板材挤出工艺
挤出成型工艺与设备 挤出成型法生产板(片)材
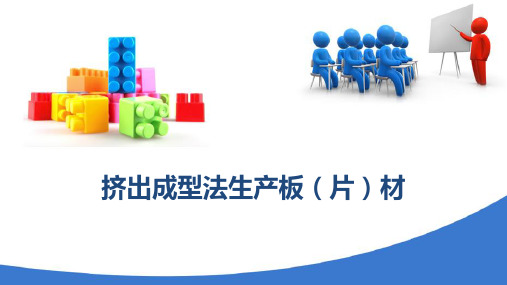
压光辊
冷却 导辊
牵引
一、生产设备
2 辅机
4)切割装置
板材的切割包括切边与切断。 切边多用圆盘切刀;切断多用电热切、锯切(硬板)和剪切(软板)。
5)自动测厚仪
采用射线自动测厚,测试时不直接与板材接触,不损伤板材;可沿板 材横向移动,并自动记录数据;精度可达0.002 mm,快而准。
目录
01 生 产 设 备 02 成 型 工 艺
目录
01 生 产 设 备 02 成 型 工 艺
目录
01 生 产 设 备 02 成 型 工 艺
一、生产设备
1 机头
机筒应加过滤网和分流板。机头与挤出机机筒之间用连接器 连接。连接器的内孔,进料端呈圆锥形,出料端由圆锥形过渡成 矩形。两端用法兰与机筒和机头模具连接。
机头为扁平机头。出料口宽而薄,熔体从料筒挤到机头内, 流道由圆形变成狭缝形,物料沿着机头宽度方向均匀分布,经模 唇挤出板材。
1)三辊压光机
三辊辊筒的温度取决于所加工的物料,一般为35~100℃之间。 辊筒是中空的,且带有夹套,通入蒸汽、油、热水或冷水进行控温。 辊筒长度比口模宽度略宽,其表面镀硬铬。
一、生产设备
2 辅机
2)牵引装置
从压光辊出来的板材在导辊的引导下进入牵引装置。
将板材均匀地牵引至切割 装置,防止在压辊处积料,而 造成板材弯曲变形,并且将板 材压光、压平。
挤出成型法生产板(片)材
挤出成型法生产板(片)材
挤出成型法可生产厚度介于0.02~20 mm的薄膜、片材和板材。 按产品厚度划分:
<0.25 mm 称为薄膜; 0.25~1 mm 称为片材; >1 mm 称为板材。
挤出成型法生产板(片)材
挤出机将物料熔融塑化,而后熔融物料在狭缝机头中成型为所需规格的 板坯,经三辊压光机压光,冷却定型,再经导辊进一步冷却,然后由切边机 切边,经二辊牵引机牵引后切割成所需规格的板材。
挤塑板生产工艺流程
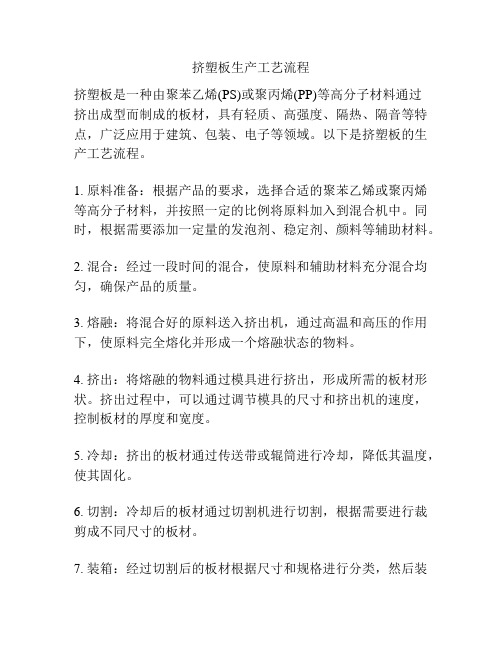
挤塑板生产工艺流程挤塑板是一种由聚苯乙烯(PS)或聚丙烯(PP)等高分子材料通过挤出成型而制成的板材,具有轻质、高强度、隔热、隔音等特点,广泛应用于建筑、包装、电子等领域。
以下是挤塑板的生产工艺流程。
1. 原料准备:根据产品的要求,选择合适的聚苯乙烯或聚丙烯等高分子材料,并按照一定的比例将原料加入到混合机中。
同时,根据需要添加一定量的发泡剂、稳定剂、颜料等辅助材料。
2. 混合:经过一段时间的混合,使原料和辅助材料充分混合均匀,确保产品的质量。
3. 熔融:将混合好的原料送入挤出机,通过高温和高压的作用下,使原料完全熔化并形成一个熔融状态的物料。
4. 挤出:将熔融的物料通过模具进行挤出,形成所需的板材形状。
挤出过程中,可以通过调节模具的尺寸和挤出机的速度,控制板材的厚度和宽度。
5. 冷却:挤出的板材通过传送带或辊筒进行冷却,降低其温度,使其固化。
6. 切割:冷却后的板材通过切割机进行切割,根据需要进行裁剪成不同尺寸的板材。
7. 装箱:经过切割后的板材根据尺寸和规格进行分类,然后装入纸箱或托盘进行包装,并贴上相应的标签。
8. 储存:包装好的挤塑板可以进行临时储存,等待后续的销售和配送。
挤塑板的生产工艺流程简单明了,但在实际操作中还需注意以下几点:1. 原料选取:选择适合的原料是确保挤塑板质量的关键。
原料的质量不好会导致挤出板材的性能下降。
2. 温度控制:挤塑板的生产和挤出过程需要控制合适的温度,过高或过低的温度都会影响挤塑板的性能。
3. 模具设计:模具的设计要合理,尺寸准确,以确保挤出的板材符合要求的尺寸和形状。
4. 切割精度:切割板材时需要保证精确度,以避免浪费和剩余料的产生。
总之,挤塑板的生产工艺流程简单高效,但在实际操作中需要严格控制各个环节和参数,以确保产品的质量和性能。
挤出成型的工艺过程。

挤出成型是一种常见的塑料加工工艺,广泛应用于塑料制品、管材、板材、薄膜等的生产。
这个过程通过将熔融的塑料材料挤压通过模具,形成所需的截面形状,然后通过冷却和固化使其保持所需的形状。
下面将详细探讨挤出成型的工艺过程及其应用。
### 1. **原料准备和预处理:**挤出成型的第一步是准备原料。
通常,塑料颗粒或颗粒状的原材料被用作挤出的起点。
这些原材料在挤出之前通常需要进行预处理,以确保它们在挤出过程中能够达到理想的熔融性和流动性。
预处理可能包括干燥、混合、添加颜料或其他添加剂,以调整塑料的性质。
### 2. **塑料熔融:**准备好的原料被送入挤出机的料斗中。
在挤出机中,原料经过加热和熔融,最终形成一个粘稠的熔融塑料。
这个过程通常涉及到一个螺杆,通过旋转将原料从进料区域推送到熔融区域。
螺杆的设计和形状可以影响熔融的均匀性和速度。
### 3. **模具设计和选择:**挤出成型的模具通常由金属制成,其截面形状决定了最终产品的形状。
模具的设计需要考虑到材料的流动性、冷却需求以及最终产品的规格。
对于不同的产品,可能需要使用不同的模具。
### 4. **挤出过程:**熔融塑料通过螺杆被挤压到模具中,形成与模具截面相匹配的产品。
挤出机通常包括一组温度控制系统,以确保塑料保持在适当的熔融状态。
挤出的过程可以是单层或多层的,具体取决于产品的要求。
在挤出过程中,可以通过挤出机上的一些装置,如冷却装置和拉伸装置,来调整最终产品的性质。
### 5. **冷却和固化:**一旦挤出的塑料通过模具,它会进入到冷却区域。
在这里,通过空气、水或其他冷却介质对熔融的塑料进行冷却。
冷却的速度和方式会影响最终产品的结晶结构和性能。
一些复杂的挤出产品可能需要通过冷却和拉伸来调整其物理性质,以确保其符合要求。
### 6. **切割和处理:**一旦产品冷却并达到足够的硬度,它可以被切割成所需的长度。
有些产品可能需要进一步的处理,如切边、打孔、表面处理等。
XPS挤塑板生产工艺及特点

XPS挤塑板生产工艺及特点XPS(Extruded Polystyrene Foam Board)挤塑板是一种以聚苯乙烯为原料,通过特殊的挤出工艺制造而成的泡沫塑料板材。
下面将详细介绍XPS挤塑板的生产工艺及特点。
一、XPS挤塑板的生产工艺:1.原料处理:首先,聚苯乙烯颗粒经过预扩、干燥和融化处理,使其达到挤出所需的状态。
2.挤出模头:将融化的聚苯乙烯通过挤出机送入挤出模头,挤出模头具有特定的形状,通过调节模具的结构和参数来决定挤出板的厚度和宽度。
3.挤出成型:将融化的聚苯乙烯通过挤出模头挤出成型,形成连续的板材。
这个过程称为挤出,挤出的板材具有均匀的密度和尺寸。
4.切割:挤出板经过一定的冷却时间后,进入切割工序。
板材通过切割机横向和纵向切割成合适的尺寸。
5.质量检测:切割后的挤塑板进入质量检测环节,检测板材的密度、尺寸和其他物理性能,确保其符合相关的标准和要求。
6.包装:经过质量检测合格的XPS挤塑板进行包装,常见的包装方式有塑料袋封装或托盘包装,以保护板材的表面免受损坏。
二、XPS挤塑板的特点:1.密度均匀:XPS挤塑板具有均匀的细胞结构和闭孔结构,表面光滑平整,密度一致,无残留气孔和不够均匀的树脂层。
这种均匀的密度分布使XPS挤塑板具有优异的抗压强度和耐久性。
2.保温性能好:XPS挤塑板的闭孔结构使其具有较低的导热系数,保温性能好。
相同厚度的XPS挤塑板可以达到更好的保温效果,减少能源消耗。
此外,XPS挤塑板还具有优异的防潮性能,不易吸湿。
3.高强度:XPS挤塑板具有较高的抗压、抗弯和抗冲击强度,可以用于抗震、抗变形的场所。
它具有优良的稳定性和耐久性,不易变形,能够保持长期使用的稳定性能。
4.耐久性好:XPS挤塑板具有优异的耐老化性能,不易受到紫外线、化学物质和微生物的侵害,保持较长时间的使用寿命。
5.施工方便:XPS挤塑板具有较轻的重量,便于搬运和安装。
板材表面平整光滑,易于切割和加工,符合不同建筑结构的需求。
挤出成型的原理和工艺流程
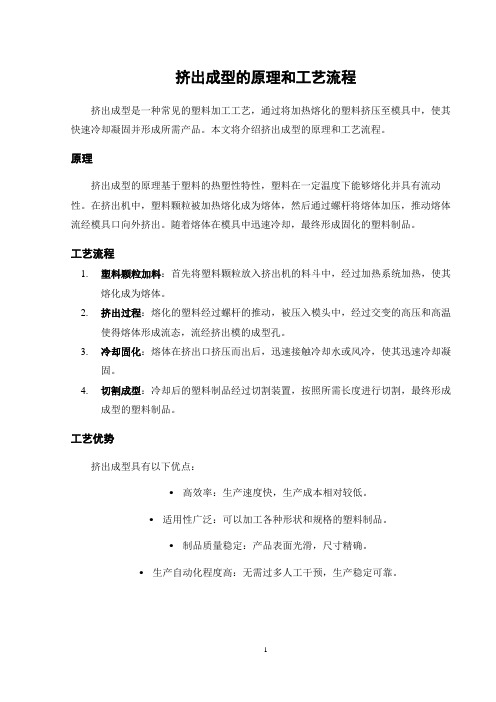
挤出成型的原理和工艺流程
挤出成型是一种常见的塑料加工工艺,通过将加热熔化的塑料挤压至模具中,使其快速冷却凝固并形成所需产品。
本文将介绍挤出成型的原理和工艺流程。
原理
挤出成型的原理基于塑料的热塑性特性,塑料在一定温度下能够熔化并具有流动性。
在挤出机中,塑料颗粒被加热熔化成为熔体,然后通过螺杆将熔体加压,推动熔体流经模具口向外挤出。
随着熔体在模具中迅速冷却,最终形成固化的塑料制品。
工艺流程
1.塑料颗粒加料:首先将塑料颗粒放入挤出机的料斗中,经过加热系统加热,使其
熔化成为熔体。
2.挤出过程:熔化的塑料经过螺杆的推动,被压入模头中,经过交变的高压和高温
使得熔体形成流态,流经挤出模的成型孔。
3.冷却固化:熔体在挤出口挤压而出后,迅速接触冷却水或风冷,使其迅速冷却凝
固。
4.切割成型:冷却后的塑料制品经过切割装置,按照所需长度进行切割,最终形成
成型的塑料制品。
工艺优势
挤出成型具有以下优点:
•高效率:生产速度快,生产成本相对较低。
•适用性广泛:可以加工各种形状和规格的塑料制品。
•制品质量稳定:产品表面光滑,尺寸精确。
•生产自动化程度高:无需过多人工干预,生产稳定可靠。
应用领域
挤出成型广泛应用于塑料制品生产行业,如管道、板材、型材、薄膜、包装材料等领域。
其高效率、高质量的特点使其成为塑料制品生产中不可或缺的一环。
总的来说,挤出成型作为一种常见的塑料加工工艺,通过简单高效的操作流程,可以生产出质量稳定的塑料制品,在工业生产中发挥着重要作用。
挤出成型的优缺点
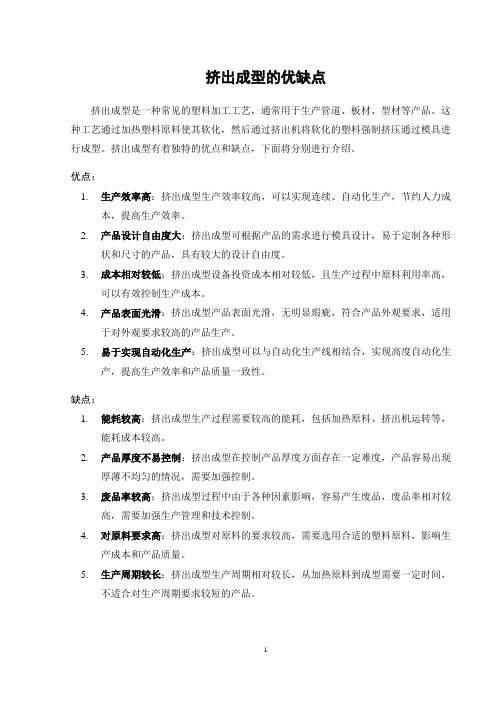
挤出成型的优缺点挤出成型是一种常见的塑料加工工艺,通常用于生产管道、板材、型材等产品。
这种工艺通过加热塑料原料使其软化,然后通过挤出机将软化的塑料强制挤压通过模具进行成型。
挤出成型有着独特的优点和缺点,下面将分别进行介绍。
优点:1.生产效率高:挤出成型生产效率较高,可以实现连续、自动化生产,节约人力成本,提高生产效率。
2.产品设计自由度大:挤出成型可根据产品的需求进行模具设计,易于定制各种形状和尺寸的产品,具有较大的设计自由度。
3.成本相对较低:挤出成型设备投资成本相对较低,且生产过程中原料利用率高,可以有效控制生产成本。
4.产品表面光滑:挤出成型产品表面光滑,无明显瑕疵,符合产品外观要求,适用于对外观要求较高的产品生产。
5.易于实现自动化生产:挤出成型可以与自动化生产线相结合,实现高度自动化生产,提高生产效率和产品质量一致性。
缺点:1.能耗较高:挤出成型生产过程需要较高的能耗,包括加热原料、挤出机运转等,能耗成本较高。
2.产品厚度不易控制:挤出成型在控制产品厚度方面存在一定难度,产品容易出现厚薄不均匀的情况,需要加强控制。
3.废品率较高:挤出成型过程中由于各种因素影响,容易产生废品,废品率相对较高,需要加强生产管理和技术控制。
4.对原料要求高:挤出成型对原料的要求较高,需要选用合适的塑料原料,影响生产成本和产品质量。
5.生产周期较长:挤出成型生产周期相对较长,从加热原料到成型需要一定时间,不适合对生产周期要求较短的产品。
综上所述,挤出成型作为一种常见的塑料加工工艺具有一定的优点和缺点,生产厂家在选择加工工艺时需根据产品特点和需求进行合理选择,充分发挥挤出成型工艺的优势,同时加强技术改进和管理控制,以提高生产效率和产品质量,降低生产成本。
pvc板材生产工艺流程图
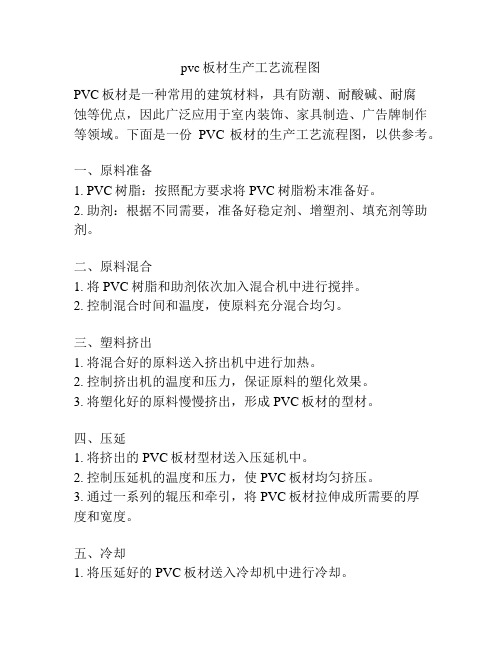
pvc板材生产工艺流程图PVC板材是一种常用的建筑材料,具有防潮、耐酸碱、耐腐蚀等优点,因此广泛应用于室内装饰、家具制造、广告牌制作等领域。
下面是一份PVC板材的生产工艺流程图,以供参考。
一、原料准备1. PVC树脂:按照配方要求将PVC树脂粉末准备好。
2. 助剂:根据不同需要,准备好稳定剂、增塑剂、填充剂等助剂。
二、原料混合1. 将PVC树脂和助剂依次加入混合机中进行搅拌。
2. 控制混合时间和温度,使原料充分混合均匀。
三、塑料挤出1. 将混合好的原料送入挤出机中进行加热。
2. 控制挤出机的温度和压力,保证原料的塑化效果。
3. 将塑化好的原料慢慢挤出,形成PVC板材的型材。
四、压延1. 将挤出的PVC板材型材送入压延机中。
2. 控制压延机的温度和压力,使PVC板材均匀挤压。
3. 通过一系列的辊压和牵引,将PVC板材拉伸成所需要的厚度和宽度。
五、冷却1. 将压延好的PVC板材送入冷却机中进行冷却。
2. 控制冷却机的温度和速度,使PVC板材迅速冷却。
六、切割1. 将冷却好的PVC板材送入切割机中。
2. 根据要求,将PVC板材切割成需要的长度和宽度。
3. 定期检查切割刀片的磨损情况,及时更换。
七、检验1. 对切割好的PVC板材进行外观检验。
2. 检查表面是否平整、无气泡、无瑕疵等问题。
八、包装1. 将合格的PVC板材依据规格、长度等进行分类。
2. 使用封包机将PVC板材进行包装,以防污染、损坏。
九、入库1. 将包装好的PVC板材送入仓库进行存储。
2. 控制好仓库的湿度和温度,避免PVC板材受潮、变形。
十、出厂1. 将需要出厂的PVC板材按订单进行分装。
2. 安排合适的运输方式,将PVC板材送往客户处。
通过以上的工艺流程,可以生产出质量稳定的PVC板材,并且满足客户不同的需求。
同时,在进行生产过程中,需要严格控制各个环节,并进行质量检验,以确保生产出的PVC板材符合相关标准和要求。
挤出成型工艺流程
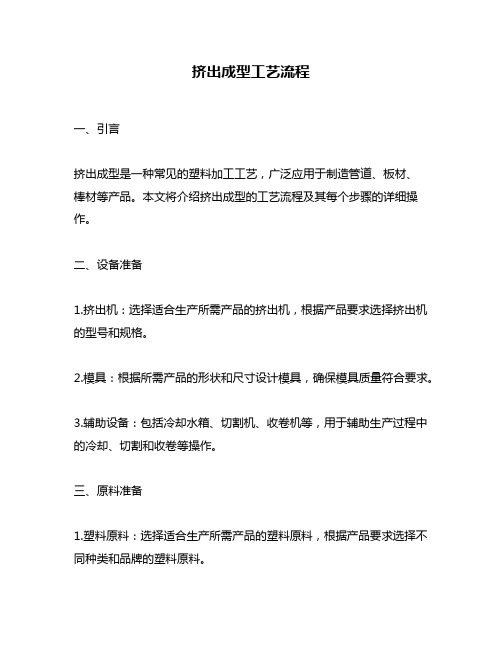
挤出成型工艺流程一、引言挤出成型是一种常见的塑料加工工艺,广泛应用于制造管道、板材、棒材等产品。
本文将介绍挤出成型的工艺流程及其每个步骤的详细操作。
二、设备准备1.挤出机:选择适合生产所需产品的挤出机,根据产品要求选择挤出机的型号和规格。
2.模具:根据所需产品的形状和尺寸设计模具,确保模具质量符合要求。
3.辅助设备:包括冷却水箱、切割机、收卷机等,用于辅助生产过程中的冷却、切割和收卷等操作。
三、原料准备1.塑料原料:选择适合生产所需产品的塑料原料,根据产品要求选择不同种类和品牌的塑料原料。
2.添加剂:根据所需产品的性能要求添加不同种类和比例的添加剂,如增强剂、稳定剂等。
3.颜色母粒:如果需要制造彩色或特殊颜色的产品,则需要添加相应颜色母粒。
四、挤出成型工艺流程1.预处理:将塑料原料加入挤出机的料斗中,同时将所需添加的添加剂和颜色母粒加入料斗中,混合均匀后进入挤出机的螺杆区。
2.熔融:在挤出机的螺杆区内,塑料原料被加热、熔化,并与添加剂和颜色母粒混合均匀。
3.挤出:经过熔融后的塑料原料被推进到模具中,通过模具的形状和尺寸,将塑料原料挤压成所需产品的形状。
4.冷却:在模具中形成产品后,需要对产品进行冷却。
通常采用水冷却或风冷却的方式进行。
5.切割:待产品完全冷却后,通过切割机将产品切割成所需长度。
6.收卷:对于某些需要收卷的产品如管道、板材等,则需要使用收卷机对其进行收卷操作。
五、质量控制1.检查原材料质量是否符合要求,包括塑料原料、添加剂和颜色母粒等。
2.检查模具质量是否符合要求,包括模具设计、制造及使用过程中是否存在损坏或变形等情况。
3.检查挤出机的运行状态是否正常,包括螺杆、加热器、冷却系统等是否正常工作。
4.检查产品的尺寸、外观、质量等是否符合要求,如有不合格品需要及时处理或重新生产。
六、安全注意事项1.操作人员必须穿戴好相应的劳保用品,如手套、口罩、耳塞等。
2.操作人员必须熟悉挤出机的操作流程和相关安全注意事项,严格按照操作规程进行操作。
- 1、下载文档前请自行甄别文档内容的完整性,平台不提供额外的编辑、内容补充、找答案等附加服务。
- 2、"仅部分预览"的文档,不可在线预览部分如存在完整性等问题,可反馈申请退款(可完整预览的文档不适用该条件!)。
- 3、如文档侵犯您的权益,请联系客服反馈,我们会尽快为您处理(人工客服工作时间:9:00-18:30)。
3、现象: ① 熔融料呈流线型,未塑化料始终呈固态
熔体输送理论
1、熔体有四种形式的流动: 正流:
正流(拖曳流)Qd(cm3/h),沿螺槽向机头方向的流动。由于螺杆转动,塑料在螺 杆根部与机筒间形成相对运动造成的,它决定挤出量的大小; 逆流: 逆流(反流)Qp,与Qd相反的流动。由机头、多孔板等阻力元件对熔体的反 压力造成,也叫压力流,随机头压力的升高而增加; 环流: 横流(环流)Qt,由分速度Vbx引起的在螺槽内与正流垂直的流动。对总挤出量 影响不大,可忽略不计,但对熔体的混合、塑化、热交换起重要作用; 漏流: 漏流Ql,由机头阻力元件引起的物料反向流动,沿螺杆与料筒间隙向加料口方
经过分析可看出物料的运动类似螺母运动。 提高固体输送的措施
① 适当提高螺杆转数N和螺槽深度H; ② 采用锥形结构料筒;在加料段料筒内壁开设纵向沟槽(提高fb);
冷却进料段防止物料提前软化; ③ 冷却螺杆加料段(减小fs),增加螺杆表面光洁度(减小fs)
熔融理论
1、研究目的: ① 预测螺槽中未熔化物料量 ② 熔化全部物料所需螺杆长度 ③ 熔融与螺杆参数、物料特性、工艺参数间的关系
说明
1、从纯粹加工的角度来看,降低分子量肯定有利于改善材料的流动性 ,橡胶行业采用大功率炼胶机破碎、塑炼胶料即为一例。但分子量降低 后必然影响材料的强度和弹性,因此需综合考虑。
2、不同的材料,因用途不同,加工方法各异,对分子量的要求不同。总体来看, 橡胶材料的分子量要高一些(约105~ 106 ),纤维材料的分子量要低一些(约104) ,塑料居其中。
板材挤出工艺-靳文涛
板材挤出流程
一条完整的板材生产线
Hale Waihona Puke 原料干燥大部分挤出
工艺都需要对 原料进行干燥 干燥的目的:去 除树脂原料中 的水分.根据原 料特性,干燥温 度和时间各不 相同
挤出机原理
固体进料的挤 出过程,塑料要 经历固体——弹 性体——粘性液 体的变化,变动 的温度、压力, 状态变化和流动 行为十分复杂, 挤出理论应用最 广的是—— 固体输送理论、 熔融理论 熔体输送理论
剪切速率/ s-1 100-101 5X101-5X102 5X102-103 101-103
3、塑料中,用于注射成型的树脂分子量应小些,用于挤出成型的树脂分子量可大 些,用于吹塑成型的树脂分子量可适中。
4、橡胶工业中常用门尼粘度表征材料的流动性,塑料工业中常用熔融指数或流动 长度表征塑料的流动性,其实也是作为最简单的方法用来判断材料相对分子量的 大小。一般橡胶的门尼粘度值大,表示流动阻力大,相对分子量高;塑料的熔融 指数大,表示流动性好,相对分子量小。
B、温度设定思路
螺杆排布分段与温度设定
二,压缩段
A、螺杆排布: . 物料在此段要达到的目的是:
使加工物料获得物理变化和部分化学变化所需的能量, 分布均匀和初步分散,做到组分均质化、粘度接近。 .一般要求物料承受较大的剪切和机筒传热,使之熔融
B、温度设定 a温度太低,树脂半融,到后段包覆性差;温度太高,树脂流动提高,混炼
熔体输送能力的分析
熔体的输送 Q = Qd - Qp - Ql, 实际的流动形式为:熔体 沿螺槽螺旋前进。类似弹簧缠绕在螺槽内。
忽略Ql,经计算熔体输送能力为:
① P↑-Q↓,机头阻力加大,产量下降。 ② N↑-Q↓,转数提高,剪切提高。 ③ D↑-Q↑↑,直径增加,产量明显增加,所以要得到
高的产量,这是最有效的手段之一。
a.螺杆直径Ds——外径( 30~200mm),最常见60~150mm ,随Ds↑→生产能力↑所以,挤 出机规格常以Ds表示。
b.长径比(L/DS) L/DS以25居多。
螺杆排布分段与温度设定
一 ,加料段
A螺杆排布思路有:
a深槽正向螺纹
b中等螺槽大导程正向螺纹,且螺槽容积由大变小,即螺纹导程由大向小 渐变。
剪切速率和剪切应力的影响
高分子流体在加工中主要表现为“剪切变稀”效应。该效应对高分子材料加 工具有重要意义。由于实际加工过程都在一定剪切速率范围内进行(见表1), 因此掌握材料粘-切依赖性的“全貌”对指导改进高分子材料加工工艺十分必要 。
表1 各种加工方法对应的剪切速率范围
加工方法 压制 开炼 密炼 挤出
螺杆转速
转速越高,剪切越大,将分散相均匀分散于基体之中;剪切越大,分 散相尺寸越细,但转速过大,摩擦大易引起热降解,同时停留时间变 短,混合不均。
转速越低,剪切越小,分散不均匀,同时停留时间长,对易分解聚合 物不利。
转速与螺杆结构都是与剪切分散有关,因此必须两者作为整体考虑。
一、影响高分子流体剪切粘度的因素
螺杆排布分段与温度设定
三 熔融段
A、螺杆组分排布 物料在此段要达到的目的是:
1. 细化分散,形成理想的尺寸和结构。 2. 注意保护成品理想的结构不被破坏。 B、温度设定 1、据基料和玻纤含量不同而不同。 2、略筒于基料熔点范围内。
固体输送理论
假设条件: ①物料与螺槽和料筒壁紧密接触形成固体塞(床),以恒速移动; ②略去物料重力、密度变化的影响; ③磨擦系数恒定,压力是螺槽长度的函数; ④螺槽为矩形
挤出机的作用是通过强制喂料使得树脂在机筒中充分熔 融,带排气功能的螺杆可以在此过程中抽走大部分水分及 低分子
渐变螺杆和突变螺杆
渐变螺杆——全长均起压缩作用。 突变螺杆——压缩段很短,甚至一个螺距。 (结晶型塑料,熔融温度范围窄,如尼龙等)
单螺杆结构图
单螺杆结构参数
1)螺杆的几何结构参数 直径、长径比、压缩比、螺槽深度 、螺旋角、间隙等
实验条件和生产工艺条件的影响 (温度T;压力p;剪切速度或剪切应力σ等)
影
响
大分子结构参数的影响
因
(平均分子量;分子量分布;长链支化度等)
素
物料结构及成分的影响 (配方成分,如添料、软化剂等)
二 实验条件和生产工艺条件的影响 1、温度和压力的影响
图1 PMMA的粘度与温度和压力的关系
总的规律:温度升高时,物料粘度下降;压力升高时,物料粘度上升。