太阳能级多晶硅中B、P杂质的危害及去除
Si基体中掺杂B,P的第一性原理研究
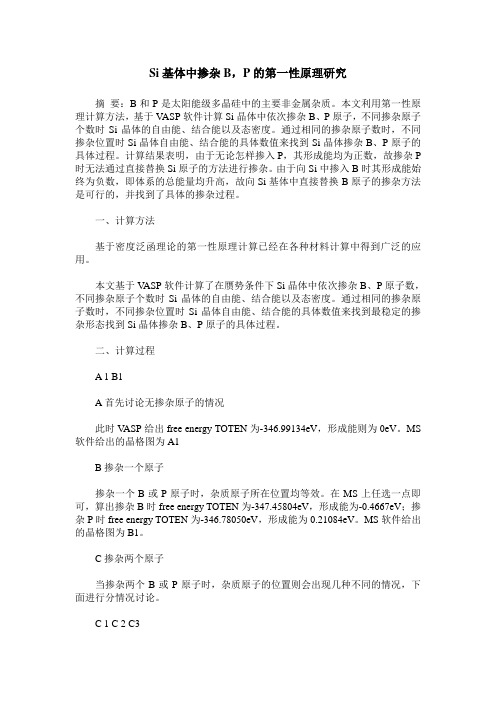
Si基体中掺杂B,P的第一性原理研究摘要:B和P是太阳能级多晶硅中的主要非金属杂质。
本文利用第一性原理计算方法,基于V ASP软件计算Si晶体中依次掺杂B、P原子,不同掺杂原子个数时Si晶体的自由能、结合能以及态密度。
通过相同的掺杂原子数时,不同掺杂位置时Si晶体自由能、结合能的具体数值来找到Si晶体掺杂B、P原子的具体过程。
计算结果表明,由于无论怎样掺入P,其形成能均为正数,故掺杂P 时无法通过直接替换Si原子的方法进行掺杂。
由于向Si中掺入B时其形成能始终为负数,即体系的总能量均升高,故向Si基体中直接替换B原子的掺杂方法是可行的,并找到了具体的掺杂过程。
一、计算方法基于密度泛函理论的第一性原理计算已经在各种材料计算中得到广泛的应用。
本文基于V ASP软件计算了在赝势条件下Si晶体中依次掺杂B、P原子数,不同掺杂原子个数时Si晶体的自由能、结合能以及态密度。
通过相同的掺杂原子数时,不同掺杂位置时Si晶体自由能、结合能的具体数值来找到最稳定的掺杂形态找到Si晶体掺杂B、P原子的具体过程。
二、计算过程A 1 B1A首先讨论无掺杂原子的情况此时V ASP给出free energy TOTEN为-346.99134eV,形成能则为0eV。
MS 软件给出的晶格图为A1B掺杂一个原子掺杂一个B或P原子时,杂质原子所在位置均等效。
在MS上任选一点即可,算出掺杂B时free energy TOTEN为-347.45804eV,形成能为-0.4667eV;掺杂P时free energy TOTEN为-346.78050eV,形成能为0.21084eV。
MS软件给出的晶格图为B1。
C掺杂两个原子当掺杂两个B或P原子时,杂质原子的位置则会出现几种不同的情况,下面进行分情况讨论。
C 1 C 2 C3如图C1,由V ASP算得掺杂B时free energy TOTEN为-347.412888eV,形成能为-0.421548eV;掺杂P时free energy TOTEN为-346.353895eV,形成能为0.637445eV。
太阳能硅片污水处理

太阳能硅片污水处理一、背景介绍太阳能硅片是太阳能电池的核心部件,其制造过程中会产生大量的污水。
这些污水含有有机物、无机盐和重金属等有害物质,如果直接排放到环境中会对水体和生态环境造成严重的污染。
因此,对太阳能硅片污水进行处理是保护环境和可持续发展的重要任务。
二、处理目标1. 去除太阳能硅片污水中的有机物、无机盐和重金属等有害物质。
2. 使处理后的水质达到国家相关标准,可以安全排放或循环利用。
三、处理工艺1. 初级处理:太阳能硅片污水首先经过初级处理,包括沉淀、过滤和调节pH值等步骤。
沉淀过程中,利用化学药剂将悬浮物和部分有机物沉淀下来,过滤则进一步去除悬浮物。
调节pH值可以使后续处理更加有效。
2. 中级处理:初级处理后的污水进入中级处理,主要采用生物处理技术。
通过好氧生物处理和厌氧生物处理,将有机物进一步降解为无害物质。
好氧生物处理利用氧气和特定菌群将有机物氧化分解,厌氧生物处理则在无氧环境下利用厌氧菌群将有机物降解为甲烷和二氧化碳。
3. 高级处理:中级处理后的污水仍然含有一定量的无机盐和重金属等有害物质,需要进行高级处理。
高级处理主要包括吸附、离子交换和膜分离等技术。
吸附技术利用吸附剂吸附污水中的有害物质,离子交换则通过交换树脂将污水中的离子去除,膜分离则利用膜的特殊结构将污水中的有害物质分离出来。
四、处理效果与数据经过上述处理工艺,太阳能硅片污水可以得到有效处理和净化。
处理后的水质达到国家相关标准,可以安全排放或循环利用。
下面是一些处理效果和数据:1. COD(化学需氧量)去除率:达到90%以上。
2. BOD(生化需氧量)去除率:达到95%以上。
3. 悬浮物去除率:达到98%以上。
4. 重金属去除率:达到90%以上。
5. pH值调节范围:6.5-8.5。
6. 循环利用率:达到80%以上。
五、处理设备和成本太阳能硅片污水处理需要一系列的处理设备和设施,包括沉淀池、过滤器、生物反应器、吸附柱、离子交换柱和膜分离装置等。
多晶硅制备过程质量的影响因素

多晶硅制备过程质量的影响因素1、气流速度的影响硅棒表面的气流速度会影响多晶硅表面沉积的均匀程度,同时也会影响硅棒表面热的扩散、粘滞层的厚度,所以将硅棒表面的气体流速控制在合理范围十分重要。
当气体流速能够达到需要的沉积速率时,炉产量会随着混合气流量的增大而增高。
流量的大小和还原炉的结构及大小有关,载体表面积与硅芯面积的比值越大,就越会增加气体对沉积面的碰撞,良率就会得到有效提高。
2、三氯氢硅的影响在目前多晶硅产品的生产过程中,对于太阳能级多晶硅原料之一的三氯氢硅的使用含量还没有一个具体的标准和数据。
但是对于其中存在的杂质,大部分企业都要求B<0.1ppbw、P<1ppbw、Fe<50ppbw、C<1ppmw。
而假如要是多晶硅中P、B的含量较高,其就会高温环境下产生P、B析出的副反应,而析出的P、B又会粘附在多晶硅上,这会大幅度的影响多晶硅的电阻率。
在多晶硅生产时,有关物质和P、B等杂质所产生的反应属于气相反应。
由于生产过程中P、B、As、Sb 等物质会漂浮在气相之中,而其他一部分反应炉内部的重金属物质也会漂浮在气相之中,当SiHCl3、H2等物质扩散至载体上时,可能会把这部分杂质带到载体之上,这对于多晶硅的品质有着很大的影响。
3、氢气的影响通过有关研究发现,由于氢气中会含有一定程度的氧和水汽,在含氧量大于20ppm,露点大于-30℃的环境下,就会出现水解或者氧化反应,这样一来,就会生成一种二氯化硅氧化层粘附在多晶硅之上,在这种被氧化的多晶硅继续沉淀时,就形成了氧化夹层。
这种夹层在光照的环境下可以看到多种多样的色彩,而且酸洗手段而不能去除这种氧化夹层。
与此同时,具有氧化夹层的硅棒在真空环境下生长单晶硅的过程中,可能会出现硅跳情况,而通常见到的状况就是熔区表面的废渣较多,导致多次引晶不成功等问题。
4、炉内温度的影响实践证明在900~1000℃间,SiHCl3以热分解为主,1080~1200℃间以还原反应为主,1200℃以上副反应、逆反应同时发生。
多晶硅的制备及其缺陷和杂质

第四章多晶硅的制备及其缺陷和杂质近年来围绕太阳能级硅制备的新工艺、新技术及设备等方面的研究非常的活跃,并出现了许多研究上的新成果和技术上的突破,那么到现在为止研究的比较多且已经产业化或者今后很有可能产业化的廉价太阳能级硅制备新工艺主要是以下几种:4.1 冶金级硅的制备硅是自然界分布最广泛的元素之一,是介于金属和非金属之间的半金属。
在自然界中,硅主要是以氧化硅和硅酸盐的形态存在。
以硅石和碳质还原剂等为原料经碳热还原法生产的含硅97%以上的产品,在我国通称为工业硅或冶金级硅[1, 2]。
在工业硅生产中,是以硅石为原料,在电弧炉中采用碳热还原的方式生产冶金级硅。
冶金级硅的杂质含量一般都比较得高。
冶金级硅一般用于如下3个方面[2]:(1)杂质比较高一点的冶金级硅一般用来生产合金,如硅铁合金、硅铝合金等,这部分约消耗了硅总量的55%以上;(2)杂质比较低一点的冶金级硅一般用于在有机硅生产方面,这一部分将近消耗了硅总量的40%;(3)剩下的5%经过进一步提纯后用来生产光纤、多晶硅、单晶硅等通讯、半导体器件和太阳能电池。
以上三个方面中,其产品附加值各有不同,其中最后的一部分所产生的附加值最大。
1冶金级硅生产工艺目前国内外的工业硅生产,大多是以硅石为原料,碳质原料为还原剂,用电炉进行熔炼。
不同规模的工业硅企业生产的机械化自动化程度相差很大。
大型企业大都采用大容量电炉,原料准备、配料、向炉内加料、电机压放等的机械化自动化程度高、还有都有独立的烟气净化系统。
中小型企业的电炉容量较小,原料准备和配料等过程比较简单,除采用部分破碎筛分机械外,不少过程,如配料,运料和向炉内加料等都是靠手工作业完成。
无论大型企业还是中小型企业,生产的工艺过程都可大体分为原料准备、配料、熔炼、出炉铸锭和产品包装等几个部分,如图4-1所示为工业硅的生产工艺流程图[3]。
工业硅生产过程中一般要做好以下几个方面。
(1)经常观察炉况,及时调整配料比,保持适宜的SiO2与碳的分子比,适宜的物料粒度和混匀程度,可防止过多的SiC生成。
工业硅中杂质P的强化析出及湿法去除研究

工业硅中杂质P的强化析出及湿法去除研究摘要:湿法提纯是冶金法制备太阳能级多晶硅技术路线中的预处理过程,即通过湿法酸浸对工业硅进行初步提纯,具备除杂效果明显、设备简单、可规模化操作等优势。
但湿法浸出对硅中非金属杂质P的去除效果很低,这与其在硅中的赋存形态有关。
关键词:工业硅杂质P;强化析出;湿法去除引言在传统化石能源日益枯竭及全球气候变化问题日益凸显的大背景下,保护环境、节能减排的呼声日益高涨,可再生能源的开发利用成为未来的必然趋势,国际社会普遍开始重视发展可再生能源,各国纷纷采取有效措施鼓励可再生能源产业的发展。
《巴黎协定》于2016年11月4日正式生效,凸显了人类在应对气候变化方面的决心。
1工业硅的生产工业硅是以硅石(石英砂)为原料,以碳质材料为还原剂,在矿热炉内冶炼得到。
矿热炉又称之为埋弧炉,其结构是一个带有耐火材料的炉膛,采用3根电极,通电时电极之间以及电极与炉底之间产生电流的电弧,产生高温,使电极周围的硅石与碳质还原剂发生化学反应,生成单质硅。
通常可选用木炭、石油焦、煤等还原剂将金属硅从硅石中还原出来。
将硅石与碳质还原剂按一定比例均匀混合送入矿热炉内,在高温下进行还原反应。
其化学反应式如下:反应后形成的单质硅呈液态,聚集在炉底,聚集到一定量后,将出硅口捣开,硅液沿着出硅口流出到抬包内。
生产得到的工业硅纯度在98%}99%之间,杂质来源主要是硅石和碳素材料(包括石油焦、精煤碳素电极等)。
一般而言,工业硅中杂质主要有非金属元素B,P,C,O以及金属元素Fe.Al,Ca.Mn.Ti.V.Cu,Cr等。
根据杂质在冶金硅中的存在形态不同,可以将其分为两类:一为固溶类杂质,这些杂质元素一般以取代硅原子或充填间隙位置为主,主要包括B,P以及微量溶解于硅中的金属杂质;二为偏析类杂质,这类杂质元素一般以化合物的形式偏析于硅晶界处,主要包括Fe.Al.Ca,Ti:V.Cu.Cr等金属类杂质,以及C,O等非金属杂质:金属类杂质因其在硅中的分凝系数较小,大多以合金化合物形式聚集偏析,而C,O则主要以Si02,SiC、金属盐的形存在。
多晶硅风险辨识与评价

多晶硅风险辨识与评价多晶硅是一种广泛应用于光伏领域的材料,具有优良的光电性能和较低的成本。
然而,作为一种新兴材料,多晶硅也存在一些风险和挑战,需要进行风险辨识与评价。
本文将从多个方面对多晶硅的风险进行分析,帮助人们更好地认识多晶硅材料。
首先,多晶硅的生产过程中存在一定的环境污染风险。
在多晶硅的生产过程中,会产生大量的废水、废气和废渣,其中含有一定量的有害物质,如氟化物、二氧化硅等。
如果这些废物没有得到有效处理和处理,将会对环境造成一定程度的污染和破坏。
因此,多晶硅生产企业需要采取合理的环境保护措施,确保废物得到有效处理和处置,以减少环境污染的风险。
其次,多晶硅的生产过程中存在一定的安全风险。
多晶硅的生产过程中涉及到高温、高压、化学品等危险因素,如果不严格按照相关的安全操作规程进行操作,可能会引发火灾、爆炸等事故,给员工生命安全和财产造成严重损失。
因此,多晶硅生产企业需要建立完善的安全管理体系,对员工进行安全培训,加强现场安全巡查,确保生产过程的安全性。
另外,多晶硅的生产过程中存在一定的质量风险。
多晶硅的质量直接影响到光伏电池的性能和寿命,如果多晶硅材料的质量不达标,会导致光伏电池的功率降低、寿命缩短,进而影响整个光伏系统的发电效率和可靠性。
因此,多晶硅生产企业需要建立完善的质量管理体系,严格按照相关的质量标准进行生产和检验,确保多晶硅材料的质量稳定和可靠。
总之,多晶硅作为一种应用广泛的光伏材料,具有优良的光电性能和较低的成本,但同时也存在一定的风险和挑战。
企业需要认识到这些风险,并采取相应的措施进行风险管理和控制。
只有合理评价和管理这些风险,才能更好地推动多晶硅材料的应用和发展。
最后,通过加强政府监管和企业自律,提高多晶硅材料的生产和应用水平,进一步降低风险,实现多晶硅材料的可持续发展。
多晶硅的危害介绍

2010/9/1 9:09:38近年,尤其是 2007年以来,我国多晶硅产业有着迅猛的发展。
1000 t 以上级别多晶 硅生产装置陆续建成。
多晶硅的危害主要在其生产过程中有氢气、液氯、三氯氢硅等有害物质生成,生产过程中又存在火灾、爆炸、中毒、窒息、触电伤害等诸多危险因素。
多晶硅生产过程中主要危险、 有害物质中氯气、氢气、三氯氢硅、氯化氢等主要危险特性有: 1) 氢气:与空气混合能形成爆炸性混合物,遇热或明火即会发生爆炸。
气体比空气轻,在 室内使用和储存时,漏气上升滞留屋顶不易排岀,遇火星会引起爆炸。
氢气与氟、氯、溴等卤素 会剧烈反应。
2) 氧气:易燃物、可燃物燃烧爆炸的基本要素之一,能氧化大多数活性物质。
与易燃物(如乙炔、甲烷等)形成有爆炸性的混合物。
3) 氯:有刺激性气味,能与许多化学品发生爆炸或生成爆炸性物质。
几乎对金属和非金属 都起腐蚀作用。
属高毒类。
是一种强烈的刺激性气体。
4) 氯化氢:无水氯化氢无腐蚀性, 但遇水时有强腐蚀性。
能与一些活性金属粉末发生反应, 放岀氢气。
遇氰化物能产生剧毒的氰化氢气体。
5) 三氯氢硅:遇明火强烈燃烧。
受高热分解产生有毒的氯化物气体。
与氧化剂发生反应, 有燃烧危险。
极易挥发,在空气中发烟,遇水或水蒸气能产生热和有毒的腐蚀性烟雾。
燃烧 解)产物:氯化氢、氧化硅。
6) 四氯化硅:受热或遇水分解放热,放岀有毒的腐蚀性烟气。
7) 氢氟酸:腐蚀性极强。
遇H 发泡剂立即燃烧。
能与普通金属发生反应 ,放岀氢气而与空气形成爆炸性混合物。
8) 硝酸:具有强氧化性。
与易燃物 (如苯)和有机物(如糖、纤维素等)接触会发生剧烈反应,甚至引起燃烧。
与碱金属能发生剧烈反应。
具有强腐蚀性。
9) 氮气:若遇高热,容器内压增大。
有开裂和爆炸的危险。
10) 氟化氢:腐蚀性极强。
若遇高热,容器内压增大,有开裂和爆炸的危险。
11) 氢氧化钠:本品不燃 ,具强腐蚀性、强刺激性,可致人体灼伤。
火灾、爆炸、中毒是多晶硅项目在生产中的主要危险、有害因素,另外,还存在触电、机械 伤害、腐蚀、粉尘等危险、有害因素。
太阳能级多晶硅生产工艺及污染防治措施

太阳能级多晶硅生产工艺及污染防治措施关键词:多晶硅生产工艺污染防治多晶硅可以直接用于太阳能电池及单晶硅的原料,在当今原料运用中具有重要意义,在人工智能、信息处理、操作控制等方面占据着基础的重要地位。
一些科技发达的国家如美国、日本等长期以来都采用市场垄断和技术封锁等手段控制多晶硅的使用和销售,而我国90%以上的多晶硅只能靠进口,面临着严重缺货、供不应求的发展和利用问题。
为了适应市场环境的发展需求,针对我国面临的现状必须采取一定的措施,加大对多晶硅生产的技术投入和执行力度,同时还必须保证不加重对周围环境的污染,提高污染防治措施的决策性和执行力度[1]。
一、生产工艺以及污染源分析1.生产工艺流程首先将结晶硅原材料粉碎直至成为粉状后,用含31%的盐酸洗涤,完成后再用水洗尽酸。
将其甩干后进行数控冶炼将其炼化,炼化过程中加入氩气,两次进行物理分凝后直至冷却,则可完成多晶硅产品的制作。
2.流程中的污染分析2.1在工艺生产的流程中,废水主要来源于水的洗涤上。
未回收的氯硅烷低沸物和氯化氢、还原炉开关的置换尾气等,各种工艺废气处理后产生了很多酸性废水。
这些废水的很大组成成分都是多晶硅的生产废水,一般来说,多晶硅废水的主要污染物是盐酸以及氯硅烷水解后产生的sio2等等,机械处理以后这些废水会沿着管道排出,进入废水处理站的调节池。
还有纯水的制备产生的排污水,包含的污染物主要是氯化物。
此外,还有硅芯和检验棒腐蚀物的洗涤废水,其中包含了硝酸、钠盐、氢氟酸等污染物,一并流入废水处理站进行处理[2]。
2.2本项目中废气主要污染源为工艺废气及工艺粉尘。
酸洗过程中通常会产生一定的酸雾,表面积约为1m2,此道工序需使用31%的盐酸,温度大概保持在30°c左右。
酸洗过程中会产生酸性废气hcl污染物,酸洗工序8小时/天。
按照这个速度,全年污染物的挥发量也都在可控制的范围内,因此对周围的环境污染影响会较小。
2.3生产多晶硅的工序中产生固体废弃物主要包括:在水洗涤过程中筛选的不合格的原料、其他一些杂工段出现的含有硅的杂质,每天排出的数量约为1200kg[3]。
- 1、下载文档前请自行甄别文档内容的完整性,平台不提供额外的编辑、内容补充、找答案等附加服务。
- 2、"仅部分预览"的文档,不可在线预览部分如存在完整性等问题,可反馈申请退款(可完整预览的文档不适用该条件!)。
- 3、如文档侵犯您的权益,请联系客服反馈,我们会尽快为您处理(人工客服工作时间:9:00-18:30)。
太阳能级多晶硅中B、P杂质的危害及去除李光明;刘龙;栾石林;李雷;赵恒利;何京鸿【摘要】介绍B、P对太阳电池性能的影响,综述当前去除B、P的主要方法与技术,分析各自的优点及不足,并对其以后的发展趋势做简要分析.【期刊名称】《太阳能》【年(卷),期】2016(000)008【总页数】4页(P26-28,25)【关键词】多晶硅;B;P;提纯【作者】李光明;刘龙;栾石林;李雷;赵恒利;何京鸿【作者单位】云南冶金新能源股份有限公司;常州天合光伏发电系统有限公司;云南冶金新能源股份有限公司;常州天合光伏发电系统有限公司;云南冶金新能源股份有限公司;常州天合光伏发电系统有限公司;楚雄师范学院物理与电子科学学院;楚雄师范学院物理与电子科学学院;楚雄师范学院物理与电子科学学院【正文语种】中文在能源短缺及环境污染的双重压力下,因太阳能资源丰富、应用广泛、绿色、可再生,近十年以太阳能利用形成的产业链(硅料、硅片、太阳电池、组件、系统应用及辅材)得到了快速发展,硅料的需求也日益增加。
多晶硅按纯度可分为冶金级硅(MG&工业级)、太阳能级硅(SG)、电子级硅(EG),其中,太阳能级硅的含Si 为99.99%~99.9999%(4~6个9)[1]。
多晶硅的纯度会直接影响到太阳电池的转换效率及电池寿命。
多晶硅生产中的主要杂质有Fe、Ni、Cu、Zn、Al、Ga、B、P、Cr、C等,其中B、P杂质是生产中很难去除的两种杂质,这两种杂质残留在多晶硅中会作为复合中心降低少数载流子寿命,影响太阳电池的转换效率[2]。
目前B、P杂质去除困难大、成本高,已成为高效晶体硅太阳电池发展的技术阻力。
因此,研究多晶硅生产中B、P杂质的去除方法、工艺技术,从而获得低成本、高纯度的多晶硅材料,以保障高效晶体硅太阳电池的高效、可靠、稳定性,具有重要的意义[3]。
原料硅石中原有的及在工业硅生产过程中大量使用的碳素材料是多晶硅中杂质元素B、P的主要来源[4]。
根据B、P电子排布结构,B、P杂质在异质结中对少数载流子有很强的复合能力,B表现为易吸附一个电子,P表现为易复合一个空穴。
在多晶硅材料制备过程中,这两种杂质会成为光生少数载流子的复合中心,容易诱导晶体产生缺陷,会降低少数载流子的寿命,严重影响太阳电池光电转换效率[5]。
对多晶硅的生产企业而言,多晶硅产品中B、P等杂质约为原料SiHCl3中B、P元素的4.8倍[6],为获得高质量的多晶硅材料,企业在生产过程中必须严格控制原料(SiHCl3)中B、P等杂质元素的含量[7],其中,B、P杂质在原料(SiHCl3)中的质量分数分别要求为1×10-7、5×10-8。
目前,大部分生产企业的原料粗品(SiHCl3)中含B、P质量分数一般在2×10-7~4×10-7。
多晶硅生产工艺技术主要有改良西门子法(Siemens)、流化床法(FBR)、硅烷法、气液沉积法(VLD)、冶金法、锌还原法等。
其中,改良西门子法技术最为成熟,可实现物料完全闭路循环生产,是目前的主流工艺,其产能约占全球总产能80%以上[8]。
该技术主要包括以下几大重要工序:SiHCl3合成、分离提纯、SiHCl3氢还原或分解、SiCl4的氢化、还原尾气分离与回收,其中,分离提纯工序是使SiHCl3中的每一种受控杂质含量均符合要求[9]。
精制SiHCl3常用的方法有精馏法和树脂吸附法。
2.1 精馏法精馏法是利用混合物内各组分的挥发度(沸点)不同,在塔顶液相回流和塔釜气相回流的作用下,气液两相逐级逐板逆向接触,进行多次部分汽化和部分冷凝,液相中的轻组分不断转移至气相中而上升到塔顶,气相中的重组分不断转移至液相中而下降到塔底,分别得到较纯的轻组分和重组分,从而达到分离的目的。
SiHCl3合成混合液中含有主产品(SiHCl3)、副产品(SiCl4、SiH2Cl2)、氢化物或氯化物杂质。
在精馏提纯工序,主产品、副产品及杂质被分离、去除,精馏工序中的装置及工业技术的设计先进性、操控精准水平将直接影响到多晶硅产品的质量和企业利润[10]。
2.1.1 精馏塔的改进精馏塔是SiHCl3提纯的主要设备,精馏塔设计和制作中,材料材质、塔板类型的选择及动力保证是获得高纯SiHCl3的基础及关键。
工业生产中,制作精馏塔的材料多采用1Cr18Ni9Ti不锈钢,该种材料易受氯离子腐蚀,会导致SiHCl3中Fe、Ni、Cr等金属杂质含量增多,且改材料价格也偏高。
近年来国内也有选用超低碳不锈钢、聚四氟乙烯材料制作精馏塔[11],但采用全四氟材料和四氟衬里材料的精馏塔,受其经济性、制作工艺、机械强度及可靠性等因素的影响,难以推广应用。
为改进精馏塔,使其在经济性、工艺、机械强度、抗腐蚀性等方面均有一定优越性,在不锈钢精馏塔内表面喷涂氟塑料46(F-46)是较好的解决方法[12]。
峨眉半导体材料研究所[13]对柱孔板、穿流筛板、溢流浮动板的理论效率进行了测定,得出柱孔塔板、穿流筛板、溢流浮动板的理论效率分别为85%~92%、65%~68%、94%~98%。
其中,溢流浮动板的效率及操作范围都略优于另外两种,但这种塔板的安装精度要求较高。
此外,采用聚四氟乙烯材料制作的溢流浮动板(四氟浮动板)在长期工作中易变形,会使浮动板不能正常工作,造成板效率下降;而采用聚四氟乙烯制作的柱孔板,在运行过程中,变形的概率较四氟浮动板低。
综合对比,采用四氟乙烯制作的柱孔板更有优势。
陈文等[14]经过理论优化及使用高效导向筛板精馏塔,实现产品质量的大幅度提高,B的含量降到极低。
黄国强等[15]发明了一种去除氯硅烷体系中B杂质的隔板吸附装置及方法,由一个与塔式吸附段高度相同、置于塔中部的隔板将该装置分为4个区域。
这种方法较以往的除B 工艺流程大为简化,大幅降低了能耗和设备费用,对B杂质的去除率达到80%。
2.1.2 精馏工艺改良西门子法(Siemens)生产多晶硅,在精馏提纯工序,SiHCl3混合液在高温水汽环境下会生成高沸点的B、P及金属络合物,通过控制精馏塔温度,这些高沸点杂质在塔顶分离出去。
除该方法反应是在气液两相间进行的,还需1台精馏塔、2台以上的沉淀槽,精馏塔作为反应器分离生成的高沸物,沉淀槽沉淀去除反应生成的固体杂质。
为解决上述提纯方法中所需精馏塔、容器较多,设备投资大,提纯效果欠佳的问题,唐前正等[16]用冶金级硅粉与HCl气体在高温环境下反应,制得SiHCl3混合物,经干法除尘、与湿气反应、通入或喷淋SiCl4液,得到液相1和气相1,气相1进入分离器,用SiCl4液体洗涤,分离得到净化后的SiHCl3合成气体和液相2。
该项发明利用了SiHCl3合成产物呈气态的特点,B、P杂质(硼、磷络合物)的去除可在气相中进行。
该工艺具有反应物能充分接触,反应迅速、充分的特点,干净的SiCl4冷凝洗涤络合反应物,有利于降低气相中生成物的浓度。
该发明因工艺简单、部分可高效循环利用,具有成本较低的优势。
刘田根等[17]对SiHCl3精馏过程进行多塔除轻、除重,并采用加压的分离方式,使B、P含量降至极低。
黄和明等[18]将合成的SiHCl3投入精馏塔(进口316 L材质制作)中,温度控制在31.5~32.5 ℃,让SiHCl3在双塔连续精馏釜中回流,按13:1~17:1回流比截留产品,保留18%~21%(质量分数)的低沸物,并在SiHCl3冷却时补充氢气,保持恒温恒压,也可得到高纯SiHCl3液体产品。
Leslaw等[19]研究表明,在SiHCl3合成气冷凝液时,循环系统中存在一些AlCl3粒子有利于杂质的去除,通过控制粒子(AlCl3)质量分数(一般控制在0.1‰),除杂率可达98%以上。
G·哥蒂[20]通过加入C13H12N4S(二苯基硫卡巴腙) 或C19H15Cl(三苯基氯代甲烷),B杂质(BCl3)和其他金属络合物会形成高沸点络合物,经第一塔蒸馏后,B杂质和其他金属杂质一起作为底馏分分离出去,第一塔蒸馏后的顶馏分进入第二塔蒸馏,蒸馏后的顶馏分为高纯SiHCl3,底馏分为第一塔残留的络合物杂质。
Tzou[21]选用有机或无机氟化物作为吸附剂,先将粗SiHCl3在室温下与络合氟盐吸附剂接触,再精馏除B,通过控制吸附剂与杂质的物质的量比(1∶1),精馏馏出液中含B杂质含量可降至1×10-10以下。
小柳信一郎等[22]先在SiHCl3合成气冷凝液中添加沸点高于馏出液的醚类化合物后再精馏,同时控制醚中水的质量分数(1%以内),防止SiHCl3产品水解。
该方法可使塔顶馏出液中的B、P等杂质的质量分数降至1×10-9以下。
2.2 树脂吸附法树脂吸附法除B、P杂质是利用杂质化合物(BCl3、PCl3)各组分化学键极性不同来进行吸附分离,以达到提纯效果。
新型树脂材料对BCl3、PCl3具有特殊的吸附性能,是一种很好的吸附材料。
这种除杂方法,设备少、工艺简单、除杂效率高、运行稳定,通过控制吸附塔运行温度、压力及SiHCl3进入吸附塔流量,SiHCl3中的B、P杂质总含量可降到3×10-8以下。
但长期运行后,树脂达到饱和,必须返厂再生,会增加成本[7]。
为提高除杂质量、降低成本,业内将精馏法与树脂吸附法组合使用,精馏可以去除沸点与主含量差异大的杂质,树脂吸附法用于去除沸点差异较小的杂质,除杂效果明显。
近年来,众多研究者对多晶硅工艺中去除B、P的方法进行了广泛的研究,大多集中于精馏法,通过精馏装置及工艺的优化,不同程度地降低了B、P的含量。
这种方法使用设备较多,操作较为复杂且存在人为因素,除B、P效果不稳定,成本昂贵。
而树脂吸附法工艺流程短,操作简单,除B、P效果稳定,具有很大的应用前景。
精馏法和树脂吸附法虽然都在一定程度上降低了B、P的含量,但成本很高,要寻求一个既经济又有效的方法,还有待进一步研究。
【相关文献】[1] 钟根香, 周浪, 周潘兵, 等. 定向凝固多晶硅的结晶组织及晶体缺陷与杂质研究[J]. 材料导报, 2008, 22(12): 14-18.[2] 蔡靖, 陈朝, 罗学涛. 高纯冶金硅除硼的研究进展[J]. 材料导报, 2009, 23(12): 81-84.[3] 何念银, 艾韬, 周建, 等. 太阳能级硅中硼磷的去除[J]. 化学世界, 增刊: 107-107.[4] 郎永沛, 储少军, 林俊峰. 多晶硅中杂质元素B、P的来源分析[J]. 铁合金, 2011, (5): 11-13.[5] 邓海, 杨德仁. 铸造多晶硅中杂质对少子寿命的影响[J]. 太阳能学报, 2007, 28(2): 152-154.[6] 杨亚君, 臧丹伟. 高纯三氯氢硅精制技术改造[J]. 化学工业与工程, 2009, 26(6): 532-534.[7] 聂少林, 汤忠科, 肖建辉, 等. 2种除三氯氢硅中硼、磷工艺的比较[J]. 氯碱工业, 2010, 46(11): 31-32.[8] 易正义. 改良西门子法仍将维持主导地位[N]. 中国电子报, 2009, 第004版: 1-1.[9] 徐远志. 改良西门子法制备工艺及其生产技术现状[J]. 云南冶金, 2011, 40(1): 52-55.[10] 张开仕. 三氯氢硅的生产技术与研究进展[J]. 无机盐工业, 2011, 43(8): 11-13.[11] 峨眉半导体材料研究所第一研究室多晶组. 高纯多晶硅的制取[J]. 稀有金属, 1979, (6): 8-18.[12] 赵敏. 关于提高和稳定多晶硅质量的几点设想[J]. 中国有色冶金, 1981, (1): 19-20.[13] 峨眉半导体材料研究所第一研究室多晶组. 高纯多晶硅的制取[J]. 稀有金属, 1979, (6): 8-18.[14] 陈文, 徐昱, 陈位强, 等. 三氯氢硅精馏新过程的研究及其节能降耗的应用[J]. 化工进展, 2009, 28(增刊): 297-300.[15] 黄国强, 石秋玲, 王红星, 等. 去除氯硅烷体系中硼杂质的隔板吸附装置及方法[P]. 中国:CN102058992, 2011-05-18.[16] 唐前正, 何劲, 李钊, 等. 改良西门子法生产多晶硅工艺中除硼、磷的方法[P]. 中国:CN101759186, 2010-06-30.[17] 刘田根. 三氯氢硅加压提纯法[J]. 江西化工, 2011, (3): 163.[18] 黄和明, 赵产奎, 夏建保. 一种三氯氢硅提纯方法[P]. 中国: CN101045536, 2007-10-03.[19] A ndreas B, Rainer W, Leslaw M, et al. Method for producing tri-chlorosilane[P]. 美国: US7056484, 2006-06-06.[20] G·哥蒂. 提纯三氯硅烷和四氯化硅的方法和设备[P]. 中国: CN101065324, 2007-10-31.[21] Tzou M S. Phosphorous removal from chlorosilane[P]. 美国: US5723644, 1998-03-03.[22] 小柳信一郎, 井関祐二. クロロミテソ類の精制方法[P].日本: JP 067919, 2005-03-17.。