.设计-GBW92外圆滚压装置设计22.NK型凝汽式汽轮机调节系统的设计23.SPT120推料装置24.T611镗床主轴箱传动设计及尾柱设计25.XQB小型泥浆泵的结构设计26.YZJ压装机整机液压系统设计27.三自由度圆柱坐标型工业机器人设计28.乳化液泵的设计29.双柱式机械式举升机设计30.外圆磨床设计31.大型制药厂热电冷三联供32.大型轴齿轮专用机床设计33.大模数蜗杆铣刀专用机床设计34.小型轧钢机设计35.巷道堆垛类自动化立体车库36.巷道式自动化立体车库升降部分37.拖拉机变速箱体上四个定位平面专用夹具及组合机床设计38.板材送进夹钳装置39.校直机设计40.棒料切割机41.涡轮盘液压立拉夹具42.液压式双头套皮辊机43.液压绞车设计44.玉米脱粒机设计45.车载装置升降系统的开发46.铲平机的设计47.5吨中级桥式起重机电气控制系统的PLC改造设计48.C618数控车床的主传动系统设计49.TH5940型数控加工中心进给系统设计50.减速器箱体钻口面孔组合机床总体设计及主轴箱设计51.拖拉机拨叉铣专机52.数控机床主传动系统设计53.数控车床主传动机构设计54.数控车床纵向进给及导轨润滑机构设计55.三通管的塑料模设计56.电气工程及其自动化(电力)毕业设计57.C616型普通车床改造为经济型数控车床58.CA6140杠杆加工工艺59.CA6140杠杆加工工艺及夹具设计60.车床后托架的加工工艺与钻床夹具设计61.CA6140车床数控改造装配图62.CG2-150型仿型切割机63.CG2-150型仿型切割机64.CKP预粉磨设计(总体及壳体)65.FXS80双出风口笼形转子选粉机66.J45-6.3型双动拉伸压力机的设计67.J45-6.3型双动拉伸压力机的设计68.J550×3000双轴搅拌机设计69.JLY3809机立窑(窑体及卸料部件)70.JLY3809机立窑(加料及窑罩部件)设计71.JLY3809机立窑(总体及传动部件)设计72.L-108空气压缩机曲轴零件73.L050压缩式垃圾车设计74.LED显示屏动态显示和远程监控的实现75.MR141剥绒机锯筒部、工作箱部和总体设计76.N10000-OSEPA选粉机77.PE10自行车无级变速器设计78.PF455S插秧机及其侧离合器手柄的探讨和改善设计79.PLC-Z30130X31型钻床控制系统的PLC改造80.PLC-三菱FX2NPLC在电梯控制中的应用205.机械手的设计206.减速器锥柱二级传动207.机油盖注塑模具设计208.杠杆Zl159-a209.杠杆工艺和工装设计210.杠杆设计211.板材坡口机总体设计212.某小区的智能化系统设计213.柴油机气缸体顶底面粗铣组合机床总体及夹具设计214.柴油机连杆的加工工艺215.柴油机齿轮室盖钻镗专机总体及主轴箱设216.柴油机齿轮室盖钻镗专机总体及夹具设计217.桥式起重机副起升机构设计218.桥梁式集装箱起重机设计219.椭圆盖220.椭圆盖板的宏程序编程与自动编程221.椭圆盖注射222.椭圆盖注射模设计223.榨汁机设计224.Φ146.6药瓶注塑模设计225.模具-五金-护罩壳侧壁冲孔模设计226.模具-五金-空气滤清器壳正反拉伸复合模设计227.模具-五金-笔记本电脑壳上壳冲压模设计228.模具-冰箱调温按钮塑模设计229.模具-冷冲扬声器模具设计230.S195柴油机机体三面精镗组合机床总体设计及左主轴箱设计231.模具-注塑-多用工作灯后盖注塑模232.模具-注塑-对讲机外壳注射模设计233.模具-注塑-手机充电器塑料模具234.模具-注塑-手机充电器模具设计235.模具-注塑-水管三通管塑料模具236.模具-电机炭刷架冷冲压模具设计237.模具-电池板铝边框冲孔模的设计238.模具-离合器板冲成形模具设计239.模具-铰链落料冲孔复合模具设计240.模具鼠标盖设计论文241.酒瓶内盖塑料模具设计242.单盘式渐开线检查仪的改进243.五层教学楼设计244.水厂给水工程设计245.公路施工设计246.毕业设计公路设计247.气门摇臂轴支座设计248.水泥粉磨选粉系统改造249.水电站水轮机进水阀门液压系统设计250.水闸的设计251.汽车半轴设计252.汽车盖板冲裁模设计253.法兰零件夹具设计254.注射器盖设计255.注射器盖设计256.配油盘受力分析与设计257.渐开线涡轮数控工艺及加工258.滤油器支架模具设计259.火灾自动报警系统设计(电气类)260.电流线圈架塑料模设计261.电动智能小车262.电源盒注射模设计263.电织机导板零件数控264.电风扇旋扭的塑料模具设计265.盐酸分解磷矿装置设计266.盒形件落料拉深模设计267.电气一次及发电机继电保护设计268.移动通信的电波衰落与抗衰落技术分析269.空气压缩机曲轴设计270.立窑烟尘和有害气体综合治理技术在水泥清洁生产中的应用设计271.立辊轧机设计272.端面齿盘的设计与加工273.笔盖的模具设计274.米T梁设计275.组合件数控车工艺与编程276.组合机床液压系统设计277.组合铣床的总体设计和主轴箱设计278.美国赛车连杆专用工装夹具设计279.美国赛车连杆专用工装夹具设计280.肥皂盒设计281.自行车脚蹬内板多工位级进模设计282.落料_拉深_冲孔复合模283.螺旋千斤顶设计284.螺旋管状面筋机总体及坯片导出装置设计285.AWC机架现场扩孔机设计286.设计-ZL15型轮式装载机287.外行星摆线马达结构设计288.工程钻机的设计289.插秧机系统设计290.搅拌器的设计291.旋转门的设计292.某大型水压机的驱动系统和控制系统293.汽车离合器(EQ153)的设计294.汽车离合器(螺旋430)的设计295.液位平衡控制系统实验装置设计296.清淤船的设计297.精密播种机298.马路保洁车299.CA6140法兰盘零件的机械加工工艺规程及工艺装备300.用于带式运输机上的传动及减速装置第301-400个题目301.S195柴油机机体三面精镗组合机床总体设计及夹具设计302.车床主轴箱箱体右侧10-M8螺纹底孔组合钻床设计303.货车底盘布置304.轴向柱塞泵设计305.轿车双摆臂悬架的设计及产品建模306.输出轴工艺与工装设计307.输出轴的工装工艺设计308.过桥齿轮轴机械加工工艺规程309.连杆零件加工工艺310.金属切削加工车间设备布局与管理311.钻四槽铣床与夹具图纸312.连杆零件加工工艺313.钻泵体盖6-φ2孔机床与夹具图纸314.钻6-φ7机床与夹具图纸315.闭式双级圆柱齿轮减速器316.青饲料切割机317.面筋成型机318.面筋成形生产线319.颗粒状糖果包装机设计320.外墙清洗机之升降机的设计321.高速数字多功能土槽试验台车的设计322.齿轮架零件的机械加工工艺规程及专用夹具设计323.齿轮泵前盖的数控加工和三维造型。
支架课程设计--支架零件的机械加工工艺规程
重庆电子工程职业学院机械制造工艺与机床夹具课程设计院系机电学院专业机械制造及工艺设计指导教师孙红年级机制1104班姓名学号2013年7月机械制造工艺学课程设计是在学完了机械制造工艺学和大部分专业课,并进行了生产实习的基础上进行的一个教学环节。
这次设计使我们能够综合运用机械制造工艺学中的基本理论,并结合生产实习中学到的实践知识,独立分析和解决工艺问题,初步具备了设计一个中等复杂程度零件的工艺规程的能力和运用夹具设计手册与图表等技术资料及编写技术文件等基本技能的一次实践机会,为今后的毕业设计及未来从事的工作打下良好的基础。
由于能力所限,经验不足,设计中还有许多不足之处,希望各位老师多加指导。
目录第1章零件分析 (4)1.1零件的作用 (4)1.2零件的工艺性分析和零件图的审查 (1)第2章选择毛坯 (1)2.1确定毛坯的成形方法 (1)2.2铸件结构工艺性分析 (1)2.3铸造工艺方案的确定 (2)第3章工艺规程设计 (2)3.1定位基准的选择 (2)3.2制订工艺路线 (2)3.3选择加工设备及刀、夹、量具 (5)3.4加工工序设计 (7)3.5填写加工工艺卡片 (13)第1章零件分析1.1零件的作用支架是机床上用于支撑轴的机构,支架以Φ80孔套在轴上。
本设计任务给定的零件转支架即传递运动并保持其他零件正确工作方式,和保持互相之间的正确位置。
其对加工平面,平行度,加工孔,垂直度,等有一定的要求,由于零件不成规则,故加工过程中需要用到复杂的夹具。
1.2零件的工艺性分析和零件图的审查分析零件图可知,该零件除主要工作表面和基准面精度要求比较高,其余表面加工精度均要求较低,不需要高精度机床加工,通过铣削的粗加工就可以达到加工要求;而主要工作表面虽然加工精度相对较高,但也可以在正常的生产条件下,采用较为经济的方法保证质量地加工出来。
对支架的加工工艺有以下几个方面要求:1.21铣底面保证长度260±0.1和铣左侧面保证长度2406.0,并且保证粗糙度为1.6.1.22镗内孔保证Φ80的孔,同轴度为0.005,直线度为0.01,平行度为0.05.第2章选择毛胚2.1 确定毛坯的成形方法该零件材料为HT15-33,大批量生产,考虑到支架工作过程中受力不大,轮廓尺寸也不大,各处壁厚相差较小,从结构形式看,几何形体不是很复杂,采用铸造生产比较合适,故可采用砂型铸造成形。
- 1、下载文档前请自行甄别文档内容的完整性,平台不提供额外的编辑、内容补充、找答案等附加服务。
- 2、"仅部分预览"的文档,不可在线预览部分如存在完整性等问题,可反馈申请退款(可完整预览的文档不适用该条件!)。
- 3、如文档侵犯您的权益,请联系客服反馈,我们会尽快为您处理(人工客服工作时间:9:00-18:30)。
1.设计的目的设计是培养机械工程类专业学生应职应岗能力的重要实践性教学环节,它要求学生能全面综合地运用所学的理论和实践知识,进行零件机械加工工艺规程和工艺装备的设计。
其基本目的是:(1)培养工程意识。
(2)训练基本技能。
(3)培养质量意识。
(4)培养规范意识。
2设计的基本任务与要求2、1、设计任务(1)设计一个中等复杂的零件的加工工艺规程;(2)设计一个专用夹具;(3)编写设计说明书。
2、2、设计基本要求(1)内容完整,步骤齐全。
(2)设计内容与说明书的数据和结论应一致,内容表达清楚,图纸准确规范,简图应简洁明了,正确易懂。
(3)正确处理继承与创新的关系。
(4)正确使用标准和规范。
(5)尽量采用先进设计手段。
3设计说明书的编写说明书要求系统性好、条理清楚、语言简练、文字通顺、字迹工整、图例清晰、图文并茂,充分表达自己的见解,力求避免抄书。
第一章工艺设计与工装设计1.基本任务:(1)绘制零件工件图一张;(2)绘制毛坯—零件合图一张;(3)编制机械加工工艺规程卡片一套;(4)编写设计说明书一份;(5)收集和研究原始资料,为夹具结构设计做好技术准备。
(6)初步拟定夹具结构方案,绘制夹具结构草图,进行必要的理论计算和分析。
选择最佳的夹具结构方案,确定夹具精度和夹具总图尺寸、公差配合与技术要求。
(7)绘制夹具总图和主要非标准件零件图,编写设计说明书。
(8)编制夹具特殊使用维护、操作、制造方面的说明或技术要求。
2.设计要求:(1)应保证零件的加工质量,达到设计图纸的技术要求;(2)在保证加工质量的前提下,尽可能提高生产效率;(3)要尽量减轻工人劳动强度,必须考虑生产安全、工业卫生等措施;(4)在立足本企业的生产条件基础上,尽可能采用国内外新技术、新工艺、新装备;(5)工艺规程应正确、完整、简洁、清晰;(6)工艺规程应满足规范化、标准化要求;(7)夹具设计保证工件的加工精度;(8)提高生产效率;(9)工艺性好;(10)使用性好;(11)经济性好。
3.方法和步骤:3.1生产纲领的计算与生产类型的确定生产类型生产纲领(件/年)大批生产小型零件(4KG)2800表1-1生产纲领和生产类型的关系3.2零件图审查3.2.1了解零件的功用及技术要求熟悉用途(机械传动有级调速)、性能及工作条件密封(保证齿轮系中无杂,无灰层进入,机油润滑),在产品中的位置(处于电机与执行机构之间)和功用(齿轮间的传动比来改变转速),3.2.2分析零件的结构工艺性零件的结构工艺分析主要应考虑以下几个方面:(1)零件的尺寸公差、形位公差和表面粗糙度的要求应经济合理,重要尺寸精度φ20,公差在0.025之内,形位公差垂直度要求0.05之内,一般尺寸精度为9-11级(2)各加工表面的几何形状应尽量简单;(3)有相互位置要求的表面应尽量在一次装夹中加工;该零件在加工时,对φ20孔加工要保证孔与孔的面距高度方向在60及孔与孔轴线垂直度在0.05之内,故对φ20加工时采用一次定位安装来加工3.3毛坯选择3.3.1毛坯的种类—铸件HT150适用于形状复杂的毛坯,良好的耐磨性、抗震性、切削加工性和铸造性能)—表1-6HT的牌号、性能及主要用途(机械制造基础)3.3.2铸件制造方法的选择毛坯制造方法应与材料的工艺性、零件的结构形状及大小、生产类型及特点以及工厂的现有条件相适应加工余量原材料工件尺寸工件形状毛坯种类制造精度(IT)砂型铸造13级以下大HT150 各种尺寸复杂表1-2各类毛坯的特点及应用范围3.3.3铸件的尺寸公差与加工余量3.3.3.1铸件的尺寸公差(GB6414-1986)规定:铸件尺寸代号为CT,分16级造型材料公差等级CT灰铸铁自硬砂11~13表1-4小批和单件生产铸件的尺寸公差等级表1-5铸件尺寸公差数值(机械制造技术课程设计)3.3.3.2铸件加工余量表1-6用于成批和大量生产与铸件尺寸公差配套使用的铸件机械加工余量等级和表1-7铸件尺寸公差配套使用的铸件机械加工余量(机械制造技术课程设计)3.3.3.3铸件最小孔径表面类型成批生产通孔15~30MM表1-8铸件最小孔径3.3.4毛坯—零件合图用查表法确定各表面的加工总余量和余量公差。
表1-5铸件尺寸公差数值(机械制造技术课程设计)表1-6用于成批和大量生产与铸件尺寸公差配套使用的铸件机械加工余量等级和表1-7铸件尺寸公差配套使用的铸件机械加工余量(机械制造技术课程设计)3.4定位基准的选择正确地选择定位基准是设计工艺过程的一项重要内容,也是保证加工精度的关键。
定位基准分为粗基准和精基准。
对于无合适定位面的零件可在毛坯上另外专门设计或加工出定位表面,称为辅助基准。
定位基准的选择原则(机械制造基础P254)粗基准的选择原则(1)应选择不加工表面为粗基准。
(2)对于具有较多加工表面的工件,粗基准的选择,应合理分配各加工表面的加工余量,以保证:1)各加工表面都有足够的加工余量;2)对某些重要的表面,尽量使其加工余量均匀;3)使工件上各加工表面总的金属切除量最小;(3)作为粗基准的表面,应尽量平整,没有浇口,冒口或飞边等其它表面缺陷,以便定位准确;(4)同一尺寸方向上的粗基准表面只能使用一次;精基准的选择原则:(1)基准重合原则(2)基准统一原则(3)互为基准原则(4)自为基准原则3.4.1夹具设计研究原始资料1、研究加工工件图样了解该工件的结构形状.尺寸.材料.热处理要求,主要是表面的加工精度.表面粗糙度及其他技术要求2、熟悉工艺文件,明确以下内容(1)毛坯的种类.形状.加工余量及其精度。
(2)工件的加工工艺过程,工序图,本工序所处的地位,本工序前已加工表面的精度及表面粗糙度,基准面的状况。
(3)本工序所使用的机床.刀具及其他辅助工具的规格。
(4)本工序所采用的切削用量。
3.4.2拟定夹具的结构方案1.确定夹具的类型2.确定工件的定位方式及定位元件的结构工件的定位方式主要取决于工件的加工要求和定位基准的形状.尺寸。
分析加工工序的技术条件和定位基准选择的合理性,遵循六点定位原则,按定位可靠.结构简单的原则,确定定位方式。
常见的定位方式有平面定位.内孔定位.外圆定位和组合表面(一面两销)定位等。
在确定了工件的定位方式后,即可根据定位基面的形状,选取相应的定位元件及结构。
(1)平面定位在夹具设计中常用的平面定位元件有固定支承.可调支承.自位支承及辅助支承,其中固定支承又可分为支承钉和支承板。
3.工件的夹紧方式,计算夹紧力并设计夹紧装置夹紧机构应保证工件夹紧可靠.安全.不破坏工件的定位及夹压表面的精度和粗糙度。
在设计夹紧装置时必须合理选择夹紧力的方向和作用点,必要时还应进行夹紧力的估算。
(1)切削力的计算(C a吃九量 f进给量 v切削速度 k修正系数)0.75 0Fz=9.81Cafvk=9.81×180×0.2×4 ×10 ×(300/190)×0.55×1.8=1561.18N0.9 0.75 0Fy=9.81Cafvk=9.81×94×0.2 ×4 ×10 ×(300/190)×1.3×1.63=1795.36N1.2 0.65 0Fx=9.81Cafvk=9.81×54×0.2 ×4 ×10 ×(300/190)×1.1×0.7=1092.82N2 2 2故总的切削力F=【〔Fz_+ Fy + Fx 〕】开平方根=2618.27N(2)夹紧力的计算Fwk=KM/LF(Fwk实际夹紧力,M切削力矩,L压板长度,F进给量)=0.1 × 2618.27×20 /50×0.2=523.65N在确定夹紧力的大小时,为简化计算,通常将夹具和工件看成一个刚性系统。
根据工件所受切削力.夹紧力(大型工件还应考虑重力.惯性力等)的作用情况,找出加工过程中对夹紧最不利的状态,按静力平衡原理计算出理论夹紧力,最后再乘以安全系数。
用压板夹紧工件端面Fwk=KM/LF(Fwk实际夹紧力,K安全系数)表3-2常见夹紧形式所需的夹紧力计算公式(2)夹紧装置的设计夹紧装置的设计实际上是一个综合性的问题,确定夹紧力的大小.方向和作用点时,必须全面考虑工件的结构.工艺方法.定位元件的结构与布置等因素。
要求夹紧装置动作迅速,操作安全省力,结构简单.易于制造并且体积小.刚度好,有足够的夹紧行程和装卸工件的间隙。
常见的夹紧机构有斜锲机构.螺旋机构.偏心机构等。
也可采用机动夹紧如液压.气动夹紧等。
1)螺旋机构螺旋机构由于其结构简单.自锁性好.扩力比大且夹紧行程不受限制,广泛应用于夹具的夹紧装置。
夹紧力基本计算公式为W=QL/tan(α+β1)0.5d+ rtanβ2 式中d螺纹中径,r磨擦半径4.确定刀具的导向方式或对刀装置表3-49~表3-62为常用的对刀元件和导向元件(机械制造技术课程设计),供设计时选用5.确定夹具体的结构类型夹具上的各种装置和元件通过夹具体连接成一个整体,因此夹具体的形状及尺寸取决于夹具各种装置的布置及夹具与机床的连接。
(1)对夹具体的要求1)有适当的精度和尺寸稳定性2)有足够的强度和刚度3)结构工艺性好4)排屑方便5)在机床上安装稳定可靠(2)夹具体毛坯的类型1)型材夹具体2)铸造夹具体3、4、3 夹具总图设计1 绘制总装图的注意问题(1)尽可能采用1:1的比例,以求直观不会产生错觉。
(2)被加工工件用双点画线表示,在图中作透明体处理,它不影响夹具元件的投影。
加工面的加工余量可用粗实线表示。
(3)视图的数量应以能完整.清晰地表示出整个结构为原则。
为直观起见,一般常以操作者在加工时所面对的视图为主观图。
(4)工件在夹具中应处于夹紧状态。
2 绘制总装图的步骤(1)布置定位元件(2)布置导向.对刀元件(3)设计夹紧装置(4)设计夹具体(5)完成总装图3 夹具总图上尺寸及精度、位置精度与技术要求的标注(1)夹具总图上应标注的尺寸和相互位置关系有如下五类1)定位副本身的精度和定位副之间的联系尺寸及精度;2)对刀元件或导向元件与定位元件之间的联系尺寸;3)夹具体与机床的连接面以及定位元件与工件表面之间的联系尺寸;4)夹具外形的最大轮廓尺寸;5)配合尺寸。
(2)尺寸公差的确定原则为满足加工精度要求,夹具本身应有较高的精度。
由于目前分析计算方法不够完善,因此夹具的有关公差仍按经验来确定。
如果生产规模较大,要求夹具具有一定寿命,夹具的有关公差可取得小些;对加工精度较低的夹具,则取较大的公差。
一般可按以下原则选取(下述文中的δk为工件相应公差);1)夹具上的尺寸和角度公差取(1/2~1/5)δk;2)夹具上的位置公差取(1/2~1/3)δk;3)当加工未注公差工件时取±0.1mm;4)未注形位公差的加工面,按GB/T11-1984中13级精度的规定选取。