电镀锌去氢原理
镀锌去氢活化

零件在酸洗、阴极电解除油及电镀过程中都可能在镀层和基体金属的晶格中渗氢,造成晶格扭歪,内应力增大,产生脆性(称为氢脆)。
为消除氢脆,一般采用镀后加热处理,使氢逸出。
去氢的效果与处理的温度和时间有关。
去氢通常在烘箱内进行。
温度为200~250℃,时间2h。
温度的高低应由基体材料决定。
锡焊件不能加温过高。
去氢处理工序对弹性材料、0.5mm以下的薄壁件及机械强度要求较高的钢铁件是必不可少的。
去氢前镀件必须彻底清洗干净,去氢时可把零件埋在石英砂里。
去氢后钝化若有困难,可在钝化前先活化一下,如可用10%硫酸活化。
最好这样做.氢脆-钢材中的氢会使材料的力学性能脆化,这种现象称为氢脆。
主要发生在碳钢和低合金钢中。
紧固件避免和消除氢脆的措施:(1)、减少金属中渗氢的数量,必须尽量减少高强度/高硬度钢制紧固件的酸洗,因为酸洗可加剧氢脆。
(2)、采用低氢扩散性和低氢溶解度的镀涂层。
在满足产品技术条件要求的情况下,可采用不会造成渗氢的涂层,如机械镀锌或无铬锌铝涂层,不会发生氢脆,耐蚀性高,附着力好,且比电镀环保。
(3)镀前去应力和镀后去氢以消除氢脆隐患若零件经淬火、焊接等工序后内部残留应力较大,镀前应进行回火处理,回火消除应力实际上可以减少零件内的陷阱数量,从而减轻发生氢脆的隐患。
⑷、控制镀层厚度,由于镀层覆盖在紧固件表面,镀层在一定程度上会起到氢扩散屏障的作用,这将阻碍氢向紧固件外部的扩散。
当镀层厚度超过2.5μm时,氢从紧固件中扩散出去就非常困难了。
因此硬度<32HRC的紧固件,镀层厚度可以要求在12μm;硬度≥32HRC的高强度螺栓,镀层厚度应控制在8μmmax。
文案编辑词条B 添加义项?文案,原指放书的桌子,后来指在桌子上写字的人。
现在指的是公司或企业中从事文字工作的职位,就是以文字来表现已经制定的创意策略。
文案它不同于设计师用画面或其他手段的表现手法,它是一个与广告创意先后相继的表现的过程、发展的过程、深化的过程,多存在于广告公司,企业宣传,新闻策划等。
电镀差异
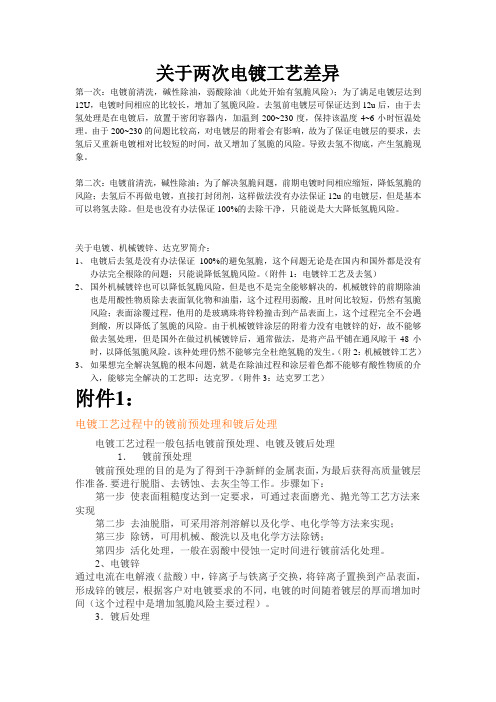
关于两次电镀工艺差异第一次:电镀前清洗,碱性除油,弱酸除油(此处开始有氢脆风险);为了满足电镀层达到12U,电镀时间相应的比较长,增加了氢脆风险。
去氢前电镀层可保证达到12u后,由于去氢处理是在电镀后,放置于密闭容器内,加温到200~230度,保持该温度4~6小时恒温处理。
由于200~230的问题比较高,对电镀层的附着会有影响,故为了保证电镀层的要求,去氢后又重新电镀相对比较短的时间,故又增加了氢脆的风险。
导致去氢不彻底,产生氢脆现象。
第二次:电镀前清洗,碱性除油;为了解决氢脆问题,前期电镀时间相应缩短,降低氢脆的风险;去氢后不再做电镀,直接打封闭剂,这样做法没有办法保证12u的电镀层,但是基本可以将氢去除。
但是也没有办法保证100%的去除干净,只能说是大大降低氢脆风险。
关于电镀、机械镀锌、达克罗简介:1、电镀后去氢是没有办法保证100%的避免氢脆,这个问题无论是在国内和国外都是没有办法完全根除的问题;只能说降低氢脆风险。
(附件1:电镀锌工艺及去氢)2、国外机械镀锌也可以降低氢脆风险,但是也不是完全能够解决的,机械镀锌的前期除油也是用酸性物质除去表面氧化物和油脂,这个过程用弱酸,且时间比较短,仍然有氢脆风险;表面涂覆过程,他用的是玻璃珠将锌粉撞击到产品表面上,这个过程完全不会遇到酸,所以降低了氢脆的风险。
由于机械镀锌涂层的附着力没有电镀锌的好,故不能够做去氢处理,但是国外在做过机械镀锌后,通常做法,是将产品平铺在通风晾干48小时,以降低氢脆风险。
该种处理仍然不能够完全杜绝氢脆的发生。
(附2:机械镀锌工艺)3、如果想完全解决氢脆的根本问题,就是在除油过程和涂层着色都不能够有酸性物质的介入,能够完全解决的工艺即:达克罗。
(附件3:达克罗工艺)附件1:电镀工艺过程中的镀前预处理和镀后处理电镀工艺过程一般包括电镀前预处理、电镀及镀后处理1.镀前预处理镀前预处理的目的是为了得到干净新鲜的金属表面,为最后获得高质量镀层作准备.要进行脱脂、去锈蚀、去灰尘等工作。
电镀锌原理及工艺流程ppt课件

CHAPTER电镀锌定义及应用领域定义电镀锌是指利用电解作用在钢铁或其他金属基体上沉积一层锌的工艺过程。
应用领域电镀锌广泛应用于汽车、家电、建筑、电子等领域,用于提高金属的耐腐蚀性、装饰性和导电性等。
电镀锌发展历程及现状发展历程自19世纪初发现锌的电镀现象以来,电镀锌技术经历了不断的发展和完善,包括工艺改进、设备更新和环保要求的提高等。
现状目前,电镀锌已成为一种成熟且广泛应用的表面处理技术,随着科技的不断进步和环保要求的日益严格,电镀锌技术也在不断向着更高效、更环保的方向发展。
电镀锌与其他镀层比较与热镀锌比较电镀锌与热镀锌相比,具有镀层薄、外观美观、氢脆风险低等优点,但耐腐蚀性相对较差。
与其他金属镀层比较与镀铬、镀镍等金属镀层相比,电镀锌具有良好的耐腐蚀性、低成本和环保性等优点,但在某些特定应用场合如高温、高湿等环境下,其耐腐蚀性可能不足。
CHAPTER电化学基础知识电极反应与电极电位电极上的氧化还原反应导致电子转移,形成电极电位差。
电解质溶液电镀锌通常采用酸性或碱性锌盐溶液作为电解质。
电极过程动力学电极反应速率受电流密度、温度、浓度等因素影响。
锌离子在阴极得到电子,还原成锌原子并沉积在阴极表面。
阴极反应阳极反应电流效率阳极发生氧化反应,如溶解氧或氢氧根离子失去电子形成氧气或水。
实际用于电镀锌的电流与总电流之比,受多种因素影响。
030201电镀锌反应机理影响电镀锌性能因素影响镀层厚度、结构和性能,过高或过低都不利于获得优质镀层。
适当提高温度可加快反应速率,但过高会导致镀层粗糙、结合力差。
加强搅拌可提高镀液均匀性,有利于获得均匀致密的镀层。
适量添加某些有机物或无机盐可改善镀层性能,如提高光泽度、耐蚀性等。
电流密度温度搅拌添加剂CHAPTER采用有机溶剂、碱液或乳化剂等清洗工件表面的油脂和污垢。
除油用稀盐酸或硫酸去除工件表面的氧化皮和锈蚀物。
酸洗用流动清水冲洗工件表面,确保表面干净无残留。
水洗前处理工艺挂具准备电镀液配制电镀操作监控与调整电镀锌工艺01020304根据工件形状和大小选择合适的挂具,确保工件在电镀过程中稳定不脱落。
电镀基本原理
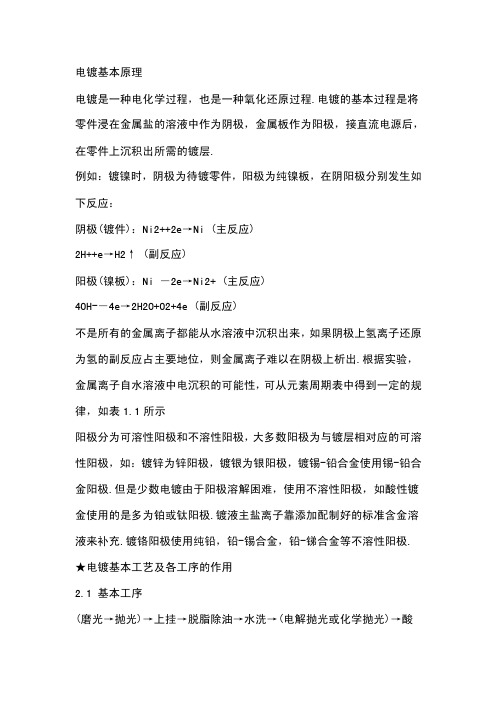
电镀基本原理电镀是一种电化学过程,也是一种氧化还原过程.电镀的基本过程是将零件浸在金属盐的溶液中作为阴极,金属板作为阳极,接直流电源后,在零件上沉积出所需的镀层.例如:镀镍时,阴极为待镀零件,阳极为纯镍板,在阴阳极分别发生如下反应:阴极(镀件):Ni2++2e→Ni (主反应)2H++e→H2↑ (副反应)阳极(镍板):Ni -2e→Ni2+ (主反应)4OH--4e→2H2O+O2+4e (副反应)不是所有的金属离子都能从水溶液中沉积出来,如果阴极上氢离子还原为氢的副反应占主要地位,则金属离子难以在阴极上析出.根据实验,金属离子自水溶液中电沉积的可能性,可从元素周期表中得到一定的规律,如表1.1所示阳极分为可溶性阳极和不溶性阳极,大多数阳极为与镀层相对应的可溶性阳极,如:镀锌为锌阳极,镀银为银阳极,镀锡-铅合金使用锡-铅合金阳极.但是少数电镀由于阳极溶解困难,使用不溶性阳极,如酸性镀金使用的是多为铂或钛阳极.镀液主盐离子靠添加配制好的标准含金溶液来补充.镀铬阳极使用纯铅,铅-锡合金,铅-锑合金等不溶性阳极. ★电镀基本工艺及各工序的作用2.1 基本工序(磨光→抛光)→上挂→脱脂除油→水洗→(电解抛光或化学抛光)→酸洗活化→(预镀)→电镀→水洗→(后处理)→水洗→乾燥→下挂→检验包装2.2 各工序的作用2.2.1 前处理:施镀前的所有工序称为前处理,其目的是修整工件表面,除掉工件表面的油脂,锈皮,氧化膜等,为后续镀层的沉积提供所需的电镀表面.前处理主要影响到外观,结合力,据统计,60%的电镀不良品是由前处理不良造成,所以前处理在电镀工艺中占有相当重要的地位.在电镀技术发达的国家,非常重视前处理工序,前处理工序占整个电镀工艺的一半或以上,因而能得到表面状况很好的镀层和极大地降低不良率.喷砂:除去零件表面的锈蚀,焊渣,积碳,旧油漆层,和其它干燥的油污;除去铸件,锻件或热处理后零件表面的型砂和氧化皮;除去零件表面的毛刺和和方向性磨痕;降低零件表明的粗糙度,以提高油漆和其它涂层的附著力;使零件呈漫反射的消光状态磨光:除掉零件表明的毛刺,锈蚀,划痕,焊缝,焊瘤,砂眼,氧化皮等各种宏观缺陷,以提高零件的平整度和电镀质量.抛光:抛光的目的是进一步降低零件表面的粗糙度,获得光亮的外观.有机械抛光,化学抛光,电化学抛光等方式.脱脂除油:除掉工件表面油脂.有有机溶剂除油,化学除油,电化学除油,擦拭除油,滚筒除油等手段.酸洗:除掉工件表面锈和氧化膜.有化学酸洗和电化学酸洗.2.2.2 电镀在工件表面得到所需镀层,是电镀加工的核心工序,此工序工艺的优劣直接影响到镀层的各种性能.此工序中对镀层有重要影响的因素主要有以下几个方面:2.2.2.1主盐体系每一镀种都会发展出多种主盐体系及与之相配套的添加剂体系.如镀锌有氰化镀锌,锌酸盐镀锌,氯化物镀锌(或称为钾盐镀锌),氨盐镀锌,硫酸盐镀锌等体系.每一体系都有自己的优缺点,如氰化镀锌液分散能力和深度能力好,镀层结晶细致,与基体结合力好,耐蚀性好,工艺范围宽,镀液稳定易操作对杂质不太敏感等优点.但是剧毒,严重污染环境.氯化物镀锌液是不含络合剂的单盐镀液,废水极易处理;镀层的光亮性和整平性优于其它体系;电流效率高,沉积速度快;氢过电位低的钢材如高碳钢,铸件,锻件等容易施镀.但是由于氯离子的弱酸性对设备有一定的腐蚀性,一方面会对设备造成一定的腐蚀,另一方面此类镀液不适应需加辅助阳极的深孔或管状零件.2.2.2.2添加剂添加剂包括光泽剂,稳定剂,柔软剂,润湿剂,低区走位剂等.光泽剂又分为主光泽剂,载体光亮剂和辅助光泽剂等.对于同一主盐体系,使用不同厂商制作的添加剂,所得镀层在质量上有很大差别.总体而言欧美和日本等发达国家的添加剂最好,台湾次之,大陆产的相对而言比前两类都逊色.主盐与具体某一厂商的添加剂的联合决定了使用的镀液的整体性能.优秀的添加剂能弥补主盐某些性能的不足.如优秀的氯化物镀锌添加剂与氯化物主盐配合得到的镀液深镀能力比许多氰化镀锌镀液的深度能力好.2.2.2.3 电镀设备挂具:方形挂具与方形镀槽配合使用,圆形挂具与圆形镀槽配合使用. 圆形镀槽和挂具更有利于保证电流分布均匀,方形挂具则需在挂具周围加设诸如铁丝网之类的分散电流装置或缩短两侧阳极板的长度,使用如图所示的椭圆形阳极排布.搅拌装置:促进溶液流动,使溶液状态分布均匀,消除气泡在工件表面的停留.电源:直流,稳定性好,波纹系数小.2.2.3 后处理电镀后对镀层进行各种处理以增强镀层的各种性能,如耐蚀性,抗变色能力,可焊性等.脱水处理:水中添加脱水剂,如镀亮镍后处理钝化处理:提高镀层耐蚀性,如镀锌防变色处理:水中添加防变色药剂,如镀银,镀锡,镀仿金等提高可焊性处理:如镀锡因此后处理工艺的优劣直接影响到镀层这些功能的好坏.3. 电镀的分类3.1按镀层组成分单金属电镀(应用较广的镀层有锌、镉、铜、铬、锡、镍、金、银等) 二元合金电镀(常用的有锡-铅合金,锌-镍,锌-钴,铜-锡等)合金电镀三元合金电镀(常用的有铜-锡-锌,锌-镍-铁等)多元合金电镀(基本处于研究阶段)复合电沉积 (电镀层中嵌入固体颗粒形成复合镀层)3.2 按获取镀层方式分挂镀(Rack Plating)常规电镀滚镀(Barrel Plating)电刷镀脉冲电镀电铸装饰性电镀,如镀金,镀银,铜╱镍/装饰铬电镀防护性电镀,如镀锌耐磨性电镀,如镀硬铬功能性电镀提高可焊性电镀,如镀锡增强导电性,如镀银,镀金……..电镀在表面处理技术领域的地位4.1 表面处理的方式和手段电镀(电沉积)阳极氧化(铝、镁、钛及它们的合金)化学氧化(铝及其合金,钢铁)电化学及化学转化铬酸盐处理(钢铁上的锌、铬镀层,铝,镁,铜)磷酸盐处理(磷化)热浸镀(常用的有热浸锌、锡、铝、铅)火焰喷涂气喷涂爆炸喷涂热喷涂电弧喷涂电喷涂等离子喷涂高频感应喷涂橡胶涂层非金属涂覆塑料涂层油漆涂层渗镀化学气象沉积扩散涂镀真空镀膜包镀达克罗(Dacromet,浸入锌铝,锌铬浆液中,形成涂层,然后烘烤干燥) 4.2 电镀的现状和发展趋势电镀由于工艺和技术成熟,在金属精饰中按吨位计占加工的首位.电镀的发展分三个时期,第一时期为改善光泽或耐蚀性,第二时期为因劳力不足而迈向胜利化、自动化,第三时期为减轻公害问题.电镀不可避免带来环境污染问题,随著其它污染小的新技术的发展,电镀使用范围正面临著逐渐被压缩的威协.另一方面,电镀本身也正在大力开发污染小新工艺,同时开发能获取新功能镀层的工艺,以拓展自身的生存空间. ★新产品开发段表面处理的工作内容5.1根据产品的用途和功能确定合适的表面处理方式.进行表面处理前需弄清使用材料,材料金属学状态,材料的表面状态,镀层厚度,耐蚀性要求,外观要求,每个电镀面的等级,镀层检验规范等.以上内容确定后才能确定合适表面处理方式和具体工艺.同为一种电镀,由于材料的种类,表面状态,金属学状态不同,所采取的工艺会有很大的不同,如钛材上镀银与普通钢材镀银工艺上的区别对钢材:除油→活化(盐酸)→镀铜→镀镍→预镀银→镀银对钛材:除油→浸蚀(含氟化物的溶液)→活化→预镀银→镀银5.2 寻找合适的供应商(针对NWE现有状况而言)基于NWE没有自己的表面处理部门,寻找到合适供应商对NWE产品的表面处理至关重要,是现阶段所有表面处理工作重心和核心.5.3 供应商的管控和辅导(针对NWE现有状况而言)由委外加工单位组织,产工和品保派相关技术工程师参与.下面是泰戈尔励志经典语录,欢迎阅读。
电镀锌的原理及相关知识

电镀锌的原理及相关知识一、概述锌易溶于酸,也能溶于碱,故称它为两性金属。
锌在干燥的空气中几乎不发生变化。
在潮湿的空气中,锌表面会生成致密的碱式碳酸锌膜。
在含二氧化硫、硫化氢以及海洋性气氛中,锌的耐蚀性较差,尤其在高温高湿含有机酸的气氛里,锌镀层极易被腐蚀。
锌的标准电极电位为-0.76V,对钢铁基体来说,锌镀层属于阳极性镀层,它主要用于防止钢铁的腐蚀,其防护性能的优劣与镀层厚度关系甚大。
锌镀层经钝化处理、染色或涂覆护光剂后,能显著提高其防护性和装饰性。
近年来,随着镀锌工艺的发展,高性能镀锌光亮剂的采用,镀锌已从单纯的防护目的进入防护-装饰性应用。
镀锌溶液有氰化物镀液和无氰镀液两类。
氰化物镀液中分微氰、低氰、中氰、和高氰几类。
无氰镀液有碱性锌酸盐镀液、铵盐镀液、硫酸盐镀液及无氨氯化物镀液等。
氰化镀锌溶液均镀能力好,得到的镀层光滑细致,在生产中被长期采用。
但由于氰化物剧毒,对环境污染严重,近年来已趋向于采用低氰、微氰、无氰镀锌溶液。
二、原理在盛有镀锌液的镀槽中,经过清理和特殊预处理的待镀件作为阴极,用镀覆金属制成阳极,两极分别与直流电源的正极和负极联接。
镀锌液由含有镀覆金属的化合物、导电的盐类、缓冲剂、pH调节剂和添加剂等的水溶液组成。
通电后,镀锌液中的金属离子,在电位差的作用下移动到阴极上形成镀层。
阳极的金属形成金属离子进入镀锌液,以保持被镀覆的金属离子的浓度[1]。
在有些情况下,如镀铬,是采用铅、铅锑合金制成的不溶性阳极,它只起传递电子、导通电流的作用。
电解液中的铬离子浓度,需依靠定期地向镀液中加入铬化合物来维持。
镀锌时,阳极材料的质量、镀锌液的成分、温度、电流密度、通电时间、搅拌强度、析出的杂质、电源波形等都会影响镀层的质量,需要适时进行控制。
三、种类1、碱性氰化物镀锌2、碱性锌酸盐镀锌3、铵盐镀锌4、钾盐镀锌5、铵钾混合浴镀锌6、硫酸盐镀锌三、镀锌层的后处理1、钝化2、去氢3、着色技术标准采用美国ASTM B695-2000及军用C-81562机械镀锌技术标准。
氢脆现象

氢脆是溶于钢中的氢聚合为氢分子,造成应力集中,超过钢的强度极限,在钢内部形成细小的裂纹,又称白点。
氢脆只可防,不可治。
出现氢脆的工件通过除氢处理(如加热等)能消除氢脆,采用真空、低氢气氛或惰性气氛加热可避免氢脆。
如电镀件的去氢都在200~240度的温度下,加热2~4小时可将绝大部分氢去除。
1.首先氢脆一经产生,就消除不了。
氢脆是溶于钢中的氢,聚合为氢分子,造成应力集中,超过钢的强度极限,在钢内部形成细小的裂纹。
又称白点。
氢脆只可防,治不了。
2.热处理对于你不适合。
热处理的方法是将工件加热至某一温度,保温一段时间,缓冷,使氢随溶解度逐渐变小,逐渐析出。
加热会破坏镀层。
3.如何防治。
你的情况主要是酸洗控制不好。
首先,尽量缩短酸洗时间;其次加缓蚀剂,减少产氢量。
======================发黑的氧化层主要成分是Fe3O4,它在加热到600多度时会转变成FeO,较疏松易脱落。
而防白点热处理温度大多在800度以上。
磷化没研究过,说不好,但肯定有氧化和磷酸盐熔化、磷渗入等弊病,连试也别试。
发黑的工件可以在较低的温度时效一下,估计能行。
磷化时效的时候可能会出现氧化的现象,表面出彩色,不知客户能不能接受2. 1 减少金属中渗氢的数量在除锈和氧化皮时,尽量采用吹砂除锈,若采用酸洗,需在酸洗液中添加若丁等缓蚀剂;在除油时,采用化学除油,清洗剂或溶剂除油,渗氢量较少,若采用电化学除油,先阴极后阳极;在电镀时,碱性镀液或高电流效率的镀液渗氢量较少 2 采用低氢扩散性和低氢溶解度的镀涂层一般认为,在电镀铬,锌,镉,镍,锡,铅时,渗入钢件的氢容易残留下来,而铜,钼,铝,银,金,钨等金属镀层具有低氢扩散性和低氢溶解度,渗氢较少。
在满足产品技术条件要求的情况下,可采用不会造成渗氢的涂层,如达克罗涂覆层可以代替镀锌,不会发生氢脆,耐蚀性提高7〜10倍,附着力好,膜厚6〜8μm之,相当于较薄的镀锌层,不影响装配。
3 镀前去应力和镀后去氢以消除氢脆隐患若零件经淬火,焊接等工序后内部残留应力较大,镀前应进行回火处理,减少发生严重渗氢的隐患。
为什么要去氢
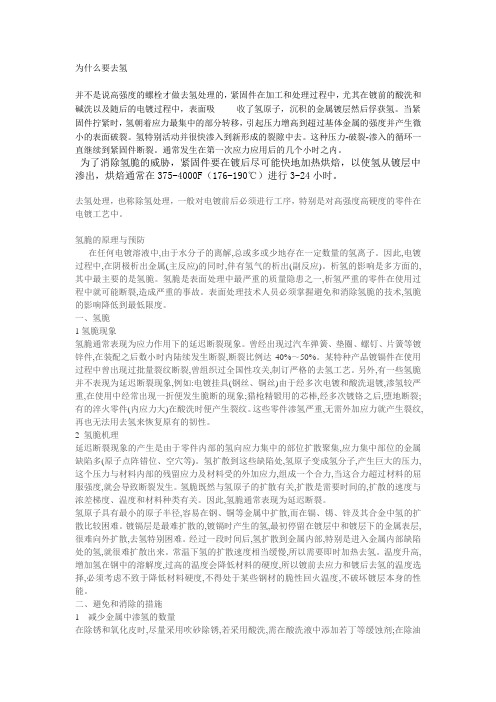
为什么要去氢并不是说高强度的螺栓才做去氢处理的,紧固件在加工和处理过程中,尤其在镀前的酸洗和碱洗以及随后的电镀过程中,表面吸收了氢原子,沉积的金属镀层然后俘获氢。
当紧固件拧紧时,氢朝着应力最集中的部分转移,引起压力增高到超过基体金属的强度并产生微小的表面破裂。
氢特别活动并很快渗入到新形成的裂隙中去。
这种压力-破裂-渗入的循环一直继续到紧固件断裂。
通常发生在第一次应力应用后的几个小时之内。
为了消除氢脆的威胁,紧固件要在镀后尽可能快地加热烘焙,以使氢从镀层中渗出,烘焙通常在375-4000F(176-190℃)进行3-24小时。
去氢处理,也称除氢处理,一般对电镀前后必须进行工序,特别是对高强度高硬度的零件在电镀工艺中。
氢脆的原理与预防在任何电镀溶液中,由于水分子的离解,总或多或少地存在一定数量的氢离子。
因此,电镀过程中,在阴极析出金属(主反应)的同时,伴有氢气的析出(副反应)。
析氢的影响是多方面的,其中最主要的是氢脆。
氢脆是表面处理中最严重的质量隐患之一,析氢严重的零件在使用过程中就可能断裂,造成严重的事故。
表面处理技术人员必须掌握避免和消除氢脆的技术,氢脆的影响降低到最低限度。
一、氢脆1氢脆现象氢脆通常表现为应力作用下的延迟断裂现象。
曾经出现过汽车弹簧、垫圈、螺钉、片簧等镀锌件,在装配之后数小时内陆续发生断裂,断裂比例达40%~50%。
某特种产品镀镉件在使用过程中曾出现过批量裂纹断裂,曾组织过全国性攻关,制订严格的去氢工艺。
另外,有一些氢脆并不表现为延迟断裂现象,例如:电镀挂具(钢丝、铜丝)由于经多次电镀和酸洗退镀,渗氢较严重,在使用中经常出现一折便发生脆断的现象;猎枪精锻用的芯棒,经多次镀铬之后,堕地断裂;有的淬火零件(内应力大)在酸洗时便产生裂纹。
这些零件渗氢严重,无需外加应力就产生裂纹,再也无法用去氢来恢复原有的韧性。
2 氢脆机理延迟断裂现象的产生是由于零件内部的氢向应力集中的部位扩散聚集,应力集中部位的金属缺陷多(原子点阵错位、空穴等)。
电镀锌原理和工艺

电镀锌的原理和工艺(一)概述与其他金属相比,锌是相对便宜而又易镀覆的一种金属,属低值防蚀电镀层.被广泛用于保护钢铁件,特别是防止大气腐蚀,并用于装饰.镀覆技术包括槽镀(或挂镀)、滚镀(适合小零件)、自动镀和连续镀(适合线材、带材).目前,国内按电镀溶液分类,可分为四大类:1.氰化物镀锌:由于(CN)属剧毒,所以环境保护对电镀锌中使用氰化物提出了严格限制,不断促进减少氰化物和取代氰化物电镀锌镀液体系的发展.要求使用低氰(微氰)电镀液.采用此工艺电镀后,产品质量好,特别是彩镀,经钝化后色彩保持好.2.锌酸盐镀锌:此工艺是由氰化物镀锌演化而来的.目前国内形成两大派系,分别为:a)武汉材保所的” DPE”系列b)广电所的”DE”系列.都属于碱性添加剂的锌酸盐镀锌;PH 值为12.5~13.采用此工艺,镀层晶格结构为柱状,耐腐蚀性好,适合彩色镀锌.典型配方:NaOH ----------- 110~120g/lZnO -------------- 11~12g/l94 ---------------- 5~7g/l94 为产品代号是”DP-EⅡ”和乙醇胺的结合物.注意:产品出槽后—>水洗—>出光(硝酸+盐酸)—>水洗—>钝化—>水洗—>水洗—>烫干—>烘干—>老化处理(烘箱内80~90oC).3.氯化物镀锌此工艺在电镀行业应用比较广泛,所占比例高达40%. 钝化后(兰白)可以锌代铬(与镀铬相媲美),特别是在外加水溶性清漆后,外行人是很难辩认出是镀锌还是镀铬的.此工艺适合于白色钝化(兰白,银白).在客户无特殊要求时,最好是选择银白钝化(色泽保持较稳定).典型配方:KCl -------------------- 180~220g/lZnCl ------------------ 65~75g/lH3BO3 --------------- 25~30g/l(缓冲剂). PH值:5~5.5CI-87 ----------------- 15~20g/l(光亮剂).4.硫酸盐镀锌此工艺适合于连续镀(线材、带材、简单、粗大型零、部件)。
- 1、下载文档前请自行甄别文档内容的完整性,平台不提供额外的编辑、内容补充、找答案等附加服务。
- 2、"仅部分预览"的文档,不可在线预览部分如存在完整性等问题,可反馈申请退款(可完整预览的文档不适用该条件!)。
- 3、如文档侵犯您的权益,请联系客服反馈,我们会尽快为您处理(人工客服工作时间:9:00-18:30)。
电镀锌件去氢
工件镀锌时,表面有拉痕处在酸洗电镀过程中易吸氢,后期加热时,此处易产生气泡。
金属材料经过酸洗除锈或者电镀,这种都有可能使材料中渗进原子态的氢。
这样的氢原子进入金属的晶格内,造成晶格的外扭,产生很大的内应力,使金属镀层和基体的韧性下降,金属材料的就变脆了,这就是“氢脆”,同时往往还有起泡和针孔等现象。
应该说金属都有此现象,只是程度不同。
一般对氢吸附能力强的金属此现象较明显。
这些金属中最大的是铬,其次是铁及其合金等,其他金属很小或者几乎没有。
这些金属材料做以上加工后都要做“驱氢”处理。
处理方法一般是将金属放到烘箱里烘或者放到热油里加热。
一、氢脆
1氢脆现象氢脆是通常表现为应力作用下的延迟断裂现象。
曾经出现过汽车弹簧、垫圈、螺钉、片簧等镀锌件,在装配之后数小时内陆续发生断裂,断裂比例达40%~50%。
某产品镀镉件在使用过程中曾出现过批量裂纹断裂。
另外,有一些氢脆并不表现为延迟断裂现象,例如:电镀挂具(钢丝、铜丝)经多次电镀和酸洗退镀,导致渗氢较严重,本来轫性不错的这些材料,在使用中经常出现轻轻一折便发生脆断的现象;猎枪精锻用的芯棒,经多次镀铬之后,堕地断裂;有些内应力大的淬火零件在酸洗过程是便产生裂纹。
这些零件渗氢严重,无需外加应力就产生裂纹,甚至直接导致断裂,再也无法用去氢来恢复原有的韧性。
2 氢脆机理延迟断裂现象的产生是由于零件内部的氢向应力集中的部位扩散聚集,应力集中部位的金属缺陷多(原子点阵错位、空穴等)。
氢扩散到这些缺陷处,氢原子变成氢分子,在金属内部产生巨大的压力,这个压力与材料内部的残留应力及材料受的外加应力,组成一个合力,当这合力超过材料的屈服强度,就会导致断裂发生。
氢脆既然与氢原子的扩散有关,扩散是需要时间的,而扩散的速度又与浓差梯度、温度和材料种类有关。
因此,氢脆更多的是表现为延迟断裂。
氢原子具有最小的原子半径,容易在钢、铜等金属中扩散,而在镉、锡、锌及其合金中氢的扩散比较困难。
镀镉层是最难扩散的,镀镉时产生的氢,最初停留在镀层中和镀层下的金属表层,很难向外扩散,去氢特别困难。
经过一段时间后,氢扩散到金属内部,特别是进入金属内部缺陷处的氢,就很难扩散出来。
常温下氢的扩散速度相当缓慢,所以需要即时加热去氢。
温度升高,增加氢在钢中的溶解度,过高的温度会降低材料的硬度,所以镀前去应力和镀后去氢的温度选择,必须考虑不致于降低材料硬度,不得处于某些钢材的脆性回火温度,不破坏镀层本身的性能。
国家有关标准对电镀锌后消除氢脆的热处理条件是根据金属材料的不同最大抗拉强度作出了温度从190度—220度(摄氏),时间为1h-24h的除氢要求。
3 氢脆的控制
在任何电镀溶液中,由于水分子的离解,总或多或少地存在一定数量的氢离子。
因此,电镀过程中,在阴极析出金属(主反应)的同时,伴有氢气的析出(副反应)。
析氢的影响是多方面的,其中最主要的是氢脆。
氢脆是表面处理中最严重的质量隐患之一,析氢严重的零件在使用过程中就可能断裂,造成严重的事故。
表面处理技术人员必须掌握避免和消除氢脆的技术,以使氢脆的影响降低到最低限度。
二、避免和消除的措施 .1 减少金属中渗氢的数量
在除锈和氧化皮时,尽量采用机械方法如喷砂、喷丸、磨光、振光除锈,若采用酸洗,需在酸洗液中添加缓蚀剂;在除油时,采用化学除油、清洗剂或溶剂除油,渗氢量较少,若采用电化学除油,要采用阳极除油或先阴极后阳极;在电镀时,酸性镀液或高电流效率的镀液渗氢量较少。
2 采用低氢扩散性和低氢溶解度的镀涂层
一般认为,在电镀Cr、Zn、Cd、Ni、Sn、Pb时,渗入钢件的氢容易残留下来,而Cu、Mo、Al、Ag、Au、W等金属镀层具有低氢扩散性和低氢溶解度,渗氢较少。
在满足产品技术条件要求的情况下,可采用不会造成渗氢的涂层,如达克罗涂覆层可以代替镀锌,不会发生氢脆,耐蚀性提高7~10倍,附着力好,膜厚6~8μm,相当于较薄的镀锌层,不影响装配。
3 镀前去应力和镀后去氢以消除氢脆隐患
若零件经淬火、焊接等工序后内部残留应力较大,镀前应进行回火处理,减少发生严重渗氢的隐患。
对电镀过程中渗氢较多的零件原则上应尽快去氢,因为镀层中的氢和表层基体金属中的氢在向钢基体内部扩散,其数量随时间的延长而增加。
新的国际标准草案规定“最好在镀后1h内,但不迟于3h,进行去氢处理”。
三、应注意的问题
材料强度越大,其氢脆敏感性也越大,这是表面处理技术人员在编制电镀工艺规范时必须明确的基本概念。
国家标准要求最大抗拉强度Rm,>1050MPa的钢材,要进行相应的镀前去应力和镀后去氢处理。
法国航空工业对屈服强度σs>90kg/mm2的钢件就要求作相应去氢处理。
由于钢材强度与硬度有很好的对应关系,因此,用材料硬度来判断材料氢脆敏感比用强度来判断更为直观、方便。
因为一份完善的产品图和机加工工艺都应标注钢材硬度。
在电镀中我们发现钢的硬度在HRC38左右时开始呈现氢脆断裂的危险。
对高于HRC43的零件,镀后应考虑去氢处理。