五金模具料带设计检讨表
设计失误资料检讨剪切及跳屑篇
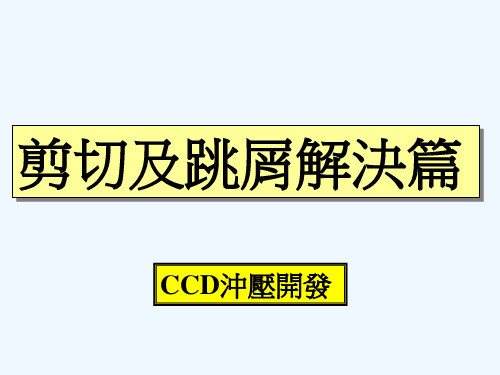
CCD沖壓開發
案例1.
•問題:衝子刃口易崩.跳屑頻繁. •原因:1.材料厚(t=0.8mm);材質硬.剪
切 力大.衝子剪切面為平面.剪切力 集中于刃口邊緣,造成邊緣崩裂.
2.剪切面積大.衝子與廢料接觸,形 成真空面積大,相應吸附力大.易 將廢料帶起,造成跳屑.
•對策:所有衝子刃口邊緣倒0.5∘的
NG之料帶 打折處
OK之料帶
案例4.
•問題:821-365及821-366模
BELLOW尺寸NG(超下限),
•(以050-010*-885為例) 原因:S23,S27站下料定位不準.
5.17
•對策: S23站加裝2PCS定位針,
S27站
• 加裝1PCS定位針; 改善結果:產品尺寸符合圖紙要求
5.23
• (規格為0.05mm MAX.); 原因:下料刀口鈍化; 0.052
•對策:將所有下料刀口及衝子
研磨保養.
• (刀口/沖子定期維修頻率:10KK沖次) 改善結果: 尺寸OK,無毛頭.
0.052
案例7.
•問題:V-CUT未打通,造成折力NG. •原因:V-CUT在下料前完成,下料刀口純
化, 導致V-CUT兩側未打通;
斜 •改善角結(果見:插1.衝圖子).無分崩散裂剪現切象力. .
2.廢料有一定變形.增大與刀 口內壁摩擦.故無跳屑產生.
0.5°
.
崩刃口處
OK衝子
案例2.
•問題點:端子表面壓傷. •原因:跳屑造成端子壓傷.
•對策:在下模座底下加裝吸廢料裝 置.
•改善效果:跳屑減少為1次/4小時
一般下料
加吸廢料機
案例3.
(3)沖子加工面粗糙(0.8s).
五金模具设计点检表(11)
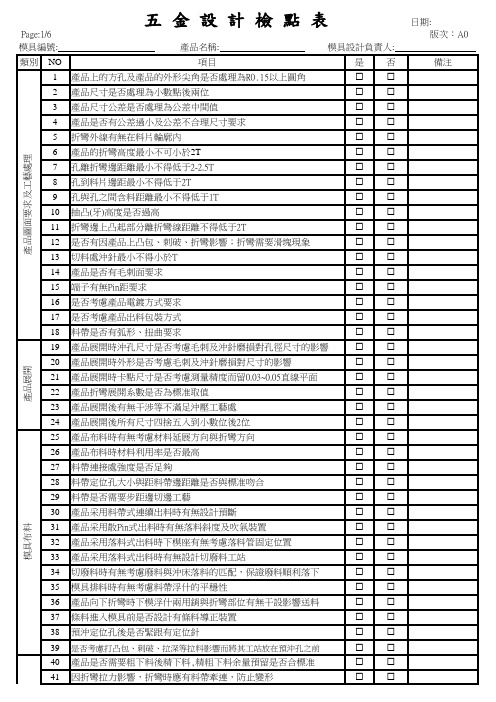
1產品上的方孔及產品的外形尖角是否處理為R0.15以上圓角☐☐2產品尺寸是否處理為小數點後兩位☐☐3產品尺寸公差是否處理為公差中間值☐☐4產品是否有公差過小及公差不合理尺寸要求☐☐5折彎外線有無在料片輪廓內☐☐6產品的折彎高度最小不可小於2T ☐☐7孔離折彎邊距離最小不得低于2-2.5T ☐☐8孔到料片邊距最小不得低于2T ☐☐9孔與孔之間含料距離最小不得低于1T ☐☐10抽凸(牙)高度是否過高☐☐11折彎邊上凸起部分離折彎線距離不得低于2T☐☐12是否有因產品上凸包、刺破、折彎影響;折彎需要滑塊現象☐☐13切料處沖針最小不得小於T ☐☐14產品是否有毛刺面要求☐☐15端子有無Pin距要求☐☐16是否考慮產品電鍍方式要求☐☐17是否考慮產品出料包裝方式☐☐18料帶是否有弧形、扭曲要求☐☐19產品展開時沖孔尺寸是否考慮毛刺及沖針磨損對孔徑尺寸的影響☐☐20產品展開時外形是否考慮毛刺及沖針磨損對尺寸的影響☐☐21產品展開時卡點尺寸是否考慮測量精度而留0.03~0.05直線平面☐☐22產品折彎展開系數是否為標准取值☐☐23產品展開後有無干涉等不滿足沖壓工藝處☐☐24產品展開後所有尺寸四捨五入到小數位後2位☐☐25產品布料時有無考慮材料延展方向與折彎方向☐☐26產品布料時材料利用率是否最高☐☐27料帶連接處強度是否足夠☐☐28料帶定位孔大小與距料帶邊距離是否與標准吻合☐☐29料帶是否需要步距邊切邊工藝☐☐30產品采用料帶式連續出料時有無設計預斷☐☐31產品采用散Pin式出料時有無落料斜度及吹氣裝置☐☐32產品采用落料式出料時下模座有無考慮落料管固定位置☐☐33產品采用落料式出料時有無設計切廢料工站☐☐34切廢料時有無考慮廢料與沖床落料的匹配,保證廢料順利落下☐☐35模具排料時有無考慮料帶浮什的平穩性☐☐36產品向下折彎時下模浮什兩用銷與折彎部位有無干設影響送料☐☐37條料進入模具前是否設計有條料導正裝置☐☐38預沖定位孔後是否緊跟有定位針☐☐39是否考慮打凸包、刺破、拉深等拉料影響而將其工站放在預沖孔之前☐☐40產品是否需要粗下料後精下料,精粗下料余量預留是否合標准☐☐41因折彎拉力影響,折彎時應有料帶牽連,防止變形☐☐產品展開模具布料產品圖面要求及工藝處理42在設計產品倒角時有無多切料防止倒角後材料延長☐☐43在設計產品倒角時有無限位或用料帶支撐防止倒角時擠料變形☐☐44為保證產品尺寸精度,有無考慮先倒角後切料☐☐45設計刀口時是否有切半邊料沖針☐☐46設計刀口時是否有廢料遺留在模板上☐☐47有無使用刀口拼出產品內外形,防止漏切現象☐☐48細小形狀,簡單刀口有無將刀口複雜化防止跳廢料處理☐☐49細小刀口是否分割成兩半,防止堵料設計☐☐50裁邊刀口是否有卡料設計☐☐51刀口是否有導料板或螺絲壓住,防止其跳出模面設計☐☐52下模料帶內螺絲與產品折彎讓位是否足夠☐☐5390度折彎時是否有設計脫料零件☐☐54是否需要考慮折彎拉料或計料而增加限位零件☐☐55折彎工序排序時其先後順序是否有相互沖突情況☐☐56折彎對距離較近邊/孔是否因拉力存在變形而采用先折彎後沖孔/邊☐☐57折彎後是否和後工序零件或浮什存在干涉而無法送料或送料不順等現象☐☐58是否有產品折彎後無法脫出成型零件而采用浮什、滑塊、斜浮什等結構☐☐59是否有偷切而防止產品折彎根部因擠料而脹大的設計☐☐6090度折彎時成型入塊是否需要采用加強筋或負角☐☐61弧高,折彎精度要求較高處是否有整形或調整設計☐☐62天線類細長折彎是否有調整折彎彎曲/上下翹曲設計☐☐63為保證折彎角度,是否需采用45度與90度錯位0.1~0.3設計☐☐64折彎退料塊浮出模面時是否有擋住折彎而無法送料的現象☐☐65導料板/浮什銷與條料間是否留有0.03的間隙設計☐☐66是否有設計在導料板內而造成脫料板無法壓住浮什銷/浮什塊的情況☐☐67采用夾板導正釘時脫料板是否使用襯套輔助脫料☐☐68魚叉類模具采用中間導正釘時下模是否有設計天橋導正料帶及掛料☐☐69采用單邊連料時脫料板是否有叉料零件分料輔助導正條料☐☐70采用對插式排料時是否有設計分料零件防止料帶向內彎曲而送料不順☐☐71雙料帶出料時是否有分料裝置便於收料盤收料☐☐72模具下料後折彎前是否有整平面工站設計☐☐73模具采用單邊切料/落料時是否有限位零件防止切口滑移☐☐74產品散PIN出料時是否有設計吹氣銷☐☐75吹氣銷浮什後有無擋住產品折彎而無法送料現象☐☐76最終切斷時上下模是否設計脫料銷防止產品粘附上下模現象☐☐77最終切斷時下模板有無銑落料斜度☐☐78料帶是否設計有調整扇形/扭曲工站☐☐79是否需設計pin距調整工站☐☐80是否需設計高低pin距調整工站☐☐81刺破/凸包有無設計退料零件☐☐82拉深類模具在拉深前料帶有無剪破便於材料流動☐☐83拉深類模具拉深系數是否合理☐☐84馬口鐵天線類有無調整平面度工站☐☐模具布料85馬口鐵天線類有無調整細長部位扭曲/上下彎曲工站☐☐86馬口鐵天線類模具吹出時導料板有無干涉現象☐☐87鐵殼類模具有無防止折彎擦傷之彎模設計☐☐88鐵殼類模具預斷零件設計於脫料板防止模印☐☐89鐵殼類模具料帶較寬時在模具終間需設計浮生零件☐☐90Z形折彎有無設計調整/整形工站☐☐91端子類模具折彎時需設計管位☐☐92端子類模具下料時需設計限位及強壓☐☐93模具內外導柱有無防呆設計☐☐94下模板材質與厚度是否與設計規范相符☐☐95下模板長度超過450mm時有無分段☐☐96模板分段後兩板間是否留有2mm左右間隙,兩板間是否有工字銷聯接☐☐97下模板熱處理要求與硬度求是否與設計規范相符☐☐98下模板導套孔與固定銷孔是否與設計規范相符☐☐99下模板與模座固定M8螺絲孔有無遺漏☐☐100下模板與下墊板固定M4螺絲孔有無遺漏☐☐101下模板進料口限位零件處模板有無線割☐☐102下模板進料口限位零件處模板側面中央有無攻M4牙壓住其限位零件☐☐103下模板導料板固定螺絲M4有無漏攻☐☐104下模板導料板ψ4固定銷有無漏割☐☐105下模板浮什銷孔/浮什兩用銷孔/導正定讓位孔有無漏割☐☐106下模板入塊型腔孔有無漏割☐☐107下模板浮什入塊型腔孔有無放0.01mm間隙☐☐108下模板壓入塊螺絲牙孔/沉頭孔有無遺漏☐☐109下模板折彎讓位有無遺漏☐☐110下模板銑讓位後入塊是否可以固定☐☐111下模板銑讓位的深度是否與圖面要求相符☐☐112下模板檢知器的位置是否符合排樣要求☐☐113下墊板材質與厚度是否與設計規范相符☐☐114下墊板長度超過450mm時有無分段☐☐115下墊板分段後兩板間是否留有2mm左右間隙☐☐116下墊板與下模板固定M4沉頭孔有無遺漏☐☐117下墊板浮升銷過孔有無遺漏☐☐118下墊板導料板ψ4固定銷敲擊孔有無遺漏☐☐119下墊板入子敲擊過孔有無遺漏☐☐120下墊板落料過孔有無遺漏☐☐121下墊板熱處理要求與硬度求是否與設計規范相符☐☐122下模座材質與厚度是否與設計規范相符☐☐123下模座導料板ψ4固定銷敲擊孔有無遺漏☐☐124下模座落料孔有無遺漏☐☐125下模座敲擊孔有無遺漏☐☐126下模座浮升銷螺絲孔有無遺漏☐☐127下模座與下模板固定M8螺絲沉頭孔有無遺漏☐☐模具布料模板設計128下模座與上模座外導柱有無做防呆設計☐☐129下模座前後倆側M16螺絲有無遺漏☐☐130下模座檢知器固定M4螺絲有無遺漏☐☐131上模座材質與厚度是否與設計規范相符☐☐132上模座長度超過450mm是否采用鋁合金模板☐☐133上模座與沖頭固定螺絲沉頭孔有無遺漏☐☐134上模座與下模座外導柱有無做防呆設計☐☐135上模座沖子敲擊孔有無遺漏☐☐136上模座與夾板固定M8漏絲有無遺漏☐☐137上模座前後倆側M16螺絲有無遺漏☐☐138上模座與蓋板固定M8螺絲有無遺漏☐☐139蓋板材質與厚度是否與設計規范相符☐☐140蓋板與沖壓機固定M12螺絲間距是否相符☐☐141蓋板與沖頭固定M12螺絲有無遺漏☐☐142蓋板沖子敲擊孔有無遺漏☐☐143蓋板與上模座固定M8螺絲沉頭孔有無遺漏☐☐144上墊板材質與厚度是否與設計規范相符☐☐145上墊板熱處理要求與硬度求是否與設計規范相符☐☐146上墊板彈簧孔有無遺漏☐☐147上墊板與夾板固定M5螺絲沉頭孔有無遺漏☐☐148上墊板內導柱孔有無遺漏☐☐149上墊板沖子敲擊孔有無遺漏☐☐150上墊板上模座與夾板固定螺絲過孔有無遺漏☐☐151夾板材質與厚度是否與設計規范相符☐☐152夾板熱處理要求與硬度求是否與設計規范相符☐☐153夾板入塊型腔孔有無漏割☐☐154夾板入塊型腔孔有無放0.01mm間隙☐☐155夾板異型沖針有無做防呆設計☐☐156夾板固定沖針壓塊有無做防呆☐☐157夾板與上墊板固定M4螺絲有無遺漏☐☐158夾板內導柱固定螺絲是否有遺漏☐☐159夾板沖針固定螺絲有無遺漏☐☐160夾板入塊有無做防呆設計☐☐161夾板內等高柱孔是否有遺漏☐☐162背脫板材質與厚度是否與設計規范相符☐☐163背脫板熱處理要求與硬度求是否與設計規范相符☐☐164背脫板沖針過孔有無遺漏☐☐165背脫板脫料板固定螺絲過孔有無遺漏☐☐166背脫板與脫料板固定M5螺絲沉頭孔有無遺漏☐☐167背脫板固定沖針的壓塊沉頭孔有無遺漏☐☐168背脫板固定沖針的螺絲沉頭孔有無遺漏☐☐模板設計169背脫板ψ5合銷孔有無遺漏☐☐170脫料板材質與厚度是否與設計規范相符☐☐171脫料板熱處理要求與硬度求是否與設計規范相符☐☐172脫料板入子型腔孔有無遺漏☐☐173脫料板ψ4合銷孔有無遺漏☐☐174脫料板入塊固定的沉頭孔有無遺漏☐☐175脫料板折彎讓位有無遺漏☐☐176脫料板銑讓位後入塊是否可以固定☐☐177脫料板料帶強壓料槽是否加工☐☐178脫料板下模入子固定螺絲洗讓位有無遺漏☐☐179脫料板導料板洗讓位有無遺漏☐☐180脫料板浮升銷洗讓位有無遺漏☐☐181脫料板導正針孔有無遺漏☐☐182脫料板與背脫板固定M5螺絲有無遺漏☐☐183脫料板內導柱固定M4螺絲有無遺漏☐☐184脫料板沖針過孔有無單邊放0.005間隙☐☐185脫料板入塊與沖針有無放0.005間隙☐☐186脫料板入塊有無做防呆設計☐☐187脫料板入塊讓位有無遺漏☐☐188脫料板洗讓位的深度是否與圖面相符☐☐189導料板材質與厚度是否與設計規范相符☐☐190導料板熱處理要求與硬度求是否與設計規范相符☐☐191導料板ψ4固定銷孔有無遺漏☐☐192導料板固定螺絲過孔有無遺漏☐☐193導料板與料帶間隙是否加工到位☐☐194導料板與脫料板洗讓位是否相符☐☐195導料板與料帶間隙是否符合設計規范☐☐199下模刀口有無做防呆設計☐☐200下模刀口有無做三層結構☐☐201下模刀口第一層是否做到厚度8.000內孔留直面3.0下單+1度斜割☐☐202下模刀口間隙是否符合設計規范☐☐203下模刀口有無做折彎讓位設計☐☐204下模刀口為預防跳料有無做拼裝設計☐☐205下模刀口固定有無做螺絲沉頭孔設計☐☐206下模刀口固定螺絲沉頭孔深度是否與圖面相符☐☐207下模墊塊1有無做落料斜度☐☐208下模墊塊2在下模刀口磨損後有無做替換墊塊☐☐模板設計209脫料板入子有無做防呆設計☐☐210脫料板入子與沖針間隙有無放到0.003mm ☐☐211脫料板入子掛台讓位是否遺漏☐☐212脫料板入子掛台深度是否與圖面相符☐☐213脫料板入子折彎讓位有無遺漏☐☐214脫料板入子有無做沖針過孔讓位☐☐215脫料板入子定位針孔有無遺漏☐☐216☐☐217☐☐218☐☐219☐☐220☐☐221☐☐222☐☐223☐☐224☐☐225☐☐226☐☐227☐☐228☐☐229☐☐230☐☐231☐☐232☐☐233☐☐234☐☐235☐☐236☐☐237☐☐238☐☐保存期零件設計。
模具设计检查表
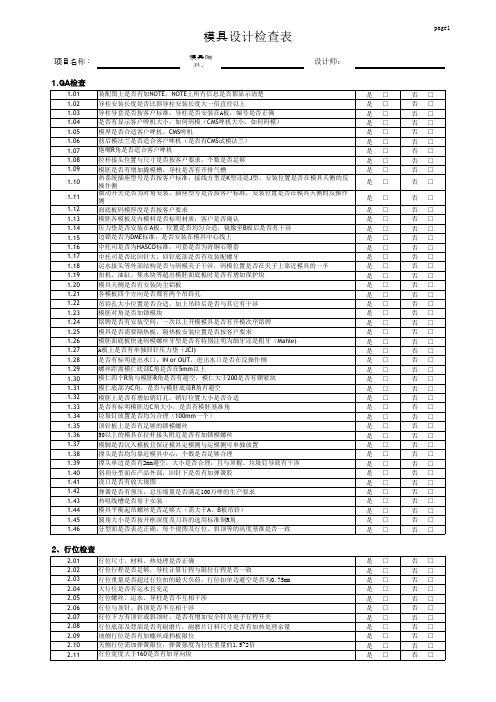
模具设计检查表
项目名称 模具编号: 设计师:
page3
6 、流道系统检查
6.01 6.02 6.03 6.04 6.05 6.06 6.07 6.08 6.09 6.10 是否有流道、浇口放大视图、流道转角处是否有加R角 流道头部是否有按要求设计圆弧过度 入水点与客供资料、3D图是否一致 热咀是否比分型面低1mm 热咀孔径是否有标公差 咀嘴处是否为平面或小于5%的斜面 牛角及潜水平面在产品上是否有做凹坑 入水点头部R处钢料强度是否足够 浇口顶针冷料是否比牛角及潜水冷料长3-5mm 水口顶针在两模仁之中是否有加水口套 是 是 是 是 是 是 是 是 是 是 □ □ □ □ □ □ □ □ □ □ 否 否 否 否 否 否 否 否 否 否 □ □ □ □ □ □ □ □ □ □
模具设计检查表
项目名称: 1.GA 检查
1.01 1.02 1.03 1.04 1.05 1.06 1.07 1.08 1.09 1.10 1.11 1.12 1.13 1.14 1.15 1.16 1.17 1.18 1.19 1.20 1.21 1.22 1.23 1.24 1.25 1.26 1.27 1.28 1.29 1.30 1.31 1.32 1.33 1.34 1.35 1.36 1.37 1.38 1.39 1.40 1.41 1.42 1.43 1.44 1.45 1.46 装配图上是否有加NOTE,NOTE上所有信息是否都显示清楚 导柱安装长度是否比斜导柱安装长度大一倍直径以上 导柱导套是否按客户标准,导柱是否安装在A板,编号是否正确 是否有显示客户啤机大小,如何码模(CMS啤机大小、如何码模) 模厚是否合适客户啤机、CMS啤机 前后模法兰是否适合客户啤机(是否有CMS试模法兰) 炮嘴R角是否适合客户啤机 拉杆接头位置与尺寸是否按客户要求,个数是否足够 模胚是否有增加撬模槽,导柱是否有开排气槽 热系统插座型号是否按客户标准,接线方型是K型还是J型,安装位置是否在模具天侧的反操作 侧 微动开关是否为对角安装,插座型号是否按客户标准,安装位置是否在模具天侧的反操作侧 面底板码模厚度是否按客户要求 模胚各模板及内模料是否标明材质,客户是否确认 压力垫是否安装在A板,位置是否均匀合适,镜像至B板后是否有干涉 边锁是否为DME标准,是否安装在模具中心线上 中托司是否为HASCO标准,司套是否为青铜石墨套 中托司是否比回针大,回针底部是否有攻装配螺牙 运水接头等外部结构是否与码模夹子干涉,码模位置是否在夹子上靠近模具的一半 扣机、油缸、集水块等超出模胚面底板时是否有增加保护块 模具天侧是否有安装防尘铝板 各模板四个方向是否都有两个吊铃孔 吊铃孔大小位置是否合适,加上吊铃后是否与其它有干涉 模胚对角是否加锁模块 铭牌是否有安装空间,一次以上开模模具是否有开模次序铭牌 模具是否需要隔热板,隔热板安装位置是否按客户要求 模胚面底板快速码模螺丝牙型是否有特别注明为细牙还是粗牙(Mahle) A板上是否有单独回针压力垫(JCI) 是否有标明进出水口,IN or OUT,进出水口是否在反操作侧 螺丝距离模仁底部C角是否在5mm以上 模仁四个R角与模胚R角是否有避空,模仁大于200是否有锲紧块 模仁底部为C角,是否与模胚底部R角有避空 模胚上是否有增加销钉孔,销钉位置大小是否合适 是否有标明模胚边C角大小,是否有模胚基准角 垃圾钉放置是否均匀合理(100mm一个) 顶针板上是否有足够的锁模螺丝 50以上的模具在拉杆接头附近是否有加锁模螺丝 模脚是否沉入模板且保证模具定模侧与运模侧可单独放置 撑头是否均匀靠近模具中心,个数是否足够合理 撑头单边是否有2mm避空,大小是否合理,且与顶棍、垃圾钉导致有干涉 斜顶分型面在产品外部,回针下是否有加弹簧胶 浇口是否有放大视图 弹簧是否有预压,总压缩量是否满足100万啤的生产要求 热咀线槽是否易于安装 模具平衡起吊螺丝是否足够大(需大于A、B板吊铃) 圆角大小是否按开框深度及刀具的选用标准倒R角 分型面是否表达正确,每个视图及行位、斜顶等的高度基准是否一致 是 是 是 是 是 是 是 是 是 是 是 是 是 是 是 是 是 是 是 是 是 是 是 是 是 是 是 是 是 是 是 是 是 是 是 是 是 是 是 是 是 是 是 是 是 是 □ □ □ □ □ □ □ □ □ □ □ □ □ □ □ □ □ □ □ □ □ □ □ □ □ □ □ □ □ □ □ □ □ □ □ □ □ □ □ □ □ □ □ □ □ □ 否 否 否 否 否 否 否 否 否 否 否 否 否 否 否 否 否 否 否 否 否 否 否 否 否 否 否 否 否 否 否 否 否 否 否 否 否 否 否 否 否 否 否 否 否 否
模具自检表格

8.不可以打编号的产品是否在水口上打上编号.
行 位 部 位
冷 却 系 统
顶出 系 统
制模 员:
10.攻牙孔的倒角位是否准确. 11.攻牙孔的孔径、孔距的尺寸是否准确无误. 1.行位起止位置是否正确可靠、装配合理、滑动顺畅.
2.行位润滑系统是否设立可靠.
1.冷却(运水)是否畅通.
2.料咀冷却水是否堵好,并无漏水现象.
有□ 没有 □
是□
否□
有□ 没有 □ 准确 □ 不准确 □ 准确 □ 不准确 □
是□
否□
是□
否□
是□
否□
是□
否□
正确 □ 不正确 □
正确 □ 不正确 □
审核:
注:试模前务必认真检查以上的重点,检查完将此表填好,交由文员存档.
目的:
模具自检表
鉴于模具制造周期较长,遗忘之事时有发生;模具试模前亦经常由于一些小疏忽 而导致重上压铸机、试模多次,浪费资源,为避免此类事情的发生,特针对一 些易遗忘和疏忽之处列于下表以备自检或互查。
型 号:
订 单 号:
开发日期:
项目
内容
资 1.模具与图纸尺寸是否合格(计缩水). 料
复 2.有公差的地方是否都准确无误. 核
1.顶针、司筒针的高度、方向、位置是否正确及无漏装.
2.顶针、斜顶及推板装配是否正确、伸缩顺畅,复位正确可 靠.
检查日
试模日
期:
期:
检查结果
备注
合格 □ 不合格 □
准确 □ 不准确 □
准确 □ 不准确 □
是□
否□
够□ 不够 □
有 □ 没有 □
平□ 不平 □
有□ 没有 □
有□ 没有 □
模具设计自检表
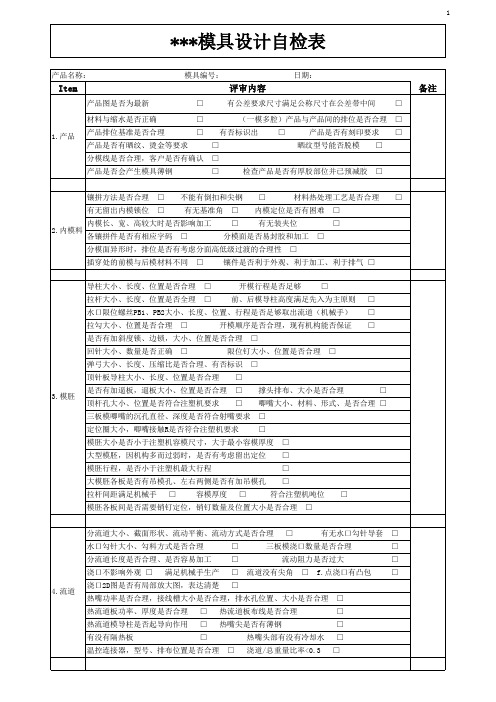
分模线是否合理,客户是否有确认 □
产品是否会产生模具薄钢
□
检查产品是否有厚胶部位并已预减胶 □
备注
镶拼方法是否合理 □ 不能有倒扣和尖钢 □
材料热处理工艺是否合理 □
有无留出内模锁位 □ 有无基准角 □ 内模定位是否有困难 □
内模长、宽、高较大时是否影响加工 □ 有无装夹位
□
2.内模料
各镶拼件是否有相应字码 □
行位限位方式是否合理 □
行位是否需要耐磨板
□
行位弹簧大小、长度、压缩比是否正确 □ 行位是否有加冷却水
□
行位尺寸较大时,是否有导滑槽
□ 是否需要作镶拼件,是否容易加工 □
行位动力机构为油缸时,油缸的缸径、行程、固定方式是否合理 □
行位出模导致产品变形时,是否有行位顶出机构 □
行位是否影响合模 □
行位是否需要延时机构 □
前模抽芯机构之型芯是否影响流道取出 □
抽芯机构复位动作是否合理
□
6.镶件 镶件定位方式是否合理 □
有无可换镶件
□
大镶件有无运水
□
镶件是否易装、拆模
□
顶针、直顶、斜顶出胶位时,是否会夹住产品 □ 顶针类避免与前模面直接碰撞 □
顶针大小、位置、长度是否合理
□
7.顶出 机构
有托顶针、扁顶针、托位避空是否足够,托位是否标准
□
有没有隔热板
□
热嘴头部有没有冷却水 □
温控连接器,型号、排布位置是否合理 □ 浇道/总重量比率<0.3 □
2
1.产品 5.机构
产品图是否为最新
□
有公差要求尺寸满足公称尺寸在公差带中间 □
行位型芯过长时,有否留出定位,防止型芯变形 □ 滑块导向长度大于全长2/3 □
五金模具设计自检表
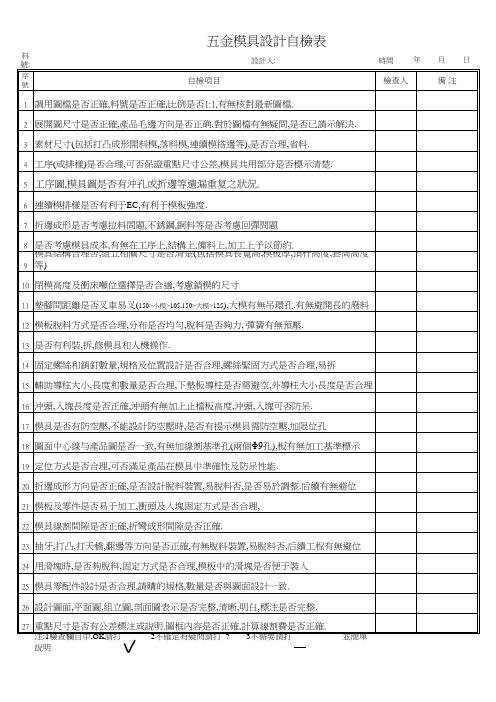
工序圖,模具圖是否有沖孔或折邊等遺漏重复之狀況.
連續模排樣是否有利于EC,有利于模板強度. 折邊成形是否考慮拉料問題,不銹鋼,銅料等是否考慮回彈問題 是否考慮模具成本,有無在工序上,結構上,備料上,加工上予以節約. 模具結構合理否,組立相關尺寸是否清楚(包括模具長寬高,模板厚,頂杆高度,套筒高度等) 閉模高度及衝床噸位選擇是否合適,考慮鎖模的尺寸 墊腳間距離是否叉車易叉(150>小模>105,150>大模>125),大模有無吊環孔.有無避開長的廢料 模板脫料方式是否合理,分布是否均勻,脫料是否夠力, 彈簧有無預壓. 是否有利裝,拆,修模具和人機操作. 固定螺絲和銷釘數量,規格及位置設計是否合理,螺絲緊固方式是否合理,易拆 輔助導柱大小,長度和數量是否合理,下墊板導柱是否需避空,外導柱大小長度是否合理 沖頭,入塊長度是否正確,沖頭有無加上止檔板高度,沖頭,入塊可否防呆. 模具是否有防空壓,不能設計防空壓時,是否有提示模具需防空壓,加限位孔 圖面中心線与產品圖是否一致,有無加線割基準孔(兩個Φ9孔),板有無加工基準標示 定位方式是否合理,可否滿足產品在模具中準確性及防呆性能. 折邊成形方向是否正確,是否設計脫料裝置,易脫料否,是否易於調整.后續有無避位 模板及零件是否易于加工,衝頭及入塊固定方式是否合理, 模具線割間隙是否正確,折彎成形間隙是否正確. 抽牙,打凸,打天橋,翻邊等方向是否正確,有無脫料裝置,易脫料否,后續工程有無避位 用滑塊時,是否夠脫料,固定方式是否合理,模板中的滑塊是否便于裝入 模具零配件設計是否合理,請購的規格,數量是否與圖面設計一致. 設計圖面,平面圖,組立圖,剖面圖表示是否完整,清晰,明白,標注是否完整. 重點尺寸是否有公差標注或說明.圖框內容是否正確,計算線割費是否正確.
注:1檢查欄目中,OK請打 2不確定有疑問請打 ? 3不需要請打 並簡單說明
塑胶开模检讨表

NO.D/R-008-B(试用版)
第 5 页,共 5 页 备注
10-1, 冷却方式:□模仁冷却 □模仁外围冷却
10-2,冷却水路加工的时间:
□T1 前加工 □T1~T2 期间加工 □待通知加工
特别要求: 冷
1.模具尺寸大于 430X430 时,运水尽可能通过模仁(尤其是公模仁),无法将运水通过模
□整体精公一个 □分体精公各一个
分体铜公组成说明:
放电间隙:精公 mm/单边 粗公 mm/单边 缩水率:
%
1.模仁材质
□进口 □国产
□718 □738 □NAK80
□S136 □S136H □
母
4材
2.模仁反装及防呆设计 □有
□无
模
质
3.模仁互换的区域 □有:
仁
□无
区域
4 模仁材料标识与位置: 必须有 位置□PL 面 □
模
滑
□无 □有
6
块 公 特别要求:
模
1. 活动件与模胚要有对应明显标志.
2. 要有限位限螺丝及斜销,尽量不使用定珠
机 型:
序
项
号
目
逻辑科技有限公司 开模检讨表
(附 A4 或 A3 图纸关存档)
内容及要求
NO.D/R-008-B(试用版)
第 4 页,共 5 页 备注
□无 □有
特别要求:
斜
1.斜/直销(顶)两侧要做油槽,.
5)下盖等“+.-”号,穴号及其它标志一般不可标志在顶针上。
□以上经逻辑,模具厂:
双方检讨确认,依此检讨进行模具设计,如有修改将书面通知对方,经对方同意
方可进行变更,书面文件存档。
□以上经逻辑,模具厂:
模具部管理工作检讨书范文模板

[公司名称][日期][部门负责人姓名][部门负责人职位][部门名称]尊敬的[公司领导职位或姓名]:您好!在此,我代表模具部全体成员,就近期在工作中出现的不足和失误,向您及公司表达诚挚的歉意,并就以下问题进行深刻检讨。
一、检讨事项1. 工作计划执行不到位。
近期,我部在执行年度工作计划过程中,未能严格按照既定目标和时间节点推进各项工作,导致部分项目进度滞后,影响了整体生产进度。
2. 模具质量把控不严。
在模具生产过程中,由于质量管理不善,导致部分模具存在尺寸偏差、表面粗糙等问题,影响了后续产品的质量。
3. 员工技能培训不足。
我部员工在专业技能方面存在一定差距,未能满足生产需求,导致生产效率低下。
4. 部门内部沟通不畅。
部门内部沟通协调不够,导致信息传递不及时,影响了工作效率。
二、原因分析1. 工作计划执行不到位:部门负责人对工作计划的重要性认识不足,未能有效监督和指导下属落实计划。
2. 模具质量把控不严:质量管理意识薄弱,对生产过程中的质量监控不力,导致质量问题出现。
3. 员工技能培训不足:部门负责人对员工技能培训重视程度不够,未能及时为员工提供培训机会。
4. 部门内部沟通不畅:部门内部缺乏有效的沟通机制,导致信息传递不畅,影响了工作效率。
三、整改措施1. 加强工作计划执行力度。
部门负责人将严格按照工作计划推进各项工作,确保按时完成各项任务。
2. 严格把控模具质量。
加强质量管理,对生产过程中的质量问题进行及时发现和纠正,确保模具质量符合要求。
3. 提升员工技能水平。
加大员工培训力度,为员工提供更多学习机会,提高员工专业技能。
4. 优化部门内部沟通。
建立健全沟通机制,确保信息传递及时、准确,提高工作效率。
四、承诺我将以此次检讨为契机,认真反思自身不足,切实改进工作作风,带领模具部全体成员,努力提高工作质量,为公司发展贡献力量。
敬请领导批评指正!此致敬礼![部门负责人签名][部门名称][公司名称]。
- 1、下载文档前请自行甄别文档内容的完整性,平台不提供额外的编辑、内容补充、找答案等附加服务。
- 2、"仅部分预览"的文档,不可在线预览部分如存在完整性等问题,可反馈申请退款(可完整预览的文档不适用该条件!)。
- 3、如文档侵犯您的权益,请联系客服反馈,我们会尽快为您处理(人工客服工作时间:9:00-18:30)。
1 产品图是否为最新产品图(最新版本号为: 2 3D产品图与2D产品图是否吻合 3 2D产品图的公差是否有放置 4 产品有字印的是否在料带里面刻印出来 )
是
否
备注
检图必备条件:2D产品图;冲床资料;客户标准;主管进行审核签字;审核无法按要求勾选时必须备注,勾选否也需备注;2次检图必须有上 次的检图规范表格进行参照。以上条件除客户原因外缺少的不做评审安排 √
料带与客户资料检查 工艺要求 料带使结构可行性性检查 图面与其他
5 废料是否可以按客户冲床指定区域掉落 6 料带是否已放置在所绘制的客户冲床内(需提供前视图和俯视图) 7 客户的冲床是否有产品传送带,是否有绘制 8 是否有接刀口要求,无要求是否按内部标准设计 9 客户是否要求提供成型可行性分析 料带的最小搭边值:前( MM)后( MM)左右之间( MM) %)是否最大化 ) %) MM) MM) ) MM) MM) 冲床上滑块调节行程( 送料器调节行程 装模高度 ( ( 10 是否有料宽和步距要求。现有设计是否能够满足 材料利用率为( 11 客户是否有指定的误检方式,有无要求时的方式为: 12 冲床吨位( 13 冲床闭合高度( 14 冲床送料高度( 15 冲床送料方向: T) 设计冲裁力( MM) MM) T) ( 设计闭模高度( 设计送料高度( 料带送料方向:
料带补充说明:
检讨参与人员:
审核:
批准:
ห้องสมุดไป่ตู้
最大冲裁力为冲床吨位的80% 现有比例为(
1 单边带料时是否做工艺带料从而使送料顺畅 2 料带双边带料时延伸系带是否不会变形到影响送料和抬料板的上插针孔 3 相对于材料薄且较长的料带是否有做加工艺筋来使料带更有强度 4 有工艺难点的工序前面是否有备2个以上的工艺方案来预防 5 有单边成形的工序是否有做工艺折弯来减少侧向力 6 产品是否需要做成型可行性分析,是否有做 7 折弯工序和成形工序是否需要放回弹是否有标示出来 8 折弯工序和成形工序需要挤R的是否有指示出来(挤R面为非基准面) 9 料带的冲孔工序是否为最后的工作工序 10 所有冲孔是否一次性完成(重要孔必须在一起冲) 11 是否可以调整刀口顺序从而减少步距 初始线的绘制是否可以满足以下几点要求:a.在2次送料时可以保证有连个插针在对 1 料带进行定位;b.可以保证在切边的过程中不会有废料留在模面上;c.厚材不存在 冲半个孔;d.成型不会单向受力;e.切边不会单边切。 优先顺序a>b>c>d>e 2 带料面是否为产品基准面,不是产品基准面时料带是否可以稳定的生产产品(注明理由) 3 刀口的分布是否可以满足下模刀口,抬料板,脱料板的强度 4 废料尺寸最大不超过300MM 5 插针的位置是否可以满足送料的顺畅和顶针的合理排布 6 双边带料时S形带料是否可以保证抬料板上插针孔的位置和送料顺畅 7 向上成形工站是否有足够的空间分布脱料板 8 向下翻边或单边成形否有足够的空间进行靠刀设计 9 所有斜楔装置是否有足够的空间设计 10 是否有足够的空步来满足结构的设计 11 是否有绘制出产品的掉落方向 12 产品漏斗是否有绘制是否最大角度的保证掉料顺畅 13 一出多样件时是否有标示使零件可以区分出来 14 掉落镜像件是否漏斗已分开掉落,废料和产品是否不会在一起掉落 1 每一站的成型力以及所需压料力时候有标示出来 2 每一站的工序名称和工作部位是否有很清晰的表达 3 图框信息是否完整 4 客户无接刀口要求的是否有做接刀口要望 5 客户没指明冲压方向的是否有做毛刺方向要望 6 有工艺难点无法把握时是否需要跟客户做要望,是否有做