POWERPRO2
TRAKTOR PRO 2安装指南说明书

“TRAKTOR PRO 2” Setup GuideBefore start (Important)Setup Wizard offers a simple setup procedure for TRAKTOR PRO 2 (Ver.2.1.2. or later).Please follow the instructions below before starting the setup procedures of TRAKTOR PRO 2.・Update the DDJ-ERGO’s firmware to the latest version. ・For Windows users:Turn on the power of DDJ-ERGO first. Then, run the TRAKTOR software.If the TRAKTOR PRO 2 is launched before the DDJ-ERGO is powered on, the DDJ-ASIO driver may not be recognized.If the DDJ-ASIO driver is not recognized, turn off both the TRAKTOR PRO 2 and the DDJ-ERGO and repeat the above procedures.Setup procedures* The screenshots used in this guide may be different depending on the version of TRAKTOR PRO 2.1. Connect the DDJ-ERGO to your computer by a USB cable and turn on the power of the controller using ON/OFF slide switch.2. Launch TRACTOR PRO 2 after DDJ-ERGO starts. Note: Ensure that DDJ Note: Ensure that DDJ--ERGO starts before launching T ERGO starts before launching TRA RA RAK K TOR TOR PRO 2. PRO 2.3. From the upper left "Help" menu, open "Start Setup Wizard" and click "Next."4. When the message "Are you using an external controller?" is displayed, select "Yes" and click "Next."5. When the messages "Choose your manufacturer" and "Choose you model" are displayed, select "Pioneer" and "DDJ ERGO" respectively. Then, click "Next."6. The message "Are you using an external mixer?" is displayed. If you use one, select "Yes" and if you do not, select "No" and click "Next."7. When "Select your setup" is displayed, select the decks you will use and click "Next."8. When "Finish" is displayed in the lower right corner of the wizard, click "Finish" to complete the Setup Wizard.9. Select [File] > [Controller Manger...]. Under [Device Setup], select the[PIONEER_DDJ-ERGO] from [Device] menu and select the device corresponding to the DDJ-ERGO at [In-Port] and [Out-Port].10. The preferences settings may be overwritten to the default settings after completing the setup wizard depending on the versions of TRAKTOR PRO 2.When using DDJ-ERGO, the following audio settings are minimal requirements. Please ensure that you go through the setup procedures.(1) Audio Setup・Audio Device: PIONEER DDJ ASIO (For Windows users) DDJ-ERGO (For Mac users)(2) Output Routing・Mixing Mode :Internal ・Output Monitor :L 3:DDJ-ERGO PHONE L R 4:DDJ-ERGO PHONE R ・Output Master :L 1:DDJ-ERGO MASTER L R 2:DDJ-ERGO MASTER R(3) Input Routing* For those who do not use external input (AUX/MIC), the following setup is not needed. ・Input AuxL(Mono) 1:DDJ-ERGO AUX/MIC L R 2:DDJ-ERGO AUX/MIC R(4) Mix Recorder・Source :Internal11. Close the TRAKTOR PRO 2, power off the DDJ-ERGO and turn it on again, and reboot the TRAKTOR PRO 2.Now, you have completed all the settings.About trademarks and registered trademarks・TRAKTOR is the registered trademark of Native Instruments GmbH.・Microsoft ®, Windows Vista ®, Windows ®, and Internet Explorer ® are either registered trademarks or trademarks of Microsoft Corporation in the United States of America and other countries. ・Apple, Macintosh, Mac OS, Safari, iTunes, and Finder are trademarks of Apple Inc., registered in the U.S. and other countries.©2012 PIONEER CORPORATION all rights reserved. PIONEER CORPORATION1-1, Shin-ogura, Saiwai-ku, Kawasaki-shi, Kanagawa 212-0031, Japan<DRH1128-B-EN>。
ABB 三相三线网络电表 M1M 30 I O Pro 安装手册说明书

2T A B 667009P 0002 07-06-2023Power MeterINSTALLATION MANUALQR Code for online User Manual.扫二维码获取在线用户手册。
Contact us ABB LV Installation Materials Co., Ltd. BeijingElectrification Business Area No. 17 Kangding Street , BeijingEconomic-Technological Development Area 100176https:///low-voltageWarning! Installation by person with electrotechnical expertise only. 警告! 只能由具有电气技术专业知识的人安装。
M1M 30 I/O Pro1.Packaging Content• Power Meter M1M 30 I/O Pro • Installation Manual 4.Operating instructions3-Phase 3-wire network with 3CTs (3 3T)3-phase 3-wire network with 2CTs (3 2T) Button Functions1Menu Access the menu and navigation 2Up Navigate in the measurementsor change a configuration value 3Down 4EnterConfirm an action and navigation3 2T Three-phase, three-wire and two-transformer 3 1TThree-phase, three-wire and one-transformer1N1T Single-phase, two-wire and one-transformerRTC 1-Phase 2-wire network with 1CT (1N1T)Digital inputs (M1M 30 I/O Pro only)Relay outputs (M1M 30 I/O Pro only) 4.1.Data entry procedure1. Press “Up” to increase the numericalcharacters from 0 to 9, until the requi-red character is obtained.Press “Down” to move the cursor in order to add a second digit to the 5.4.Current Transformer ratio1. Enter the current transformer primary and select the magnitude, and confirm it by pressing “Enter”.2. Select the current transformer secon-dary,and confirm it by pressing “Enter”.5.5.Voltage Transformer ratio1. Enter the voltage transformer primaryand select the magnitude, and confirm it by pressing “Enter”.2. Enter the voltage transformer secon-dary, and confirm it by pressing “Enter”.1.包装清单• 电力智能监控仪表 M1M 30 I/O Pro • 安装手册电力智能监控仪表安装说明书联系我们三相三线 3个电流互感器 (3 3T)三相三线2个电流互感器(3 2T)单相两线 1个电流互感器 (1N1T)继电器输出 (仅M1M 30 I/O Pro)数字输入(仅M1M 30 I/O Pro)4.操作说明按键描述1菜单访问菜单和导航2向上测量中导航或更改配置值3向下4确认确认操作和导航4.1.数据输入步骤1. 按 “向上” 键增加数字字符,从0到9,直到获得所需字符。
罗技 PTZ PRO 2 摄像头设置指南说明书

PTZ PRO 2 Setup Guide | 设置指南3 EN GLISH8简体中文2Camera1. 10X lossless zoom2. Camera LED3. Kensington®Security Slot Remote4. Mirror5. Zoom in6. Pan and tilt7. Zoom out8. Camera presets1, 2, and 39. Video mute10. Far end control11. Home12. Remotebattery doorAccessories13. Camera mount14. Cable lock15. Cables1314231English 31. Set up camera by placing on table or by using camera mount on table or wall.2. Attach cable lock before plugging the cable into the camera port.3. Connect to external power.4. Connect the USB cableto your computer.5. The camera LED will flash when the camera is connecting. Once complete, the camera head will rotate.6. If the camera cannot connect,try again. If issues persist, consult /support/ptz2 or call technical support.7. Start your video call fromyour application. The camera LEDwill illuminate when streaming.4 EnglishVISIT PRODUCT CENTRALDiscover your product’s full potential. Get valuable information and usage tips by browsing easy-to-use FAQs. Find answers to product questions and get help setting up your product. See if there’s software availablefor download that can enhance your product experience. To enjoy all the benefitsof your Logitech product,visit /support/ptz2 and take advantage of Logitech’s wide range of useful support services.– Troubleshooting– Diagnostics– Firmware upgrades– Support community– Software downloads– In-box documentation– Warranty information– Spare parts (if available)English 5USE YOUR PRODUCTVideo– Starting the video: Video will start once a video call/capture session is opened and the camera is selected. The camera LED will illuminate when the video is streaming.– Pan and tilt the camera usingthe remote control. Press once for incremental movement or pressand hold for continuous pan or tilt. Caution: Do not manually rotate webcam head. Doing so may damage unit.– Zoom the camera up to 10X by pressing the zoom button.– Home: Press the Home buttonto return to the default, out-of-box home position.– Camera presets: You can set upto 3 preset positions. First, positionthe camera using the pan and tilt controls, and then press and hold one of the preset buttons for 3 secondsto save that position. You may return to your defined position at any timeby pressing the preset button once.Use Preset 1 as your own defined “home” position. When the camerais reconnected to the PC, it will return to the position set in Preset 1. If no position is set for Preset 1, the camera will return to the default home position.All three presets are by default set to the out-of-box home.– Far end control: This function allows you to control the pan, tilt, and zoom of any remote Logitech ConferenceCam or select Logitech Webcams.Some applications support this feature natively, while others can be enabled by using an application downloaded from /support/ptz2. Please visit the download page listed for more information.– Camera settings application:You can use this program to control the pan, tilt, zoom, focus,and image quality (like brightnessand contrast) of the camera from your computer. This applicationcan be downloaded from/support/ptz2.6 EnglishMounting your camera Changing the remote control battery/for troubleshooting tips,English 7摄像头1. 10X 无损变焦2. 摄像头指示灯3. Kensington®防盗锁插孔遥控4. 镜像5. 放大6. 水平与垂直遥摄7. 缩小8. 摄像头预置 1、2和 39. 视频静音10. 远端控制11. Home12. 遥控器电池盖配件13. 摄像机底座14. 线缆锁15. 线缆13142318 简体中文1. 将摄像头置于桌子上,或通过摄像头底座将摄像头支在桌子或墙上。
3D打印PRO2用户手册说明书

V12 Dec 153D PrintPRO 2USER MANUALContents01 02 Overview of your Extraction system (front) Overview of your Extraction system (back) 1 01 Unpacking and unit placement 3 01 02 Connecting to power supply Optional Added Features 4 01 Turning extractor On 5 01 02Important safety notes Safety labels2 01 02 Cleaning the unit Filter replacement6 013D Print Pro 2 Specifications801 Consumable Spares & Filter Disposal 7OverviewLidClipsAir Inlet011Company BrandingFilter ConditionLightFeetOverviewFuse CompartmentAir Outlet/Motor Cooling021Main IsolationSwitchMains InletFuse RatingSafety InstructionsImportant safety notesConcerning symbols used on the extraction unit and referred to within this manual.DangerRefers to an immediately impending danger. If the danger is not avoided, it could result in death or severe (crippling) injury. Please consult the manual when this symbol is displayed.WarningRefers to a possibly dangerous situation. If not avoided it could result in death or severe injury. Please consult the manual when this symbol is displayed.CautionRefers to a possibly harmful situation. If not avoided,damage could be caused to the product or something in its environment.Important (Refer to manual)Refers to handling tip and other particularly usefulinformation. This does not signify a dangerous or harmful situation. Refer to manual when this symbol is displayed.Electrical SafetyThe 3D Print Pro 2 has been designed to meet the safety requirements of the Low Voltage Directive 2006/95/EC (previously numbered 73/23/EEC)WarningWhen working with the pump/motor housing open, Live 230/115 volt mains components are accessible. Ensure that the rules and regulations for work on live components are always observed.ImportantTo reduce the risk of fire, electric shock or injury:1. Always isolate the system from the mains powersupply before removing the pump/motor access panel.2. Use only as described in this manual.3. Connect the system to a properly grounded outlet.Dangers to eyes, breathing and skinOnce used, the filter within the 3D Print Pro system may contain a mixture of particulates, some of which may be sub-micron size. When the used filters are moved it may agitate some of this particulate, which could get into the breathing zone and eyes of the operative. Additionally, depending on the materials being used, the particulate may be an irritant to the skin.This unit should not be used on processes with sparks of flammable materials or with explosive dusts and gases, without implementation of additional precautions.Caution: When changing used filters always wear a mask, safety shoes, goggles and gloves.Carbon selectionPlease note that the media within the filter fitted in the 3D Print Pro 2 is capable of adsorbing a wide range of organic compounds. However, it is the responsibility of the user to ensure it is suitable for the particular application it is being used on.BOFA Technical ServiceIf problems arises with your 3D Print Pro unit please contact us: • •Mon-Fri, 9am-5pm.Email:*****************.ukSerial NumberFor future reference, fill in your system details in the space provided. The serial number is on the rating label located on the side/rear of the unit. Serial Number:012Safety InstructionsWarning and Information labelsThe following listing details labels used on your 3D Print Pro extraction unit.Goggles, Gloves & Mask LabelLocation: Front face of filter.Meaning: Goggles, Gloves and Masks should be worn while handling used filters.Do Not Cover LabelLocation: Bottom panel.Meaning: Do not cover any louvers or holes adjacent to the label.Electrical DangerLocation: Bottom PanelMeaning: Removal of panels with this label attached will allow access to potentially live components.Warning LabelLocation: Next to release clips.Meaning: Power should be isolated before the panel with this label attached is opened/ removed.Serial Number LabelLocation: Next to mains inlet.Meaning: This label contains a variety of information about the extraction unit, including.• Company name, Address & Contact number • Extractor model • Unit serial number• Operating voltage range • Maximum current load • Operating frequency • Year of Manufacture• Relevant approval markings/ logosPLEASE NOTE: If the equipment is used in a manner not specified by the manufacturer, the protection provided by the equipment maybe compromised. Fire Risk WarningIn the very rare event that a burning ember or spark isdrawn into the fume extraction unit, it may be possible that the filters will ignite.Whilst any resultant fire would typically be retained within the fume extraction unit, the damage to the extractor could be significant. It is therefore essential to minimise the possibility of this occurring by undertaking an appropriate Risk assessment to determine:-a). Whether additional fire protection equipment should be installed.b). Appropriate maintenance procedures to prevent the risk of build-up of debris which could potentially combust.This unit should not be used on processes where sparks could occur, with explosive dusts and gases, or withparticulates which can be pyrophoric (can spontaneously ignite), without implementation of additional precautions It is essential that nozzles or other extraction/ fume capture devices and hoses/pipework are cleaned regularly to prevent the build-up of potentially ignitable debris022Before InstallationPackaging Removal & Unit PlacementBefore installation, check the extraction unit for damage. All packaging must be removed before the unit is connected to the power supply.Please read all instructions in this manual before using this extractor.1. Move the unit to the location where it is going to beinstalled and remove the outer packaging. This unit should be installed in a well-ventilated area.Ensure that 500 mm space is available around any vented panels on the extractor to ensure adequate airflow.2. Check the filter is located in its correct position before replacing the lid and securing the clipsCautionDo not block or cover the airflow and motor cooling ports on the unit, as this severely restricts airflow and may cause damage to the unit.CautionUnder no circumstances should the exhaust outlet/s be covered as this will restrict the airflow and cause overheating.013InstallationSpecification: 3D Print Pro 2Dimensions: Height 338mm Depth 270mm Width 283mm Weight: 8.2kg Voltage: 115-230V Frequency: 50/60Hz Full load current: 0.2A Power: 6.6W Capacity: 43 m³hConnection to Power SupplyPlease follow the above specification when selecting the power supply outlet for the extraction system, ensure the power supply is suitable before connecting the 3D Print Pro system.Check the Integrity of the electrical power cable, if the supply cord is damaged the extraction unit should not be connected to the mains. The supply cord should only be replaced by a BOFA engineer as an electrical safety test may be required after replacement.The extraction unit MUST be connected to a properly earthed outlet.If your extraction system was ordered with any optional extras please read section 4.02 beforethe power connection is made as additional connections may be required before power is connected to the extractor.Connect the power cable to an isolated electrical supply.The mains socket should be installed near the extractor it should be easily accessible and able to be switched On/ Off. The cable run should be arranged so as not to create a trip hazard.Pairing with the 3D printer SystemThe 3D PrintPRO 3 has been specially designed to be used alongside a wide spectrum of middle range 3D printers available on the market.Fume can be captured in a number of ways including nozzles and funnels.The extraction point needs to be as close as possible to the printing area without interfering with the 3D printing process to ensure effective fume extraction.014InstallationOptional added featuresRemote Stop/Start featureEnables the extraction unit to be remotely turned On / Off via an external signal.Note: Care must be taken to ensure that the system is correctly wired in order for the extraction unit to function correctly.DC Voltage inputThis configuration requires the Black & Red cores of the signal cable (Refer to section 1 for location) to be connected to a known and tested DC power supply, in order to start the extractor.The operating voltage for this signal is 24VDC. Only this voltage should be connected. Voltages connected outside of this range may cause irreversible damage to the relay. Red cable = V+ Black cable = V-When the extractor is provided with the correct DC voltage the motor will start. When the DC voltage is removed the motor will slow down and come to a stop.The extractor will need to be turned on (See section 5 for turning the extractor on) in order for this feature to operate.024OperationTurning extraction unit OnThe 3D Print Pro 2 features a fused IEC inlet for the mains cable as well as a main isolation switch. The unit can be powered on and off by pressing the red rocker switch to the right hand side.Main Isolation SwitchMains InletFuse Compartment01 5MaintenanceMaintenance UKIt is a legal requirement, under regulation 9 of the COSHH regulations that all local exhaust ventilation systems are thoroughly examined and tested at least once every 14 months (typically carried out annually). The approved code of practice recommends that a visual check should be carried out at least once a week.COSHH requires the annual inspection and testing to be carried out by a competent person and specifies that documentation results are recorded in a log.Contact the seller for more information about inspection and certification.Maintenance GeneralUser maintenance is limited to cleaning the unit and filter replacement, only the manufacturers trained maintenance technicians are authorised to carry out component testing and replacement. Unauthorised work or the use of unauthorised replacement filters may result in a potentially dangerous situation and/or damage to the extractor unit and will invalidate the manufacturer’s warranty.Cleaning the unitThe powder coat finish can be cleaned with a damp cloth and non-aggressive detergent, do not use an abrasive cleaning product as this will damage the finish.The cooling inlets and outlets should be cleaned once a year to prevent build-up of dust and overheating of the unit.Filter InformationA log of filter changes should be maintained by the user. The filters require attention when the display shows the configuration shown on the next page or when the extractor no longer removes fume efficiently.It is recommended that a spare set of filters are kept on site to avoid prolonged unit unavailability. Part numbers for replacement filters can be found on the filters fitted in your system.To prevent overheating, units should not be run with a blocked filter condition, or with dust obstruction of Inlets / Outlets.Fire Risk WarningIn the very rare event that a burning ember or spark is drawn into the fume extraction unit, it may be possible that the filters will ignite.Whilst any resultant fire would typically be retained within the fume extraction unit, the damage to the extractor could be significant.It is therefore essential to minimise the possibility of this occurring by undertaking an appropriate Risk assessment to determine:-a). Whether additional fire protection equipment should be installed.b). Appropriate maintenance procedures to prevent the risk of build-up of debris which could potentially combust.This unit should not be used on processes where sparks could occur, with explosive dusts and gases, or with particulates which can be pyrophoric (can spontaneously ignite), without implementation of additional precautionsIt is essential that nozzles or other extraction/ fume capture devices and hoses/pipework are cleaned regularly to prevent the build-up of potentially ignitable debris01 6MaintenanceFilter ReplacementThe 3D Print Pro 2 will alert the user when its filter needs tobe replaced. When the filter becomes full the red ‘FilterCondition light will glow.To remove and replace the pre filter follow the proceduredetailed below.1.Isolate the electrical supply to the extractor2.Undo the clips on the sides of the unit and removethe lid.3.Lift the pre filter pad out of the top of thecombined filter. Replace with a new pad.4.Replace the lid and secure the clips.To remove and replace the combined filter follow theprocedure detailed below.1.Isolate the electrical supply to the extractor2.Undo the clips on the sides of the unit and removethe lid.3.Lift the filter out of the unit and remove the prefilter pad from the top. Once removed it isrecommend that the used filters are bagged andsealed.4.Lower the new filter into position and replace thepre filter pad.5.Replace the lid and fasten the clips.Note: The filter MUST be fitted when the extractor is inuse.026Replacement PartsConsumable SparesThe 3D Print Pro 2 contains a combined filter. These shouldbe replaced when instructed to do so by the 3D Print Proextraction system (see section 6 for replacing the filters)To maintain performance it is important that the filters arereplaced with identical BOFA filters. To re-order please referto the Filter number printed on the filter installed in yourextraction unit.Maintenance ProtocolUsers can record changes in filter change intervals on thetable below.Filter disposalThe combined filter is manufactured from non-toxicmaterials. Filters are not re-usable, cleaning used filters isnot recommended. The method of disposal of the usedfilters depends on the material deposited on them.For your guidance017System SpecificationsUnit: 3D Print Pro 2Capacity: 43 m³h Weight: 8.2kg Motor: Axial Fan Output: 6.6WElectrical supply: 115-230V Hertz: 50/60HzFull Load Current: 0.2A Noise Level: Below 50 dBA (at typical operating speed)Environmental operating range:Temperature: +5o C to + 40o CHumidity: Max 80% RH up to 31o C Max 50% RH at 40o C018Contact Information BOFA Headquarters19-20 Balena Close Creekmoor industrial Estate PooleDorsetBH17 7DUUKPhone: +44 (0) 1202 699 444 BOFA Americas303 S.Madison Street StauntonIllnois62088USAPhone: +1 (618) 205 5007 BOFA International GmbH Sudring 62D-21465Wentorf bei Hamburg GermanyPhone: +49 (0) 40 7393735-15。
2LKPLC编程软件培训教程
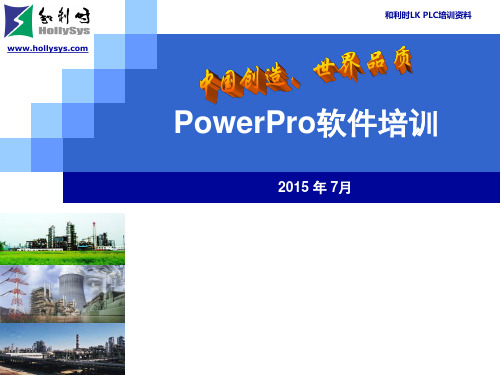
第三章 PowerPro 存储区和变量
变量定义
所谓变量,就是用字母、数字和下划线组成的一个标识符。在使用前, 就需要对这个标识符进行定义,用来说明这个标识符所标识的对象。 每一个标识符对应一种数据类型。
在LK系列PLC中,可以用定义的标识符来表示一些实时改变的参数
使用变量,可以替代存储器寻址方式在程序中使用,可以根据实际定
第二章 PowerPro快速入门
配置普通模块
1.添加PROFIBUS DP总线主卡
PROFIBUS DP主卡参数相对本地背板总线要多,其中基本参数由系统自动生成, 不能进行修改。“DP参数”中保证站地址为“1”。“总线参数”一般需要设 臵通讯的波特率为500kBit/s,其他参数使用默认值即可。
Date: 2015-7-16 Page: 17
境,采用符合 IEC61131-3 国际标准的编程软件编写应用程序,具有五种 编程语言(LD、IL、FBD、ST、SFC),并且可相互转化
Date: 2015-7-16 Page: 4
第一章 PowerPro软件概述
第二节 PowerPro软件特点
可以任意调用不限点数的定时器和计数器,定时器最长时间可达最 长49天; 支持多种数据类型存储方式,如时间型、时间日期型、自定义的一维、 二维和三维数组、指针型、枚举型、结构型等; 软件具有超强的运算功能,如PID运算、初等数学运算等等; 支持用户自定义函数功能库,大大提高了程序的可再利用性; 具有离线仿真功能,极大地方便了程序的调试;
第二章 PowerPro快速入门
4 创建新工程 新建工程
CPU配臵:根据CPU型号进行选择。各项参数的默认设臵已能满足绝大 多数应用需求。
Parker PROmech LP28线性位器说明书

Product Release Third Quarter 2008HMI • Controls • Drives Linear Motor PositionersServo Motors043008PROmech Strip Seal Features and Benefits 4Specifications 5MPJ Features and Benefits 8 Specifications 9Aries Drive/Controller Features and Benefits 12 Specifications13Compax3 ETHERNET Powerlink Features and Benefits 16 Specifications 17XPR15 PowerStation Features and Benefits 20 Specifications 21Product Overview22Table of ContentsAn optional strip seal cover provides increased protectionand a longer life, reducing downtime with the PROmech™LP28 linear positioner.3PROmechParker has developed an optional cover seal for the PROmech™ LP28 series linear positioners. The new cover seal protects the screw from particulate matter and other debris, resulting in longer product life, a cleaner-running solution and an aesthetically appealing design. The PROmech series is now a more well-rounded solution for light-industrial OEM applications with more protection than ever.Available in two models, the LP28 and the LD28, PROmech series positioners are designed for Life Science OEM instrument manufacturers working to speed their time to market and reduce the overall installed cost for linear motion axes. The new strip seal option on theLP28 adds just 17 mm in overall length due to the carriage design, but adds no overall width or height, thus maintaining a compact footprint that allows OEMs to make the most of their machine space. In addition to the new strip seal option on the LP Series, the PROmech Series comes completely assembled and tested and includes drive screw, thrust bearings, motor mount, coupling and motor.FEATURES• Uses fiber impregnated seal to maintain rigidity and prevent seal stretch or seal wear• Uses UHMW polyethylene to keep seal friction to a minimum and reduce seal wear, increasing seal life• Provides protection to an IP30 rating• Matches the black actuator body for optically sensitive environments • Is easy to mount with strip seal clamp• Allows for minimum seal bend radius for low overall height4PROmech Part Numbering System[1] D01 not available with M7xx[2] D26 not available with M1xx[3] Tables with travel 75 mm or less may have limited sensorcapabilities and may be limited to 0, 1 or 2 sensors5The MaxPlus-J is designed for applications with aMPJ SeriesParker Hannifin has added a high inertia option to the popular MPP (MaxPlusPlus) motor family. This new motor family with higher rotor inertia is called the MaxPlus-J (MPJ). The MPJ is designed for the demanding applications found in today’s high-performance servo systems and offers the same design specifications as the MPP motors, but gives users even higher inertia. Now, on many applications where customers might add a gearhead, they can simply use an MPJ motor, saving money and eliminating the speed constraints normally associated with a gearhead.Parker’s MPJ motors feature the same segmented lamination technology as the MPP motors, which yields as much as 40% higher torque per unit size than conventionally wound servo motors. “Potted” stators improve heat transfer for better thermal efficiency, resulting in increased torque at the motor shaft. High-performance neodymium magnets are employed for higher acceleration rates. The MPJ is offered as a standard option on four frame sizes from 092 to 142. It is available as a custom motor option on the MPP190, MPP230, and MPP270mm motors.FEATURES• Three to ten times the inertia of the standard MPP servo motors.• Higher inertia available in four standard frame sizes: 92mm, 100mm, 115mm, and 142mm• Motor brake option available for all MPJ motors• Segmented core Technology — 40% higher torque compared to standard wound servo motors.• Exceptional torque density resulting in more torque / volume.• Potted stator design resulting in better heat transfer and more available torque.• Thermistor protection• UL and CE approved• Two-year warranty89All published product specifications are subject to change without notice.Combining the versatile and cost-effective Aries digitalservo drive platform with the advanced control capabilitiesof the ACR servo controller, Parker’s new Aries Controlleroffers users a single-axis servo drive/controller withEthernet communication and HMI connectivity.11Aries ControllerThe Aries Controller single-axis servo drive delivers a wide range of standalone capabilities with Ethernet connectivity, onboard I/O, and easy-to-use project development tools, commissioning single-axis motion is simple and efficient.Leveraging the industry-leading performance of the ACR9000 motion platform in a single-axis form factor, the Aries Controller contains motion and programming capabilities far beyond its peers. From multitasking programmability to encoder-based following with real-time phase advance, the Aries Controller is the highest-performance single-axis controller in its class.FEATURES• 7 onboard inputs [4 standard, 3 high speed], 4 outputs• Advanced multitasking of up to 16 simultaneous programs• Integrated 2 port Ethernet hub• ACRView Software Development Kit• Rotary or linear servo motor control• 3, 4.5 and 6.3 A RMS continuous current• 120/240 VAC power input• Multiple feedback options—Smart encoder, quadrature encoder, Heidenhain EnDat absoluteencoder• Auto-tuning• CE [EMC & LVD], UL RecognizedAries Controller Part Numbering System12All published product specifications are subject to change without notice.Compax3 EPLThe Compax3 digital servo drives are now enabled with ETHERNET Powerlink (EPL) motionbus technology. With all 12 power levels of the Compax3 drives now EPL enabled, system performance is increased while overall system cost and installation time have been decreased. The Compax3 family joins three power levels of the Aries EPL servo drives as well as the ACR9030 and ACR9040 multi-axis EPL controllers in Parker’s expanding line of EPL products.ETHERNET Powerlink is a high-speed, digital motion-bus solution connecting a motion controller to multiple drives and I/O points using standard Ethernet networking hardware. This centralized, real-time communication system for automation and motion control makes Ethernet deterministic for real-time industrial applications. ETHERNET Powerlink systems combine the high performance of centralized motion control with the lower costs of decentralized machine architectures. System design and machine installation times are greatly reduced due to the simplified, inexpensive and readily available Ethernet cables that replace traditional, expensive analog control and feedback cables.FEATURES• Available in both 120/240 VAC and 480 VAC input versions• Current output from 2.5A RMS continuous to 155A RMS continuous • 8 inputs and 4 outputs• Available with ETHERNET Powerlink motionbus• Certified Category 3 Safety (EN954-1 Cat. 3)• Support for SSI or secondary encoder feedback for master signal• Resolver, Encoder, Sine-Cosine or Stegmann feedback• Internal regeneration circuitry with external resistor connections• Programs with ACRView• Easy-to-use wizards-based configuration via C3 ServoManager™• Full diagnostic, tuning and 4-channel oscilloscope features provided in the standard C3 ServoManager TM software• CE (EMC & LVD) without adding extra hardware16Compax3 Part Numbering System17New 15” XPR model offers the largest display size yetXPR15PowerStationThe XPR15 brings Interact Xpress’ unique distributed HMI capabilities to the largest display size ever. The XPR family now includes 6, 8, 10.4 and 15” display sizes. XPR PowerStations come with Interact Xpress runtime and online development software and are specifically designed to optimize the performance, storage and connectivity features of Xpress.Interact Xpress HMI applications are developed, edited, published and run in an HMI that is a Web Server, allowing users and OEMs to easily publish upgrades and applications to any global location with an Internet connection and a web browser. Interact Xpress combinesa rich, graphical runtime interface with HMI development tools that can be accessed from either the HMI panel or any PC running Internet Explorer®.FEATURES• Sophisticated graphics look and feel• Intuitive development environment• Eliminates version control issues• Integrated Web Publishing capability for distributed applications• No version control issues with Web published development• Applications can be served, created and edited online from any PC with Internet Explorer• Available offline development software, allows work on applications when a live internet connection isn’t available• Advanced security for single or multi-user applications• Tools for historical alarm data• Capacity for complex graphics and animations• Standard Ethernet port for both networking and controller communications • More than 35 device communication driversNew Interact Xpress Version 1.62 SoftwareParker Product Code: 757 Model #Interact Xpress Manager Version 1.62 Development IXM-01502021XPR PowerStations come with Interact Xpresssoftware pre-installed. Xpress fully leverages the wide availability of web browsers to enable Distributed HMI, remote support and application sharing on the Internet and IP Networks Xpress HMI applications are developed, edited, published and run in an HMI that is a Web Server.All published product specifications are subject to change without notice.10-500 Hz 1grms (random-operational-CompactFlash)*Actual storage volumes may be higher~ Class 1 Div. 2 Agency Approval [optional] pending on 8”, 10.4” and 15” Display Options.For more information about XPR PowerStations visit /Xpress .22About Parker Hannifin CorporationParker Hannifin is a leading global motion-control company dedicated to delivering premier customer service. A Fortune 500 corporation listed on the New York Stock Exchange (PH), our components and systems comprise over 1,400 product lines that control motion in some 1,000 industrial and aerospace markets. Parker is the only manufacturer to offer its customers a choice of hydraulic, pneumatic, and electromechanical motion-control solutions. Our company has the largest distribution network in its field, with over 7,500 distributors serving nearly 400,000 customers worldwide.The Aerospace Groupis a leader in the development, design,manufacture and servicing of control systems and components for aerospace and related high-technology markets, while achieving growth through premier customer service.The Fluid Connectors Groupdesigns, manufactures and markets rigid and flexible connectors, and associated products used in pneumatic and fluid systems.The Hydraulics Groupdesigns, produces and markets a full spectrum of hydraulic components and systems to builders and users of industrial and mobile machinery and equipment.The Automation Groupis a leading supplier of pneumatic andelectromechanical components and systems to automation customers worldwide.The Climate & Industrial Controls Groupdesigns, manufactures and markets system-control and fluid-handling components andsystems to refrigeration, air-conditioning andindustrial customers worldwide.The Seal Groupdesigns, manufactures and distributes industrialand commercial sealing devices and relatedproducts by providing superior quality and totalcustomer satisfaction.The Filtration Groupdesigns, manufactures and markets qualityfiltration and clarification products, providingcustomers with the best value, quality,technical support, and global availability.The Instrumentation Groupis a global leader in the design, manufactureand distribution of high-quality criticalflow components for worldwide processinstrumentation, ultra-high-purity, medical andanalytical applications.Parker’s CharterT o be a leading worldwide manufacturer of components and systems for the builders and users of durable goods. More specifically, we will design, market and manufacture products controlling motion, flow and pressure. We will achieve profitable growth through premier customer service.Product InformationNorth American customers seeking product information, the location of a nearby distributor, or repair services will receive prompt attention by calling the Parker Electromechanical Automation Division at our toll-free number: 1-800-358-9070.2324Servo and Stepper Motion Control Systems Rotary and Linear Servo Motors P: 707.584.7558 or 800.358.9070F: 707.584.3793Human-Machine Interface and Integrated Machine Control P: 513.831.2340 or 800.233.3329F: 513.831.5042© Copyright 2008, Parker Hannifin Corporation. All rights reserved.Electromechanical Positioning Systems Gearhead and Linear Systems P: 724.861.8200 or 800.245.6903F: 724.861.3330Electromechanical Actuator & IPS P: 330.336.3511F: 330.334.3335Technical Support and Customer Service ContactsDivision ContactsServo and Stepper Motion Control Systems Rohnert Park, CAP: 707.584.7558 or 800.358.9070F: 707.584.3715Human-Machine Interface and Integrated Machine Control Milford, OHP: 513.831.2340 or 800.233.3329F: 513.831.5042Electromechanical Positioning Systems Irwin, PAP: 724.861.8200 or 800.245.6903F: 724.861.3330Electromechanical Actuator & IPS Wadsworth, PA P: 330.336.3511F: 330.334.3335Gearheads and Linear Systems Port Washington, NYP: 516.484.5353 or 800.305.4555F: 516.629.8000Rotary and Linear Servo Motors New Ulm, MNP: 507.354.1616 or 866.506.3573F: 507.233.2390CD Contents:Competitive Data, PowerPoint Presentations, Fliers, Pricing, Images,Press Releases, Sales Bulletins, Software and User Guides (if applicable).25Parker Hannifin Corporation Electromechanical North America Division 5500 Business Park DriveRohnert Park, CA 94928800.358.9068。
智能悬挂相机KP2 Pro安装指南说明书

DISTRACTION DETECTEDKP2PROINSTALLATIONGUIDENot an Installer? ...............................................................................12LED & BUZZER SPECIFICATIONS ...............................................13TECHNICAL SPECIFICATIONS . (14)Prepare Your KP2 ...............................................................................6Attach Your Camera to the Windshield ........................................7Connect the KP2 to Your Vehicle’s Power Source.....................8HOW TO TEST YOUR INSTALLATION .. (9)EVENT TRIGGERKP2PRO INSTALLATION GUIDEKP2 Vehicle RecorderDouble-Sided 3M™Tape(One Adhered to Bracket, One Extra Pc.)*64GB SD Card (Pre-Installed)*128GB SD AvailableUpon RequestSquare AdhesiveCable Clips (x5)Alcohol Prep Pad (x2)Nano SIM Card (Pre-Installed)Power Cable 1 From BracketRemovable Wedge Block(Driver-Facing Camera Ordered Separately)Torx ® WrenchPower Cable 2 (3-Wire Type)Windshield BracketLens Angle LockUnscrew the right-side bracket.Remove the KP2 from thebracket to adjust camera angleor insert/remove SIM/SD card.Applied screws for designpurpose only.FRONTSIDECamera LensSIDE COVER OPENBACKNano SIM Slot (4FF)Release TabMicro SD Card SlotMemory SD Card Slot2nd Camera(Model: KP2-DFC)Ecall/Panic ButtonLED Types:Warning LED (RED)Record LED(BLUE)Network LED(GREEN)Bluetooth Pairing ButtonDISCLAIMERThe KP2 installation featured in this guide is designed for professional installation. SmartWitness assumesinstallers possess knowledge of current, generally accepted industry installation standards and practices.The process outlined in this document accounts for driver positioning on the left side of the vehicle.Please adjust the installation accordingly if you’re working with driver positioning on the vehicle’s right side.1. Use the Torx ® wrench provided in the package contents to open the side cover of the device. You’ll notice that both the microSD and SIM cards come pre-installed. See Diagram A .2. Keep the side panel open. It allows you to remove the KP2 from its mount and adjust the driver- and road-facing cameras. Prep the cameras for adjustments. • Loosen the KP2’s top screw (for the road-facing lens) with the Torx wrench. • The driver-facing camera has a release tab next to the lens.Note: You must order the KP2’s driver-facing camera as a separate accessory. White-label KP2s are exceptions.3. Go to your vehicle, and hold your KP2 where you’ll mount the bracket. Your KP2 placement should reduce the windshield’s blind-spot footprint, with the road-facing camera within the top 2" of the wiper path. The device should reside close to the center of the windshield. See Diagram B .Note: The driver-facing lens needs complete visibility of the driver,without any physical or visual obstructions. Ensure your vehicle’s sun visor doesn’t complicate camera visibility.4. While holding the KP2 in place, rotate each camera until they’re at the desired angle.5. Remove the protective decals from each lens.6. Use the Torx wrench to tighten the top screw on the KP2 and lock the road-facing camera’s position.Once you’ve secured the road-facing camera, please go on to Attach Your Camera to the Windshield .HOW TO INSTALL YOUR KP2Diagram B Diagram AYour vehicle’s windshield temperature shouldn’t be too hot or cold. SmartWitness recommends installing your KP2 in moderate temperatures (50°F~80°F).If in severe cold weather, use the vehicle defrosters to warm and dry out the windshield.Ensure your windshield is dry and has no chips or cracks before installation. If the windshield is compromised, device application may cause chips or cracks to spread.1. Clean the windshield with your alcohol wipe. See Diagram C . Allow time to dry.2. Remove any film left over from the solution.3. Remove the plastic from the tape on the mounting bracket.4. When attaching the KP2 to the windshield, position the bracket so it’s flush with the windshield.Note: When installing the KP2 in a truck, FMCSA mandates that the device’s camera is in the top 2" of the windshield wiper sweep.5. Apply your KP2 to the windshield, and maintain pressure for at least 30 seconds.6. After mounting your KP2, use the Torx ® wrench to re-secure the device’s side cover. This locks both camera positions in place.7. Go outside the vehicle, and check whether 80%–90% of the tape’s surface area connects with the glass. Momentarily apply pressure where the camera doesn’t connect to the glass (if necessary).Once the device is correctly attached to the windshield, continue to Connect the KP2 to Your Vehicle’s Power Source.Diagram CHOW TO INSTALL YOUR KP2If you are not a professional technician, click here to request installation from an approved SmartWitness installer. By continuing this process without a certified installer, you accept the ramifications of tampering with your vehicle’s power source.1. Turn off your vehicle.2. Take your main power cable, and place it where it’ll reside alongside the vehicle’s headliner and A-pillar. This shows you where to route the cable and how much slack to leave to connect the adapter cable to the vehicle’s power source.3. Clean the space where the cable clips will reside with an alcohol wipe. Allow time to dry.4. Once the windshield is dry, attach clips where you’ll place the cable. Ensure the clips are evenly spaced, around 6" apart. Keep the opening of the clips face up, and ensure the cable remains taut.5. Slide the power cable from the bracket into the clips. Your cable should look like Diagram D .6. Route the power cable around the side and behind interior panels or weather stripping to secure it. See Diagram E . The cable should fall near the vehicle’s fuse box/power source.7. Attach the KP2 main power cable to one of the compatible poweradapter options. Let’s use the bare 3-wire connection adapter provided in the box for this walk-through. See Diagram F .Note: SmartWitness provides optional power adapter accessories separately.8. Identify each connection wire on the 3-wire adapter: black, white and red. Note: Ensure your 3-wire connection has fuses attached to the red and white wires within 4" of the power source. This is a requirement that protects both your device and your vehicle.9. Connect each wire to its associated power source. • Black – ground or battery (-) • W hite – true ignition or ACC • R ed – power or battery (+)Go to How to Test Your Installation to ensure you’ve properlyapplied power to your device.Diagram DDiagram EDiagram FHOW TO INSTALL YOUR KP2After installing the KP2 in your vehicle, test whether it is operational.1. Turn on your vehicle. Your camera should power on.2. You’ll see a Red /Blue /Green light sequence during your camera’s boot-up process (see LED Reference Table ).3. After your camera completes the boot-up process, check for a solid Blue light. This indicates proper operation and recording.4. Check for a Green light that remains on, indicating connectivity.5. Watch for a Blue light. After 5 minutes, if both the Green and Blue lights don’t remain on, an error has occurred. See Diagram G .TROUBLESHOOTING ERROR SCENARIOS If your KP2 has:• S olid Red , Blue and Green lights, then a camera isn’t receiving a video signal. Check your camera’s connection.• A solid Blue light, but the Green light is blinking or is off, then clean and correctly reinsert your SIM card.- I f the Green light still blinks, this is a configuration or server issue that requires SmartWitness support .• A Red blinking light, then there is an SD card error or corruption. Contact your local distributor or SmartWitness support to repair or replace your SD card.• A solidRed light, then your device isn’t receiving enough voltage or amperage. Check the output of your power source or your ground (black wire) connection.If your KP2 install is operational, please move on to How to Calibrate Your G-Sensor .Diagram GPark your vehicle on a flat surface for calibration.After your camera boots up, press the G-sensor calibration button. This is the small Red buttonto the right of the e-call/panic button.You’ll hear a beep, and the KP2 LED light will blink briefly to indicate that the G-sensor calibration has registered.You’ve completed the first steps of your KP2 installation. To adjust your settings, continue toHow to Configure KP2 Settings.To finalize your installation and onboard your device, scan the QR code. Download and open the app. Scan your device’sIMEI label, and follow the walk-through featured below.Access KP2 Installation App7. After you’ve made changes and activated the appropriate features, click Confirm to save your configuration.5. Choose preferences for in-cabin alerts, an alert’s volume level or activation of different ADAS and DSM events.8. On the home screen, you’ll see a success message validating your saved configuration.6. If you’re unaware of asetting’s function, click the infoicon to learn more.1. Ensure the IMEI code in the app matches your device’s IMEI. If there isn’t a match, click No and contact SmartWitness support. If there’s a match, click Yes to continue.4. If you adjust either camera, click Refresh Images to update road- and driver-facing camera e the arrows to adjust yourvehicle’s “Horizon” and “Hood” lines.Ensure your “Hood” line is in the bottom one-fourth of your image. Scroll down and click Next to save the “Horizon” and “Hood” lines.2. Read the instructions to understand more about yourvehicle’s “Horizon” and “Hood” lines.Click Show Me How for a brief video walk-through of the device attachment process.3. Select your KP2 camera configuration.Choose the driver’s side of the vehicle (from the perspective of the front of the vehicle).ClickNext to set your vehicle’s“Horizon” and “Hood” lines.Congratulations. You’ve configured your device settings.You’ve finished your KP2 installation and device calibration. Your KP2 is ready to go.If you have any complications during the installation process or have any questions, please contact our support team at ************************ or call us.North America, South America, APAC +1 (312) 981-8774 EMEA+44 (0) 1483 397005NOT AN INSTALLER?Once you complete the training (about a 30-minute webinar), SmartWitness will provide you with login credentials for the SmartOPS portal.To schedule training, please complete the online form here.|FOR MORE INFORMATION, CONTACT *********************************Chris Garbade 512.387.2980 x715。
vLocPro2系列管线仪操作手册
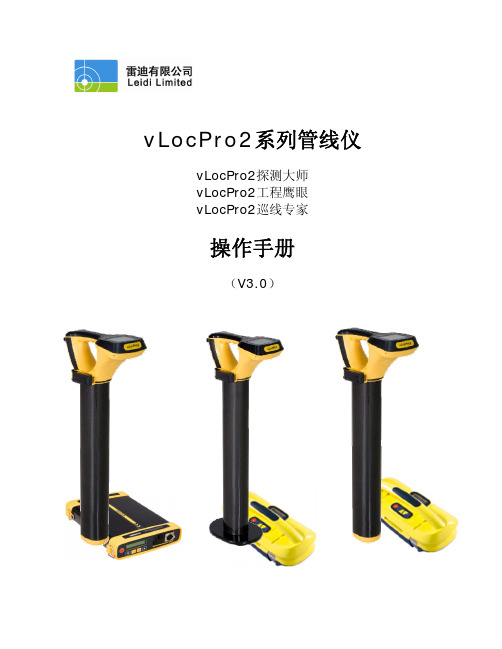
2 标准接收机...................................................................................................................................................... 8
2.4 定位模式 .................................................................................................................................. 14 2.4.1 接收线圈与定位信号 ......................................................................................................... 14 2.4.2 峰值定位模式.................................................................................................................... 15 2.4.3 峰值箭头定位模式............................................................................................................. 17 2.4.4 宽峰定位模式.................................................................................................................... 18 2.4.5 谷值定位模式.................................................................................................................... 19 2.4.6 示踪探头模式.................................................................................................................... 20