缝隙腐蚀试验1
缝隙腐蚀

2. 环境因素的影响
溶液中溶解的氧浓度:氧浓度增加,缝外阴极还原反应更易
进行缝隙腐蚀加剧 0.5×106
溶液中氯离子浓度:氯离子浓度增加,缝隙腐蚀加剧 0.1% 温度: 1 )温度升高使传输过程反应动力学加速,从而增大 阳极反应速度;2)溶解氧浓度随温度升高而下降,缝隙腐蚀速 度会下降 pH:pH降低,缝隙腐蚀量增加 腐蚀介质的流速:增加缝隙溶液的流速,使输送到缝隙外部 的金属表面上的氧量增加,缝隙腐蚀量也增加。但流速快则沉 积物不易附着,可能减少缝隙腐蚀。
(1)阴极保护:外加电流或牺牲阳极法将金属材料的电
位降于临界缝隙腐蚀电位以下。 (2)阳极保护:在金属表面上通入足够的阳极电流使电 位达到并保持在钝化区内。
接头设计
尽可能不采用铆接结构而采用焊接结构
容器壁 支管
焊接 部位
管板 热电 偶套管
Ø25.4
3.2 mm 适当加大热电偶套管和支管 管壁的间隙,避免液体停滞
2.8 mm
加大管子和管板的间隙
增大间隙尺寸,消除闭塞条件
缝隙 胀接
缝隙
缝隙
绝热环型焊接
常规型焊接
背部深孔密封焊
热交换器管子和管板的联接
为了避免容器底部与多孔性基础之间产生缝隙腐蚀,罐 体不要直接座在多孔性基础上,可在罐体上加裙式基座 或其他支座。
垫圈的选择
垫圈不宜采用石棉、纸质等吸湿性材料:如用聚四氟乙烯 则较为理想
缝隙腐蚀
缝隙腐蚀
缝隙腐蚀的定义
缝隙的种类
缝隙腐蚀的特征
缝隙腐蚀的形成条件&机理
点蚀和缝隙腐蚀的比较 缝隙腐蚀的影响因素 缝隙腐蚀的防止措施
缝隙腐蚀的定义
在腐蚀介质中的金属构件,由于金属与金属或金属与 非金属之间存在特别小的缝隙,造成缝内介质处于滞 流状态而发生的一种局部腐蚀形态称为缝隙腐蚀。
腐蚀试验标准

GB/T 13671-1992 GB/T 15748-1995 GB/T 10119-1988 GB/T 10123-2001 GB/T 10126-2002 GB/T 10127-2002 GB/T 15970.2-2000 GB/T 15970.4-2000 GB/T 15970.5-1998 GB/T 15970.6-1998 GB/T 15970.7-2000 GB/T 16482-1996 GB/T 16545-1996 GB/T 17897-1999 GB/T 17898-1999 GB/T 17899-1999 GB/T 18590-2001 GB/T 19291-2003 GB/T 19292.1-2003 GB/T 19292.2-2003 GB/T 19292.3-2003 GB/T 19292.4-2003 GB/T 2526-1996 GB 5776-1986GB/T 19747-2005 GB/T 19746-2005 GB/T 15970.8-2005 GB/T 5776-2005 GB/T 13448-2006 GB/T 20121-2006 GB/T 20122-2006 GB/T 20120.1-2006 GB/T 8650-2006 GB/T 20120.2-2006 GB/T 4157-2006JB/T 7901-1999 GB/T 19745-2005 GB/T 10126-1988 GB/T 10127-1988 GB/T 8152.11-2006 GB/T 8152.12-2006 GB/T 8152.4-2006 GB/T 8152.7-2006 GB/T 8152.9-2006 YB/T 5344-2006 YB/T 5362-2006 GB/T 15970.6-2007 GB/T 15970.9-2007 GB/T 20852-2007 GB/T 20853-2007 GB/T 20854-2007 SL 105-2007ICS国际标准分类目录之77.060金属的腐蚀址: 电话:400-7255 888 QQ:569872709 MSN/Email:csres@不锈钢缝隙腐蚀电化学试验方法船用金属材料电偶腐蚀试验方法黄铜耐脱锌腐蚀性能的测定金属和合金的腐蚀 基本术语和定义铁-铬-镍合金在高温水中应力腐蚀试验方法不锈钢三氯化铁缝隙腐蚀试验方法金属和合金的腐蚀 应力腐蚀试验 第2部分:弯梁试样的制备和应用金属和合金的腐蚀 应力腐蚀试验 第4部分:单轴加载拉伸试样的制备和应用金属和合金的腐蚀 应力腐蚀试验 第5部分:C型环试样的制备和应用金属和合金的腐蚀 应力腐蚀试验 第6部分:预裂纹试样的制备和应用金属和合金的腐蚀 应力腐蚀试验 第7部分:慢应变速率试验荧光级氧化钇铕金属和合金的腐蚀 腐蚀试样上腐蚀产物的清除不锈钢三氯化铁点腐蚀试验方法不锈钢在沸腾氯化镁溶液中应力腐蚀试验方法不锈钢点蚀电位测量方法金属和合金的腐蚀 点蚀评定方法金属和合金的腐蚀 腐蚀试验一般原则金属和合金的腐蚀 大气腐蚀性 分类金属和合金的腐蚀 大气腐蚀性 腐蚀等级的指导值金属和合金的腐蚀 大气腐蚀性 污染物的测量金属和合金的腐蚀 大气腐蚀性 用于评估腐蚀性的标准试样的腐蚀速率的测定氧化钆金属材料在表面海水中常规暴露腐蚀试验方法金属和合金的腐蚀 双金属室外暴露腐蚀试验金属和合金的腐蚀 盐溶液周浸试验金属和合金的腐蚀 应力腐蚀试验 第8部分 焊接试样的制备和应用金属和合金的腐蚀 金属和合金在表层海水中暴露和评定的导则彩色涂层钢板及钢带试验方法金属和合金的腐蚀 人造气氛的腐蚀试验 间歇盐雾下的室外加速试验(疮痂试验)金属和合金的腐蚀 滴落蒸发试验的应力腐蚀开裂评价金属和合金的腐蚀 腐蚀疲劳试验 第1部分:循环失效试验管线钢和压力容器钢抗氢致开裂评定方法金属和合金的腐蚀 腐蚀疲劳试验 第2部分:预裂纹试样裂纹扩展试验金属在硫化氢环境中抗特殊形式环境开裂实验室试验金属材料实验室均匀腐蚀全浸试验方法人造低浓度污染气氛中的腐蚀试验铁-铬-镍合金在高温水中应力腐蚀试验方法不锈钢三氯化铁缝隙腐蚀试验方法铅精矿化学分析方法 汞量的测定 原子荧光光谱法铅精矿化学分析方法 镉量的测定 火焰原子吸收光谱法铅精矿化学分析方法 锌量的测定 EDTA滴定法铅精矿化学分析方法 铜量的测定 火焰原子吸收光谱法铅精矿化学分析方法 氧化镁的测定 火焰原子吸收光谱法铁-铬-镍合金在高温水中应力腐蚀试验方法不锈钢在沸腾氯化镁溶液中应力腐蚀试验方法金属和合金的腐蚀 应力腐蚀试验 第6部分:恒载荷或恒位移下的预裂纹试样的制备和应用金属和合金的腐蚀 应力腐蚀试验 第9部分:渐增式载荷或渐增式位移下的预裂纹试样的制金属和合金的腐蚀 大气腐蚀防护方法的选择导则金属和合金的腐蚀 人造大气中的腐蚀 暴露于间歇喷洒盐溶液和潮湿循环受控条件下的加金属和合金的腐蚀 循环暴露在盐雾、“干”和“湿”条件下的加速试验水工金属结构防腐蚀规范(附条文说明)1993-7-1 1996-8-1 1989-1-2 2002-5-1 2002-1-2 2002-12-1 2001-9-1 2001-9-1 1999-7-1 1999-7-1 2000-1-2 1997-1-1 1997-4-1 2000-8-1 2000-8-1 2000-8-1 2002-5-1 2004-4-1 2004-4-1 2004-4-1 2004-4-1 2004-4-1 1997-1-1 1986-1-1 2005-10-1 2005-10-1 2005-10-1 2005-10-1 2006-8-1 2006-9-1 2006-9-1 2006-9-1 2006-9-1 2006-9-1 2006-9-12000-1-1 2005-10-1 1989-1-1 1989-1-1 2007-2-1 2007-2-1 2007-2-1 2007-2-1 2007-2-1 2006-10-11 2006-10-11 2007-12-1 2007-12-1 2007-10-1 2007-10-1 2007-10-1。
腐蚀试验方法ppt课件
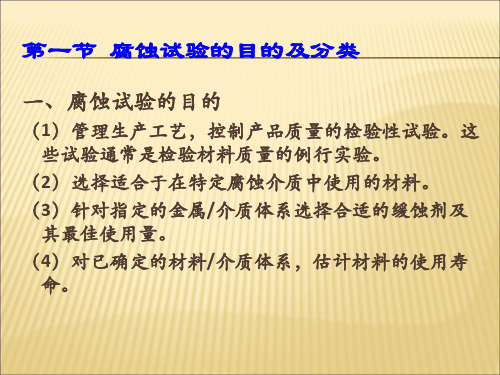
篮球比赛是根据运动队在规定的比赛 时间里 得分多 少来决 定胜负 的,因 此,篮 球比赛 的计时 计分系 统是一 种得分 类型的 系统
(1)模拟试验 一种不加速的长期试验,在实验室的小型
模拟装置中,尽可能地精确地模拟自然界或工 业生产中所遇到的介质及条件,虽然介质和环 境条件的严格重现是困难的,但主要影响因素 要充分考虑。
篮球比赛是根据运动队在规定的比赛 时间里 得分多 少来决 定胜负 的,因 此,篮 球比赛 的计时 计分系 统是一 种得分 类型的 系统
常用的绝缘材料有环氧树脂、清漆、聚 四氟乙烯和石蜡、松香等。
篮球比赛是根据运动队在规定的比赛 时间里 得分多 少来决 定胜负 的,因 此,篮 球比赛 的计时 计分系 统是一 种得分 类型的 系统
试样的安放应保证试样与试样之间、试样与容器 之间、试样与支架之间电绝缘; (2)防止缝隙腐蚀
试样与试样之间、试样与容器之间、试样与支架 之间不产生缝隙;
试样表面与介质充分接触。同时,要求试样装取 方便、牢固可靠;支架本身耐蚀等。
篮球比赛是根据运动队在规定的比赛 时间里 得分多 少来决 定胜负 的,因 此,篮 球比赛 的计时 计分系 统是一 种得分 类型的 系统
纯试剂精确地配制试验溶液,以严格控制试液的成 分。
在试验过程中,还必须防止由于溶液蒸发及其它 原因引起介质浓度、成分和体积的变化,以免影响 介质的腐蚀性能和结果的可靠性。
篮球比赛是根据运动队在规定的比赛 时间里 得分多 少来决 定胜负 的,因 此,篮 球比赛 的计时 计分系 统是一 种得分 类型的 系统
2 试验温度 腐蚀试验温度应尽量模拟实际腐蚀介质的
温度。 实验室控温方法:水浴、油浴或空气恒温箱中 进行。
控制的温度应是整个试样的表面温度,但 为简便起见,往往以试液温度为控制对象。
第5章 局部腐蚀试验方法

Multielectrode Array Sensor (MAS) in ProcessStream of Chemical PlantBefore cleaningMaximum penetration rate:~149 mil/yr (3.73 mm/yr) Coupon tests showed 100to 200 mil/yr (2.5 to 5mm/yr) pitting rateAfter cleaning Dorsey, et al, CORROSION/2004, paper # 04077, 2004•蚀孔通常往重力方向增长•一般蚀孔需要几个月或几年才穿透金属。
通常在出现可以看到的蚀孔之前,需要一段很长的孕育期。
•这段时间由数月到数年,它取决于金属和腐蚀介质的种类。
•然而一旦开始,蚀孔就以不断增长的速度穿透金属。
早期点蚀 破坏性点蚀•点蚀浸泡试验溶液中的氧化剂通常具有较高的氧化还原电位,常用的氧化剂有Fe3+、Cu2+、Hg2+、MnO-、H2O2等。
4•选用不同的氧化剂时将呈现不同的氧化还原电位,因此应谨慎选择氧化剂的种类和数量。
•化学浸泡的点蚀试验溶液种类较多,采用的氧化剂也不同。
1.3 现场试验方法试片实际工况介质测定材料表面发生点蚀的几率测定点蚀发展速度•方法:在试验过程的不同时刻取出一批试片,以其最大点蚀深度对时间作图,并通过数学分析找出它们之间的相关性(关系式),据此可比较点蚀发展速度。
•为使结果可靠,试片的面积应尽可能大一些,每批次取出的试片也要尽可能多一些。
多缝隙腐蚀试验• (a )铜—铁 (b )铜—铝•图 两种不同电化学性质的金属材料接触后诱发的电偶腐蚀 当两种金属或合金相接触,在溶液中可以发现在该液中电位较负的金属腐蚀速度加大,而电位较正的金属受到保护,这种现象就是电偶腐蚀。
电偶腐蚀(接触腐蚀、异金属腐蚀)用极化曲线预测电偶腐蚀行为的示意图ISO大气电偶腐蚀标准方法的试样1-阳极板 2- 阴极板 3- 微断面 4-拉伸试样 5-螺栓 6-垫圈 7-绝缘垫圈 8- 绝缘套管 9-螺帽阴、阳极板状金属用螺栓联结暴露后可用失重和抗拉强度降低评价电偶作用ASTM大气腐蚀试验标准试样1-金属2-胶木套管3-胶木垫圈4-金属5-胶木垫圈阴、阳极板状金属用螺栓联结暴露后可用失重和抗拉强度降低评价电偶作用。
不锈钢缝隙腐蚀电化学试验方法
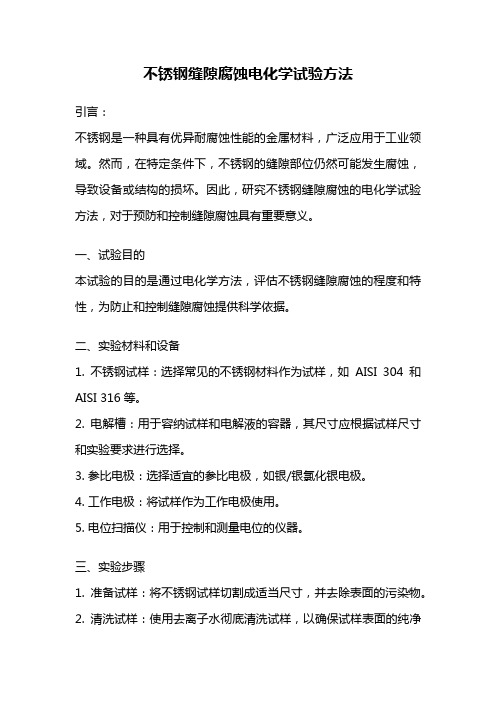
不锈钢缝隙腐蚀电化学试验方法引言:不锈钢是一种具有优异耐腐蚀性能的金属材料,广泛应用于工业领域。
然而,在特定条件下,不锈钢的缝隙部位仍然可能发生腐蚀,导致设备或结构的损坏。
因此,研究不锈钢缝隙腐蚀的电化学试验方法,对于预防和控制缝隙腐蚀具有重要意义。
一、试验目的本试验的目的是通过电化学方法,评估不锈钢缝隙腐蚀的程度和特性,为防止和控制缝隙腐蚀提供科学依据。
二、实验材料和设备1. 不锈钢试样:选择常见的不锈钢材料作为试样,如AISI 304和AISI 316等。
2. 电解槽:用于容纳试样和电解液的容器,其尺寸应根据试样尺寸和实验要求进行选择。
3. 参比电极:选择适宜的参比电极,如银/银氯化银电极。
4. 工作电极:将试样作为工作电极使用。
5. 电位扫描仪:用于控制和测量电位的仪器。
三、实验步骤1. 准备试样:将不锈钢试样切割成适当尺寸,并去除表面的污染物。
2. 清洗试样:使用去离子水彻底清洗试样,以确保试样表面的纯净度。
3. 安装试样:将试样安装在电解槽中,并保证试样与电解液充分接触。
4. 准备电解液:根据实验要求,选择适当的电解液,如盐酸溶液或硫酸溶液,并根据实验要求调整其浓度和pH值。
5. 连接电极:将参比电极和工作电极连接到电位扫描仪,并确保电极与电解槽中的试样相连。
6. 电位扫描:使用电位扫描仪,以一定速率扫描试样的电位,记录电流随电位变化的曲线。
7. 数据分析:根据电流-电位曲线,分析不锈钢缝隙腐蚀的特性和程度。
四、实验注意事项1. 实验操作应规范,注意安全,避免发生意外。
2. 实验前应确保试样的表面光洁,并避免手触摸试样表面。
3. 电解槽和电解液应清洁,以避免杂质对实验结果的影响。
4. 实验过程中应控制电位扫描速率和范围,以确保实验结果的准确性。
5. 实验结束后,应及时清洗试样和设备,以防止腐蚀物对设备和试样的损害。
五、实验结果分析根据电流-电位曲线,可以得到不锈钢缝隙腐蚀的特性和程度。
缝隙腐蚀

IR PH 和腐蚀产物的交互作用
• 当Ph下降到平衡值的时候,ipass处于它的最 大值,但是I可以随着越来越多的缝隙溶液 获得它的平衡而继续增加。因此,越来越 多的缝隙壁有着这么大的ipass值。超过这 个时间,当所有的缝隙溶液都在它的平衡 PH,整个缝隙壁就处于相应的ipass值,当 腐蚀产物的聚集持续发生时R也持续增加, 因此IR>ΔΦ的条件最终会得到满足
IR PH 和腐蚀产物的交互作用
• 1 对于较低的Ex=0值,IR>ΔΦ条件可能在 PH降低到它的平衡值以前或者电解质横截 面通过腐蚀产物的聚集而减少以前就得到 满足 • 2 对于一些大的Ex=0值,IR>ΔΦ条件在PH 下降到平衡值从而增加缝隙在长度方向上 缝隙电解质碎片同时腐蚀产物持续积累时 发生
讨
• 铬酸盐的影响
在中性0.2 M Na2SO4溶液中 在不同浓度的 K2CrO4条件下 铁的腐蚀活性
论
PdH PH探针
• 钯只有在吸收了适当数量的氢以便于形成 一个其中氢的活性是固定的两相的微观结 构的时候才能被用作PH感应器
IR PH 和腐蚀产物的交互作用
• 这篇论文中有两个变量在实验中被观察, PH从9.1降到3.5,缝隙中腐蚀产物在增 加。随着PH的降低,倾向是缝隙中ipass和腐 蚀产物聚集(在这里特别是氢气)增加, 这导致I和R分别增加。PH能够降低到系统 的平衡水解PH(对于铁来说典型的是3到4) 然而腐蚀产物的聚集并没定义明确的限制
IR PH 和腐蚀产物的交互作用
• 3 对于一些更大的Ex=0值,孕育期可能在 整个缝隙电解质全部带到它的平衡PH以后 仍然继续,但是IR>ΔΦ条件最终会随着R (不是I)由于腐蚀产物对缝隙的填充导致 的的增加而得到满足
腐蚀事例

第二章:电偶腐蚀:实例1:六十年代初,美国破冰船壳上的焊缝很快腐蚀,比船壳钢板腐蚀还更严重,原因是焊接金属对船壳是阳极。
加之船壳的涂层系统被冰擦伤,阴极保护系统的阳极也被冰刮落,失去了保护作用。
Eg:焊缝是阳极,船壳是阴极,这就构成了小阳极大阴极的电偶腐蚀电池。
在“制造”部分已经讲到,由于焊缝高温熔化和冷却过程中成分和组织的变化,如果焊条选择不当,很容易造成焊缝耐腐蚀性低于母体,使焊缝发生优先腐蚀。
如果焊缝的电位比母体低得多,那么焊缝与母材组成电偶腐蚀电池,焊缝的腐蚀将大大的加速。
所以在选择焊接金属时一个基本的原则:焊缝相对于母材应是阴极性的。
///对于船舶来说,船壳上都有涂层,大多数还使用阴极保护。
涂料层如果完整致密,将船体和海水隔开,而阴极保护又将船壳控制在同一个保护电位,消除了电位的差异。
所以只要涂层和阴极保护正常。
那么焊缝与母材的电偶腐蚀问题是不会发生的。
实例2:某发电厂凝汽器的管束材质为黄铜,花板未碳钢。
原来使用河水作凝汽器的冷却水,后来因为缺水,便掺入了一些海水。
结果许多设备的腐蚀都加剧了,特别是凝汽器的花板,膨接处的腐蚀率达到20-25mm/a。
Eg:黄铜管束与碳钢花板组成了电偶对,碳钢作为阳极而黄铜作为阴极。
由于黄铜管束面积比碳钢面积大得多,这又是一个小阳极大阴极的组合。
因而天花板可能遭到电偶腐蚀。
///在使用河水作冷却水时电偶腐蚀问题并不明显,没有引起注意;而在河水中掺入海水是电偶腐蚀问题突出了。
这是因为河水的电阻率大,导电性不好,而海水的导电性很好。
腐蚀电池的电流回路包括溶液的欧姆电阻,欧姆电阻大则电池工作阻力大,腐蚀电流小。
海水电阻率小,腐蚀电池电流回路的欧姆电阻笑,因而阳极碳钢花板的电偶腐蚀大大加剧。
实例2:某啤酒厂的大啤酒罐,用碳钢制造,表面涂覆防腐涂料,用了20年。
为了解决罐底涂料层容易损坏的问题,新造贮罐采用了不锈钢板作罐底,筒体仍用碳钢。
认为不锈钢完全耐蚀就没有涂覆涂料。
第5章 局部腐蚀试验方法

1.3 现场试验方法
试片 实际工况介质
测定材料表面发生孔蚀的几率
测定孔蚀发展速度
方法:在试验过程的不同时刻取出一批试片,以其最大孔蚀 深度对时间作图,并通过数学分析找出它们之间的相关性 (关系式),据此可比较孔蚀发展速度。 为使结果可靠,试片的面积应尽可能大一些,每批次取出的 试片也要尽可能多一些。
2.缝隙腐蚀试验
2.1化学浸泡试验方法 2.2电化学测试方法
缝隙腐蚀 在电解液中,金属与金属或金属与非金属表面之间构 成狭窄的缝隙,缝隙内有关物质的移动受到了阻滞, 形成浓差电池,从而产生局部腐蚀,这种腐蚀被称为 缝隙腐蚀。
缝隙腐蚀常发生在设备中法兰的连接处,垫圈、衬板、 缠绕与金属重叠处,它可以在不同的金属和不同的腐 蚀介质中出现,从而给生产设备的正常运行造成严重 障碍,甚至发生破坏事故。 介质中,氧气浓度增加,缝隙腐蚀量增加;PH值减小, 阳极溶解速度增加,缝隙腐蚀量也增加;活性阴离子 的浓度增加,缝隙腐蚀敏感性升高。但是,某些含氧 阴离子的增加会减小缝隙腐蚀量。
-
Cl
2
-
e 2H++2eH e
2+ 2
M
2+ n
+H S 2
FeCl HCl
含H2S的酸性 氯化物溶液
间或有FeCl .4H O结晶
2 2
H
2
S
Fe
+H
2
OFeOH
+
+H
+
Fe2+
2+ FeFe +2e
蚀孔的生长
氢离子和氯离子都能促进大多数金属和合金的溶解,并且 整个过程随时间而加速。 由于氧在蚀孔溶液中的浓度实际等于零,所以蚀孔内不存 在氧的阴极还原过程。溶解氧是在蚀孔附近的表面上进行 阴极反应,故这部分表面不受腐蚀。也就是说,孔蚀使蚀 孔之外的金属表面受到阴极保护,而使蚀孔之内的金属表 面不断溶解而被腐蚀。 综上所述,蚀孔生长的机理和缝隙腐蚀的机理实 质上是相同的。孔蚀是缝隙腐蚀的一种自身诱发的腐蚀形 态——即它不需一条缝隙,它自己创造蚀孔。
- 1、下载文档前请自行甄别文档内容的完整性,平台不提供额外的编辑、内容补充、找答案等附加服务。
- 2、"仅部分预览"的文档,不可在线预览部分如存在完整性等问题,可反馈申请退款(可完整预览的文档不适用该条件!)。
- 3、如文档侵犯您的权益,请联系客服反馈,我们会尽快为您处理(人工客服工作时间:9:00-18:30)。
Temperature and potential dependence of crevicecorrosion of AISI 316stainless steelP.T.Jakobsen *,1,E.MaahnMaterials Technology,Department of Manufacturing Engineering,Technical University of Denmark,Building 204,DK-2800Lyngby,DenmarkReceived 16March 2000;accepted 9October 2000AbstractCrevice corrosion of AISI 316steel has been investigated in a modi®ed ÔAvesta Cell Õ.Po-tentiodynamic scans have been made in sodium chloride solutions of various pH values at di erent temperatures with and without crevice.The breakthrough potential changes dis-continuously with temperature.At all temperatures the attack is localised to the crevice,and the breakthrough potential is lower than for experiments without the crevice.The experiments in acidi®ed environments indicate that crevice corrosion at low temperatures results from acidi®cation in the crevice.At higher temperatures crevice corrosion is believed to be the result of metastable pitting stabilised by the crevice.Ó2001Elsevier Science Ltd.All rights re-served.Keywords:Stainless steel;Polarisation;Crevice corrosion1.IntroductionCrevice corrosion is one of the most common forms of corrosion of stainless steels.Because it cannot easily be discovered before it is fatal for the construction,crevice corrosion is a very detrimental form of corrosion.Crevice corrosion of stainless steel shares many similarities with pitting corro-sion of stainless steel [1].Both phenomena are in¯uenced by pH,bulk chloride/locate/corsciCorrosion Science 43(2001)1693±1709*Corresponding author.Tel.:+46-8-674-17-00;fax:+46-8-674-17-80.E-mail address:pia.jakobsen@corr-institute.se (P.T.Jakobsen).1Present address.Swedish Corrosion Institute,Roslagsv a gen 101,hus 23A,SE-10405Stockholm,Sweden.0010-938X/01/$-see front matter Ó2001Elsevier Science Ltd.All rights reserved.PII:S 0010-938X (00)00167-0concentration and temperature,and in much the same way.Crevice corrosion is induced by less severe conditions than pitting corrosion.The resistance against these forms of corrosion is often expressed as a critical temperature [1,2].For pitting corrosion it is found that there exists a potential independent critical pitting corrosion temperature (CPT)[3,4].Below this temperature pitting is not possible and only transpassive corrosion occurs.Above this temperature pitting is possible,but it depends on the potential whether it will actually occur.This is illus-trated in Fig.1,which shows the temperature dependence of the breakthrough po-tential.The potential independent CPT is the temperature at which a sudden change in breakthrough potential is observed.A curve of the shape shown in Fig.1is found if the breakthrough potential is found from potentiodynamic scanning experiments on a specimen free from crevices as shown by Qvarfort [5,6].By potentiostatic testing with increasing temperature it is possible to determine the potential independent CPT if the potential is chosen between the upper end of the pitting potential range and the lower end of the transpassive corrosion range [4].On the other hand if the chosen potential is within the pitting potential range a potential dependent CPT is deter-mined [4].Arnvig and Bisg ard [4]determined a potential independent CPT whereasMellstr om and Bernhardsson [7]determined a potential dependent CPT.Crolet and Defranoux [8]and Old®eld and Sutton [9]have described a theory for initiation of crevice corrosion of stainless steels by a gradual change of the en-vironment in the crevice.Following Old®eld and Sutton [9],there is a neutral chloride solution containing dissolved oxygen inside and outside the crevice at the outset.Two reactions take place within as well as outside the crevice:Metal dissolution :Me 3Me z z e À1 Oxygen reduction :O 2 2H 2O 4e À34OH À21694P.T.Jakobsen,E.Maahn /Corrosion Science 43(2001)1693±1709Reaction2consumes oxygen which inside the crevice is only replenished by di usion. If the crevice is su ciently deep and tight a part of the crevice will be depleted from oxygen.Reaction1can still take place within the crevice balanced by reaction2 occurring on surfaces external to the crevice.The metal ions thus generated in the crevice will have a positive charge,and to maintain charge neutrality metal ions will migrate out and chloride ions will migrate into the crevice.The main process will be ingress of chloride ions into the crevice.At the same time the metal ions(particularly chromium)will hydrolyse thereby forming acid,e.g.:Cr3 H2O3Cr OH 2 H 3 These processes lead to a more aggressive environment in the crevice(higher chloride content and more acidic).This will accelerate the metal dissolution process(reac-tion1)leading to further migration of chloride ions into the crevice and to fur-ther acidi®cation due to hydrolysis.This continues until the environment formed is su ciently aggressive to break down the passive®lm permanently within the crevice. Once this happens crevice corrosion has initiated[9].Stockert and B o hni suggested that crevice corrosion initiates by a geometrical stabilisation of metastable pitting corrosion[10].A metastable pit is a small pit which initiates and grows for a while under a cover,which presumably is a remnant of the passive®lm.The growth of the pit leads to the formation of a concentrated environment within the pit,and an osmotic pressure builds up over the cover.When the osmotic pressure exceeds the strength of the cover the cover ruptures[10,11].It is found that the concentration of metal ions on the corroding surface of a cavity must exceed about75%of saturation concentration if rapid dissolution are to continue [12].Based on this®gure and a consideration of the steady state di usion out of an open hemispherical cavity Pistorius and Burstein[11]®nd that the product of the pit radius r and the current density i must ful®ll the criteria given in Eq.(4)for con-tinued pit growth to follow the rupture of the cover:ir P 3zFD D C2p; 4where z is the average charge of the metal ions,F is the Faraday number,D is the di usion coe cient and D C is the di erence in metal ion concentration from the corroding pit surface to the bulk solution.The product ir is called the pit stability product.If the pit stability product does not ful®ll the criteria given by Eq.(4)the metastable pit will repassivate when the cover ruptures.The current density by which a metastable pit grows is constant during the metastable growth period[11].A metastable pit initiated at a higher potential on average will grow with a higher current density.Pistorius and Burstein[13]further found that the radius of the metastable pit when the cover ruptures is almost in-dependent of the current density by which the metastable pit grows.This means that the probability that a metastable pit will be able to continue to grow as a stable pit after the cover ruptures will increase with increasing potential[11,13]. Metastable pitting will occur in a crevice as well as on open surfaces.If the metastable pit occurs in a particularly tight point in the crevice the opposite crevice P.T.Jakobsen,E.Maahn/Corrosion Science43(2001)1693±170916951696P.T.Jakobsen,E.Maahn/Corrosion Science43(2001)1693±1709wall will act as a di usion barrier.If the di usion out of the pit is limited su ciently the metastable pit will be stabilised even if it would not have survived on an open surface[10].This is geometrical stabilisation.The radius when the cover ruptures presumably will be una ected by the crevice,and thus a metastable pit growing at a smaller current density can be stabilised in a crevice.A metastable pit growing at a smaller current density will require a smaller crevice width to become stabilised. It is found that the number of metastable pits per unit area of the crevice must exceed a certain number before it is sure that initiation of crevice corrosion has happened[10].This is linked to the property that only su ciently tight points in the crevice are e ective as initiation sites.According to Laycock et al.(1998)[14]a metastable pit at temperatures below the potential independent CPT will repassivate by precipitation of a salt layer in a manner similar to that of iron passivating in sulphuric acid.The critical current density for passivation will increase with temperature.The current density required for stabilisation of a metastable pit will also increase with temperature but slower than the critical current density for passivation.The temperature where these two current densities are equal is the CPT[14].The current density required to stabilise the pit in the crevice is smaller than the current density required to stabilise the metastable pit on an open surface.The critical current density for passivation presumably will not depend on whether the pit is inside or outside the crevice.Following the argument of Laycock et al.(1998)[14] this will mean that the critical crevice corrosion temperature(CCT)will be lower than the CPT.However,the CCT will depend on the tightness of the point in crevice where the metastable pit happens.The CPT can be determined by electrochemical methods,for instance in Refs. [4,7].It may also be determined by simple immersion in solutions with increasing temperature[1].The CCT can also be determined by immersion tests[1,2]or by electrochemical tests[15].It appears from the literature that the CCT most often is determined by immersion tests.Some authors have determined breakthrough po-tentials for crevice corrosion by potentiodynamic scanning[16±18].These investi-gations only used one ycock et al.(1997)[19]measured breakthrough potentials as a function of temperature on rods of904L stainless steel with two o-rings as crevice formers.This paper presents a determination of the breakthrough potential for crevice corrosion as a function of temperature and aims at answering the question whether a potential independent crevice corrosion temperature exists in analogy with the po-tential independent CPT.2.ExperimentalTheÔAvesta CellÕwas developed to test pitting corrosion without the in¯uence of crevice corrosion[5].This is achieved by placing a®lter-paper gasket between the test specimen and the cell and having a small¯ow of distilled water through this gasket. This eliminates the possibility of crevice corrosion.TheÔAvesta CellÕhas later beenmodi®ed to test a larger exposed area of the test specimen [4].This larger area makes it possible to apply a crevice onto the exposed area of the test specimen in the ÔAvesta Cell Õ.In this way the e ect of the test specimen edges is eliminated from the test for crevice corrosion resistance.Fig.2is a schematic drawing of the Ôcrevice corrosion ÔAvesta Cell Õ(CCAC)Õ.The crevice in the CCAC is formed between the test specimen surface and a ring-shaped crevice former of polyvinylidene ¯uoride (PVDF).The crevice former is ground on silicon carbide paper to a #1000®nish.The crevice former is attached to a silicone rubber ring which in turn is attached to a connection piece.The silicone rubber ring ensures that the crevice forming surfaces are aligned.The connection piece is extended by a glass tube which allows the application of pressure onto the crevice.Pressure is applied by compressing the disc springs with the screw.The heating coil allows the cell temperature to be controlled.The small ¯ow of distilled water increases the electrolyte volume.To counteract this the CCAC has an over-¯ow.The dilution caused by the ¯ow of distilled water is compensated for by adding solution of the same composition but higher concentration than the bulk electrolyte.To assure an even ¯ow of distilled water,the distilled water is allowed to ®ll the exposed area before the electrolyte is poured into the cell.An even ¯ow is necessary if crevice corrosion between test specimen and cell is to be avoided.The electrolyte is diluted less than 2&.The exposed area of the test specimen is 10cm 2including the crevice area.The crevice area is 2.4cm 2.The ¯ow rate of distilled waterisFig.2.Schematic drawing of the CCAC.P.T.Jakobsen,E.Maahn /Corrosion Science 43(2001)1693±17091697approximately 40ml/h.The crevice was applied after the electrolyte had been poured into the cell,which means that the electrolyte will ®ll the volumes inside and outside the crevice former.The crevice will also be ®lled with electrolyte from the start of the experiment.The springs were compressed with a force of 220Æ10N.The test specimens were made from cold rolled,as delivered AISI 316plate.The surface is designated 2B according to EN 10088.The composition of the speci®c material used is given in Table 1.The test specimens were washed with hot water and soap,degreased by rinsing with acetone and ethanol,and following this dried in hot air.The test solution was 1MNaCl made from distilled water and analytical grade NaCl.A few experiments were done in 1MNaCl acidi®ed with HCl.Polarisation scans in anodic direction,starting from 0mV/SCE,were made at di erent temperatures.The scan rate was 1mV/min.The scan was stopped when the current density reached a predetermined value.All current densities are referred to the exposed area of 10cm 2.The test solution was held thermostatically at the desired temperature Æ0:5°C.3.ResultsFig.3shows breakthrough potentials as a function of temperature for pitting corrosion measurements.The breakthrough potential is taken as the potential at which the current density continuously exceeds 10l A/cm 2.The data used in Fig.3were found without applying the crevice.The test specimen surface has thus been openly exposed to the electrolyte in these experiments.In Fig.3linear regressions for the data are included.These are included to show the overall tendency of the data and thus assist the interpretation of the ®gure.The data for pitting corrosion show the potential independent CPT to be 15.5°C.Fig.3only includes few points,but more points would not have changed the conclusion signi®cantly,as the CPT is described by other authors [4]to be well de®ned.Fig.4shows breakthrough potentials for crevice corrosion experiments as a function of temperature.Linear regressions of the data are included in this ®gure for the same reasons as in Fig.3.The data for crevice corrosion in some respects re-semble and in some respects di er from the data for pitting corrosion.The data for crevice corrosion does not have a sharp transition from high to low breakthrough potentials.The transition happens over a temperature interval,and in this tem-perature interval also intermediate values of the breakthrough potential are observed.The breakthrough potential for crevice corrosion is lower than the breakthrough potential found on an open surface both at temperatures above and below the transition temperature interval (tti)(hereafter transition interval).TheTable 1Composition of the AISI 316steel used for the investigation Element Cr Ni Mo Si Mn C N P S Others Fe %17.0412.702.620.451.690.0150.0540.0280.0010.96Balance1698P.T.Jakobsen,E.Maahn /Corrosion Science 43(2001)1693±1709limits of the breakthrough potentials for crevice corrosion at temperatures in the transition interval are seen to be set by the behaviour at temperatures aboveandP.T.Jakobsen,E.Maahn /Corrosion Science 43(2001)1693±17091699below the transition interval.It is found that the attack is localised to the crevice at all temperatures (even at temperatures below the transition interval)for the crevice corrosion experiments.Fig.5shows a typical curve from potentiodynamic scanning with the crevice at a temperature above the transition interval.The passive current density increases very slightly as the potential increases.When the breakthrough is reached the current rises quite fast.This behaviour is typical for localised corrosion of stainless steel.The increase in current from 1to 100l A/cm 2is typically observed to happen over 100±150mV at temperatures above the transition interval.This is somewhat slower than seen for pitting corrosion,but the propagation of crevice corrosion in the early stages is slowed down by the electrolyte resistance in the crevice cavity [20].The attacks seen above the transition interval are in a few distinct positions in the crevice,most commonly just one or two.The attack is a patch of uniform corrosion,and it is deeper at the outer circumference of the crevice area.The attacks observed on specimens from experiments in the transition interval are not signi®cantly di erent from those observed above the transition interval.This implies that the attacks are initiated by the same mechanism in and above the transition interval.Fig.6shows typical curves from potentiodynamic scanning with the crevice in 1M NaCl solutions of various pH values at a temperature below the transition interval.Considering the curve in 1MNaCl solution it is seen that this curve di ers from the curve in Fig.5in several ways.Firstly by the higher breakthrough potential.However,this is the characteristic by which the 1MNaCl curve in Fig.6isde®ned1700P.T.Jakobsen,E.Maahn /Corrosion Science 43(2001)1693±1709as being below the transition interval,and the curve in Fig.5is above the transition interval.At a potential around 750mV/SCE the current density in the 1MNaCl curve in Fig.6becomes almost constant until the breakthrough starts.If the ex-periment is stopped at low current density,a ring of yellowish brown discoloration can be seen approximately halfway between the inner and outer peripheries of the crevice area.The attack seen when the experiment is stopped at a higher current density will be a large number of small patches of uniform attack evenly distributed along the circle and with discoloration between the patches.There will be more patches of attack near the outer periphery of the crevice area than near the inner periphery.Fig.7shows typical curves from potentiodynamic scanning in 1MNaCl solutions of various pH values in experiments where the crevice was not used.The experiments were made at a temperature below the potential independent CPT.This means that the resulting corrosion was transpassive corrosion.The 1MNaCl curve in Fig.7is characterised by having a local maximum in the passive current density at a potential around 750mV/SCE.At a higher potential a local minimum in the current density is observed.The curves shown in Fig.7for experiments done without crevice in 1MNaCl acidi®ed to pH 4and pH 2show that the current density in the maximum becomes higher the lower the pH is.The change is small at pH 4.At pH 2the maximum current density is near 10l A/cm 2.The current density measured at the minimum is also higher the lower the pH is.At pH 2the current density decreases to about 2l A/cm 2.At pH 1the current simply increases without passing through amaximum.P.T.Jakobsen,E.Maahn /Corrosion Science 43(2001)1693±17091701The rise of the current starts where the increase towards the maximum starts when the pH value is higher.This behaviour indicates primary transpassive corrosion followed by a secondary passivation and ®nally secondary transpassive corrosion [6].This kind of behaviour has been observed by other authors for stainless steels [6,21].After terminating experiments done without crevice below the CPT the solutions smelled as chlorinated water does.This indicates that the current rise after the minimum was due to oxidation of chloride,although it is possible that some oxygen evolution took place simultaneously.The secondary passivity is in¯uenced by pH and is not possible if the pH decreases too much.The curves shown in Fig.6for experiments done with crevice in 1MNaCl acidi®ed to pH 4and pH 2show that the behaviour in the pH 4solution is very similar to the behaviour in 1MNaCl.At pH 2the current passed 1l A/cm 2at a lower potential than in 1MNaCl.Between 10and 15l A/cm 2the current rose very slowly in the pH 2solution.4.DiscussionAt temperatures below the transition interval the initiation of crevice corrosion appears to happen quite uniformly in the part of the crevice where the distance to the edges of the crevice area is largest.The experiments done in acidic bulk solutions help to explain the mechanism of initiation of crevice corrosion at temperatures below the transition paring the curves done at the same pH value from Figs.6and 7it is seen that the overall behaviour of the two curves is the sameuntil1702P.T.Jakobsen,E.Maahn /Corrosion Science 43(2001)1693±1709the potential at which the maximum in current density occurs for the experiment done without crevice.As the potential increases above the value at the maximum the current density decreases for the experiment without the crevice,but it remains almost constant for the experiment with the crevice.Thus no secondary passivation is observed in the experiments with crevice although it is probable that secondary passivation will occur outside the crevice in these experiments.The current density within the crevice will therefore increase during the interval in which almost constant current density is observed.A rising current density inside the crevice can be rationalised if the pH within the crevice is lower,cf.Fig.7.The occurrence of sec-ondary passivation in the experiments without crevice show that primary transpas-sive corrosion has taken place[22,23].By primary transpassive corrosion soluble Cr(VI)-species are formed,e.g.[24]:Cr 4H2O3HCrOÀ4 7H 6eÀ 5 It is seen that acid is formed simultaneously with the Cr(VI)-species.Convection will make the concentration of Cr(VI)-species and acid low at the surface of the metal outside the crevice.Inside the crevice there is no convection,and the concentration of Cr(VI)-species and acid will increase.In Appendix A[26]the pH in the crevice is calculated based on assumptions as indicated in the appendix.Depending on the crevice width used in the calculation the pH is found to be between0.57and1.57. However,the curve found in Appendix A for the current within the crevice indicates that secondary passivation does take place in the crevice before breakthrough.Thus it is proposed that crevice corrosion below the transition interval initiates due to a gradual acidi®cation of the environment in the crevice,but initiation is only possible once secondary passivation has occurred in the crevice.When secondary passivation occurs the passive®lm becomes more iron-rich.It appears that the environment formed in the crevice is only able to break down the more iron-rich®lm. Experiments atÀ0.5°C in which the potential was scanned by1mV/min to 600mV/SCE and then held potentiostatically at600mV/SCE for48h showed de-creasing current density during the potentiostatic period.Similar experiments but with the potential held at800mV/SCE also showed decreasing current density during the potentiostatic period.Thus it appears that an over-potential is necessary for stable propagation of crevice corrosion at temperatures below the transition interval.This mechanism can be considered a modi®cation of the mechanism pro-posed by Crolet and Defranoux[8]and by Old®eld and Sutton[9].However,it is important to note that the mechanism proposed here depends critically on the high potential to produce an acidic environment and that probably initiation is only possible once secondary passivation has occurred within the crevice.In and above the transition interval the corrosion attack is seen as one or perhaps a few patches of uniform corrosion in the crevice.This indicates that the initiation is pointwise.The geometrical stabilisation of metastable pitting theory of Stockert and B o hni[10]will lead to pointwise initiation.Under the experimental conditions used in this investigation the number of metastable pits as a function of temperature and potential during potentiodynamicscanning becomes important.Pistorius and Burstein[11,13]found that the meta-stable pitting rate(number of metastable pits per unit area per unit time)has a maximum at intermediate potentials(which actually are quite low).The number of possible metastable pitting sites increases with potential at®rst and then becomes constant[11,13].Gar®as-Mesias and Sykes[25]did potentiodynamic scanning on 25Cr duplex stainless steel.Their curves show some transients but each of these probably includes several metastable transients.They also®nd a maximum in metastable pitting rate at intermediate potentials.At higher potentials the transients are few and occur randomly.The size and number of observed transients increase with temperature in the measurements of Gar®as-Mesias and Sykes[25].This pre-sumably signi®es that the number of transients increase with temperature and that the current density at which the individual metastable pit is growing also increases with temperature.It is assumed that at temperatures above the transition interval the number of metastable events at low potentials exceeds the number necessary to initiate crevice corrosion.The breakthrough potential therefore is low.As the metastable events are distributed randomly over the surface,the actual number of events happening before the initiation will vary.This explains the variation in the breakthrough potential at one temperature.If the temperature is decreased the number and size of the meta-stable events decreases.Both of these e ects will shift the breakthrough potential to higher values with decreasing temperature.In the transition interval it is believed that the number of metastable events at low potentials will not exceed the number necessary to initiate crevice corrosion.Thus the initiation might happen at low potentials,or it might happen at higher potentials. If crevice corrosion does not initiate at low potentials the breakthrough will appear to happen coincidentally,because the metastable events occur randomly.This is the reason for the large variation of the breakthrough potential in the transition interval. When decreasing the temperature further,the size of the metastable pits becomes too small to initiate crevice corrosion,because the crevice width is not su ciently small. At this temperature the mechanism of initiation shifts from geometrical stabilisation of metastable pitting to gradual acidi®cation(moving towards lower temperatures). The lowest temperature at which a metastable pit can be stabilised in the crevice is a CCT in the sense that initiation of crevice corrosion will not(normally)be possible at lower temperatures where the redox-potential of the bulk solution will have to be unusually high to give crevice corrosion.The transition interval arises because of the variations in crevice geometry be-tween the experiments and because the metastable pits occur in random positions on the surface.The tightness of the tightest points probably will not be the same in each experiment and a metastable pit might not occur in the tightest points.Both these factors might lead to a scatter in temperature as well as potential.Thus the ap-pearance of a transition interval is presumably unavoidable for experimental de-termination of crevice corrosion behaviour.At the lowest temperature in the transition interval it will be possible to initiate crevice corrosion by geometrical stabilisation of metastable pitting at a low potential although this situation will not be realised in every experiment due to the dependence。