7挤出成型工艺及模具设计.pptx
合集下载
挤出成型工艺及模具设计_课件
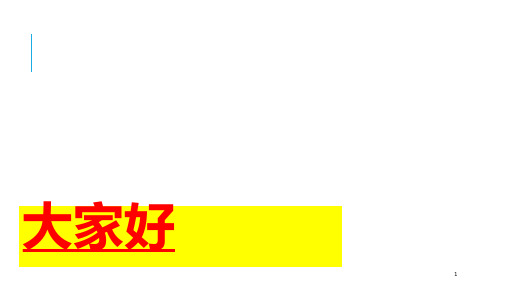
9
二、挤出成型机头概述
1. 挤出机头的作用 使熔融塑料由螺旋运动变为直线运动; 产生必要的成型压力,保证制品密实; 使塑料通过机头得到进一步塑化; 通过机头口模以获得截面形状相同、连续的塑料制品。
10
2. 机头的分类
按机头的几何形状分类 圆环机头:管材机头、棒材机头、造粒机头等 平板状机头:平模机头、板材机头、异型材机头等
内装置电热器时导入导线。
38
2. 管材的定径和冷却
为了使管材获得较低的表面粗糙值、准确的尺寸和几何 形状,管材离开口模时,必须立即进行定径和冷却,由定 径套来完成。
有两种方法: ❖ 外径定型 ❖ 内径定型
我国塑料管材标 准大多规定外径为基 本尺寸,故国内较常 用外径定型法。
39
(1)外径定型 适用于管材外径尺寸精度要求高、外表面粗糙度要求低的
按机头进出料方向分类 水平直通式机头 直角式机头
按机头的用途分类 吹膜机头、管材机头、板材机头、棒材机头、异型材 机 头等。
11
3.挤出机头的组成(以直通式管材机头为例)
口模 芯棒 分流器和分流器支架 机头体 过滤网和过滤板 连接部分 定径套
12
① 口模和芯棒 ② 挤出模的主要成型零件,口模用来成型塑件的外表
41
(2)内径定型
通过定径套内的循环水冷却定型 特点:保证管材内孔圆度,操作方便;宜用于直角式挤管机头
和旁侧式挤管机头。
适用:内径尺寸要求准确、圆度要求高的情况。
1-管材 2-定径芯模 3-芯棒 4-回水流道
5-进水管 6-排水管 7-进水嘴
42
定径芯长度:与管材壁厚及牵引速度有关,一般取80~ 300mm,牵引速度和壁厚大时,取大值。反之,取小值。 定径芯直径:一般比管材内径直径大2%~4%,始端比终端 直径大,锥度为0.6:100~1.0:100。
二、挤出成型机头概述
1. 挤出机头的作用 使熔融塑料由螺旋运动变为直线运动; 产生必要的成型压力,保证制品密实; 使塑料通过机头得到进一步塑化; 通过机头口模以获得截面形状相同、连续的塑料制品。
10
2. 机头的分类
按机头的几何形状分类 圆环机头:管材机头、棒材机头、造粒机头等 平板状机头:平模机头、板材机头、异型材机头等
内装置电热器时导入导线。
38
2. 管材的定径和冷却
为了使管材获得较低的表面粗糙值、准确的尺寸和几何 形状,管材离开口模时,必须立即进行定径和冷却,由定 径套来完成。
有两种方法: ❖ 外径定型 ❖ 内径定型
我国塑料管材标 准大多规定外径为基 本尺寸,故国内较常 用外径定型法。
39
(1)外径定型 适用于管材外径尺寸精度要求高、外表面粗糙度要求低的
按机头进出料方向分类 水平直通式机头 直角式机头
按机头的用途分类 吹膜机头、管材机头、板材机头、棒材机头、异型材 机 头等。
11
3.挤出机头的组成(以直通式管材机头为例)
口模 芯棒 分流器和分流器支架 机头体 过滤网和过滤板 连接部分 定径套
12
① 口模和芯棒 ② 挤出模的主要成型零件,口模用来成型塑件的外表
41
(2)内径定型
通过定径套内的循环水冷却定型 特点:保证管材内孔圆度,操作方便;宜用于直角式挤管机头
和旁侧式挤管机头。
适用:内径尺寸要求准确、圆度要求高的情况。
1-管材 2-定径芯模 3-芯棒 4-回水流道
5-进水管 6-排水管 7-进水嘴
42
定径芯长度:与管材壁厚及牵引速度有关,一般取80~ 300mm,牵引速度和壁厚大时,取大值。反之,取小值。 定径芯直径:一般比管材内径直径大2%~4%,始端比终端 直径大,锥度为0.6:100~1.0:100。
塑料挤出成型工艺及模具设计
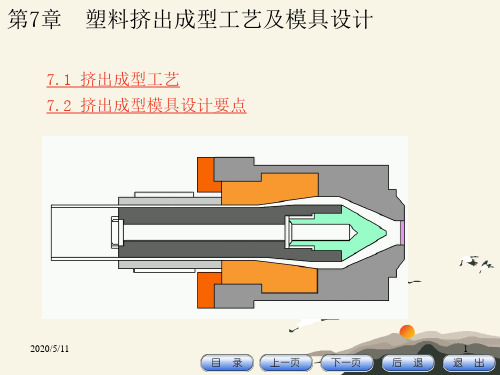
第7章 塑料挤出成型工艺及模具设计
7.1 挤出成型工艺 7.2 挤出成型模具设计要点
2018/11/26
1
第7章 塑料挤出成型工艺及模具设计
7.1 挤出成型工艺 7.2 挤出成型模具设计要点
2018/11/26
2
7.1 挤出成型工艺
挤出成型是热塑性塑料重要的加工方法之一,
主要用于生产管材、棒材、板材、片材、线材和薄膜等连 续塑料型材。
16
2018/11/26
7.2
7.2.5 挤管机头设计要点
7.2.5.1 典型结构
常用的挤管机头有直通式、直角式与旁侧式三种。 7.2.5.2 直通式挤管机头工艺参数的确定
工艺参数主要包括口模、芯棒、分流器及分流器支 架的形状和尺寸。在设计时首先需有已知的数据,包括 挤出机型号、制品的内径、外径及制品所用的材料。
2018/11/26 19
②按管材壁厚计算: L1=nt (7-3)
D——管材外径的公称尺寸(mm)。 t——管材壁厚(mm);
2018/11/26 15
7.2
机头与挤出机的连接方式二: 机头以12个内六角螺钉与机头法兰连接固定,然后 机头法兰又与挤出机法兰以铰链螺栓连接,而且在两者 间有定位销1定位,保证同心度
1—定位销
2—机筒
3—螺杆 4—栅板 5—挤出机法兰 6—铰链 7—机头法兰 图7-7 机头连接形式之二 8—螺钉
2018/11/26 18
(7-1
7.2
(2)定型段长度L1:口模和芯棒的平直部分的长度称为定型段 塑料通过定型段,随着料流阻力增加使制品致密
定型段的长度过长:时会使料流阻力增加很大; 定型段的长度过短:起不到定型作用。 ①按管材外径计算: L1=(0.5~3)D (7-2) n——系数,见表7-6。 通常情况下,当管材直径较大时,长度应取小值,因这时 管材的被定型面积较大,阻力较大,反之就取大值。挤软管时 取大值,挤硬管时取小值。
7.1 挤出成型工艺 7.2 挤出成型模具设计要点
2018/11/26
1
第7章 塑料挤出成型工艺及模具设计
7.1 挤出成型工艺 7.2 挤出成型模具设计要点
2018/11/26
2
7.1 挤出成型工艺
挤出成型是热塑性塑料重要的加工方法之一,
主要用于生产管材、棒材、板材、片材、线材和薄膜等连 续塑料型材。
16
2018/11/26
7.2
7.2.5 挤管机头设计要点
7.2.5.1 典型结构
常用的挤管机头有直通式、直角式与旁侧式三种。 7.2.5.2 直通式挤管机头工艺参数的确定
工艺参数主要包括口模、芯棒、分流器及分流器支 架的形状和尺寸。在设计时首先需有已知的数据,包括 挤出机型号、制品的内径、外径及制品所用的材料。
2018/11/26 19
②按管材壁厚计算: L1=nt (7-3)
D——管材外径的公称尺寸(mm)。 t——管材壁厚(mm);
2018/11/26 15
7.2
机头与挤出机的连接方式二: 机头以12个内六角螺钉与机头法兰连接固定,然后 机头法兰又与挤出机法兰以铰链螺栓连接,而且在两者 间有定位销1定位,保证同心度
1—定位销
2—机筒
3—螺杆 4—栅板 5—挤出机法兰 6—铰链 7—机头法兰 图7-7 机头连接形式之二 8—螺钉
2018/11/26 18
(7-1
7.2
(2)定型段长度L1:口模和芯棒的平直部分的长度称为定型段 塑料通过定型段,随着料流阻力增加使制品致密
定型段的长度过长:时会使料流阻力增加很大; 定型段的长度过短:起不到定型作用。 ①按管材外径计算: L1=(0.5~3)D (7-2) n——系数,见表7-6。 通常情况下,当管材直径较大时,长度应取小值,因这时 管材的被定型面积较大,阻力较大,反之就取大值。挤软管时 取大值,挤硬管时取小值。
挤出成型工艺及模具设计

2020/3/31
2020/3/31
2020/3/31
三、管材挤出机机头的设计
常用的挤管机头有:直通式、直角式和旁侧式
直通式挤管机头
1-芯棒 2-口模 3-调节螺钉 4-分流器支架 5-分流器 6-加热器 7机头体
2020/3/31
2020/3/31
2020/3/31
挤出机头结构
1-管材 2-定型模 3-口 模 4-芯棒 5-调节螺钉 6-分流器 7-分流器支架 8-机头体 9-过滤网 10电加热圈
④ 压缩角 低粘度塑料45~ 60° ,高粘度塑料30 ~ 50° 。
2020/3/31
(3) 分流器和分流器支架 ① 分流器设计需确定的尺寸
❖分流器的角度α
低粘度塑料30°~80°, 高粘度塑料取30°~60°。
❖分流锥长度L3
L3 =(1~1.5) D0
❖分流器头部圆角半径r
取0.5~2mm
2020/3/31
② 分流器支架
① 支承分流器及芯棒,另外起搅拌物料的作用。 ② 小型机头,分流器和分流器支架可以做成一个整体。 ③ 为了消除塑料通过分流器后形成的接合线,分流器支架
上的分流肋应做成流线型,一般3~8根。 ④ 分流器支架设有进气孔和导线孔,用以通入压缩空气和
内装置电热器时导入导线。
2020/3/31
2020/3/31
④机头内设有调节装置
调节熔体流量、口模和芯棒侧隙、挤出压力、成型温度、 挤出速度等。
⑤合理选择材料
机头的零件要承受熔体的压力作用,所以要有足够的强度 。必要时对连接零件进行强度校核。
与熔体接触的零件要有足够的耐磨性和耐腐蚀性,必要时 表面要镀铬处理。主要零件进行调质处理,硬度45~ 50HRC。
2020/3/31
2020/3/31
三、管材挤出机机头的设计
常用的挤管机头有:直通式、直角式和旁侧式
直通式挤管机头
1-芯棒 2-口模 3-调节螺钉 4-分流器支架 5-分流器 6-加热器 7机头体
2020/3/31
2020/3/31
2020/3/31
挤出机头结构
1-管材 2-定型模 3-口 模 4-芯棒 5-调节螺钉 6-分流器 7-分流器支架 8-机头体 9-过滤网 10电加热圈
④ 压缩角 低粘度塑料45~ 60° ,高粘度塑料30 ~ 50° 。
2020/3/31
(3) 分流器和分流器支架 ① 分流器设计需确定的尺寸
❖分流器的角度α
低粘度塑料30°~80°, 高粘度塑料取30°~60°。
❖分流锥长度L3
L3 =(1~1.5) D0
❖分流器头部圆角半径r
取0.5~2mm
2020/3/31
② 分流器支架
① 支承分流器及芯棒,另外起搅拌物料的作用。 ② 小型机头,分流器和分流器支架可以做成一个整体。 ③ 为了消除塑料通过分流器后形成的接合线,分流器支架
上的分流肋应做成流线型,一般3~8根。 ④ 分流器支架设有进气孔和导线孔,用以通入压缩空气和
内装置电热器时导入导线。
2020/3/31
2020/3/31
④机头内设有调节装置
调节熔体流量、口模和芯棒侧隙、挤出压力、成型温度、 挤出速度等。
⑤合理选择材料
机头的零件要承受熔体的压力作用,所以要有足够的强度 。必要时对连接零件进行强度校核。
与熔体接触的零件要有足够的耐磨性和耐腐蚀性,必要时 表面要镀铬处理。主要零件进行调质处理,硬度45~ 50HRC。
第七章-挤出成型

5、螺杆的选用
(1)材料
对结晶型塑料:突变型螺杆
对无定型塑料:渐变型螺杆
等距不等深
等距不等深
(2)L/D
对硬塑料,塑化时间长,L/D大些;对粉末料,要求多 塑化一些时间, 应L/D大;对结晶型塑料, L/D大。
(3)A 根据不同的塑炼选用不同的压缩比。
例:硬料,A小;软料,A大。
(硬质PVC,A=2~3; 软质PVC,A=3~4)
▲ 料筒内壁光滑;
▲ 加料段特设纵向沟槽-物料与料筒表面的切向摩擦力
第二十四页,编辑于星期三:十六点 二十六分。
2、熔化理论(塑料的熔化过程)
塑料在压缩段是从固体状态到完全熔化状态,同时要受 到压缩作用,在该段,物料温升快,物料内摩擦作用大, 压缩作用大。
在压缩段塑料由固相 液相转变
物料受到挤压:压缩比的作用
螺杆的直径D
螺杆的压缩比A
螺杆角 θ
螺杆与料筒的间隙
螺杆的长径比L/Ds 螺槽深度H 螺纹棱部宽度E
第九页,编辑于星期三:十六点 二十六分。
▲ 螺杆的直径D
代表挤出机的规格。D ,挤出机的生产能力 。
▲ 螺杆的长径比L/Ds (15~25) 影响挤出机的产量和挤出质量(衡量塑化效率)。
L/Ds ,塑料的停留时间 ,混合塑化效果 。
如果忽略环流(QT)的影响,则均化段熔体的输送量(流率) 为:
Q=QD-(QP+QL)
与螺杆的结构参数、T、P、 有η 关。
宏观上看只有物料沿螺杆螺槽的轨迹运动。 图7-19
第三十三页,编辑于星期三:十六点 二十六分。
三、单螺杆挤出机产生能力的计算
1、实测法
在挤出机上测出制品从机头口模中挤出的线速度,由此来确 定产量,准确实观不通用。
【大学课件】塑料挤出成型工艺及模具设计PPT

1 口模 (1) 口模的内径D
巴鲁斯效应和冷却收缩等原因使塑件外径不等 于口模内径 确定口模的内径D方法1: 确定口模的内径D方法2:
D=d/K
I
D2 Ds2
d2 ds2
Page 17
7.3.1 直通式挤出机头工艺参数的确定
1 口模 (2) 定型段长度L1 口模与型棒的平直部分Байду номын сангаас长度成为定型段
第七章 塑料挤出成型工艺及模具设计
7.1挤出成型工艺 主要用于生产具有恒定截面形状的管材、
棒材、板材、片材、线材和薄膜等。
此外,也可用于塑料的着色造粒、 共混、中空塑件型坯的生产。
Page 2
7.1.1 挤出成型原理及特点
挤出成型优点: 连续成型、生产量大、
生产效率高、设备简单
Page 3
成本低、操作方便
7.1.2 挤出成型工艺过程
原材料的准备阶段 塑化阶段 成型阶段 定径阶段 塑件的牵引、卷曲和切割阶段
Page 4
7.1.3 挤出成型工艺参数
温度 压力 挤出速度 牵引速度
Page 5
7.2 挤出成型机头概述
挤出成型的模具成为挤出成型机头
7.2.1 挤出机头的作用及分类 1 挤出机头作用
Page 24
7.3.2 管材的定径和冷却
1 外径定径 外径定径适用于对管材外径尺寸精度要求高、 外表面粗糙度低的情况。 按照压力产生方式不同,外径定径又分为内压法 和真空法。
Page 25
Page 26
Page 27
Page 28
7.3.2 管材的定径和冷却
1 外径定径 (1) 内压法外定径 定型套内径径向尺寸应考虑管材定型后收缩因素、
确定分流器上的角度α,分流锥长度、分流器头部 圆角半径、分流器表面粗糙度、过滤版与分流器顶间隔
巴鲁斯效应和冷却收缩等原因使塑件外径不等 于口模内径 确定口模的内径D方法1: 确定口模的内径D方法2:
D=d/K
I
D2 Ds2
d2 ds2
Page 17
7.3.1 直通式挤出机头工艺参数的确定
1 口模 (2) 定型段长度L1 口模与型棒的平直部分Байду номын сангаас长度成为定型段
第七章 塑料挤出成型工艺及模具设计
7.1挤出成型工艺 主要用于生产具有恒定截面形状的管材、
棒材、板材、片材、线材和薄膜等。
此外,也可用于塑料的着色造粒、 共混、中空塑件型坯的生产。
Page 2
7.1.1 挤出成型原理及特点
挤出成型优点: 连续成型、生产量大、
生产效率高、设备简单
Page 3
成本低、操作方便
7.1.2 挤出成型工艺过程
原材料的准备阶段 塑化阶段 成型阶段 定径阶段 塑件的牵引、卷曲和切割阶段
Page 4
7.1.3 挤出成型工艺参数
温度 压力 挤出速度 牵引速度
Page 5
7.2 挤出成型机头概述
挤出成型的模具成为挤出成型机头
7.2.1 挤出机头的作用及分类 1 挤出机头作用
Page 24
7.3.2 管材的定径和冷却
1 外径定径 外径定径适用于对管材外径尺寸精度要求高、 外表面粗糙度低的情况。 按照压力产生方式不同,外径定径又分为内压法 和真空法。
Page 25
Page 26
Page 27
Page 28
7.3.2 管材的定径和冷却
1 外径定径 (1) 内压法外定径 定型套内径径向尺寸应考虑管材定型后收缩因素、
确定分流器上的角度α,分流锥长度、分流器头部 圆角半径、分流器表面粗糙度、过滤版与分流器顶间隔
《挤出工艺讲课用》课件
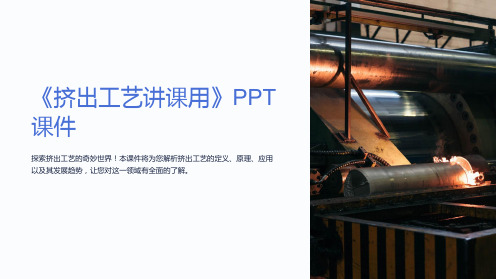
挤出工艺的应用展望
塑料包装材料 应用
探索塑料包装材料在 食品、医疗等领域的 广泛应用,满足人们 的需求。
人造板材加工 应用
了解人造板材挤出工 艺的加工特点,以及 用于家具、装饰等领 域。
生物质能源材 料应用
探索挤出工艺在生物 质能源材料领域的应 用,推动可再生能源 的发展。
未来发展方向 和创新机会
全球产业布局和市场前景
挤出工艺的全球产业布局和市场前景将带来更大的机遇和挑战。
挤出工艺的案例分析
1 塑料袋生产线
通过挤出工艺生产高品质的塑料袋,满足不同行业的包装需求。
2 PVC管材生产线
应用挤出工艺生产优质的PVC管材,用于建筑、电力等领域。
3 电缆绝缘材料生产线
利用高效的挤出工艺生产优质电缆绝缘材料,确保电力传输的安全可靠。
挤出工艺的过程
1
输送系统
将塑料颗粒输送到挤出机螺杆中。
加热和融合
2
通过电加热将塑料颗粒融化,并与其他
添加剂混合均匀。
3
模头结构和温度控制
根据产品要求,选择合适的模头结构,
挤出速度和拉伸速度
4
并进行温度控制。
控制挤出速度和拉伸速度,实现产品的 均匀挤出和拉伸。
产品特性与改进方法
塑料膜、片和薄板
探索塑料膜、片和薄板的特性, 以及改进方法,实现更高的质量 和可持续性。
《挤出工艺讲课用》PPT 课件
探索挤出工艺的奇妙世界!本课件将为您解析挤出工艺的定义、原理、应用 以及其发展趋势,让您对这一领域有全面的了解。
什么通过模头挤出加工成连续型材的技术。
原理
通过融化塑料颗粒,利用螺杆的推动,将熔化的塑料挤出成型。
应用
- 1、下载文档前请自行甄别文档内容的完整性,平台不提供额外的编辑、内容补充、找答案等附加服务。
- 2、"仅部分预览"的文档,不可在线预览部分如存在完整性等问题,可反馈申请退款(可完整预览的文档不适用该条件!)。
- 3、如文档侵犯您的权益,请联系客服反馈,我们会尽快为您处理(人工客服工作时间:9:00-18:30)。
①芯棒外径d d=D-2δ
δ-口模与芯棒的单边间隙, δ =(0.83~0.94)t 。
②定型长度段L1 与口模定型长度 L 相当或稍长。
③ 压缩段长度L2
④
压缩段 (也称锥面段) 主要作用是使进入定型区之前的
塑料熔体的分流痕迹被熔合消除。
L2=(1.5~2.5) D0
D0-塑料熔体在过滤板出口处的流道直径
④机头内设有调节装置
调节熔体流量、口模和芯棒侧隙、挤出压力、成型温度、 挤出速度等。
⑤合理选择材料
机头的零件要承受熔体的压力作用,所以要有足够的强度。 必要时对连接零件进行强度校核。
与熔体接触的零件要有足够的耐磨性和耐腐蚀性,必要时 表面要镀铬处理。主要零件进行调质处理,硬度45~ 50HRC。
挤出成型设备——挤出机
④ 压缩角 低粘度塑料45~ 60° ,高粘度塑料30 ~ 50° 。
(3) 分流器和分流器支架 ① 分流器设计需确定的尺寸
❖分流器的角度α
低粘度塑料30°~80°, 高粘度塑料取30°~60°。
❖分流锥长度L3
L3 =(1~1.5) D0
❖分流器头部圆角半径r
取0.5~2mm
② 分流器支架
① 支承分流器及芯棒,另外起搅拌物料的作用。
② 小型机头,分流器和分流器支架可以做成一个整体。
③ 为了消除塑料通过分流器后形成的接合线,分流器支架 上的分流肋应做成流线型,一般3~8根。
挤出机:挤出系统、传动系统、加热冷却系统、机身
辅机: 机头、定型装置、冷却装置、牵引装置、切割
装置、卷取装置 控制系统
2. 挤出成型工艺过程
原材料准备
塑化
挤出成型
冷却定型
塑件的牵引、 卷曲、切割
挤塑生产线
3. 挤出成型工艺参数
① 温度
❖ 加料段的温度不宜过高,压缩段和均化段的温度可高一些 ❖ 机头的温度控制在塑料热分解温度以下 ❖ 口模的温度比机头温度可稍低一些,但要保证塑料有良
② 足够的压缩比
为了使塑件结构密实和消除分流器支架造成的熔料接合缝, 机头应该有一定的压缩比的压缩区域。低粘度塑料压缩比取 4~10,高粘度塑料在2.5~6为宜。
③ 正确的成型区截面形状及尺寸
口模的形状及尺寸和塑件的形状及尺寸并不是一致的。熔 体膨胀和牵引力引起的收缩变形,会使塑件的尺寸与口模尺寸 产生一定的偏差。所以在设计时要考虑这一因素。
1. 直通式挤管机头工艺参数的确定
2. (1) 口模
① 口模内径D ❖经验公式: D = d /K
d——管材外径 K——补偿系数
❖按拉伸比确定
② 定型段长度L
❖ 按管材外径:L=(0.5~3)d ❖ 按管材壁厚:L=nt
(2) 芯捧(芯模)
芯棒与分流器之间通过螺纹连接,其中心孔用来通入压 缩空气,以便对管材产生内压,实现外径定径。
第7章 塑料挤出成型工 艺及模具设计
一、挤出成型工艺
挤出成型是热塑性塑料重要的加工方法之一,主要用 于生产管材、棒材、板材、片材、线材和薄膜等连续塑料 型材。
1、挤出成型原理
将颗粒状或粉状塑料加入挤出机料筒内,在旋转的挤出机
螺杆的作用下,塑料沿螺杆的螺槽向前方输送。在此过程中, 不断地接受外加热和摩擦热,逐渐熔融成粘流态,然后在挤 压系统的作用下,塑料熔体经过滤板后通过具有一定形状的 挤出模具(机头)口模以及一系列的辅助装置,从而获得等 横截面的各种型材。
按机头进出料方向分类 水平直通式机头 直角式机头
按机头的用途分类 吹膜机头、管材机头、板材机头、棒材机头、异型材 机 头等。
3.挤出机头的组成(以直通式管材机头为例)
口模 芯棒 分流器和分流器支架 机头体 过滤网和过滤板 连接部分 定径套
① 口模和芯棒
② 挤出模的主要成型零件,口模用来成型塑件的外表 面,芯棒用来成型塑件的内表面。通过调节螺钉5,可 调节口模和芯棒之间的间隙,从而控制塑件的壁厚。Βιβλιοθήκη 拆 出 的 口 模 状 况
拆 开 口 模 后 露 出 芯 棒 的 状 况
图8.1 挤出机头结构
1-管材 2-定型模 3-口模 4-芯棒 5-调节螺钉 6-分流器 7-分流器支架 8-机头体 9-过滤网 10-电加热圈
3. 挤出机头的设计原则
① 内腔呈流线型
各连接处不应该有使熔料滞留的死角,避免熔料过热而分 解。
好的流动性。
② 压力
合理控制螺杆转速,保证温控系统的精度,以减小压力 波动。
③ 挤出速度
单位时间内由挤出机口模中挤出的塑化好的物料 量(kg/h)或塑件长度(m/min)。它表示挤出能力的高低。
④牵引速度
牵引速度与挤出速度相当,可略大于挤出速度。 即牵引比(牵引速度与挤出速度的比值)等于或大于1。
4. 机头与挤出机的关系
机头安装在挤出机的头部
三、管材挤出机机头的设计
常用的挤管机头有:直通式、直角式和旁侧式
直通式挤管机头
1-芯棒 2-口模 3-调节螺钉 4-分流器支架 5-分流器 6-加热器 7机头体
挤出机头结构
1-管材 2-定型模 3-口 模 4-芯棒 5-调节螺钉 6-分流器 7-分流器支架 8-机头体 9-过滤网 10电加热圈
⑥ 熔料通过分流器分流形成管状制品的胚形,并进一步 加热塑化。分流器支架用于支撑分流器和芯棒,同时对 分流后的塑料熔体加强剪切混合作用。
⑥ 定径套
⑦ 通过冷却定型,使从机头口模挤出的高温塑件已 形成的横截面形状稳定下来,并进行修正。
定 径 套 实 物 图 片
返回
正 在 挤 出 塑 料 管 材
塑 料 管 坯 进 入 定 径 装 置
二、挤出成型机头概述
1. 挤出机头的作用 使熔融塑料由螺旋运动变为直线运动; 产生必要的成型压力,保证制品密实; 使塑料通过机头得到进一步塑化; 通过机头口模以获得截面形状相同、连续的塑料制品。
2. 机头的分类
按机头的几何形状分类 圆环机头:管材机头、棒材机头、造粒机头等 平板状机头:平模机头、板材机头、异型材机头等
口模实物图片 返回
芯 棒 实 物 图 片
返回
② 过滤网和过滤板
③ 使从挤出机出来的塑料熔体由旋转流动变为平直流 动,且沿螺杆方向形成挤出压力,增加塑料的塑化均匀 度。
③ 机头体 ④ 机头的主体,相当于模架,用来组装并支撑机头的
各零件。 ④ 连接部分:
机头与挤出机用螺钉及法兰连接
⑤ 分流器和分流器支架
δ-口模与芯棒的单边间隙, δ =(0.83~0.94)t 。
②定型长度段L1 与口模定型长度 L 相当或稍长。
③ 压缩段长度L2
④
压缩段 (也称锥面段) 主要作用是使进入定型区之前的
塑料熔体的分流痕迹被熔合消除。
L2=(1.5~2.5) D0
D0-塑料熔体在过滤板出口处的流道直径
④机头内设有调节装置
调节熔体流量、口模和芯棒侧隙、挤出压力、成型温度、 挤出速度等。
⑤合理选择材料
机头的零件要承受熔体的压力作用,所以要有足够的强度。 必要时对连接零件进行强度校核。
与熔体接触的零件要有足够的耐磨性和耐腐蚀性,必要时 表面要镀铬处理。主要零件进行调质处理,硬度45~ 50HRC。
挤出成型设备——挤出机
④ 压缩角 低粘度塑料45~ 60° ,高粘度塑料30 ~ 50° 。
(3) 分流器和分流器支架 ① 分流器设计需确定的尺寸
❖分流器的角度α
低粘度塑料30°~80°, 高粘度塑料取30°~60°。
❖分流锥长度L3
L3 =(1~1.5) D0
❖分流器头部圆角半径r
取0.5~2mm
② 分流器支架
① 支承分流器及芯棒,另外起搅拌物料的作用。
② 小型机头,分流器和分流器支架可以做成一个整体。
③ 为了消除塑料通过分流器后形成的接合线,分流器支架 上的分流肋应做成流线型,一般3~8根。
挤出机:挤出系统、传动系统、加热冷却系统、机身
辅机: 机头、定型装置、冷却装置、牵引装置、切割
装置、卷取装置 控制系统
2. 挤出成型工艺过程
原材料准备
塑化
挤出成型
冷却定型
塑件的牵引、 卷曲、切割
挤塑生产线
3. 挤出成型工艺参数
① 温度
❖ 加料段的温度不宜过高,压缩段和均化段的温度可高一些 ❖ 机头的温度控制在塑料热分解温度以下 ❖ 口模的温度比机头温度可稍低一些,但要保证塑料有良
② 足够的压缩比
为了使塑件结构密实和消除分流器支架造成的熔料接合缝, 机头应该有一定的压缩比的压缩区域。低粘度塑料压缩比取 4~10,高粘度塑料在2.5~6为宜。
③ 正确的成型区截面形状及尺寸
口模的形状及尺寸和塑件的形状及尺寸并不是一致的。熔 体膨胀和牵引力引起的收缩变形,会使塑件的尺寸与口模尺寸 产生一定的偏差。所以在设计时要考虑这一因素。
1. 直通式挤管机头工艺参数的确定
2. (1) 口模
① 口模内径D ❖经验公式: D = d /K
d——管材外径 K——补偿系数
❖按拉伸比确定
② 定型段长度L
❖ 按管材外径:L=(0.5~3)d ❖ 按管材壁厚:L=nt
(2) 芯捧(芯模)
芯棒与分流器之间通过螺纹连接,其中心孔用来通入压 缩空气,以便对管材产生内压,实现外径定径。
第7章 塑料挤出成型工 艺及模具设计
一、挤出成型工艺
挤出成型是热塑性塑料重要的加工方法之一,主要用 于生产管材、棒材、板材、片材、线材和薄膜等连续塑料 型材。
1、挤出成型原理
将颗粒状或粉状塑料加入挤出机料筒内,在旋转的挤出机
螺杆的作用下,塑料沿螺杆的螺槽向前方输送。在此过程中, 不断地接受外加热和摩擦热,逐渐熔融成粘流态,然后在挤 压系统的作用下,塑料熔体经过滤板后通过具有一定形状的 挤出模具(机头)口模以及一系列的辅助装置,从而获得等 横截面的各种型材。
按机头进出料方向分类 水平直通式机头 直角式机头
按机头的用途分类 吹膜机头、管材机头、板材机头、棒材机头、异型材 机 头等。
3.挤出机头的组成(以直通式管材机头为例)
口模 芯棒 分流器和分流器支架 机头体 过滤网和过滤板 连接部分 定径套
① 口模和芯棒
② 挤出模的主要成型零件,口模用来成型塑件的外表 面,芯棒用来成型塑件的内表面。通过调节螺钉5,可 调节口模和芯棒之间的间隙,从而控制塑件的壁厚。Βιβλιοθήκη 拆 出 的 口 模 状 况
拆 开 口 模 后 露 出 芯 棒 的 状 况
图8.1 挤出机头结构
1-管材 2-定型模 3-口模 4-芯棒 5-调节螺钉 6-分流器 7-分流器支架 8-机头体 9-过滤网 10-电加热圈
3. 挤出机头的设计原则
① 内腔呈流线型
各连接处不应该有使熔料滞留的死角,避免熔料过热而分 解。
好的流动性。
② 压力
合理控制螺杆转速,保证温控系统的精度,以减小压力 波动。
③ 挤出速度
单位时间内由挤出机口模中挤出的塑化好的物料 量(kg/h)或塑件长度(m/min)。它表示挤出能力的高低。
④牵引速度
牵引速度与挤出速度相当,可略大于挤出速度。 即牵引比(牵引速度与挤出速度的比值)等于或大于1。
4. 机头与挤出机的关系
机头安装在挤出机的头部
三、管材挤出机机头的设计
常用的挤管机头有:直通式、直角式和旁侧式
直通式挤管机头
1-芯棒 2-口模 3-调节螺钉 4-分流器支架 5-分流器 6-加热器 7机头体
挤出机头结构
1-管材 2-定型模 3-口 模 4-芯棒 5-调节螺钉 6-分流器 7-分流器支架 8-机头体 9-过滤网 10电加热圈
⑥ 熔料通过分流器分流形成管状制品的胚形,并进一步 加热塑化。分流器支架用于支撑分流器和芯棒,同时对 分流后的塑料熔体加强剪切混合作用。
⑥ 定径套
⑦ 通过冷却定型,使从机头口模挤出的高温塑件已 形成的横截面形状稳定下来,并进行修正。
定 径 套 实 物 图 片
返回
正 在 挤 出 塑 料 管 材
塑 料 管 坯 进 入 定 径 装 置
二、挤出成型机头概述
1. 挤出机头的作用 使熔融塑料由螺旋运动变为直线运动; 产生必要的成型压力,保证制品密实; 使塑料通过机头得到进一步塑化; 通过机头口模以获得截面形状相同、连续的塑料制品。
2. 机头的分类
按机头的几何形状分类 圆环机头:管材机头、棒材机头、造粒机头等 平板状机头:平模机头、板材机头、异型材机头等
口模实物图片 返回
芯 棒 实 物 图 片
返回
② 过滤网和过滤板
③ 使从挤出机出来的塑料熔体由旋转流动变为平直流 动,且沿螺杆方向形成挤出压力,增加塑料的塑化均匀 度。
③ 机头体 ④ 机头的主体,相当于模架,用来组装并支撑机头的
各零件。 ④ 连接部分:
机头与挤出机用螺钉及法兰连接
⑤ 分流器和分流器支架