QA出货检验流程图
药品生产质量控制(QA)过程流程图
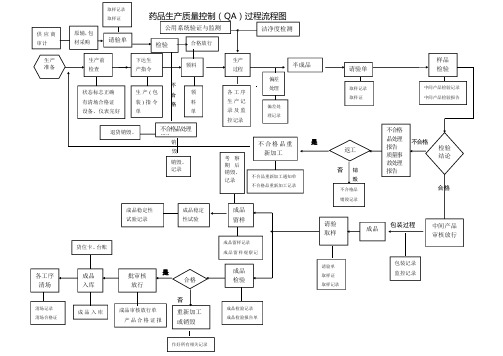
不合格销是不合格毁否销毁合格包装过程是否药品生产质量控制(QA)过程流程图生产准备生产前检查下达生产指令生产过程偏差处理样品检验检验结论返工成品成品留样生产(包装)指令单各工序生产记录及监控记录偏差处理记录半成品请验单取样记录取样证中间产品检验记录中间产品检验报告中间产品审核放行请验取样请验单取样证取样记录成品稳定性试验成品稳定性试验记录成品检验成品检验记录成品检验报告单成品留样记录成品留样观察记批审核放行合格成品入库成品审核放行单产品合格证报重新加工或销毁作好所有相关记录成品入库不合格品处理报告质量事故处理报告不合格品销毁记录不合格品重新加工不合品重新加工通知单不合格品重新加工记录状态标志正确有清场合格证设备、仪表完好领料领料单各工序清场清场记录清场合格证包装记录监控记录货位卡、台账洁净度检测公用系统验证与监测考察期后销毁、记录供应商审计原辅,包材采购请验单取样记录取样证检验合格放行不合格品处理报告退货销毁、销毁、记录文件产品质量标准省级以上药品检验报告单组织机构代码证税务登记证书应为合法有效版本审计:公司每年对所选择供应商进行审计(现场审计、非现场审计)并出具公司质量部的审计报告,具体按供应商审计管理标准内容进行。
每年未应制定出下年度的合格供应商目录,并受权人签字确认,分发至物料部门采购部门,质量部存档1.按以上目录内先择相应0购入材料的供应商,并签定购销合同及质量保证协议书同货存档,再进行采购。
1采购到位的合法材料,在进入库前进行初验,填写初验记录。
合格后进行待验区,做好状态标示及货位卡,填写请验单,请验质量部。
2.取样员取样应填写取样单、取样证、带好取样器具取样,并做好取样记录,填好货位卡的取样量。
物料部门应在取样前后做好取样车使用记录。
取过样的物料应放至最上层,生产时应先出。
1.取样后按时效进行分样检验(检验原始记录、检验台账(合格与不合格)、试剂领用、配制记录(毒剧试剂的领用、配制、销毁记录)、标准品、液领用、配制记录、标定复标记录、检验仪器使用记录、检定菌传代与使用销毁记录)并出具报告单(一式三份)。
QA检验流程

4.1.5.1、如果判定合格,检验员在产品包装盒上贴“QA PASS”标签并在《产品入库报验单》上“OK”区打“√”并签名。若让步接收,检验员在产品包装盒上贴“QA PASS”标签并在《产品入库报验单》上“特采”区打“√”并签名。QA检验员将《产品入库报验单》和检验完毕的产品实物交报验人,报验人入库。
4.1.2、QA检验员对报验产品数量进行确认后方可接收报验产品。
4.1.3、确认报验产品数量无误后,检验员根据相关订单要求检验产品尺寸及出货工单上相关参数及信息,产品尺寸测量记录填写在《QA检验记录表》中.工单检验完毕后,加盖“QA PASS”印章,然后根据对应的外观检验标准进行外观检验.
4.1.4、检验完毕QA检验员填写《QA检验报告》并做出判定后将《QA检验报告》提交QA组长审核,并给出处理意见,品保部经理批准。
4.1.5.2、如果判定不合格,检验员在《产品入库报验单》上“NG”区打“√”并签名。QA检验员将《产品入库报验单》和检验完毕的产品实物退回包装组。如果是一般不符合,包装组做出相应处理并记录结果。如不合格是严重不符,QA组长应填写《纠正和预防措施处理单》,并执行《改进控制程序》中相关内容。
4.2、报表
QA将每次检验的质量情况登记于《QA检验记录表》上,每天统计并在上午之前将前一天检验情况汇报至品质经理及品质文员处,填写《QA出货检验月报告》,交品质经理审核,总监批准。
QA工作流程
文件编号
QA-000
版本号
A0
生效日期
编制
审核
批准
4.3、QA工作流程图:
报验人填写《产品入库报验单》
退回包装组
QA对产品数量进行确认
QA对产品进行100%拆箱核对数量
产品质量检验管理程序(含流程图)
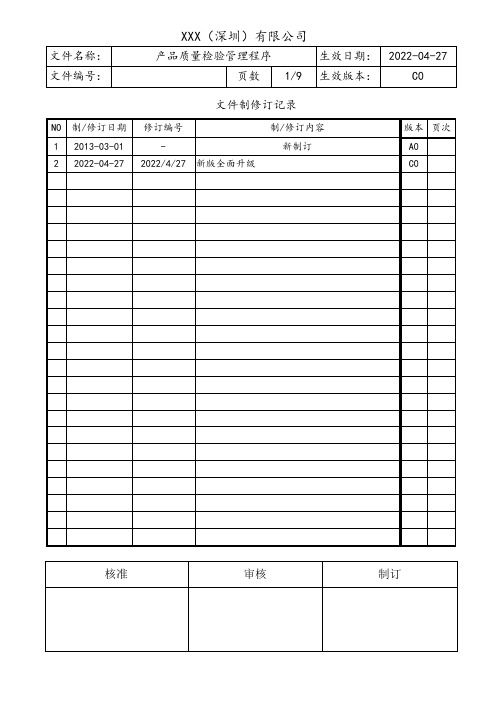
文件制修订记录1.0目的为了有效测量与监控产品从进料、制程、成品及出货各阶段检验作业能始终符合产品工程规范的各项要求。
2.0范围:适用于品管IQC、IPQC、QA过程作业。
3.0权责:3.1品管部:负责各阶段品质检验的执行、标识、追溯的管理、实际验货。
3.2工程部:产品作业标准的制定与检查。
3.3生产部:依生产计划、工程标准、验收标准执行生产作业。
3.4业务部:依订单需求验收出货数量。
3.5资材部:采购物料的外部联络。
4.0定义:无5.0作业内容:5.1进料检验5.1.1收料5.1.1.1供应商依据采购订单交货到公司仓库。
5.1.1.2仓管依据采购订单核对送货单是否一致,如若不符则退货并要求供应商重新交货,符合则点收数量并开出[进货单]。
5.1.1.3仓管将[进货单]连同要求供应商提供的相关文件(如材质报告、检验报告、测试报告等)交品管部,通知IQC进行检验。
5.1.1.4检验参照依据AQL表或依客户端需求作抽样检验。
5.1.1.5品管部IQC接到[进货单]后对供应商所提供的文件进行验证,(有法规环保类要求的产品必须依客户指定或经国家认可有检测能力机构出具的测试报告,如“SGS报告”等);品管部可以根据批量大小、价值贵重程度来对供应商所提供产品的材质进行一次确认。
5.1.1.5下列几项物料必须由品管部进料检验:a)生产性原材料。
b)外发加工产品。
c)包装材料等。
5.1.2需应用下列一种或多种方法进行验收、检验5.1.2.1接收检验及测试:a)核对材质证明(限自购原材料,样品或来料加工产品可不需要提供材质证明),核对供应商提供的相关文件。
b)依《检验标准书》逐项检验与填写[进料检验报告],无《检验标准书》时,依图面求或样板检验,检验结果可直接记录于[进料检验报告]上。
c)凡属客户提供来料进行加工,如无图面,依据客户提供的规格进行检验;如既无规格又无图面,IQC只针对其外观进行检验并记录于[进料检验报告]上。
品质稽核(QA)
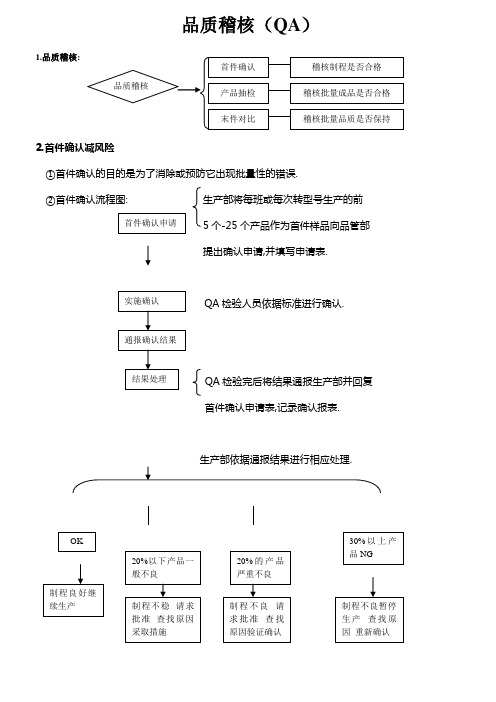
品质稽核(QA)1.品质稽核:2.①首件确认的目的是为了消除或预防它出现批量性的错误.④在自动化作业水平较高的生产中,可适当放宽首件确认的间隔。
比如,在下列情况下可以免除首件确认:仅仅是换班,并没有检修机器、更换材料、变更流程等。
3.产品抽检再放行①品管部对生产部的完成品以批量为基准实施抽样检验,合格时放行,不合格时拒收.②产品抽检的工作原理:4.末件对比能保本①末件:是指从上一批生产的最后阶段随机抽样的合格品,一般抽1PCS.对比:是指末件与本批正在生产中的QCPASS 产品进行对比.末件对比目的:确保此批产品品质不低于上批.②末件对比实施流程图:QA 工程师从已入库的上一批同MODEL 产品(最好是靠近生产结尾的)中随机抽1PCS. 如果已出货就取标准样板.QA 工程师从生产部把正在生产中的合格品随 机抽1PCS(最好是生产进行到批1/3状态 时)①②③CAR 是QA 工作最有力的武器之一,通过发行CAR,对出现的和即将要出现的问题实施纠正和预防,从而达到保证品质的目的.6.样板管理①QA 管理的样板类别在批量生产过程中抽取的代表产品质量水准并符合要求的产品.制造产品时提供的具有代表产品标准组装状态的示范作用产品. 制造产品时提供的具有代表产品标准性能状态的示范作用产品.制造产品时提供的具有代表产品某特定部位质量水准并符合要求的供操作参考的产品.检验产品时提供的具有代表产品最低接收界限的示范作用产品.① 企业提供给顾客为了取得其认可的产品② 顾客提供给企业的标准产品.提供给QC 人员用于识别检验工序工程状态的合格的产品.提供给QC 人员用于识别检验工序工程状态的不合格的产品.② 样板标签贴在样品上用以识别并表示样板性质的标志.a. 红底黑字圆标(SAMPLE): 用以醒目识别样板b. 样板标签格式7.让步也要有尺度①让步的底线 让步的结果绝对不能导致顾客不满意.②有偿让步 此处退让,彼处加强.即通过偿还措施保持总体不变③特许让步 对需要让步的事项取得顾客同意后再实施④实施让步要求 a.限定让步的数量; b.限定让步的时期c.确保让步产品的追溯性;d.采取适当的标识方法;⑤让步不是许可化 虽然接受了让步,但仍然要采取预防措施,以防下次.⑥让步的情况不宜经常发生.8.执行更严格的品质标准品质标准是指生产过程中用以控制产品和过程特性的各种规范性要求.如: ● 临控计划 ●产品规格 ●国家标准● 指导书 ●样板 ●国际标准● 工艺规范 ●过程参数 ●行业相关标准● 作业程序 ●流程图 ●公司标准所谓执行更严格的品质标准是指当顾客或其他相关方没有明确要求时,假如品质标准有三个级别,那么品管部将自动选择其中最严格的一个级别使用.同理,顾客默认时也选择最严格的品质标准使用,而绝对不是反过来选择最轻松的用.9.品质比成本更重要●损失一分钱的成本,其真正的损失也就是一分钱.而损失一分钱的品质,其真正的损失可能是它的100倍.●导致品质不良的一个重大原因是马虎,而比马虎还要更重大的原因是偷工减料.10.IQC:IN COME QUALITY CONTROL 进料品质管理IPQC:IN PROCESS QUALITY CONTROL 制程品质管理FQC:FIAL QUALITY CONTROL 最终品质管理QA:QUALITY AUDIT 品质稽核OQC:OUT QUALITY CONTROL 出货品质管理QST:QUALITY SYSTEM TEAM 品质体系小组QE:QUALITY ENGALE 品质工程师QC:QUALITY CHECK 品质检验厂务部2007.12.29。
工厂出货检验流程图及工作细则
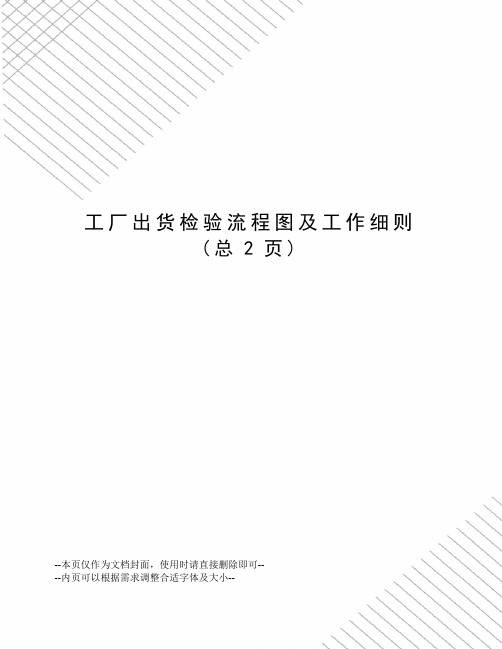
4、OQC根据《发货单》,按《组件出货检查表》进行检验检查。
5、OQC检验完毕,填写《组件出货检查表》进行检验检查。
6、OQC检验合格,在发货单上签名(须签全名,不允许只签姓名或者一个字、或字迹潦草—详见范本一);如发现不符合项,处理流程参见《不合格品控制程序》。
工厂出货检验流程图及工作细则(总2页)
流程
责任部门
工作内容
相关文件/表单
商务部
商务部、仓库
仓库
OQC检验员
OQC检验员
OQC检验员
仓库
保安
1、商务部根据出货计划安排,在OA上公布具体出货明细。
2、商务制定《发货单》,并督促销售和财务审核,由仓库打印、仓管员签名确认。仓管员确认单据明细无误后,由仓库账务员做销售出库单,将帐调出仓库,打印《销售出库单》并由仓管员和OQC共同签名确认。
7、仓管员在得到OQC检验员确认货物合格之后,尽快装箱发货,不得以各种理由推迟发货。
8、该批产品在厂门检查,保安人员须确认《发货单》上具备可识别的OQC人员的签名,否则不得放行出货。
《发货单》
《销售出库单》
《组件出货检查表》、《唛头打印规范》、《组件成品检验标准》
《不合格品控制程序》、《HOLD单》、《重工作业程序》、《重工单
工厂出货检验流程图及工作细则
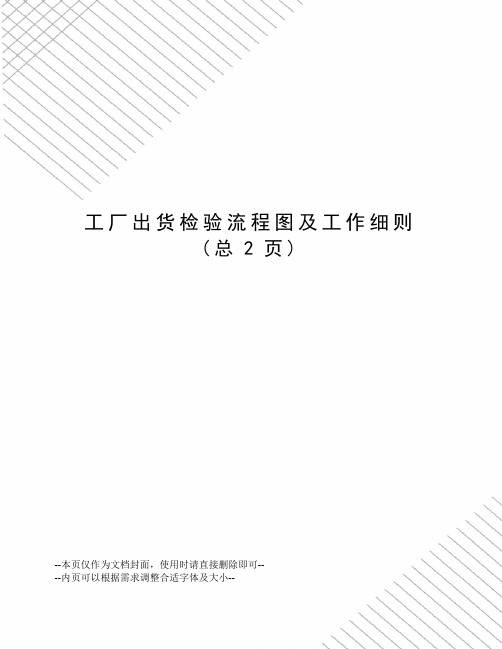
《发货单》
《销售库单》
《组件出货检查表》、《唛头打印规范》、《组件成品检验标准》
《不合格品控制程序》、《HOLD单》、《重工作业程序》、《重工单》
各种表单需经相关部门领导审批后方可生效。
OQC检验员
OQC检验员
仓库
保安
1、商务部根据出货计划安排,在OA上公布具体出货明细。
2、商务制定《发货单》,并督促销售和财务审核,由仓库打印、仓管员签名确认。仓管员确认单据明细无误后,由仓库账务员做销售出库单,将帐调出仓库,打印《销售出库单》并由仓管员和OQC共同签名确认。
3、仓库依据发货通知单上的产品型号、规格、数量进行备货。
4、OQC根据《发货单》,按《组件出货检查表》进行检验检查。
5、OQC检验完毕,填写《组件出货检查表》进行检验检查。
6、OQC检验合格,在发货单上签名(须签全名,不允许只签姓名或者一个字、或字迹潦草—详见范本一);如发现不符合项,处理流程参见《不合格品控制程序》。
7、仓管员在得到OQC检验员确认货物合格之后,尽快装箱发货,不得以各种理由推迟发货。
发货单销售出库单组件出货检查表唛头打印规范组件成品检验标准不合格品控重工作业程序重工单各种表单需经相关部门领导审批后方可生结束保安确认仓库出货仓库备货oqc检验检验结果出货通知开始填写检验表订单审核
工厂出货检验流程图及工作细则(总2页)
流程
责任部门
工作内容
相关文件/表单
商务部
商务部、仓库
仓库
OQC检验员
qa检验流程及注意事项

qa检验流程及注意事项
QA检验流程是对产品从生产到出货的各个环节进行质量控制的关键步骤。
主要包括产品完成后的成品出货检验:OQC接到《出货检验通知单》后,依据规定执行抽检,记录于《出货检验单》,合格则盖PASS章或客户指定标识后放行,不合格则隔离并按流程处理。
此外,还包括日常巡检以符合GMP要求,预防污染与交叉污染,以及实验室检验测试等。
注意事项:
1. QA人员应提前准备,严格检查环境、设备、物料标识等是否合规。
2. 保持专业形象,遵守着装规定,避免在检验期间使用手机。
3. 对待检验过程严谨认真,确保所有出货产品均通过规定的质量标准。
4. 对不合格品及时隔离处置,并跟踪纠正措施的有效性。
5. 在实验室检测中遵循操作规范,确保数据准确可靠。
QA检验流程职责和工作要求
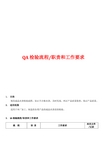
1.目的
规范成品出货检验流程,防止不合格出货,及时发现、纠正产品质量隐患,保证产品质量。
2.适用范围
适用于本厂加工、制造的各类产品的成品出货前的检验。
3.QA检验流程/职责和工作要求
流程
职责
工作要求
相关文件/记录首件源自验生产生产检验员
OQC组长
QE
PIE/OQC组长/PQC组长
OQC
PIE
生产部
OQC组长
检验员
OQC组长/PQC组长/PIE
OQC主管
检验员
PIE
每一订单生产的第一台机送OQC检验
按订单、样机、检验标准或规范、说明书、ECN、料表、设计文件作首件检验
填写《首件检查表》(外观、功能)
QE对首件及《首件检查表》确认,并签署合格与否意见
OQC、PQC和PIE对机确认,
不合格发出《OQC检验报告》,注明首件检查
OQC组长
检验员
作业员
OQC组长/领班
QE/PIE
OQC
PIE
批量抽检合格,组长在《OQC检验报告》签字确认
合格话机在生产部产成品送检单上盖蓝色QA PASS章,外箱贴绿色QA合格证贴纸,客户产品盖蓝色QA PASS章,
记录每一订单箱号范围、流水号范围、物流码范围
生产线封箱,OQC监督,外箱底部贴白色封箱签
工程PIE分析原因,发出《坏机分析报告》
已投产机返工,生产再重送首件
首件检验合格,OQC通知生产线组长在《首件确认表》上签字确认后,生产部批量生产
首件检验合格,OQC批量抽检
根据产品检验标准、规范,《产品检验抽样规定》,设计文件,批量抽检
记录抽检的每台机流水号
首批检验合格机抽一箱做整箱落地试验