挤出复合剥离强度的影响因素
复合薄膜剥离强度影响因素探讨

作 用 。 化 学 作 用 发 生 在 黏 合 剂 与 薄 膜 表 面 的 活 性 基 团 之 间 ;物 理 作 用 主 要 是 ” 锚 效 应 ”和 分 子 间 的 作 用 力 。 投
黏合效果既由黏合剂决定 , 由复合材料的表面状态决 又 定 。由于黏合过程较复杂 . 在现有条件下无法进行测试和检
维普资讯
【 包 专ห้องสมุดไป่ตู้】 曼堕 _ 软 装 刊 蕉
P it g T c n lg r i e h oo y nn
复合 薄膜剥离强度
大连 大 富塑料彩 印有 限公 司 邢顺 川
剥离强度 是检测复合薄膜 物理性 能的一项 重要指标 。
一
5
4
5
4
5
5
5
5
4
m 5
∞ 电晕 电流 ∞ ∞ ∞ ∞ 布量 ∞ P 膜种类 黏合 剂选择 涂 ∞ E ∞ ∞
次要 因素
5
7
主要 因素
D E F F D E E F D
0
畸= 2
5
, 5
印刷 技术 一 0 6 1 — 3 — 2 0 / 3
维普资讯
一
剥离强度

挤出复合薄膜剥离强度的影响因素挤出复合工艺具有投资少,成本低,生产效率高,操作简便等多方面的优点,因此,它在塑料薄膜的复合加工中占有相当重要的地位。
但是,在实际生产中也难免会出现这样或那样的问题,在此,就以最为常见的剥离强度差为例与大家共同分析探讨。
基材对剥离强度的影响1.基材表面处理效果对剥离强度的影响被涂布基材应当预先进行电晕处理,使表面张力达到4.0×10-2N/m以上,以改进基材同熔融挤出树脂的黏结性,从而提高挤出复合强度。
因此,生产前要检测基材的表面张力是否达到要求,一旦发现表面张力太低,应立即更换基材或对基材重新进行表面处理。
此外,经表面处理过的薄膜,其表面张力应当是均匀一致的,否则也会对剥离强度产生一定的影响,造成剥离强度不均匀、不一致。
2.基材表面清洁度对剥离强度的影响被涂布基材表面应当无灰尘、无油污。
如果基材表面的清洁度差,黏附了灰尘、油脂等污物,就会直接影响到熔融树脂与塑料薄膜表面的黏合力,从而使挤出复合膜的黏结强度下降。
3.其他因素的影响对于一些易吸湿的薄膜材料(如尼龙薄膜),如果已经发生吸湿现象,也会影响挤出复合膜的黏结牢度。
因此,对于易吸湿的薄膜材料一定要注意防潮,尼龙薄膜在使用前和使用后应当及时用铝箔包裹好。
油墨对剥离强度的影响1.油墨质量对剥离强度的影响在实际生产过程中,有时候会出现无油墨或油墨较少部位的剥离强度好,而有油墨或油墨较多部位的黏合牢度比较差的现象。
这就是由于所用的油墨印刷适性不好,油墨与基材之间黏结不良,从而造成挤出复合膜的剥离强度差。
一旦发生这种情况,应当及时更换合适的油墨,并同油墨厂商联系,共同协商和研究解决办法。
2.油墨干燥性对剥离强度的影响如果油墨干燥不良,特别是当油墨中大量地使用了甲苯、丁醇等沸点比较高的溶剂,而且干燥箱温度设置不当时,就会有少量或较大量的溶剂残留在油墨层中,复合后可能会造成复合膜的分层,使剥离强度变差。
因此,在印刷过程中一定要对油墨的干燥性能进行严格的控制,保证油墨能够充分干燥。
挤出复合剥离强度的影响因素

挤出复合剥离强度的影响因素随着我国挤出复合设备技术性能的不断提高,涂复级树脂如LDPE、PP等及复合粘接级树脂EVA、EMA、EAA等的不断开发,挤出复合工艺以本钱低、无残留溶剂等长处,逐渐被广大软包装企业所同意。
而高涂复速度和高剥离强度是困扰众多软包装企业的两难问题。
笔者按照生产实践,就挤出复合工艺对剥离强度的影响因素与包装同行一路探讨。
一、树脂塑化混炼程度挤出复合是将热塑性树脂如LDPE、PP、EVA、EMA、EAA等加入料筒,在螺杆的作用下,经紧缩区高温熔融成粘流态,在均化区高温、高压、高剪切条件下,进一步塑化混炼均匀,随着螺杆的推动而被定压、定量、定温地经T模头持续均匀挤出。
树脂的塑化混炼程度是影响挤出复合剥离强度的主要因素之一。
树脂塑化混炼越充分,复合后剥离强度越高。
通常采用以下方式增加树脂塑化混炼程度:1.选用熔融指数(MI)较大的树脂熔融指数(MI)越大,流动性越好,塑化混炼效果越好。
但MI太大,则挤出薄膜发生边厚现象。
故宜选用MI为8g/10min左右的树脂。
2.适当提高加热温度紧缩区、均化区加热温度越高,树脂塑化混炼越充分;但温度太高树脂易分解。
加热温度的设定要按照树脂种类及其熔融指数(MI)来设定。
如牌号为1C7A的LDPE树脂,其加热温度在300~325℃范围内设定。
3.适当提高熔体压强熔体所受压强越大,塑化混炼就越充分;增加熔体压强,常采用增加滤网层数或目数的方式。
如牌号为1C7A的LDPE树脂采用目数别离为85、110、85的三层滤网,使溶体压强在1.2~1.4MPa范围内。
4.适当提高螺杆转速螺杆转速越大,单位熔体所受螺杆剪切次数越多,塑化混炼就越充分。
但螺杆转速增大,挤出薄膜厚度增加。
故应注意螺杆转速、涂复速度与挤出薄膜厚度三者的匹配。
二、树脂的氧化程度粘流态树脂经模唇挤出到接触基材的进程中,被空气中的氧气氧化而产生极性,提高挤出复合剥离强度。
气隙即模唇到两薄膜(即挤出薄膜与基材)复合线的距离。
造成剥离强度偏低的几大原因
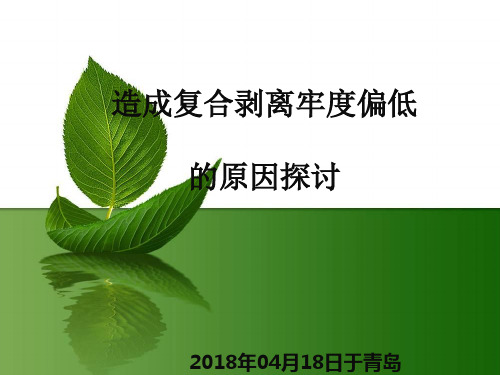
2021/5/27
15
3、油墨残留溶剂消耗固化剂: 此类现象在使用聚氨酯油墨的产品上比较多见,由于聚氨酯油
墨中的羟基与双组分胶黏剂中的-NCO发生反应,消耗掉部分固化剂, 导致胶水不能完全固化,影响产品剥离强度。因的溶剂,在印刷工序中,尽量减少 溶剂的残留。
2021/5/27
30
残留溶剂太多引起析皱脱层;
2021/5/27
31
五、其它因素影响:
1、生产车间周边环境脏、灰尘多;湿度大影响: 环境因素影响如灰尘及杂质、水气,胶液中含有其它物质,胶液混 浊反白都会影响复合牢。
R-NCO+H2O----R-NH2+CO2
这一步反应虽然不是很快,但比起固化剂中的异氰酸酯和主剂反应 要快得多约20倍。若加上空气中的灰尘或杂质形成有核的气泡
2021/5/27
16
常用的塑料油墨、胶粘剂(检测适用)标准:
1、细度:GB/T13217.3—2008; 2、粘度: GB/T13217.4—2008; 3、初干性: GB/T13217.5—2008; 4、着色力: GB/T13217.6—2008; 5、附着牢度: GB/T13217.7—2008; 6、QB/T2024—2012凹版塑料薄膜复合油墨; 7、QB/T1046—2012表印油墨;
2021/5/27
19
B-1芳香族---固化剂异氰酸酯基(NCO)直接与芳香环相连接,经 水解后会变成芳香胺,生成的聚氨酯有较大的毒性,是一种致癌物, 不可用于水煮、蒸煮袋。
B-2脂肪族---NCO不直接与芳香环相接,水解后只生成脂肪胺,一 般可用于水煮蒸煮袋用胶。
2021/5/27
20
三、胶粘剂原因:
2021/5/27
浅谈软塑包装复合剥离强度及控制方法
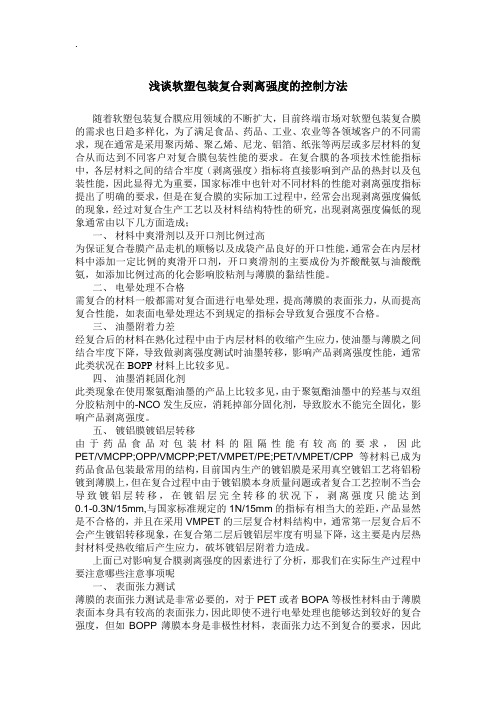
浅谈软塑包装复合剥离强度的控制方法随着软塑包装复合膜应用领域的不断扩大,目前终端市场对软塑包装复合膜的需求也日趋多样化,为了满足食品、药品、工业、农业等各领域客户的不同需求,现在通常是采用聚丙烯、聚乙烯、尼龙、铝箔、纸张等两层或多层材料的复合从而达到不同客户对复合膜包装性能的要求。
在复合膜的各项技术性能指标中,各层材料之间的结合牢度(剥离强度)指标将直接影响到产品的热封以及包装性能,因此显得尤为重要,国家标准中也针对不同材料的性能对剥离强度指标提出了明确的要求,但是在复合膜的实际加工过程中,经常会出现剥离强度偏低的现象,经过对复合生产工艺以及材料结构特性的研究,出现剥离强度偏低的现象通常由以下几方面造成;一、材料中爽滑剂以及开口剂比例过高为保证复合卷膜产品走机的顺畅以及成袋产品良好的开口性能,通常会在内层材料中添加一定比例的爽滑开口剂,开口爽滑剂的主要成份为芥酸酰氨与油酸酰氨,如添加比例过高的化会影响胶粘剂与薄膜的黏结性能。
二、电晕处理不合格需复合的材料一般都需对复合面进行电晕处理,提高薄膜的表面张力,从而提高复合性能,如表面电晕处理达不到规定的指标会导致复合强度不合格。
三、油墨附着力差经复合后的材料在熟化过程中由于内层材料的收缩产生应力,使油墨与薄膜之间结合牢度下降,导致做剥离强度测试时油墨转移,影响产品剥离强度性能,通常此类状况在BOPP材料上比较多见。
四、油墨消耗固化剂此类现象在使用聚氨酯油墨的产品上比较多见,由于聚氨酯油墨中的羟基与双组分胶粘剂中的-NCO发生反应,消耗掉部分固化剂,导致胶水不能完全固化,影响产品剥离强度。
五、镀铝膜镀铝层转移由于药品食品对包装材料的阻隔性能有较高的要求,因此PET/VMCPP;OPP/VMCPP;PET/VMPET/PE;PET/VMPET/CPP等材料已成为药品食品包装最常用的结构,目前国内生产的镀铝膜是采用真空镀铝工艺将铝粉镀到薄膜上,但在复合过程中由于镀铝膜本身质量问题或者复合工艺控制不当会导致镀铝层转移,在镀铝层完全转移的状况下,剥离强度只能达到0.1-0.3N/15mm,与国家标准规定的1N/15mm的指标有相当大的差距,产品显然是不合格的,并且在采用VMPET的三层复合材料结构中,通常第一层复合后不会产生镀铝转移现象,在复合第二层后镀铝层牢度有明显下降,这主要是内层热封材料受热收缩后产生应力,破坏镀铝层附着力造成。
影响粘结力和剥离强度的因素

影响塑料薄膜粘结力和剥离强度的因素塑料薄膜表面电晕处理不好,表面张力低,就会导致墨层附着牢度低,复合膜粘结强度低,在薄膜投入前应认真检测其表面张力值务必提高到3.8×10-2N/m以上,最好能达到4.0-4.2×10-2N/m,因为3.8×10-2N/m只是最低要求,表面张力值低于3.8×10-2N/m的薄膜根本就不能使油墨和胶粘剂完全铺展,复合后的成品当然达不到剥离强度的要求。
检测薄膜表面张力的方法通常有两种:1)达因笔测试,达因笔的笔液通常呈红色,规格有3.8×10-2N/m、4.0×10-2N/m、4.2×10-2N/m、4.4×10-2N/m以及4.8×10-2N/m这五种,如果用达因笔在薄膜上的笔液不收缩,均匀,无断层,则说明薄膜的表面张力已经达到使用要求,相反,笔液收缩,消失,不均匀,不连续,则说明处理不够;2)用BOPP单面胶布测试,将BOPP单面胶布贴在待测薄膜表面再撕开,电晕处理好的通常剥离声音小,粘贴牢固,相反则粘贴不牢,容易剥离,这种测试方法要依靠经验,不适合测试PET、PA等薄膜。
电晕处理不符合要求的基材决不能进行复合,因为复合后肯定达不到包装产品对剥离强度的要求。
常用基材的表面张力值为:BOPP3.8×10-2N/m、PET5.0×10-2N/m、PA5.2×10-2N/m。
溶剂残留量太高影响剥离强度,影响粘结力残留溶剂太多,复合后会形成许多微小气泡,使相邻的复合基材脱离、分层、气泡越多,剥离强度越低,要提高剥离强度,就必须减少气泡的产生。
气泡的产生与许多因素有关,诸如上胶不均匀,烘干道温度过低,热压辊温度偏低及室内温湿度不合适等,通常,室内温度宜控制在23-25℃,相对湿度应控制在50%-60%为宜,另外,避免使用高沸点溶剂,也可减少气泡的产生。
总之为提高剥离强度,提高粘接力应尽可能降低残留溶剂。
层间剥离强度差的原因及解决方法,请收好!

层间剥离强度差的原因及解决方法,请收好!
珠光膜复合产品剥离强度不高的原因主要包括层间剥离强度问题和热封剥离强度问题。
接下来,本文将重点讲解导致层间剥离强度差的原因及解决方法。
层间剥离强度差的原因:
①珠光膜材料或印刷BOPP材料表面张力低,不符合印刷或复合要求。
②干燥温度控制不当或使用的溶剂大量残留影响剥离强度。
③印刷油墨与印刷基材不亲和,相容性不好。
④选择的黏合剂不合。
⑤复合烘箱温度控制不当,对溶剂挥发造成严重影响。
⑥复合辊温度太低。
⑦熟化时间或温度控制上出现问题。
双组份聚氨酯黏合剂熟化时间一般控制在24~48小时,熟化温度控制在50%左右。
解决办法是:
①提高材料的表面张力。
BOPP38达因,PET50达因。
②调整印刷温度或降低印刷速度,对溶剂进行调节。
③严禁混用不相同的树脂体系油墨。
④更换黏合剂,建议选择专用的黏合剂。
该黏合剂主要特点是胶体柔软,抗冷冻性特别好,产品不发硬,高流动性,使用成本更低,固化速度快,8小时就可分切加工,复合适性及产品平整性佳。
⑤提高胶水的浓度,检测刮刀的角度,检测涂胶辊的网孔深度与线数。
⑥温度采用由低到高的控制方法,另外要考虑排风系统的风速问题,或降低复合机速。
⑦提高复合辊温度。
其实复合辊温度的高低,应该与机速、材料的厚薄有很大的关系,还与胶水的性质有关系。
⑧控制好熟化时间和温度。
复合薄膜竟出现剥离强度低的现象,搞不清楚这几点就晚了!
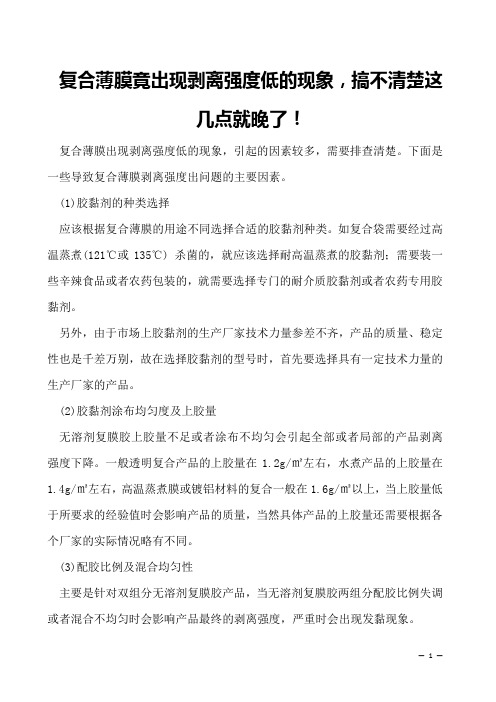
复合薄膜竟出现剥离强度低的现象,搞不清楚这几点就晚了!复合薄膜出现剥离强度低的现象,引起的因素较多,需要排查清楚。
下面是一些导致复合薄膜剥离强度出问题的主要因素。
(1)胶黏剂的种类选择应该根据复合薄膜的用途不同选择合适的胶黏剂种类。
如复合袋需要经过高温蒸煮(121℃或135℃) 杀菌的,就应该选择耐高温蒸煮的胶黏剂;需要装一些辛辣食品或者农药包装的,就需要选择专门的耐介质胶黏剂或者农药专用胶黏剂。
另外,由于市场上胶黏剂的生产厂家技术力量参差不齐,产品的质量、稳定性也是千差万别,故在选择胶黏剂的型号时,首先要选择具有一定技术力量的生产厂家的产品。
(2)胶黏剂涂布均匀度及上胶量无溶剂复膜胶上胶量不足或者涂布不均匀会引起全部或者局部的产品剥离强度下降。
一般透明复合产品的上胶量在1.2g/㎡左右,水煮产品的上胶量在1.4g/㎡左右,高温蒸煮膜或镀铝材料的复合一般在1.6g/㎡以上,当上胶量低于所要求的经验值时会影响产品的质量,当然具体产品的上胶量还需要根据各个厂家的实际情况略有不同。
(3)配胶比例及混合均匀性主要是针对双组分无溶剂复膜胶产品,当无溶剂复膜胶两组分配胶比例失调或者混合不均匀时会影响产品最终的剥离强度,严重时会出现发黏现象。
(4)复合基材的表面张力当复合基材的表面张力低于要求值时,会严重影响产品复合后的剥离强度,一般薄膜电晕处理后应尽快使用,随着时间的延长,处理过的薄膜表面张力会逐渐降低。
建议每次开机前用达因笔检查待复合材料的表面张力是否合格。
(5)熟化程度无溶剂胶无溶剂胶黏剂的分子量较低,基本没有初黏力;复合后需要在40~ 50°C的熟化室中进行进一步的交联固化。
当熟化室温度过低、熟化时间较短或者低温存放时间过长都会影响产品的最终剥离强度,有些重新放置熟化也没有明显的效果,这主要是部分异氰酸酯组分已经与水汽发生了反应的缘故。
(6)基材添加剂等其他因素的影响塑料薄膜中添加剂 (如滑爽剂)迁移到复合材料的表面与胶黏剂的异氰酸酯组分反应,降低产品最终的剥离强度;可以适当降低熟化温度来减少塑料薄膜中添加剂的迁移。
- 1、下载文档前请自行甄别文档内容的完整性,平台不提供额外的编辑、内容补充、找答案等附加服务。
- 2、"仅部分预览"的文档,不可在线预览部分如存在完整性等问题,可反馈申请退款(可完整预览的文档不适用该条件!)。
- 3、如文档侵犯您的权益,请联系客服反馈,我们会尽快为您处理(人工客服工作时间:9:00-18:30)。
挤出复合剥离强度的影响因素随着我国挤出复合设备技术性能的不断提高,涂复级树脂如LDPE、PP等及复合粘接级树脂EVA、EMA、EAA等的不断开发,挤出复合工艺以成本低、无残留溶剂等优点,逐渐被广大软包装企业所接受。
而高涂复速度和高剥离强度是困扰众多软包装企业的两难问题。
笔者根据生产实践,就挤出复合工艺对剥离强度的影响因素与包装同行共同探讨。
一、树脂塑化混炼程度挤出复合是将热塑性树脂如LDPE、PP、EVA、EMA、EAA等加入料筒,在螺杆的作用下,经压缩区高温熔融成粘流态,在均化区高温、高压、高剪切条件下,进一步塑化混炼均匀,随着螺杆的推动而被定压、定量、定温地经T模头持续均匀挤出。
树脂的塑化混炼程度是影响挤出复合剥离强度的主要因素之一。
树脂塑化混炼越充分,复合后剥离强度越高。
通常采用以下方法增加树脂塑化混炼程度:1.选用熔融指数(MI)较大的树脂熔融指数(MI)越大,流动性越好,塑化混炼效果越好。
但MI太大,则挤出薄膜发生边厚现象。
故宜选用MI为8g/10min左右的树脂。
2.适当提高加热温度压缩区、均化区加热温度越高,树脂塑化混炼越充分;但温度过高树脂易分解。
加热温度的设定要根据树脂种类及其熔融指数(MI)来设定。
如牌号为1C7A的LDPE树脂,其加热温度在300~325℃范围内设定。
3.适当提高熔体压强熔体所受压强越大,塑化混炼就越充分;增加熔体压强,常采用增加滤网层数或目数的方法。
如牌号为1C7A的LDPE树脂采用目数分别为85、110、85的三层滤网,使溶体压强在1.2~1.4MPa范围内。
4.适当提高螺杆转速螺杆转速越大,单位熔体所受螺杆剪切次数越多,塑化混炼就越充分。
但螺杆转速增大,挤出薄膜厚度增加。
故应注意螺杆转速、涂复速度与挤出薄膜厚度三者的匹配。
二、树脂的氧化程度粘流态树脂经模唇挤出到接触基材的过程中,被空气中的氧气氧化而产生极性,提高挤出复合剥离强度。
气隙即模唇到两薄膜(即挤出薄膜与基材)复合线的距离。
气隙大、氧化程度高。
但气隙过大,热损失就大,从而降低剥离强度。
气隙一般在9~12cm范围内调整。
三、树脂温度与基材接触时的树脂温度高,则剥离强度高。
通常采用提高模头温度的方法,来提高树脂温度。
但模头温度过高,则挤出薄膜发生边厚,且易使模唇发生氧化、树脂发生碳化现象。
如挤出牌号为1C7A的LDPE树脂时,模头各区温度在323~328℃范围内设定。
要注意做好日常的模唇维护保养工作。
停车时要使树脂挤出模唇外少许,防止氧气进入;开车时要用软铜片反复清理模唇,防止碳化的树脂附在其上,影响复合质量。
四、挤出薄膜在高温状态与基材接触的时间树脂经模唇挤出后,其在高温状态与基材接触的时间越长,剥离强度越高。
故应调整模头适当偏向胶辊侧少许,使挤出薄膜与基材接触的时间增加。
但要注意被复合基材的耐高温性,以免影响复合质量。
五、压辊压力与冷却辊状态1.挤出薄膜与基材接触后经冷却辊与胶辊挤压后粘接在一起。
压辊压力大,冷却辊与胶辊对复合膜的挤压力大,剥离强度就大。
但要考虑设备的承受能力,一般压辊压力在4kg/cm2左右调节。
2.冷却辊表面温度应适当提高,可增加剥离强度。
但温度过高不利于操作,一般在20~25℃范围内,在不影响产品外观的情况下,选用网线式冷却辊,可增加对薄膜的挤压面积,从而提高挤出复合的剥离强度。
六、涂复速度涂复速度降低,则可提高挤出复合剥离强度。
但涂复速度降低,意味着班产量降低、产品成本增加。
七、被复合基材的表面张力及温度被复合基材的表面张力越大,挤出复合剥离强度越高;其表面张力应大于38dyn/cm2。
被复合基材与挤出薄膜复合时的温度差越小,挤出复合剥离强度越高。
因而在保证被复合基材干燥清洁的基础上,通过干燥箱对基材进行预热,降低与挤出薄膜复合时的温度差。
八、涂布异氰酸酯类AC剂或双组份聚氨酯粘合剂在挤出复合工艺,基材涂布异氰酸酯类AC剂后,经干燥箱干燥后与挤出薄膜复合,可提高挤出复合剥离强度。
也可采用涂布双组份聚氨酯粘合剂,以较少的干量如1~2g来获得理想的剥离强度。
提高挤出复合的剥离强度,还可通过对螺杆的专业化设计来进行。
拥有挤出复合设备的软包装企业,要通过对以上各工艺因素的优化组合,在保证产品剥离强度的基础上,提高生产效率,降低制造成本,不断提升企业市场竞争力。
挤出复合工艺具有投资少、成本低、生产效率高、操作简便等多方面的优点,因此,它在塑料薄膜的复合加工中占有相当重要的地位。
但是,在实际生产中也难免会出现这样或那样的问题。
本文,就以最为常见的剥离强度差为例与大家共同进行分析探讨。
一、薄膜基材对剥离强度的影响1、基材表面处理效果对剥离强度的影响。
被涂布基材应当预先进行电晕处理,电晕处理后的表面张力应当达到40达因以上,这样可以改进基材同熔融挤出树脂的粘结性,从而提高挤出复合强度。
因此,在生产前要检测基材的表面张力是否达到要求,一发现表面张力太低,应立即更换基材或对基材重新进行表面处理。
此外,经表面处理过的薄膜,其表面张力应当是均匀一致的,否则也会对剥离强度产生一定的影响,造成剥离强度不均匀、不一致的问题。
2、基材表面清洁度对剥离强度的影响。
被涂布基材表面应当清洁、干净,无灰尘、无油污,如果基材表面不太清洁,粘附了灰尘、油脂等污物,就会直接影响到熔融树脂跟塑料薄膜表面的粘合力,从而使挤出复合膜的粘接强度下降。
3、其它因素的影响。
对于一些易吸湿的薄膜材料(比如尼龙薄膜),如果已经发生吸湿现象,这也会影响挤出复合膜的粘接牢度。
因此,对于易吸湿的薄膜材料一定要注意防潮,尼龙薄膜在使用前和使用后应当及时用铝箔将其包裹好。
二、油墨对剥离强度的影响1、油墨质量对剥离强度的影响。
在实际生产过程中,有时候会出现无油墨或油墨较少部位的剥离强度好、而有油墨或油墨较多部位的粘合牢度反而比较差的现象,这就是由于所用的印刷油墨的适性不好,油墨与基材之间的粘接不良,从而造成挤出复合膜的剥离强度差。
一旦发生这种情况,应当及时更换合适的油墨,并同油墨厂商联系,共同协商和研究解决办法。
2、油墨干燥性对剥离强度的影响。
如果油墨干燥不良,特别是当油墨中大量地使用了甲苯、丁醇等沸点比较高的溶剂,而且干燥箱温度设置不当的话,就会有少量或较大量的溶剂残留在油墨层中,复合后可能会造成复合膜的分层,使剥离强度变差。
因此,在印刷过程中一定要对油墨的干燥性能进行严格的控制,保证油墨能够充分干燥。
此外,在印刷过程中还要注意对印刷速度和干燥温度等工艺条件的控制,因为它们也会对油墨中溶剂的挥发速度产生一定的影响。
如果印刷速度较快,且印刷机干燥箱的温度又比较低的话,油墨中的溶剂可能无法完全挥发掉,这些残留的溶剂就会在薄膜上形成一些小泡,使复合膜粘接牢度下降。
一般来说,在设定干燥箱的温度时,必须要综合考虑印刷速度、油墨的干燥速度、承印物材料的种类以及印刷图像的大小等因素。
三、挤出复合用树脂对剥离强度的影响1、树脂类型对剥离强度的影响。
挤出涂布复合用树脂可以是聚乙烯、聚丙烯、EVA、Surlyn、 Nucler、Bynel、EVAL、EAA、EMAM等。
挤出涂布复合的目的不同,选用的树脂也不同。
例如,用于普通层复合塑料制袋用的,可以采用热封性较好的各种热封用树脂;用于夹心挤复用的树脂,要求同面层和内封层塑料层均有良好的相容性的,可根据面层及内封层材料的不同选用各种相容剂树脂,如 Surlyn、Nucler、Bynelr等。
如果树脂选用不当,会影响到它同被涂布基材的相容性,从而影响到挤出复合强度。
2、树脂熔融指数(MI)对剥离强度的影响。
熔融指数(MI)是指树脂熔融料在一定温度和一定压力下,在lOmin内通过标准毛细管的重量值,以克/1Omin表示。
熔融指数(MI)是树脂流动性的一种指标,一般来说,树脂的熔融指数(MI)越高,则其流动性越好,熔融薄膜的粘度越低,粘合力越大。
在挤出复合工艺中,不宜选用熔融指数(MI)太小的树脂。
如果树脂的熔融指数(MI)偏小,其分子量较大,则融合性比较差,不能与被涂布基材很好地粘合,致使剥离牢度有所下降。
比如在使用LDPE树脂进行挤出复合时,一般选用熔融指数(MI)在4--7g/1Omin 的LDPE树脂。
3、树脂密度对剥离强度的影响。
树脂的密度越小,支链含量越高,表面越容易被活化,粘合力就越大,对剥离强度的提高也就越有利。
4、树脂中助剂及水分含量对剥离强度的影响。
树脂中的助剂,特别是润滑剂对挤出复合膜的剥离强度有着很大的影响,比如在使用LDPE树脂进行挤出复合时,应当选用不含或少含润滑剂的挤出涂覆级树脂粒子,例如北京燕山石化公司的1C7A树脂。
此外,如果树脂中所含的水分比较多的话,在挤出复合过程中可能会发生塑化不良现象,从而影响复合膜的剥离强度。
四、挤出复合工艺对剥离强度的影响1、挤出机温度对剥离强度的影响。
挤出机机筒温度和T模温度的控制极为重要,是挤出复合工艺的关键和核心。
温度太低,树脂塑化不良,从模口流延下来不能很好地与基材复合,致使剥离牢度下降;温度高,流出的熔薄膜氧化越充分,表面产生极性分子,对基材的亲和力越大,剥离强度也就越高。
但是温度也不宜过高,否则树脂容易分解,还可能会烫伤基材,而且还会产生烟雾,污染工作环境。
一般来说,挤出机机筒的温度通常控制在150℃一340℃之间,T模的温度通常控制在310℃--340'C左右,这还要根据挤出复合设备和所用树脂的具体情况来设定。
2、树脂温度对剥离强度的影响。
树脂温度高,有利于熔融塑料膜在被涂布基材上的润湿和渗透,因而有利于复合强度的提高,但过高会引起分解,一般不超过350℃。
如果树脂与基材压着时的温度过低,树脂表面氧化不充分,应当适当提高树脂温度。
3、气隙对剥离强度的影响。
气隙是指从挤出模口到复合冷却钢辊、压力辊接触线之间的距离。
由于气隙的存在,热熔膜表面会同空气中的氧气发生氧化作用,氧化后的热熔膜被涂布塑料薄膜复合时的剥离牢度会大大提高。
气隙的大小对挤出剥离强度也有很大的影响,气隙太小,树脂表面氧化不充分,致使挤出复合强度变差;气隙大,热熔膜同空气接触的时间长,热熔膜表面被空气中氧气氧化的程度越厉害。
增加极性基因,树脂同基材表面的黏结力也就越大,从而有利于复合强度的提高。
但如果气隙太大,则热熔膜的热损失过大,温度会降低得过多,在复合时的温度过低,反而会引起剥离强度的下降,而且热封性也变差。
因此,挤出复合时应当根据实际情况来调节气隙的大小,一般来说,气隙控制在 50mm—l00mm之间为宜。
4、复合压力对剥离强度的影响。
复合压力小,熔融树脂与基材之间贴合不紧密,会使剥离牢度下降。
但复合压力也不可太大,否则基材容易被压变形。
5、冷却钢辊表面温度对剥离强度的影响。
冷却辊采用的是表面镀铬的钢辊筒,其作用是将熔融树脂薄膜的热量带走,让粘合后的复合膜立即冷却、固化,以形成较强的内聚力,使熔融薄膜跟被涂布基材粘牢、定型,不产生相对位移,从而保证良好的剥离强度。