基于PROCAST的82B连铸二冷温度场分布及凝固传热的研究
小方坯齿轮钢连铸过程中的宏观偏析模拟

小方坯齿轮钢连铸过程中的宏观偏析模拟王亚栋1),张立峰2)✉,张海杰1)1) 北京科技大学冶金与生态工程学院,北京 100083 2) 燕山大学亚稳材料制备技术与科学国家重点实验室,秦皇岛 066004✉通信作者,E-mail :*******************.cn摘 要 基于国内某厂齿轮钢小方坯连铸生产过程,利用ProCAST 软件建立移动切片模型,能够高效模拟连铸过程中的宏观偏析,模型分别模拟研究了不同过热度、二冷水量和拉坯速度等对宏观偏析的影响. 模拟结果与碳偏析检测结果吻合良好,验证了移动切片模型模拟连铸坯宏观偏析的准确性. 由于溶质浮力的影响,内弧侧的宏观偏析强于外弧侧. 随着过热度的增加,铸坯中心碳偏析度从1.06增加至1.15. 过热度控制在25 ℃范围内,可以保证铸坯的宏观碳偏析度控制在1.10范围内.随着连铸二冷水量的增加,铸坯中心偏析改善程度较小,铸坯中心碳偏析度从1.16降低至1.13. 随着拉坯速度的增加,铸坯中心偏析呈现加重的趋势,铸坯中心碳偏析度由1.14增加至1.21,拉坯速度控制在1.4 m·min –1范围内,可保证铸坯中心碳偏析度低于1.15.关键词 宏观偏析;过热度;二冷水量;拉坯速度;齿轮钢分类号 TF777.3Simulation of the macrosegregation in the gear steel billet continuous casting processWANG Ya-dong 1),ZHANG Li-feng 2)✉,ZHANG Hai-jie 1)1) School of Metallurgical and Ecological Engineering, University of Science and Technology Beijing, Beijing 100083, China 2) State Key Lab of Metastable Materials Science and Technology, Yanshan University, Qinhuangdao 066004, China✉Corresponding author, E-mail: *******************.cnABSTRACT Macrosegregation forms due to relative motion between liquid and solid phases on the macro scale during solidification.As macrosegregation is formed during a solidification process, it is difficult to remove it in the subsequent rolling and heat treatment processes, thereby deteriorating the mechanical properties and stability of products. Studies of macrosegregation of billets for industrial trials have become a challenge due to the high temperature of the casting process. To improve macrosegregation of billet, a moving slice model was developed using the ProCAST software based on a continuous casting process of gear steel billet in a domestic steel mill.During the continuous casting process, macrosegregation can be calculated using the above model. The effects of superheat, secondary cooling water flows, and casting speed on macrosegregation were simulated. These results were consistent with the measured outcomes of carbon macrosegregation, validating the moving slice model to calculate the macrosegregation of billet. The solute concentration on the loose side is higher than that on the fixed side due to solute buoyancy. The degree of carbon segregation in the billet center increases from 1.06 to 1.15, with an increase in superheat, which should be controlled below 25 ℃ to ensure the degree of carbon segregation within 1.10. However, the degree of carbon segregation in the billet center decreases from 1.16 to 1.13, with an increase of secondary cooling water flow and a little improvement in central segregation. With an increase in casting speed, the central segregation becomes serious, and the degree of carbon segregation in the billet center increases from 1.14 to 1.21. However, when the casting speed is lower than 1.4 m·min −1, the degree of carbon segregation in the billet center comes lower than 1.15.KEY WORDS macrosegregation ;superheat ;secondary cooling water flow ;casting speed ;gear steel收稿日期: 2020−02−27基金项目: 国家自然科学基金资助项目(U186026,51725402)工程科学学报,第 43 卷,第 4 期:561−568,2021 年 4 月Chinese Journal of Engineering, Vol. 43, No. 4: 561−568, April 2021https:///10.13374/j.issn2095-9389.2020.02.27.001; 宏观偏析是由于凝固前沿高溶质浓度的钢液发生相对流动而形成[1]. 宏观偏析发生在1 cm~1 m 的大尺度范围,在后续的轧制和均匀化热处理过程中并不能完全消除[2],进而对产品的机械性能和稳定性产生重要影响,严重制约高端钢材的生产和应用[3].为了改善铸坯的宏观偏析,提升铸坯及钢材的质量,众多学者通过试验和数值模拟的方法进行了大量研究[4−7]. An等[8]通过工业试验研究发现随着结晶器电磁搅拌电流的增加,铸坯中心偏析得到改善;随着结晶器电磁搅拌频率的增加,铸坯中心偏析同样得到改善. Li等[9]通过对比结晶器电磁搅拌、结晶器+末端电磁搅拌(复合电磁搅拌)条件下低倍结果和铸坯中心碳偏析结果,表明复合电磁搅拌模式得到的铸坯中心疏松和缩孔更小、更均匀,能够有效改善铸坯中心碳偏析. Bleck 等[10]通过实验室试验研究了轻压下区间内不同中心固相率与中心偏析和内部裂纹的关系,结果显示在中心固相率为0.89~0.94的区间内进行压下试验,能够改善铸坯中心偏析,但是铸坯内部裂纹发生率增加. 王文培等[11]进行小方坯高碳钢的工业试验,结果表明随着钢液过热度的升高,碳偏析指数增大,控制钢水过热度在30 ℃以内可保证碳偏析指数在1.10内. Jiang等[12]建立了二维的多相凝固模型并与机械压下模型耦合,分别研究不同压下量、压下区间等对液相流动和溶质传输的影响. 研究结果显示,机械压下能够挤压铸坯芯部钢液,减缓溶质富集液相向凝固终点的流动速度,有效降低铸坯中心偏析. 随着压下量的增加,中心偏析明显改善;提出最佳的压下区间为中心液相率在0.95~0.01之间. Wu和Ludwig[13]利用多相凝固模型研究了钢锭凝固过程中的溶质传输行为,研究表明宏观偏析仅在熔体对流或者枝晶沉降过程中形成. Sun和Zhang[14]建立了电磁搅拌、传热和溶质传输的耦合模型并预测了连铸坯的宏观偏析,模拟结果与实验室检测结果吻合较好. 马长文[15]利用连续介质模型,研究了钢锭侧面和底面冷却条件下的偏析行为,侧面冷却时在铸锭顶部形成正偏析,底部形成负偏析;底部冷却时铸锭内部产生垂直生长的通道偏析. 陈华标[16]针对板坯连铸过程建立了全连铸三维中心偏析模型,并模拟研究了连铸凝固过程中板坯内溶质的分布特征及中心偏析的形成机理.由于连铸过程为高温作业,各种传输过程复杂,难以直接观察且试验过程耗费较多的人力和物力,越来越多的研究者采用数值模拟的方法研究连铸凝固过程. 然而,在连铸的数值模拟中,由于连铸模型庞大、计算量较大、计算时间较长,很难及时反馈模拟结果. 本文基于ProCAST软件建立简化的移动切片模型,能够高效模拟连铸过程中的宏观偏析,研究了不同过热度、二冷水量和拉坯速度等对宏观偏析的影响规律.1 数学模型本研究基于国内某钢厂小方坯齿轮钢连铸生产,利用ProCAST软件建立移动切片模型,模拟连铸坯的宏观偏析. 由于实际连铸过程较为复杂,为了简化模型以提高计算效率做出如下假设:连铸坯沿拉坯方向的导热量约占总热量的3%~6%,因此忽略连铸坯纵向传热[17];连铸二冷区同一段采用均匀冷却的经验公式[18];凝固过程未考虑枝晶沉降和固相移动[19];未考虑实际生产中电磁搅拌的影响. 模型中偏析的计算主要由连续性方程、动量方程、能量方程和溶质传输方程控制,方程(1)、(2)和(3)分别为连续性方程、动量方程和能量方程,方程(4)和(5)分别为液相和固相中的溶质传输方程.式中,f l (f s)为液(固)相率;ρl (ρs)为液(固)相密度,kg·m−3;t为时间,s;u l (u s)为液(固)相速度,m·s−1;μl为液相黏度,Pa·s;K为渗透率,m2;g为重力加速度,m·s−2;p为压力,Pa;h l (h s)为液(固)相焓,J·mol−1;D l (D s)为液(固)相扩散系数,m2·s−1;T为节点温度,℃;k m为热导率,W·m−1·K−1;c l (c s)为实· 562 ·工程科学学报,第 43 卷,第 4 期际的液(固)相浓度;c sl 为界面浓度;λ2为二次枝晶间距,m ;l ,S 为常数.小方坯齿轮钢断面尺寸为165 mm×165 mm ,拉坯速度为1.4 m·min −1,连铸机弧型段半径为10 m ,结晶器有效长度为0.85 m. 齿轮钢成分如表1所示,钢种的固液相线温度分别为1463 ℃和1514 ℃.图1为本研究建立的移动切片模型示意图. 通过ProE 建立切片模型,模型边长和厚度分别为165 mm 和10 mm ,采用6面体网格,体网格总数为15125个.移动切片从弯月面开始,按照图1所示连铸坯移动示意图进行运动,分别经历结晶器冷却、二冷区冷却和空冷区,最终完全凝固. 连铸各区长度和冷却水量如表2所示. 为了将重力对偏析的影响加入模型,本模型将连铸弧形段不同位置处的重力加速度分别沿径向和切向进行分解,进而加载至偏析模型[12, 20],如图1所示.表 1 齿轮钢成分(质量分数)Table 1 Element content of the gear steel%C Si Mn P S Al Cr Ti 0.2150.2400.8900.0200.0200.0201.0900.006MoldZone1Zone2Zone3Slice modelCasting directionHorizontal segementAir cooling zoneRθθgg Rg T图 1 移动切片模型Fig.1 Moving slice model表 2 各区长度和冷却水量Table 2 Length and cooling water flow in each zone Cooling zoneWater flow/(m 3·h −1)Length/m Mold 1080.9Zone1 3.320.35Zone2 2.20 1.78Zone31.031.85式中:θ为连铸坯弧形段不同位置处径向与水平方向的夹角;u c 为拉坯速度,m·min −1;t θ为弧形段开始至弧形段任意位置的时间,s ;R 为连铸机半径,m ;g R 为重力加速度径向分量,m·s −2;g T 为重力加速度切向分量,m·s −2.连铸生产过程中,铸坯表面与结晶器铜板接触,通过铜板内的冷却水将热量导出,在二冷区主要利用喷嘴向铸坯表面喷水(水雾)的方式冷却.在空冷区主要由铸坯表面向周围辐射散失热量.因此,需将上述传热边界条件分开处理. 结晶器铜板与铸坯表面的热流密度采用平均热流密度[21]:式中,q m 为铸坯表面的平均热流密度,W·m −2;ρ为结晶器冷却水密度,kg·m −3;C p 为冷却水的比热容,J·kg −1·℃−1;Q 为冷却水流量,m 3·s −1;ΔT 为结晶器铜板进出水温度差,℃;F 为结晶器铜板与铸坯的有效接触面积,m 2.二冷区冷却方式主要包括喷嘴冷却、辊子与铸坯间的接触传热、二冷水聚集蒸发散热和辐射散热等,本研究采用经验公式进行计算[22]:式中,h 为综合换热系数,W·m −2·℃−1;W 为二冷各区的平均水流密度,L·cm −2·min −1;T w 为冷却水的温度,℃.空冷区主要通过铸坯表面与周围环境的辐射换热散失热量,采用公式(12)进行计算[18, 23].式中,q rad 为铸坯表面辐射换热的热流密度,W·m −2;σ为Stefan-Boltzmann 常数,取值为5.67×10−8 W·m −2·K −4;ε为辐射换热系数,取值为0.8;T s 、T e 分别为铸坯表面温度和环境温度,℃. 模型中齿轮钢的热物性参数通过ProCAST 软件自带的热力学数据库计算得出,钢种的热导率、密度、热焓、黏度和固相率随温度的关系如图2所示.2 模型验证为了验证移动切片模型的准确性,本文基于连铸实际工况进行模拟并与检测结果进行对比.实际连铸条件如下:拉速1.4 m·min −1,过热度35 ℃,二冷水量为正常水量,如表2所示. 图3为铸坯表面红外测温与模型计算得到的温度场对比结果,可以看出计算得到的温度场与现场测温结果基本吻合,进而验证了模型温度场的准确性. 为了进一步验证宏观偏析模型的准确性,需要检测铸坯横王亚栋等: 小方坯齿轮钢连铸过程中的宏观偏析模拟· 563 ·断面的宏观偏析情况. 铸坯宏观偏析检测方法为:首先进行铸坯横断面低倍浸蚀,从浸蚀后的横断面找到铸坯的凝固末端位置,过凝固末端位置从内弧至外弧做垂线,并用直径为6 mm 的钻头沿着垂线进行钻屑取样,最后利用碳硫分析仪(Leco CS844)检测碳元素含量. 该检测方法的优势是能够准确定位凝固末端位置,进而得到更准确的中心偏析结果. 图4为碳偏析检测结果与模拟结果的对比,可以看出计算得到的碳偏析度与检测结果基本吻合,进而验证了模型计算宏观偏析的准确性. 碳偏析度通过公式(13)计算,其中,r i 为检测位置i 处的碳偏析度,m i 为检测位置i 处的碳含量,m 0为钢液中碳的初始含量.图 2 钢的热物性参数. (a )热导率;(b )密度;(c )热焓;(d )黏度;(e )固相率Fig.2 Thermophysical parameters of the steel: (a) conductivity; (b) density; (c) enthalpy; (d) viscosity; (e) solid fraction图 3 计算得到的铸坯表面温度和测量结果的对比Fig.3 Comparison between the calculated and measured results of the billet surface temperature· 564 ·工程科学学报,第 43 卷,第 4 期r i =m i m 0(13)检测结果显示,铸坯表层为负偏析,这是由于结晶器电磁搅拌导致钢液冲刷凝固前沿,将凝固前沿的富集溶质带至中间钢液,进而导致铸坯表层的负偏析. 随着连铸凝固的进行,碳含量逐渐增加,在距铸坯表面1/4处出现较严重的正偏析,如图4所示,该位置与连铸坯柱状晶向等轴晶的转变位置相吻合,此位置的正偏析主要是由于枝晶转变导致[24−25],枝晶转变处枝晶变得更加粗大且交错排布,阻碍了选分结晶产生的溶质进一步流动,进而在枝晶转变处产生正偏析. 随后碳含量逐渐降低,在凝固中心附近出现负偏析,在凝固中心处为严重的正偏析,碳偏析度可达1.16,这主要是因为在凝固末端,钢液凝固收缩形成的负压抽吸附近高浓度溶质钢液,导致严重的中心偏析和凝固中心附近的负偏析. 模拟结果显示,铸坯中心附近的负偏析偏离凝固中心较远,这是因为模型未考虑凝固收缩导致. 内弧侧的溶质浓度整体高于外弧侧,这主要是因为溶质浮力引起的热对流导致高溶质浓度钢液向内弧侧流动导致.3 模拟结果为了研究不同连铸参数对铸坯宏观偏析的影响规律,本研究分别模拟了不同过热度、二冷水量和拉坯速度条件下的宏观偏析. 钢中同时存在C 、Si 、Mn 、P 、S 、Cr 等易偏析元素,连铸凝固过程中易偏析元素均存在不同程度的偏析现象,易偏析元素的偏析规律基本一致[25−27],因此,为表征铸坯的宏观偏析程度,本文选用碳偏析度作为铸坯偏析程度的标准.拉速1.4 m·min −1,正常二冷水量条件下,本文分别模拟了过热度15、25和35 ℃工况铸坯横断面的宏观偏析情况. 图5为铸坯横断面碳元素的分布云图,图6为铸坯横断面中垂线上碳元素宏观偏析的定量结果. 可以看出,随着过热度的增加,枝晶转变处正偏析有所增加,铸坯中心偏析明显增强,铸坯中心碳偏析度从1.06增加至1.15. 中心偏析的增强主要是因为在相同冷却条件下提高浇铸温度,铸坯凝固时间延长,溶质元素有更长的时间扩散,使得更多的溶质元素扩散至后期凝固的钢液,进而加剧了铸坯的中心偏析. 可以看出,过热度在不超过25 ℃时,铸坯中心偏析和枝晶转变处偏析可以控制在一个比较低的水平. 因此,将过热度控制在25 ℃以内,可以保证铸坯的宏观碳偏析度控制在1.10范围内.模拟结果显示,铸坯内弧侧的偏析程度要强Simulated results Chilled layer Columnar zone Mixed zoneEquiaxed zoneMeasured results 900.70.8Degree of segregationFixed sideLoose side0.9 1.0 1.1 1.2165 m m图 4 检测得到的碳含量与模拟结果对比Fig.4 Comparison between the calculated and measured results of the carbon contentLoose side15 ℃25 ℃35 ℃Mass fraction of C/%0.26000.25270.24530.23800.23070.22330.21600.20870.20130.19400.18670.17930.17200.16470.15730.1500图 5 过热度对铸坯宏观偏析的影响Fig.5 Effect of superheat on the macrosegregation of the billet王亚栋等: 小方坯齿轮钢连铸过程中的宏观偏析模拟· 565 ·于铸坯的外弧侧. 这是由于连铸过程中,当铸坯切片运动至弧形段以及水平段后,重力方向将不再垂直于铸坯横断面,进而产生平行于铸坯横断面的重力分量,钢液受到溶质浮力的影响而产生对流,溶质元素富集的钢液会向内弧侧流动,进而导致内弧侧的宏观偏析强于外弧侧.为研究连铸二冷水量对铸坯横断面宏观偏析的影响,在拉速为1.4 m·min −1,过热度为35 ℃的条件下,本模拟分别计算了二冷水量降低20%、正常水量、二冷水量增加20%三种工况下铸坯的宏观偏析. 图7为铸坯横断面碳元素的分布云图,图8为铸坯横断面中垂线上碳元素宏观偏析的定量结果. 可以看出,连铸二冷水量对铸坯中心偏析和枝晶转变处偏析影响较小,且影响规律不明显.随着连铸二冷水量的增加,铸坯中心偏析有所改善,但是改善程度很小,铸坯中心碳偏析度从1.16降低至1.13. 这主要是因为在凝固中后期,凝固坯壳较厚,二冷水量的改变对铸坯芯部的冷却条件影响较小,即对凝固后期钢液的凝固时间影响较小,溶质扩散时间改变有限,进而对铸坯中心偏析影响较小.Loose sideDecrease 20%Increase 20%NormalMass fraction of C/%0.26000.25270.24530.23800.23070.22330.21600.20870.20130.19400.18670.17930.17200.16470.15730.1500图 7 二冷水量对铸坯宏观偏析的影响Fig.7 Effect of secondary cooling water flow on macrosegregation of the billet图 8 二冷水量对铸坯宏观偏析的定量影响Fig.8 Effect of secondary cooling water flow on the quantized results of macrosegregation为研究拉坯速度对铸坯横断面宏观偏析的影响,在过热度为35 ℃,正常二冷水量条件下,本模型分别计算了1.2、1.4和1.6 m·min −1三种拉速条件下的宏观偏析. 图9为铸坯横断面碳元素的分布云图,图10为铸坯横断面中垂线上碳元素宏观偏析的定量结果. 可以看出,拉速的变化对铸坯中心偏析的影响较为显著,随着拉坯速度的增加,铸坯中心偏析呈现加重的趋势,铸坯中心碳偏析度由1.14增加至1.21. 主要是因为随着拉坯速度的提高,连铸坯在结晶器区和二冷区停留时间变短,使得凝固末端向后移动,图11显示拉坯速度在1.2、1.4和1.6 m·min −1时,凝固末端位置距离弯月面分别为9.6、11.7和13.9 m. 进而溶质元素有更长的扩散时间,使得更多的溶质元素扩散到后期凝固的钢液中,加剧了铸坯的中心偏析.4 结论本文建立了连铸移动切片模型,能够高效模拟连铸过程中的宏观偏析并及时反馈模拟结果.图 6 过热度对铸坯宏观偏析的定量影响Fig.6 Effect of superheat on the quantized results of the macro-segregation· 566 ·工程科学学报,第 43 卷,第 4 期红外测温和碳偏析检测结果与模拟结果吻合良好,验证了移动切片模型模拟连铸坯宏观偏析的准确性. 模型分别模拟研究了不同过热度、二冷水量和拉坯速度对铸坯宏观偏析的影响,得出如下结论:(1)由于钢液受到溶质浮力的影响,溶质元素富集的钢液会向内弧侧流动,导致内弧侧的宏观偏析强于外弧侧.(2)随着过热度的增加,枝晶转变处正偏析有所增加,铸坯中心偏析明显增强,铸坯中心碳偏析度从1.06增加至1.15. 过热度控制在25 ℃范围内,可以保证铸坯的宏观碳偏析度控制在1.10范围内.(3)随着连铸二冷水量的增加,铸坯中心偏析改善程度较小,铸坯中心碳偏析度从1.16降低至1.13.(4)随着拉坯速度的增加,铸坯中心偏析呈现加重的趋势,铸坯中心碳偏析度由1.14增加至1.21. 拉速控制在1.4 m·min −1范围内,可保证铸坯中心碳偏析度低于1.15.参 考 文 献Ludwig A, Wu M H, Kharicha A. On macrosegregation. Metall Mater Trans A , 2015, 46(11): 4854[1]Ahmadein M, Wu M H, Ludwig A. Analysis of macrosegregationformation and columnar-to-equiaxed transition during solidifica-tion of Al-4wt. %Cu ingot using a 5-phase model. J Cryst Growth ,2015, 417: 65[2]Lesoult G. Macrosegregation in steel strands and ingots: cha-racterisation, formation and consequences. Mater Sci Eng A , 2005,413-414: 19[3]Flemings M C. Our understanding of macrosegregation: past and present. ISIJ Int , 2000, 40(9): 833[4]Oh K S, Chang Y W. Macrosegregation behavior in continuouslycast high carbon steel blooms and billets at the final stage of solidification in combination stirring. ISIJ Int , 1995, 35(7): 866[5]Vušanović I, Vertnik R, Šarler B. A simple slice model forprediction of macrosegregation in continuously cast billets // The 3rd International Conference on Advances in Solidification Processes . Aachen, 2011: 012056[6]Wu M H, Kharicha A, Ludwig A. Discussion on modelingcapability for macrosegregation. High Temp Mater Processes ,2017, 36(5): 531[7]An H H, Bao Y P, Wang M, et al. Effects of electromagneticstirring on fluid flow and temperature distribution in billet[8]Loose side1.2 m·min −1 1.6 m·min −11.4 m·min −1Mass fraction of C/%0.26000.25270.24530.23800.23070.22330.21600.20870.20130.19400.18670.17930.17200.16470.15730.1500图 9 拉坯速度对铸坯宏观偏析的影响Fig.9 Effect of casting speed on macrosegregation of the billet图 10 拉坯速度对铸坯宏观偏析的定量影响Fig.10 Effect of casting speed on the quantized results of macrosegregation图 11 拉坯速度对凝固坯壳厚度的影响Fig.11 Effect of casting speed on the shell thickness of the billet王亚栋等: 小方坯齿轮钢连铸过程中的宏观偏析模拟· 567 ·continuous casting mould and solidification structure of 55SiCr.Metall Res Technol , 2018, 115(1): 103Li J C, Wang B F, Ma Y L, et al. Effect of complex elec-tromagnetic stirring on inner quality of high carbon steel bloom.Mater Sci Eng A , 2006, 425(1-2): 201[9]Bleck W, Wang W J, Bulte R. Influence of soft reduction oninternal quality of high carbon steel billets. Steel Res Int , 2006,77(7): 485[10]Wang W P, Liu L X, Li H, et al. High carbon stranded steelSWRH82B central carbon segregation control practice. Special Steel , 2019, 40(5): 24(王文培, 刘列喜, 李海, 等. 高碳绞线钢SWRH82B 中心碳偏析控制实践. 特殊钢, 2019, 40(5):24)[11]Jiang D B, Wang W L, Luo S, et al. Numerical simulation of slabcenterline segregation with mechanical reduction during continuous casting process. Int J Heat Mass Transfer , 2018, 122:315[12]Wu M H, Ludwig A. A three-phase model for mixed columnar-equiaxed solidification. Metall Mater Trans A , 2006, 37(5): 1613[13]Sun H B, Zhang J Q. Study on the macrosegregation behavior forthe bloom continuous casting: model development and validation.Metall Mater Trans B , 2014, 45(3): 1133[14]Ma C W. Numerical Simulation on Centerline Segregation inContinuous Casting Process [Dissertation]. Beijing: Tsinghua University, 2004( 马长文. 连铸过程中心偏析的数值模拟研究[学位论文]. 北京:清华大学, 2004)[15]Chen H B. Investigations on Solute Redistribution during theSolidification of Iron-based Multicomponent Alloys and Centerline Segregation in Continuous Casting Slab [Dissertation]. Chongqing:Chongqing University, 2018( 陈华标. 铁基多元合金凝固溶质再分配与连铸板坯中心偏析研究[学位论文]. 重庆: 重庆大学, 2018)[16]Yang X G. Control of Transverse Corner Cracks on Low CarbonMicro-alloyed Continuous Casting Slabs [Dissertation]. Beijing:University of Science and Technology Beijing, 2016[17]( 杨小刚. 低碳微合金钢铸坯角部横裂纹控制研究[学位论文].北京: 北京科技大学, 2016)Cabrera-Marrero J M, Carreno-Galindo V, Morales R D, et al.Macro-micro modeling of the dendritic microstructure of steel billets processed by continuous casting. ISIJ Int , 1998, 38(8): 812[18]Zhang H J. Numerical Simulation and Optimization on theMacrosegregation and Solidificatin Structure of Oil Casting Steel [Dissertation]. Beijing: University of Science and Technology Beijing, 2016( 张海杰. 石油套管钢连铸坯宏观偏析和低倍组织的模拟与优化[学位论文]. 北京: 北京科技大学, 2016)[19]Dong Q P. Numerical Study on the Porosity and Macrosegregationin Continuously Cast Billet [Dissertation]. Beijing: University of Science and Technology Beijing, 2018( 董其鹏. 方坯连铸疏松及宏观偏析的模拟研究[学位论文]. 北京: 北京科技大学, 2018)[20]Wang X L. Study on Heat Transfer Behavior of High SpeedContinuous Casting of Steel Slabs [Dissertation]. Beijing:University of Science and Technology Beijing, 2014( 王晓连. 高拉速板坯连铸传热行为研究[学位论文]. 北京: 北京科技大学, 2014)[21]Morales R D, Lopez A G, Olivares I M. Heat transfer analysisduring water spray cooling of steel rods. ISIJ Int , 1990, 30(1): 48[22]Wang Q Q, Zhang L F. Influence of FC-mold on the fullsolidification of continuous casting slab. JOM , 2016, 68(8): 2170[23]Wang Y, Zhang L F, Zhang H J, et al. Mechanism and control ofsulfide inclusion accumulation in CET zone of 37Mn5 round billet.Metall Mater Trans B , 2017, 48(2): 1004[24]Choudhary S K, Ghosh A. Morphology and macrosegregation incontinuously cast steel billets. ISIJ Int , 1994, 34(4): 338[25]Chen H B, Long M J, Chen D F, et al. Numerical study on thecharacteristics of solute distribution and the formation of centerline segregation in continuous casting (CC) slab. Int J Heat Mass Transfer , 2018, 126: 843[26]Maidorn C, Blind D. Solidification and segregation in heavyforging ingots. Nucl Eng Des , 1985, 84(2): 285[27]· 568 ·工程科学学报,第 43 卷,第 4 期。
铸造学07讲铸件凝固温度场ppt课件

Tw f (t)
Tqx,y,z,t
n
T = n
TwTf
温度场计算的解析法
➢ 解析方法是直接应用现有的数学理论和定律去推导和演绎 数学方程(或模型),得到用函数形式表示的解,也就是 解析解。
➢ 优点:是物理概念及逻辑推理清楚,解的函数表达式能够清楚地表
达温度场的各种影响因素,有利于直观分析各参数变化对温度高低的 影响。
所以得(铸件侧温度分布):
同理可得铸型侧温度场方程式为:
对于公式中的界面温度Ti,可以通过在界面处热流的
连续性条件求出,
• 即:上式中, b1 = λ1 c1 ρ1 ,为铸件的蓄热系 数; b 2 = λ2 c 2 ρ2 ,为铸型的蓄热系数。最后
可得铸件、铸型内温度分布的解析解为:
半无限大平板铸件凝固过程的 一维不稳定温度场(温度分布)
并令:
R V1 A1
➢ 可得一般铸件凝固时间的近似计算公式:
R
K
➢ R为铸件的折算厚度,称为“模数”。“模数法”
也称为“折算厚度法则”。
➢ 从传热学角度来说,模数代表着铸件热容量与散热表 面积之间的比值关系,凝固时间随模数增大而延长。 ——对于形状复杂的铸件,其体积与表面积的计算都 是比较麻烦的,这时可将复杂铸件的各部分看作是形 状简单的平板、圆柱体、球、长方体等单元体的组合, 分别计算出各单元体的模数,但各单元体的结合面不 计入散热面积中。一般情况下: 模数最大的单元体的凝固时间即为铸件的凝固时间。
1)解析法(理论法):
➢ 因铸型温度分布为:T 2b 1 T 1 b 10 b b 2 2 T 20 b 1 T b 110 b b 1 2 T 20 er 2 fx a2t
➢ 所以其温度梯度有:
二冷控制模型

2021/7/17
·收敛条件
(1)对于绝热边界节点AC边、C点、CB边和内部节点
t C(x)2
4(Khx)
(2)对于对流边界节点OA边、A点、B点、BO边
t C(x)2
4K
(3)对于角部节点O点
t C(x)2
2(2Khx)
在ΔX、ΔY一定时,Δt要从这三个数值中取最小值,才 能满足上述差分方程的收敛和稳定性条件。
选取差分网格大小必须考虑使其同时满足解法精度和 计算时间两者的要求。
50
计 算 时 间 ( s)
40
30
20
10
0
2
4
6
8
10
空 间 步 长 × 1 0 3( m m )
图3-7 计算时间与空间步长的关系(收敛标准取1.0℃)
(铸坯断面为260mm×180mm,计算长度为16.36m)
在工程上要求计算时间小于等于5秒,空间步长必须大 于等于4.1×10-3mm才能满足此要求;从利用软件进行计算
[K(T2,np+T1,n-1p-2T1,np)+h(Ta-T1,np)Δx] [K(2T2,jp+T1,j+1p+T1,j-1p-4T1,jp)+2h(Ta-T1,jp)Δx]
Ti,jp+1=Ti,jp+
t
C(x)2
[K(Ti+1,jp+Ti-1,jp+Ti,j+1p+ Ti,j-1p -4Ti,jp)]
方坯连铸二冷配水模型的研究
炼钢研究所
2021/7/17
第一章 文献综述 第二章 大方坯连铸二冷配水模型研究 第三章 大方坯连铸二冷配水软件设计 第四章 凝固传热模型计算结果与讨论 第五章 方坯连铸二冷配水模型及软件的应用 第六章 结论
Procast
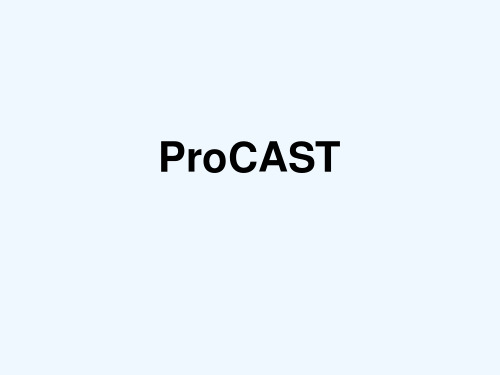
如果几何体没问题
删除细节以提高网格质量
几何体 • ProCAST • Iges • Step • Parasolid • Stl
如果有未划分网格的面
• 检查几何体 • 修复几何体 • 调整几何体 • 保存 prefix.gmrst 文件 • 划分面网格 • 检查网格 • 修复网格 • 保存 prefix.sm 文件 • 划分体网格 • 检查网格质量 • 修复网格质量 • 平滑处理 • 优化处理 • 保存 prefix.mesh 文件
辐射分析模块
本模块大大加强了基本模块中关于辐射计算的功 能。专门用于精确处理单晶铸造、熔模铸造过程 热辐射的计算。特别适用于高温合金例如铁基或 镍基合金。此模块被广泛用于涡轮叶片的生产模 拟。该模块采用最新的“灰体净辐射法”计算热辐 射自动计算视角因子、考虑阴影效应等,并提供 了能够考虑单晶铸造移动边界问题的功能。此模 块还可以用来处理连续性铸造的热辐射,工件在 热处理炉中的加热以及焊接等方面的问题。
SolStar SOLIDA 华铸CAE
英国 日本 中国
FVM DFDM FDM
—— —— 软件不限制
各种铸造 多数铸造 各种铸造
ProCAST分析模块
• • • • • • • • 有限元网格划分 MeshCAST 传热分析及前后处理 Base License 流动分析 Fluid flow 应力分析 Stress 热辐射分析 Rediation 显微组织分析 Micromodel 电磁感应分析 Electromagnetics 反向求解 Inverse
重力定义
1. 单击Process/Gravity, 弹出重力定义窗口 2.用左键单击X、 Y、Z来选择重力 大小和方向
3.单击Apply
82B线材连续冷却转变曲线测定及组织规律研究

内 蒙 古 科 技 大 学 学 报
J u n lo n rMo g h n v ri fS in e a d T c n lg o r a fI e n o a U ie st o ce c n e h oo y n y
De e e , c mb r 201 1
1 试 验 材 料 及 试 验 方 法
1 1 试 验 材 料 .
试 验钢选 用包 钢 天诚 线材 有 限公 司生产 的轧 态 8 B线材 , 主要化 学成 分 见表 1 2 其 .除表 1中所 列 成
分 外 , 中还添加 了微量 合金 元素 . 钢
表 1 试验钢的化学成分 ( 质量分数 , ) %
i h rtc lc ol ae t o re ic st e c iia o i r t o fr ma tnst . ng m
热 轧 8 B高碳 钢 盘 条 是 生产 高 强 度 、 松 弛 预 2 低 应力 钢 丝或 钢绞 线 的重 要 原 料 , 而这 些 产 品 主要 用
组织 为 珠 光 体 和 少 量 渗 碳 体 ; 冷 却 速 度 为 1~ 当 3 /时 , s 组织 为珠 光体 和少 量 索 氏体 ; 当冷 却速 度 为 6— 8℃/ 时 , 织全部 为索 氏体 , 且 索 氏体 逐 s 组 并 渐 细化 ; 当冷却 速度 为 1 0~l 5℃/ 时 , 织 为索 氏 s 组 体和少 量 马 氏 体 ; 速继 续增 大 , 氏体 量 随 之 增 冷 马 加, 并且 有少 量残 余 奥 氏体 . 在温度 一 间对数 坐标 中 , 相 同性 质 的相变 开 时 将 始 点 和结束 点分别 连 成 连续 冷却 转 变 曲线 —— C T C
i ae ng r ts
ProCAST软件在铸造凝固模拟中的应用
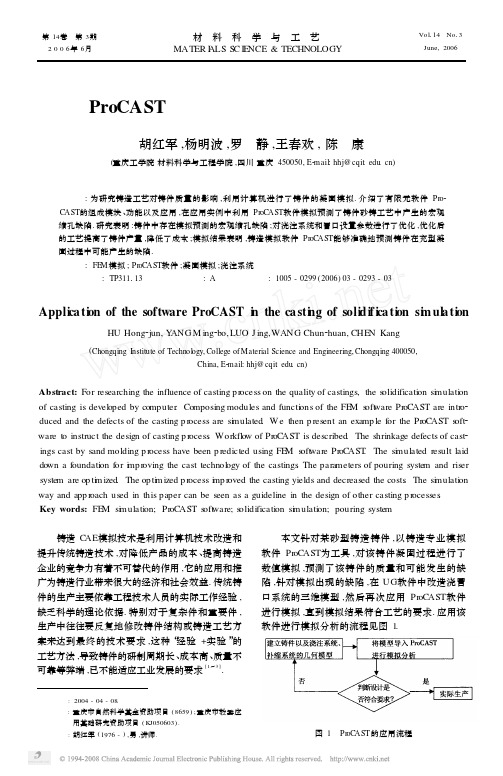
图 5 初始模型的宏观孔隙预测
图 6 修改后的 3D 模型
4 结 论
用有限元软件 ProCAST预测铸件中存在的 宏观缩孔 ,直观地显示出充型凝固的温度场分布 、 温度梯度 、金属液流动行为 、热节部位 、缩松缩孔 等. 针对模拟的结果 ,修改铸件工艺设计的 3D 模 型 ,修改了原始的浇冒口设计. 实验表明应用修改 后的铸造工艺进行铸造 ,提高了铸件的质量 ,提高 了工艺出品率 ,降低了成本.
在砂铸中 ,有时冲砂是不可避免的. 如果冲砂 发生在铸件的关键部位 ,将影响铸件的质量. Pro2 CA ST可以通过对速度场和压力场的分析确认冲 砂的产生. 通过虚拟粒子跟踪则能很容易确认最 终夹砂的区域. 215 冷隔及浇不足
在浇注成型过程中 ,一些不当的工艺参数如型 腔过冷 、浇速过慢 、金属液温度过低等会导致一些缺 陷的产生. 通过传热和流动的耦合计算 ,设计者可以 准确计算充型过程中的液体温度下降. 在充型过程 中凝固了的金属将会改变充型的流动形式. ProCAST 可预测这些铸造充型过程中发生的现象 ,并可以随 后快速地检验相应的改进设计方案. 216 压铸模寿命
摘 要 : 为研究铸造工艺对铸件质量的影响 ,利用计算机进行了铸件的凝固模拟. 介绍了有限元软件 Pro2 CAST的组成模块 、功能以及应用 ,在应用实例中利用 ProCAST软件模拟预测了铸件砂铸工艺中产生的宏观 缩孔缺陷. 研究表明 :铸件中存在模拟预测的宏观缩孔缺陷 ;对浇注系统和冒口设置参数进行了优化 ,优化后 的工艺提高了铸件产量 ,降低了成本 ;模拟结果表明 ,铸造模拟软件 ProCAST能够准确地预测铸件在充型凝 固过程中可能产生的缺陷. 关键词 : FEM 模拟 ; ProCAST软件 ;凝固模拟 ;浇注系统 中图分类号 : TP311113 文献标识码 : A 文章编号 : 1005 - 0299 (2006) 03 - 0293 - 03
ProCAST 连铸介绍

6
稳态模型
热分析 热分析 + 流动分析 弯曲型 案例研究
Copyright © ESI Group, 2011. All rights reserved.
Steady state calculations - Thermal only
Copyright © ESI Group, 2011. All rights reserved.
an X-Ray plot).
Copyright © ESI Group, 2011. All rights reserved. 12
Case Study: Steel VCC 模具应力
模具温度云图分布
模具的正应力
模具与铸件缝隙
Copyright © ESI Group, 2011. All rights reserved.
1.E+06 1.E+05 1.E+04 1.E+03 1.E+02 1.E+01 1.E+00 1.E-01
Z
0
0.01
0.02
0.03
0.04
y (m)
0.05
0.06
0.07
0.08
Copyright © ESI Group, 2011. All rights reserved.
15
铸铁的连铸
Christof Sommitsch, Project Leader, Böhler Edelstahl GmbH & Co KG, Austria
Hot tears
Microsegregation - Phase appearances
Nucleation
Copyright © ESI Group, 2011. All rights reserved.
连铸二冷区技术原理

148CHINA INSTRUMENTATION2010年 增刊由于铸坯凝固速度比拉坯速度慢很多,随着浇注的进行,铸坯内形成一个很长的液相穴。
铸坯带着液芯进入二冷区接受喷水冷却,目的是使铸坯完全凝固,表面温度分布均匀,内外温度梯度小,然后进入拉矫机。
铸坯在二冷区要全部凝固还需散出 210~294kJ/kg 的热量。
所以,从结晶器出口到拉矫机前的一定范围内设置一个喷水冷却区,叫二冷区,向铸坯表面喷射雾化水滴,铸坯表面温度突然降低,铸坯表面和中心之间形成了较大的温度梯度,这是铸坯向外传热的动力。
二冷水的控制特点是要求流量控制范围大,控制精度高,因此常采用高精度的电磁流量计对水流量进行检测。
凌钢1700ASP 连铸铸坯生产过程中,边角温度下降快,二冷区采取气—水雾化冷却系统控制,借以避免局部水楔和开浇、停浇时残流所造成的冷却不均匀。
2 系统概况凌钢1700ASP 连铸二冷水系统采取气—水雾化冷却控制,即在8个冷却区中,第1区(即结晶器喷水区)喷水冷却,防止拉漏和鼓肚,2~8区采取气—水雾化冷却。
气—水冷却系统分区如图1所示。
以上各冷却区均设置流量调节阀,一级计算机根据钢坯横截面、拉速、钢种等修正参数、设定冷却水、二冷空气流量的设定值,同时控制各区的流量调节阀的开度,实现对气水配比控制。
二次冷却水流量与拉速满足以下关系:Qi A v B v C xax i i i 2=++b ^h 式中:Qi 为某一控制回路的流量设定值;连铸二冷区技术原理The Theory of Second Cooling Zone1 引言众所周知,在连铸生产工艺流程中,从结晶器拉出来的铸坯凝固成一个薄的外壳,而中心仍为高温钢水。
(1)中国仪器仪表 CHINA INSTRUMENTATION2010年 增刊149v 为拉坯速度;α为过冷补偿系数;β为喷水宽度调整补偿系数(仅第三段控制回路有此项)。
3 气水冷却配比控制在汽水冷却段,为了达到气水喷雾冷却的预期效果,必须保证冷却水与压缩空气的正确配比。
- 1、下载文档前请自行甄别文档内容的完整性,平台不提供额外的编辑、内容补充、找答案等附加服务。
- 2、"仅部分预览"的文档,不可在线预览部分如存在完整性等问题,可反馈申请退款(可完整预览的文档不适用该条件!)。
- 3、如文档侵犯您的权益,请联系客服反馈,我们会尽快为您处理(人工客服工作时间:9:00-18:30)。
基于PROCAST的82B连铸二冷温度场分布及凝固传热的研究 马光林①1,李京社2,刘纲2,龚荣波1,杨宏博2,毕秀荣2 (1.首钢水城钢铁集团有限公司炼钢厂,贵州 六盘水 553028;2.北京科技大学冶金与生态工程学院 北京 100083) 摘 要:以水钢炼钢厂2号连铸机二冷优化改造为研究对象,利用Procast数值模拟软件建立凝固传热模型,结合射钉实验,共同研究小方坯连铸机典型钢种拉坯工艺(拉速、过热度)对铸坯温度场分布的影响。通过对连铸机二冷制度的优化调整,探明二冷制度优化对提升铸坯凝固组织的作用,为首钢水钢连铸机二冷制度的优化改造提供了可靠的理论支撑和改造方案,从而提高铸坯质量,降低钢坯质量缺陷。 关 键 词:Procast;模拟;温度场分布;凝固传热;拉坯工艺;质量缺陷 1 前言 在品种钢的开发过程中,铸坯中心偏析、疏松和缩孔等级偏高,特别是高碳钢,碳的选择性结晶造成中心偏析严重,对钢坯质量的稳定性影响较大,这直接制约着各钢厂品种钢开发的步伐[1]。 为此,首钢水钢以提高铸坯质量为攻关点,以连铸机二冷制度的优化改造为攻关切入点,通过二冷制度的优化控制,攻克典型钢种质量缺陷对其产品开发的影响。本文以首钢水城钢铁(集团)有限责任公司炼钢厂二连铸2#铸机二冷为研究对象,利用Procast数值模拟研究铸坯的温度场分布,建立满足水钢炼钢厂现有工艺、装备条件下的二冷数学模型,优化二冷凝固传热过程,提高铸坯质量,降低缺陷的发生。 2 Procast数值模拟研究 2.1 初始条件设定 初始条件包括:(1)结晶器液面温度。考虑到结晶器内部温度无法测量,以及水钢现场采用了中间包保护浇铸的措施,所以可以认为结晶器液面温度约等于中间包温度。(2)型腔初始温度。(3)重力方向为竖直向下。 2.2 边界条件设定 由于整个二冷过程不仅有动量传输同时也有热量传输,所以边界条件分为速度边界条件和传热边界条件。 1)速度边界条件 速度以现场拉速为准,由于Procast默认的单位是国际标准单位,所以需要将现场的拉速单位转换为国际标准单位。 2)传热边界条件 由于本模型包括结晶器段、足辊段、二冷一段、二冷二段、二冷三段和空冷段。所以传热边界条件比较复杂,应当分阶段分别确定。 (1)结晶器段传热 结晶器坯壳生长速度取决于结晶器的传热速率,而结晶器传热速率取决于结晶器内钢水热量传给冷却水间的换热系数,也可以说取决于结晶器内钢水与冷却水间的总热阻。结晶器的传热可以用下式来描述[2,3]。 q=h(TMS-TCW)=1/RT(TMS-TCW) 式中 q—结晶器壁的热流量,W/m2; h—总换热系数,W/(m2·K); TMS—结晶器内钢水温度,℃; TCW—结晶器冷却水温度,℃; RT—总热阻,m2·K/W。 结晶器壁的总热阻可以用各部分热阻之和来表示,公式如下: RT=R1+R2+R3+R4+R5+R6 式中 R1—结晶器壁冷却水间的热阻,m2·K/W; R2—通过结晶器铜铸坯的热阻,m2·K/W; R3—通过气隙的热阻,m2·K/W; R4—通过保护渣膜的热阻,m2·K/W; R5—通过坯壳的热阻,m2·K/W; R6—钢水-坯壳间的热阻,m2·K/W。 由于准确确定结晶器每个热阻的数值相当困难,所以考虑采用热流密度表示结晶器的传热能力。结晶器是用冷却水进行强制冷却的,若忽略从结晶器液面向保护渣所传的热量,冷却水所带走的热量应等于钢水的导出热量。因此,可将单位面积单位时间内由结晶器导出的热量称为结晶器的平均热流量,它与拉速,所浇筑的钢种,保护渣及冷却水量,流速,温差等参数有关,其计算公式为: q=qm·C·Δt/F 式中 q—结晶器平均热流量,W/m2; qm—冷却水流量,kg/s; C—冷却水比热容,J/(kg·K); Δt—冷却水进出温差,℃; F—结晶器有效面积,m2。 其中,冷却水流量qm由现场使用的水流量换算得到;结晶器的有效面积可通过结晶器的几何尺寸计算得到,通过计算可以得到水钢现场的结晶器有效面积为0.608m2。具体数据见表1。
(2)二冷段传热 在二冷区,铸坯表面接受喷水或气雾冷却,坯壳中存在着较大的温度梯度,热量源源不断地从铸坯内部传递到表面,然后被冷却水带走(大约210~294kJ/kg的热量被水带走),铸坯才能全部凝固。根据热平衡估算,二冷区铸坯表面的主要传热方式如图1所示[4,5]。 铸坯被带走的热量比例为:冷却水蒸发带走的热量33%;冷却水加热带走的热量25%;铸坯表面辐射热为25%;铸坯与支撑辊接触传导传热为17%。在铸机设备和工艺条件一定的情况下,铸坯辐射散热变化不大,支撑辊的接触导热变化也不大,占主导地位的是冷却水与铸坯表面的热交换(对流换热)。 由于无法精确确定同一时刻内冷却水蒸发量和未蒸发量,所以二冷段的换热系数的计算常采用经验公式进行计算。本文采用M.Ishiguro等提出的经验公式[6]: h=0.581W0.451(1-0.0075Tw) 式中 Tw—冷却水温度。 由此公式可以计算出二冷区各个分段的换热系数。 3 82B温度场及凝固传热的模型 基于82B钢的物理特性,对现场工艺条件下的82B钢连铸过程进行了数值模拟。现场工艺参数如表2。
根据表2中的工艺参数,设定合理的初始条件和边界条件,通过模拟计算得到如图2所示结果。
从图2至图4的数值模拟结果可以得到整个铸坯凝固过程各阶段的温度场和凝固状态分布。通过分析拉矫前铸坯的温度场和凝固率分布结果,可得出该工艺条件下,铸坯拉矫前处温度在固相线以上的范围为:宽80mm,高88mm;固相率在90%以下的范围为:宽11mm, 高27mm。(凝固率大于90%的铸坯组织已经很致密,在拉矫过程中不易发生变化,也不易产生应力裂纹或者收缩裂纹)连铸过程关键位置铸坯横截面的温度场和固相率展示了铸坯经过结晶器、足管段、二冷一段、二冷二段、二冷三段、拉矫段以及火焰切割段的温度分布和固相率分布情况,通过对各个阶段温度场和固相率分布情况可以指导生产,调节相应的配水强度以达到所需的结果。
4 结果分析与讨论 4.1 拉速对二冷区内温度场分布的影响 随着拉坯速度的提高,铸坯表面温度提高,铸坯液芯长度增加,表面温度梯度减少,二冷强度也应做相应的调整,保证凝固过程的稳定。拉速的增大液芯长度不变长,并且液芯长度和拉速近似成线性关系,关系式为: y=9.567v-5.172 式中 v—拉速,m/min; y—液芯长度,m。 钢坯在凝固阶段,由于钢坯内部潜热的释放,钢坯中心温度降幅很小,从而在铸坯内部形成较长的液相穴,根据射钉试验的分析,随着拉速的提高,铸坯坯壳厚度减小,液芯变长,铸坯热应力与拉应力增加,在二力的共同作用下加速导致铸坯中间裂纹形成[7-10]。 4.2 钢液过热度对二冷区温度场分布的影响 随着钢液过热度的提高,铸坯表面温度也升高,铸坯坯壳厚度减薄,液芯长度增长。随着钢液过热度的降低,铸坯表面温度也降低,温度场分布更均匀,铸坯坯壳厚度增加,液芯长度减少,钢坯夹杂物含量也降低,钢材洁净度明显提高。浇注温度的升高液芯长度不断变长,并且液芯长度和浇注温度近似成线性关系。液芯长度和浇注温度的关系式为: y=0.0404t-44.1408 式中 t—浇注温度,℃; y—液芯长度,m。 5 结论 1)铸坯液芯长度和拉速近似成线性关系,关系式为: y=9.567v-5.172 式中 v—拉速,m/min; y—液芯长度,m。 依据该公式可以得出,在配水量不变的情况下,拉速每增大0.1m/min,液芯长度增加0.9567m; 2)液芯长度和浇注温度的关系式为: y=0.0404t-44.1408 式中 t—浇注温度,℃; y—液芯长度,m。 浇注温度每提高1℃,液芯长度延长0.0404m。 参 考 文 献: [1] Lerner V.S,Lerner Y.S.Solidification Modeling of Continuous Casting Process[J].Journal of Materials Engineering and Performance,2005,Vol.14:258-262. [2] Shi Shengli,Huang Zhiqiang,Wang Haisheng.Research on process and equipment for cast iron small bar with double-current horizontal continuous casting[J].Zhuzao Jishu/Foundry Technology,2005,Vol.26:14-17. [3] KivelaE,KonttinenJ,Rautaruukki O.Dynamic secondary Cooling Model for continuous casting [A].Steelmaking Conference Proceedings [C].America 1995,341. [4] 蔡开科,程士富.连续铸钢原理与工艺[M].北京:冶金工业出版社,1994. [5] Cui Kai,Xu Qingyan,Yu Jing.Radiative heat transfer calculation for super alloy turbine blade in directional so lidification process[J].Jinshu Xuebao/Acta Metallurgica Sinica,2007,Vol.43:465-471. [6] Seshadri V,Da Silva C.A,Silva I.A etal.A tundish to mold model for grade change during ladle change-over in continuous casting[J].Iron and Steel Making,2006,vol.2:499-510. [7] Griffiths,William David,Kayikci Ramazan.The effect of varying chill surface roughness on interfacial heat transfer during casting solidification [J].Journal of Materials Science,2007,Vol.42:4036-4043. [8] 粟伟,朱国森,王万军,王新华.连铸坯液相穴长度的测定研究.北京科技大学学报,2003(4):315 -318. [9] T A Blasé,Z X Guoa.A 3D Conjugate Heat Transfer Model for Continuous Wire Casting [J].Materials Science and Engineering,2004(A365):318-324. [10] You Bong Sun,Yim Chang Dong,KimSu Hyeon.Solidification of AZ31 magnesium alloy plate in a horizontal continuous casting process[J].Materials Science and Engineering A,2005,Vol.413:139-143.