ING_7.B8000 Wheels Off-vehicle fatigue test
高考英语一轮复习Unit9Wheels单元主题语篇训练(一)(含解析)北师大版必修
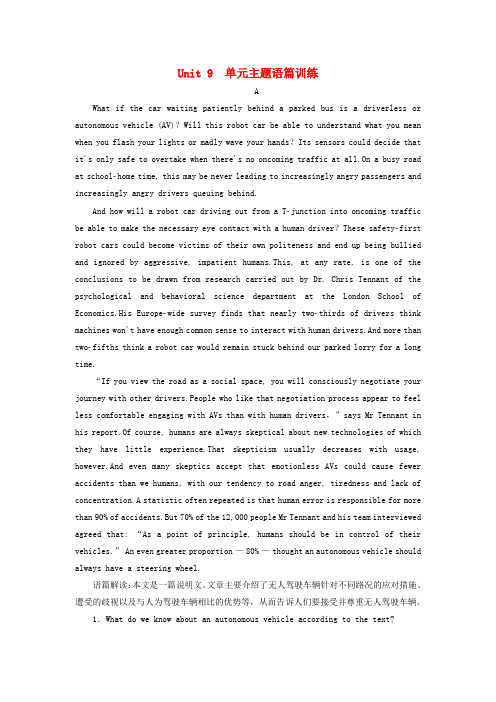
Unit 9 单元主题语篇训练AWhat if the car waiting patiently behind a parked bus is a driverless or autonomous vehicle (AV)?Will this robot car be able to understand what you mean when you flash your lights or madly wave your hands?Its sensors could decide that it's only safe to overtake when there's no oncoming traffic at all.On a busy road at schoolhome time, this may be never leading to increasingly angry passengers and increasingly angry drivers queuing behind.And how will a robot car driving out from a Tjun ction into oncoming traffic be able to make the necessary eye contact with a human driver?These safetyfirst robot cars could become victims of their own politeness and end up being bullied and ignored by aggressive, impatient humans.This, at any rate, is one of the conclusions to be drawn from research carried out by Dr. Chris Tennant of the psychological and behavioral science department at the London School of Economics.His Europewide survey finds that nearly twothirds of drivers think machines won't have enough common sense to interact with human drivers.And more than twofifths think a robot car would remain stuck behind our parked lorry for a long time.“If you view the road as a social space, you will consciously negotiate your journey with other drivers.People who like that negotiation process appear to feel less comfortable engaging with AVs than with human drivers,”says Mr Tennant in his report.Of course, humans are always skeptical about new technologies of which they have little experience.That skepticism usually decreases with usage, however.And even many skeptics accept that emotionless AVs could cause fewer accidents than we humans, with our tendency to road anger, tiredness and lack of concentration.A statistic often repeated is that human error is responsible for more than 90% of accidents.But 70% of the 12,000 people Mr Tennant and his team interviewed agreed that: “As a point of principle, humans should be in control of their vehicles.” An even greater proportion —80% —thought an autonomous vehicle should always have a steering wheel.语篇解读:本文是一篇说明文。
飞行汽车介绍英语作文
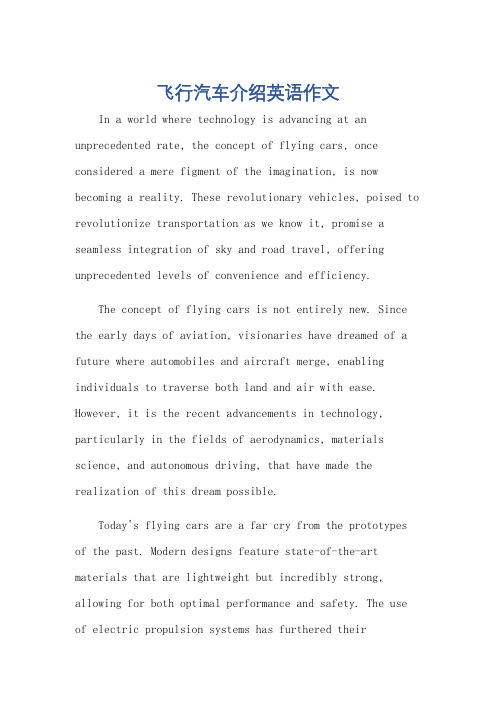
飞行汽车介绍英语作文In a world where technology is advancing at an unprecedented rate, the concept of flying cars, once considered a mere figment of the imagination, is now becoming a reality. These revolutionary vehicles, poised to revolutionize transportation as we know it, promise a seamless integration of sky and road travel, offering unprecedented levels of convenience and efficiency.The concept of flying cars is not entirely new. Since the early days of aviation, visionaries have dreamed of a future where automobiles and aircraft merge, enabling individuals to traverse both land and air with ease. However, it is the recent advancements in technology, particularly in the fields of aerodynamics, materials science, and autonomous driving, that have made the realization of this dream possible.Today's flying cars are a far cry from the prototypes of the past. Modern designs feature state-of-the-art materials that are lightweight but incredibly strong, allowing for both optimal performance and safety. The use of electric propulsion systems has furthered theirenvironmental sustainability, eliminating the need for fossil fuels and reducing carbon emissions.The integration of autonomous driving technology is another key aspect of modern flying cars. These vehicles are equipped with sensors and algorithms that enable them to navigate both roadways and airspace with precision and safety. This technology not only reduces the potential for accidents but also opens up the possibility of fully automated transportation systems, where passengers can simply sit back, relax, and enjoy the ride.The potential benefits of flying cars are vast. They offer a viable solution to the issues of traffic congestion and limited parking spaces in urban areas. With the ability to take off and land vertically, flying cars can bypass the need for roads, reducing the amount of time spent commuting and increasing overall travel efficiency. Additionally, they provide access to areas that are currently inaccessible by road, such as remote locations or densely populated urban cores.Despite the promise of flying cars, there are also challenges that need to be addressed. Regulatory frameworksneed to be updated to accommodate this new mode of transportation, ensuring that both air and road safety are maintained. There are also concerns about noise pollution and the potential impact of increased airspace traffic on the environment. However, with continued research and development, it is likely that these challenges will be overcome in time.In conclusion, the introduction of flying cars marks a significant milestone in the history of transportation. They represent not just a technological advancement but also a leap forward in terms of how we view and experience travel. While there are still many challenges to overcome, the potential benefits of these revolutionary vehicles are too great to ignore. As we move into the future, it is exciting to imagine what new possibilities await us as we embrace the dawn of a new era in transportation: the age of flying cars.**飞行汽车的介绍**随着科技的飞速进步,飞行汽车这一概念已不再是遥不可及的幻想,而是逐渐成为现实。
Fatigue & Fracture of Engineering Materials & Structures

25 1
252
G. P.TlLLY
In practice measured stresses are usually lower than design values. There have been a limited number of field measurements for reinforcement in bridges. Ruhl and Walker [4] measured stresses produced by the passage of a test truck and reported values of up to 103 N/mm2 and 144 N/mm2 for transverse reinforcement in two separate bridge decks. For the types of bar used in such bridges the stress range to give an endurance of 5 . lo6 cycles is quoted as being from 159 to 197 N/mm2. This apparently gives a safe situation but the margin is actually less because fatigue strengths at 10’ cycles can be as much as 25% lower than at 5 . lo6 cycles. Furthermore corrosion can decrease the fatigue strength whilst the dynamic interaction between the superstructure and vehicle can increase the applied stresses. There has been much research into fatigue of reinforcement. This has been intensified in recent years by the introduction of higher strength materials, the development of advanced applications such as offshore structures and the adoption of new design codes. In addition i t is becoming recognised that features such as corrosion, type of bar, form of manufacture, etc. can cause the fatigue lives to be substantially lower than are normally given in reference data. Although attention has been focussed mainly on the reinforcement bars, consideration must also be given to the fatigue performance of concrete in relation to bridges and highway pavements. In addition to a structural role, concrete protects the reinforcement from corrosion. Cracking of the concrete matrix is controlled by the type and spacing of the reinforcement bars. Research work on fatigue of concrete has recently been reviewed by Raithby [5]. There have been excellent reviews of many aspects of the fatigue of reinforcement bars written mainly as aids to the design engineer 16-81. In the review by Menzies [S] it was found that there was a scarcity of data for fatigue of British reinforcement and it was necessary to base design proposals largely on data for European steels. There are difficulties in appraising published data because there are several different types of test; one school of thought favours axial tests on unclad reinforcement in air and another favours bending tests on reinforced concrete beams. Since Menzies’ review a considerable number of investigations have been reported and data have become available for British steels. A number of new investigations have been commenced albeit mainly concerned with marine environments. It is therefore timely to review the current state-of-the-art. This paper is concerned mainly with conditions relevant to concrete structures such as highway bridges. No consideration is given to fracture mechanics partly because there has been comparatively little work relevant to reinforcement and partly because unlike requirements for welded plate bridges detailed knowledge of fracture behaviour is not required for current design practice related to concrete bridges.
汽车专业英语 PPT-Unit8

Part One Warming ups of auto repair and detect and make a match.
1.A car was hung in the repair shop, maybe there is something wrong with the chassis. ( C )
2.This is an auto emergency kit, and we can see many tools such as wench, screwdriver. ( F )
√ thousand, million) were ever made.
Part Two Listening
Task 1 :
Listen to a challenging passage and decode the message by finding out the correct choices in the brackets according to what you have heard.
wax hood injector sound decision face with broken down tip consult organization inquire resolution
v. 给……上蜡 n. 汽车发动机罩 n. 喷油器, 喷射器 adj.合理的; 可靠的; 健全的, 健康的 n. 决定, 决心; 决议
A. diagnostic tester B. program card slot C. engine performances analyzer D. auto multi-meter E. oxygen sensor F. test cable G. auto faults decoder H. four-channel oscilloscope I. auto diagnostic computer J. temperature sensor
ISUZU N-Series REWARD轻型货车说明书

Light-Duty Trucks GVM 3.1-9.5tonN-Series REWARD brings higher performance on every level with styling, power, economical operation and safety features geared to increased capacity.By offering a wide range of GVM, REWARD meets the needs of business with a model perfect forevery application while working in harmony with society and the environment.Built for You. For the way you drive. For the way you work. For the jobs you do that benefit us all.Advanced ISUZU diesel engine seriesThe next-generation 4HK1-TCN powerplant is the latest in ISUZU’s lineup of clean and fuel-efficient diesel engines. This advanced engine offers outstanding power as well as great fuel economy, making it ideal for businesses seeking cost-effective operation. Also in the lineup are the high-output 4JJ1-TC, which features outstanding torque for its displacement, and 4HG1 and 4JB1-TC engines with their proven reliability.Direct-injection DOHC intercooled turbo •Displacement 2,999cc•Max. Output 96kW(130PS)/2,800rpm(net)•Max. Torque 330N •m(34.0kg •m)/1,600-2,600rpm(net)4JJ1-TCDirect-injection OHV intercooled turbo •Displacement 2,771cc•Max. Output 67kW(91PS)/3,400rpm(net)•Max. Torque 196N •m(20.0kg •m)/2,000rpm(net)4JB1-TCDirect-injection OHV•Displacement 2,771cc•Max. Output 59kW(80PS)/3,600rpm(net)•Max. Torque 175N •m(17.8kg •m)/2,000rpm(net)4JB1-NADirect-injection OHC intercooled turbo •Displacement 5,193cc•Max. Output 110kW(150PS)/2,600rpm(net)•Max. Torque 404N •m(41.0kg •m)/1,500-2,600rpm(net)4HK1-TCNDirect-injection OHC •Displacement 4,570cc•Max. Output 89kW(121PS)/3,200rpm(ISO-gross)•Max. Torque 304N •m(31.0kg •m)/1,600rpm(ISO-gross)4HG1Professional styling for a professional toolThe styling is simple and powerful for timeless a p p e a l. A g g r e s s i v e l y d e l i n e a t e d f r o n t -e n d components and a six -hole continental grille— the identifying mark of ISUZU vehicles —make a distinctive statement.Cubicle form (high cab / w ide cab)The windshield and side windows are designed for maximum verticality, creating a boxy cab that optimizes both aerodynamic performance and interior space in comparison with previous models.In pursuit of aerodynamic perfectionThe aerodynamic front corners and roof cut air resistance especially when rear cargo bodies are mounted, contributing to better fuel economy.Improved cooling performanceComputer analysis and actual testing of vehicles ensure that the cooling system is more than a match for the high performance of engines and emission treatment systems.Excellent ingress/egressThe upright front pillars allow doors to open to a wide angle and provide a larger door opening foreffortless cab access. Also contributing to ingress/egress are the longer steps and expanded floor areas.Vertical outside handlesVertical handles make it easier to access tall vehicles. In addition, grips are designed to accommodate thick gloves.Common-rail fuel injection systemElectronic control precisely injects fuel at extremely high pressure in 1/1000 second units and determines optimal injection amounts, reducing NOx and particulate matter (PM).(4JJ1-TC, 4HK1-TCN)16-valve DOHCValve operation is accurately timed even at high rpm, increasing air intake and discharge from cylinders, thereby raising intake and exhaust efficiency.These optimal combustion conditions reduce PM and black smoke while raising fuel economy.(4JJ1-TC)Manual transmissionPowerful yet economical and easy to handle. Reliability and durability you can count on.Trucks equipped with the 4HK1-TCN powerplants come with a six-speed transmission except NPS models.Solid & Sculpted Boxy cab: upright front pillars and side body,a design of functional beauty that is both aerodynamicand makes efficient use of space.Standard cabWide cab*Gray radiator grille : OptionShown is 4JJ1-TCPowerful & toughNext-generation engines build on the proven performance of ISUZU powerplants.Power and durability are taken to a higher level.Shown is 4HK1-TCNFog lamps (option)Increase the level of safety during nighttime operation.Exhaust brake (option)Assures safe stopping everyMulti-reflector halogen headlampsClear resin lenses and step reflectors provide outstanding illumination over a broad area to improve nighttime visibility and safety.Door-side turning lampsImproved side visibility alerts others sharing the road to the presence of the vehicle and helps prevent accidents. Cornering lamps are also available.Reinforced door waistMinimizes distortion in the shape of the cab in the event of accident.Wide field of visionDrivers enjoy a clear view of the area surrounding the vehicle, making safety checks easy and reducing driving fatigue.Compound curvature outside mirrorsMirror surfaces feature a compound curvature, enhancing indirect views.Jet wipersEnhanced wiper performance for a clear windshield.ELR 3-point system seatbelts(Center seat : 2-points) Effectively restrain andprotect driver and passengers during a collision.Enhanced Braking Full air braking in GVM 9.5 ton model is engineered for tough conditions and meets ECE regulations. A wheel park lever locks wheels in place.Front and rear drum brakesExtra-large brakes improve braking performance.ACTIVE SAFETYPASSIVE SAFETYSafe and Secure, AlwaysAdvanced digital analysis makes the cab more rigid andreduces weight:truck safety is evolving in a RearFrontExhaust brake-linked lampsEngaging the exhaust brake activates the brake lamps, warning following vehicles.LED metersMeter panel graphics are totally renewed and incorporate ISO-compliant warning symbols. Meters are also easier to read, allowing drivers to confirm vehicle status at a glance. Moreover, LED lighting uses less electrical power, and lamps have a long service life.More space for DIN devicesVehicles are being equipped with more devices that use DIN connectors,a n d t h e r e i s p l e n t y o f r o o m t o n e a t l y i n s t a l l i n f o r m a t i o n t e r m i n a l s a n d a u d i o equipment. Up to six DIN devices can be installed, double the previous number.The instrument panel uses a “hard wave” motif to expand the sense of interior space. Curved cockpit surfaces are designed to fit natural hand movements and put controls at drivers’ fingertips.Even the form and angle of switches are carefully considered, resulting in a dramatic improvement in operability.The Ultimate WorkspaceStep up and experience the ultimate mobile office. With excellent accessibility,the cabin is a full-featured workspace designed for maximum utility, safety and comfort.Enhanced vehicle operabilityWorld-class comfort, expanded tilt/telescopic adjustment and effortless power steering are all standard, giving operators total control over both the vehicle and cab environment. Seats have been redesigned to recline up to 26.5 degrees and the hip-pointWide cab (R.H.D)The Freedom of ComfortThe global standard of expanded cabin space:unprecedented comfort and freedom.Ready for BusinessVinyl seat (Option) *Standard for dump modelHeader tray (option)Glove box without lid (option)Door pull case (option)Power window switch (option)140-liter fuel tank (option)Tilt cabLarge guard bar Driver’s seat sunvisorColumn combination switchesDoor ashtray Assist grips(Optional for co-driver side)Convenient hookCard holderBack panel tray(Wide cab except Crew cab)Cup holdersDriver’s seatback pocket Center seat back tray Glove box Door pockets Vinyl seat (Option) *Standard for dump modelWide cabConvenient features and plenty of storage space:N-Series is comfortable and efficient, and ready for business.Vinyl seat (Option)Cloth seat (Standard)Wide crewcab rear seat4JB1-NA59kW(80PS)/3,600rpm(net)175N •m(17.8kg •m)/2,000rpm(net)4JB1-NA59kW(80PS)/3,600rpm(net)175N •m(17.8kg •m)/2,000rpm(net)A Truck for Every ApplicationThree Drop Gate DumpThere is a wide variety of rear bodies, application-specific models and modifications to choose from, depending on the specialized needs of your business.。
车辆专业英语试题及答案
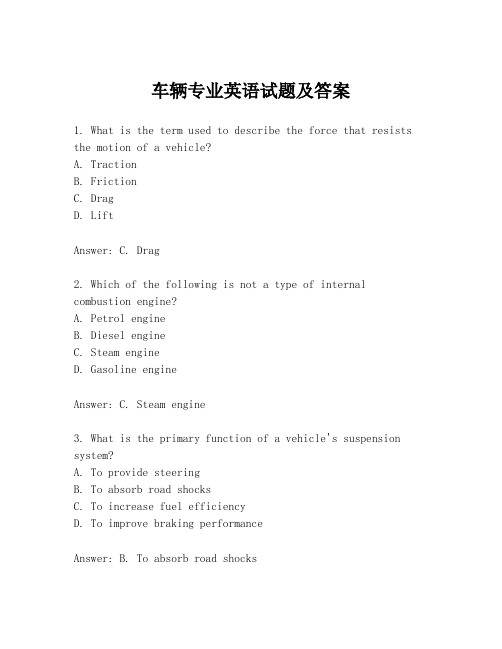
车辆专业英语试题及答案1. What is the term used to describe the force that resists the motion of a vehicle?A. TractionB. FrictionC. DragD. LiftAnswer: C. Drag2. Which of the following is not a type of internal combustion engine?A. Petrol engineB. Diesel engineC. Steam engineD. Gasoline engineAnswer: C. Steam engine3. What is the primary function of a vehicle's suspension system?A. To provide steeringB. To absorb road shocksC. To increase fuel efficiencyD. To improve braking performanceAnswer: B. To absorb road shocks4. What does the acronym ABS stand for in vehicle technology?A. Anti-lock Braking SystemB. Advanced Braking SystemC. Automatic Braking SystemD. Auxiliary Braking SystemAnswer: A. Anti-lock Braking System5. What is the term used to describe the process of converting the rotational energy of an engine into linear motion?A. TransmissionB. PropulsionC. Torque conversionD. Power transferAnswer: A. Transmission6. Which of the following is not a component of a vehicle's braking system?A. Brake padsB. Brake rotorsC. Shock absorbersD. Brake calipersAnswer: C. Shock absorbers7. What is the purpose of a vehicle's differential?A. To change the direction of power flowB. To allow wheels to rotate at different speedsC. To increase engine powerD. To reduce fuel consumptionAnswer: B. To allow wheels to rotate at different speeds8. What does the acronym CVT stand for in vehicle technology?A. Continuous Variable TransmissionB. Constant Velocity TransmissionC. Controlled Variable TransmissionD. Conventional Variable TransmissionAnswer: A. Continuous Variable Transmission9. What is the term used to describe a vehicle's ability to maintain traction on slippery surfaces?A. GripB. TractionC. AdhesionD. FrictionAnswer: B. Traction10. What is the primary function of a vehicle's steering system?A. To change the direction of the vehicleB. To control the speed of the vehicleC. To improve the vehicle's stabilityD. To regulate the vehicle's brakingAnswer: A. To change the direction of the vehicle。
SAE J267-1999 Wheels Rims-Trucks-Performance Requirements and Test Procedures
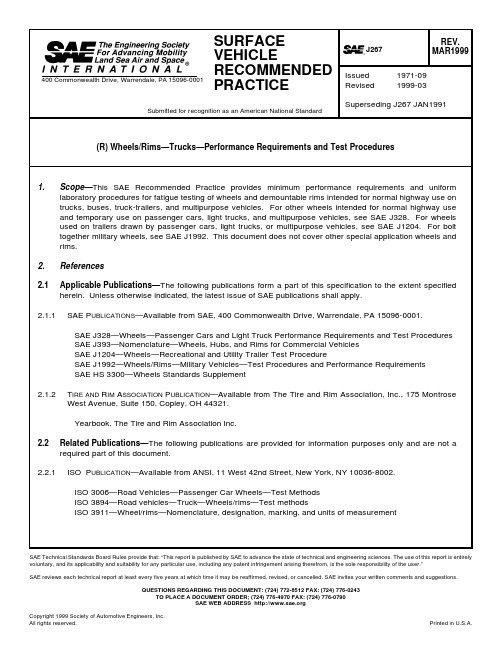
SAE Technical Standards Board Rules provide that: “This report is published by SAE to advance the state of technical and engineering sciences. The use of this report is entirely voluntary, and its applicability and suitability for any particular use, including any patent infringement arising therefrom, is the sole responsibility of the user.”SAE reviews each technical report at least every five years at which time it may be reaffirmed, revised, or cancelled. SAE invites your written comments and suggestions.QUESTIONS REGARDING THIS DOCUMENT: (724) 772-8512 FAX: (724) 776-0243TO PLACE A DOCUMENT ORDER; (724) 776-4970 FAX: (724) 776-0790SAE WEB ADDRESS 2.2.2OSHA P UBLICATION —OSHA Publication Office, Room S-4203, 200 Constitution Avenue NW, Washington,DC 20210.OSHA Standard 29 CFR Part 1910.177—Servicing of Multi-Piece and Single-Piece Rim Wheels3.Dynamic Cornering Fatigue—The test wheels, when subject to the following test procedures, shall meet the minimum performance requirement specified in Table 1.3.1Equipment—Use a test machine that:a.Imparts a constant rotating bending moment to the wheel. See Figure 1A or 1B.b.Maintains the test load within ±3%.c.Monitors and measures the deflection of the system.d.Has a rigid load arm shaft.3.2Proceduree a test adapter, studs, and nuts representative of those specified for the wheel.b.Verify the mating surfaces of the adapter are free of foreign material or excessive wear.c.Attach the wheel to a rigid load arm shaft and test adapter.d.Tighten the nuts to the torque specified in Appendix A for the stud size and type of nut. Torque shall be checked and reset periodically during the course of a test in order to compensate for the "wearing in" of mating surfaces.e.Clamp the rim securely to the test device.f.Adjust the system so that shaft runout is not more than 0.25 mm (0.010 in) total indicator reading at the point of loading.TABLE 1—CORNERING FATIGUE TESTTEST LOAD FACTORS AND CYCLE REQUIREMENTSDisc Wheel/Rim Description (All Mountings)MaterialDisc Wheel/Rim Description (All Mountings)Rim DiameterCodeDisc Wheel/Rim Description (All Mountings)Inset/Outsetmm Disc Wheel/Rim Description (All Mountings)Inset/Outsetin Performance Requirements Accelerated Test FactorPerformance Requirements Minimum Cycle LifeFerrous 13, 14, 15Less than 101.6Less than 4 1.6018 000Ferrous 16 and larger (1)1.Exclude 17.5 and larger with rim width of 266.7 mm (10.50 in) and wider (wide base tire wheels).Less than 101.6Less than 4 1.4530 000Ferrous All 101.6 or more 4 or more 1.101.3060 00040 000Aluminum 16127 or more5 or more1.351.63250 00080 000Aluminum17.5 and larger (1)AllAll1.35250 000FIGURE 1A—FIGURE 1—CORNERING FATIGUE—90 DEGREE LOADING METHOD (TYPICAL SETUP)3.3Test Loadinga.Test Load and Bending Moment Determination—The test load is determined by Equation 1:(Eq. 1)M is determined by Equation 2:(Eq. 2)where:M = Bending moment, N-m (lbf-in)u = Coefficient of friction developed between tire and road, use 0.7 for u.slr =Largest static loaded radius of the tires to be used on the wheel as specified by the currentTire and Rim Association Yearbook or the vehicle/wheel manufacturer, mm x 10–3 (in). Use the values of slr found in Appendix B.d = Inset or outset, mm x 10–3 (in). (Positive for inset, negative for outset) of the wheel. If wheelmay be used as inset or outset, use inset. See SAE J393.S =Accelerated test factor. See Table 1.L =Load rating of the wheel as specified by the wheel manufacturer, N (lbf).b.For minimum cycle life, see Table 1.c.Apply the test load parallel to a plane through the center of the rim as shown in Figure 1A or 1B. Load may push against shaft or pull the shaft.3.4Test Wheels—Use only fully processed new wheels, which are representative of wheels intended for the vehicle and ready for road use. New wheels/rims and new related components of multi-piece rims will be used for each test.3.5Test Criteria/Test Termination—The wheel under test must complete the minimum number of test cycles prior to test termination. The test shall be terminated by the inability of the wheel to sustain load and/or a visually detected fatigue crack penetrating through a section. Broken studs or other parts of the test fixture do not require test termination but may result in damage to the wheel and test invalidation.4.Dynamic Radial Fatigue Test, Disc Wheels, and Demountable Rims—The test wheels, when subject to the following test procedures, shall meet the minimum performance requirement specified in Table 2.4.1Equipment—Use a test machine that:a.Has a driven rotatable drum which presents a smooth surface wider than the loaded test tire section width.b.Has a suggested drum diameter of 1707.06 mm (67.23 in), giving 187.5 revolutions per kilometer (300revolutions per mile).c.Imparts a constant load to the wheel. This load must be perpendicular to the surface of the drum and in line radially with the center of the test wheel and the center of the drum.d.Can maintain the test load and inflation within ±3%.e.Holds the axis of the test wheel and the drum parallel.Test Load MMoment arm--------------------------------- (see Figure 1A or 1B)=M L ()u slr ()d +[]S ()=4.2Procedurea.Select test tires that are representative of the maximum size and type approved by the vehicle or wheel manufacturer for the wheel under test.e a test adapter, studs, and nuts (and clamps for demountable rims) that are representative of those specified for the wheel/rim.c.Mount and inflate the tire to 448 kPa ± 14 kPa (65 psi ± 2 psi) for tires with usage pressure of 310 kPa (45 psi) or less. For wheels and tires intended for use at higher pressures, use 1.2 times the usage pressure, but not less than 448 kPa ± 14 kPa (65 psi ± 2 psi).d.Tighten the nuts to the torque specified in Appendix A for the stud size and type of nut. Torque shall be checked and reset periodically during the course of a test in order to compensate for the "wearing in" of mating surfaces.e.There may be an increase in inflation pressure during the test. This is normal, but it is permissible to adjust back to the test pressure.4.3Radial Test Loadinga.Radial Load Determination—The radial load is determined as follows in Equation 3:(Eq. 3)where:R =Radial load, N (lbf)S =Accelerated test factor. See Table 2.L =Load rating of the wheel/rim as specified by the wheel/rim manufacturer, N (lbf)b.For minimum cycle life, see Table 2.TABLE 2—RADIAL FATIGUE TESTTEST LOAD FACTORS AND CYCLE REQUIREMENTSDisc Wheel/Rim Description (All Mountings)MaterialDisc Wheel/Rim Description (All Mountings)Rim DiameterCode Disc Wheel/Rim Description (All Mountings)Inset/Outset (1)mm1.Offset for demountable rims.Disc Wheel/Rim Description (All Mountings)Inset/Outset (1)inPerformance Requirements Accelerated Test FactorPerformance Requirements Minimum Cycle Life Ferrous13, 14, 15, 16,175 degrees DropCenter AllAll2.21.8500 0001 000 000Ferrous 15, 17, 18, 20,22, 245 degrees Flat Base 17.5HC, 19.5,22.5, 24.515 degrees DropCenterAll All2.01.91.81.71.6500 000600 000700 000850 0001 000 000Aluminum 16127 or more5 or more2.82.0100 0001 000 000Aluminum17.5 and largerAllAll2.82.0100 0001 000 000R S ()L=4.4Test Wheels—Use only fully processed new wheels/rims which are representative of wheels/rims intended forthe vehicle and ready for road use. New wheels/rims and new related components of multi-piece rims will be used for each test.4.5Test Criteria/Test Termination—The wheel under test must complete the minimum number of test cyclesprior to test termination. The test shall be terminated by the inability of the wheel to sustain load and/or a visually detected fatigue crack penetrating through a section. Failure of the test tire, broken studs, or other parts of the test fixture do not require test termination but may result in damage to the wheel and test invalidation.5.Notes5.1Marginal Indicia—The change bar (l) located in the left margin is for the convenience of the user in locatingareas where technical revisions have been made to the previous issue of the report. An (R) symbol to the left of the document title indicates a complete revision of the report.PREPARED BY THE SAE TRUCK AND BUS WHEEL SUBCOMMITTEEOF THE SAE TRUCK AND BUS CHASSIS COMMITTEEAPPENDIX ATABLE A1—TEST TORQUESApplication (1)1.For applications and sizes not shown, use torque recommendations prescribed by thewheel/rim or vehicle manufacturer.Thread Size Dry Torque (2)+10%, –0%N-m2.Dry torque means no additional lubricants are applied.Dry Torque (2)+10%, –0%lbf-ftDisc Wheels Light Truck60 degree Cone NutsM12 × 1.57/16 – 201/2 – 209/16 – 185/8 – 18110110110170170808080125125Hub Piloted Mounting 1-piece Nut9/16 – 1811/16 – 16160410120300Hub Piloted Mounting 2-piece nut9/16 – 185/8 – 183/4 – 167/8 – 14(3)7/8 – 14M12 x 1.75M14 x 1.75M14 x 1.5M18 x 1.5M20 x 1.5M22 x 1.53.Bus Front.17018041048061011518015026038061012513030035045085130110190280450Hub Piloted Mounting with Clamp Plate and 90 degree Cone Nuts9/16 – 18M14 x 1.55/8 –18150150180110110130Ball Seat Mounting3/4 – 161- 1/8 – 16610610450450Heavy-Duty Ball Seat Mounting 15/16 – 121- 5/16 – 1210201020750750 Demountable Rims Studs and Nuts3/4 – 10270200APPENDIX BTABLE B1—STATIC LOADED RADII FOR BENDING MOMENT CALCULATIONSTABLE B1a - Light Truck TiresTable B1b - Heavy Truck Tires Sizeslr mm slr in Sizeslr mm slr in 6.50–16 LT 35614.08.25–2047218.67.50–16 LT 38115.09.00–2048819.2LT225/95–1740616.010.00–2050820.011.00–2051620.312.00–2053120.913.00–2054121.314.00–2058423.016.00–2061224.110.00–2253120.911.00–2254121.3Tubeless - 5 degree 11.00–2457222.5LT225/70(1)161.For tire sizes not shown, use the slr listed in the individual tire manufacturer’s Tire Data Book.33013.012.00–2458222.9LT235/70(1)1633513.214.00–2463525.0LT255/70(1)1634013.4LT275/70(1)1634813.7LT225/75-1634513.6LT245/75-1635814.1Tubeless-15 degreeLT265/75-1637114.68R17.5 HC 37114.6LT285/75-1638415.19R17.5 HC 39115.4LT215/85-1636114.210R17.5 HC 40115.8LT235/85-1637314.711R17.5HC 41916.5LT255/85-1638915.38–19.540916.1225/70R19.538115.0LT265/70R1737114.6285/70R19.540916.1305/70R19.542416.7245/75R19.539415.5265/75R19.539915.78–22.544717.69–22.546518.310–22.548819.211-22.550319.8Wide Base - Tubeless - 15 degree 12-22.551320.212.5–22.551820.415–19.547018.512.75–22.552120.516.5–19.547818.8255/70R22.543417.118–19.550519.9305/70R22.546218.2245/75–22.543717.215–22.550820.0265/75–22.545718.016.5–22.552120.5295/75–22.548018.918–22.553321.0385/65R22.549519.5275/80R22.547218.6425/65R22.552120.5315/80R22.549919.6445/65R22.553120.911–24.552820.812–24.553621.1285/75(1)24.549519.5275/80R24.548819.2Rationale—Not applicable.Relationship of SAE Standard to ISO Standard—Not applicable.Application—This SAE Recommended Practice provides uniform laboratory procedures for fatigue testing certain production disc wheels, and demountable rims intended for normal highway use on trucks, buses, truck-trailers, and multipurpose passenger vehicles. This document does not cover bolt together divided wheels or other special application wheels and rims.Reference SectionSAE J328—Wheels—Passenger Cars and Light Truck Performance Requirements and Test Procedures SAE J393—Nomenclature—Wheels, Hubs, and Rims for Commercial VehiclesSAE J1204—Wheels—Recreational and Utility Trailer Test ProcedureSAE J1992—Wheels/Rims—Military Vehicles—Test Procedures and Performance RequirementsSAE HS 3300—Wheels Standards SupplementYearbook, The Tire and Rim Association Inc.ISO 3006—Road Vehicles—Passenger Car Wheels—Test MethodsISO 3894—Road vehicles—Truck—Wheels/rims—Test methodsISO 3911—Wheel/rims—Nomenclature, designation, marking, and units of measurementDeveloped by the SAE Truck and Bus Wheel SubcommitteeSponsored by the SAE Truck and Bus Chassis Committee。
汽车专业英语Unit-6
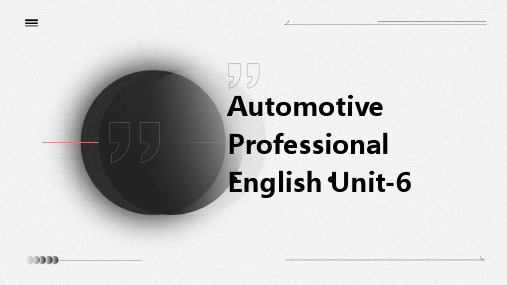
The main structure that holds the cylinders and other components together
03
An engine component that uses exhaust gases to spin a turbine, which in turn compresses air entering the engine, increasing power and efficiency
The working principle of the engine
• Working principle of braking system: The braking system converts the kinetic energy of the vehicle into thermal energy through friction and dissipates it into the air, thereby slowing down or stopping the vehicle.
Electric motor
Hybrid engine
Turbocharger
An engine that converts electrical energy into mechanical energy It is quiet, clean, and effective
A combination of an internal combustion engine and an electric motor, which uses both power sources to optimize performance and fuel efficiency
- 1、下载文档前请自行甄别文档内容的完整性,平台不提供额外的编辑、内容补充、找答案等附加服务。
- 2、"仅部分预览"的文档,不可在线预览部分如存在完整性等问题,可反馈申请退款(可完整预览的文档不适用该条件!)。
- 3、如文档侵犯您的权益,请联系客服反馈,我们会尽快为您处理(人工客服工作时间:9:00-18:30)。
2 REFERENCES 7-G0030 7-G0112 07691 Significance of items under test (PGE) Threaded connection tightening tests on systems/complete vehicles (PGE) Weibull analysis
B -
Issue 4 - "Test schedule" section removed. Issue 5 - Title changed, completely revised for updating. Issue 6 - Set up test and targets changed Issue 7 - Added Help 6
Date MAY 1996 SEP 1996 OCT 1997 APR 2001 NOV 2001 MAR 2004 JUL 2004 JUL 2011 11 MAR 2013 Issue 1 - New.
Description of change
- Issued in accordance with Technical Memorandum Procedure. - Text revised, data transmission form added. Issue 2 - Test schedule revised. Issue 3 Extended to cover wheel bolts, text revised, layout revised. Test schedule revised (DR) (DR) (DR) (MV) (DC) (DC)
CONFIDENTIAL THIS DOCUMENT MUST NOT BE REPRODUCED OR CIRCULATED TO THE THIRD PARTIES WITHOUT PRIOR WRITTEN CONSENT BY FGA S.P.A. IN CASE OF DISPUTE THE ONLY VALID REFERENCE IS THE ITALIAN EDITION. IF THE ITALIAN EDITION IS NOT AVAILABLE OR NOT UPDATED, THE ENGLISH EDITION IS THE VALID REFERENCE.
3 TEST EQUIPMENT
CONFIDENTIAL THIS DOCUMENT MUST NOT BE REPRODUCED OR CIRCULATED TO THE THIRD PARTIES WITHOUT PRIOR WRITTEN CONSENT BY FGA S.P.A. IN CASE OF DISPUTE THE ONLY VALID REFERENCE IS THE ITALIAN EDITION. IF THE ITALIAN EDITION IS NOT AVAILABLE OR NOT UPDATED, THE ENGLISH EDITION IS THE VALID REFERENCE.
To define test methods for production release or qualification approval.
Supervisor
Manager
Ch. A
CHASSIS & VEHICLE DYNAMICS - BENCH TESTING CHASSIS & VEHICLE DYNAMICS - BENCH TESTING
Edition
7
Ch.
A
1 APPLICATION CRITERIA
Code
PME
Page 2 di 19 Change Build Level: A[ ] - B[ ] - C[. ] - D[ ] - E[ ] Component Type: Supplier:
7.B8000
Job: Drawing Number: Last Change:
Supervisor department
Manager department
AS UPDATE STATUS OF PRINTOUTS CANNOT BE MONITORED, CHECK THE WEB SITE FOR THE LATEST EDITION OF DOCUMENT
PUBLISHED BY FGA - NORMAZIONE
GAROFANO GIANLUIGI
Fiat Group Automobiles normazione
CAPRA LUIGI
WHEELS Off-vehicle fatigue test
PERFORMANCE STANDARD
7.B8000
Page: Date: 1 of 19 11 MAR (Mirafiori plant). Test setup No. 1 (Arese plant). Test setup No. 2 (Arese plant). One tire per wheel to be tested selecting the widest and lowest. Wheel bolts to be replaced for each new wheel tested Shims to be inserted between wheel and test setup supports. gage, round point wrench, 15 daNm fsd Weighing scales, 30 daN fsd Equivalent test equipment may be substituted but must be equal or superior in performance.
Note:
Date:…………………………………………………….. Test Engineer:………………………………….………