圆坯连铸凝固传热数学模型及应用
连铸坯凝固过程中的传热计算研究

x erf 2 a L
x TM Ti TM 0 Ti erf 2 a M
上式分别反映了凝固过程不同时刻铸件及铸型中的温度分布。
8
(2)实验法
通过在铸型中安放热电偶直接测出合金凝固过程的温度变化情况。 可以看出铸件中不同位置上: 开始凝固时间、凝固结束时间、 凝固进行时间、在凝固过程中不同时刻 两相区的宽度。 可用模型实验并借助于相似原理 推广到实际铸件。 相似: 几何相似kl、物理相似kλkα、时间相似kτ 边界条件相似ks 按傅里叶导热微分方程可得相似条件:
1. 传热条件与凝固方式 2. 凝固过程传热的方式与特点 3.凝固过程传热的研究方法 4. 温度场与凝固过程的分析
2
1. 传热条件与凝固方式 (1)定向凝固过程
通过维持热流一维传导使凝固界面逆热流方向推进, 完成凝固,称为:定向凝固。 从界面附近的热流平衡可获得凝固速率的控制方程,忽热平衡: q2 - q1 = q3 由傅里叶导热定律: q h R
第四章 凝固过程中的传热、传质与液 体流动
一、凝固过程中的传热 二、凝固过程中的传质 三、凝固过程中的液体流动
1
一、凝固过程中的传热
在凝固过程中,伴随着潜热的释放、液相与固相降温放出物理热,定向凝 固时,还需外加热源使凝固过程以特定的方式进行,各种热流被及时导 出,凝固才能维持。 宏观上讲,凝固方式和进程主要是由热流控制的。
R2>R1及R2<R1的情况:
旧稳定状态→过渡区(高度、距离、时间长短)→新的稳定状 态(陡峭情况、面积)
19
凝固初期非稳态与末端过渡区的溶质分布: 凝固初期非稳态的溶质分布:
Pohl于1954年以菲克第二定律一维公式为基础对凝固过程初期非稳 态过程的溶质分布进行了求解。 假设(1)液相无对流只有扩散;(2)k0为常数;(3)忽略界面扰动; (4)忽略固相扩散;(5)试样横截面尺寸恒定;(6)无元素气化。 k R R R K值很小时: 1 k x 1 k x 1 k
方坯连铸凝固传热数学模型及其软件

图 2-2 网格划分示意图
由泰勒级数展开式知:
T in1 =T in (x i +Δx)= T in +Δx/1!(
T n ) i +(Δx) 2 /2!( x T n T in1 =T in (x i -Δx)= T in -Δx/1!( ) i +(Δx) 2 /2!( x
T n ) i +… (2-2) x x T n ) i -… (2-3) x x
选用如下两个经验公式[60]:
Tl=1539-(90%C+6.2%Si+1.7%Mn+28%P+40%S+2.6%Cu+2.9%Ni+1.8%Cr+5.1%Al) Ts=1536-(415.3%C+12.3%Si+6.8%Mn+124.5%P+183.9%S+1.4%Cr+4.1%Al) (2-16) (2-17)
2.3 凝固传热模块计算结果分析
在凝固传热模块部分,依据钢液在凝固过程的传热行为建立数学模型,通
过模型计算出铸坯表面温度曲线、 坯壳厚度曲线、 各个关键点的铸坯表面温度以 及坯壳厚度和液芯长度。
2.2 凝固过程数学模型计算程序
在所建立的方坯连铸凝固传热数学模型中,考虑了钢的热物性参数随温度 变化关系,并考虑了铸机的设备条件。这样,就做到了数学模型所用的边界条件 尽可能地与实际的连铸凝固过程的条件相符合,使模型更加精确和符合实际。 计算程序图 2-3 见图。连铸凝固传热模型总体结构如图 2-4 所示。
2.1.4 物性参数的确定
(1)钢的液相温度(Tl) 、固相温度(Ts) : 钢的液、固相温度取决于化学成分,与 C、Si、Mn、P、S、Cu、Cr、Al 等 元素含量有关。
连铸坯凝固与传热

连铸坯凝固与传热连铸过程中铸坯的凝固和传热是连铸设备设计工艺、工艺控制和质量控制的基础,是连铸工作必须掌握的知识。
第1节连铸坯凝固传热的特点钢液在连铸过程中的凝固是一个热量释放和传递的过程,有两个特点。
*在运动(动态)过程中凝固放热*在不同时期散热和传热的方式是不同的一、连铸坯的凝固过程实质上是一个传热的过程。
钢液在转变成固态过程中是分为几个过程。
热量Q包括:1.过热:从浇注温度T C冷却到液相线温度T L放出的热量,C1(T C-T L);2.潜热:从液相线温度T L冷却至固相线温度T S放出的热量以L f表示;3.显热:从固相线温度T S冷却到环境温度To放出的热量C S(Y S-T O);大约有1/3的热量是从液态→固态放出的, 而其余热量是完全凝固后冷却放出的。
连铸过程中钢液凝固可分三个传热冷却区。
*一次冷却区:形成足够厚度的坯壳以保证铸坯出结晶器不漏钢。
*二次冷却区:使铸坯完全凝固。
*三次冷却区:空冷区。
从热平衡来看*钢水结晶器→二冷区→空冷区大约有60%的热量放出来,铸坯才能完全凝固。
这部分热量放出的速度决定了铸机的生产率和铸坯的质量。
*铸坯切割后还有40%热量要放出来,为了利用这部分热量,节约能源,采用热装直轧或连浇连轧工艺。
二钢热凝固过程是液体转变固体的加工过程凝固是发生在铸坯传热过程中的主要现象,铸坯在运动过程中凝固,实质是固——液交界面潜热的释放和传递过程。
1.凝固温度区间(T L-T S)将液体转变成固体加工过程。
这时在固——液交界面有个脆性区,其强度σ=0;收缩率ψ=0。
极易在此区产生裂纹,因此称裂纹敏感区。
固——液界面糊状区。
晶体强度和塑性都非低或称临界强度,如这时受到外力作用。
如热应力,鼓肚应力,矫直力等超上述临界值(ó为1-3N/mm2,由应变到断裂的临界应变为0.2-0.4%)产生裂纹和偏析裂纹。
2.在二冷区受喷水冷却时在这个区已凝固坯壳不断进行线收缩和坯壳温度分布不均匀性及坯壳鼓胀和夹辊不完全对中等原因,是坯壳受到机械和热应力的作用(有时是反复的)也易使铸坯产生裂纹。
第三章 连铸坯的凝固与传热
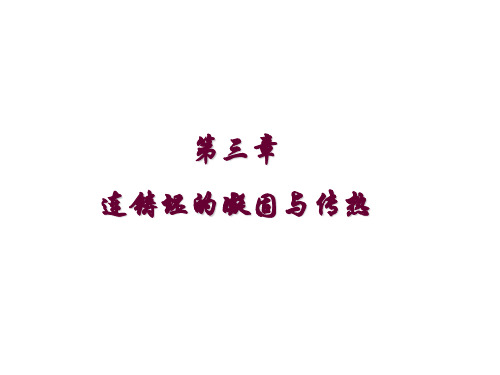
2、坯壳及气隙的形成
注入结晶器的钢液除受结晶器壁的强制冷却外,还通过钢 液面辐射传热及拉坯方向的传导传热,使钢液形成一定厚度的 坯壳。其传出热量的比值大约为30:0.15:0.03。因此,结晶器 内钢水可近似地看作向结晶器壁的单向传热,其散热量的波动
与坯壳表面和结晶器壁的接触状况有关。
钢水热量传出途径:钢水→坯壳→气隙→结晶器铜壁→铜 板与冷却水界面→冷却水。
取24~26 mm/min1/2 ; 板坯取17~22 mm/min1/2 ; 圆坯
取20~25 mm/min1/2 。 小方坯出结晶器下口坯壳厚度8~10 mm,板坯、大方坯大于 15mm。
5、影响结晶器凝固传热的因素
研究指出:气隙热阻占总热阻的 70~90% ,因此改善结 晶器传热最重要的是减小气隙热阻。气隙的形成与演变决定 于凝固壳的收缩、坯壳高温强度、结晶器润滑和结晶器几何 形状等因素。
喷水冷 却 凝固壳
辐射冷 却
铸坯热送热装和连铸连轧等工艺。
连铸机冷却区示意图
2、连铸坯的凝固是沿液相穴在凝固温度区间 将液体转变为固体的加工过程
连铸坯可看成是液相穴很长的钢锭(板坯可达30m),以一定速度
在铸机内运动并凝固,也可看成是在凝固温度区间(TL → TS)把液体转
变为固体的加工过程。 在固—液交界面附近,存在一个凝固脆化区,此处强度、塑性接
从结晶器内凝固传热考虑,应避免高温钢水浇注。
6、确保坯壳出结晶器下口有足够厚度及均匀生 长的措施
① 浇注温度不能过高,保持低温浇注; ② 水口与结晶器严格对中; ③ 结晶器冷却水的水质、流速、水量达到要求,均匀冷却; ④ 合理的结晶器锥度;
⑤ 结晶器液面保持稳定;
⑥ 选择性能良好的结晶器保护渣,以形成均匀的保护渣膜等; ⑦ 合适的浇注速度。
铸件凝固传热数学模型与铸铁在金属型铸模浇注后温度分布

铸件凝固传热数学模型与铸铁在金属型铸模浇注后温度分布作者:姜帅琦来源:《中国科技纵横》2014年第04期【摘要】为方便了解和比较金属凝固传热后的一些温度数据和各项特性指标,建立铸件凝固传热的数学模型。
并绘制铸铁在金属型铸模浇注后的参数和温度分布。
【关键词】铸件数学模型金属型温度分布1 铸件凝固传热数学模型液态金属浇入铸型后在型腔内的冷却凝固过程,是一个通过铸型向周围环境散热的过程。
在这个过程中,铸件和铸型的内部温度分布是随时间而变化的。
由于影响铸件凝固过程的因素众多,在求解中把所有因素都考虑进去不太现实。
因此对铸件凝固过程必须进行合理简化,一般作如下基本假设:(1)认为液态金属在瞬时充满铸型后开始凝固——假定初始液态金属温度为定值,或为已知各点的温度值。
(2)不考虑液、固的流动——传热过程只考虑导热。
(3)不考虑合金的过冷——假定凝固是从液相线温度开始,固相线温度结束。
根据以上假设则可得到铸件凝固传热数学模型。
其一维系统如下:在铸件中不稳定导热的控制方程表达式为2 铸铁在金属型铸模浇注后温度分布2.1 金属型的选择及其热物性参数本文仅以铸铁金属模具为例加以说明,为减少金属模的表面温差,金属模材料的选择有以下措施:(1)选择蓄热系数大的金属材料。
(2)选择导热系数大的金属材料。
(3)选择膨胀系数小的材料等。
由表1可知不同材质的热性能。
所以一般选用灰铁材质的金属模。
为了方便计算本文中金属模的热物性参数见表2。
2.2 金属型的预热未预热的金属型不能进行浇注。
这是因为金属型导热性好,液体金属冷却决,流动性剧烈降低,容易使铸件出现冷隔、浇不足夹杂、气孔等缺陷。
未预热的金属型在浇注时,铸型,将受到强烈的热击,应力倍增,使其极易破坏。
因此,金属型在开始工作前,应该先预热,适宜的预热温度(即工作温度),随合金的种类、铸件结构和大小而定,一般通过试验确定。
金属型的预热方法有:(1)用喷灯或煤气火焰预热;(2)采用电阻加热器;(3)采用烘箱加热,其优点是温度均匀,但只适用于小件的金属型;(4)先将金属型放在炉上烘烤,然后浇注液体金属将金属型烫热。
连铸热过程数学模型的建立

连铸热过程数学模型的建立2.1连铸热过程数学模型的建立连铸热过程为连铸坯的凝固冷却过程。
连铸坯在凝固过程中,凝固传热量不仅影响铸机生产效率和设备寿命,而且对铸坯的表面质量和内部质量都有重要影响。
因此薄板坯凝固传热规律的研究,对该工艺的生产和设计,都具有十分重要的意义。
板坯凝固冷却过程可分为三个阶段:(1)结晶器冷却。
钢液在近结晶器壁处快速冷却,形成薄的坯壳;(2)二冷区冷却。
坯壳具有足够厚度时,铸坯从结晶器中拉出,在二冷区受到强烈的喷水冷却,液芯逐渐凝固;(3)空冷区冷却。
铸坯在空气中较缓慢地冷却,铸坯断面上温度逐渐趋于均匀。
根据板坯的凝固冷却过程,连铸热过程数学模型包括结晶器、二冷区和空冷区这三部分。
结晶器中热传递主要沿水平方向进行。
传热过程包括:(1)钢水以对流和导热形式将热量传给坯壳;(2)凝固坯壳的导热;(3)凝固坯壳与结晶器壁的传热;(4)结晶器壁的导热;(5)喷淋水与结晶器壁的强制对流传热。
其中在传热过程(3)中,填充于铸坯壳与结晶器壁气隙中的渣膜控制铸坯壳向结晶器的传热量,在结晶器的传热过程中显得尤为重要。
因此,应进一步分析气隙中渣膜特性对传热的影响,建立坯壳与结晶器气隙的传热模型。
为全面分析结晶器的传热,将该模型于铸坯凝固和结晶器壁的传热祸合起来,建立统一的结晶器传热数学模型。
带有液芯的铸坯进入二冷区达到完全凝固。
在二冷区铸坯向外传热方式主要有:(1)由喷射水滴蒸发带走的热量;(2)铸坯表面与周围环境的辐射换热;(3)铸坯与支撑辊、导辊的接触换热。
喷淋水和支撑辊、导辊与铸坯的传热对铸坯内液芯长度的控制十分重要。
铸坯进入拉矫机后进入空冷区,铸坯主要以辐射换热方式和自然对流的方式进行冷却。
2.1.1 基本假设为建立连铸过程温度场数学模型,需对物理模型进行简化,作如下假设:(1)连铸生产线工况稳定;(2)由于铸坯的贝克来数很高(~ 105),忽略整个铸坯沿拉坯方向传热; (3)钢液面上保护渣具有保温作用,忽略钢液表面的散热量;(4)沿结晶器和薄板坯宽度方向传热具有对称性,只计算1/2截面的温度场; (5)注入结晶器的钢液温度恒定;(6)结晶器壁与坯壳间的气隙层厚度不随位置和时间变化; (7)不考虑结晶器内凝固壳表面的振痕对传热的影响。
连铸过程中板坯凝固的数值模拟

连铸过程中板坯凝固的数值模拟
QS C PVT
(5-10) 由式(5-9)与式(5-10)等量置换可得
f S C P T / L
(5-11) 此法采用固相率的增加来代替前热的放出,如果 f S 1 ,则表明该领域 V 的 凝固结束。
热焓法
凝固过程金属的焓可定义为
H cdT (1 f s ) L
L ——潜热, J / kg ;
f s ——固相率;
T ——温度, C ;
——时间, s ;
连铸过程中板坯凝固的数值模拟
——导热系数, W /(m K ) ;
x, y ——二维坐标, m 。
对于实用多元和金,要确定固相率和温度的关系,通常可以先采用热分析法 求出凝固开始温度 TL (液相线温度)和结束温度 TS (固相线温度),假定如下: (1)假定为线性分布时
式中, L ——补偿对流换热的等效导热系数;
m ——经验常数,钢液导入区, m 4 ~ 8 ;
S ——静止钢液的导热系数。
热物性参数的数值处理方法
由于导热系数、比热和密度是随温度变化的,其处理方法一般有常数法、线 形函数法和插值法等,在不同的温度区间内用二次曲线拟合的方法得到温度导热系数、温度-比热之间关系的曲线,来确定导热系数、比热值。 对于板坯密度的取值,可在不同相区内取不同的值。 (1) 固相区: S 7.6 10 3 kg / m 3 ;
薄板坯连铸凝固过程数值模拟
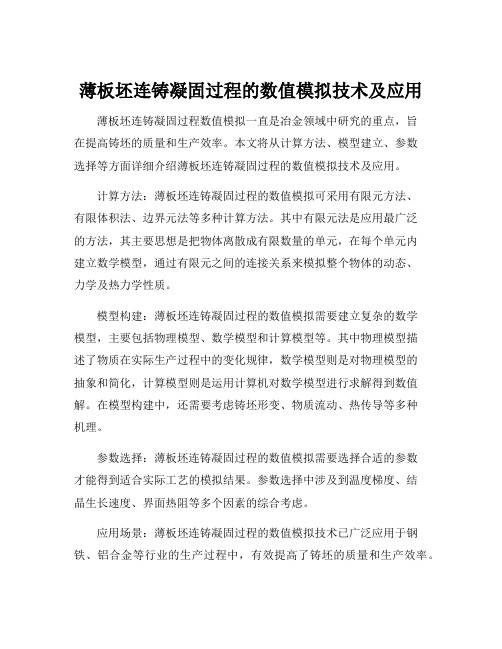
薄板坯连铸凝固过程的数值模拟技术及应用薄板坯连铸凝固过程数值模拟一直是冶金领域中研究的重点,旨
在提高铸坯的质量和生产效率。
本文将从计算方法、模型建立、参数
选择等方面详细介绍薄板坯连铸凝固过程的数值模拟技术及应用。
计算方法:薄板坯连铸凝固过程的数值模拟可采用有限元方法、
有限体积法、边界元法等多种计算方法。
其中有限元法是应用最广泛
的方法,其主要思想是把物体离散成有限数量的单元,在每个单元内
建立数学模型,通过有限元之间的连接关系来模拟整个物体的动态、
力学及热力学性质。
模型构建:薄板坯连铸凝固过程的数值模拟需要建立复杂的数学
模型,主要包括物理模型、数学模型和计算模型等。
其中物理模型描
述了物质在实际生产过程中的变化规律,数学模型则是对物理模型的
抽象和简化,计算模型则是运用计算机对数学模型进行求解得到数值解。
在模型构建中,还需要考虑铸坯形变、物质流动、热传导等多种
机理。
参数选择:薄板坯连铸凝固过程的数值模拟需要选择合适的参数
才能得到适合实际工艺的模拟结果。
参数选择中涉及到温度梯度、结
晶生长速度、界面热阻等多个因素的综合考虑。
应用场景:薄板坯连铸凝固过程的数值模拟技术已广泛应用于钢铁、铝合金等行业的生产过程中,有效提高了铸坯的质量和生产效率。
同时,数值模拟技术也成为创新的生产手段,为钢铁、铝合金等行业的技术升级和发展带来积极的推动作用。
- 1、下载文档前请自行甄别文档内容的完整性,平台不提供额外的编辑、内容补充、找答案等附加服务。
- 2、"仅部分预览"的文档,不可在线预览部分如存在完整性等问题,可反馈申请退款(可完整预览的文档不适用该条件!)。
- 3、如文档侵犯您的权益,请联系客服反馈,我们会尽快为您处理(人工客服工作时间:9:00-18:30)。
圆坯连铸凝固传热数学模型及应用
作者:唐海燕, 李京社, 韩丽敏, 温德松, Tang Haiyan, Li Jingshe, Han Limin, Wen Desong
作者单位:唐海燕,李京社,韩丽敏,Tang Haiyan,Li Jingshe,Han Limin(北京科技大学冶金与生态工程学院,北京,100083), 温德松,Wen Desong(北京科技大学冶金与生态工程学院,北京
100083;天津钢管集团有限公司炼钢厂,天津300301)
刊名:
特殊钢
英文刊名:SPECIAL STEEL
年,卷(期):2009,30(4)
1.曹晓兵;梁爱生连铸机二冷区传热系数的研究 1999(04)
2.李永林大断面连铸圆坯的凝固过程及矫直变形研究 2005
3.蔡开科连续铸钢 1990
4.蔡开科;程士富连续铸钢原理与工艺 1995
1.郑忠.胡燕.罗小刚.占贤辉.ZHENG Zhong.HU Yan.LUO Xiao-gang.ZHAN Xian-hui基于交替方向隐式差分算法的连铸坯凝固传热模型[期刊论文]-过程工程学报2008,8(z1)
2.车芳.程常桂.赵威.帅静.余乐.万文成.CHE Fang.CHENG Chang-gui.ZHAO Wei.SHUAI Jing.YU Le.WAN Wen-cheng物性参数对连铸结晶器传热模型计算结果的影响[期刊论文]-过程工程学报2010,10(z1)
3.匡世波.李环.王学斌.邹宗树自漩流中间包可行性初探[会议论文]-2003
4.孙开明.付继成.李京社.温德松.Sun Kaiming.Fu Jicheng.Li Jingshe.Wen Desong圆坯连铸凝固传热数学模型及应用[期刊论文]-钢管2009,38(3)
5.王赟.钟云波.王保军.任忠鸣.雷作胜.任维丽连铸离心中间包内钢液流动行为的数值模拟[会议论文]-2008
6.冯科.韩志伟.曹建峰.孔意文.FENG Ke.HAN Zhi-wei.CAO Jian-feng.KONG Yi-wen薄板坯连铸传热过程与应力状态仿真软件的开发[期刊论文]-工业加热2010,39(5)
7.王俊杰.杨吉春.卢翔宇.WANG Jun-jie.YANG Ji-chun.LU Xiang-yu连铸板坯热送过程传热模型研究[期刊论文]-包头钢铁学院学报1999,18(2)
8.胡跃武.卢克斌.郭朝晖.许晞.宋雯琪连铸二冷过程的仿真研究[期刊论文]-连铸2003(2)
9.郝晋兵.王重华集装箱桥吊仿真训练器及其数学模型[会议论文]-2003
10.孙福伟可编程序控制器系统的可靠性数学模型和应用[期刊论文]-应用数学2002,15(2)
本文链接:/Periodical_tsg200904002.aspx。