FMEA培训资料最新版42982PPT课件
2024年度FMEA培训教材ppt完整版

等级并制定应对措施,可提高系统或产品的可靠性和安全性。
2024/3/23
02 03
改进策略的制定
根据FMEA分析结果,针对高风险和中风险故障模式制定改进策略,包 括设计优化、工艺改进、材料替换等,以降低故障发生的可能性和影响 程度。
改进效果的跟踪
实施改进策略后,需对改进效果进行跟踪和评估,确保改进措施的有效 性。同时,将改进经验反馈到FMEA分析中,不断完善和优化分析过程 。
掌握了FMEA实施的基本技能
通过课程中的案例分析和实践操作,学员们表示已经掌握 了FMEA实施的基本技能,能够独立完成简单的FMEA分析 工作。
增强了团队协作和沟通能力
在课程中,学员们分组进行讨论和案例分析,不仅增强了 团队协作能力,还提高了沟通能力。
34
未来发展趋势预测
2024/3/23
01 02 03
23
05 FMEA在产品设 计阶段应用实践
2024/3/23
24
产品设计阶段FMEA实施流程
流程概述
01 明确FMEA在产品设计阶段的
目标和重要性,以及实施的基 本步骤。
团队组建与培训
02 组建专业的FMEA团队,并进
行必要的培训和技能提升。
功能分析与结构分解
03 对产品的功能进行详细分析,
并进行结构分解,以明确潜在 故障模式。
12
评估方法选择及实施流程
• 方法选择:根据失效模式的性质和影响程度选择合适的评 估方法,如风险矩阵、风险指数等。
2024/3/23
13
评估方法选择及实施流程
实施流程
1. 明确评估目标和范围
2. 收集相关数据和信息
2024/3/23
14
FMEA培训教材-PPT精选全文

客户要求 方便调整
舒适 移动顺畅
ቤተ መጻሕፍቲ ባይዱ
产品规格 调节高度 坐垫厚度 旋转角度 椅轮松紧
9
1
3
9
3
1
9
9
重要性 60% 30% 10%
分值
640
330
180
90
FMEA 得原理
客户要求 方便调整
舒适 移动顺畅
分值
产品规格 调节高度 坐垫厚度 旋转角度 椅轮松紧
9
1
3
9
3
1
9
9
640
330
180
90
参数
上升50CM
FMEA 得原理
一、FMEA基本知识
练习:
公司产品:车门 客户要求:
•方便开关 •噪音小 •安全
FMEA 得原理
FMEA 得原理
FMEA 得原理
客户质量要求 Input
客户质量目标
FMEA Output
CTQ 清单 CP 控制计划
FMEA
FMEA 得原理
Output
CTQ 清单
CTQ产出原则:
压 合 状 态
方法
特
样本Sample
殊 特 性 分
产品特 性/过程 参数规 格/公差
评价/ 测量技
术
容 量
频率
类
《
首检
MODULE 检验标
准》
5-20倍 显微镜
6P CS
:6PCS/ 抽检 : 每10PCS
抽1PCS
反应计
控制方法/ 统计技术
责任人
划
《CD-HFM0419701 LCM 镜检 不良明细
措施?
fmea培训资料最新版(141页)

FMEA培训资料最新版(141页)FMEA(失效模式和影响分析)是一种系统的、结构化的方法,用于识别和评估产品或过程中的潜在失效模式,以及这些失效模式对最终用户的影响。
FMEA培训资料旨在帮助参与者了解FMEA的基本概念、方法和工具,以便在实际工作中应用FMEA来提高产品或过程的质量和可靠性。
一、FMEA概述FMEA是一种预防性的质量工具,它通过系统性地识别和分析潜在的失效模式,以及这些失效模式对产品或过程的影响,来降低失效风险。
FMEA通常分为两个阶段:设计FMEA(DFMEA)和过程FMEA (PFMEA)。
DFMEA关注于产品设计和开发阶段,而PFMEA关注于制造和装配过程。
二、FMEA的基本步骤1. 定义项目范围:确定要分析的系统和子系统的范围。
2. 建立团队:组建一个跨职能的团队,包括设计、工程、制造和质量等部门的代表。
3. 识别失效模式:团队成员共同识别潜在的失效模式,并记录下来。
4. 分析失效影响:评估每个失效模式对最终用户的影响,包括安全性、成本、性能和可维护性等方面。
5. 评估失效严重性:根据失效影响的严重程度,对每个失效模式进行评分。
6. 评估失效发生概率:根据失效模式的已知历史数据或专家经验,评估每个失效模式的发生概率。
7. 评估检测难度:评估检测每个失效模式的难度,包括检测方法的有效性和成本。
8. 计算风险优先级数(RPN):将严重性、发生概率和检测难度相乘,得到每个失效模式的风险优先级数。
9. 采取预防措施:根据RPN,制定和实施预防措施,以降低失效风险。
10. 跟踪和更新:定期跟踪和更新FMEA,以确保其持续有效。
三、FMEA工具和模板FMEA工具和模板可以帮助团队更有效地进行FMEA分析。
常用的FMEA工具包括:1. FMEA表格:用于记录失效模式、影响、严重性、发生概率、检测难度和RPN等信息。
2. FMEA软件:提供自动化的FMEA分析功能,包括数据输入、计算和分析报告。
FMEA培训资料ppt
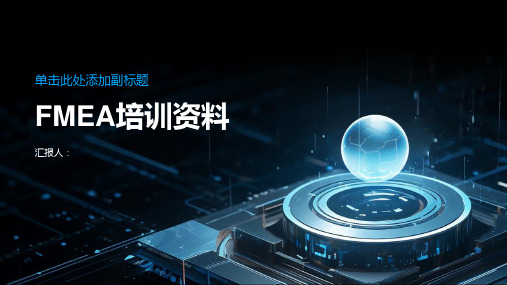
风险评估:对故障进行风 险评估,确定其危害程度 和发生概率
改进措施:提出针对该故 障的改进措施,包括设计、 工艺等方面的改进
实施效果:对改进措施的 实施效果进行评估和验证, 以确保改进的有效性。
如何整理和撰写FMEA报告
确定报告的目的 和范围
收集相关数据和 信息
整理和分析数据
撰写报告并完善 内容
FMEA报告的实例分享及解析
评估流程:按照规定的流程进行 风险评估,包括风险识别、分析、 评价等环节
添加标题
添加标题
添加标题
添加标题
评估标准:制定评估标准,包括 风险等级、严重程度等
数据采集:采集相关的数据和信 息,包括历史数据、行业数据等
FMEA中风险评估的步骤和要点
添加标题
确定评估对象:明确评估的对象,包括产品、过程、 系统等,并确定评估的范围和重点。
问题:FMEA分析缺乏系统性,未形成完整的分析流程 解决方法:建立完善的FMEA分 析流程,确保分析的全面性和系统性 解决方法:建立完善的FMEA分析流程,确保分析的全面性和系统性
问题:FMEA分析结果未得到有效应用,未发挥应有的作用 解决方法:加强 FMEA分析结果的应用,将分析结果应用于设计和生产中,提高产品质量和安全性。 解决方法:加强FMEA分析结果的应用,将分析结果应用于设计和生产中,提高产品质量和 安全性。
等。
案例分析:通过 具体的案例分析,
展示如何运用 FMEA解决实际 问题,并分享从 中获得的经验和
教训。
添加标题
结论:总结 FMEA实践经验 的重要性,并强 调其在提高产品 质量和降低风险 方面的贡献。
FMEA在实践中的应用案例
案例1:汽车行业中的FMEA应用 案例2:医疗器械中的FMEA应用 案例3:航空航天中的FMEA应用 案例4:化工行业中的FMEA应用
FMEA培训课件(五大工具)
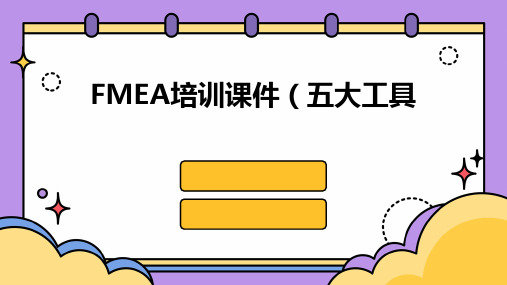
FMEDA不仅关注故障模式的影响,还特别强调对检测性的评估,以便更全面地了解潜在问题的影响以及在出现故障时能否及时发现并进行修复。
在FMEDA中,检测性的评估通常采用量化的方式进行,以便更准确地确定故障模式的可检测性。通过提高检测性,可以降低因未及时发现故障而导致的事故风险。
详细描述
在FMESi中,严重度评估通常采用量化的方式进行,以便更准确地确定故障模式对系统性能的影响程度。
总结词:故障模式、影响与风险优先数分析(FMERP)是一种综合性的质量工具,旨在识别、评估和解决潜在的故障模式及其对系统性能的影响。
总结词
故障模式、影响与检测性分析(FMEDA)是一种质量工具,用于评估潜在的故障模式及其对系统性能的影响以及检测的可能性。
详细描述
DFSS(Design for Six Sigma)是一种设计方法论,旨在提高产品的设计质量和可靠性。通过结合FMEA,可以对产品设计中的潜在失效模式进行分析和预防,从而提高产品的设计质量和可靠性。这种结合有助于在设计阶段就考虑产品的性能、可靠性和安全性,从而减少后期的改进成本和时间。
THANKS
总结词
电子产品行业对质量和可靠性要求极高,FMEA在此领域的应用同样广泛且重要。
在电子产品案例中,FMEA被用于分析电子产品的设计和生产过程。通过FMEA分析,可以发现潜在的故障模式,并采取相应的预防措施,提高产品的可靠性和稳定性。此外,FMEA还可以帮助企业优化产品设计,降低生产成本,提高市场竞争力。
FMEA培训课件(五大工具
FMEA基础介绍FMEA实施流程FMEA分析方法FMEA应用案例FMEA与其他工具的结合应用
FMEA培训教材(ppt)(2024)

后果分析
针对每种失效模式,分析 其可能对产品功能、安全 性、可靠性等方面造成的 影响和后果。
风险评估
对每种失效模式及其后果 进行风险评估,确定其严 重度、发生度和检测度等 级。
14
评估风险等级并采取预防措施
风险等级评估
综合考虑严重度、发生度 和检测度等级,对每种失 效模式进行风险等级评估 。
2024/1/30
4
FMEA发展历程
起源
FMEA起源于20世纪40年代的军事领域,当 时主要用于评估武器系统的可靠性。
发展
随着工业技术的进步,FMEA逐渐应用于民 用领域,如汽车、航空航天、电子、医疗等 。
标准化
为了规范FMEA的实施,国际标准化组织( ISO)和美国汽车工程师学会(SAE)等制定 了相应的标准和指南。
。
2024/1/30
可靠性增长
在产品设计阶段,通过不断测试和 验证,提高产品的可靠性和稳定性 ,降低失效模式的发生概率。
持续改进
在产品设计和生产过程中,持续关 注失效模式的变化和趋势,及时采 取改进措施,确保产品质量的持续 改进和提升。
16
04
FMEA在生产过程控制中应用
2024/1/30
17
识别生产过程中潜在失效模式及后果
通过引入先进设备、优化工艺流程、提高员工技能等手段 ,提升生产过程的能力和效率,降低潜在失效模式的发生 概率。
风险管理机制完善
建立完善的风险管理机制,包括风险识别、评估、预防、 监控和应对等环节,形成闭环管理,确保生产过程风险的 有效控制和持续改进。
20
05
FMEA在设备维护保养中应用
2024/1/30
21
《FMEA培训教材》课件

FMEA的分类和流程
1
设计FMEA
在产品设计阶段使用FMEA来预防潜在问题。
2
过程FMEA
在生产或服务过程中使用FMEA来改进质量和效率。
3
系统FMEA
在整个系统中使用FMEA来保证整体可靠性。
FMEA的实施步骤
确定团队
组建一个跨部门的团队,包括设计、工程、质量等。
2 缺点
需要投入大量的时间和资源来收集和分析数 据。
FMEA的基本原理
分析失效模式
识别可能的故障和失效模式。
评估影响程度
衡量失效对系统或过程的影响 程度。
制定改进措施
采取措施预防或减轻潜在风险。
FMEA的工具和方法
风险评估矩阵
鱼骨图
用于确定失效的概率和影响程度。 帮助识别失效的根本原因。
失效模描述
收集数据
收集与产品或过程相关的数据和信息。
识别失效
识别可能的失效模式和其潜在影响。
FMEA团队的组成和角色
组长
负责组织和协调FMEA团队的工作。
专家
提供专业知识和经验,帮助分析和评估风险。
记录员
负责记录 FMEA 会议和结果。
《FMEA培训教材》PPT课 件
这份《FMEA培训教材》PPT课件为您逐步介绍FMEA的应用和原理,从基本概 念到实际案例,让您全面了解这一重要的风险管理工具。
什么是FMEA
FMEA(失效模式与影响分析)是一项系统性的风险管理工具,用于识别和 评估潜在的失效模式及其对系统或过程的影响。
FMEA的应用领域
汽车制造
在汽车设计和生产过程中, FMEA被广泛应用于预防和控 制潜在故障或缺陷。
FMEA培训教材PPT完整版(2024)

产品设计阶段FMEA案例分析
案例一
某型号汽车发动机设计FMEA分 析。针对发动机系统可能出现的 故障模式进行分析,如气缸磨损 、活塞环断裂等,制定相应的改
进措施。
案例二
某型号手机电池设计FMEA分析 。针对电池可能出现的过热、短 路等故障模式进行分析,优化电 池结构和电路设计,提高电池安
全性。
26
过程控制阶段FMEA流程
定义过程范围和功能
01
识别潜在的故障模式
02
评估故障影响的严重度、发生
度和检测度
03
计算风险优先数(RPN)并排 序
04
制定并实施控制措施
2024/1/29
05
跟踪验证控制措施的有效性并
更新FMEA
06
27
过程控制阶段FMEA案例分析
案例一
某汽车制造厂涂装车间过程FMEA分 析
为生产过程FMEA提供支持
产品设计阶段FMEA的输出可以为生产过程 FMEA提供重要的输入和支持。
20
产品设计阶段FMEA流程
组建FMEA团队
由多部门、多学科的专业 人员组成,包括设计、制 造、质量、采购等。
2024/1/29
定义系统和子系统
明确产品的结构和功能, 划分系统和子系统。
识别故障模式
针对每个子系统或部件, 识别所有可能的故障模式 。
9
组建FMEA团队并分配任务
02
01
03
2024/1/29
组建多学科团队
包括设计、制造、质量、采购等相关领域专家。
分配角色与责任
明确团队成员的角色和责任,确保任务有效执行。
提供培训与支持
为团队成员提供FMEA培训,确保掌握相关知识和技 能。
- 1、下载文档前请自行甄别文档内容的完整性,平台不提供额外的编辑、内容补充、找答案等附加服务。
- 2、"仅部分预览"的文档,不可在线预览部分如存在完整性等问题,可反馈申请退款(可完整预览的文档不适用该条件!)。
- 3、如文档侵犯您的权益,请联系客服反馈,我们会尽快为您处理(人工客服工作时间:9:00-18:30)。
DO IT RIGHT THE FIRST TIME —— 第一次就做好
Avoid TRIAL AND ERROR —— 避免尝试和失
误 关注产品系统的可靠性安全性
——有关术语
FMEA
第二讲 有关术语与概念
2.1 可靠性与可靠度 2.2 失效与寿命特征参数 2.3 系统与可靠性模型 2.4 可靠性工程 2.5 失效模式
SS
失效的三种形式
失效的三种形式: 1) 功能 失效 2) 参数 失效 3) 破坏 失效
分析,发展成危害度分析,即CA,与FMEA合 称FMECA; 以后在世界范围内得到广泛应用,并形成相 应标准。
SS
—— 概述
FMEA
1.3 现 状
在航天工程研制中,己被规定为必须采用的 方法;
在汽车制造业中,已成为汽车OEM厂商及其 供应商质量体系要求之一; 如: QS9000与VDA6.1 → TS16949
第三章:着重于DFMEA,包括,建立分析的范围、框图使 用、 DFMEA的各种类型,小组的组建、分析的基本程序、 措施计划、后续行动、RPN的可选方法、与PFMEA以及确认 计划的联系。
第四章:着重于PFMEA,包括,建立分析的范围、流程图 的使用、 小组的组建、分析的基本程序、措施计划、与 DFMEA以及控制计划的开发的联系。
产品特点: 大规模复杂系统 高科技产品
SS
ISO/TS16949技术规范
体系要求的五大核心工具之一:
PPAP : 生产件批准程序 APQP : 产品质量先期策划 SPC : 统计过程控制 FMEA: 潜在失效模式及后果影响分析 MSA : 测量系统分析
FMEA 参考手册
由北美三大汽车公司(克莱斯勒、福特和通用)FMEA工 作组编写;是一本设计FMEA和过程FMEA的开发指南;目 的不在于定义要求,而是在于阐明FMEA技术开发中的问 题;
1993年2月发布第一版;1995年2月发布第二版; 2001年7月发布第三版;2008年6月发布第四版;
2001年11月发布《设备和工装潜在失效模式及后果分析 (MFMEA )》第一版;
手册提供了应用 FMEA 技术的总体指南,但并没有给出 如何完成每一 FMEA 项目的具体说明,也不是综合性的 参考资料或培训资料。
FMEA参考手册第四版的变化
包含与系统、子系统、接口和零部件等级别的设计相关 的方法,以及与制造和装配的过程相关的方法;
增加索引、示例,重要段落予以标示,更易理解使用; 定义并强化设计和过程FMEA的联系的理解,同时定义了
和其他工具的关联; 改进了严重度、发生频度、探测度的评级表,以便对实
累积故障概率的估计值:
F^(t)
=
r(t) ——No——
其中: No、 R(t) 同可靠度计算
可靠性
SS
2.2 失效与故障
FMEA
2.2.1 定义:
产品或产品的一部份不能或将不能完成预定 功能的事件或状态。
故障与失效在英文中统称 failure; 故障 → 可修复产品 失效 → 不可修复的产品。
标题
FMEA
潜在失效模式及其后果分析 (FMECA)
SS
引言
FMEA
引言 从神舟载人飞船谈起
SS
引言
FMEA
产品可靠性 —— 现代产品质量的关键
产品二种质量指标
性能指标 —— 产品完成规定功能所需的性 能
可靠性指标 —— 产品性能随时间保持的能
力
产品竞争谁的不焦重点视可靠性必将受到惩罚 !
对组织和管理者的影响
对组织和管理者的影响
1.4 FMEA 技术的应用:
设计---- 一开始就使缺陷降到最低 尽可能完善, 管理效益↑↑
制造---- 不是根据发生的问题采取措施, 而是事先对可能发生的问题进
行 先期控制
事物---- 经验/认识的程度↑↑ 避免在过程阶段化费大量人力
1.4 FMEA 技术的应用:
SS
2.1 可靠性与可靠度
FMEA
2.1.1 可靠性
产品在规定的条件下和规定的时间内完成规 定功能的能力。
规定条件:使用条件、环境条件、贮存条件 规定时间:小时、频次、里程 规定功能:故障判据
产品质量特性随时间变化的内在规律
SS
2.1.1 可靠性
FMEA
可靠性的形成
} 设计过程形成:分析、评估、优化 固有 可靠性 生产过程形成:控制计划
际分析和使用更有意义; 介绍了行业内目前使用的可选方法,不再强调“标准表
格” 建议不要把RPN作为风险评估的首要方法。
FMEA参考手册第四版的变化
第一章:提供了FMEA通用指南,提出管理者支持的需求和 定义一个开发并维持FMEA的过程的需求,以及持续改进需 求;
第二章:描述了在DFMEA和PFMEA之间比较通用的应用方法, 其中包括:策划、策略、措施计划、管理者支持的需求和 FMEA中的职责;
障的
r(t): 在0→t时刻的工作时间内,发生故
100台计算机开始工作
产品数
仍有95台在工作
t=0
有5台发生故障
t t=1000hSSຫໍສະໝຸດ —— 有关术语可靠性
2.1.3 累积故障概率
产品在规定的条件下和规定的时间内, 丧失规定功能的概率
亦称为不可靠度
F(t) = P ( T ≤ t )
SS
—— 有关术语
SS
第一讲 概 述
FMEA
1.1 FMECA包含两部分
失效模式及后果分析(FMEA); 危害度分析(CA); FMEA与CA合并为FMECA。
可靠性工程中最基本、最有效和最重要的 分析技术之一
SS
——概述
FMEA
1.2 发展过程
FMEA60年代中期由美国军方研发和建立; 首先在航空航天及核技术中应用; 后对可能造成特别严重后果的失效进行单独
使用过程形成:使用规范
使用可靠性
SS
—— 有关术语
FMEA
2.1.2 可靠度
产品在规定的条件下和规定的时间内完
成规定功能的概率。
可靠度是时间的递减函数。
R(t)= P( T > t )
SS
—— 有关术语
可靠性
可靠度的估计值:
^ R (t) N=o-—r(—t)——— No
其中:No : t=0时刻,在规定条件下工作的产品数