板簧前吊耳强度计算分析报告
钢板弹簧行驶不能断裂(前板簧强度校核计算)

项目 输入参数 车轮静止力半径 前桥一级落差 后轮中心到弹簧座距离 前簧总片高
单位
cm cm cm cm
后簧总片高
cm
整车质心高度
M
前桥非簧载质量
n
后桥非簧载质量
n
前桥超载质量
n
后桥超载质量
n
前桥满载质量
n
后桥满载质量
n
后桥空载负荷
n
前轴空载负荷
n
轴距m
M
地面附着系数
弹性模量
N/mm2
前桥超载簧下载荷
结果
35.7 6 6.7 6.8
8
落差6.7斜垫板厚2.0 簧高11、斜垫板2.09
0.98 200 300
2355 4140 1597 2033 1005
1275
2.6 0.7
20580000.00
21119.00 37632.00 13970.00 38400.00 10535.00 6909.00
N
后桥超载簧下载荷
N
前桥满载簧下载荷
N
后桥满载簧下载荷
N
前桥空载簧下载荷
N
后桥空载簧下载荷
N
二、前板簧计算
1、前板簧计算输入参数
板簧规格表示
主片数
n1
副片数
n2
符号 Rc m1 m2 ∑h1 ∑h2 hg Gu1 Gu2 G1 G2 G1 G2
m2 m1 L ф
E
单面槽截面1300x75x9-6(2)g
T1+(P1d×La+T1×ha)×sinβ/((hb -ha)×sinβ+(La+Lb)cosβ)
吊耳满载时夹角(°)
β
吊耳强度计算书
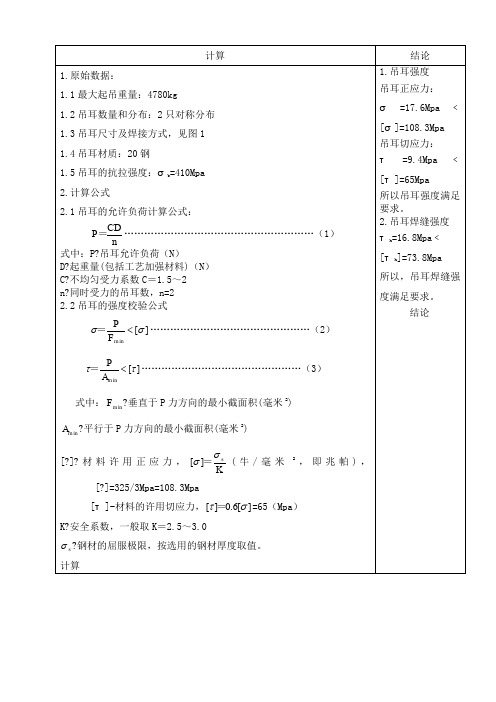
3.2吊耳强度校验
3.2.1正应力
将P=35169N,Fmin=80×25mm2=2000mm2,代入公式
…………………………………………(2)
得σ=17.6Mpa
σ=17.6Mpa﹤[σ]=108.3Mpa
3.2.2切应力
将P=35169N,Amin=150×25mm2=3750mm2,代入公式 …………………………………………(3)
计算
结论
1.原始数据:
1.1最大起吊重量:4780kg
1.2吊耳数量和分布:2只对称分布
1.3吊耳尺寸及焊接方式,见图1
1.4吊耳材质:20钢
1.5吊耳的抗拉强度:σb=410Mpa
2.计算公式
2.1吊耳的允许负荷计算公式:
…………………………………………………(1)
式中:P吊耳允许负荷(N)
D起重量(包括工艺加强材料)(N)
图1
图2
C不均匀受力系数C=1.5~2
n同时受力的吊耳数,n=2
2.2吊耳的强度校验公式
…………………………………………(2)
…………………………………………(3)
式中: 垂直于P力方向的最小截面积(毫米2)
平行于P力方向的最小截面积(毫米2)
[]材料许用正应力, (牛/毫米2,即兆帕),[]=325/3Mpa=108.3Mpa
计算
结论
得τ=9.4Mpa
τ=9.4Mpa﹤[τ]=65Mpa
所以,吊耳强度满足要求。
3.3吊耳的焊缝强度校核
如图1和图2所示,将D=46892N, ×8=5.7mm,∑l=(110×2+25)×2=490mm,代入公式 ,
计算得τh=16.8Mpa
钢板吊耳有关计算

附件二:钢板吊耳有关计算本工程吊耳材料采用Q235B钢,按《钢结构设计规范》GB50017-2003对应的钢材板厚强度设计值(N/mm2),取抗拉、抗压、抗弯值[σ]=205, 抗剪值[τ]=120 。
吊耳采用坡口熔透焊,角焊缝取抗拉、抗压、抗弯值[σ1]=160。
一、翻转吊耳:支承段吊耳按2只翻转吊耳计算。
钢煤斗支承段总重14.59吨,约等于143000N.A.吊耳的允许负荷吊耳的允许负荷按下式计算:P=CN/n= 1.2*143000/2=85800(N)式中: P −吊耳允许负荷N −荷载C −不均匀受力系数(一般取值在1.1~1.3之间)n −同时受力的吊耳数B.拉应力计算如图所示,拉应力的最不利位置在A-A断面,其强度计算公式为:σ=N*D/S1=71500*1.2/7500=11.44 ≤[σ]/K=205/2.8=73.2 合格式中:σ――拉应力N――荷载(14300N/2=71500N)D――动载系数(一般取值在1.1~1.3之间)S1――A-A断面处的截面积[σ]――钢材允许拉应力k――钢材允许拉应力系数(一般取2.5~3.0)C. 剪应力计算如图所示,剪应力的最不利位置在B-B断面,其强度计算公式为:τ= N*D/S2=71500*1.2/2700=31.78≤[τ]/K=120/2.5=48 合格式中:τ――剪应力N――荷载(14300N/2=71500N)D――动载系数(一般取值在1.1~1.3之间)S2――B-B断面处的截面积[τ]――钢材允许剪应力k――钢材允许拉剪应力系数(一般取2.5~3.0)D.局部挤压应力计算如图所示,局部挤压应力的最不利位置在吊耳与销轴的结合处,其强度计算公式为:σcj=N*D/(t×d)=71500*1.2/(30×35.1)=81.48≤[σcj]/2.5=205 /2.5=82 合格式中:σcj――局部挤压应力N――荷载(14300N/2=71500N)t――吊耳厚度D――动载系数(一般取值在1.1~1.3之间)d――销轴直径(13.5t卸扣,销轴直径35.1mm)[σcj]――钢材允许压应力k――钢材允许拉应力系数(一般取2.5~3.0)E.焊缝计算P=N*D/LW×h =71500*1.5/(800-42)×21 =6.74≤[σ1]/K=160/2.8=57.1式中:P――焊缝应力N――荷载D――动载系数(一般取值在1.3~1.5之间)LW――焊缝长度(一般取焊缝周长,减去2倍焊缝高度)h――焊缝高度(取30mm钢板的0.7倍)[σ1]――焊缝允许应力k――焊缝允许应力系数(一般取2.5~3.0)注:以上许用应力数据采自《钢结构设计规范》GB50017-2003.二:提升吊耳:顶盖、直筒段共重31.87t,约等于312326N。
吊耳强度计算书

n同时受力的吊耳数,n=2
吊耳的强度校验公式
…………………………………………(2)
…………………………………………(3)
式中: 垂直于P力方向的最小截面积(毫米2)
平行于P力方向的最小截面积(毫米2)
[]材料许用正应力, (牛/毫米2,即兆帕),[]=325/3Mpa=
[τ]-材料的许用切应力, =65(Mpa)
我们只按a)情况进行计算。公式如下:
………………………………………………(5)
式中:D-作用于吊耳上的垂直拉力(N);
a-焊缝宽度尺寸,如图2所示,
∑lห้องสมุดไป่ตู้焊缝总长度,mm
[τh]-焊缝许用切应力(N/mm2),[τh]=σb=
3.计算
吊耳的允许负荷计算
将D=4780×
……………………………………………………(1)
吊耳强度计算书
计算
结论
1.原始数据:
最大起吊重量:4780kg
吊耳数量和分布:2只对称分布
吊耳尺寸及焊接方式,见图1
吊耳材质:20钢
吊耳的抗拉强度:σb=410Mpa
2.计算公式
吊耳的允许负荷计算公式:
…………………………………………………(1)
式中:P吊耳允许负荷(N)
D起重量(包括工艺加强材料)(N)
K安全系数,一般取K=~
钢材的屈服极限,按选用的钢材厚度取值。
计算
1.吊耳强度
吊耳正应力:
σ=﹤[σ]=
吊耳切应力:
τ=﹤[τ]=65Mpa
所以吊耳强度满足要求。
2.吊耳焊缝强度
τh=﹤
[τh]=
所以,吊耳焊缝强度满足要求。
作业指导书吊耳强度计算

1 吊耳设计1.1水冷壁吊耳设计根据本期工程的水冷壁吊装样式,共设计两种水冷壁吊装吊耳形式:第一种吊耳为前墙、侧墙上段带辅射再热器的水冷壁管屏、折焰角组件的吊耳;第二种吊耳为侧墙上段中后组件、前后墙冷灰斗组件、侧墙下段中间组件等处的吊耳;第三种为其它组件重量在6吨以下的水冷壁组件、角部管屏及其它小型散件的吊耳。
下面分别进行设计计算。
第一种形式吊耳设计:通过统计此类吊装组件的重量,其中最重件为30222kg,依据吊装形式确定,此类组件共设六个吊点,其中上方两个吊点为水冷壁的上集箱,下部四个吊点焊接于水冷壁的鳍片上,每个吊点所受的最大拉力为10吨,下面按此值进行设计。
考虑吊装时的1.1倍动载系数,每个吊板的设计受力为:F=1.1×10000/2=5500kgf通过计算分析,此种形式吊装吊耳采用厚度为δ=8mm钢板,与水冷壁鳍片的焊缝高度为5mm,不但减少了与水冷壁的焊接工程量而且其强度满足安全吊装的需要。
B第二种形式吊耳设计:通过对此类组件重量的统计,其中最重件为29700kg,依据吊装形式确定,此类组件共设四个吊点,分别设置在组件的上部和下部,采用在水冷壁鳍片上切割开孔的方法设置吊耳,下面每个吊点所受的最大拉力为10吨进行设计。
考虑吊装时的1.1倍动载系数,每个吊板的设计受力为:F=1.1×10000/2=5500kgfA-A截面的强度校核:(同第一种)B-O截面的强度校核:(同第一种)焊缝的强度校核:(反面支撑筋板)τ=11000/(12×0.6×0.7×0.9×8)=303kgf/cm 2<[τ] 吊装用销轴强度校核:(同第一种)通过计算分析,此种形式吊装吊耳采用厚度为δ=8mm 钢板,与水冷壁鳍片的焊缝高度为5mm ,不但减少了与水冷壁的焊接工程量而且其强度满足安全吊装的需要。
B第三种形式吊耳设计:通过对较轻重量组件的统计,依据吊装形式确定,此类组件共设四个吊点,分别设置在组件的上部和下部,采用在水冷壁鳍片上切割开孔的方法设置吊耳,下面每个吊点所受的最大拉力为3吨进行设计。
2021年吊耳强度计算介绍模板

[τ]-材料的许用切应力, =65(Mpa)
K安全系数,一般取K=2.5~3.0
钢材的屈服极限,按选用的钢材厚度取值。
计算
1.吊耳强度
吊耳正应力:
σ=17.6Mpa﹤[σ]=108.3Mpa
吊耳切应力:
τ=9.4Mpa﹤[τ]=65Mpa
计算
结论
得τ=9.4Mpa
τ=9.4Mpa﹤[τ]=65Mpa
所以,吊耳强度满足要求。
3.3吊耳的焊缝强度校核
如图1和图2所示,将D=46892N, ×8=5.7mm,∑l=(110×2+25)×2=490mm,代入公式 ,
计算得 τh=16.8Mpa
τh=16.8Mpa﹤[τh]=73.8Mpa
所以,吊耳焊缝强度满足要求。
我们只按a)情况进行计算。公式如下:
………………………………………………(5)
式中:D-作用于吊耳上的垂直拉力(N);
a-焊缝宽度尺寸,如图2所示,
∑l-焊缝总长度,mm
[τh]-焊缝许用切应力(N/mm²),[τh]=0.18σb=73.8Mpa
3.计算
3.1吊耳的允许负荷计算
将D=4780×9.81N=46892N,C=1.5.N=2代入公式
式中: P吊耳允许负荷(N)
D起重量(包括工艺加强材料)(N)
C不均匀受力系数 C=1.5~2
n同时受力的吊耳数,n=2
2.2吊耳的强度校验公式
2.2.1正应力
…………………………………………(2)
2.2.2切应力
…………………………………………(3)
式中: 垂直于P力方向的最小截面积(毫米2)
前钢板弹簧吊耳加工工艺过程计算

前钢板弹簧吊耳加工工艺过程计算
前钢板弹簧吊耳的加工工艺过程计算如下:
1. 材料准备:根据设计要求,选择合适的钢材,并进行切割或切割成需要的尺寸和形状。
2. 缩径:将钢材端面缩径到设计要求的直径。
3. 卷制弹簧圈数计算:根据设计要求和钢材弹性模量等参数计算出所需卷制弹簧的圈数。
4. 张力计算:根据设计要求和弹簧圈数计算出所需的张力。
5. 弯曲加工:在卷制弹簧的同时,对吊耳部分进行弯曲加工,并通过计算确定所需的角度和圆心位置。
6. 尾部打扁:根据设计要求,在弹簧的末端打扁。
7. 清洗:对加工后的弹簧进行清洗和除油处理。
8. 表面处理:根据需要,对弹簧表面进行镀铬、喷涂等处理。
9. 检验:对加工好的弹簧吊耳进行检验,确保其符合设计要求和质量标准。
以上是前钢板弹簧吊耳加工工艺过程计算的一般步骤,具体加工过程可根据不同的设计要求和实际情况进行适当调整。
直立设备板式吊耳强度计算

第 )) 卷 第 # 期 !""# 年 ( 月 (!""#) 文章编号:%"""$(#’’ "#$""#&$"!
石 油 化 工 设 备 <=*T;$>U=P9>.? =+09<P=:*
! ! ( 校核条件为" 5 $6/ 。 4 $$( . "$ 4"!) #$ 4#!), " ! !
尾部吊耳结构及尺寸见图 0, 其承受载荷 "9 " !! " " # ! "$ 。 232 截面上的切应力为 #%$ " ! "9 ) ] , 校核条件为 #%: 5 $6! [ ’( 。 截面上 " % ( % # +) ! 737 ] , 校核条件为 "%: 5 的拉应力"%$ " "9 [ ) ’( % (% # +) 。尾 部 吊 耳 焊 缝 所 受 的 拉 应 力 ";$ " "9 ) $6/ " ! (! ,( % , 校核条件为";$ 5 $6/ $) "%。
图 . 垂直状态吊耳 应力校核图
#
结语 在直立设备的吊装过程中, 吊耳与壳体连接处
的局部应力可按 <=83$>9 方法计算。此外还要考 虑设备整体的抗弯强度及起吊时裙座基础环板的强 度, 要综合考虑各因素才能确保在吊装及使用过程 中吊耳和设备不被破坏。
参考文献:
设备吊耳 [C] [$] ?@ ) A !$/9. # B., 1 (张编)
- 1、下载文档前请自行甄别文档内容的完整性,平台不提供额外的编辑、内容补充、找答案等附加服务。
- 2、"仅部分预览"的文档,不可在线预览部分如存在完整性等问题,可反馈申请退款(可完整预览的文档不适用该条件!)。
- 3、如文档侵犯您的权益,请联系客服反馈,我们会尽快为您处理(人工客服工作时间:9:00-18:30)。
板簧前吊耳强度计算分析报
告
内容提要
分析目的:
根据蒙派克财富快车降成本项目,开发财富快车简化版底盘,为非独立悬架结构。
要验证钢板弹簧车身前后安装点结构设计的可靠性,降低设计风险。
使用软件:
CAD模型:CATIA。
前处理:HyperMesh。
求解器: Nastran。
后处理:HyperMesh。
分析方法:
利用HyperMesh建立相关部件的有限元模型,模拟连接并加载,利用Nastran 求解,利用HyperMesh将计算结果进行后处理。
分析结果:
在给定的两种极限工况下,前吊耳多个部位的等效应力值已超出材料的许用应力,个别位置如板簧前吊耳的支撑筋处出现较大应力集中,其等效应力值超过了材料的屈服极限值,值得关注。
结论:
为保证板簧前吊耳在较恶劣工况下的工作可靠性,建议改进其设计结构。
目录
目录.................................... I II
一、任务的提出 (1)
二、计算模型的建立 (1)
2.1有限元模型 (1)
2.2材料参数 (2)
2.3约束方式 (2)
三、承载计算工况与计算结果 (2)
3.1 计算工况 (2)
3.2 颠簸路面工况计算结果 (3)
3.3 制动工况计算结果 (5)
3.4 计算结果分析 (6)
四、结论及建议 (7)
一、任务的提出
根据蒙派克财富快车降成本项目,开发财富快车简化版底盘,将原有的独立悬架改为非独立悬架结构,为了验证板簧车身前后安装点结构设计的可靠性,预知易疲劳破坏部位,降低设计风险,对其进行强度分析计算。
二、计算模型的建立
2.1 有限元模型
有限元模型中悬架吊耳结构是由板金结构和销轴连接而成,对于钣金构件采用壳单元,销轴单元采用梁单元模拟。
用RBE2及实体单元单元来模拟钣金之间的点焊连接。
模型中长度单位为毫米,力单位为牛,重力加速度取9800mm/s2。
前吊耳的有限元模型如图2-1所示。
图2-1 前吊耳有限元模型
2.2 材料参数
零件材料为SPCE,性能参数如下:弹性模量 2.1×105MPa,泊松比0.3,密度7.8×10-6kg/mm3,屈服极限185MPa,抗拉强度325MPa,疲劳强度许用应力σ-1=抗拉强度×疲劳系数=325×0.43=139.75MPa,许用应力=疲劳强度许用应力/安全系数=139.75/1.3=107.5MPa。
2.3 约束方式
板簧前吊耳与车架点焊连接,在焊点部位对车架约束6个自由度,如图2-2所示。
图2-2 前吊耳有限元模型的约束方式
三、承载计算工况与计算结果
3.1 计算工况
为满足颠簸路面及紧急制动时吊耳的强度要求,根据设计部门提供的相关加载数据,分两种极限工况进行加载分析。
(1)颠簸路面工况Ⅰ根据客货车的动荷系数取值经验,取动荷系数为3.0。
垂直载荷=静载×动荷系数=4323.43×3.0=12970.3N
(2)紧急制动工况Ⅱ 考虑制动过程中产生的惯性力,所以除了在有限元模型上施加一个垂直载荷以外,还要施加一个水平向后的制动力,此制动力平衡制动加速度产生的惯性力,制动加速度a 取值为0.8g 。
垂直载荷=静载=4323.43N
制动力=簧载质量×制动加速度/6=(1325+1580-258)×0.8×9.8/6=3458.75N
3.2 颠簸路面工况计算结果
颠簸路面工况下,板簧前吊耳等效应力分布云图见图3-1、图3-2所示。
由图中可以看出,前吊耳多个部位(1~4位置)等效应力值超出了许用应力值,其中等效应力较大部位出现在左右支架的支撑筋部位,图中部位1最大等效应力达到189MPa ,已超过屈服极限,但小于抗拉极限。
部位2~4处等效应力分别为186 MPa 、131 MPa 、152 MPa ,均超出许用应力值。
板簧前吊耳的最大位移为0.09mm ,如图3-3所示。
图3-1 颠簸路面工况下前吊耳等效应力云图 1 3 2 4
189MPa
152MPa (a)两个筋位置的等效应力
186MPa
131MPa
(b)其它部位较大的等效应力
图3-2 颠簸路面工况下前吊耳局部较大等效应力云图
图3-3 颠簸路面工况下前吊耳变形云图
3.3 制动工况计算结果
在制动工况下,板簧前吊耳的等效应力分布云图见图3-4、图3-5所示。
由图中可以看出,前吊耳等效应力较大部位出现在左支架的支撑筋部位和右支架顶部拐角处,其中部位1等效应力值较大,达到115 MPa,超出了许用应力,但没有超过屈服极限,部位2等效应力值为85 MPa,接近许用应力。
吊耳的最大位移为0.048mm,如图3-6所示。
图3-4 制动工况下前吊耳等效应力云图1
2
图3-5 制动工况下前吊耳局部较大等效应力云图
图3-6 制动工况变形云图
3.4 计算结果分析
由应力云图可以看出,在颠簸路面工况和制动工况下板簧前吊耳的左右支撑筋部位和右侧吊耳支架顶端拐角等处存在较大应力集中,超出了许用应力值,个别部位最大值85MPa 69MPa
达到189MPa,超过屈服极限值,具体数值如表3-1所示。
颠簸路面工况最大变形为0.097mm,制动工况最大变形为0.04mm,可以接受。
表3-1 板簧前吊耳在颠簸路面工况及制动工况下等效应力值
四、结论及建议
在两种极限工况即颠簸路面工况及制动工况下,经过模拟计算分析,前吊耳支架上多处等效应力值超过了许用应力,个别部位等效应力值超过了屈服极限,但均未超过抗拉极限,其中左右支撑筋处为较薄弱环节,建议改进结构设计以降低其等效应力值,提高使用可靠性。
由于极限工况与实际使用的差别及有限元模拟的局限性,模拟结果与实际应力状况会存在一定差异,但是由应力云图所反映的应力较大部位的趋势建议适当关注。
以上结论是基于仿真计算得出的结果,建议安排试验对吊耳结构进行验证。