膜厚测试报告
关于膜厚测试的标准单位换算

关于膜厚测试标准单位换算标准文件GX-MQ-001起草:审核:批准:20 年月日发布 20 年月日实施在连接器或线材行业中,免不了要做膜厚报告,其中经常会碰到关于膜厚报告中常用到U",这个单位是怎么回事呢?为什么读音念”麦”?关于膜厚单位这个问题,在五金行业可以说是非常重要的,在电镀行业更是不可忽视的。
有人说,1μm等于39.37 u",这个单位无从查考,但这个u"(读音为“麦”)却在电镀行业风行,对它的含义却少有人研究或考证,另外还有mil(密耳)这个单位也容易混淆。
笔者就来研究这个问题。
(1)首先说μm和μin的关系。
μin是不是u"(读mai),姑且不论,μin的确就是μinch,中文叫微英寸,下面论述1μm=39.37μinch是如何推导出来的。
1inch=10000000μin ch1英尺=12英寸=0.914市尺=30.48厘米,1英寸=25.4毫米,英尺=12英寸如上所述,微英寸即为μin= 0.0254/1000米,即μin= 0.0254mm, 1mm=1000μm1000μin= 25.4μm,即1μm=39.37μin(2)其次再说说u"和μm的关系。
u"是镀层膜厚单位;全称就是micro inch,就是微英寸,因为μin就是u"的简写符号,uin是μinch的简写符号,只是μinch并不是纲量定律指定的单位。
μin= u"故1μm=39.37u"在网上经常可以看到1000μin=25.4μm,变换公式就是:μm=39.37u",注意:1μin(微英寸)并不是μm(微米),首先μm(念谬)与u"(念麦)是不同的概念,而电镀行业经常将这两个概念误用,比如镀金来讲吧,如果误用,应该有相当大的成本损耗或引起经济上的纠纷。
例如用u"表示为:镀银为80 u"镀金为:1u"雾锡:80u"镀镍:50u"而用微米μm来表示则为:滚镀锌4-8 μm。
镀膜误差分析报告范文

镀膜误差分析报告范文1. 引言镀膜技术在光学领域具有广泛的应用,用于改善材料的光学性能。
然而,在制备过程中可能出现误差,导致镀膜膜层的质量和性能下降,进而影响产品的品质。
本报告旨在对一个镀膜过程中的误差进行分析和解决,以提高镀膜质量和减少产品缺陷。
2. 问题描述在一个光学镜片的镀膜过程中,出现了膜层厚度不均匀的问题,即中心区域膜层厚度过薄,边缘区域膜层厚度过厚。
2.1 数据收集我们首先对多个镜片进行了厚度测量,得到了不同位置的厚度数据。
具体数据如下:位置厚度测量值(nm)中心点150边缘点3002.2 问题分析通过对数据的分析,我们可以得出以下结论:- 中心点的厚度测量值明显低于边缘点的厚度测量值;- 在多个镜片中都出现了相似的问题。
3. 原因分析为了找出引起厚度不均匀的原因,我们对镀膜过程进行了分析,并找到了可能的原因。
3.1 激发电流不均匀性在镀膜过程中,激发电流的不均匀性可能会导致镀膜层的厚度分布不均。
通过对设备进行检查,我们发现部分电极存在连接问题,导致电流分布不均匀。
3.2 蒸发船温度控制问题镀膜过程中,蒸发船的温度是影响膜层厚度的重要参数。
通过观察,我们发现蒸发船的温度控制存在不稳定的问题,导致镀膜层的厚度不一致。
4. 解决方案基于以上的原因分析,我们提出了以下解决方案。
4.1 修复电极连接问题我们将对设备中的电极进行维修和更换,以确保激发电流分布均匀。
这样可以消除电流不均匀性对膜层厚度的影响。
4.2 温度控制系统升级我们将对蒸发船的温度控制系统进行升级,以确保温度的稳定性。
这样可以改善蒸发过程中温度的不均匀性,从而提高膜层厚度的均匀性。
4.3 进行多次测试和优化在实施解决方案之后,我们将对镀膜过程进行多次测试和优化,以确保镀膜厚度的均匀性和一致性。
5. 结论通过对镀膜过程中厚度不均匀问题的分析,我们确定了激发电流不均匀性和蒸发船温度控制问题是造成问题的原因。
通过修复设备中的电极连接问题和升级温度控制系统,可以解决该问题。
涂层厚度检测作业指导书

涂层厚度检测1适用范围本作业指导书适⽤于快速⽆损地测量导磁材料表⾯上⾮导磁覆盖层厚度。
例如:铁和钢上的铜、锌、镉、铬镀层和油漆层等。
2 检测时标准GB/T 4956-2003 《磁性基体上⾮磁性覆盖层覆盖层厚度测量磁性法》;GB/T 18226-2015 《公路交通⼯程钢构件防腐技术条件》;GB/T 31439.1-2015 《 波形梁钢护栏第1部分两波形梁钢护栏》。
GB 50205-2001 《钢结构⼯程施⼯质量验收规范》GB/T 50621-2010 《钢结构现场检测技术标准》3仪器设备HCC-24型磁阻法测厚仪。
4检测目的检测道路交通安全设施涂层厚度值满⾜《磁性基体上⾮磁性覆盖层覆盖层厚度测量磁性法》GB/T 4956-2003规范和设计图纸要求。
检测钢结构⼯程施⼯涂层厚度值满⾜《钢结构⼯程施⼯质量验收规范》GB 50205-2001规范和设计图纸要求。
5资料收集1⼯程名称、钢构件表⾯保护层材料和⼯艺分类及相应图纸;2建设、设计、施⼯及监理单位名称。
6现场检测6.1抽查频率6.1.1波形梁钢护栏每公⾥抽查不少于1处;6.1.2波形梁钢护栏每处测不少于5点;6.1.3钢结构中按构件数抽查10%,且同类构件不应少于3件。
6.2技术指标依据GB/T 18226-2015《公路交通⼯程钢构件防腐技术条件》,所检的波形梁护栏镀层厚度值检测值应在规范要求允许偏差范围内或符合设计要求。
依据GB 50205-2001《钢结构⼯程施⼯质量验收规范》,涂料、涂装遍数、涂层厚度均应符合设计要求。
当设计对涂层厚度⽆要求时,涂层⼲漆膜总厚度:室外应为150um,室内应为125um,其允许偏差应为-25um。
每遍涂层⼲漆膜厚度的允许偏差为-5um。
依据GB/T 50621-2010《钢结构现场检测技术标准》,每处3个测点的涂层厚度平均值不应⼩于设计厚度的85%,同⼀构件上的15个测点的涂层厚度平均值不应⼩于设计厚度。
电镀产品出厂检验报告
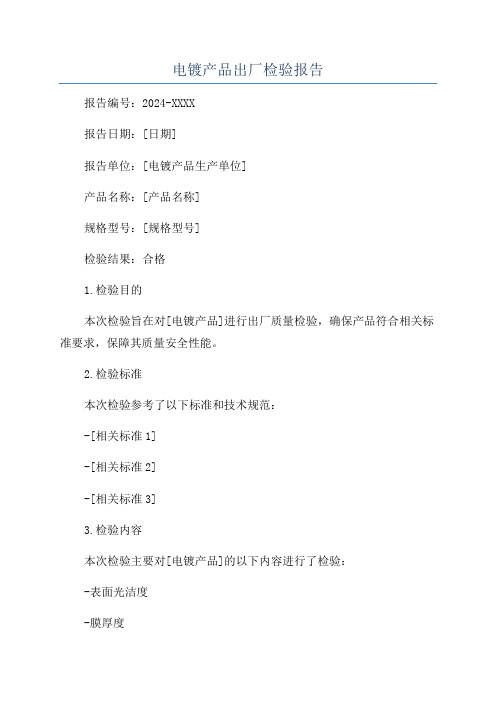
电镀产品出厂检验报告报告编号:2024-XXXX报告日期:[日期]报告单位:[电镀产品生产单位]产品名称:[产品名称]规格型号:[规格型号]检验结果:合格1.检验目的本次检验旨在对[电镀产品]进行出厂质量检验,确保产品符合相关标准要求,保障其质量安全性能。
2.检验标准本次检验参考了以下标准和技术规范:-[相关标准1]-[相关标准2]-[相关标准3]3.检验内容本次检验主要对[电镀产品]的以下内容进行了检验:-表面光洁度-膜厚度-附着力-相容性-耐腐蚀性4.检验方法(1)表面光洁度检验:使用显微镜对产品表面进行观察,检查是否存在明显缺陷、气泡、杂质等。
(2)膜厚度测量:使用膜厚测量仪对产品膜层厚度进行测量,确保其符合标准要求。
(3)附着力测试:使用划格法对产品膜层与基材之间的附着力进行测试,判断其附着力是否合格。
(4)相容性测试:将产品暴露于指定试剂中,观察其表面是否出现异常变化。
(5)耐腐蚀性测试:将产品置于指定的腐蚀介质中,浸泡一段时间后观察其表面情况,判断其耐腐蚀性能。
5.检验结果经过以上检验项目的检测,本次[电镀产品]出厂检验结果如下:(1)表面光洁度:经观察,产品表面光洁,没有明显缺陷、气泡和杂质。
(2) 膜厚度:产品膜层厚度测量值为XXum,符合标准要求。
(3)附着力:产品膜层与基材之间的附着力经划格法测试,均达到标准要求。
(4)相容性:产品暴露于指定试剂中,表面没有出现异常变化。
(5)耐腐蚀性:产品经过腐蚀介质浸泡后,表面没有明显腐蚀现象。
6.结论根据本次检验结果,[电镀产品]通过出厂检验,符合相关标准要求,质量合格。
产品可进行包装出货,并符合相关标诺。
7.检验人员签名:[签名]8.备注如有其他特殊说明或发现的问题,在备注中进行详细说明,并提出后续处理建议。
关于涂层测厚检测实验报告
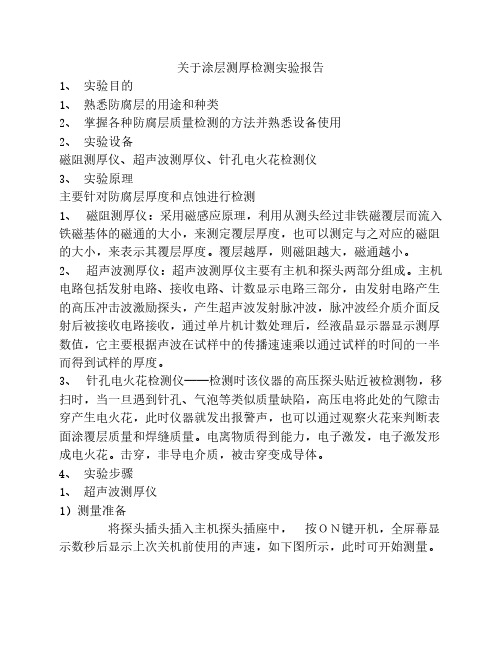
关于涂层测厚检测实验报告1、 实验目的1、 熟悉防腐层的用途和种类2、 掌握各种防腐层质量检测的方法并熟悉设备使用2、 实验设备磁阻测厚仪、超声波测厚仪、针孔电火花检测仪3、 实验原理主要针对防腐层厚度和点蚀进行检测1、 磁阻测厚仪:采用磁感应原理,利用从测头经过非铁磁覆层而流入铁磁基体的磁通的大小,来测定覆层厚度,也可以测定与之对应的磁阻的大小,来表示其覆层厚度。
覆层越厚,则磁阻越大,磁通越小。
2、 超声波测厚仪:超声波测厚仪主要有主机和探头两部分组成。
主机电路包括发射电路、接收电路、计数显示电路三部分,由发射电路产生的高压冲击波激励探头,产生超声波发射脉冲波,脉冲波经介质介面反射后被接收电路接收,通过单片机计数处理后,经液晶显示器显示测厚数值,它主要根据声波在试样中的传播速速乘以通过试样的时间的一半而得到试样的厚度。
3、 针孔电火花检测仪——检测时该仪器的高压探头贴近被检测物,移扫时,当一旦遇到针孔、气泡等类似质量缺陷,高压电将此处的气隙击穿产生电火花,此时仪器就发出报警声,也可以通过观察火花来判断表面涂覆层质量和焊缝质量。
电离物质得到能力,电子激发,电子激发形成电火花。
击穿,非导电介质,被击穿变成导体。
4、 实验步骤1、 超声波测厚仪1)测量准备将探头插头插入主机探头插座中, 按ON键开机,全屏幕显示数秒后显示上次关机前使用的声速,如下图所示,此时可开始测量。
2)声速的调整如果当前屏幕显示为厚度值,按 VEL 键进入声速状态,屏幕将显示当前声速存储单元的内容。
每按一次,声速存储单元变化一次,可循环显示五个声速值。
如果希望改变当前显示声速单元的内容,用▲或▼键调整到期望值即,时将此值存入该单元。
3)校准 在每次更换探头、更换电池之后应进行校准。
此步骤对保证测量准确度十分 关键。
如有必要,可重复多次。
将声速调整到 5900m/s 后按 ZERO 键,进入校准状态,屏幕显示:在随机试块上涂耦合剂,将探头与随机试块耦合,屏幕显示的横线将逐条消失,直到屏幕显示 4.00mm 即校准完毕。
外墙漆检验报告
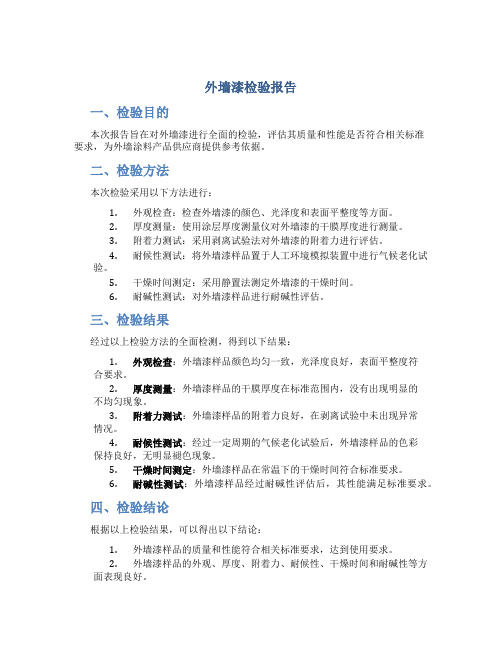
外墙漆检验报告一、检验目的本次报告旨在对外墙漆进行全面的检验,评估其质量和性能是否符合相关标准要求,为外墙涂料产品供应商提供参考依据。
二、检验方法本次检验采用以下方法进行:1.外观检查:检查外墙漆的颜色、光泽度和表面平整度等方面。
2.厚度测量:使用涂层厚度测量仪对外墙漆的干膜厚度进行测量。
3.附着力测试:采用剥离试验法对外墙漆的附着力进行评估。
4.耐候性测试:将外墙漆样品置于人工环境模拟装置中进行气候老化试验。
5.干燥时间测定:采用静置法测定外墙漆的干燥时间。
6.耐碱性测试:对外墙漆样品进行耐碱性评估。
三、检验结果经过以上检验方法的全面检测,得到以下结果:1.外观检查:外墙漆样品颜色均匀一致,光泽度良好,表面平整度符合要求。
2.厚度测量:外墙漆样品的干膜厚度在标准范围内,没有出现明显的不均匀现象。
3.附着力测试:外墙漆样品的附着力良好,在剥离试验中未出现异常情况。
4.耐候性测试:经过一定周期的气候老化试验后,外墙漆样品的色彩保持良好,无明显褪色现象。
5.干燥时间测定:外墙漆样品在常温下的干燥时间符合标准要求。
6.耐碱性测试:外墙漆样品经过耐碱性评估后,其性能满足标准要求。
四、检验结论根据以上检验结果,可以得出以下结论:1.外墙漆样品的质量和性能符合相关标准要求,达到使用要求。
2.外墙漆样品的外观、厚度、附着力、耐候性、干燥时间和耐碱性等方面表现良好。
五、改进建议为了进一步提升外墙漆的质量和性能,以下是一些建议:1.加强原材料的质量控制,确保原材料的稳定性和可靠性。
2.定期进行外墙漆生产线的设备、仪器的维护和保养,以确保生产过程的稳定性和一致性。
3.继续加强新产品的研发和推广,满足市场对不同特性的外墙漆的需求。
4.加强与供应商的沟通和合作,及时解决产品质量问题和用户反馈。
六、备注本报告所述结果仅为对样品外墙漆进行一次性检验的结果,不代表样品的长期性能和稳定性。
对于长期使用的外墙漆产品,建议定期进行检验和评估,并根据实际使用情况进行调整和改进。
钝化实验报告
钝化实验报告钝化实验报告一、引言钝化是一种常见的金属表面处理方法,通过在金属表面形成一层致密的氧化物膜,来提高金属的耐腐蚀性能。
本次实验旨在探究钝化对不同金属材料的影响,并分析其机理和应用前景。
二、实验材料和方法1. 实验材料:铁、铜、铝等金属材料。
2. 实验方法:a. 清洗:将待处理的金属材料用去离子水清洗干净,去除表面的杂质。
b. 钝化处理:将清洗后的金属材料放入含有适量酸性溶液的容器中,经过一定时间的处理。
c. 洗净:将钝化后的金属材料用去离子水洗净,去除残留的酸性溶液。
d. 干燥:将洗净后的金属材料放置在通风处晾干。
三、实验结果与分析1. 钝化前后的表面形貌观察实验结果显示,经过钝化处理后,金属表面的颜色发生了变化。
铁表面呈现出深红色,铜表面呈现出深绿色,铝表面呈现出银白色。
这些颜色的变化表明钝化处理后金属表面形成了一层氧化物膜。
2. 钝化膜的厚度测量使用显微镜对钝化后的金属表面进行观察,并测量钝化膜的厚度。
实验结果显示,铁表面的钝化膜厚度约为10微米,铜表面的钝化膜厚度约为5微米,铝表面的钝化膜厚度约为2微米。
可以看出,不同金属的钝化膜厚度存在差异。
3. 腐蚀性能测试通过对钝化前后金属材料的腐蚀性能进行测试,可以评估钝化处理的效果。
实验结果显示,经过钝化处理后,金属材料的腐蚀速率显著降低。
尤其是在酸性环境下,钝化后的金属材料几乎没有发生腐蚀现象。
这证明钝化处理能够有效提高金属材料的耐腐蚀性能。
四、钝化机理探究1. 氧化反应钝化处理中,金属表面与氧气发生氧化反应,生成金属氧化物。
这些金属氧化物具有致密的晶格结构,能够有效阻止金属与外界环境的接触,从而减缓金属的腐蚀速度。
2. 影响钝化效果的因素钝化处理的效果受到多种因素的影响,包括金属材料的种类、酸性溶液的浓度和温度等。
不同金属材料的钝化膜形成速度和厚度存在差异,这与金属的电化学性质有关。
五、钝化的应用前景1. 航空航天领域钝化处理对于提高飞机、火箭等航空器的耐腐蚀性能至关重要。
膜厚不良分析改善报告2
四、原因分析
经至生产现场了解确认: 该产品在自动机生产时,由于个别端子变形【端子高低PIN 】,插端时端子刮到自动机镶件上所造成;
端子变形个别高低PIN
因端子高低PIN,插端时高PIN端子刮在自动机镶件上 导致端子镀层刮伤
8
五、改善对策
1.立即通知电镀供应商在电镀制程中端子不可以碰到任何 异物,电镀收盘时端子及纸带不可以拉的太紧,避免把端 子拉变形; 2.在搬运过程中轻拿轻放,不可以挤压或碰撞端子保护盘;
2
二、验证
1.取客户寄回不良测试确认:发现第5PIN 膜厚NG,其他均 OK
n= 1 Au 1 = n= 2 Au 1 = n= 3 Au 1 = n= 4 Au 1 = n= 5 Au 1 = n= 6 Au 1 =
17.5 μ" Ni 2 = 20.3 μ" Ni 2 = 16.0 μ" Ni 2 = 17.2 μ" Ni 2 = 13.5 μ" Ni 2 = 19.7 μ" Ni 2 =
3.IQC加严检验,发现端子变形时立即退回电镀商处理;
9
五、改善对策
4.我司调机生产时,调机产品立即报废处理;生产时发 现端子不良时,作业员立即换盘使用【因不良比例极小】 5.现场班组长早会宣导,加强作业员的品质意思;在生 产搬运过程中轻拿轻放; 6.针对类似不良公司水平展开,杜绝类似不良再次发生;
4
二、验证
3.取不良品至放大镜下发现:端子表面有明显电镀后刮痕, 镀金层有轻微破坏【端子的最高点,即测试点】
5PIN端子镀金层有刮痕
5
二、验证
4.取库存端子批次:2012/12/19 2013/1/22测试均OK
6
水乳型沥青防水涂料检验报告格式
水乳型沥青防水涂料检验报告格式一、报告目的本报告是针对水乳型沥青防水涂料进行的检验结果总结,旨在评估该产品的质量和性能是否符合相关标准要求,以提供客观、全面的检验结果,供相关部门和用户参考。
二、检验项目及方法1.外观检查:通过目测和手感,评估涂料的色泽、光泽、均匀度、涂布性能等。
2.干燥时间:按照标准要求,在规定温度和湿度条件下,观察涂料表面的干燥时间。
3.膜厚测定:采用涂膜厚度测量仪测量涂料的干膜厚度,确保符合标准规定的要求。
4.附着力测试:采用划格法或剥离试验,评估涂膜与基材的附着力。
5.耐水浸泡性能:将涂料试件置于水中浸泡一定时间,观察涂膜是否起泡、起皮、变色等情况。
6.耐臭氧性能:将试件放置在含臭氧的环境中,观察涂膜是否出现裂纹、断裂、变色等现象。
7.抗热稳定性:将试件暴露在高温环境下,评估涂膜的耐热性能。
8.细菌污染抑制性能:通过接种试验,评估涂膜对常见细菌的抑制效果。
三、检验结果1.外观检查:涂料的色泽均匀,光泽度良好,涂布性良好。
2.干燥时间:涂料在标准温度和湿度条件下,干燥时间为X小时。
3.膜厚测定:涂膜干膜厚度为X毫米,符合标准要求。
4.附着力测试:涂膜与基材的附着力达到X级,符合标准要求。
5.耐水浸泡性能:涂膜在X小时的浸泡后,未出现起泡、起皮、变色等异常现象,符合标准要求。
6.耐臭氧性能:涂膜在臭氧环境下未出现裂纹、断裂、变色等异常现象,符合标准要求。
7.抗热稳定性:涂膜在高温环境下未出现变形、开裂等异常现象,符合标准要求。
8.细菌污染抑制性能:试验结果显示,涂料对常见细菌有较好的抑制效果,抑菌率达到X%以上。
四、结论与建议根据以上检验结果,水乳型沥青防水涂料经检验符合相关标准要求,质量和性能良好。
建议用户在使用时遵循产品说明书,做好涂料的施工前准备工作,确保施工质量。
五、附录1.检验记录表2.相关标准要求3.其他附加信息(如产品样本照片等)。
色漆和清漆漆膜厚度的测定
GB/T 13452.2-2008 色漆和清漆漆膜厚度的测定色漆和清漆漆膜厚度的测定1范围本部分规定了一系列用于测量涂敷至底材上的涂层的厚度的方法,包括测量湿膜厚度、干膜厚度、未固化粉末涂层厚度及粗糙表面上漆膜厚度的方法。
在有单个测试方法标准存在时,本部分直接引用这些标准,否则就把这些测试方法详细描述出来。
附录A给出了测试方法概述,对每个测试方法规定了适用范围、现有标准和精密度。
本部分也对与漆膜厚度测量有关的术语作了定义。
2规范性引用文件下列文件中的条款通过GB/T 13452的本部分的引用而成为本部分的条款。
凡是注日期的引用文件,其随后所有的修改单(不包括勘误的内容)或修订版均不适用于本部分,然而,鼓励根据本部分达成协议的各方研究是否可使用这些文件的最新版本。
凡是不注日期的引用文件,其最新版本适用于本部分。
IS0 463产品几何量技术规范(GPS)尺寸量具机械式千分表的设计和计量学特性IS0 3611 测量外部尺寸用螺旋测微器IS0 4618:2006 色漆和清漆术语和定义IS0 8503-1涂装油漆和有关产品前钢材预处理喷射清理钢材的表面粗糙度特性第1部分:评定磨料喷射清理表面粗糙度的ISO比较样块的技术要求和定义3术语和定义IS0 4618:2006确立的以及下列术语和定义适用于。
3.1底材substrate涂料涂敷或即将涂敷的表面。
[IS0 4618:2006]3.2涂层 coating将涂料单次或多次涂敷至底材后形成的连续层。
[IS0 4618:2006]3.3漆膜厚度 film thickness漆膜表面与底材表面间的距离。
3.4湿膜厚度 wet-film thickness涂料涂敷后立即测量得到的刚涂好的湿涂层的厚度。
3.5干膜厚度 dry-film thickness涂料硬化后存留在表面上的涂层的厚度。
3.6未固化粉末涂层的厚度 thickness of uncured powder layer在粉末涂料涂敷后、烘烤前立即测量得到的刚涂好的粉末涂层的厚度。