数控电火花加工的主要工艺指标及其提高途径
电火花加工精度的改善措施

汇报人: 2024-01-02
目录
• 电火花加工原理及精影响因 素
• 提高电火花加工精度的措施 • 新技术在电火花加工中的应用 • 电火花加工精度改善的实践与
展望
01
电火花加工原理及精度影响因 素
电火花加工原理简介
电火花加工是一种利用电火花放电产生的高温来去除材料的加工方法。在加工过 程中,工具电极和工件之间产生瞬时的高电压和高温,导致工件材料的熔化和汽 化,最终实现材料的去除。
02
减小放电间隙的方法包括优化电 参数、改进工作液循环系统和提 高电极材料质量等。
优化电极的损耗
电极的损耗会影响加工精度和表面质 量,因此优化电极的损耗是提高加工 精度的关键措施之一。
优化电极损耗的方法包括选择合适的 电极材料、减小电极截面尺寸和采用 电极修整技术等。
选用合适的加工液
加工液的选用对电火花加工精度和表面质量有重要影响。选 用合适的加工液可以减小工件表面粗糙度和提高加工精度。
案例二
在某大型模具的电火花加工中,采用 先进的数控技术,实现了高精度、高 效率的加工,提高了模具的成品率和 使用寿命。
案例三
针对某航空零件的电火花加工,通过 引入先进的误差补偿技术,有效减小 了加工误差,提高了零件的几何精度 和表面质量。
未来研究方向与展望
研究方向一
深入研究电火花加工过程的物理机制和数学模型,为进一步提高加工 精度提供理论支持。
加工参数的选择
工作液的选用
加工参数的选择对加工精度和表面质量有 很大影响,需要根据实际情况选择合适的 加工参数。
工作液的选用对电火花加工精度和表面质 量有较大影响,需要选择合适的工作液, 以保证加工精度和表面质量。
数控电火花线切割加工
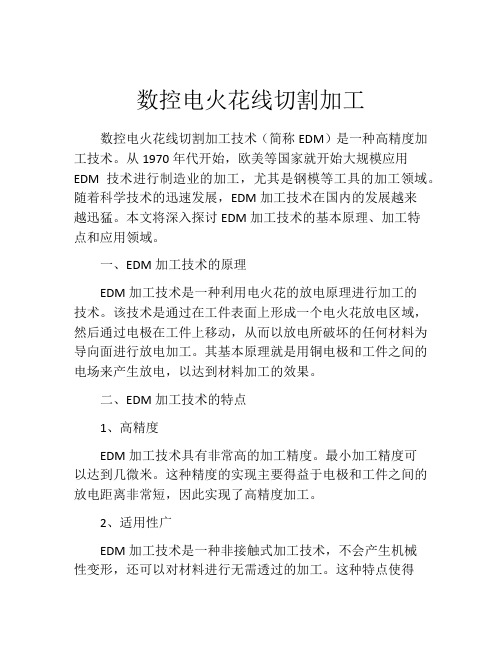
数控电火花线切割加工数控电火花线切割加工技术(简称EDM)是一种高精度加工技术。
从1970年代开始,欧美等国家就开始大规模应用EDM技术进行制造业的加工,尤其是钢模等工具的加工领域。
随着科学技术的迅速发展,EDM加工技术在国内的发展越来越迅猛。
本文将深入探讨EDM加工技术的基本原理、加工特点和应用领域。
一、EDM加工技术的原理EDM加工技术是一种利用电火花的放电原理进行加工的技术。
该技术是通过在工件表面上形成一个电火花放电区域,然后通过电极在工件上移动,从而以放电所破坏的任何材料为导向面进行放电加工。
其基本原理就是用铜电极和工件之间的电场来产生放电,以达到材料加工的效果。
二、EDM加工技术的特点1、高精度EDM加工技术具有非常高的加工精度。
最小加工精度可以达到几微米。
这种精度的实现主要得益于电极和工件之间的放电距离非常短,因此实现了高精度加工。
2、适用性广EDM加工技术是一种非接触式加工技术,不会产生机械性变形,还可以对材料进行无需透过的加工。
这种特点使得EDM加工技术被广泛应用于制造业的各个领域,如钢模、微孔加工、局部加热、特种材料加工等领域。
3、加工效率高EDM加工技术擅长处理小型工件,能够以高速度进行加工,并且适合加工硬度较高的材料。
其加工速度比传统加工方式快数倍。
同时,EDM加工技术还可以实现多种复杂形状的加工。
三、EDM加工技术的应用1、模具加工在模具的制造过程中,EDM加工技术几乎不可或缺。
在制造钢模等高精度模具时,人们越来越依赖EDM加工技术来提高高精度模具的生产效率和质量。
例如EDM加工技术可以用来制造汽车制动器,轮胎、零部件等。
2、微孔加工EDM加工技术在微细加工领域也具有潜力,可以用来加工出各类细小的孔洞和小圆形孔,例如墨盒的喷嘴孔、医疗器械的药孔等。
3、局部加热EDM在融合、碳化、钎焊和热处理等领域中,可充当局部加热剂,并被广泛地应用。
四、EDM加工技术发展趋势随着科学技术的不断发展,EDM加工技术还有很多的发展方向和潜力。
电火花加工中的加工深度和精度控制
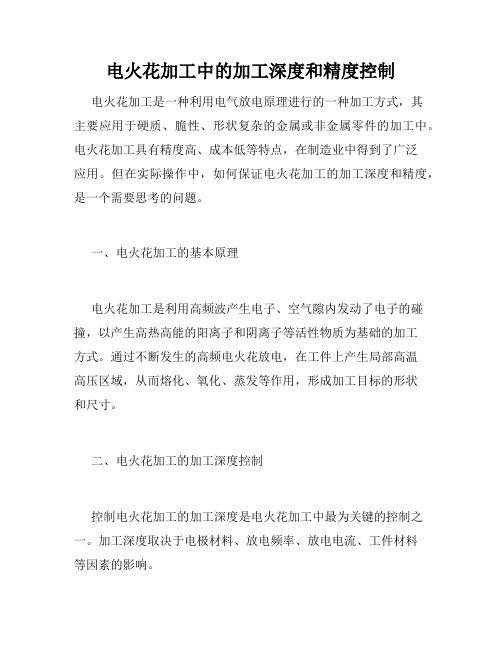
电火花加工中的加工深度和精度控制电火花加工是一种利用电气放电原理进行的一种加工方式,其主要应用于硬质、脆性、形状复杂的金属或非金属零件的加工中。
电火花加工具有精度高、成本低等特点,在制造业中得到了广泛应用。
但在实际操作中,如何保证电火花加工的加工深度和精度,是一个需要思考的问题。
一、电火花加工的基本原理电火花加工是利用高频波产生电子、空气隙内发动了电子的碰撞,以产生高热高能的阳离子和阴离子等活性物质为基础的加工方式。
通过不断发生的高频电火花放电,在工件上产生局部高温高压区域,从而熔化、氧化、蒸发等作用,形成加工目标的形状和尺寸。
二、电火花加工的加工深度控制控制电火花加工的加工深度是电火花加工中最为关键的控制之一。
加工深度取决于电极材料、放电频率、放电电流、工件材料等因素的影响。
1、电极材料电极材料的选择会对加工深度产生一定的影响,正常情况下,电极材料较软时,加工深度较小;电极较硬时,加工深度较深。
一般来说,电极材料应该尽量选用成分稳定、均匀的高温材料,如铜、银、钨等。
2、放电频率放电频率是指每秒钟反复发生的电火花放电次数,也是影响加工深度的因素之一。
放电频率越高,对工件的加工深度影响越小。
3、放电电流放电电流越大,加工深度越大。
但在实际应用中,过大的电流对电极的消耗也会变大,同时也会导致工件表面的粗糙度增加。
4、工件材料工件材料也是影响加工深度的因素之一。
一般来说,工件硬度越大,加工深度就会越小。
同时,工件的导热性能也会影响加工深度。
导热性差的工件可以通过提高工件表面温度,从而使电火花的能量有效地转移到加工目标上,提高加工深度。
三、电火花加工的加工精度控制除了加工深度的控制外,电火花加工中还需要控制其加工精度,从而保证加工质量的稳定性和一致性。
1、电极材料电极材料对加工精度的影响也非常大。
一般来说,使用高稳定性的电极能有效地保证加工精度。
2、放电电流和电压放电电流和电压的稳定控制是保证加工精度的重要手段。
《机械零件加工》数控电火花成型加工
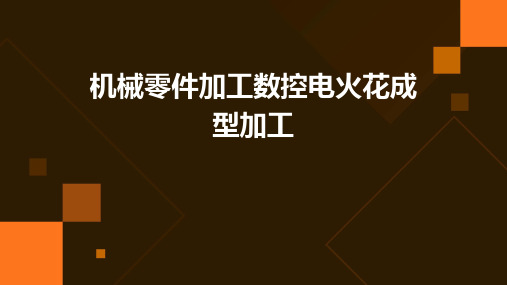
开始加工
启动机床,开始电火花成型加工。
加工过程监控
实时监控加工过程中的放电状态、电极磨损情况 等,及时调整参数。
加工完成
达到预定加工深度后,停止机床运行,取出工件进行检 验。
加工参数及影响因素
伺服进给速度
决定电极与工件的相对运动速 度,影响加工精度和效率。
工作液
用于冷却和排屑,其成分和浓 度影响放电稳定性和加工质量。
了解设备的价格、售后服务和技术支持等情况,进行综 合评估。
05
数控电火花成型加工工艺 设计
工艺路线规划
零件分析与工艺性估
对零件图纸进行详细分析,了解零件的结构特点、尺寸精 度和表面质量要求,评估其工艺性,确定加工难点和关键 工艺。
加工方法选择
根据零件的材料、硬度、形状复杂程度和加工精度要求, 选择合适的电火花成型加工方法,如电火花穿孔、电火花 线切割等。
仿真验证
在编程软件中,对编制好的数控 程序进行仿真验证,检查电极形 状、加工路径和干涉情况,确保 程序的正确性。
实际操作步骤及注意事项
电极装夹与定位
将电极装夹在机床主轴上,并进行精确的定位和找正,确保电极与工 件之间的相对位置精度。
工件装夹与找正
将工件装夹在机床工作台上,并进行精确的找正,确保工件的加工精 度和稳定性。
机械零件加工数控电火花成 型加工
目录
• 引言 • 数控电火花成型加工原理 • 机械零件加工需求分析 • 数控电火花成型加工设备介绍 • 数控电火花成型加工工艺设计 • 数控电火花成型加工实施过程 • 数控电火花成型加工效果评价
01
引言
目的和背景
提高加工精度
提高生产效率
数控电火花成型加工技术能够实现高 精度、高质量的机械零件加工,满足 现代制造业对高精度零件的需求。
第7章数控电火花加工工艺
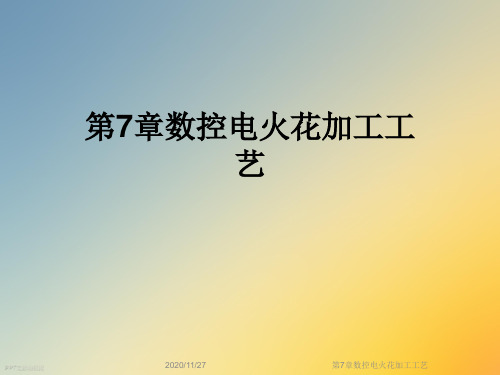
PPT文档演模板
第7章数控电火花加工工艺
7.1 数控电火花成形加工
PPT文档演模板
•图 7-9 加工液的处理方式
第7章数控电火花加工工艺
7.1 数控电火花成形加工
(3)吸引法也分为电极吸引法及底孔吸引法。如图7-9(c)和 图7-9(d)所示。
吸引法常用在深孔的精加工,在数控电火花机床上进行螺纹、 斜齿轮加工时,也常使用,但是由于这时加工液的路径较长而且 是螺线形,所以最好在电极的侧面加工出像丝锥沟那样的槽,以 利于加工液的流通如图7-10所示。
PPT文档演模板
第7章数控电火花加工工艺
7.1 数控电火花成形加工
PPT文档演模板
•图7-10 螺纹电极侧面切槽
第7章数控电火花加工工艺
7.1 数控电火花成形加工
(4)喷射法。喷射法一般采用如图7-11所示方式,主要用于 窄小的不通缝隙加工。
PPT文档演模板
•图7-11 喷射法
第7章数控电火花加工工艺
PPT文档演模板
第7章数控电火花加工工艺
7.1 数控电火花成形加工
PPT文档演模板
•图7-1 数控电火花成形加工
第7章数控电火花加工工艺
7.1 数控电火花成形加工
电火花成形加工须具备以下条件:
(1)自动进给调节系统保证工件与电极之间经常保持一定距 离以形成放电间隙。一般为0.01~0.1mm左右,间隙不能过大或过小。 间隙过大,极间电压不能击穿极间介质,无法产生电火花。间隙 过小、容易形成短路接触,同样不能产生电火花。
7.1 数控电火花成形加工
(2)电火花加工的适用范围。如图7-4所示为电火花加工的适用 范围,具体有以下几方面:
① 可以加工任何难加工的金属材料和导电材料。
数控电火花加工的主要工艺指标及其提高途径

勇于开始,才能找到成功的路
t
i
=
1200s
电 极 —纯 铜 工 件 —钢 加 工 极 性 —正
隙来不及消电离引起加工
稳定性变差,导致加工速
0 100 200 300 400 500 600 to / s
度降低。
图2 脉冲间隔与加工速度的关系曲线
• 3.峰值电流的影响
当脉冲宽度和脉冲间隔一定时,
vw / (mm3 / min)
在电火花加工过程中会不断产生气体、金属 屑末和碳黑等,如不及时排除,则加工很难 稳定地进行。加工稳定性不好,会使脉冲利 用率降低,加工速度降低。为便于排屑,一 般都采用冲油(或抽油)和电极抬起的办法。
冲(抽)油压力的影响度的关 系曲线
在加工中对于工件型腔较浅或易 于排屑的型腔,可以不采取任何 辅助排屑措施。但对于较难排屑 的加工,不冲(抽)油或冲(抽)油压 力过小,则因排屑不良产生的二 次放电的机会明显增多,从而导 致加工速度下降;但若冲油压力 过大,加工速度同样会降低。
0
10
100 1000 ti / s
图6 电极材料和加工极性对加工速度的影响
• 在加工中选择极性,不能只考虑加工速度,还必须考虑电极 损耗。如用石墨做电极时,正极性加工比负极性加工速度高, 但在粗加工中,电极损耗会很大。故在不计电极损耗的通孔 加工、取折断工具等情况,用正极性加工;而在用石墨电极 加工型腔的过程中,常采用负极性加工。
数控电火花加工的主要 工艺指标及其提高途径
2021/7/16
一、影响加工速度的主要因素
• 1 加工速度VWA:用以反映加工效率的
重要指标,通常所说的加工快慢。
(mm2/min)
• 影响加工速度的因素分电参数和非电参数两大
电火花加工精度的改善措施
引入先进控制技术
加强工艺研究和经验积累
如模糊控制、神经网络等,实现加工过程 的实时监测和智能调整,进一步提高加工 精度和效率。
深入研究电火花加工过程中的各种影响因 素,总结和积累实践经验,不断完善和优 化加工工艺。
未来研究方向和挑战
复合加工技术研究 将电火花加工与其他加工方法相 结合,形成复合加工技术,以进 一步提高加工精度和效率。
采用高精度滚珠丝杠、直线导轨等传动元件,确保机床各轴的高精度运
动。
03
控制系统升级
采用高性能数控系统,实现加工过程的精确控制,提高加工精度和稳定
性。同时,引入先进的自适应控制算法,实时调整加工参数,以应对不
同工况下的加工需求。
04
实施措施与效果验证
改善措施的实施计划
1. 设备升级与更新
2. 优化加工工艺参数
加工能量控制
放电能量的大小和持续时间直接 影响到工件的去除速度和加工精 度。
加工精度的重要性
01
02
03
产品质量
高精度的电火花加工能确 保产品几何形状和尺寸精 度符合设计要求,提高产 品质量。
性能保障
精确的加工能减少工件表 面的损伤和残余应力,保 障产品的力学性能和稳定 性。
降低成本
提高加工精度可以减少废 品率和返工率,降低生产 成本。
。
工作液选择
选择合适的工作液,如煤油、去离 子水等,以改善放电条件,提高加 工稳定性和精度。
加工速度调整
在保证加工精度的前提下,适当提 高加工速度,以实现高效高精度电 火花加工。
增强机床精度和稳定性
01
机床结构设计优化
采用高刚度、低热变形的机床结构,减少加工过程中的振动和变形,提
数控精密电火花加工技术
图1-2电火花线切割加工机
数控精密电火花加工技术
电火花线切割加工在特种加工中它又属于电火花加 工一类,是直接利用电能和热能进行加工的工艺方法。加 工时电极丝与工件在X、Y及U、V两个水平方向同时有相 对伺服进给运动及垂直方向的直线相对运动。因为这种方 法是用一根移动着的金属线(电极丝)作为工具电极与工件 之间产生火花放电对工件进行切割,故称为线切割加工。
数控精密电火花加工技术
数控精密电火花加工技术
表1.1常见电火花加工的分类情况及各类加工方法的主要特点与用途
电火花成形 加工
特点
①工具和工件间主要只有一个 相对的伺服进给运动
②工具为成形电极,与被加工 表面有相同的截面和相反的形 状
电火花线切 割加工
①工具电极为顺电极丝轴线方 向转动着的线状电极
②工具与工件在两个水平方向 同时有相对伺服进给运动
用途
①穿孔加工:加工各 种冲模、挤压模、粉 末冶金模、各种异形 孔及微孔等 ②型腔加工:加工各 类型腔模及各种复杂
的型腔零件
①切割各种冲模和具 有直纹面的零件 ②下料、截割和窄缝 加工
说明
约占在电火花机床总 数的30 % ,典型机床 有北京阿奇SE系列及 日本SodickAM系列等 电火花成形机床
约占电火花机床总数 的60%,典型机床有 DK7725及日本Sodick AQ数控电火花线切割 机床
电火花高速 小孔加工
①采用细管电极,管内冲人高 压水基工作液②细管电极旋转 ③穿孔速度较高
①线切割穿丝预孔
约占电火花机床的2.5
②深径比很大的小孔, % , 典型机床有北京
如喷嘴小孔等
阿奇SD1 电火花小孔
加工机床
数控精密电火花加工技术
数控电火花加工技术
❖⑤-⑥: 脉冲截止,极间电压下降、电流下 降
电火花加工的三个必备条件
❖1.电极和被加工表面之间必须保持一定大 小的放电间隙
❖没有间隙意味着电极与工件直接接触,整 个电路呈直接导通状态,不可能产生电火 花;间隙过大将无法击穿绝缘介质,不会 产生火花放电;间隙过小易形成短路,不 能正常放电加工。
❖2.必须使用单向脉冲电
电火花成形加工机床的电源
❖ 1)高低压复合脉冲
❖ 所谓高低压复合脉冲,就是在每个低压脉冲电压 (60~90V)波形上叠加一个小能量的高压(约 300V)脉冲,如图所示。低压脉冲的特点是电压 低、电流大,主要起蚀除加工作用,所在回路称 为加工回路;高压脉冲的特点是电压高、电流小、 能量小,主要起击穿间隙作用,所在回路称为高 压引燃回路。加工时先由高压回路击穿间隙,再 由低压回路放电加工,可大大提高脉冲的击穿率 和利用率,加工过程稳定,在“钢打钢”时显示 出很大的优越性。
❖ 一旦进入脉冲间隔期,电压和电流迅速下降至零, 导致温度骤然下降。失去电磁场的压缩作用,气 泡会爆炸,爆炸力使熔融的金属飞离工件表面, 向周围排射并撞击电极,如图所示。若电极为脆 性或结构疏松的材料,并且此时得不到及时冷却 时,电极会出现撞击损耗。
❖7)一个脉冲结束时,由于材料被移除,工 件上产生了一个凹坑,未被抛离的熔融金 属凝固成重铸层,如图所示。
❖新的工作液涌入型腔,冲走杂质,冷却工 件和电极表面,恢复两极间的绝缘状态。
❖8)被抛离的金属凝固成圆形小颗粒并分散 在工作液中,如图所示,没有破碎的气泡 浮到工作液表面,紧接着下一个放电周期 又开始了。
❖总体看来,一个脉冲周期内两极间的电压、 电流经历了如图所示的变化:
❖①-②: 电源输出脉冲,极间电压上升 ❖②-③: 击穿延时 ❖③: 击穿点 ❖③-④: 击穿后,极间电压下降、电流增大 ❖④-⑤: 火量柱下面的材料将处 于熔融状态。
《模具特种加工实训》题库
现代模具特种加工实训——电火花加工实训习题集一、填空题1、电火花加工是将电极形状到工件上的一种工艺方法。
2、数控电火花机床数控摇动的伺服方式有、、。
3、是放电时工具电极和工件之间的距离。
4、电火花加工中常用的电极结构形式是、、。
5、在用法校正电极丝垂直度时,电极丝要运转以免电极丝断裂。
6、电化学加工包括从工件上去除金属的加工和向工件上沉积金属、加工两大类。
7、线切割加工的主要工艺指标是、、、。
8、是直接利用、、、、、及等能量达到的加工方法。
9、电火花线切割加工的根本原理是用移动的作电极,对工件进行,切割成形。
10、数控电火花线切割机床能加工各种、、导电材料。
11、第一台实用的电火花加工装置的是、的拉扎林科夫妇发明的。
12、电火花线切割加工中被切割的工件作为,电极丝作为。
电极丝接脉冲电源的,工件接脉冲电源的。
13、根据走丝速度,电火花线切割机通常分为两大类:一类是电火花线切割机或往复走丝电火花线切割机,这类机床的电极作高速往复运动,一般走丝速度为8—10m/s ,用于加工中、低精度的模具和零件。
快走丝数控线切割机床目前能到达的加工精度为正负0.01mm ,表面粗糙度Ra= 2.5—0.6um 。
另一类是电火花线切割机或单向走丝电火花线切割机,一般走丝速度低于0.2m/s ,用于加工高精度的模具和零件。
慢走丝数控线切割机床的加工精度可达正负0.001um ,表面粗糙度Ra< 0.32 。
14、高速走丝线切割机主要由、、三大部分组成。
15、高速走丝电火花线切割机的导电器有两重:一重是的,电极丝与导电器的圆柱面接触导电,可以轴向移动和圆周转动以满足多次使用的要求;另一重是的薄片,电极丝与导电器的大面积接触导电,方形薄片的移动和圆形薄片的转动可满足多次使用的要求。
16、线切割加工中罕用的电极丝有、、和。
其中和应用快速走丝线切割中,而应用慢速走丝线切割。
17、线切割加工时,工件的装夹方式有装夹,装夹,装夹,和装夹。
- 1、下载文档前请自行甄别文档内容的完整性,平台不提供额外的编辑、内容补充、找答案等附加服务。
- 2、"仅部分预览"的文档,不可在线预览部分如存在完整性等问题,可反馈申请退款(可完整预览的文档不适用该条件!)。
- 3、如文档侵犯您的权益,请联系客服反馈,我们会尽快为您处理(人工客服工作时间:9:00-18:30)。
vw / (mm3 / min)
电 极 —纯 铜
工 件 —钢
1000
^i
=
e
150^ieA=
80
A
加
工
极
性
—正
i^e= 40 A
100
^ie= 30 A
较大部分散失在电极与工件之中,
不起蚀除作用。同时,在其它加工 条件相同时,随着脉冲能量过分增 大,蚀除产物增多,排气排屑条件
10 01
10 100 1000 ti /s
冲(抽)油压力的影响度的关 系曲线
在加工中对于工件型腔较浅或易 于排屑的型腔,可以不采取任何 辅助排屑措施。但对于较难排屑 的加工,不冲(抽)油或冲(抽)油压 力过小,则因排屑不良产生的二 次放电的机会明显增多,从而导 致加工速度下降;但若冲油压力 过大,加工速度同样会降低。
这是因为冲油压力过大,产生干 扰,使加工稳定性变差,故加工 速度反而会降低。图5是冲油压 力和加工速度关系曲线。
电火花加工的主要工艺指标及其提 高途径
• 目标 • 一、影响加工速度的主要因素
• 二、影响电极损耗的主要因素
• 三、 影响加工精度的主要因素 • 四、加工表面质量及其影响因素
一、影响加工速度的主要因素
• 1 加工速度VWA:用以反映加工效率的
重要指标,通常所说的加工快慢。
(mm2/min)
• 影响加工速度的因素分电参数和非电参数两大
恶化,间隙消电离时间不足导致拉
弧,加工稳定性变差等。因此加工 图1 脉冲宽度与加工速度的关系曲线
速度反而降低。
• 2.脉冲间隔对加工速度 的影响
在脉冲宽度一定的条件下, vw / (mm3 / min)
若脉冲间隔减小,则加工 300 速度提高(如图2)。但若脉 200 冲间隔过小,会因放电间 100
从图4可看出,峰值电流不同, 最小临界加工面积也不同。因 此,确定一个具体加工对象的 电参数时,首先必须根据加工 面积确定工作电流,并估算所 需的峰值电流。
图4 加工面积与加工速度的关系曲线
• (2)排屑条件的影响
在电火花加工过程中会不断产生气体、金属 屑末和碳黑等,如不及时排除,则加工很难 稳定地进行。加工稳定性不好,会使脉冲利 用率降低,加工速度降低。为便于排屑,一 般都采用冲油(或抽油)和电极抬起的办法。
vw/ (mm3 / min)
300
ti= 1200s
200
to= 400s电 极 — Nhomakorabeau 工 件 —T10A 加 工 极 性 —负
100
0 0.01 0.03 0.05 0.07 0.09 P / (kg / c3m)
图5 冲油压力和加工速度的关系曲线
•(3)电极材料的影响
vw / (mm3 / min) 工 件 材 料 —钢
ti= 1200s
电 极 —纯 铜 工 件 —钢 加 工 极 性 —正
隙来不及消电离引起加工
稳定性变差,导致加工速
0 100 200 300 400 500 600 to / s
度降低。
图2 脉冲间隔与加工速度的关系曲线
• 3.峰值电流的影响
当脉冲宽度和脉冲间隔一定时,
随着峰值电流的增加,加工速
度也增加(如图3)。因为加大峰
• 5).工作液的影响
• 在电火花加工中,工作液的种类、粘度、清洁度对加 工速度有影响。就工作液的种类来说,大致顺序是: 高压水>(煤油+机油)>煤油>酒精水溶液。在电火花成 形加工中,应用最多的工作液是煤油。
二、影响电极损耗的主要因素
电极损耗是电火花成型加工中的重要工艺指标。 在生产中,衡量某种工具电极是否耐损耗,不 只是看工具电极损耗速度VE的绝对值大小,还 要看同时达到的加工速度VW,即每蚀除单位重 量金属工件时,工具相对损耗多少。因此,常 用相对损耗或损耗比作为衡量工具电极耐损耗 的指标,即VW/VE 电火花加工中,电极的相对损耗小于1%,称 为低损耗电火花加工。
值电流,等于加大单个脉冲能
量,所以加工速度也就提高了。
但若峰值电流过大(即单个脉冲 放电能量很大),加工速度反而
下降。此外,峰值电流增大将
降低工件表面粗糙度和增加电
极损耗。在生产中,应根据不
同的要求,选择合适的峰值电
流。
图3 峰值电流与加工速度的关系曲线
• 2 非电参数的影响 (1)加工面积的影响
• 由上所述,电极材料对电火花加工非常重要,正确选择电极 材料是电火花加工首要考虑的问题。
• 4)工件材料的影响
• 在同样加工条件下,选用不同工件材料,加工速度也 不同。这主要取决于工件材料的物理性能(熔点、沸点、 比热、导热系数、熔化热和汽化热等)。
• 一般说来,工件材料的熔点、沸点越高,比热、熔化 潜热和气化潜热越大,加工速度越低,即越难加工。 如加工硬质合金钢比加工碳素钢的速度要低40~60%。 对于导热系数很高的工件,虽然熔点、沸点、熔化热 和气化热不高,但因热传导性好,热量散失快,加工 速度也会降低。
• 从图6还可看出,在同样加工条件和加工极性情况下,采用不 同的电极材料,加工速度也不相同。例如,中等脉冲宽度、 负极件加工时,石墨电极的加工速度高于铜电极的加工速度。 在脉冲宽度较窄或很宽时,铜电极加工速度高于石墨电极。 此外,采用石墨电极加工的最大加工速度,比用铜电极加工 的最大加工速度的脉冲宽度要窄。
0
10
100 1000 ti / s
图6 电极材料和加工极性对加工速度的影响
• 在加工中选择极性,不能只考虑加工速度,还必须考虑电极 损耗。如用石墨做电极时,正极性加工比负极性加工速度高, 但在粗加工中,电极损耗会很大。故在不计电极损耗的通孔 加工、取折断工具等情况,用正极性加工;而在用石墨电极 加工型腔的过程中,常采用负极性加工。
500
Gr+ 1
Gr- 1
200 Cu- 1
100 Gr- 3
50 Cu- 3
20
Gr+ 1—石 墨 正 极^ie性= 42 A Gr- 1—石 墨 负 极i^e性= 42 A Cu- 1—紫 铜 负 极i^e性= 42 A Gr- 3—石 墨 负 极i^e性= 14 A Cu- 3—紫 铜 负 极i^e性= 14 A
类。电参数主要是脉冲电源输出波形与参数;非电 参数包括加工面积、深度、工作液种类、冲油方式、 排屑条件及电极的材料、形状等。
电规准的影响
所谓电规准,是指电火花加工时选用的电 加工参数,主要有脉冲宽度ti(μs)、脉冲间 隙to(μs)及峰值电流Ip等参数。
• 一. 脉冲宽度对加工速度
的影响
脉冲宽度增加,加工速度随 之增加,因为随着脉冲宽度的增加, 单个脉冲能量增大,使加工速度提 高。但若脉冲宽度过大,加工速度 反而下降(如图1)。这是因为单个脉 冲能量虽然增大,但转换的热能有