光学零部件的基本测量
光学检测的综述
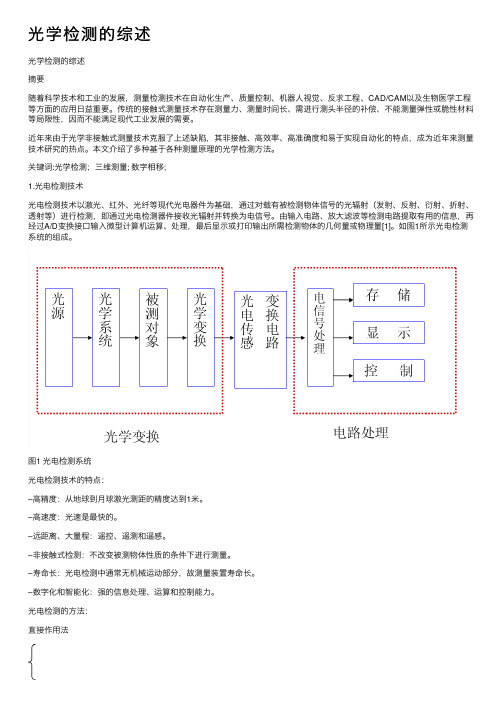
光学检测的综述光学检测的综述摘要随着科学技术和⼯业的发展,测量检测技术在⾃动化⽣产、质量控制、机器⼈视觉、反求⼯程、CAD/CAM以及⽣物医学⼯程等⽅⾯的应⽤⽇益重要。
传统的接触式测量技术存在测量⼒、测量时间长、需进⾏测头半径的补偿、不能测量弹性或脆性材料等局限性,因⽽不能满⾜现代⼯业发展的需要。
近年来由于光学⾮接触式测量技术克服了上述缺陷,其⾮接触、⾼效率、⾼准确度和易于实现⾃动化的特点,成为近年来测量技术研究的热点。
本⽂介绍了多种基于各种测量原理的光学检测⽅法。
关键词:光学检测;三维测量; 数字相移;1.光电检测技术光电检测技术以激光、红外、光纤等现代光电器件为基础,通过对载有被检测物体信号的光辐射(发射、反射、衍射、折射、透射等)进⾏检测,即通过光电检测器件接收光辐射并转换为电信号。
由输⼊电路、放⼤滤波等检测电路提取有⽤的信息,再经过A/D变换接⼝输⼊微型计算机运算、处理,最后显⽰或打印输出所需检测物体的⼏何量或物理量[1]。
如图1所⽰光电检测系统的组成。
图1 光电检测系统光电检测技术的特点:–⾼精度:从地球到⽉球激光测距的精度达到1⽶。
–⾼速度:光速是最快的。
–远距离、⼤量程:遥控、遥测和遥感。
–⾮接触式检测:不改变被测物体性质的条件下进⾏测量。
–寿命长:光电检测中通常⽆机械运动部分,故测量装置寿命长。
–数字化和智能化:强的信息处理、运算和控制能⼒。
光电检测的⽅法:直接作⽤法差动测量法补偿测量法脉冲测量法光电检测系统◆主动系统/被动系统(按信息光源分)–主动系统通过信息调制光源,或者光源发射的光受被测物体调制。
如图2所⽰图2 主动系统的组成框图–被动系统光信号来⾃被测物体的⾃发辐射。
如图3所⽰图3 被动系统的组成框图◆红外系统/可见光系统(按光源波长分)[2]–红外系统多⽤于军事,有⼤⽓窗⼝,需要特种探测器。
–可见光系统多⽤于民⽤◆点探测/⾯探测系统(按接受系统分)–⽤单元探测器接受⽬标的总辐射功率。
第3章第1节曲率半径的测量
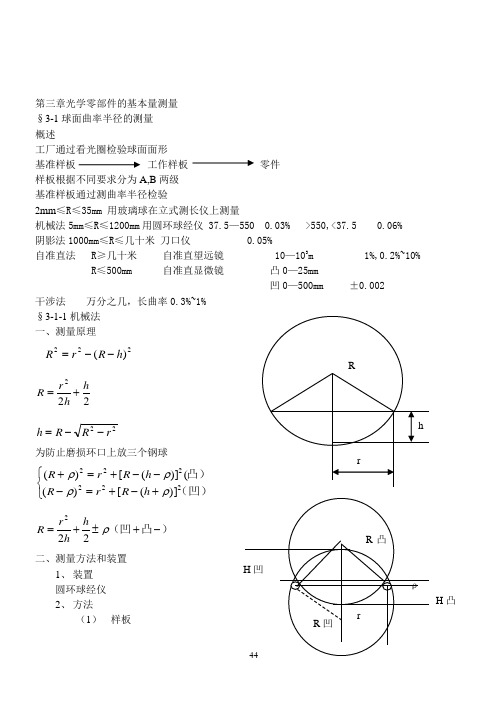
第三章光学零部件的基本量测量 §3-1球面曲率半径的测量 概述工厂通过看光圈检验球面面形基准样板 工作样板 零件 样板根据不同要求分为A,B 两级 基准样板通过测曲率半径检验2mm ≤R ≤35mm 用玻璃球在立式测长仪上测量机械法5mm ≤R ≤1200mm 用圆环球经仪 37.5—550 0.03% >550,<37.5 0.06% 阴影法1000mm ≤R ≤几十米 刀口仪 0.05%自准直法 R ≥几十米 自准直望远镜 10—103m 1%,0.2%~10% R ≤500mm 自准直显微镜 凸0—25mm凹0—500mm ±0.002 干涉法 万分之几,长曲率0.3%~1% §3-1-1机械法 一、测量原理222)(h R r R --=222h h r R +=22r R R h --=为防止磨损环口上放三个钢球⎩⎨⎧+-+=---+=+(凹)凸)222222)]([)(()]([)(ρρρρh R r R h R r R )凸(凹-+±+=ρ222h h r R二、测量方法和装置1、 装置 圆环球经仪2、 方法(1) 样板A 平板玻璃放在还口上读取a1B 球面放在还口上读取a2C 计算h=a2-a1)凸(凹-+±+=ρ222h h r R(2)标准样板(对板)A 凸面放在环口上读取a1B 凹面放在环口上读取a2C 计算 2h=a2-a1⎪⎩⎪⎨⎧--=-+=2022220)(2r R R h r R r r r ρ 2220hh r R +=420H H r R +=3、 测量误差分析h r r R =∂∂ 22221h r h R -=∂∂,1±=∂∂ρR 22222222)1(41ρσσσσ+-+=h r R hr h rmm r 001.0=σmm 0005.0=ρσh σ由下列影响因素(1) 刻尺误差 经修正可达mm h 0004.01=σ (2) 阿基米德螺旋线测微目镜误差mm s h 0002.05/001.0/2===βσσ(3) 显微镜对准误差mm h 00013.0581.0073.0073.03±=⨯±=Γ±=δσ mm h h h h 0005.0103.12224224222232221±=⨯⨯+⨯+±=++±=-σσσσ(4) 不同重量引起的测量环变形 精度RRσ37.5—550 0.03% >550,<37.5 0.06% 4、环口选择 另Rr K =)11(2K R h --= )()11()11(122K f K K K R r h r r R A =--=--==∂∂=)(11122122222K f KK h r h R B -=----=-=∂∂=222221)()(h r R K f K f σσσ+=1f (K ),2f (K )在定义域内为单调函数有端值5、 优缺点1) 优点:精度高、测量范围宽、零件不用抛光、操作方便 2) 缺点:磨损§3-1-2自准直法一、 准直望远镜法 1、 测量原理f x d R --=+-x x f f d f x f d f x d R ''+''-='-''-+='-+=)()(2当f x R d '' ,时x f R ''-≈2 2、 测量装置及方法 1)、装置:带有伸缩筒的自准直望远镜 2)、方法A 用平面反射镜自准读取a1B 用被测球面自准读取a2C 计算21a a x -='x x f f d R ''+''-=)(,3、误差分析1=∂∂=d R C ,x x f f R B ''+'='∂∂=2,22x f x R A ''='∂∂=22222d f x R B A σσσσ++±='' 实际上用x f R ''-≈2分析 x f R '-'=-lg lg 2)lg(xx d f f d R dR ''-''=222)()(4x f Rx f R'+'±=''σσσ其中%1.0±=''f f σx 'σ主要有三个因素决定(1) 纵向调焦误差'1x σ调焦误差222)3429.0(31DD SD λασ()+Γ±=屈光度)()2(58.02dD SD -'Γ±=δσ自准时222)3429.0(3212DD SDλασ()+Γ±= 调焦两次1222)3429.0(32222SD SD D D σλασ=+Γ±=()1210001SD x f σσ'='(2)平面镜的面形误差20241DN R SD λσ±==10004100022222f D N f SD x '±='='λσσ 修正1111R R R ±=凹面取正凸面取负 (3)伸缩筒格值误差mm x 001.02±='σ例:用自准直望远镜测一透镜曲率半径已知D=50mm,D/f ′0=1/10Γ=20×平面镜口径D 0=60mm,N=0.2(在50mm 范围内)测得x ˊ=5mm,1mm,25mm 解:22)()(4x f Rx f R'+'±=''σσσ%1.0±=''f f σ)/1(1070.1)50356.045020129.0(66)3429.0(32242222221m D D SD -⨯±=⨯⨯+⨯⨯±=+Γ±=()()λασ4106.6)222050(206158.0)2(58.0-⨯±=⨯-⨯⨯±=Γ-Γ±=d D SDδσ取清晰度法0425.0107.11000500100042121=⨯⨯='=-'SD xf σσ4-2202101.246056.02.0441⨯=⨯⨯=±==D N R SD λσ 031.010********.241000424-222=⨯='±='f D N x λσ053.0031.00425.022±=+±='x σ若x ˊ=5mm, mm x f R 50000550022==''-= %1.1)50053.0(%)1.0(4)()(42222=+±='+'±=''x f R x f Rσσσ 若x ˊ=1mm, mm x f R 250000150022==''-= %3.5)10053.0(%)1.0(4)()(42222=+±='+'±=''x f R x f Rσσσ 若x ˊ=25mm, mm x f R 100002550022==''-= %291.0)250053.0(%)1.0(4)()(42222=+±='+'±=''x f R x f Rσσσ 若d=200mm mm x x f f d R 1030025)25500(500200)(=+-=''+''-=50.295.0)25255002(053.0)25500()2()(222222222222=⨯+⨯+±=''+'+''±=''f x R x x f x f σσσ%9.2%10010300300%,295.01030050.29=⨯==R Rσ 4、 优缺点(1) 优点:可测大曲率半径、非接触测量、设备简单 (2) 缺点:精度低(0.2%~10%)、只适用于大曲率半径、被测零件要抛光二、 准直显微镜法 1、 测量原理2、 测量方法和装置(1) 装置:光学球经仪(2) 方法:自准直显微物镜可换A 显微镜的准球心看到自准反射象记下读数a1B 显微镜的准球面看到自准反射象记下读数a2C 计算R=a2-a1+x 03、 误差分析A 夹持器座定位误差m μσ0.31=B 刻尺刻线误差m μσ5.02=C 投影读数器误差m μσ5.03≈D 显微镜两次调焦(清晰度法)的标准偏差)()32073.0662224mm NA n NA λασ()(+Γ±=例:用光学求经仪测曲率半径,已知:110,56.0,1.0,4'==Γ===⨯⨯αμλβm m NA 求调焦误差可见提高↑β和↑NA 可提高测量精度 但1、β大NA 大工作距小凸面测量受限3、 零件口径D/R 小时NA 不能充分利用达不到提高精度的目的反而会因放大率大光束孔径小使视场暗降低调焦精度 4、 优缺点(1) 优点:非接触测量表面不会磨损、可测小曲率半径、精度高R σ(0.001~0.002) (2) 缺点:表面必须抛光、测量范围小(凸大于25mm 凹小于500mm )、仪器调整复杂 §3-1-3阴影法 1、 测量原理R=SO=HO△R=R-L=HO-HA ≈BO △ ABC ∽△HH ˊOH H BO HO AO O H AB '==' 2/21D R R ∆=δRD R 4δ=∆HS H ´AB δLD L R D L R L R 44δδ+≈+=∆+= 2、 测量装置及方法(1)装置:刀口仪(2)测量方法A 使刀口位于球心处(通过观察阴影图)B 量LC 计算LD L R 4δ+=波差和几何像差的关系R R D W ∆=228即W D R R 228=∆3、 测量误差分析A 米尺误差)1~5.0(mm L =∆B 调焦误差R D h 82=,228R R D h ∆=∆ h DR R ∆=∆2228 m h μλ4012055.020≈±=±=∆2222222500010004088D R D R h D R R ±=⨯±=∆=∆ 例:D=130mm,R=1300mmmm D R R 02.013050001300500022222±≈⨯±=±=∆ 可见调焦误差很小不是主要矛盾mm R R R R 5.0121±=∆=∆+∆=∆%04.0%13005.0±=±=∆R R 精度%05.0±=∆RR 4、 优缺点(1) 优点:非接触测量、可测大曲率半径。
零件光学超精密加工检测技术
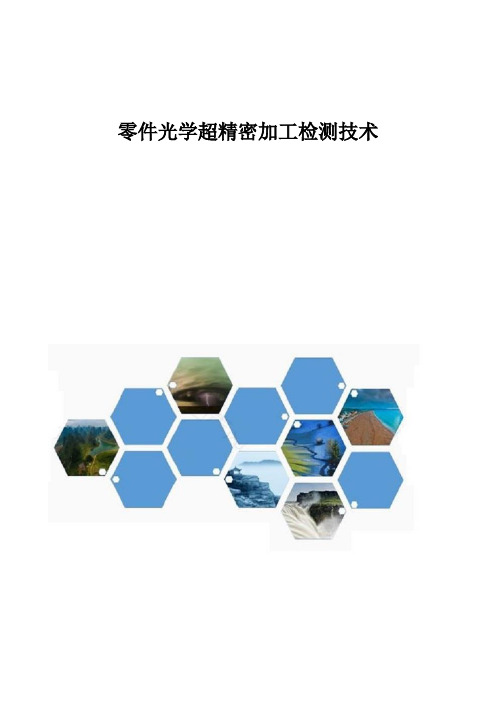
零件光学超精密加工检测技术摘要:随着数字数控机床和加工平台的产生与发展,机械零件的加工方式也向着大批量、专一化方向发展。
导致对机械零件的需求也逐渐加大,零件的尺寸和表面加工质量是否符合标准使用要求是影响机械零件正常工作的关键,因此,对机械零件的光学超精密检测成为主要研究任务。
机械零件表面的加工质量和尺寸大小虽然对零件的正常使用影响较低,但直接影响零件的可靠性、质量和使用寿命,而机械零件使用时间决定零件经济效益。
随着光学超精密加工技术的不断发展,零件光学超精密加工检测技术已成为超精密加工迫在眉睫的关键难题。
人工智能技术是一种新兴的用于模拟、延伸和扩展的智能理论、方法、技术及应用系统的一门新的技术科学。
人工智能技术中的机械学习法,使机械零件的光学超精密检测过程大大简化,并将操作结果保存在存储器中,便于后续光学超精密检测过程的快速执行。
关键词:光学检测;现状;发展引言单参数精密测量是精密测量中最简单的问题,近年来在复杂探测等问题中有了重要应用。
多参数精密测量复杂得多,参数之间存在精度制衡。
如何减少参数之间的精度制衡以实现多参数最优测量,是多参数精密测量的重要问题之一。
为了消除参数之间的精度制衡,研究人员将单参数测量实验中控制增强的次序测量技术应用到多参数测量中,通过调控测量系统动力学演化,完全解决了正演化算法中参数之间的精度制衡问题,实现了最优测量。
1测量系统将四组视觉传感器单元(包括CCD相机和激光器)分别竖直放置于精密零件两侧,垂直于精密零件中轴线,安装在精密零件两侧的立柱上;其中两组视觉传感器单元放置于精密零件一侧立柱上,另外两组视觉传感器单元放置于精密零件另一侧立柱上。
首先利用激光跟踪仪建立基坐标系统,然后对每个视觉传感器单元进行相机参数标定、光平面参数方程标定以及全局标定,最终得到相机的内参矩阵、相机到基坐标系下的全局标定矩阵以及激光平面在基坐标系下的平面方程,完成系统使用以及测量前的预处理。
光学测试技术-第2章-光学准直与自准直技术1

(-z-)--z处的光斑半径(光强下降到光斑中心光强的
1/ e处2 的光斑半径; ----激光波长; --n--传播空间的折
射率,在大气中传输时取为1。
第一节 激光束的准直与自准直技术
其中
2
(
z)
02
1
z 02n
2
(1)束腰处的波阵面为平面,此时 R(0) (取束腰位于
坐标原点),则有:
q0
与望远镜视放大率有关,此外还和高斯光束结构参数
( 10,)z1 有关。增大 (z束1 腰远离望远镜 )L,1 压缩比
也增大,光束准直性将更好些。
第一节 激光束的准直与自准直技术
总结:望远镜两透镜的距离为 D f1,f2其 中
f2 f1
如果有一高斯分布的激光光束,其发散角为 ,从左方
入射到倒置的望远系统,出射后的发散角 f1
第一节 激光束的准直与自准直技术
由于激光具有极好的方向性,一个经过准直的连续输出的 激光束,可以认为是一条粗细几乎不变的直线。因此可以用 激光束作为空间基准线,这样的激光准直仪能够测量直线度、 平面度、平行度、垂直度,也可以做三维空间的基准测量。
激光准直仪和平行光管、经纬仪等一般的准直仪相比, 具有工作距离长,测量精度高和便于自动控制、操作方便等 优点,可以广泛地用于隧道开凿、管道铺设、高层建筑建造、 造桥、修路、开矿以及大型设备的安装、定位等。
(例如中心斑直径 70m , 保持约1m范围内光强分布基本不变)
这一特点,在测量上可有许多用途。
图示为用于测量物 体表面轮廓的一个
扫描反射镜
CCD相机
例子。准直激光束
通过轴锥镜成为近
似的零阶贝塞尔光 束,经扫描反射镜。 光束在被测表面扫 一条细亮线。
光学零件通用技术要求最新
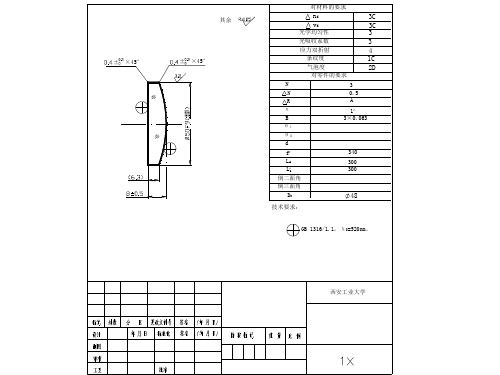
平板零件的类型 不平行度
滤光镜 高精度 3″-1′
保护镜 一般精度 1′-10′
分划板
10′-15′
表面涂层的反射镜 10′-15′
背面涂层的反射镜 2″-30″
光楔精度 公差 高精度 ±(0.2″-10″) 中等精度 ±(10″-30″) 一般精度 ±(30″-1 ′)
十三、对光学部件的技术要求
方案之3:光圈检验
外表形状公差〔N 、ΔN〕
n 对光圈数N和局部光圈ΔN的要求
n 光波在被检光学外表与参考光学外 表间由于干预所形成的条纹。它表 示被检光学零件外表曲率半径误差。
R
4NR2
D2
n 被检光学零件外表与参考光学外表由干 预所形成的干预条纹的不规那么程度, 它表示面形精度。
n ΔN应由光学设计确定。
第二节 对光学零件的要求
n 透镜
曲率半径及面形精度 中心误差 外圆直径及公差 厚度及公差 外表粗糙度 外表疵病 气泡度
棱镜
角度及直线尺寸误差 屋脊棱镜误差 非圆形零件的保护性倒角 平面度 分辨率 研磨外表的粗糙度 抛光外表的疵病 气泡度
一、气泡度q
n 限定气泡大小,可以不限制也可以限制数量
n q=0.01 n q=0.01×3
n N和ΔN的取值应协调一致。一般ΔN= 〔0.2~0.1〕N
曲率半径及面形精度
三、标准样板精度等级△R
n 标准样板的精度ΔR分为A、B两级。
精
标准样板的曲率半径R
度 0.5~5 >5~10 >10~35 >35~350 >350~1000 >1000~4000
等
半径允差
级
ΔR(µm)
相对R名义尺寸的百分比
十五、光学零件图
第章光学零件通用技术要求
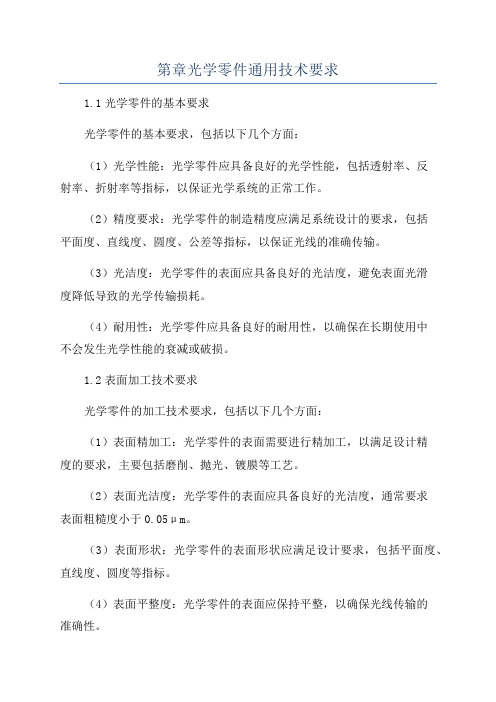
第章光学零件通用技术要求1.1光学零件的基本要求光学零件的基本要求,包括以下几个方面:(1)光学性能:光学零件应具备良好的光学性能,包括透射率、反射率、折射率等指标,以保证光学系统的正常工作。
(2)精度要求:光学零件的制造精度应满足系统设计的要求,包括平面度、直线度、圆度、公差等指标,以保证光线的准确传输。
(3)光洁度:光学零件的表面应具备良好的光洁度,避免表面光滑度降低导致的光学传输损耗。
(4)耐用性:光学零件应具备良好的耐用性,以确保在长期使用中不会发生光学性能的衰减或破损。
1.2表面加工技术要求光学零件的加工技术要求,包括以下几个方面:(1)表面精加工:光学零件的表面需要进行精加工,以满足设计精度的要求,主要包括磨削、抛光、镀膜等工艺。
(2)表面光洁度:光学零件的表面应具备良好的光洁度,通常要求表面粗糙度小于0.05μm。
(3)表面形状:光学零件的表面形状应满足设计要求,包括平面度、直线度、圆度等指标。
(4)表面平整度:光学零件的表面应保持平整,以确保光线传输的准确性。
1.3镀膜技术要求镀膜技术是光学零件制造过程中的重要环节,其技术要求包括以下几个方面:(1)膜层性能:镀膜膜层应具备良好的透射、反射和抗反射特性,以满足光学系统的设计要求。
(2)膜层均匀性:镀膜膜层应均匀附着在光学零件表面,避免膜层厚度不均匀导致的光学性能差异。
(3)膜层硬度:镀膜膜层应具备一定的硬度,以防止膜层在使用过程中因受力而变形或损坏。
(4)膜层附着力:镀膜膜层应具备良好的附着力,以确保在使用过程中不会轻易脱落或剥离。
1.4检测技术要求光学零件的检测技术是保证产品质量的重要环节,其技术要求包括以下几个方面:(1)表面检测:通过光学显微镜、扫描电子显微镜等设备对光学零件的表面进行检测,以确保几何形状和光洁度的满足设计要求。
(2)光学性能检测:通过光学测试仪器对光学零件的透射、反射、折射等性能进行测试,以确保性能指标符合设计要求。
(整理)光学零件检验方法
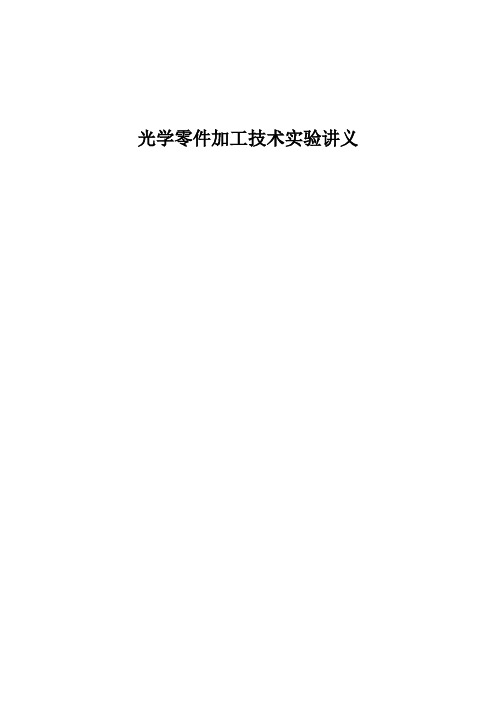
光学零件加工技术实验讲义实验一 光学零件毛坯的成型一、实验目的:1、了解古典法加工块料毛坯粗磨成型的工艺过程;2、熟悉所用设备、材辅料等相关知识。
二、实验设备及用品切割机、粗磨机、滚圆机、K9玻璃、金刚砂 三、实验步骤1、 取块料玻璃,在切割机上按30x30x20mm 切割;2、 在平面粗磨机上,分别用100#,240#金刚砂磨平第一面;3、 将磨平的一面用胶粘在平的垫板上,排列均匀;4、 在粗磨机上,手持垫板,用100#,240#金刚砂整盘研磨第二面,要不断更换垫板位置,使之研磨均匀。
同时要用卡尺测量,保证厚度和平行度; 5、 将两面磨平的平行玻璃板粘成条,宽:长=1:8~1:10;6、 在滚圆机上,将玻璃条滚圆成棒,∆Φ+Φ=Φ0;7、 将玻璃棒在电热板上加热,使粘胶熔化并逐一拆开玻璃板; 8、 用酒精等有机溶剂清洗玻璃;9、 用粗磨盘开球面,手持比例移动,更换位置,开出具有一定曲率半径的球面零件; 10、检验,用铁样板或试擦贴度的方法。
四、讨论1、在粗磨平面时,为什么第一面磨平单块加工,而第二面磨平可成盘加工?2、检验时,铁样板或试擦贴度为何从边缘接触密切?实验二金刚石磨轮铣磨球面一、实验目的1、验证光学零件铣磨原理;2、了解粗磨铣磨工艺过程;3、熟悉铣磨机工作原理和调整方法;4、要求铣磨如图1所示的透镜。
二、实验设备与用具透镜铣磨机QM08A 、金刚石磨轮(M D =20mm ,r=2mm ,粒度#100,浓度100%)、千分尺、扳手、透镜毛胚 (mm 010.025-φ,d15mm )、擦镜盘等。
三、铣磨原理球面零件的铣磨原理如图2、图3所示。
磨轮轴轴线与工作轴轴线相交于0点,两轴线的交角为α,筒形磨轮1绕自身轴线作高速旋转,工件2绕工件轴转动。
磨轮断面在工件表图3-2凸球面铣磨原理 图3-3凹球面铣磨原理 按图2与图3,有以下关系式:)(2sin r R D M±=α (1)式中 α——磨轮轴与工作轴夹角;M D ——磨轮中径;R ——工件被加工面的曲率半径; r ——磨轮端面圆弧半径(凸面取“+”号,凹面取“-”号)上式也可以写成r D R Mαsin 2=(2)当磨轮选定后,M D 与r 均为,调节不同的α角,既可加不同曲率半径的球面零件。
光学测量技术及应用

光学测量技术及应用
光学测量技术是一种利用光学仪器测量物体大小、形状、位置、速度、色彩等特征的
技术。
光学测量技术具有高精度、高速度、无接触、非破坏等特点,被广泛应用于机械制造、航空航天、医疗保健、环境监测等领域。
本文将对光学测量技术的原理和应用进行介绍。
光学测量技术的原理主要是利用光的散射、反射、折射、干涉、衍射等现象来测量物
体的各种特性。
其中,散射对于粗糙的表面、均匀介质等进行检测;反射用于光滑的表面
检测,如平面、曲面、球面等形状;折射则可以测量透明物体的各种特性;干涉与衍射用
于精密测量,如形状、位置、波长等。
光学测量技术的应用十分广泛。
机械制造领域常常使用光学测量技术来检测零件的几
何形状、尺寸误差和表面质量等,以确保生产零部件的精度和质量。
航空航天领域利用光
学测量技术测量飞行器及卫星的姿态、速度、位置等参数,评估其稳定性、安全性和性能。
医疗保健领域则使用光学测量技术测量人体特征,如血液压力、血流速度、视力等。
环境
监测方面使用光学测量技术测量空气质量、水质污染、地震预警等。
总之,光学测量技术的现代化发展已经成为推动产业升级和技术进步的重要支撑力量,带动了许多领域的发展和改革。
未来,随着技术的不断革新和创新,光学测量技术将会有
更加广泛和深入的应用,为人类的生产和生活带来更多的便利和福利。
- 1、下载文档前请自行甄别文档内容的完整性,平台不提供额外的编辑、内容补充、找答案等附加服务。
- 2、"仅部分预览"的文档,不可在线预览部分如存在完整性等问题,可反馈申请退款(可完整预览的文档不适用该条件!)。
- 3、如文档侵犯您的权益,请联系客服反馈,我们会尽快为您处理(人工客服工作时间:9:00-18:30)。
干 涉 法
8
第一节 光学面形偏差的检测
特点:
具有更高的测试灵敏度和准确度; 绝大部分的干涉测试都是非接触式的,不会 对被测件带来表面损伤和附加误差;
较大的量程范围;
抗干扰能力强;
干 涉 法
操作方便;
在精密测量、精密加工和实时测控的诸多领 域获得广泛应用。
9
第一节 光学面形偏差的检测
分类:
干涉测试技术
按光波 分光方式
按相干光束 传播路径
按用途
干 涉 法
动 态 干 涉
10
分 振 幅 式
分 波 阵 面 式
共 程 干 涉
非 共 程 干 涉
静 态 干 涉
第一节 光学面形偏差的检测
1、干涉的概念
1)相干光 (1)频率相同 (2)位相差恒定 (3)光矢量振动方向相同 (4)光程差小于波列长度
θ
影响干涉条纹对比度的因素 -f 在干涉测量中,采取尽量减小光源尺 a) ②光源大小与空间相干性 b) c) 寸的措施,固然可以提高条纹的对比 图4-3 光阑孔大小对干涉条纹对比度的影响 干涉图样的照度,在很大程度上取决于光源 干 图 4-2 等厚干涉仪中的扩展光源 度,但干涉场的亮度也随之减弱。 的尺寸,而光源的尺寸大小又会对各类干涉 涉 图样对比度有不同的影响 : 当采用激光作为光源时,因为光源上 法
12
1 §4-1 激光干涉测试技术基础 第一节 光学面形偏差的检测
K
在波动光学中,把光通过相干 x 长度所需要的时间称为相干时 1.2 影响干涉条纹对比度的因素 I 间,其实质就是可以产生干涉 ①光源的单色性与时间相干性 的波列持续时间,(其对应产 生干涉的两列波的光程差)。 如图,干涉场中实际见到的条纹是 λ到λ+Δλλ干 λ+Δλ 因此,激光光源的时间相干性 中间所有波长的光干涉条纹叠加的结果。 涉 比普通光源好得多,一般在激 m 0 1 2 3 4 5 6 当λ+Δ λ 的第m 级亮0 1 2 3 4 5 6 法 光干涉仪的设计和使用时不用 λ+Δ 图4-1 各种波长干涉条纹的叠加 考虑其时间相干性。 纹与λ的第m+1级亮纹重
由平行平板产生的等倾干涉,无论多么宽的光源 各点所发出的光束之间有固定的相位 尺寸,其干涉图样都有很好的对比度。 关系,形成的干涉条纹也有固定的分 布,而与光源的尺寸无关。激光光源 杨氏干涉实验只在限制狭缝宽度的情况下,才能 的大小不受限制,激光的空间相干性 看清干涉图样。 比普通光源好得多。 由楔形板产生的等厚干涉图样,则是介于以上两 种情况之间。
干 涉 法
7
第一节 光学面形偏差的检测
历史进程: 1905年,爱因斯坦(Albert Einstein)提出相对论原 理。 1924年,Louis de Broglie推导出de Broglie波方程, 认为所有的运动粒子都具有相应的波长,为隧道显微镜、 原子力显微镜的诞生做了理论准备。 1960年,梅曼(Maiman)研制成功第一台红宝石激光器, 以及微电子技术和计算机技术的飞速发展,使光学干涉 技术的发展进入了快速增长时期。 1982年,G.Binning和H.Rohrer研制成功扫描隧道显微 镜,1986年发明原子力显微镜,从此开始了干涉技术向 纳米、亚纳米分辨率和准确度前进的新时代。
2 2L
干 涉 法
因此,必须用单色光源,使同一光源发出的光束分成两束,且 光程差不能太大。钠光 (100 ~ 200) mm , 激光 (10 ~ 几十米)
11
第一节 光学面形偏差的检测
影响干涉条纹对比度的因素 干涉条纹对比度可定义为 K I max I min
干 涉 法
5
第一节 光学面形偏差的检测
现代干涉技术是物理学理论和当代技术有机结合的产物。 激光、光电探测技术和信号处理技术对于干涉技术的发 展起着重要的作用。 历史进程:
17世纪后半叶,玻意耳(Boyle)和纹(后被称作牛顿 环),人类从此开始注意到了干涉现象。 1690年,惠更斯出版《论光》,提出“波动”说。
光学测量
第三章 光学零部件的基本测量
光学测量
第三章 光学零部件的基本测量
第三章 光学零部件的基本测量
第一节 光学面形偏差的检测
光学测量
第一节 光学面形偏差的检测
4
第一节 光学面形偏差的检测
概述: 光学干涉测试技术最初在光学零件和光学系统 的检验中获得广泛应用。 在光学零件面型、平行度、曲率半径等的测量 中,斐索型干涉测量法与在光学车间广泛应用的 牛顿型干涉测量法(样板法或牛顿型干涉法)相 比,属于非接触测量。
合后,所有亮纹开始重 (m 1) m( ) 合,而在此之前则是彼此分开的。则尚能分辨干 由此得最大干涉级 涉条纹的限度为m = λ/Δλ ,与此相应的尚能产生干涉
条纹的两支相干光的最大光程差(或称光源的相干长度)为
LM
2
13
第一节 光学面形偏差的检测 S r
S0
1704年,牛顿出版《光学》,提出了“微粒”说。 1801年,托马斯· 杨(Thomas Young)完成了著名的杨氏双 缝实验,人们可以有计划、有目的地控制干涉现象。
干 涉 法
6
第一节 光学面形偏差的检测
历史进程: 1818年,阿喇果和菲涅尔发现两个正交的偏振光不能 干涉,导致杨和菲涅尔得出光是横波的结论。 1860年,麦克斯韦(C.Maxwell)的电磁场理论为干涉技 术奠定了坚实的理论基础。 1881年,迈克尔逊(A.Michelson)设计了著名的干涉实 验来测量“以太”漂移,导致“以太”说的破灭和相 对论的诞生。他还首次用干涉仪以镉红谱线与国际米 原器作比对,导致后来用光波长定义“米”。 1900年,普朗克(Max Planck)提出辐射的量子理论, 成为近代物理学的起点。
I max I min
式中,Imax、Imin 分别为静态干涉场中光强的最大值和最小值, 也可以理解为动态干涉场中某点的光强最大值和最小值。
干 涉 法
当 Imin = 0时K=1,对比度有最大值;而当 Imax= Imin时K= 0,条纹消失。在实际应用中,对比度一般都小于1。 对目视干涉仪可以认为:当 K > 0.75 时,对比度就算是好的; 而当K>0.5时,可以算是满意的;当K=0.1时,条纹尚可辨 认,但是已经相当困难的了。 对动态干涉测试系统,对条纹对比度的要求就比较低。