凝固过程数值模拟
铸造凝固过程数值模拟
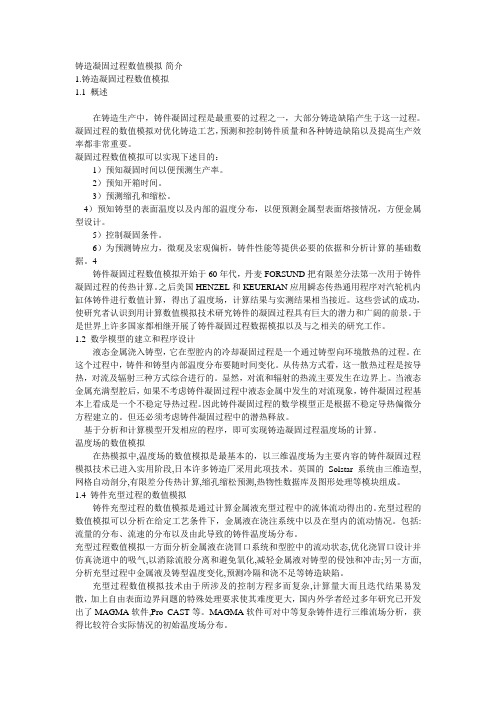
铸造凝固过程数值模拟-简介1.铸造凝固过程数值模拟1.1 概述在铸造生产中,铸件凝固过程是最重要的过程之一,大部分铸造缺陷产生于这一过程。
凝固过程的数值模拟对优化铸造工艺,预测和控制铸件质量和各种铸造缺陷以及提高生产效率都非常重要。
凝固过程数值模拟可以实现下述目的:1)预知凝固时间以便预测生产率。
2)预知开箱时间。
3)预测缩孔和缩松。
4)预知铸型的表面温度以及内部的温度分布,以便预测金属型表面熔接情况,方便金属型设计。
5)控制凝固条件。
6)为预测铸应力,微观及宏观偏析,铸件性能等提供必要的依据和分析计算的基础数据。
4铸件凝固过程数值模拟开始于60年代,丹麦FORSUND把有限差分法第一次用于铸件凝固过程的传热计算。
之后美国HENZEL和KEUERIAN应用瞬态传热通用程序对汽轮机内缸体铸件进行数值计算,得出了温度场,计算结果与实测结果相当接近。
这些尝试的成功,使研究者认识到用计算数值模拟技术研究铸件的凝固过程具有巨大的潜力和广阔的前景。
于是世界上许多国家都相继开展了铸件凝固过程数据模拟以及与之相关的研究工作。
1.2 数学模型的建立和程序设计液态金属浇入铸型,它在型腔内的冷却凝固过程是一个通过铸型向环境散热的过程。
在这个过程中,铸件和铸型内部温度分布要随时间变化。
从传热方式看,这一散热过程是按导热,对流及辐射三种方式综合进行的。
显然,对流和辐射的热流主要发生在边界上。
当液态金属充满型腔后,如果不考虑铸件凝固过程中液态金属中发生的对流现象,铸件凝固过程基本上看成是一个不稳定导热过程。
因此铸件凝固过程的数学模型正是根据不稳定导热偏微分方程建立的。
但还必须考虑铸件凝固过程中的潜热释放。
基于分析和计算模型开发相应的程序,即可实现铸造凝固过程温度场的计算。
温度场的数值模拟在热模拟中,温度场的数值模拟是最基本的,以三维温度场为主要内容的铸件凝固过程模拟技术已进入实用阶段,日本许多铸造厂采用此项技术。
英国的Solstar系统由三维造型,网格自动剖分,有限差分传热计算,缩孔缩松预测,热物性数据库及图形处理等模块组成。
大钢锭的凝固工艺数值模拟研究

大钢锭的凝固工艺数值模拟研究
大钢锭的凝固工艺数值模拟研究是指使用数值模拟方法对大钢锭凝固过程进行研究和优化。
凝固是钢坯生产过程中关键的环节,直接影响其质量和性能。
通过数值模拟可以模拟凝固过程中的温度场、相变、应力和变形等物理现象,从而预测和优化大钢锭的凝固结构和性能。
具体而言,大钢锭的凝固工艺数值模拟研究可以包括以下方面:
1. 温度场模拟:通过数值方法计算大钢锭凝固过程中的温度分布,包括凝固壳层和内部的温度变化。
这可以帮助预测凝固过程中的热流动和热扩散等现象。
2. 相变模拟:钢的凝固过程涉及到相变,包括凝固前的熔池区域和凝固后的固相区域。
数值模拟可以模拟相变过程中的组分分布、晶体生长和偏析等现象。
3. 应力和变形模拟:凝固过程中会产生应力和变形,这对大钢锭的质量和性能具有重要影响。
通过数值模拟可以模拟应力场和变形场,预测和优化凝固过程中的应力集中和变形破碎等问题。
4. 凝固结构分析:通过数值模拟可以分析大钢锭的凝固结构和组织特征,包括晶粒形貌、晶粒尺寸和晶界取向等。
这可以提供指导大钢锭的后续加工和热处理的依据。
大钢锭的凝固工艺数值模拟研究可以通过有限元方法、有限差分方法等数值方法进行。
通过合理的模拟参数和边界条件,可以精确模拟大钢锭的凝固过程,为生产提供科学依据和优化策略。
基于ANSYS的铸件充型凝固过程数值模拟的开题报告

基于ANSYS的铸件充型凝固过程数值模拟的开题报告1. 研究背景铸造是一种重要的制造工艺,广泛应用于工业生产中。
铸造的过程中,充型凝固是其中最基本的环节之一,其质量直接影响着铸件的成型和性能。
传统的充型凝固过程试验需要大量人力、物力和财力投入,成本较高,同时也难以控制实验条件,因此利用数值模拟方法对铸造过程进行分析与预测就显得格外重要。
ANSYS是一种应用广泛的数值分析软件,它可以应用于多个领域的工程仿真,包括铸造领域。
基于ANSYS的铸造充型凝固过程数值模拟可以较为精确地模拟铸造工艺,对铸件质量控制有着重要的作用。
因此,本文拟研究基于ANSYS的铸造充型凝固过程数值模拟方法。
2. 研究内容本文主要研究基于ANSYS的铸造充型凝固过程数值模拟方法。
研究的具体内容包括:(1)建立充型凝固数值模型:通过ANSYS建立铸造模型,并在模型中考虑充型、凝固和冷却等因素,确定模型的边界条件。
(2)数值模拟求解:利用ANSYS的求解功能,对模型进行数值模拟,获得充型凝固过程的温度和流动场分布等参数。
(3)结果分析:对数值模拟结果进行分析,评估充型凝固过程的质量,提出改进方案并进行优化。
3. 预期成果本研究的预期成果主要包括:(1)建立基于ANSYS的铸造充型凝固数值模型,实现对铸造过程的数值模拟。
(2)通过数值模拟获得铸造过程中的温度和流动场分布等参数,并对其进行分析。
(3)评估充型凝固过程的质量,提出改进方案并进行优化。
4. 研究意义本研究的意义主要体现在以下几个方面:(1)通过数值模拟方法获得铸造过程中的温度和流动场等参数,可以更准确地评估充型凝固过程的质量。
(2)实现基于ANSYS的铸造充型凝固数值模拟,可以在一定程度上避免传统充型凝固实验的高成本和实验条件不易控制的问题。
(3)本研究的方法可以为铸造行业提供参考,为铸造过程的质量控制提供技术支持。
5. 研究进程安排本研究的进程安排如下:(1)前期准备阶段:熟悉铸造充型凝固过程数值模拟理论,了解ANSYS软件的使用方法,确定研究方向。
金属液流动与凝固过程数值模拟分析方法研究

金属液流动与凝固过程数值模拟分析方法研究金属液流动和凝固过程数值模拟分析方法研究概述金属液流动和凝固过程是金属材料加工中的重要环节,对于金属制品的质量和性能有着重要影响。
因此,研究金属液流动和凝固过程的数值模拟分析方法具有重要的理论价值和实际应用价值。
本文将针对金属液流动和凝固过程的数值模拟分析方法进行研究,探讨其原理、步骤和应用。
一、数值模拟方法原理数值模拟方法是通过将物理系统离散化为有限的控制体积或网格,建立物理方程组,并使用数值计算方法求解,从而获得系统的增量或离散化解。
在金属液流动和凝固过程的数值模拟中,通常采用的是计算流体力学方法(CFD)或有限元方法(FEM)。
计算流体力学方法以连续介质力学为基础,通过对连续介质流动进行方程建模和求解,获得流动场的信息,进而研究流动的性质和变化规律。
在金属液流动和凝固过程的数值模拟中,流动方程通常采用Navier-Stokes方程,并结合运动边界条件、控制方程和物理方程对金属液流动过程进行数值模拟。
有限元方法是通过将物理系统划分为有限个单元,通过使用多项式近似解的方法,得到局部解之后,通过求解单元间的关系得到整体解。
在金属液流动和凝固过程的数值模拟中,有限元方法通常采用二维或三维的网格划分方法,将金属液的流动与凝固过程离散化为有限个单元,然后针对每个单元进行方程建模和求解,最终获得整体的解。
二、数值模拟方法步骤1. 建立几何模型:首先需要建立金属液流动和凝固过程的几何模型,通过CAD软件或者网格生成软件能够实现。
2. 网格划分:将几何模型离散为有限个单元或控制体积,进行网格划分。
在金属液流动和凝固过程的数值模拟中,网格划分需要根据流场的特点和凝固过程的要求进行合理的选择。
3. 建立物理模型:在金属液流动和凝固过程的数值模拟中,需要对流动方程、凝固方程和物理方程进行建模。
根据流动的性质和过程的要求,可以选择不同的物理模型。
4. 边界条件和初始条件:通过观察实验或实际生产中的数据,确定流场和凝固过程的初始条件和边界条件,以供数值模拟求解时使用。
凝固过程数值模拟---单值性条件

班级:成型0902姓名:郭海龙学号:**********
一.凝固过程数值模拟的单值性条件的主要内容
1.几何条件(物体的几何形状与尺度)
如:平壁或圆筒壁;厚度、直径等
2.物理条件(材料的热物性,包括他们是否随温度而变化以及是否均匀等条件)
如:物性参数、c和的数值,是否随温度变化;有无内热源、大小和分布;是否各向同性
试凑法。该法是在测量了钢锭和钢锭模内部几点温度后,通过控制│ - │<ε(ε为人为规定的误差),来求解界面热阻 (h=1/ 。 如果 和 分别为钢锭模内距界面10mm处的计算和测量温度值。也就是说,设在一定的时间间隔内 是某一常数,将不同的 分别代入计算方程,直到满足│ - │<ε为止,然后再转入下一个时间间隔的计算。这种方法可求出h-τ曲线,但在钢锭模内距界面10mm处的计算温度虽然较准确,而在其它点的计算温度误差较大。
3.初始条件-时间条件(为所研究的系统过程在开始所求物理量的分布值)
说明在时间上导热过程进行的特点;稳态导热过程不需要时间条件,与时间无关;对非稳态导热过程应给出过程开始时刻导热体内的温度分布
=(x,y,z,0)
4.边界条件(所求系统在不同介质之间边界上的热交换条件,不同边界类型,不同热交换现象)
说明导热体边界上过程进行的特点;反映过程与周围环境相互作用的条件
其中,L是节点中心距。
实际上,铸件-铸型界面属于非理想接触,因为铸件在铸型内冷却凝固时,它的体积要逐渐收缩,而铸型受热要铸件膨胀。此时,在铸件-铸型之间就形成了一层很薄的气体层,这一气体层和铸型内表面上的涂料层合在一起称为气隙。由于空隙的存在,在铸件-铸型之间就要产生界面温度差 。除铸件包围泥芯凝固的情况外,在大多数铸件几何体中都会发生界面温度差这种情况。
热型连铸凝固过程微观组织形成的数值模拟
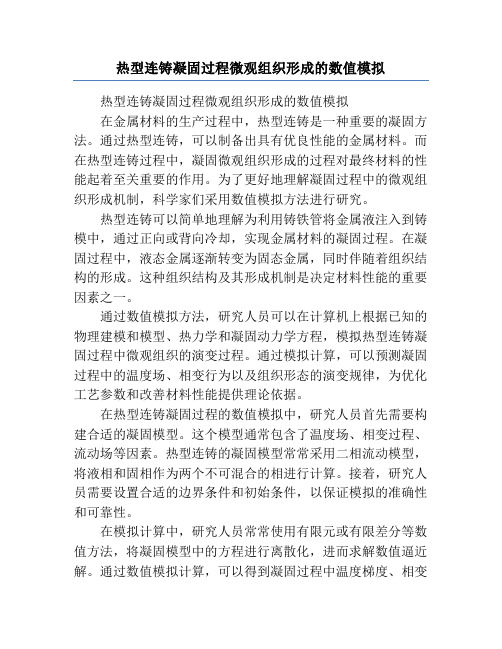
热型连铸凝固过程微观组织形成的数值模拟热型连铸凝固过程微观组织形成的数值模拟在金属材料的生产过程中,热型连铸是一种重要的凝固方法。
通过热型连铸,可以制备出具有优良性能的金属材料。
而在热型连铸过程中,凝固微观组织形成的过程对最终材料的性能起着至关重要的作用。
为了更好地理解凝固过程中的微观组织形成机制,科学家们采用数值模拟方法进行研究。
热型连铸可以简单地理解为利用铸铁管将金属液注入到铸模中,通过正向或背向冷却,实现金属材料的凝固过程。
在凝固过程中,液态金属逐渐转变为固态金属,同时伴随着组织结构的形成。
这种组织结构及其形成机制是决定材料性能的重要因素之一。
通过数值模拟方法,研究人员可以在计算机上根据已知的物理建模和模型、热力学和凝固动力学方程,模拟热型连铸凝固过程中微观组织的演变过程。
通过模拟计算,可以预测凝固过程中的温度场、相变行为以及组织形态的演变规律,为优化工艺参数和改善材料性能提供理论依据。
在热型连铸凝固过程的数值模拟中,研究人员首先需要构建合适的凝固模型。
这个模型通常包含了温度场、相变过程、流动场等因素。
热型连铸的凝固模型常常采用二相流动模型,将液相和固相作为两个不可混合的相进行计算。
接着,研究人员需要设置合适的边界条件和初始条件,以保证模拟的准确性和可靠性。
在模拟计算中,研究人员常常使用有限元或有限差分等数值方法,将凝固模型中的方程进行离散化,进而求解数值逼近解。
通过数值模拟计算,可以得到凝固过程中温度梯度、相变速率以及组织演变规律等信息。
这些信息对于工艺优化和材料性能的改善起到了重要的指导作用。
为了更好地验证数值模拟结果的准确性,研究人员通常会进行实验验证。
实验验证常常包括金属样品的制备、显微组织的观察和性能测试等步骤。
通过与实验结果的对比,可以验证数值模拟的准确性,并进一步改进模型和计算方法。
通过热型连铸凝固过程微观组织形成的数值模拟,研究人员可以更好地理解材料凝固过程中组织形成的机制,为优化工艺参数和改善材料性能提供科学依据。
薄板坯连铸凝固过程数值模拟
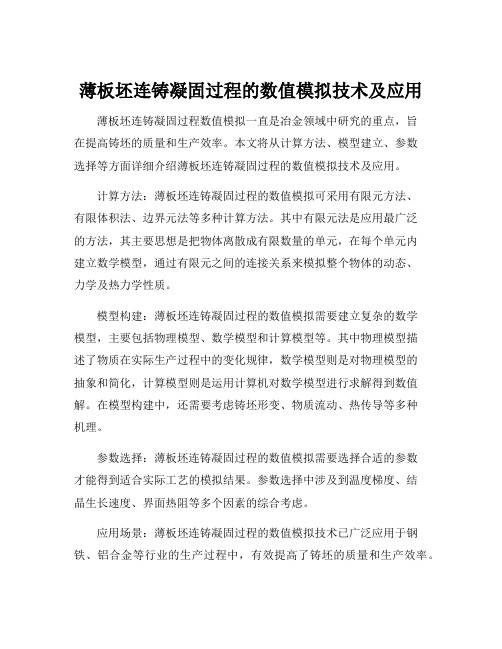
薄板坯连铸凝固过程的数值模拟技术及应用薄板坯连铸凝固过程数值模拟一直是冶金领域中研究的重点,旨
在提高铸坯的质量和生产效率。
本文将从计算方法、模型建立、参数
选择等方面详细介绍薄板坯连铸凝固过程的数值模拟技术及应用。
计算方法:薄板坯连铸凝固过程的数值模拟可采用有限元方法、
有限体积法、边界元法等多种计算方法。
其中有限元法是应用最广泛
的方法,其主要思想是把物体离散成有限数量的单元,在每个单元内
建立数学模型,通过有限元之间的连接关系来模拟整个物体的动态、
力学及热力学性质。
模型构建:薄板坯连铸凝固过程的数值模拟需要建立复杂的数学
模型,主要包括物理模型、数学模型和计算模型等。
其中物理模型描
述了物质在实际生产过程中的变化规律,数学模型则是对物理模型的
抽象和简化,计算模型则是运用计算机对数学模型进行求解得到数值解。
在模型构建中,还需要考虑铸坯形变、物质流动、热传导等多种
机理。
参数选择:薄板坯连铸凝固过程的数值模拟需要选择合适的参数
才能得到适合实际工艺的模拟结果。
参数选择中涉及到温度梯度、结
晶生长速度、界面热阻等多个因素的综合考虑。
应用场景:薄板坯连铸凝固过程的数值模拟技术已广泛应用于钢铁、铝合金等行业的生产过程中,有效提高了铸坯的质量和生产效率。
同时,数值模拟技术也成为创新的生产手段,为钢铁、铝合金等行业的技术升级和发展带来积极的推动作用。
薄板坯连铸凝固过程数值模拟

薄板坯连铸凝固过程数值模拟连铸技术是钢铁工业中最重要的生产工艺之一。
薄板坯连铸是其中一种重要的连铸工艺。
在薄板坯连铸过程中,钢液经过水冷铜模具,在模具内凝固成为一块薄板坯,成为下一步轧制的原材料。
准确的数值模拟可以帮助优化生产工艺,提高产品质量。
薄板坯连铸凝固过程的数值模拟主要包括两个方面,一是数值模拟的方法和原理,二是模拟的结果和应用。
数值模拟的方法和原理主要包括数学模型、计算方法和边界条件。
数学模型是指将连铸过程中的物理过程转化为数学表达式,通常包括质量守恒、动量守恒、能量守恒以及物质相变方程等。
计算方法是指将数学模型转化为计算机可以计算的算法,常见的方法包括有限元法、有限差分法、有限体积法等。
边界条件是指模拟过程中需要考虑的约束条件,如温度、流速、壁面热通量等。
这些约束条件对模拟结果具有重要影响。
模拟的结果和应用主要包括凝固形态、温度场分布、应力分布等。
凝固形态是指钢液在模具内凝固的形态,包括结晶器壳层、过渡层、液相区等。
温度场分布是指钢液在凝固过程中的温度变化情况,包括初始温度、凝固过程中的温度变化以及完成凝固后的温度分布。
应力分布是指凝固过程中产生的应力分布情况,包括结晶器壳层的应力、板坯中心的应力等。
这些结果可以帮助生产工艺优化和产品质量控制。
数值模拟在薄板坯连铸中的应用越来越广泛。
通过数值模拟,可以帮助优化结晶器的设计、改进冷却水流量、调整钢液流速等,从而提高产品质量和生产效率。
同时,数值模拟可以预测板坯内部缺陷、预测板坯形变等,提前发现问题,减少生产事故和损失。
薄板坯连铸凝固过程的数值模拟是一项复杂的工作,需要考虑多个因素的影响,但是它可以帮助钢铁企业优化生产工艺,提高产品质量和生产效率。
随着计算机技术的不断发展,数值模拟在钢铁行业的应用将会越来越广泛。
- 1、下载文档前请自行甄别文档内容的完整性,平台不提供额外的编辑、内容补充、找答案等附加服务。
- 2、"仅部分预览"的文档,不可在线预览部分如存在完整性等问题,可反馈申请退款(可完整预览的文档不适用该条件!)。
- 3、如文档侵犯您的权益,请联系客服反馈,我们会尽快为您处理(人工客服工作时间:9:00-18:30)。
必须解决问题:
(1)铸型瞬态区域厚度的计算 (2)非均匀网格 (3)内部计算区域的标识 (4)不同区域采用不同时间步长
2015/11/13
铸件缩孔和缩松的形成原因
• 1、铸件结构方面的原因 • 2、熔炼方面的原因 • 3、工艺设计的原因
缩孔的预测
缩孔预测中主要是预测出缩孔的形状、位置大小以及所在的 位置
2015/11/13
铸件凝固模拟计算区域优化
分区计算的基本思想源于压铸过程的数值模拟研究中Barone和 Caulk提出的“瞬态层”的概念
压铸模具瞬态层示意图
分区计算的作用就是可以大大提高凝固模拟的计算效率
2015/11/13
分区域计算的实现
分区计算的核心内容:
是实现不同的区域采用不同的网格尺寸和不同的时间
铸件凝固过程数值模拟
• 主 讲 人 :贺腾博 • 小组成员:黄萍、徐晓欢、贺腾博、韩丽 梅、刘靓
铸件凝固过程
图1:斧锤型铸件
图2:新山英铺的模拟结果
铸件凝固过程数值模拟的任务
数学模型
数值求解
缺陷位置
凝固规律
铸 件 凝 固 过 程 数 值 模 拟 流 程 图
2015/11/13
铸件的凝固过程基本上可以认为是一个不稳定的 导热过程
t+Δ t
t t-Δ t
热流密度矢量
q gradt
温 度 场
• 温度场模拟是预测缩孔缩松形成,微观组织形
成以及热烈变形等的基础;
• 温度场计算的正确性取决于初始条件,边界条
件,热物性参数,合理的潜热处理等方法。
控制方程
凝固导热过程中,温度、时间和空间的关系可用傅里叶导热 方程描述即:
• 导热分析的研究归结为研究:温度随空间、 时间的变化,在直角坐标系中,也就是求 解方程:
T=f(x,y,z,t)
上述方程称为温度场的数学描述。
温
温度场
T = f (x, y, z,t)
度
场
t+Δt t t-Δt 等温线疏密程度的物理意义
等温面与等温线
t r t r Lim n n 温度梯度 gradt n 0 n n
2015/11/13
补缩单元
当单元的固相率 高于一个临界值 fsc时,就不再具 有流动能力,因 此也就不再具有 补缩能力
2015/11/13
补缩单元
(a)未考虑孤立熔池热节 (b)考虑孤立热节
2015/11/13
温度场模拟软件CAE
模拟的主要步骤:
(1)工艺三维建型 (2)新建工程 (3)前处理网格划分 (4)参数设定与技术分析 (5)后处理数据可视化
要解决的主要问题:
1.如何计算收缩量? 2.如何进行补缩通道的判断? 3.哪些单元可以进行补缩?
2015/11/13
多热节判断
多热节的判 断就是判断 出补缩通道 的情况,从 而确定出热 节的收缩量 和缩孔位置
2015/内所有单元在第m时间步长内的体
积收缩量的计算如下:
2015/11/13
后处理数据可视化
凝固过程的后处理主要包含:
(1)铸件色温 (2)温度梯度 (3)铸型色温
(4)凝固液相
(5)凝固次序
2015/11/13
左边第二项是枝晶间液体流动的热对流,由于潜热释放、两 相区温度梯度及液相率比较小,可忽略不计,式可修改为:
2015/11/13
初始条件:
冲型完毕时金属液和型腔的温度场即是凝固开始的温度场
边界条件:
边界条件是指铸件——铸型交界面或不同种类造型材料之间的 交接面。 界面热流率为:
如果界面换热系数为h,则界面两侧相邻节点之间的等效换热系 数为: