磨工工艺 第三章 磨削用量
磨削工艺系数(常用)
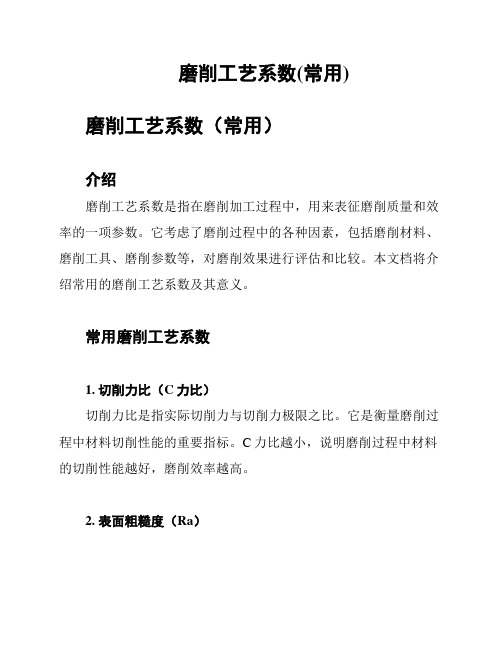
磨削工艺系数(常用)
磨削工艺系数(常用)
介绍
磨削工艺系数是指在磨削加工过程中,用来表征磨削质量和效率的一项参数。
它考虑了磨削过程中的各种因素,包括磨削材料、磨削工具、磨削参数等,对磨削效果进行评估和比较。
本文档将介绍常用的磨削工艺系数及其意义。
常用磨削工艺系数
1. 切削力比(C力比)
切削力比是指实际切削力与切削力极限之比。
它是衡量磨削过程中材料切削性能的重要指标。
C力比越小,说明磨削过程中材料的切削性能越好,磨削效率越高。
2. 表面粗糙度(Ra)
表面粗糙度是指工件表面在磨削加工后的表面质量。
它反映了磨削加工过程中的磨料和工件之间的相互作用情况。
Ra值越小,表面质量越好,磨削效果越理想。
3. 磨削温度(T)
磨削温度是指在磨削过程中磨削区域的温度。
磨削温度对磨削效果和工件表面质量有很大影响。
一般来说,磨削温度越低,磨削效果越好,工件表面质量越高。
4. 磨损量(W)
磨损量是指磨削过程中磨削工具的磨损情况。
磨削工具的磨损量越小,说明磨削过程中磨料的消耗越少,磨削效率越高。
结论
磨削工艺系数是评价磨削过程中材料切削性能、工件表面质量和磨削效果的重要指标。
切削力比、表面粗糙度、磨削温度和磨损量是常用的磨削工艺系数。
通过合理控制这些参数,可以提高磨削效率,优化磨削工艺。
以上是对磨削工艺系数(常用)的简要介绍。
如需深入了解,请参考相关资料。
磨削加工中的磨削参数

磨削加工中的磨削参数磨削加工是工业制造中重要的加工方式之一,其广泛应用于汽车制造、航空航天、能源等众多领域。
磨削加工的主要功能是通过磨头或磨轮切削被加工物表面的材料,使其达到所需形状和尺寸。
磨削加工中磨削参数的选取对加工效率和产品的质量均有决定性影响,因此研究和掌握磨削参数的选取方法是磨削加工中的一项重要任务。
1. 磨削参数的种类磨削加工中常用的磨削参数包括磨料种类、磨粒尺寸、磨削速度、磨削深度、进给速度、接触时间等。
其中,磨削速度是指砂轮旋转的速度;磨削深度是指切削的深度,其与磨头的尺寸、磨头硬度、砂轮至被加工物的距离等因素有关;进给速度是指砂轮在被加工物表面穿切的速度,其与旋转速度、磨头形状、被加工物硬度等因素有关;接触时间是指砂轮与被加工物表面接触的时间,在磨削加工过程中,其中一个参数变化都会对加工效果产生影响。
2. 磨削参数的影响因素磨削参数的选取需要考虑多种因素,例如被加工物的性质、粘结材料的类型和砂轮的硬度等。
不同的材料需要选用不同的磨料,并且在磨削加工中还需要考虑材料的韧性、硬度和加工前表面的粗糙度等因素。
例如,在加工较硬的材料时,应使用较细的磨粒,旋转速度和进给速度应适当降低,以避免磨具损坏和加工效率低下。
3. 磨削参数的设计方法在确定磨削参数时,需要进行实验和分析评估,并且需要考虑到实际加工的情况。
在实验中,需要根据被加工物和砂轮的性质等因素,设计不同的实验方案,并且通过观测被加工物表面的状态、测量表面粗糙度和表面变形等指标来对磨削加工效果进行评估。
如果磨削效果不理想,则需要对磨削参数进行调整,并重新进行实验。
此外,为了避免磨削加工中磨削参数的误选所带来的不必要浪费和产品质量的降低,还可以应用计算机辅助加工技术,通过建立数值模型,对磨削参数进行模拟分析和优化设计,从而提高磨削加工的效率和质量。
4. 磨削加工中磨削参数的优化针对特定的磨削加工过程,通过对磨削参数不断调整和优化,可以达到更好的加工效果。
磨工第三章

六、常用夹具
图3-11 圆柱塞规
(3)用花盘装夹工件 花盘是一种铸铁圆盘(图3-8),在 花盘平面上有很多径向分布的T形槽,可以安插各种螺 柱,以螺旋压板夹紧工件,也可以通过精密90°角铁装 夹工件。
六、常用夹具
(4)闭式中心架 内圆磨削用的中心架为闭式中心架, 由架体1、上盖9和爪8等组成,见图3-10。
图3-6 三爪自定心卡盘 1—锥齿轮 2—卡盘体 3—卡爪 4—丝盘
六、常用夹具
图3-7 四爪单动卡盘 1—卡爪 2—螺杆 3—卡盘体
六、常用夹具
(2)四爪单动卡盘 四爪单动卡盘由卡爪、螺杆、卡盘 体等组成(见图3-7)。
图3-8 用花盘装夹工件
六、常用夹具
图3-9 压板的装夹方法
六、常用夹具
三、内圆磨削的方法
表3-1 内圆磨削中的加工余量(单位:mm)
三、内圆磨削的方法
表3-2 内圆磨削用量表(单位:mm)
四、内圆砂轮的选择
(1)砂轮直径的选择 砂轮直径的选择在内圆磨削中是 一个比较复杂的问题。
表3-3 内圆砂轮直径的选择(单位:mm)
(2)砂轮宽度的选择 采用较宽的砂轮,有利于提高工 件表面质量和生产效率,并可降低砂轮的磨耗。 (3)砂轮硬度的选择 内圆磨削的磨削弧较大,工件散 热条件差,只有充分发挥砂轮的“自锐性”,才能减 小磨削力和磨削热。
图3-1 内圆磨削的形式
一、内圆磨削的形式
图3-2 M2110型内圆磨床
二、内圆磨削的特点
1)内圆磨削时,所用砂轮直径较小,砂轮转速又受到内 圆磨具转速的限制(目前一般内圆磨具的转速在10000~ 20000r/min之间),因此磨削速度一般在20~30m/s之间。 2)内圆磨削时,由于砂轮与工件成内切圆接触,砂轮与 工件的磨削弧比外圆磨削大,因此磨削热和磨削力都 比较大,磨粒容易磨钝,工件容易发热或烧伤。 3)内圆磨削时,切削液不易进入磨削区域;磨屑也不容 易排出。
第三节 外圆磨床的磨削方法

充分发挥砂轮的切削能力,磨削效率高,同时也适用于成形磨削。然而,在磨削过程中砂轮受到磨削力大,工件易发生变形和烧伤。
3.深磨法
是一种比较先进的方法,生产效率高,磨削余量一般为0.1mm~0.35mm.用这种方法可一次走刀将整个余量磨完。
4.综合磨法
综合了横磨法和纵磨法的优点,生产效率比纵磨法高,精度和表面质量比横磨法高。
无中心孔的圆柱形零件多采用三爪自定心卡盘装夹,不对称或形状不规则的工件则采用四爪单动卡盘或花盘装夹。空心工件常安装在心轴上磨削外圆。
三、磨削外圆
工件的的外圆一般在普通外圆磨床上磨削。外圆磨削一般有纵磨、横磨、深磨和综合磨法四种。
1.纵磨法
常用于磨削较大的工件,是单件、小批量生产的常用方法。纵磨每次的纵向进给量小,磨削力小,散热条件好,充分提高了工件磨削 的精度和表面质量,但磨削效率较低。
(1)表面粗糙度大。
(2)生产效率较低。磨内圆时,砂轮轴长且细,刚度很差,不宜采用较大的切削深度和进给量。
五、磨内、外圆锥面
磨内外圆锥面与磨内外圆面相似,主要区别是工件和砂轮的相对位置不同。磨内外锥面时,工件轴线相对于砂轮轴线偏斜一圆锥斜角。常用的加工方法有转动头架或转动工作台两种。
任务小结
回顾本次任务所学知识,强调本节课的重点与难点,本课主要讲解磨削的四要素、外圆磨削的方法、内圆磨削的方法等基础知识。
四、磨削内圆
磨内圆是用高速旋转的砂轮精加工孔的方法。内圆的磨削可在万能外圆磨床上进行,其尺寸公差可达IT7,表面粗糙度值Ra为1.6~0.4μm.
磨内圆时,砂轮旋转为主运动,零件的低速旋转为圆周进给运动。
1.内圆的磨削方法
与外圆磨削类似,内圆磨削也可分为纵磨法和横磨法。 在多数情况下都采用纵磨法。
磨削加工参数

磨削加工参数
1磨削要素
磨削速度v:砂轮旋转运动的线速度,单位为m/s。
工件速度vw:工件运动的线速度,单位为m/min。
轴向进给量fa:对平面磨削而言,指工作台每单行程或双行程后砂轮轴向移动量,单位为mm/单行程或mm/双行程,本“推荐表”采用mm/双行程为单位。
对外圆、内圆磨削而言,指工件每相对于砂轮的轴向移动量,单位为mm/r。
径向进给量fr:砂轮径向切入工件的深度,单位为mm。
Ra:以轮廓算术平均偏差评定的表面粗糙度参数,单位为μm。
B:砂轮宽度,单位为mm。
2平面磨削
3外圆磨削
4内圆磨削。
磨削加工通用工艺

磨削加工通用工艺范围本守则规定了磨削加工的工艺规则,适用于公司的磨削加工。
2 工件的装夹2.1 轴类工件装夹前应检查中心孔,不得有椭圆、碰伤、毛刺等缺陷,并擦干净,经热处理的工件,须修好中心孔,并加好润滑油。
2.2 在两顶尖间装夹轴类工件时,装夹前要调整尾部,使两顶尖轴线重合在外圆磨床上用尾座顶紧顶紧工件磨削时,其顶紧力应适当,在磨削中还应根据工件的涨缩情况调整顶紧力。
2.4 在平面磨床上用磁盘吸住磨削支承面较小或较高的工件时,应在适当位置增加挡铁,以防磨削时工件飞出。
3 砂轮的选用和安装3.1根据工件的材料、硬度、精度和表面粗糙的要求,合理选用砂轮牌号和精度。
根据目前的生产情况,一般选用的砂轮牌号是GZ、GB,粒度为36#-46#。
3.2安装砂轮时,不得使用两个尺寸不同或不平的法兰盘,并在法兰盘和砂轮之间垫入橡皮等弹性垫。
3.3装夹砂轮时,必须在修砂轮前后进行静平衡,并进行空运转。
3.4修砂轮时,应不间断的充分使用冷却液。
4 磨削加工4.1在磨削工件前,机床应空运转5min以上。
4.2在磨削过程中,不得中途停车,要停车时,必须先停止进给退出砂轮。
4.3 砂轮使用一段时间后,如发现工件产生棱形振痕,应拆下砂轮重新校平衡后使用。
4.4 在磨削细长轴时,严禁使用切入法磨削。
4.5 在平面磨床上磨削的工件,加工完应去磁。
4.6 磨深孔时,尽可能先用较粗的磨杆,以增加刚性,砂轮转整要适当降低。
4.7 在精磨结束前,应无进给量的多次走刀至无火花止。
5 一般精磨外圆的切削用量5.1 纵进给量根据所要求的表面粗糙度而定。
表面粗糙度Ra1.6 SB=(0.5-0.8)Bm 表面粗糙度Ra0.8-0.4 SB=(0.25-0.5)Bm SB—纵进给量(mm/r) Bm—磨轮宽度mm 5.2 横进给量铣削加工通用工艺范围本守则规定了铣削加工的工艺规则,适用于本公司的铣削加工。
2 铣刀的选择及装夹2.1 应根据铣削的宽度、深度、选择铣刀的直径,一般铣削的宽度和深度大而深,铣刀直径也应越大。
磨削加工技术
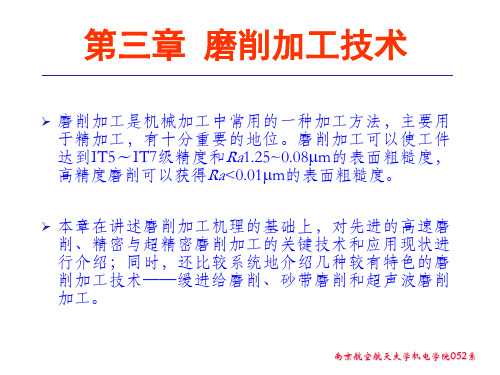
南京航空航天大学机电学院052系 南京航空航天大学机电学院052系
六、砂轮磨损和修整
1、砂轮磨损 、
(1)磨粒损耗 ) 1)磨粒的钝化 2)磨粒的破碎 3)磨粒的脱落 (2)砂轮失效 ) 1)砂轮工作表面变钝 2)砂轮工作表面堵塞 3)砂轮轮廓畸变
南京航空航天大学机电学院052系 南京航空航天大学机电学院052系
六、砂轮磨损和修整
2、砂轮耐用度及磨削比 、
砂轮耐用度T是砂轮相邻两次修整间的磨削时间,也 可以是磨削的工件个数。可以通过实验建立T和各因 素间的经验公式。
二、磨削过程
砂轮表面上磨粒可近似地看作是一把把微小的铣刀齿 ,其几何形状和角度有很大差异。致使切削情况相差 较大。因此必须研究单个磨粒的磨削过程。 1、单个磨粒磨削过程 、
(1)磨粒形状
β
rn
(a)磨粒外形 图3.1.12 磨粒的形状
(b)典型磨粒断面
南京航空航天大学机电学院052系 南京航空航天大学机电学院052系
二、磨削过程
图3.1.13 磨削的磨粒
南京航空航天大学机电学院052系 南京航空航天大学机电学院052系
二、磨削过程
(2)磨屑形成过程 单个磨粒的磨削过程大致分为滑擦、刻划和切削三个 阶段:
图3.1.14 磨粒的切削过程
南京航空航天大学机电学院052系 南京航空航天大学机电学院052系
二、磨削过程
南京航空航天大学机电学院052系 南京航空航天大学机电学院052系
切削用量三要素计算公式

切削用量三要素计算公式
摩擦削用量计算公式:
M=P*f*k
其中:
M:摩擦削用量,单位为N/cm
P:摩擦削的特定压力,单位为N/cm2
f:摩擦削速度,单位为m/min
k:摩擦削的摩擦系数,它取决于摩擦削时应用的机床和切削工具以
及切削介质。
摩擦削过程中,主要是由滚子对工件表面产生切削压力,从而达到加
工目的。
在实际的摩擦削加工过程中,P,f,k三个参数占据着重要的地位,它们共同决定了摩擦削的效果。
P(摩擦削的压力):摩擦削的压力对于摩擦削质量的影响是极其重
要的,过大的压力可能导致刃痕和侧锋过深,而低于最佳压力的压力,会
显著地增加摩擦削的时间,且可能出现齿轮齿合精度不佳的现象。
因此,
正确选择合适的压力是摩擦削进行中重要的一步。
f(摩擦削速度):摩擦削速度是另一个决定摩擦削效果的关键因素,摩擦削速度如果太低,会降低摩擦削的生产效率;摩擦削的速度如果太快,则会出现摩擦削压力不均匀的现象,甚至会使切削工具过热,汽化,甚至
熔化,极易损坏切削工具。
k(摩擦削的摩擦系数):摩擦削的摩擦系数取决于摩擦削时应用的机床和切削工具以及切削介质。
- 1、下载文档前请自行甄别文档内容的完整性,平台不提供额外的编辑、内容补充、找答案等附加服务。
- 2、"仅部分预览"的文档,不可在线预览部分如存在完整性等问题,可反馈申请退款(可完整预览的文档不适用该条件!)。
- 3、如文档侵犯您的权益,请联系客服反馈,我们会尽快为您处理(人工客服工作时间:9:00-18:30)。
二、工件圆周速度
工件圆周速度是表示工件被磨削表面上任意一点,在每分钟内所走 过的路程,用μw表示,计算式为
w
d w nw
1000
式中dw—工件外圆直径(mm); nw—工件转速(r/min); Vw—工件圆周速度(m/min)。 工件的圆周速度远低于砂轮的圆周速度,一般为5~30m/min。 在实际生产中,工件直径是已知的,加工时通常需要确定工件的转速,为此 可将上式变换为
LOGO
磨工工艺
襄阳技师学院 刘军
第三章 磨削用量
切削用量是用于表示切削时主运动、进给运动和切入参数的数值,以 便于调整机床,取得良好的切削效果 根据磨削的特点,不同的磨削方式有不同的磨削用量。以外圆磨削为 例,其磨削用量包括砂轮的圆周速度μ 0、工件的圆周速度μ w、纵向 进给量厂及横向进给量
fnw 1000
式中f—纵向进给量(mm) nw—工件转速(r/min); μf—工时,在每次行程结束后,砂轮在纵向进给方向上的移动量,叫做横向进给量, 用apo表示。他是衡量磨削深度大小的参数,又称背吃刀量。其尺寸从垂直于进给方向运动 测量。 计算公式为 式中D—进给前工件直径(mm); d—进给后工件直径(mm); ap—横向进给量(mm)。
磨床、工件等具体情况,在综合分析确定。
一、砂轮的圆周速度
砂轮外圆表面上任一磨粒在单位时间内所经过的磨削路程,称为砂轮的圆 周速度,用μ 0表示。此速度也即磨削主运动速度。μ 0的单位为m/s,按下式 计算:
0
Do no
1000 60
式中Do—砂轮直径(mm); no—砂轮转速(r/min) Vo—砂轮的圆周速度(m/s)。
w
1000w 318w dw dw
三 纵向进给量
工件每转一转,砂轮相对工件在纵向进给方向的移动量,叫做纵向进给量,
用f表示(见图3—7)。 计算式为; f=(0.2~0.8)B
式中B—砂轮宽度(mm)
f—纵向进给量(mm) 纵向进给量与工作台的纵向速度有关,
其计算式为
f
ap
Dd 2
外圆磨削时,横向进给量很小,一般取0.005~0.04mm,精磨时取小值,粗磨时取大值。 切削速度、进给量、背吃刀量通常称为“切削三要素”磨削时应合理选择。 磨削用量的选择原则是:粗磨时以提高生产效率为主,选大的背吃刀量和纵向进给量;精
磨时以保证精度和表面粗糙度要求为主,选择较小的背吃刀量和纵向进给量。同时还要考虑