材料失效分析案例分析..
金属材料失效分析案例PPT

04
案例四:金属材料脆性断裂 失效
失效现象描述
金属材料在无明显塑性变形的情况下 突然断裂,断口平齐,呈脆性断裂特 征。
断裂发生时,材料内部存在大量微裂 纹和空洞。
断裂前材料未出现明显的塑性变形, 无明显屈服现象。
失效原因分析
材料内部存在缺陷,如微裂纹、夹杂物等,降低 了材料的韧性。
金属材料在加工过程中受到较大的应力集中,如 切割、打孔等操作,导致材料内部产生微裂纹。
失效机理探讨
电化学腐蚀
金属材料与腐蚀介质发生 电化学反应,导致表面氧 化或溶解。
应力腐蚀
金属材料在应力和腐蚀介 质的共同作用下发生脆性 断裂。
疲劳腐蚀
金属材料在交变应力和腐 蚀介质的共同作用下发生 疲劳断裂。
03
案例三:金属材料热疲劳失 效
失效现象描述
金属材料表面出现裂 纹
疲劳断裂,即在交变 应力的作用下发生的 断裂
02
疲劳断裂通常发生在应力集中的 部位,如缺口、裂纹或表面损伤 处。
失效原因分析
金属材料在循环应力作用下,微观结 构中产生微裂纹并逐渐扩展,最终导 致断裂。
应力集中、材料内部缺陷或表面损伤 等因素可加速疲劳裂纹的萌生和扩展 。
失效机理探讨
金属疲劳断裂是一个复杂的过程,涉及微观结构、应力分布、材料缺陷等多个因素。
应力腐蚀开裂
在腐蚀介质和应力的共同作用下,焊接接头 处发生应力腐蚀开裂,裂纹扩展导致断裂。
感谢您的观看
THANKS
金属材料在低温环境下工作,材料的韧性下降, 容易发生脆性断裂。
失效机理探讨
金属材料的脆性断裂通常是由 于材料内部存在缺陷或应力集 中导致的微裂纹扩展。
在低温环境下,金属材料的韧 性下降,容易发生脆性断裂。
fmea失效模式分析案例
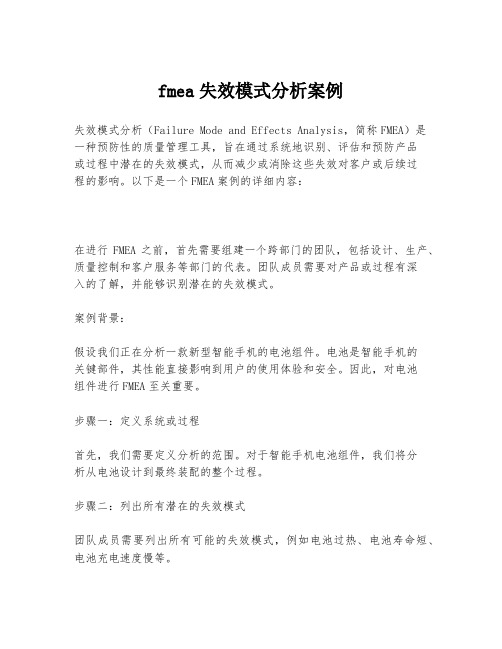
fmea失效模式分析案例失效模式分析(Failure Mode and Effects Analysis,简称FMEA)是一种预防性的质量管理工具,旨在通过系统地识别、评估和预防产品或过程中潜在的失效模式,从而减少或消除这些失效对客户或后续过程的影响。
以下是一个FMEA案例的详细内容:在进行FMEA之前,首先需要组建一个跨部门的团队,包括设计、生产、质量控制和客户服务等部门的代表。
团队成员需要对产品或过程有深入的了解,并能够识别潜在的失效模式。
案例背景:假设我们正在分析一款新型智能手机的电池组件。
电池是智能手机的关键部件,其性能直接影响到用户的使用体验和安全。
因此,对电池组件进行FMEA至关重要。
步骤一:定义系统或过程首先,我们需要定义分析的范围。
对于智能手机电池组件,我们将分析从电池设计到最终装配的整个过程。
步骤二:列出所有潜在的失效模式团队成员需要列出所有可能的失效模式,例如电池过热、电池寿命短、电池充电速度慢等。
步骤三:确定失效模式的潜在原因对于每个失效模式,团队需要确定可能导致该失效的原因。
例如,电池过热可能是由于电池设计不当、材料选择错误或制造过程中的缺陷。
步骤四:评估失效模式的严重性使用1到10的评分系统,团队需要评估每个失效模式的严重性。
评分越高,表示失效对客户或后续过程的影响越大。
步骤五:确定失效模式的潜在后果团队需要确定每个失效模式可能导致的后果。
例如,电池过热可能导致设备损坏或用户受伤。
步骤六:评估当前控制措施的有效性团队需要评估现有的控制措施是否能够有效预防或检测到潜在的失效模式。
例如,是否有严格的质量控制流程来检测电池的过热问题。
步骤七:计算风险优先数(RPN)风险优先数是通过将严重性(S)、发生概率(O)和检测难度(D)的评分相乘得到的。
RPN越高,表示该失效模式的风险越大。
步骤八:制定改进措施对于高RPN值的失效模式,团队需要制定改进措施。
这些措施可能包括重新设计电池、改进制造工艺或加强质量控制。
失效案例分析

30
15
b.氢致开裂(HIC)
在钢的内部发生氢鼓 泡区域,当氢的压力 继续增高时,小的鼓 泡裂纹趋向于相互连 接,形成有阶梯特征 的氢致开裂。氢致开 裂发生不需要外加应 力(载荷应力、残余 应力),故从概念讲 不属于应力腐蚀破坏 范畴。
31
32
16
33
c.硫化物应力腐蚀开裂(SSCC)
• 硫化氢在液相水中,由于电化学的作用,在阴极反应时生成氢 原子渗透到钢的内部,溶解于晶格中,导致脆性增加(氢原子 渗透到钢的内部晶格,在亲和力的作用下生成氢分子,钢材晶 格发生变形,材料韧性下降,脆性增加),在外加拉应力或残 余应力的作用下形成开裂。
2、焊接裂纹有不同的特性,要根据不同的裂纹产生机理 及形式选择检测的时机与方法,提高检验的有效性。
• 延迟裂纹 • 液化裂纹
3、对于易产生焊接裂纹的钢种,一旦发现裂纹,应扩大 检验比例。
11
案例1:反应流出物换热器管箱入口不锈钢法兰开裂
某石化炼油厂,2010年大修检验发现,反应流出物换热器管箱入口 不锈钢法兰开裂。 主要原因:
P≤0.008%、Mn≤1.30%,且应进行抗HIC性能试验或恒 负荷拉伸试验。
40
20
在湿硫化氢应力腐蚀环境中使用的其它材料制设备和管 道应符合下列要求:
铬钼钢制设备和管道热处理后母材和焊接接头的硬度应不 大于HB225(1Cr-0.5Mo、1.25Cr-0.5Mo)、HB235 (2.25Cr-1Mo、5Cr-1Mo)或HB248(9Cr-1Mo);
27
湿硫化氢环境分类(NACE 8X196) 一类:不选用抗HIC钢,可不做热处理 二类:可选抗HIC钢,要进行热处理 三类:选用抗HIC钢,要进行热处理
基于人工智能的材料失效案例分析和腐蚀预测模型

基于人工智能的腐蚀预测模型构建
01
02
03
04
数据收集与处理
收集大量关于材料、环境 因素和腐蚀程度的数据, 并进行预处理,以提高模 型的准确性。
特征选择与提取
从数据中提取与腐蚀行为 相关的特征,如温度、湿 度、pH值、材料机器学习算法 ,利用训练数据对模型进 行训练和优化,以提高预 测精度。
传统分析方法的局限性
传统的材料失效分析方法通常基于经验和实验室试验,难以全面、快速地分析复杂服役 条件下的材料失效原因。
人工智能技术的应用
随着人工智能技术的发展,利用机器学习、深度学习等技术对材料失效案例进行智能分 析和预测成为可能,有助于提高失效分析的准确性和效率。
研究目的和任务
• 研究目的:本研究旨在利用人工智能技术对材料失效案例进 行深入分析和预测,为预防和减少材料失效提供科学依据和 技术支持。
实际应用中,失效案例可能较为 稀少,导致训练数据不足。解决 方案包括数据扩充、迁移学习等 技术。
特征提取
从非结构化或半结构化数据中提 取与失效相关的特征是一项挑战 。需采用深度学习方法自动提取 特征。
模型泛化能力
为提高模型的泛化能力,需采用 集成学习等技术,结合多种模型 进行预测。
03
腐蚀预测模型
基于人工智能的材料失效案 例分析和腐蚀预测模型
汇报人: 2024-01-08
目录
• 引言 • 材料失效案例分析 • 腐蚀预测模型 • 人工智能技术在材料失效和腐
蚀预测中的应用 • 基于人工智能的材料失效和腐
蚀预测的未来展望
01
引言
研究背景和意义
材料失效问题
材料在服役过程中由于各种原因(如腐蚀、疲劳、高温等)发生失效,可能导致重大安 全事故和经济损失。
金属材料失效分析案例
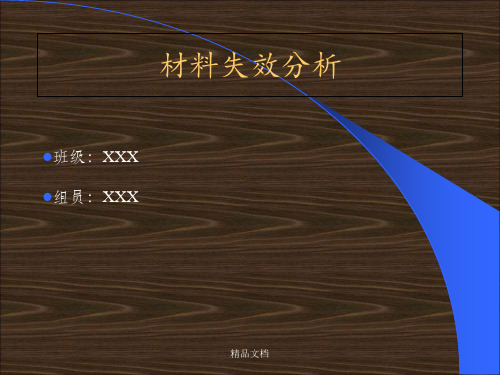
3 分析
(1)断裂叶片的金相组织为正常的回火索氏体,材料化学成分 合格,主要性能指标也基本正常。
(2)叶片断裂部位在倒*形槽根部的横断面上,亦即在应力集 中部位,是裂纹源萌生地,断口具有典型的疲劳断裂特征, 裂纹扩展属穿晶走向。
精品文档
(3)叶片根部疲劳断裂与装配质量有关,高压转子叶片安 装时通常要求根部紧配合,但裂断的第+级叶片根部却是 松配合,遂导致叶片在运行过程中产生振动并传至根部, 根部与叶轮槽表面产生摩擦,从而使根部表层晶粒持续滑 移带极易萌生裂纹,即产生疲劳源,随后裂纹不断扩展, 最终造成根部疲劳断裂。
疲劳断裂。
精品文档
材料失效分析
班级:XXX 组员:XXX
精品文档
案例 漳平电厂1号机叶片断裂失效分析
1、背景
2 检查、试验
2.1宏观检查2Biblioteka 2 断口微观检查2.3化学成分
2.4硬度测试
2.5 冲击试验
2.6 金相检查
3 分析
4 结论
精品文档
1、背景 漳平电厂1号机系北京重型电机厂制造的冲动凝汽 式汽轮机,其高压转子第8级叶片材料为2Cr13。1998年4月 大修揭盖后发现该级叶片有一段围带残缺约10cm长,有一 个叶片在根部断裂丢失,部分围带铆钉头有弹起现象。修 复工作由电厂委托北京重型电机厂进行,其修复过程为: 拆除5段围带及43片叶片,更换断裂和受损的2个叶片及损 坏的2段围带,复装后叶片与围带采用焊接固定,并对2段 围带铆钉头弹起的部位进行打磨后焊补,修后机组恢复运 行。2000年5月7日,汽轮机出现异常响声,且振动不断加 剧,揭缸后发现高压转子第8级叶片丢落19个,部分围带脱 落,第9级叶片及8、9、10级部分隔板磨损变形。对照1998 年4月大修记录,发现此次丢落的19个叶片大部分为当时修 复处理过的叶片。由于此次叶片断裂事故对转子损伤较为 严重,故把整个转子送到制造厂修复。为了找出叶片断裂 的原因,我们开展了一系列精的品文失档 效分析工作。
失效分析案例讲解
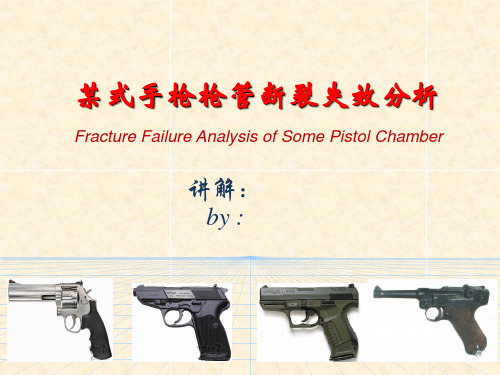
原始资料收集及失效件初步检查
枪管加工工艺 枪管材料:30CrNi2WVA 军工钢(GJB) 长:111 mm 内径:9mm 壁厚:115 mm (内壁镀铬,有6条膛线) 原材料由φ42 mm的棒材通过锻造改拔成φ28 mm 的棒材,然后经以下工艺流程制成枪管成品: 下料→调质→深孔钻→电解抛光→挤丝→去应力→ 机加工→热处理→校直→机加工→酸洗(去除氧化膜) → 镀铬→打高压弹→磁粉探伤→检验→入成品库
失效机理分析及模拟验证 模拟验证试验
取20根与断裂枪管同状态的枪管进行校直模拟试验,对 枪管施加约1 t的压力使其变形,然后进行校直(以上工艺与 实际校直工序相同),校直后进行磁粉探伤,没有发现裂纹,因 此断裂不是由于校直裂纹扩展引起的。 探伤后,所有样品放在酸洗液(去除氧化膜酸溶液)中浸 30 min,取出后清洗并放置24 h,然后再次进行探伤, 5根枪 管出现了裂纹,长度在0.5-1cm之间,裂纹源在校直压点截面 的两侧,两侧均有裂纹产生。 对裂纹枪管进行高压试验,枪管马上断裂,其断口的宏观、 微观形貌与失效件基本一致,说明裂纹是由应力腐蚀引起的。
断口分析 断口宏观分析
宏观断口观察发现裂纹源在枪管内表面阴、阳线的交 界线上,裂纹扩展部分有明显的放射条纹,裂纹以裂源为中 心呈弧形向外扩展,最终断裂部位有明显的剪切唇。 用显微镜观察裂纹,发现裂纹源部分有约0.02 mm深 的渗铬层(图5白色部位),明显大于整体渗铬层深度(0.01 mm),说明枪管在内膛镀铬前已经产生了裂纹。
失效件初步检查
断裂枪管的裂纹都出现在管中部(图1),即进行校直时 的压点处。裂纹源在枪管内壁阴线与阳线的交界线上,成曲 线向外扩展,裂纹长度在410cm左右。根据断口的宏观形貌 (图2),可发现断口为脆性断口,裂源区、扩展区和瞬断区分 明。
螺母凸焊失效分析报告
螺母凸焊失效分析报告开始写内容:本次螺母凸焊失效分析报告旨在分析螺母凸焊失效的原因,以及提出相应的解决方案。
以下将对失效案例进行详细描述,并进行分析。
失效案例描述:在某工程项目的装配过程中,发现一批已焊接螺母的零件出现了失效现象。
具体表现为,螺母与基板的凸焊处出现脱落和松动,导致装配中的结构不稳定。
这一失效现象严重影响了产品的使用寿命和性能。
失效分析:经过对失效零件的分析和试验,发现失效的主要原因是焊接工艺不当导致的焊点强度不足。
具体分析如下:1. 材料选择问题:初步分析表明,焊接螺母和基板所选用的材料并不匹配。
材料强度差异较大,导致焊点处的应力不均匀分布,易导致焊点脱落。
2. 焊接参数不合理:焊接过程中,焊接参数设置不合理,导致焊接温度过高或过低,影响焊点的强度和密封性。
此外,焊接时间过短也会导致焊点质量下降。
3. 焊接工艺不规范:焊接工艺操作不规范,如焊接机器的摆放不正确、焊接过程中的振动或冲击等,都可能导致焊点结构松动。
解决方案:为解决螺母凸焊失效问题,我们提出以下解决方案:1. 材料选择优化:重新评估螺母和基板的材料匹配性,选择相匹配的材料,以提高焊点的强度和耐久性。
2. 焊接参数优化:根据材料特性和焊接要求,调整焊接参数,确保适当的焊接温度、时间和压力,提高焊接质量。
3. 焊接工艺规范化:制定严格的焊接工艺规范,明确操作要求和流程。
同时,加强对焊接工艺的培训和监控,确保操作人员掌握正确的焊接技术。
结论:通过对螺母凸焊失效案例的分析,我们发现焊接工艺不当是导致螺母凸焊失效的主要原因。
为了提高产品的质量和性能,我们将采取上述解决方案,优化材料选择、焊接参数和焊接工艺,以确保焊点的强度和稳定性。
这将有助于预防类似失效事件的再次发生,提高产品的可靠性和安全性。
模具失效案例分析
2 模具失效分析
• 通常,热锻模的常见失效形式有: 表面磨损,高温 氧化,热疲劳裂纹。本公司的前胎模具的主要失 效形式为型腔表面磨损。表面磨损是指坯料在模 具型腔中塑性变形时,沿型腔表面既流动又滑动 ,使型腔表面与坯料之间产生剧烈的摩擦,从而 导致模具磨损而失效。型腔磨损的结果是使成型 的坯料实际尺寸偏离设计尺寸,因此磨损达一定 程度后的模具因不能再使用而报废。对失效模具 进行如下分析。
模具失效分析案例1Fra bibliotek012Al 钢模具失效分析
以高速锻前胎模具为 对象,研究其早期失效 机制,在此基础上优化 热处理工艺,提高模具 使用寿命,取得了一定 成效。
2
1 前胎模具材料及寿命
前胎模具的外形如图1 所示,是 轴承行业普遍应用的热挤压模, 用012Al( 5Cr4Mo3SiMnVAl) 模 具钢制作。012Al 钢具有较高的 高温强度和较优良的热疲劳性能 [1],其热处理工艺流程为: 球 化退火—淬火—3 次回火,最终 硬度要求为59 ~ 61HRC。
1) 材料成分
用直读光谱法对前胎模具材料成分进行分 析,结果列于表1,模具成分与012Al 钢 的标准成分[1]相符合。
2) 材料硬度
• 沿前胎模具横向切割 试块,如图2箭头所示 从里到外测定的硬度 值依次为58 HRC,57 HRC,56 HRC,54 HRC,56 HRC,56 HRC,57HRC,没有 达到技术要求值( 59 ~ 61 HRC)
5 结论
• 012Al 钢热挤压模具早期失效是由于球化退 火和淬火工艺不合理,导致模具显微组织 不良、硬度偏低所致。按改进后的工艺退 火和淬火后,该模具的显微组织明显改善 ,硬度也达到了技术要求,因此使用寿命 有了大幅度提高。
失效分析实例
材料失效分析
材料失效分析
2、实验过程
• 图7 .58是两个断口表面的低倍放大照 片,图7. 59 和这两个端口表面的位 置和方向。在照片中分辨出两个明显 的区域:外表面,即承受载荷时的最 大纤维应力区,没有发生尺寸改变的 迹象,而在中心区域则看到一些尺寸 改变。此外在表面上有一些明显的塑 性变形,应该是发生最后断裂的地点。 • 将钳柄上的塑料套剥掉以曝露钳柄的 区域。钳的前部镀铬,直至塑料套的 边缘。钳柄的表面上有一层乌黑的物 质,该钳必定是要装塑料套后再进行 电镀的。表面上的乌黑层或是塑料套 留下的,或是一种热处理造成的。 • 目视检查后,分三步进行分析以决定 失效的原因。首先评价对改签剪线操 作的设计应力水平,之后对所用材料 及热处理工艺进行金相检验,最后利 用扫SEM对断口进行仔细的检验
材料失效分析
3、实验结果
• 断口形貌
低倍放大的断口形貌如图7.28所示,没有宏观塑性变形的迹 象。裂纹从左边缘向内扩展通过厚度1/4左右,断裂表面粗糙无 规律,而其余的断口表面是光滑的,在光滑的表面上可以看到贝 壳状花纹,故断裂模式是疲劳。粗糙的断口表面显示出这是最后 因超载而分离的区域并向前扩展到一个孔的边缘,表明疲劳裂纹 不是起源于此孔的边缘,而是沿着右边缘的。这一点在观察断口 表面时也就是在切开试样之后得到证实。贝壳状条纹的弯曲部分 表明疲劳裂纹直接起源于另一螺栓孔的下面(图7 .29),与围绕 该螺栓孔的同心圆槽重合 • 在接近末端处偏离开其中之一螺棒孔的断口表面已严重研 磨(但仍能看到有贝壳状花纹)(图7. 28)而另一端则很少的 磨损伤,并发现有疲劳条纹(图7.31)(疲劳条纹在显微组织复 杂的钢中不常出现。本案例中的显微组织主要是晶粒尺寸均匀的 单相铁素体。)试块切开后产生的断口表面如图7 .32所示,且 有韧窝状的形貌,表面这个区域是因空洞聚集而产生的 •
失效分析案例
案例3 3Cr2W8V钢热锻模具淬火开裂原因分析 1 背景 2 检验内容及结果
2 1 原材料化学成分 2 2 硬度测定 2 3 断口形貌
(1)宏观检查 (2)断口微观检查 2. 4 显微组织分析 3 讨论 4 结论
1、背景 某厂选用3Cr2W8V钢制造热锻模具用于锻造 25钢的齿状零件,模具加工成型后外部尺寸为500mm ×250mm×115mm,模具质量为110kg。在同一模具上
开出预锻和终锻两个型腔,加工时发现模具毛坯锻件硬 度偏高,采用HR150型洛氏硬度计测试硬度为30HRC。 为便于加工,该厂将模具进行了一次降低硬度退火,但温度 和时间已无纪录。加工后的模具由本厂进行热处理,淬火 加热炉采用箱式电阻炉。为防止氧化,在模具周围填充旧 渗碳剂加以保护。模具淬火时先采用500℃、850℃两次 预热,后经1050℃×4h保温,冷却介质选用N15号机油。 淬火过程中听到模具开裂声音,随即停止冷却,并放在 630℃回火炉中回火,回火时裂纹继续扩展使模具成为多个 碎块。由于发现模具开裂, 中止继续回火。
图6的金相组织表明,奥氏体晶粒粗大,马氏体粗大,属于明 显的过热现象。但模具表层细瓷状断口(图2、3)和细小晶 粒(图5),属于正常的淬火组织。分析认为:厂方在加工模具 时,发现锻件的硬度偏高,曾经进行一次降低硬度退火,但退 火保温时间不够,仅使表层重结晶细化,因此出现了表层的 细晶粒和细瓷状断口。
2 3 断口形貌
(1)宏观检查 模具横向多处断裂,裂纹特征有直裂纹、弯 折裂纹和圆弧裂纹,
在模具碎块的横断面表层可观察到有约30mm细瓷状 断口,见图2。断口内部有山脊状扩展形貌,放射线中心朝 向模具心部,表明裂纹源形成于模具心部。心部为粗晶状 断口,有十分明显的金属光泽。上述特征可以判定该模具 的开裂是由心部脆性解理断裂引发的。