挤出复合剥离强度的影响因素
挤出复合工艺谈

挤出复合工艺谈(上)挤出复合概述1.挤出复合及其优缺点挤出复合是将热熔性树脂,如PE、EVA、EAA等,由塑料挤出机熔融塑化后经T型模头挤出在一种基材上,同时与另一基材复合贴压在一起,冷却后制成复合薄膜的一种方法。
实际中,往往也把挤出涂布归为挤出复合,并不特别列出。
挤出涂布是将热熔性树脂连续均匀地挤出,在一种基材上直接冷却收卷成复合薄膜,不与另一基材贴合的工艺。
挤出复合目前主要有三种方式:单层挤出复合,串联挤出复合,共挤出复合。
与其他复合方式相比,挤出复合有其独特的优点,也有一定的缺点。
挤出复合的优点如下:(1)复合速度快,适合大批量生产;(2)可自由选择基材;(3)加工成本较低,省去了一道热封膜生产工序,黏合剂使用量极少;(4)可任意设定挤压厚度;(5)可一次性连线生产多达9层的复合材料。
挤出复合的缺点如下:(1)初期设备投资较大;(2)在升温、更换挤出树脂时,损耗较大;(3)生产控制、质量控制较困难;(4)所用LDPE等原料的耐热性低,复合制品有异味;(5)产品平整度较差。
2.挤出复合发展趋势挤出树脂和挤出复合设备的发展推动了挤出复合工艺的发展。
(1)挤出复合用黏结性树脂和热封合树脂不断改进和发展,极大地扩大了挤出复合产品的品种和性能。
(2)随着包装产品向多品种、少批量的方向发展,节约资源、提高效率已成为趋势,挤出复合设备向自动化、数字化、智能化方向发展。
如快速自动调节的模头,厚度自动测量装置,遥控生产控制系统等。
(3)共挤出复合技术不断发展。
共挤出复合可以生产特殊的功能性薄膜,可减少生产流程,一次性生产出多层薄膜,且无须溶剂和AC剂,可降低成本,减少昂贵树脂的用量。
总之,共挤出复合的发展适应了缩短生产周期、节省资源、增加附加值的需求。
(4)连线生产设备不断发展。
综合性的生产线越来越多,比如挤出复合与印刷相组合、与湿法复合相组合、与底涂上光相组合等,可以一次性生产结构非常复杂的产品,尤其适用于生产液体包装、医药包装、高阻隔产品包装、调味料包装、牙膏包装等。
造成剥离强度偏低的几大原因75页PPT

谢谢
11、越是没有本领的就越加自命不凡。——邓拓 12、越是无能的人,越喜欢挑剔别人的错儿。——爱尔兰 13、知人者智,自知者明。胜人者有力,自胜者强。——老子 14、意志坚强的人能把世界放在手中像泥块一样任意揉捏。——歌德 15、最具挑战性的挑战莫过于提升自我。——迈克尔·F·斯特利
பைடு நூலகம்
造成剥离强度偏低的几大原因
36、“不可能”这个字(法语是一个字 ),只 在愚人 的字典 中找得 到。--拿 破仑。 37、不要生气要争气,不要看破要突 破,不 要嫉妒 要欣赏 ,不要 托延要 积极, 不要心 动要行 动。 38、勤奋,机会,乐观是成功的三要 素。(注 意:传 统观念 认为勤 奋和机 会是成 功的要 素,但 是经过 统计学 和成功 人士的 分析得 出,乐 观是成 功的第 三要素 。
LDPE挤出复合技术

LDPE挤出复合技术挤出复合是塑料包装材料生产中广泛使用的一种比较经济实用的复合加工方法。
原理是用挤出机将聚乙烯等热塑性塑料塑化后,通过模头呈薄膜状挤出,在两辊筒之间将熔融树脂和基材压合,冷却后制成复合薄膜。
1DPE树脂的选用挤出复合产品的物理性质取决于树脂的熔融指数和密度,通常情况下,挤出复合用的LDPE熔融指数选用2~l5,密度在0.915~0.935范围内。
熔融指数是衡量树脂流动性的指标,与平均分子量的关系很大,分子量小,熔融指数就高,流动性就好。
密度和结晶度、分子中短支链数有关,短支链多,结晶度低,因而密度低。
在选用树脂时要考虑到熔融指数和密度对复合产品性能、挤出复合加工性的影响。
可以看出,树脂的熔融指数和密度变化时,挤出复合产品的物理性质和成型加工性的各项指标不是同一方向变化,因此选择树脂时要均衡复合产品物理性能和成型加工性各项指标。
在生产过程中,应注意对树脂的缩幅量进行控制。
缩幅越大,复合膜两边偏厚就越严重,需修边量就越大,损耗就越大。
缩幅特性主要取决于熔融树脂的表面张力和回弹的平衡。
树脂的熔融弹性愈大,即分子,量大,长支链多,分子量分布广,缩幅性就愈小。
缩幅也因工艺参数变化而变化,树脂温度越高,缩幅就越大,加工速度就越低。
基材和树脂的粘结性基材和树脂粘结性的衡量指标是基材和树脂的剥离强度,在挤出复合生产中,剥离强度需定期检测控制,是复合产品的一项重要质量指标。
树脂的熔融指数和密度对粘结性的影响:1.熔融指数高的树脂粘度低,对基材润湿和浸透良好,容易获得高的粘结强度;2.低密度树脂短支链多,有双键的倾向,易起氧化作用,对粘结强度有利;3.树脂温度越高,氧化度越大。
生产中一般将LDPE树脂温度控制在300 320*(2;4.气隙是指从模唇到冷却辊和硅胶辊接触线间的距离,实际生产中,气隙一般控制在50~ll0n-an之间。
气隙通过时间=气隙÷加工速度从以上公式可知,为了获得适当的氧化度,确保复合膜的粘结强度,必须注意选择适当的树脂温度、气隙和加工速度。
干式复合常见问题探讨
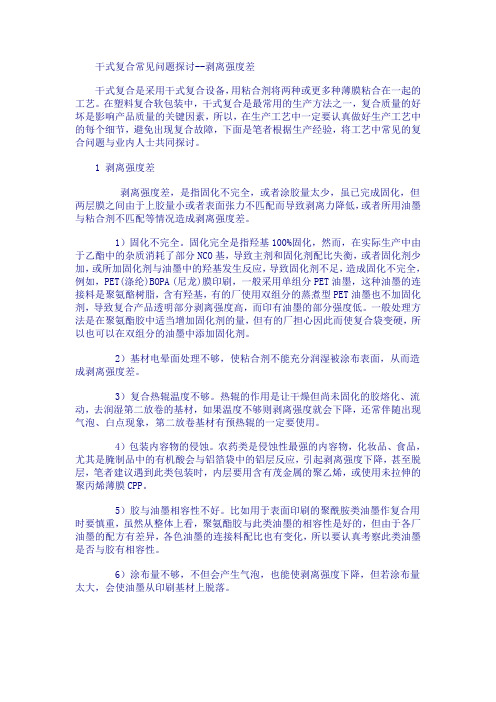
干式复合常见问题探讨--剥离强度差干式复合是采用干式复合设备,用粘合剂将两种或更多种薄膜粘合在一起的工艺。
在塑料复合软包装中,干式复合是最常用的生产方法之一,复合质量的好坏是影响产品质量的关键因素,所以,在生产工艺中一定要认真做好生产工艺中的每个细节,避免出现复合故障,下面是笔者根据生产经验,将工艺中常见的复合问题与业内人士共同探讨。
1 剥离强度差剥离强度差,是指固化不完全,或者涂胶量太少,虽已完成固化,但两层膜之间由于上胶量小或者表面张力不匹配而导致剥离力降低,或者所用油墨与粘合剂不匹配等情况造成剥离强度差。
1)固化不完全。
固化完全是指羟基100%固化,然而,在实际生产中由于乙酯中的杂质消耗了部分NCO基,导致主剂和固化剂配比失衡,或者固化剂少加,或所加固化剂与油墨中的羟基发生反应,导致固化剂不足,造成固化不完全,例如,PET(涤纶)BOPA (尼龙)膜印刷,一般采用单组分PET油墨,这种油墨的连接料是聚氨酪树脂,含有羟基,有的厂使用双组分的蒸煮型PET油墨也不加固化剂,导致复合产品透明部分剥离强度高,而印有油墨的部分强度低。
一般处理方法是在聚氨酯胶中适当增加固化剂的量,但有的厂担心因此而使复合袋变硬,所以也可以在双组分的油墨中添加固化剂。
2)基材电晕面处理不够,使粘合剂不能充分润湿被涂布表面,从而造成剥离强度差。
3)复合热辊温度不够。
热辊的作用是让干燥但尚未固化的胶熔化、流动,去润湿第二放卷的基材,如果温度不够则剥离强度就会下降,还常伴随出现气泡、白点现象,第二放卷基材有预热辊的一定要使用。
4)包装内容物的侵蚀。
农药类是侵蚀性最强的内容物,化妆品、食品,尤其是腌制品中的有机酸会与铝箔袋中的铝层反应,引起剥离强度下降,甚至脱层,笔者建议遇到此类包装时,内层要用含有茂金属的聚乙烯,或使用未拉伸的聚丙烯薄膜CPP。
5)胶与油墨相容性不好。
比如用于表面印刷的聚酰胺类油墨作复合用时要慎重,虽然从整体上看,聚氨酯胶与此类油墨的相容性是好的,但由于各厂油墨的配方有差异,各色油墨的连接料配比也有变化,所以要认真考察此类油墨是否与胶有相容性。
双面胶带剥离强度测试的影响因素

双面胶带剥离强度测试的影响因素采用4种典型双面胶带(特殊泡棉胶带VHB4914-15、无纺布基材双面胶带9448A、无基材双面胶带468 MP和PET基材双面胶带55258),系统研究了剥离角度、背材厚度种类以及剥离速度对于剥离强度测试的影响并从力学和能量的角度进行了深入分析。
测试结果符合经典的剥离模型的预测,但是不同的双面胶带结构导致对于模型预测的不同程度偏离。
标签:双面胶带;剥离强度;角度;背材;速度剥离(Peel)、初粘(Tack)和剪切(Shear)是压敏胶带的3项最重要的基本性能。
剥离测试直接表征破坏单位面积的粘接部位所需的能量[1],操作方便快捷,数据重复性好,并且能够提供非常丰富的信息。
通过剥离测试的数值、曲线和破坏模式,可以推断压敏胶带对被粘基材的亲和程度、压敏胶带的内聚强度和均匀程度等重要特征[2],因此被广泛采用作为压敏胶带质量控制和来料检测的有效手段,全球主要标准体系(ASTM、PSTC、FINAT、AFERA、JIS和GB 等)都有相关的详细描述和规定。
为了更好地模拟应用情形,实际使用的剥离测试经常会与标准方法存在一定差别。
压敏胶带的剥离强度对测试条件变化的敏感程度对于胶带选型、受力分析和粘接接头设计等实际应用具有指导意义,值得深入研究,但是目前很少有相关研究报道。
本研究选用市场中常见的厚度相同或者接近的4种不同结构的双面胶带,分别考查角度(Angle)、背材(Backing)和速度(Velocity)对剥离强度测试结果的影响。
1 实验部分1.1 实验材料镜面不锈钢测试板(SUS304),美国ChemInstruments;异丙醇,分析纯,成都科龙化工试剂厂;不同厚度的聚酯薄膜(PET),日本三菱化学;0.13 mm厚度氧化铝箔,美国ChemInstruments。
所有胶带样品均为市售3M产品(见表1),详细规格可参考公开的3M产品技术规格。
1.2 测试设备万能材料实验机,美国INSTRON 5569;桌面型剥离强度测试机,美国IMASS SP-2000;电动碾压辊轮(辊轮质量约2 kg),日本HYCHTECH。
塑料挤出成型工艺影响因素

塑料挤出成型工艺影响因素塑料挤出成型是一种常见的塑料加工方法,广泛应用于塑料制品的生产中。
在塑料挤出成型过程中,有许多因素会直接影响成型制品的质量和性能。
这些因素包括挤出机、模头结构、挤出工艺参数等,下面将详细探讨这些影响因素。
首先,挤出机的类型和性能是影响塑料挤出成型的重要因素之一。
挤出机的压力、温度控制、螺杆转速等参数会直接影响到挤出塑料的挤出效果和成型质量。
不同类型的挤出机适用于不同类型的塑料材料,选择合适的挤出机对成型效果至关重要。
其次,模头结构的设计对塑料挤出成型也有着至关重要的影响。
模头结构的设计直接影响到挤出塑料的流动性和成型形状。
合理的模头结构可以确保挤出制品的尺寸精准、表面光滑。
因此,设计精良的模头结构是保证塑料挤出成型质量的关键之一。
另外,挤出工艺参数的选择也是影响挤出成型质量的重要因素。
挤出温度、压力、速度等参数的选择需要根据具体的塑料材料和产品要求进行合理调整。
不同的塑料材料在挤出过程中对工艺参数的要求也有所不同,因此操作人员需要根据实际情况进行灵活调整。
此外,原料的质量和配比也会直接影响到塑料挤出成型的效果。
优质的原料可以保证成型制品的性能稳定,而不合理的原料配比则会导致挤出过程中出现问题,影响制品质量。
因此,在挤出过程中选择优质的原料并根据配比要求进行合理搭配至关重要。
综上所述,塑料挤出成型工艺的质量受多方面因素影响,需要在挤出机、模头结构、挤出工艺参数和原料质量等方面严格把控,才能保证成型制品的质量和性能。
只有在这些关键影响因素得到充分考虑和合理控制的情况下,塑料挤出成型工艺才能达到最佳效果,生产出高质量的塑料制品。
1。
压敏胶胶粘剂对剥离强度的影响

压敏胶粘剂对剥离强度的影响压敏胶粘剂的组成及其基本特征是决定压敏胶制品剥离强度值最重要的因素。
(一)压敏胶层的厚度对剥离强度的影响1、胶层厚度越大,180°剥离强度值越高,也越容易发生胶层内聚破坏;2、低速剥离时主要发生胶层内聚破坏,胶层厚度的影响不明显;高速剥离时主要发生界面粘合破坏,胶层厚度影响显著;3、胶层厚度越大,胶层内聚破坏向界面粘合破坏的转变在越高的剥离速度时出现。
(二)压敏胶拉伸强度和弹性模量的影响。
1、压敏胶制品的剥离强度在很大程度上取决于它的压敏胶粘剂的拉伸强度和弹性模量。
剥离强度与胶接界面上的拉伸破坏应力σf的平方成正比,与压敏胶的弹性模量Ea成反比。
2、当压敏胶的拉伸强度较低时,剥离测试出现胶层内聚破坏,且剥离强度值较高;当压敏胶的拉伸强度较高时,剥离测试出现界面粘合破坏,且剥离强度值随拉伸强度的增加而逐渐下降的趋势还很明显。
(三)压敏胶本体粘度的影响1、粘贴压敏胶制品时压敏胶对被粘表面的润湿速度与压敏胶的本体粘度成反比,即本体粘度越小,压敏胶越容易润湿被粘表面。
2、随着压敏胶本体粘度的降低,压敏胶制品的180°剥离强度会迅速增加。
但随着本体粘度的降低,压敏胶的拉伸强度和弹性模量也会下降,剥离测试时就可能出现胶层内聚破坏。
因此,一个实用压敏胶粘剂的本体粘度应该保持在一定的范围内,一般都在(105~107)Pa•s。
(四)压敏胶玻璃化转变温度的影响1、压敏胶的玻璃化转变温度Tg决定于压敏胶的组成。
玻璃化温度Tg可以用下述Fox公式进行计算:1/Tg=W1/Tg1+W2/Tg2+••••+ Wn/Tgn其中W为参与共聚合的各种单体的质量分数,T分别为这些单体的均聚物的玻璃化温度(用绝对温度表示)。
(五)压敏胶分子极性的影响1、压敏胶分子极性的增加哦能够显著提高压敏胶制品对极性被粘材料的剥离强度。
2、压敏胶分子极性的增加不仅增大了胶接界面上分子之间的相互作用力(尤其是对极性被粘表面)、改善了界面粘合条件,从而增加了界面粘附力,而且还改变了压敏胶层的力学性质和流变学性质,例如增加了内聚强度和弹性模量,提高了玻璃化温度和本体粘度等,这些都影响着压敏胶180°剥离强度和其他压敏胶粘性能。
影响木塑复合材料挤出成型质量因素分析

木塑复合材 料 的挤 出成型是指 热塑性塑 料和木 质
表 1 木塑型材挤 出成型 中异常现象及产生原因
纤维材料在挤 出机 中通过加 热 、 加压 , 使受热熔 化 的塑
料与木质纤维材料 混合 、 塑化 , 最后连续 通过 口模 成 型 的方法 。由于木 塑复合材料 的挤 出成 型是利用 塑料 的 传统挤 出加工方 式 ,所 以采 用的挤 出成 型设备也 主要
2 各 因素影 响分析
21 温度 .
林 业 机 械 与 木 工 设 备
第3 卷 6
的熔体压力 , 压力 的大小决定被挤 出型材是否密实 。当
机头压力较低 时 , 很难得 到致密 、 连续 和外观 良好 的制
品 。机头压力 的建立主要与两方面的 因素有关 , 一是机
头本身 的建压能 力 , 主要取决 于机头 的压缩 比, 聚乙 如 烯常用螺杆 压缩 比为 3 4 聚丙烯 螺杆压缩 比为 3 ~ ; ~, . 4 7
是 在塑料挤 出机 的基础上 ,以满 足木塑 复合材料 的加
工要求而 改进 的。由于添加 了木 质纤维材 料 , 使得塑料
的加工流变行为发 生改变 ,同时木质纤 维材料又 是一
① 过 牵 随度 快
型 品收 大 ② 不 材制 缩 冷却 充分 ③ 水 偏高 冷却 水温
①构度 高 饥温 过
析 。结果表明 , 艺设计和控 制在 生产过程 中非常重要 , 工 应根 据所用原料 , 结合 配方进行 实时调 整。
关键词 : 木塑复合材料 ; 出成型质量 ; 挤 生产工 艺 中图分类号 :B 3 T 32 文献标识码 : A 文章编号 :0 14 6 (0 8 0 — 0 5 0 10 — 4 2 2 0 )7 0 1— 3
- 1、下载文档前请自行甄别文档内容的完整性,平台不提供额外的编辑、内容补充、找答案等附加服务。
- 2、"仅部分预览"的文档,不可在线预览部分如存在完整性等问题,可反馈申请退款(可完整预览的文档不适用该条件!)。
- 3、如文档侵犯您的权益,请联系客服反馈,我们会尽快为您处理(人工客服工作时间:9:00-18:30)。
挤出复合剥离强度的影响因素随着我国挤出复合设备技术性能的不断提高,涂复级树脂如LDPE、PP等及复合粘接级树脂EVA、EMA、EAA等的不断开发,挤出复合工艺以成本低、无残留溶剂等优点,逐渐被广大软包装企业所接受。
而高涂复速度和高剥离强度是困扰众多软包装企业的两难问题。
笔者根据生产实践,就挤出复合工艺对剥离强度的影响因素与包装同行共同探讨。
一、树脂塑化混炼程度挤出复合是将热塑性树脂如LDPE、PP、EVA、EMA、EAA等加入料筒,在螺杆的作用下,经压缩区高温熔融成粘流态,在均化区高温、高压、高剪切条件下,进一步塑化混炼均匀,随着螺杆的推动而被定压、定量、定温地经T模头持续均匀挤出。
树脂的塑化混炼程度是影响挤出复合剥离强度的主要因素之一。
树脂塑化混炼越充分,复合后剥离强度越高。
通常采用以下方法增加树脂塑化混炼程度:1.选用熔融指数(MI)较大的树脂熔融指数(MI)越大,流动性越好,塑化混炼效果越好。
但MI太大,则挤出薄膜发生边厚现象。
故宜选用MI为8g/10min左右的树脂。
2.适当提高加热温度压缩区、均化区加热温度越高,树脂塑化混炼越充分;但温度过高树脂易分解。
加热温度的设定要根据树脂种类及其熔融指数(MI)来设定。
如牌号为1C7A的LDPE树脂,其加热温度在300~325℃范围内设定。
3.适当提高熔体压强熔体所受压强越大,塑化混炼就越充分;增加熔体压强,常采用增加滤网层数或目数的方法。
如牌号为1C7A的LDPE树脂采用目数分别为85、110、85的三层滤网,使溶体压强在1.2~1.4MPa范围内。
4.适当提高螺杆转速螺杆转速越大,单位熔体所受螺杆剪切次数越多,塑化混炼就越充分。
但螺杆转速增大,挤出薄膜厚度增加。
故应注意螺杆转速、涂复速度与挤出薄膜厚度三者的匹配。
二、树脂的氧化程度粘流态树脂经模唇挤出到接触基材的过程中,被空气中的氧气氧化而产生极性,提高挤出复合剥离强度。
气隙即模唇到两薄膜(即挤出薄膜与基材)复合线的距离。
气隙大、氧化程度高。
但气隙过大,热损失就大,从而降低剥离强度。
气隙一般在9~12cm范围内调整。
三、树脂温度与基材接触时的树脂温度高,则剥离强度高。
通常采用提高模头温度的方法,来提高树脂温度。
但模头温度过高,则挤出薄膜发生边厚,且易使模唇发生氧化、树脂发生碳化现象。
如挤出牌号为1C7A的LDPE 树脂时,模头各区温度在323~328℃范围内设定。
要注意做好日常的模唇维护保养工作。
停车时要使树脂挤出模唇外少许,防止氧气进入;开车时要用软铜片反复清理模唇,防止碳化的树脂附在其上,影响复合质量。
四、挤出薄膜在高温状态与基材接触的时间树脂经模唇挤出后,其在高温状态与基材接触的时间越长,剥离强度越高。
故应调整模头适当偏向胶辊侧少许,使挤出薄膜与基材接触的时间增加。
但要注意被复合基材的耐高温性,以免影响复合质量。
五、压辊压力与冷却辊状态1.挤出薄膜与基材接触后经冷却辊与胶辊挤压后粘接在一起。
压辊压力大,冷却辊与胶辊对复合膜的挤压力大,剥离强度就大。
但要考虑设备的承受能力,一般压辊压力在4kg/cm2左右调节。
2.冷却辊表面温度应适当提高,可增加剥离强度。
但温度过高不利于操作,一般在20~25℃范围内,在不影响产品外观的情况下,选用网线式冷却辊,可增加对薄膜的挤压面积,从而提高挤出复合的剥离强度。
六、涂复速度涂复速度降低,则可提高挤出复合剥离强度。
但涂复速度降低,意味着班产量降低、产品成本增加。
七、被复合基材的表面张力及温度被复合基材的表面张力越大,挤出复合剥离强度越高;其表面张力应大于38dyn/cm2。
被复合基材与挤出薄膜复合时的温度差越小,挤出复合剥离强度越高。
因而在保证被复合基材干燥清洁的基础上,通过干燥箱对基材进行预热,降低与挤出薄膜复合时的温度差。
八、涂布异氰酸酯类AC剂或双组份聚氨酯粘合剂在挤出复合工艺,基材涂布异氰酸酯类AC剂后,经干燥箱干燥后与挤出薄膜复合,可提高挤出复合剥离强度。
也可采用涂布双组份聚氨酯粘合剂,以较少的干量如1~2g来获得理想的剥离强度。
提高挤出复合的剥离强度,还可通过对螺杆的专业化设计来进行。
拥有挤出复合设备的软包装企业,要通过对以上各工艺因素的优化组合,在保证产品剥离强度的基础上,提高生产效率,降低制造成本,不断提升企业市场竞争力。
挤出复合工艺具有投资少、成本低、生产效率高、操作简便等多方面的优点,因此,它在塑料薄膜的复合加工中占有相当重要的地位。
但是,在实际生产中也难免会出现这样或那样的问题。
本文,就以最为常见的剥离强度差为例与大家共同进行分析探讨。
一、薄膜基材对剥离强度的影响1、基材表面处理效果对剥离强度的影响。
被涂布基材应当预先进行电晕处理,电晕处理后的表面张力应当达到40达因以上,这样可以改进基材同熔融挤出树脂的粘结性,从而提高挤出复合强度。
因此,在生产前要检测基材的表面张力是否达到要求,一发现表面张力太低,应立即更换基材或对基材重新进行表面处理。
此外,经表面处理过的薄膜,其表面张力应当是均匀一致的,否则也会对剥离强度产生一定的影响,造成剥离强度不均匀、不一致的问题。
2、基材表面清洁度对剥离强度的影响。
被涂布基材表面应当清洁、干净,无灰尘、无油污,如果基材表面不太清洁,粘附了灰尘、油脂等污物,就会直接影响到熔融树脂跟塑料薄膜表面的粘合力,从而使挤出复合膜的粘接强度下降。
3、其它因素的影响。
对于一些易吸湿的薄膜材料(比如尼龙薄膜),如果已经发生吸湿现象,这也会影响挤出复合膜的粘接牢度。
因此,对于易吸湿的薄膜材料一定要注意防潮,尼龙薄膜在使用前和使用后应当及时用铝箔将其包裹好。
二、油墨对剥离强度的影响1、油墨质量对剥离强度的影响。
在实际生产过程中,有时候会出现无油墨或油墨较少部位的剥离强度好、而有油墨或油墨较多部位的粘合牢度反而比较差的现象,这就是由于所用的印刷油墨的适性不好,油墨与基材之间的粘接不良,从而造成挤出复合膜的剥离强度差。
一旦发生这种情况,应当及时更换合适的油墨,并同油墨厂商联系,共同协商和研究解决办法。
2、油墨干燥性对剥离强度的影响。
如果油墨干燥不良,特别是当油墨中大量地使用了甲苯、丁醇等沸点比较高的溶剂,而且干燥箱温度设置不当的话,就会有少量或较大量的溶剂残留在油墨层中,复合后可能会造成复合膜的分层,使剥离强度变差。
因此,在印刷过程中一定要对油墨的干燥性能进行严格的控制,保证油墨能够充分干燥。
此外,在印刷过程中还要注意对印刷速度和干燥温度等工艺条件的控制,因为它们也会对油墨中溶剂的挥发速度产生一定的影响。
如果印刷速度较快,且印刷机干燥箱的温度又比较低的话,油墨中的溶剂可能无法完全挥发掉,这些残留的溶剂就会在薄膜上形成一些小泡,使复合膜粘接牢度下降。
一般来说,在设定干燥箱的温度时,必须要综合考虑印刷速度、油墨的干燥速度、承印物材料的种类以及印刷图像的大小等因素。
三、挤出复合用树脂对剥离强度的影响1、树脂类型对剥离强度的影响。
挤出涂布复合用树脂可以是聚乙烯、聚丙烯、EVA、Surlyn、Nucler、Bynel、EVAL、EAA、EMAM等。
挤出涂布复合的目的不同,选用的树脂也不同。
例如,用于普通层复合塑料制袋用的,可以采用热封性较好的各种热封用树脂;用于夹心挤复用的树脂,要求同面层和内封层塑料层均有良好的相容性的,可根据面层及内封层材料的不同选用各种相容剂树脂,如Surlyn、Nucler、Bynelr等。
如果树脂选用不当,会影响到它同被涂布基材的相容性,从而影响到挤出复合强度。
2、树脂熔融指数(MI)对剥离强度的影响。
熔融指数(MI)是指树脂熔融料在一定温度和一定压力下,在lOmin内通过标准毛细管的重量值,以克/1Omin表示。
熔融指数(MI)是树脂流动性的一种指标,一般来说,树脂的熔融指数(MI)越高,则其流动性越好,熔融薄膜的粘度越低,粘合力越大。
在挤出复合工艺中,不宜选用熔融指数(MI)太小的树脂。
如果树脂的熔融指数(MI)偏小,其分子量较大,则融合性比较差,不能与被涂布基材很好地粘合,致使剥离牢度有所下降。
比如在使用LDPE树脂进行挤出复合时,一般选用熔融指数(MI)在4--7g/1Omin的LDPE 树脂。
3、树脂密度对剥离强度的影响。
树脂的密度越小,支链含量越高,表面越容易被活化,粘合力就越大,对剥离强度的提高也就越有利。
4、树脂中助剂及水分含量对剥离强度的影响。
树脂中的助剂,特别是润滑剂对挤出复合膜的剥离强度有着很大的影响,比如在使用LDPE树脂进行挤出复合时,应当选用不含或少含润滑剂的挤出涂覆级树脂粒子,例如北京燕山石化公司的1C7A树脂。
此外,如果树脂中所含的水分比较多的话,在挤出复合过程中可能会发生塑化不良现象,从而影响复合膜的剥离强度。
四、挤出复合工艺对剥离强度的影响1、挤出机温度对剥离强度的影响。
挤出机机筒温度和T模温度的控制极为重要,是挤出复合工艺的关键和核心。
温度太低,树脂塑化不良,从模口流延下来不能很好地与基材复合,致使剥离牢度下降;温度高,流出的熔薄膜氧化越充分,表面产生极性分子,对基材的亲和力越大,剥离强度也就越高。
但是温度也不宜过高,否则树脂容易分解,还可能会烫伤基材,而且还会产生烟雾,污染工作环境。
一般来说,挤出机机筒的温度通常控制在150℃一340℃之间,T模的温度通常控制在310℃--340'C左右,这还要根据挤出复合设备和所用树脂的具体情况来设定。
2、树脂温度对剥离强度的影响。
树脂温度高,有利于熔融塑料膜在被涂布基材上的润湿和渗透,因而有利于复合强度的提高,但过高会引起分解,一般不超过350℃。
如果树脂与基材压着时的温度过低,树脂表面氧化不充分,应当适当提高树脂温度。
3、气隙对剥离强度的影响。
气隙是指从挤出模口到复合冷却钢辊、压力辊接触线之间的距离。
由于气隙的存在,热熔膜表面会同空气中的氧气发生氧化作用,氧化后的热熔膜被涂布塑料薄膜复合时的剥离牢度会大大提高。
气隙的大小对挤出剥离强度也有很大的影响,气隙太小,树脂表面氧化不充分,致使挤出复合强度变差;气隙大,热熔膜同空气接触的时间长,热熔膜表面被空气中氧气氧化的程度越厉害。
增加极性基因,树脂同基材表面的黏结力也就越大,从而有利于复合强度的提高。
但如果气隙太大,则热熔膜的热损失过大,温度会降低得过多,在复合时的温度过低,反而会引起剥离强度的下降,而且热封性也变差。
因此,挤出复合时应当根据实际情况来调节气隙的大小,一般来说,气隙控制在50mm—l00mm之间为宜。
4、复合压力对剥离强度的影响。
复合压力小,熔融树脂与基材之间贴合不紧密,会使剥离牢度下降。
但复合压力也不可太大,否则基材容易被压变形。
5、冷却钢辊表面温度对剥离强度的影响。
冷却辊采用的是表面镀铬的钢辊筒,其作用是将熔融树脂薄膜的热量带走,让粘合后的复合膜立即冷却、固化,以形成较强的内聚力,使熔融薄膜跟被涂布基材粘牢、定型,不产生相对位移,从而保证良好的剥离强度。