塑胶模具的设计与制造
注塑模具的设计及制造

注塑模具的设计及制造注塑模具是用于注塑成型的模具,它的设计和制造直接关系到产品质量和生产效率。
本文将从设计和制造两个方面介绍注塑模具的相关知识。
一、注塑模具的设计1.产品设计分析:在进行注塑模具设计之前,首先要对即将生产的产品进行分析。
了解产品的形态尺寸、材料特性、注塑工艺和生产要求等,为模具设计提供依据。
2.模具结构设计:根据产品要求和注塑工艺,设计模具的结构。
包括模具的开合方式、定位方式、注塑道设计和冷却系统设计等。
合理的结构设计可以提高模具使用寿命和生产效率。
3.模具零件设计:根据模具结构设计,对各个零件进行详细设计。
比如模具芯、模具腔、滑块、顶出机构、定位销和定位套等。
零件设计要考虑到材料选择、加工工艺和装配要求等。
4.模具标准件选用:在模具设计过程中,可以选用一些标准件,如模具基础板、导向套和注塑嘴等。
合理选用标准件不仅可以减少设计工作量,还可以提高模具加工精度和降低成本。
5.注塑模具的通气设计:在注塑过程中,模具内会产生大量的气体,如果不能有效排出,会导致产品缺陷。
所以,在模具设计中要合理设置通气孔和排气槽,以确保注塑过程的质量。
二、注塑模具的制造1.模具材料选择:注塑模具常用的材料有优质合金钢和工具钢,比如P20、718、2738等。
材料的选择要根据产品要求、生产批量和制造成本等因素综合考虑。
2.模具加工工艺:注塑模具的加工工艺包括铣削、镗削、磨削、电火花和线切割等。
不同的加工工艺需要选用不同的设备和工装,操作人员要熟悉模具加工过程和技术要求。
3.模具热处理:模具在使用过程中需要经过热处理,以提高材料的硬度和耐磨性。
常见的热处理方法有淬火、回火和表面处理等,要根据模具材料和要求选择适当的热处理方法。
4.模具组装和调试:在模具制造完成后,需要对各个零部件进行组装和调试。
确保模具各部件的精度和配合度,在注塑生产前进行试模和修正,以保证产品质量。
总之,注塑模具的设计和制造对于提高注塑产品的质量和生产效率至关重要。
塑胶模具开发设计的最常见方法及工艺三篇.doc
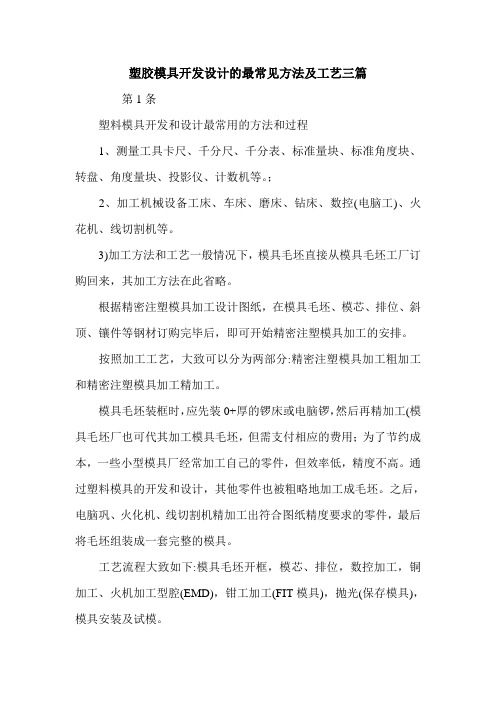
塑胶模具开发设计的最常见方法及工艺三篇第1条塑料模具开发和设计最常用的方法和过程1、测量工具卡尺、千分尺、千分表、标准量块、标准角度块、转盘、角度量块、投影仪、计数机等。
;2、加工机械设备工床、车床、磨床、钻床、数控(电脑工)、火花机、线切割机等。
3)加工方法和工艺一般情况下,模具毛坯直接从模具毛坯工厂订购回来,其加工方法在此省略。
根据精密注塑模具加工设计图纸,在模具毛坯、模芯、排位、斜顶、镶件等钢材订购完毕后,即可开始精密注塑模具加工的安排。
按照加工工艺,大致可以分为两部分:精密注塑模具加工粗加工和精密注塑模具加工精加工。
模具毛坯装框时,应先装0+厚的锣床或电脑锣,然后再精加工(模具毛坯厂也可代其加工模具毛坯,但需支付相应的费用;为了节约成本,一些小型模具厂经常加工自己的零件,但效率低,精度不高。
通过塑料模具的开发和设计,其他零件也被粗略地加工成毛坯。
之后,电脑巩、火化机、线切割机精加工出符合图纸精度要求的零件,最后将毛坯组装成一套完整的模具。
工艺流程大致如下:模具毛坯开框,模芯、排位,数控加工,铜加工、火机加工型腔(EMD),钳工加工(FIT模具),抛光(保存模具),模具安装及试模。
在实际制造中,几种塑料模具的开发、设计和加工技术相互交织,需要塑料模具开发设计人员和模具大师来安排各个环节。
一个步骤出错,所有的锅都是负面返工,这通常会导致模具损坏。
成品精密注塑模具加工不美观。
如果要补救,只能改变,这会增加时间和成本,而且大多数时间是最重要的。
目前,精密注塑模具加工行业的竞争非常激烈。
客户非常渴望给模具室时间,不能按时交付模具。
最终,他们将失去对客户的各种加工机械和设备功能的简要介绍。
1、工床,用于手工铣削、切削较简单形状的工件、规则,如直线、斜线;通常用于加工精度较低的工件,如毛坯开口、模芯、线开口等。
2、车床,主要用于圆形工件加工,如泵送喷嘴、定位环、法兰、圆形模具(CORE)、圆形铜等。
;精度可以达到更高的要求。
塑胶模具的设计及制造

內容綱要一.塑模產品介紹.二.塑模結構介紹.三.塑模常用材質介紹.四.塑膠模具制造流程.五.塑模設計.六.塑模加工.七.模仁拋光與咬花.八.模具組立及模仁的表面處理.九.模具試模.十.模具移轉.一.塑模產品介紹.1.塑件產品的划分.2.主要承制的產品介紹.1.1 塑件產品的划分1.2 主要承制的產品介紹二. 塑膠模具結構介紹1.常用模座結構介紹.2.模具機構介紹.3.模具動作的原理.2.1 常用模座結構介紹二板模2.1 常用模座結構介紹三板模2.1 常用模座結構介紹熱澆道模具2.2 模具機構介紹a. 澆口的形式介紹.b. 抽芯機構的型式介紹.c. 頂出及回位裝置的介紹.d. 冷卻水道的設置.2.2-a 澆口的型式介紹一.直接進澆與針點式進澆2.2-a 澆口的型式及優缺點介紹二.側邊進澆.2.2-a 澆口的型式及優缺點介紹三.潛伏式進澆.2.2-b 抽芯機構的型式介紹滑塊抽芯2.2-b 抽芯機構的型式介紹2.2-b 抽芯機構的型式介紹2.2-c 頂出及回位裝置的介紹一.頂針頂出二.頂出塊頂出此側壁太深頂出塊(1) 成品的側壁太深時.(2) 框架狀成品且不易排頂針時.三.延遲頂出頂出及回位裝置的介紹2.2-c四.急回機構2.2-d 冷卻水道的設置(a)(b)(d) (c)冷卻水道的設置形式二板模動作原理(1)公模側在成型機的拉動下與母模側分開,分開到設定距離時停止不動.(2)在成型機脊桿地推動下,頂出板帶動頂出機構將成品頂出.(3)在成型機地推動下,公模側向母模側運動,公母模完全合緊後,成型機上的噴嘴與模具上的注口襯套密合,開始注塑.三板模動作原理(1) 母模板隨著公模板一起向後運動,運動到設定距離時,被小拉桿限位塊擋住,由于母模板隨注塑機繼續向後運動,這樣小拉桿也被帶動,它又帶動剝料板運動將料頭打下.(2)成型機繼續向後運動,拉力不斷增大,超過開閉器鎖緊力.母模板與公模板分開.(3)在脊桿地推動下,頂出板帶動頂出機構(頂針,頂桿,斜稍)開始頂出運動,將成品頂出(4)在成型機地推動下,公模側向母模側運動,公模板壓向母模板和剝料板,最後完全合緊,成型機上的噴嘴與模具上的注口襯套密合,開始注塑.PCEG DT(II)塑模廠三.模具常用材質介紹.1.常用塑膠材質介紹.2.常用模仁材質介紹.3.1 常用塑膠材質介紹塑膠類型名稱主要性能成型工藝性ABS 易於成型和機械加工.具有優良的物理機械性能和低溫抗衝擊性,電性能,耐磨性,尺寸穩定性,耐化學性,染色性等.ABS具有優良的流動性能和良好的綜合性能.PC/ABS由于PC/ABS是ABS和PC混合而成的.因此,PC/ABS不但具有PC的優良的韌性,极佳的光澤性,還具有ABS優良的加工性能.流動性也優于PC,另外由于PC良好的耐燃性能,PC/ABS具有ABS所沒有耐燃性能.PC/ABS的熔體粘度相對來說小于PC,其流動性能比PC要好,成型加工時相對容易一.PC/ABS的低翹曲,低收縮率和尺寸穩定性,使得PC/ABS原料做出的產品的尺寸穩定性比較的高,產品也不易變形.PC 透明度好,僅次于PMMA,剛硬且沖擊韌性好,工程塑料中韌性最好,尺寸穩定性好,耐熱性好,耐蠕變,電性能好,适合作絕緣材料.PC由於含有強极性基團,它對水分很靈敏,當 PC中含有极少量水分時,輕者會在產品上形成銀絲,嚴重時在高溫高壓下水分就會和PC發生降解反應,使塑膠的分子量大大的降低,進而使塑膠的性能受到很大的影響,做出的產品很脆.因此,PC在成型前要嚴格的干燥.PC塑膠的分子鏈的剛性大,容易形成應力集中,同時由于 PC料對溫度不是太敏感,成型時可以采用較高的溫度和較小的壓力.PA 具有優良的耐磨性,自潤滑性,機械強度較高.但吸水性較大,因而尺寸穩定性較差.POM是一種密度高,結晶的線性高分子,它是一種自潤滑材料.POM的機械性能在工程塑料中最接近金屬,尺寸穩定性好,耐水,油,耐化學試劑.具有優良的耐磨性能,是較理想的代替銅,錫等有色金屬的工程塑料.HIPS HIPS是最便宜的工程塑料之一,和ABS,PC/ABS,PC相比,材料的光澤性比較差,綜合性能也相對差一些.PA是具有自潤滑結構的結晶性高分子,產品极其耐磨,但是PA的吸水性很大,對產品的尺寸影響很大.泛用塑膠工程塑膠3.2 常用模仁材質介紹鋼材類別鋼材編號使用硬度特性用途説明SKD61(JIS)H13(AISI)8407(ASSAB公司)DAC(日立公司)S7(ASSAB公司)HRC54~58高強度、高韌性、耐衝擊工具鋼,加工性好。
塑料模具设计与制造工艺流程
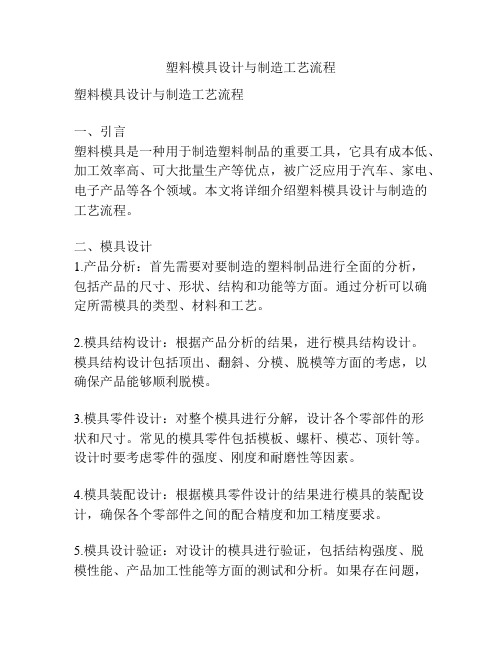
塑料模具设计与制造工艺流程塑料模具设计与制造工艺流程一、引言塑料模具是一种用于制造塑料制品的重要工具,它具有成本低、加工效率高、可大批量生产等优点,被广泛应用于汽车、家电、电子产品等各个领域。
本文将详细介绍塑料模具设计与制造的工艺流程。
二、模具设计1.产品分析:首先需要对要制造的塑料制品进行全面的分析,包括产品的尺寸、形状、结构和功能等方面。
通过分析可以确定所需模具的类型、材料和工艺。
2.模具结构设计:根据产品分析的结果,进行模具结构设计。
模具结构设计包括顶出、翻斜、分模、脱模等方面的考虑,以确保产品能够顺利脱模。
3.模具零件设计:对整个模具进行分解,设计各个零部件的形状和尺寸。
常见的模具零件包括模板、螺杆、模芯、顶针等。
设计时要考虑零件的强度、刚度和耐磨性等因素。
4.模具装配设计:根据模具零件设计的结果进行模具的装配设计,确保各个零部件之间的配合精度和加工精度要求。
5.模具设计验证:对设计的模具进行验证,包括结构强度、脱模性能、产品加工性能等方面的测试和分析。
如果存在问题,需要进行相应的修改和优化。
三、模具制造1.原材料准备:根据模具设计的结果,准备所需的模具材料,通常使用的材料有钢材和铝合金等。
根据不同情况选择合适的材料。
2.粗加工:将材料进行粗加工,包括锻造、剪切、车削等步骤,使材料初步呈现出设计要求的形状和尺寸。
3.精加工:对粗加工的模具零部件进行精加工,包括铣削、磨削、钻孔等步骤,使零部件达到设计要求的精度和表面光洁度。
4.热处理:对加工好的模具零部件进行热处理,通过控制温度和时间等参数,使零部件具有良好的硬度和韧性。
5.装配调试:将加工好的零部件进行装配调试,在装配过程中进行配合精度和尺寸精度的检测和调整,确保模具的正常使用。
四、模具试模1.试模准备:在进行试模前,需要对模具进行清洁和润滑处理,确保模具表面的光洁度和顺滑度。
2.材料预热:根据所使用的塑料材料,对材料进行预热处理,使其达到适宜的流动性和熔融温度,以便顺利注入模具。
塑料制品模具的制造与优化设计

塑料制品模具的制造与优化设计塑料制品模具的制造与优化设计在现代制造业中起到了至关重要的作用。
本文将从模具制造的流程和优化设计两个方面进行探讨,并提出一些改进的建议。
一、模具制造的流程模具制造的流程主要包括设计、加工、装配和调试四个环节。
首先是设计阶段。
在模具设计中,需要根据产品的形状和尺寸要求制定模具的结构和工艺。
此外,还需要综合考虑模具的材质选择、加工工艺以及模具寿命等因素。
设计人员应充分了解塑料制品的特性和生产要求,确保模具的质量和生产效率。
其次是加工阶段。
根据设计图纸,模具制造商将进行材料切割、加工和零部件的制造。
加工工序包括车削、铣削、磨削等,要求加工精度高,尺寸精准。
同时,在加工过程中要注意避免模具表面的划伤和变形,以保证模具的使用寿命和产品质量。
再次是装配阶段。
完成各个零部件的加工后,模具制造商将进行装配工作。
装配工作要求操作精确,各个部件要紧密结合,确保模具的正常运行和使用。
最后是调试阶段。
在模具制造完成后,需要进行调试操作,以确保模具的顺利运行和产品的质量。
调试工作包括模具的装卸、零件的调整以及试模等,以验证模具的性能和工作效果。
二、优化设计优化设计是提高塑料制品模具质量和生产效率的关键。
以下是一些常见的优化设计方法:1. 材料选择优化:根据不同的模具工作条件和要求,选择合适的材料。
例如,对于需要高耐磨性的模具,可以选择高硬度的材料来增加模具的寿命。
2. 结构设计优化:通过优化模具的结构设计,可以减少材料的浪费和加工的难度,提高模具的使用寿命和生产效率。
例如,在零件的设计中,可以合理设置卸模斜度,以方便产品的取出。
3. 冷却系统的设计优化:模具在生产过程中会受到热胀冷缩的影响,因此合理设计冷却系统可以提高模具的稳定性和生产效率。
在冷却系统的设计中,应合理设置冷却孔的位置和大小,以确保模具能够均匀冷却,避免因温度过高导致变形或破裂。
4. 精确加工和装配:在加工和装配环节,要求操作人员具有一定的技术水平,能够保证模具的加工精度和装配质量。
塑胶模具设计及加工

塑胶模具设计及加工塑料模具之设计与制造,是一种高度专门化的技术范围.一个模具师在他的工作范围内要熟练的话,需要经过几年的刻苦磨练.在塑料工业开始要蓬勃发展之时,熟练模具人才之缺乏就已经是一个严重的问题.现在想要在这方面一展抱负之模具人才,依然有多数就业机会在等他.因模具是一精密昂贵的设备,同时从设计到加工完成.须数月时间.而每一套模具的设计,都要因产品的需要而作灵活运用,因此其结构上的每一细节,都须仔细考量和详加研究.假如现在我们接到一项开模通知单,将如何来展开开模动作呢?下面我们就一起一步一步来学习:1.一般塑模结构简介:首先让我们来了解一下一套模具的基本结构(附模型)及作用(口述),如下图:模具的几个常用名词:1. 溶注口或水口(sprue)塑料由此进入模腔内,亦称主流道.溶注口瀙套连接喷嘴与模具,已形成标准件.有些母模板较薄的模具,不须瀙套,直接在模具上钻出溶注口.2. 冷料穴(cold-slug well)喷嘴最前端的熔融塑料温度较低,形成冷料渣.在进料口的末端公模仁上开设洞穴,以防止冷料渣进入模腔,造成堵塞流道.减缓料流速度,产品上形成冷料痕结合线.为了开模时从瀙套内拉出冷凝料,一般在冷料穴末端设置拉料杆(顶针上).3. 分流道(runne)分流道是主流道的连接部分,是塑料流入模腔的信道,它可在压力损失最小的条件下,将主流道内的塑料以较快的速度送到浇口处,其主要类型有:圆形.半圆形.矩形.梯形. 要求分流道的表面积或侧面积与其截面积的比值为最小.4. 栅门(gates)亦称浇口,是分流道和型腔之间连接部分,也是浇注系统的最后部分.其作用是使流道内熔融塑料以较快速度进入模腔.型腔充满后浇口能很快冷却封闭,防止型腔内未冷却料回流.其类型.位置.形状.多种多样.主要有:盘形.扇形.环形.点状.侧进胶.直接进胶.潜伏进胶.5. 排气槽(vent)当模具完全闭合时,模腔与浇道内充满空气.注射时必须将空气排出模具以外,否则将产生烧焦,填充不满,毛边,气泡,银线等不良.排气槽的形式,大小.深度因材料和模具结构不同而异(如上表),其方法主要有:分模面排气法,顶针排气法,镶件排气法,水路排气法,真空排气法.6. 顶出系统(Ejection device)是将产品从模具上脱出之装置,亦称脱模机构.是模具的重要组成部分,其形式和推出方式因产品形状,结构和塑料特性有关,其零件有顶针,推板,顶出块,斜梢,司筒,油缸或气缸,齿轮等,它与模仁之间是间隙配合,表面积尽可能大,设在不影响外观和功能处,注意脱模平衡.7. 模穴模仁(Mold cavity)模穴是在模板上挖框,,以便埋入模仁,主要是节省材料和加工方便方面考虑.有些分模面断差大的模具母模侧,会不挖模穴直接在模板上加工产品部分.模仁主要指模具的产品部分,其精度,材质要求比模胚部分要高,其形状,形式对不同的模具有不同的要求,为整套模具最重要部分.8. 模具钢(Mold Steel)一套模具外观看似乎都是一样的钢铁,其实它的各部位因要求不同必须使用不同之材质,模具钢之选择对模具寿命,加工性,精度等影响很大.模具钢材料因模具之构造塑料产品要求不同而异.选材要求主要如下:1. 采购容易2. 机械加工性优良3. 耐磨,耐腐蚀,耐热性好4. 组织细密一致,无针孔等内部缺陷5. 适合热处理变形小6. 经济,降低成本又能满足使用要求模具与成型设备之关系模具要生产,必须架设在相应的成型设备上才能发挥其作用.所以从广义上讲,模具也是成型机的一个组成部分.两者之间相辅相成,互为关联.在模具设计中必须了解此模具生产中适用机台之相关规格.才能设计出符合要求之模具:1. 注射机型号及生产厂商2. 最大注射量3. 最大锁模力4. 喷嘴球面半径及喷嘴孔径5. 定位孔直径6. 顶杆间距坐标7. 闭合高度(最大最小)8. 注塑机能配合的脱模方式9. 注塑机开模行程及开距10. 其它相关要求模具设计思路一套模具的好坏,可以说一半取决于设计.而一套模具设计的好坏,牵涉面极广,除了要求设计者有丰富的模具方面理论知识和经验外,对设计前的周详检讨与思考也同样重要:1. 了解产品图----是否具备开模条件:脱模斜度,收缩变形,能否顶出.2. 确认产品材质----塑料材料种类繁多,确定材质以决定收缩率,了解流动性以决定注口及浇道设计.3. 模具材质----根据不同之塑料及产品要求,来正确选择模具钢,以便达到品质及模具寿命要求,这要求设计者对塑料和钢材有足够了解.4. 成型机规格----了解夹模压力,注射容量,装模高度,定位环尺寸,喷嘴半径,托模孔位置.5. 模穴及其排列----由产品的投影面积,形状,精度,产量及效益来确定.各方面互相协调制约,多方面考虑来达到一最佳组合,并确定模胚和标准件.6. 浇道方式----热浇道,绝热浇道,无浇道,直接进胶(二板模),间接进胶(三板模)及其它方式.7. 浇口方式----种类繁多,因需求而异,须注意浇口是否有外观要求及流动,平衡,结合线,排气等问题,.浇口型号尺寸是否足以充满整个产品.8. 分模面----为模具设计重要环节,由设计师灵活运用,须考虑产品外观,顶出方式,模具加工等9. 模仁----须考虑外观,加工方式,模具强度,脱模方式,冷却方式,流动性,排气等问题.10. 侧凹----有滑块,油(气)缸,马达,斜梢,强行脱模及其它特殊方式,此部分变化最多,最复杂之设计.11. 顶出----多种方式,顶针.扁梢.司筒.托板.滑块.二段顶出.油(气)压.注意脱模平衡,模具强度,外观,功能,冷却效果.12. 排气----对保证产品品质至关重要,利用多种形式进行排气,注意防止产品真空吸附及模具拉不开.13. 冷却----冷却对模具生产影响很大,而设计工作较繁杂,既要考虑冷却效果及冷却一致性,又要考虑冷却系统对模具整体结构的影响.14. 加工方式----所有模具设计都须确实考虑模具加工可行性,才有实用价值.否则将脱离现场模具制造经验而成为一次失败的设计.15. 模具图----按上述构思进行绘制模具图,含组立图,零件图及相关之加工用图.在绘制过程中进一步完善模具各系统之间协调,以趋完美.16. 校对审核----模具设计完成,必须协同客户及相关人员进行校对审核,以对总体结构,加工可行性及绘图过程中的疏漏作一全面检查,征求客户意见,避免因设计失误造成模具制造和使用困难,甚至报废.模具加工常识一套设计再好的模具,如果在加工时不能达到设计要求,将严重影响整套模具之质量和寿命.这是现场模具师的责任,也是设计者必须了解的加工可行性重点.根据模具的难易程度,我们必须选择不同的加工方法来达到加工效果,总体来说,可分为传统加工和特殊加工:传统加工铣削,车削,磨削,钻削,氩焊,钳工,一般热处理等.特殊加工火花放电,线切割,CNC加工,化学腐蚀,雕刻,激光,特殊热处理,表面处理电铸电镀压铸等.模具的加工过程,要靠加工者丰富的现场经验和熟练的操作技巧及先进的设备来保证.它可以引深为另一门专业学科,对于我们设计者来说,不要求精通每一个加工过程和细节,但必须结合工厂实际,清楚每一种加工工序,充分了解加工可行性,才可在低成本下设计出符合要求之模具.避免因模具设计缺陷造成模具质量问题. 模具的加工过程,可用如下示意图简述:模具的製作。
塑料注塑模具设计与制造

塑料注塑模具设计与制造一、引言塑料注塑模具是塑料制品生产过程中必不可少的工具,它直接关系着产品质量、生产效率和成本控制等方面。
本文将深入探讨塑料注塑模具的设计与制造,介绍其中的关键要素和技术要求。
二、塑料注塑模具设计要素1. 产品结构分析在进行塑料注塑模具设计时,首先要对待生产的塑料制品进行结构分析,了解产品的形状、材料、尺寸等特点,以便为模具设计提供准确的参考依据。
2. 材料选择模具材料的选择对模具的使用寿命、成本和生产效率等方面有重要影响。
常用的模具材料包括工具钢、热作钢和硬质合金等,应根据具体情况选择合适的材料。
3. 模具结构设计模具结构设计要考虑产品的复杂程度、成型方式以及模具的拆装方便性等因素。
合理的结构设计可以提高生产效率、降低成本并保证产品质量。
4. 流道系统设计流道系统是塑料注塑模具中的一个重要组成部分,它直接影响着塑料制品的充填、冷却和排气等过程。
流道系统设计应兼顾流道断面尺寸、长度、分布和排气等要素,以确保产品质量。
5. 冷却系统设计冷却系统的优劣直接关系到注塑周期和产品质量,合理的冷却系统设计可以提高生产效率和产品质量。
应注意冷却水的流量、压力以及冷却孔的数量、尺寸和分布等要素。
三、塑料注塑模具制造技术要求1. 数控加工技术数控加工技术在塑料注塑模具制造中具有重要地位,它可以提高模具的精度和加工效率。
数控加工包括车削、铣削、钻削和线切割等,应根据模具结构和加工要求选择合适的数控加工方式。
2. 表面处理技术塑料注塑模具的表面处理对产品的外观质量和模具的耐磨性有重要影响。
常用的表面处理技术包括电镀、喷涂和抛光等,选择适当的表面处理方式可以提高产品的质量和模具的寿命。
3. 热处理技术经过热处理的模具具有较高的硬度和耐磨性,可以提高模具的使用寿命。
常用的热处理技术包括淬火、回火、表面渗碳和氮化等,应根据模具材料和使用要求选择合适的热处理方式。
4. 组装调试技术模具制造完成后需要进行组装和调试工作,以确保模具的正常运行。
塑胶模具制作工艺流程
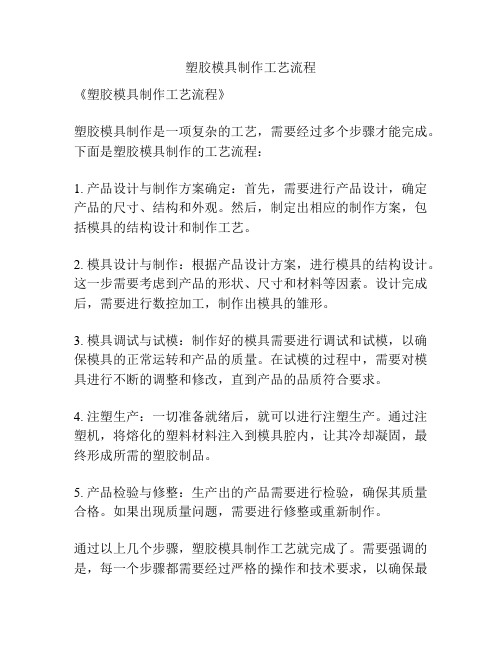
塑胶模具制作工艺流程
《塑胶模具制作工艺流程》
塑胶模具制作是一项复杂的工艺,需要经过多个步骤才能完成。
下面是塑胶模具制作的工艺流程:
1. 产品设计与制作方案确定:首先,需要进行产品设计,确定产品的尺寸、结构和外观。
然后,制定出相应的制作方案,包括模具的结构设计和制作工艺。
2. 模具设计与制作:根据产品设计方案,进行模具的结构设计。
这一步需要考虑到产品的形状、尺寸和材料等因素。
设计完成后,需要进行数控加工,制作出模具的雏形。
3. 模具调试与试模:制作好的模具需要进行调试和试模,以确保模具的正常运转和产品的质量。
在试模的过程中,需要对模具进行不断的调整和修改,直到产品的品质符合要求。
4. 注塑生产:一切准备就绪后,就可以进行注塑生产。
通过注塑机,将熔化的塑料材料注入到模具腔内,让其冷却凝固,最终形成所需的塑胶制品。
5. 产品检验与修整:生产出的产品需要进行检验,确保其质量合格。
如果出现质量问题,需要进行修整或重新制作。
通过以上几个步骤,塑胶模具制作工艺就完成了。
需要强调的是,每一个步骤都需要经过严格的操作和技术要求,以确保最
终产品的质量和精度。
塑胶模具制作是一门综合性很强的工艺,需要有丰富的经验和技术支撑。
- 1、下载文档前请自行甄别文档内容的完整性,平台不提供额外的编辑、内容补充、找答案等附加服务。
- 2、"仅部分预览"的文档,不可在线预览部分如存在完整性等问题,可反馈申请退款(可完整预览的文档不适用该条件!)。
- 3、如文档侵犯您的权益,请联系客服反馈,我们会尽快为您处理(人工客服工作时间:9:00-18:30)。
5.1-a Design review分析報告 .
報告范例
5.1-a Design review分析報告 .
報告范例
5.1-a Design review分析報告 .
報告范例
5.1-a Design review分析報告 .
報告范例
5.1-a Design review分析報告 .
報告范例
三.模具常用材質介紹.
1. 常用塑膠材質介紹.
2. 常用模仁材質介紹.
3.1 常用塑膠材質介紹
塑膠類型 名稱 主要性能 易於成型和機械加工.具有優良的物理機械性能 和低溫抗衝擊性,電性能,耐磨性,尺寸穩定性,耐 化學性,染色性等. 由于PC/ABS是ABS和PC混合而成的.因 此,PC/ABS不但具有PC的優良的韌性,极佳的光 澤性,還具有ABS優良的加工性能.流動性也優于 PC,另外由于PC良好的耐燃性能,PC/ABS具有 ABS所沒有耐燃性能. HIPS是最便宜的工程塑料之一,和 ABS,PC/ABS,PC相比,材料的光澤性比較差,綜合 性能也相對差一些. 成型工藝性
ABS
ABS具有優良的流動性能和良好的綜合性能.
泛 用 塑 膠
PC/ABS
PC/ABS的熔體粘度相對來說小于PC,其流動性能比PC要好,成型加 工時相對容易一.PC/ABS的低翹曲,低收縮率和尺寸穩定性,使得 PC/ABS原料做出的產品的尺寸穩定性比較的高,產品也不易變形.
HIPS
盡管HIPS的衝擊強度比PS的衝擊強度高出很多,但其綜合性能還是 不如ABS,PC/ABS等.
PC
透明度好,僅次于PMMA,剛硬且沖擊韌性好,工程 PC在成型前要嚴格的干燥.PC塑膠的分子鏈的剛性大,容易形成應力 塑料中韌性最好,尺寸穩定性好,耐熱性好,耐蠕 集中,同時由于 PC料對溫度不是太敏感,成型時可以采用較高的溫 變,電性能好,适合作絕緣材料. 度和較小的壓力.
工 程 塑 膠
PPE
黏性低,尺度穩定性極好,加入Nylon後化學穩定性 熱膨脹率低,只有0.2%左右,絕緣性好,適合成型家電產品的插 增強,高溫穩定性好。 接件。
1.2 主要承制的產品介紹
二. 塑膠模具結構介紹
1.常用模座結構介紹. 2.模具機構介紹. 3.模具動作的原理.
2.1 常用模座結構介紹
二板模
2.1 常用模座結構介紹
三板模
2.1 常用模座結構介紹
熱澆道模具
2.2 模具機構介紹
a. 澆口的形式介紹. b. 抽芯機構的型式介紹. c. 頂出及回位裝置的介紹. d. 冷卻水道的設置.
內容綱要
一.塑模產品介紹.
二.塑模結構介紹.
三.塑模常用材質介紹. 四.塑膠模具制造流程.
五.塑模設計.
六.塑模加工. 七.模仁拋光與咬花.
八.模具組立及模仁的表面處理.
九.模具試模. 十.模具移轉.
一.塑模產品介紹.
1. 塑件產品的划分.
2. 主要承制的產品介紹.
1.1 塑件產品的划分
5.1-a Design review分析報告 .
報告范例
5.1-b 模 流 分 析
冷卻分析
目的:
1.預知冷卻各水管吸熱效率. 2.預知公母模面產品溫度差異.
5.1-b 模 流 分 析
充填分析
目的:
1.預知塑料流動狀況,充填的時間及壓力. 2.預知是否有短射. 3.預知最后充填處.
4.預知接合線及包風位置.
2.2-b 抽芯機構的型式介紹
斜梢抽芯
2.2-c 頂出及回位裝置的介紹
一.頂針頂出
扁頂針
套筒頂針
雙節頂針Βιβλιοθήκη 2.2-c 頂出及回位裝置的介紹
二.頂出塊頂出
(1) 成品的側壁太深時.
此側壁太深
(2) 框架狀成品且不易排頂針時.
頂出塊
2.2-c 頂出及回位裝置的介紹
三.延遲頂出
2.2-c 頂出及回位裝置的介紹
3.2 常用模仁材質介紹 常用模仁材質介紹
鋼材類別 鋼材編號
SKD61(JIS) H13(AISI)
使用硬度
特性
用途説明
熱 作 鋼
出 廠 硬 度 約 為 HB185,高 級 耐 熱 鋼 , 經 真 空 8407 HRC48~52 熔 煉 , 結 晶 細 微 化 處 理 , 鋼 材 純 淨 , 組 織 細 ( ASSAB公 司 ) 緻,抗熱疲勞性好。 DAC (日立公司) S7 HRC54~58 高 強 度 、 高 韌 性 、 耐 衝 擊 工 具 鋼 , 加 工 性 ( ASSAB公 司 ) 好。 高鉻、高韌性工具鋼、高溫特性佳、硬度 VIKING HRC48~52 高、耐腐蝕性也佳。 高強度,鏡面效果特佳,放電加工良好,焊 NAK80 HRC37~43 接性能佳。 (大同公司) 硬度良好,耐磨性高,加工性能良好,適合 電蝕加工。 出 廠 硬 度 約 為 HB185,高 級 耐 熱 鋼 , 經 真 空 FDAC HRC40~44 熔 煉 , 結 晶 細 微 化 處 理 , 鋼 材 純 淨 , 組 織 細 (日立公司) 緻,抗熱疲勞性好。 不生銹塑膠模具鋼,具備最佳的鏡面抛光性 STAVAX HRC50~54 及 耐 腐 蝕 性 , 不 怕 酸 鹼 及 腐 蝕 性 塑 膠 , 不 怕 ( ASSAB公 司 ) 潮濕,不生銹。 P20( AISI)
Ny lo n (PA)
溶液粘度低,流動性好,但容易形成廢邊。 收縮率之安全性不良。 熔解溫度以外時之硬度高,對型模,螺桿等有 損傷之虞。
為使能防止廢邊形成,必需使用精密型模。 用於工業製品之型模,溫度升高,必需對成型材料結晶化注意。 成品設計需防止凹陷發生,並考慮尺寸穩定性。 成型收縮率約為1 .5 ~2 .5 %左右。
2.2-a 澆口的型式介紹
一.直接進澆與針點式進澆
直接澆口
針點澆口
2.2-a 澆口的型式及優缺點介紹
二.側邊進澆.
邊緣澆口
搭接澆口
扇形澆口
2.2-a 澆口的型式及優缺點介紹
三.潛伏式進澆.
隱道式澆口
牛角式澆口
2.2-b 抽芯機構的型式介紹
滑塊抽芯
2.2-b 抽芯機構的型式介紹
檢討內容:
1.模座(模板)檢討. 2.公母模仁檢討. 3.澆注系統檢討. 4.頂出,抽芯,冷卻 機構檢討.
5.3 3D拆模
3D結構圖
拆模需考量: 1.加工合理性. 2.組立合理性. 3.量產合理性.
5.4 零件圖檢查與確認
零件圖
零件圖檢查與確認分類: 1.模板類零件圖點檢. 2.模仁類零件圖面點檢. 3.模仁線割圖點檢. 4.滑塊與斜梢類零件圖點檢.
2.3 模具動作的原理
三板模動作原理
(1) 母模板隨著公模板一起向後運動,運動到
設定距離時,被小拉桿限位塊擋住,由于母模 板隨注塑機繼續向後運動,這樣小拉桿也被帶 動,它又帶動剝料板運動將料頭打下.
(2)成型機繼續向後運動,拉力不斷增大,超過
開閉器鎖緊力.母模板與公模板分開. (3)在脊桿地推動下,頂出板帶動頂出機構(頂 針,頂桿,斜稍)開始頂出運動,將成品頂出 (4)在成型機地推動下,公模側向母模側運動, 公模板壓向母模板和剝料板,最後完全合緊, 成型機上的噴嘴與模具上的注口襯套密合,開 始注塑.
備註:JIS-----Japanese Industrial Standards AISI-----American Iron Standards 備註:JIS-----Japanese Industrialand Steel Institute
日本工業標準 美國鋼鐵學會 日本工業標準
四.塑膠模具的制造流程
四.急回機構
2.2-d 冷卻水道的設置
冷卻水道的設置形式
(a) (c)
(d) (b)
2.3 模具動作的原理
二板模動作原理
(1)公模側在成型機的拉動下與母 模側分開,分開到設定距離時停止不 動. (2)在成型機脊桿地推動下,頂出板 帶動頂出機構將成品頂出. (3)在成型機地推動下,公模側向母 模側運動,公母模完全合緊後,成型 機上的噴嘴與模具上的注口襯套密 合,開始注塑.
HRC29~35
預 硬 鋼
ASSAB-718
Ni-Cr-Mo 合 金 工 具 鋼 , 出 廠 時 已 熱 處 理 至 大 型 塑 膠 模 具 , 要 求 表 面 光 亮 者 , 如 家 HRC54~58 30 -33HRC, 具 備 優 良 的 抛 光 性 、 咬 花 性 , 電 用 品 、 汽 車 儀 表 板 、 電 腦 、 音 響 等 熱 也 可 火 焰 硬 化 至 52HRC。 塑性塑膠模。
五. 塑模設計
1. 產品的工程分析.
2. 組立圖檢討.
3. 3D拆模.
4. 零件圖點檢.
5.1 產品的工程分析
a. DESIGN REVIEW分析報告.
b. 模流分析報告.
5.1-a Design review分析報告 .
5.1-a Design review分析報告 .
報告范例
5.1-b 模 流 分 析
保壓分析
目的:
1.預知產品收縮狀況. 2.預知單位時間內鎖模力狀況及所需最大鎖模力.
5.1-b 模 流 分 析
翹曲分析
目的: 1.預知因冷卻不良產生變形量(X,Y,Z方向之趨勢) 2.預知因設計或製程不良產生變形量(X,Y,Z方向之趨勢).
5.2 組立圖檢討
組立圖
熱間作業泛用鋼種,適用於鋁鋅壓鑄, 鋁擠型,熱鍛,塑膠模具等。