铸件凝固过程数值模拟的新进展
金属液流动与凝固过程数值模拟分析方法研究

金属液流动与凝固过程数值模拟分析方法研究金属液流动和凝固过程数值模拟分析方法研究概述金属液流动和凝固过程是金属材料加工中的重要环节,对于金属制品的质量和性能有着重要影响。
因此,研究金属液流动和凝固过程的数值模拟分析方法具有重要的理论价值和实际应用价值。
本文将针对金属液流动和凝固过程的数值模拟分析方法进行研究,探讨其原理、步骤和应用。
一、数值模拟方法原理数值模拟方法是通过将物理系统离散化为有限的控制体积或网格,建立物理方程组,并使用数值计算方法求解,从而获得系统的增量或离散化解。
在金属液流动和凝固过程的数值模拟中,通常采用的是计算流体力学方法(CFD)或有限元方法(FEM)。
计算流体力学方法以连续介质力学为基础,通过对连续介质流动进行方程建模和求解,获得流动场的信息,进而研究流动的性质和变化规律。
在金属液流动和凝固过程的数值模拟中,流动方程通常采用Navier-Stokes方程,并结合运动边界条件、控制方程和物理方程对金属液流动过程进行数值模拟。
有限元方法是通过将物理系统划分为有限个单元,通过使用多项式近似解的方法,得到局部解之后,通过求解单元间的关系得到整体解。
在金属液流动和凝固过程的数值模拟中,有限元方法通常采用二维或三维的网格划分方法,将金属液的流动与凝固过程离散化为有限个单元,然后针对每个单元进行方程建模和求解,最终获得整体的解。
二、数值模拟方法步骤1. 建立几何模型:首先需要建立金属液流动和凝固过程的几何模型,通过CAD软件或者网格生成软件能够实现。
2. 网格划分:将几何模型离散为有限个单元或控制体积,进行网格划分。
在金属液流动和凝固过程的数值模拟中,网格划分需要根据流场的特点和凝固过程的要求进行合理的选择。
3. 建立物理模型:在金属液流动和凝固过程的数值模拟中,需要对流动方程、凝固方程和物理方程进行建模。
根据流动的性质和过程的要求,可以选择不同的物理模型。
4. 边界条件和初始条件:通过观察实验或实际生产中的数据,确定流场和凝固过程的初始条件和边界条件,以供数值模拟求解时使用。
铸件凝固过程微观组织模拟研究状况
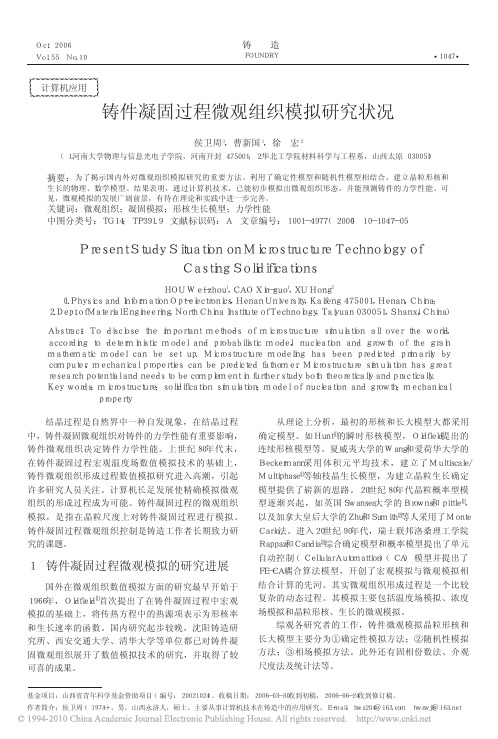
Monte Carlo法的原理是,将宏观传热的计算单元 划分为数量为N的更细小的单元,一般为正方形或六 边形网格,假设网格中某节点i,并给它赋予一个正整 数Pi 用于表示晶粒指数,在形核开始之前Pi =0( 表示 液态),然后按下列规则进行形核、生长计算:当温度 低于液相线时,在网格中随机选取节点n,计算其形核 率P(n t+Δt),其表达式为Pn=δN·Vm。式中Vm为网格单 元的体积;δN为t 到t +Δt 时刻单元体积内熔体的形核 数目,其值可由Oldfield[1]连续形核模型或Rappaz模型 求出。将(Pn t+Δt) 与一随机数发生器(n 0≤n≤1) 作 比较。若P(n t+Δt)>n 则该单元形核凝固。随机赋予Pi 一个从1到Q的正整数晶向值( Q为可取的晶向数),表 示晶向。液体金属发生形核以后,原子陆续向晶面堆 砌,发生长大过程。 1.3 相场模型法
!"
Oct. 2006 Vol.55 No.10
铸造
FOUNDRY
!"
!!!!!!" 计算机应用
铸件凝固过程微观组织模拟研究状况
·1047·
!!!!!!"
侯卫周1,曹新国1,徐 宏2
( 1.河南大学物理与信息光电子学院,河南开封 475001;2.华北工学院材料科学与工程系,山西太原 030051)
扩散控制,枝晶界面在任何时刻均为等浓度面,并假
设,①晶粒内温度分布均匀;②晶粒外围溶质扩散发
生在一球体扩散层内;③溶质守恒;④热平衡;⑤晶
粒生长速度由枝晶尖端生长动力学方程给出。采用显
式有限差分法计算浓度场、冷却曲线、固相分数以及
数值模拟在铸造充型及凝固过程的应用进展
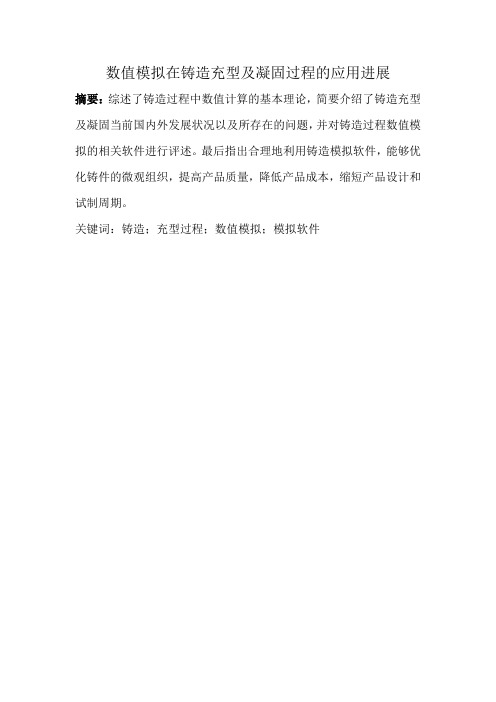
数值模拟在铸造充型及凝固过程的应用进展摘要:综述了铸造过程中数值计算的基本理论,简要介绍了铸造充型及凝固当前国内外发展状况以及所存在的问题,并对铸造过程数值模拟的相关软件进行评述。
最后指出合理地利用铸造模拟软件,能够优化铸件的微观组织,提高产品质量,降低产品成本,缩短产品设计和试制周期。
关键词:铸造;充型过程;数值模拟;模拟软件The Application of Numerical Simulation in Mold Fillingand Solidification ProcessAbstract:The basic theory of numerical calculations is summarized, and a brief introduction of the developing situation and existing problems of the casting mold filling and solidification process at home and abroad,reviewed the numerical simulation software of casting process. In the end, it also clearly shows that it can optimize the casting microstructure, improve the quality, decrease the cost and reduce the design and trial cycle for the products by using the numerical simulation software properly.Key words: Casting; Filling and Solidification process; Numerical Simulation; Simulation Software1 前言铸造过程就是将高温的液态金属浇注到封闭的型腔中,通过充型和凝固过程最终获得所需形状铸件的热成形过程。
铸件凝固过程温度场的数值模拟
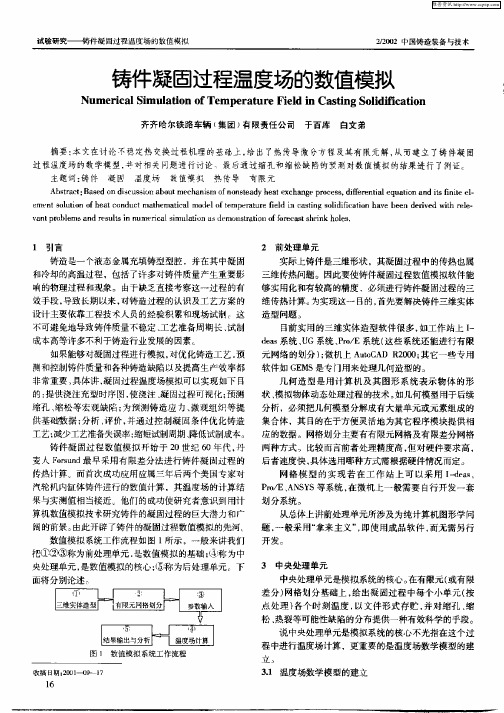
3 中央处 理 单元
从总体上讲前处理单拿来 主义” 即使用成品软件 , , 而无需另行
开 发。
中央处理单元是模拟系统 的核心。 在有限元 ( 或有限 差分) 网格划分基础上 , 给出凝 固过程 中每个小单元 ( 按
点处理 ) 各个时刻温度 , 以文件形式存贮 , 并对缩孔 、 缩
实际上铸件是三维形状 ,其凝固过程中的传热也属
三维传热问题 。因此要使铸件凝固过程数值模拟软件能
够实用化和有较高的精度 ,必须进行铸件凝固过程 的三 维传热计算 。 为实现这一 目的, 首先要解决铸件三维实体
造 型问题 。
目 前实用的三维实体造型软件很多 , 如工作站上 I — da 系统 、G系统、r E系统 ( es U Po / 这些系统还能进行有限
状、 模拟物体动态处理过程 的技术。 如几何模型用于后续
缩孔 、 缩松等宏观缺陷 ; 为预测铸造应力 、 微观组织等提 分析,必须把几何模型分解成有大量单元或元素组成的 供基础数据 ; 分析 、 评价 , 并通过控制凝固条件优化铸造 集合体 ,其 目的在于方便灵活地为其它程序模块提供相 工艺; 减少工艺准备失误率; 缩短试制周期 、 降低试制成本。 应的数据 。网格划分主要有有 限元网格及有限差分网格 铸件凝 固过程数值模拟 开始于 2 0世纪 6 年代 , o 丹 两种方式 比较而言前者处理精度高 , 但对硬件要求高, 麦人 Fr n 最早采用有 限差分法进行铸件凝 固过程 的 os d u 后者速度快 , 具体选用哪种方式需根据硬件情况而定 。 传热计算。而首次成功应用应属 三年后两个美国专家对 网格 模型 的实现 若在 工作 站上可 以采用 Ida 、 - es 汽轮机内缸体铸件进行的数值计算 ,其温度场的计算结 PoE A S S等系统 , r 、N Y / 在微机上一般需要 白行开发一套 果与实测值相当接近。他们 的成功使研究者意识到用计 划 分系统 。 算机数值模拟技术研究铸件的凝固过程的巨大潜力和广 阔的前景。 由此开辟了铸件的凝固过程数值模拟的先河。 数值模拟系统工作流程如图 1 所示 ,一般来讲我们 把①②⑧称为前处理单元 , 是数值模 拟的基础 ; ④称 为中 央处理单元 , 是数值模拟的核心 ; ⑤称为后处理单元 下 面将 分别论 述 ÷
铸件凝固过程的微观组织数值模拟研究进展
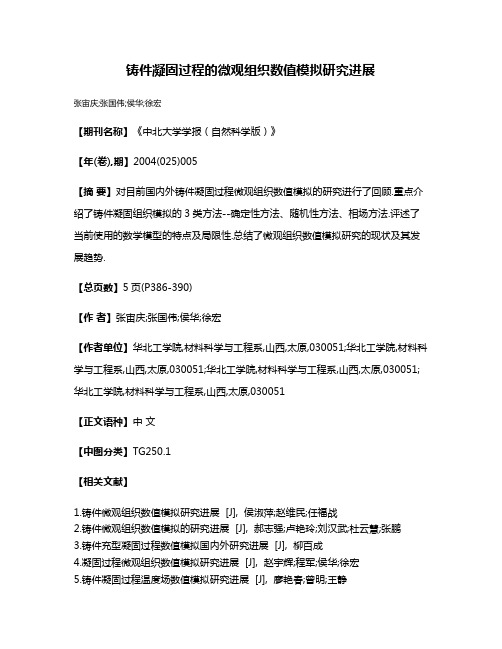
铸件凝固过程的微观组织数值模拟研究进展
张宙庆;张国伟;侯华;徐宏
【期刊名称】《中北大学学报(自然科学版)》
【年(卷),期】2004(025)005
【摘要】对目前国内外铸件凝固过程微观组织数值模拟的研究进行了回顾.重点介绍了铸件凝固组织模拟的3类方法--确定性方法、随机性方法、相场方法.评述了当前使用的数学模型的特点及局限性.总结了微观组织数值模拟研究的现状及其发展趋势.
【总页数】5页(P386-390)
【作者】张宙庆;张国伟;侯华;徐宏
【作者单位】华北工学院,材料科学与工程系,山西,太原,030051;华北工学院,材料科学与工程系,山西,太原,030051;华北工学院,材料科学与工程系,山西,太原,030051;华北工学院,材料科学与工程系,山西,太原,030051
【正文语种】中文
【中图分类】TG250.1
【相关文献】
1.铸件微观组织数值模拟研究进展 [J], 侯淑萍;赵维民;任福战
2.铸件微观组织数值模拟的研究进展 [J], 郝志强;卢艳玲;刘汉武;杜云慧;张鹏
3.铸件充型凝固过程数值模拟国内外研究进展 [J], 柳百成
4.凝固过程微观组织数值模拟研究进展 [J], 赵宇辉;程军;侯华;徐宏
5.铸件凝固过程温度场数值模拟研究进展 [J], 廖艳春;曾明;王静
因版权原因,仅展示原文概要,查看原文内容请购买。
铸件凝固过程数值模拟的新进展

在处理奥氏体生长过程时
,Fras[ 4 ]等人采用了不
同于
Goettsch和
Dantzig的作法
,Fras等人认为奥氏
体枝晶的生长贯穿整个凝固过程
,并分别采用
:
xE = 1 -exp (-xe) (5)
xD = 1 -exp (-xd)= 1 -exp (-fix) (6)
μeΔTe
将共晶团内片层间距与晶粒半径相联系的模拟研究。
式
(9)中
,ε是共晶团的片层系数
;ΔTe是共晶生长的
—35 —
. 1995-2004 Tsinghua Tongfang Optical Disc Co., Ltd. All rights reserved.
以模拟铸件凝固过程中温度场变化规律为基础
内容的数值模拟
,如今已被许多学者称之为铸件凝固
过程的宏观模拟
(Macro2Modelling) [1~4]。铸件凝固
过程的宏观模拟经
30多年的不断发展
,目前已是成
熟技术
,它可以预测与铸件温度场直接相关的铸件的
宏观缺陷
,如
,有学者
[7、8 ]提出
:球墨铸铁凝固
的传统理论可能是不正确的。
在铸件凝固过程微观模拟的早期研究中
,研究者
们皆采用了完全形成共晶组织的合金或完全形成枝
晶组织的合金
,并且都是针对形状简单的小试样
(Biot数
< 0. 1)进行模拟研究的。显然
,这与实际铸
件的情况有很大差异
Rappaz对定向凝固的灰
凝固过程数值模拟铸造CAE软件在船用铸钢件上的应用

型与凝固过程数值模拟铸造CAE软件在船用铸钢件上的应用1 前言铸件的生产过程有许多不可知因素,特别是充型与凝固过程,这些因素使得缺陷的形成原因和部位无法确定,因此也就只能凭经验采取预防措施。
随着科学技术的发展,计算机技木在铸件生产上的应用,使许多不可知因素可以用计算机进行温度场的数值模似而变为可知。
然而如果仅应用能量守恒方程进行铸件凝固过程的数值模拟,而忽略充型过程中的传热,必然会对凝固过程的温度场计算造成误差。
因此铸件温度场的数值模拟,只有在前期充型过程温度场与流动场的耦合模拟基础上进行才更有意义。
我厂是生产船用大马力低速柴油机的专业厂家,对铸件的生产要求很高,面且铸件大部分是单件小批量的中大件,为提高铸件质量减少试制费用,提高铸件出品率,1997年9月就开始用华中理工大学研制的“流动场与温度场耦合模拟及凝固模拟”软件代替原来使用的“纯温度场模拟”软件。
2 软件简介软件在Windows操作坏境下工作,硬件需要586以上的CPU;硬盘>1G;内存>16M。
软件包括3个部分:前置处理软件系统(实体造型和网格剖分);铸钢铸造CAE系统和结果显示系统。
2.1 前置处理软件系统这个系统包括了实体造型和网格剖分,实体造型借用了AutoCAD R12.0 For Windows的实体造型系统AME ( Advanced Modeling Extension )铸件三维造型完成以后,接下来就是要进行网格单元剖分,生成计算分析所需要的有限差分网格。
利用AutoCAD Rl2.0 for Windows集成开发环境ADS (AutoCAD Develop ment System)提供的1套完整的二次开发函数,研制出的铸件有限差分网格自动剖分模块以应用程序形式,外挂于AutoCAD Rl2.0 fOr Windows之上,使三维造型与网格剖分融为一体,具有人机界面友好、剖分速度快等优点。
2.2 铸钢铸造CAE系统本系统利用网格剖分后生成的文件,经输入基本参数(如初始温度、化学成份、各材料的热物性值、边界条件、“动态松弛因子”、收敛判据等)形成初始文件,然后进行计算,并自动存贮计算文件。
铸造行业的凝固过程数值模拟技术

铸造行业的凝固过程数值模拟技术
上一章山东伊莱特重工详细描述过铸造行业发展计算机的应用技术,今天,作为环形锻件行业的领军企业,伊莱特继续详细讲述铸造行业的凝固过程数值模拟技术。
即用数值计算方法求解凝固成形的物理过程所对应的数学离散方程,并由计算机显示其计算的结果。
这项技术诞生多年来,近几年获得了很大的进展,在许多方面已达到实用程度,成为提高铸造业技术水平和铸件竞争能力的关键技术之一。
可以实现的目标有:预知凝固时间、开箱时间、确定生产率;预测缩孔和缩松形成的位置和大小;预知铸型的表面及内部的温度分布,方便铸型(特别是金属型)的设计;控制凝固条件,为预测铸件应力、微观及宏观偏析、铸件性能等提供必要的依据和分析计算的数据。
凝固过程数值模拟不仅可以形象地显示液态充填型腔和在型腔中冷却凝固的进程,还可预测可能产生的缺陷,所以可在制造计划现场实施前,综合评价各种工艺方案和参数,优化工艺方案,取代或减少现场试制,这对大型复杂形状或贵重材料凝固成形铸件的生产,其优越性和经济效益尤为突出。
由于凝固过程数值模拟可以揭示许多物理本质过程,所以也促进了凝固理论的发展,近年来研究和发展的微观组织模拟,可预测晶粒大小和力学性能,可望在不久的将来用于生产实际。
- 1、下载文档前请自行甄别文档内容的完整性,平台不提供额外的编辑、内容补充、找答案等附加服务。
- 2、"仅部分预览"的文档,不可在线预览部分如存在完整性等问题,可反馈申请退款(可完整预览的文档不适用该条件!)。
- 3、如文档侵犯您的权益,请联系客服反馈,我们会尽快为您处理(人工客服工作时间:9:00-18:30)。
・综述 Survey ・铸件凝固过程数值模拟的新进展西安交通大学(陕西省西安市710049) 张云鹏 杨秉俭 苏俊义西安理工大学 王贻青摘 要 铸件凝固过程的宏观模拟虽然已是成熟技术,但也存在着不足。
近10年来,在国际上铸件凝固过程的微观模拟愈来愈引起人们的重视。
目前,铸件凝固过程的微观模拟正在经历着由试验研究向实际生产应用过度的发展过程。
关键词:凝固过程 数值模拟 进展R ecent Progresses of Numerical Modelling on C asting Solidif ication ProcessZhang Yunpeng Y ang Bingjian Su J unyi(Xian Jiaotong University )Wang Y iqing(Xian University of Technology )Abstract Although numerical modelling of casting solidification process is an already mature technology ,there are some deficiency in it.For nearly ten years ,the micro 2modelling of casting solidification process has been paided more and more attention in the world.At present ,the micro 2modelling of casting solidification process is undergo 2ing a transition period from test research to actual application.K ey w ords :Solidification process Numerical modelling Progress 以模拟铸件凝固过程中温度场变化规律为基础内容的数值模拟,如今已被许多学者称之为铸件凝固过程的宏观模拟(Macro 2Modelling )[1~4]。
铸件凝固过程的宏观模拟经30多年的不断发展,目前已是成熟技术,它可以预测与铸件温度场直接相关的铸件的宏观缺陷,如:缩孔、缩松、热裂、宏观偏析等,并且可用于进行铸件的铸造工艺辅助设计,有力地促进了铸件生产的技术进步。
在国际上,许多先进的铸造企业已将铸件凝固过程的宏观模拟作为提高铸件质量、缩短生产周期、降低生产成本的有效手段。
然而,铸件凝固过程的宏观模拟也存在着两方面不足:(1)在宏观模拟中,与潜热释放量线性相关的固相分数的变化量(Δf s )总是被间接地处理成温度变化量(ΔT )的函数:Δf s =f (ΔT )(1)这样,在数值模拟中潜热的释放量与温度的状态有关而与结晶时的动力学过程无关。
实质上,潜热的释放量归根到底是由晶粒的生核与长大产生的,晶粒生长的具体过程必然对潜热释放速率产生一定影响。
所 3机械工业部教育司科技基金资助和西安交通大学科技基金资助以,忽略掉结晶动力学因素必然会影响模拟结果的精确程度。
(2)宏观模拟中,由于潜热的释放量通过固相分数的变化量间接地表示为温度变化量的函数,所以,模拟结果只能得到温度场的变化规律,而不能预测铸件凝固组织的特征(如晶粒度、晶粒尺寸等)。
1 铸件凝固过程的微观模拟预测铸件的组织特征进而推断其机械性能是铸造工作者由来已久的愿望。
早在1966年,Oldfield [5]就首次提出了在铸件凝固过程宏观模拟的基础上,将传热方程中的热源项表示成形核率与生长速率的函数,从而可得到能反映铸件凝固组织的模拟结果的基本思想。
在随后的20多年里,由于铸件凝固过程的宏观模拟尚在发展之中,所以,微观模拟也未能取得显著进展。
近10年来,随着铸件凝固过程宏观模拟的日臻成熟,以及许多合金的凝固动力学规律进一步被揭示,铸件凝固过程的微观模拟愈来愈引起人们的重视,国际上已举行了几次有关这一研究领域的专题会议。
铸件凝固过程的微观模拟正逐步成为铸造学科中人们研究的热点之一。
—43—铸件凝固过程数值模拟的新进展《铸造技术》1/1998所谓铸件凝固过程的微观模拟(Micro 2Mod 2elling ),是指在晶粒尺度上模拟铸件的凝固过程。
它与铸件凝固过程宏观模拟的根本区别在于处理潜热释放速率时采用的方式不同。
铸件凝固过程的微观模拟是从凝固热力学与结晶动力学两方面出发,通过晶粒形核和长大的数学模型计算凝固潜热的释放量。
在铸件凝固过程的微观模拟中,与潜热释放量线性相关的固相分数的变化量是形核率(N )与生长速率5R5te n g 的函数:Δf s =f N ,5R5t Yu(2)2 铸件凝固过程微观模拟的早期研究铸件凝固过程微观模拟的早期研究,其目的主要在于得到合金的模拟冷却曲线,通过比较模拟冷却曲线与实测冷却曲线验证所采用的形核、生长模型及模拟计算方法是否合理可靠。
在这些数值模拟中,试样凝固后的晶粒密度是作为已知参数需要预先知道的。
这类模拟对于验证人们关于某种合金凝固机理的认识(通过验证形核、生长模型)是否正确是极有价值的。
例如:关于共晶灰铸铁的微观模拟结果[6]表明,采用:N =A ・ΔT ・d Tdt(3)d Rdt=B ・ΔT 2(4)(其中 N 、ΔT 、d T dt分别是形核率、过冷度及冷却速度;dRdt是生长速度;A 、B 是由具体实验条件确定的常数)。
描述共晶团的形核与长大过程,可以得到与实测冷却曲线十分接近的模拟冷却曲线,说明人们对共晶灰铸铁凝固规律的上述认识是正确的。
但当根据球墨铸铁传统的凝固理论(即:石墨球首先成核析出并很快被奥氏体壳包裹,随后,碳原子通过奥氏体壳扩散附着在石墨球上,依此方式,石墨球与奥氏体进行共生生长)建立起来的数学模型模拟球铁的冷却曲线[7]时,只有在形核率的数值比试样晶粒密度高3~4个数量级时,模拟所得冷却曲线与实测冷却曲线才比较接近。
据此,有学者[7、8]提出:球墨铸铁凝固的传统理论可能是不正确的。
在铸件凝固过程微观模拟的早期研究中,研究者们皆采用了完全形成共晶组织的合金或完全形成枝晶组织的合金,并且都是针对形状简单的小试样(Biot 数<0.1)进行模拟研究的。
显然,这与实际铸件的情况有很大差异,但通过早期研究,使研究者们普遍认为微观模拟的方法是有效的,它可用于模拟铸件凝固组织的发展变化。
3 铸件凝固过程微观模拟的新进展进入90年代后,铸件凝固过程的微观模拟开始由试验研究向实际应用发展。
G oettsch 和Dantzig [9]以及Fras [4]等人模拟了亚共晶灰口铁的凝固过程。
在G oettsch 和Dantzig 的工作中,初生奥氏体的量由平衡相图求得,共晶团的形核与长大在剩余液体中进行。
共晶凝固被认为是只有共晶团形核与长大的过程。
G oettsch 和Dantzig 还进一步模拟了试样凝固之后的共析转变过程,并利用灰铸铁金相组织与机械性能之间的近似关系预测了所模拟灰铸铁的强度、硬度等性能。
在处理奥氏体生长过程时,Fras [4]等人采用了不同于G oettsch 和Dantzig 的作法,Fras 等人认为奥氏体枝晶的生长贯穿整个凝固过程,并分别采用:x E =1-exp (-x e )(5)x D =1-exp (-x d )=1-exp (-f i x )(6)作为描述共晶和枝晶固相分数的数学模型。
式中 x E 、x D 代表共晶和枝晶的固相分数;x e 、x d 、x 分别是不考虑接触(Impingement )因素时共晶晶粒的体积分数、枝晶的体积分数以及枝晶尖端所构成的球形晶粒的体积分数;f i 是球形晶粒内部的固相分数。
这里所谓的“接触因素”,是指当凝固进行到一定程度时,生长着的晶粒彼此间将相互接触,在随后的生长过程中,晶粒不再是假设中的圆球状,其有效生长面积也发生了变化。
此时,若仍简单地延用球状晶粒的假设计算固相分数及其变化率,必然产生较大的误差。
因此,在进行凝固过程的微观模拟中,上述现象必须予以考虑,并称其为“接触因素”。
处理接触因素的常用方法是借用Johnson 2Meh1方程[10]。
对于初晶和共晶阶段的凝固,Fras [4]等人作了如下处理:当凝固在液相线与共晶温度之间进行时,只有初生奥氏体枝晶析出,其固相分数由式(6)表示。
低于共晶温度后,既有共晶凝固,也有枝晶凝固,固相分数的变化率被表示为:dx E =exp (-x e -x d )dx e (7)dx D =exp (-x e -x d )dx d(8)Fras [4]等人的工作中还涉及到当合金为共晶成分时,可通过公式[11]:λ=εμeΔT e (9)将共晶团内片层间距与晶粒半径相联系的模拟研究。
式(9)中,ε是共晶团的片层系数;ΔT e 是共晶生长的—53—铸件凝固过程数值模拟的新进展《铸造技术》1/1998过冷度。
Z ou 和Rappaz [12]研究了单向凝固灰铸铁圆棒凝固组织形成过程的数值模拟(试样尺寸: 50mm ×120mm )。
对于具有非均匀温度场的试样,Z ou 和Rappaz 首先将其作空间分割处理(网格化),假设分割后的每个体积单元具有均匀温度,而各单元之间的温度彼此不同。
由于各单元的温度不同,即彼此不在同一时刻形核及再辉(Recalescence )。
这样,相邻单元的温度变化将相互干涉,导致各点的冷却过程出现了“回弹”现象(Rebounding Phenomenon )[2],于是,在各点的冷却曲线上出现了较大幅度的连续脉动,再辉及共晶平台也失去了原有的特征。
这一现象的出现,使得问题复杂化了。
Z ou 和Rappaz 通过改变网格数及时间步长对此进行研究,结果表明,细化网格和缩短时间步长,可以有效地减弱“回弹现象”。
另外,由于凝固过程中,各点温度没有明显的“再辉”,这样,在模拟计算中停止形核的时间便失去了依据。
对于这一问题,Z ou 和Rappaz 借鉴Lesoult 与其合作者[13]的处理方法,假设当晶粒相互接触时(f s =π/6≈0.5),停止形核。
通过上述处理,Z ou 和Rappaz 对定向凝固的灰铸铁圆棒进行了冷却曲线、晶粒尺度、共晶团片层间距等方面的数值模拟。
其结果与实验数据接近。
4 展望从已有的研究工作看,铸件凝固过程的微观模拟仍属于试验研究的水平,在国内尚处于起步阶段。
然而,由于铸件凝固过程微观模拟的重要性,在国际上关于铸件凝固过程微观模拟的研究已愈来愈引起人们的重视,有理由相信,随着铸件生产技术要求的不断提高,以及凝固过程微观模拟研究的深入开展,不久的将来,铸件凝固过程的微观模拟将在铸件生产中发挥重要作用。